Can ceramic media replace glass beads in shot peening?
December 11, 2024
Shot peening is a key surface treatment technology in modern manufacturing. Choosing the right shot peening medium is crucial to process effect and economy. This article will compare the advantages and disadvantages of glass beads and ceramic media in shot peening, revealing that ceramic shot peening has gradually replaced glass beads as a more popular choice under high-performance and environmental protection requirements.
The function of Shot Peening
The core function of shot peening is to form a compressive stress layer on the surface of the material through the high-speed impact of the medium particles, thereby improving the performance of the material.
According to application requirements and industry characteristics, these functions can be divided into the following four aspects:
Improve fatigue strength
Enhance corrosion resistance
Improve wear resistance
lmprove surface roughness
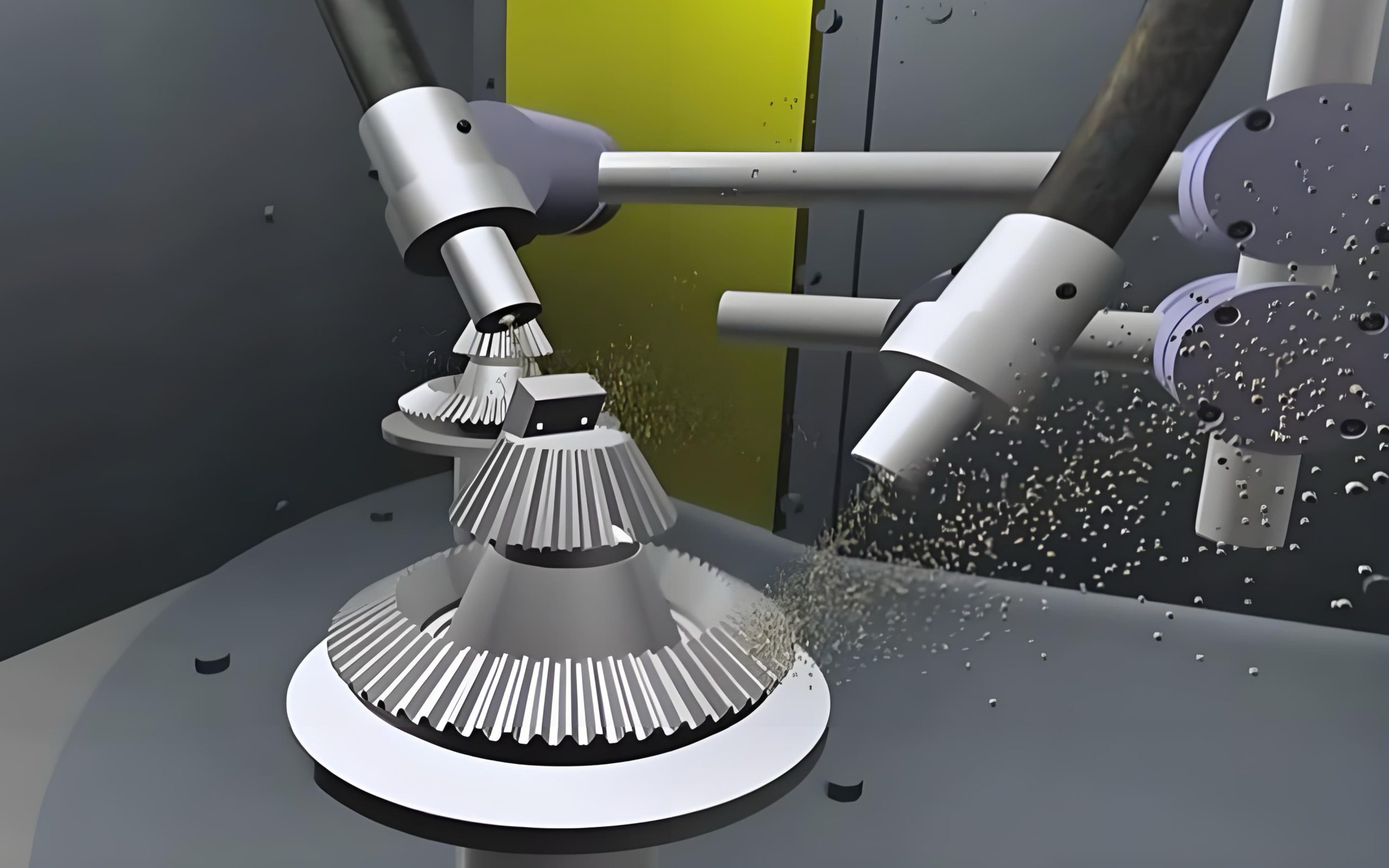
After discussing the specific functions of shot peening, choosing the right medium becomes a key link affecting the technical effect.
Glass beads and ceramic shot peening are two mainstream media, and their respective physical properties and performance determine their applicable fields and process effects.
Next, we will focus on analyzing the characteristics and application performance of the two to lay the foundation for functional comparison.
Introduction to glass beads and ceramic shot peening
Glass beads
Historical background:
Glass beads, as a common medium for sandblasting and polishing, have a history of use that can be traced back to the early 20th century. At first, the application of glass beads was mainly concentrated on metal surface cleaning and surface finishing processes.
Afterward, glass beads became an irreplaceable shot peening medium when processing precision castings, non-ferrous metal devices, and some parts that require fine surface treatment because of their advantages such as small particle size, small contact area with parts, and more uniform stress elimination.
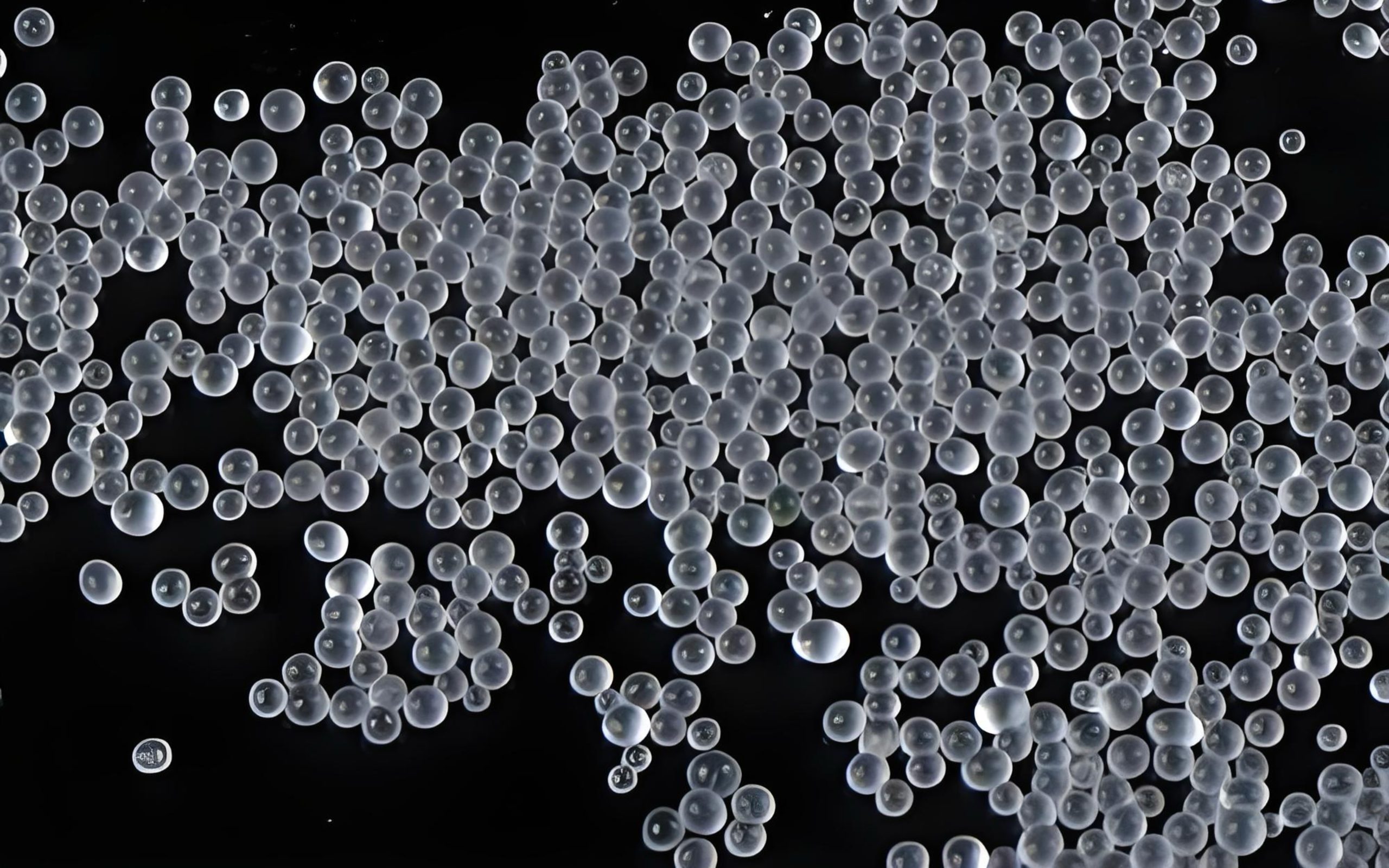
Physical properties:
A particle made from high-purity silica sand or recycled glass.
Mostly transparent or translucent, uniformly spherical, with a smooth surface, low density, and hardness usually between 5-7 Mohs hardness.
It can provide low-impact force and is suitable for surface finishing rather than deep strengthening.
Historical background:
The origin of ceramic shot peening can be traced back to the mid-20th century. It was originally used in the aerospace and military fields to meet high-strength and high-precision processing requirements.
As its production technology matures, ceramic media has gradually been introduced into other industries such as automobile manufacturing, mold processing, and building steel structures. Its excellent hardness, wear resistance, and environmental protection characteristics make it stand out in high-end manufacturing.
Physical properties:
Shot peening media made by high-temperature melting of ceramic raw materials, cooling, and grinding.
It is a white sphere with a uniform and round shape, usually between 8-9 Mohs hardness, and a high density.
It has good wear resistance and is suitable for high-strength surface treatment requirements.
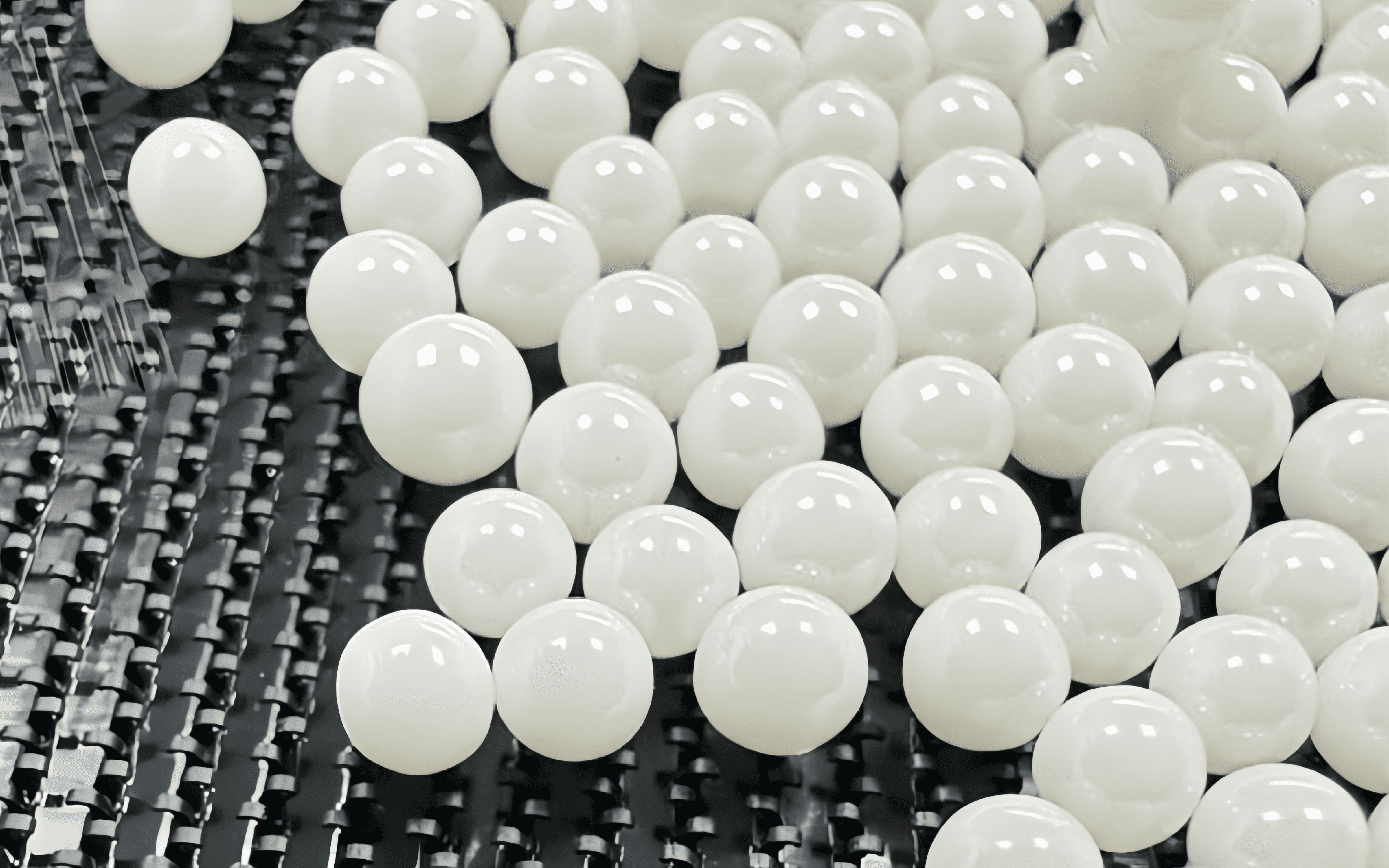
Please see the table below for chemical properties:
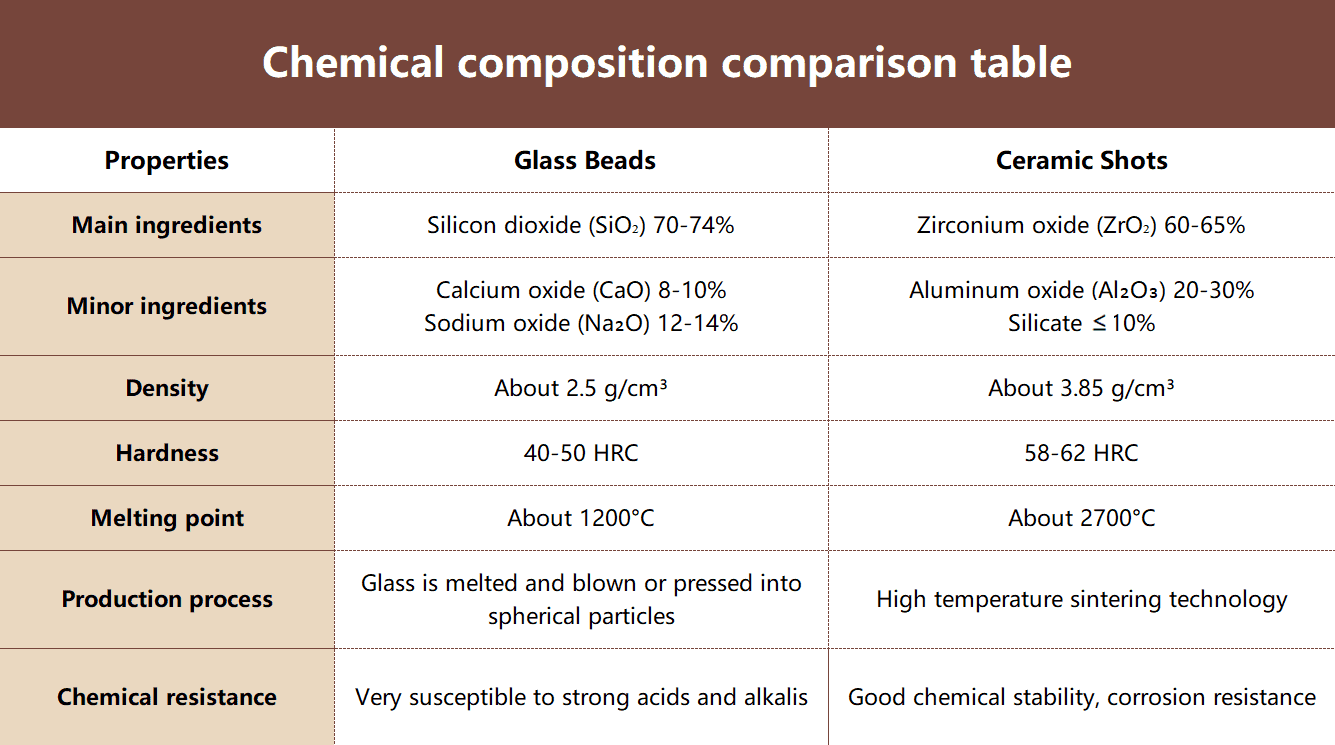
After understanding the basic information about glass beads and ceramic media, we will further compare the functions and application effects of these two media, analyze their advantages and disadvantages in shot peening, and help customers make a more scientific choice.
Similar application industries
Aerospace
Used for aircraft structural parts and engine components, such as turbine blades and fuselage skins.
Automotive industry
Used to enhance the fatigue life of key components such as automotive suspension springs, gears, and drive shafts.
Energy industry (wind power and nuclear power)
The main shaft and blade connection parts of wind power generation equipment need shot peening to resist long-term high-frequency loads; the pressure vessels and turbine components of nuclear power plants also rely on shot peening to extend their life.
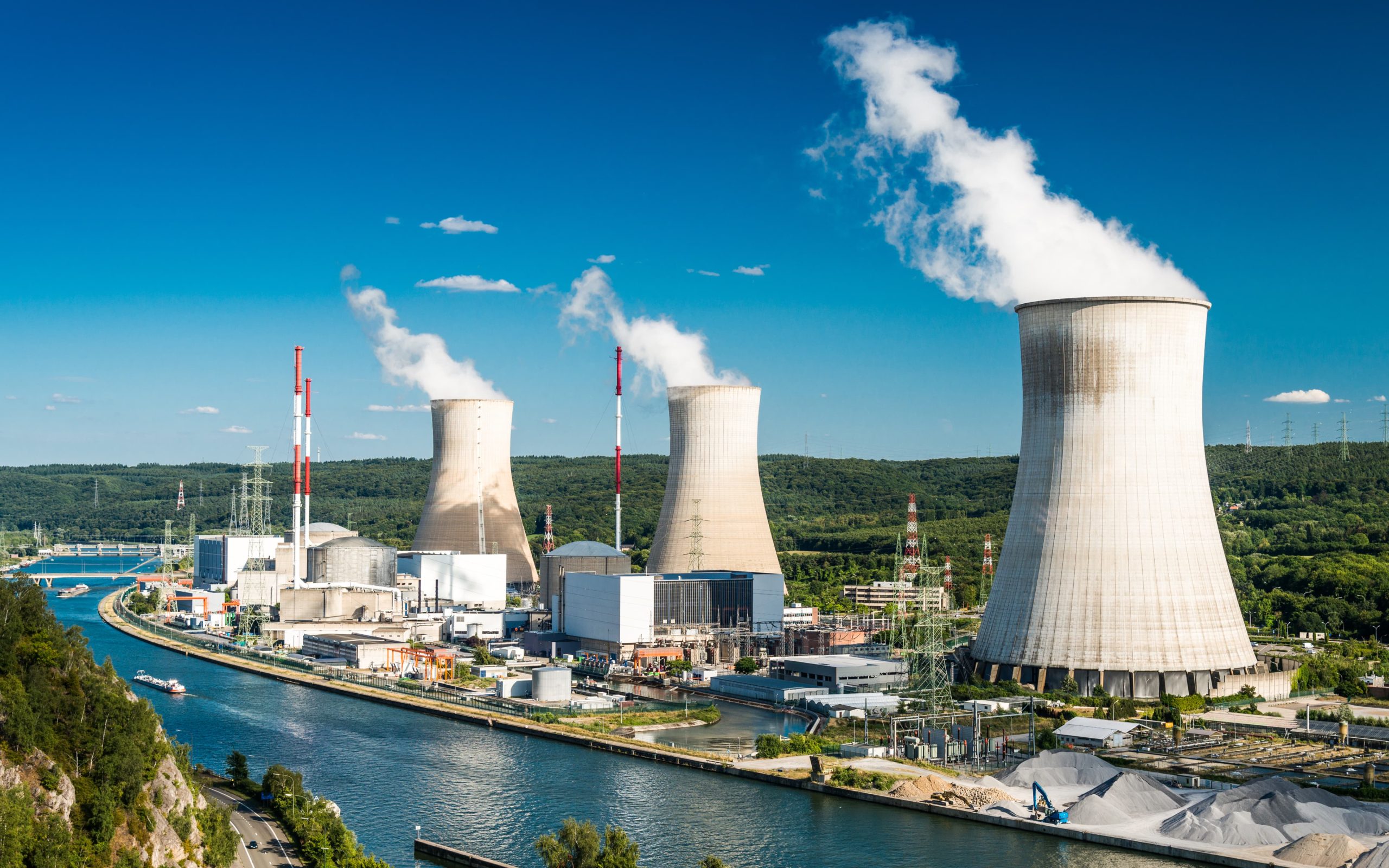
Mold manufacturing
Shot peening the mold surface can slow down wear and increase service life.
Medical devices
Used to strengthen the surface of implants (such as hip prostheses, screws, etc.) to increase fatigue strength.
Although the functions and application fields of shot peening are very wide, in actual production, customers often face a series of pain points, which are the key to determining the choice of media.
Next, we will further analyze the common problems and needs of customers in the shot-peening process.
Customer pain point analysis
Surface strengthening uniformity and stability
Customers generally worry about whether the shot peening media can continue to provide a stable surface-strengthening effect during use. This includes:
- Processing consistency: Whether the shape and size of the media particles are uniform directly affects the uniformity of the surface strengthening layer. Uneven stress distribution during processing may cause component performance degradation or failure.
- Durability and stability: In high-intensity use scenarios, the wear resistance, breakage rate, and retention performance of the media are reliable, which is related to the repeatability of surface quality.

Material compatibility
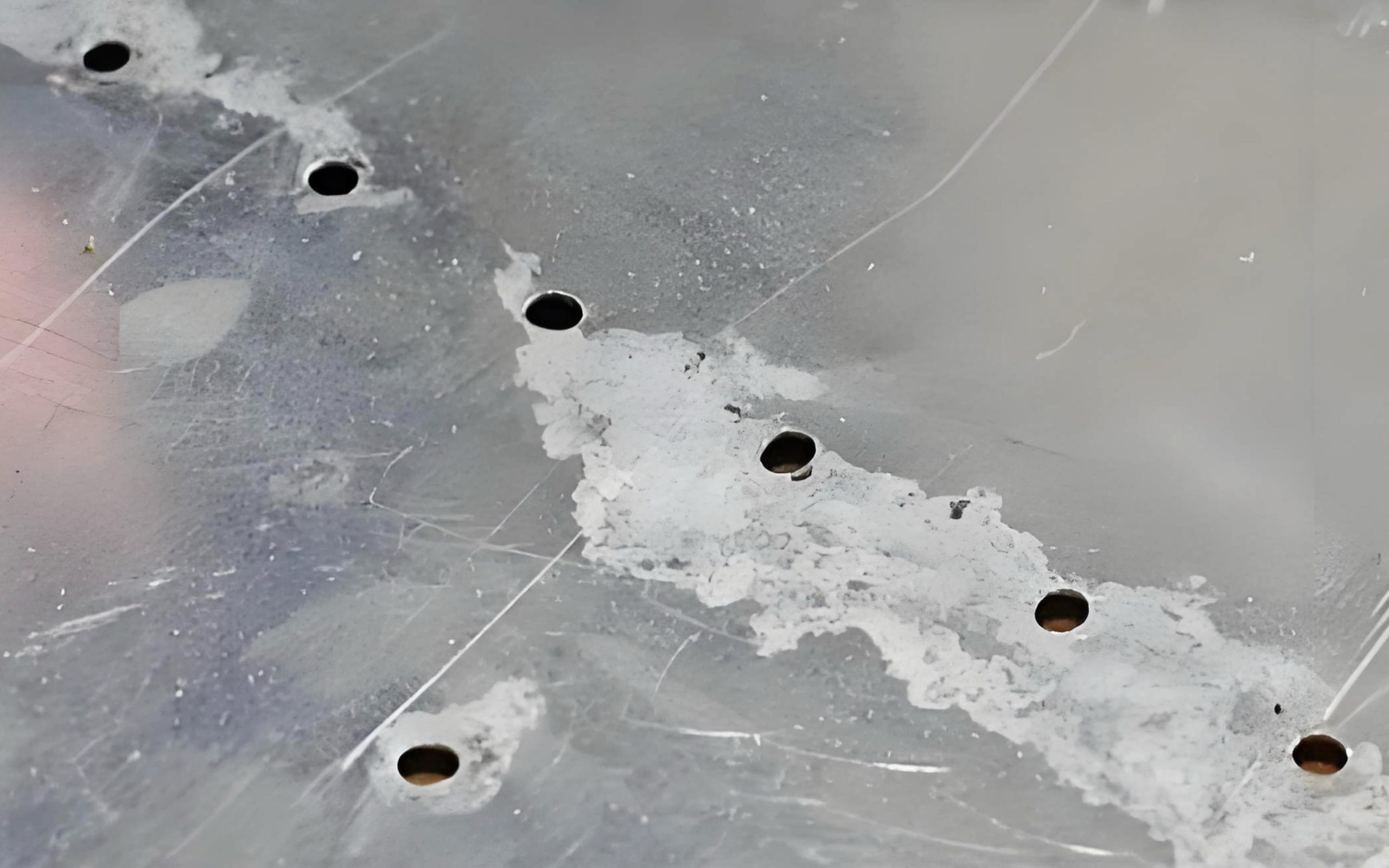
Workpieces of different materials (such as aluminum alloy, high-strength steel, stainless steel, and titanium alloy) have different requirements for the hardness, density, and elastic modulus of shot peening media. Customers need to clarify the following issues:
- Whether the surface of flexible materials (such as aluminum and magnesium) will be damaged due to the media being too hard or too dense.
- Whether high-strength materials (such as titanium alloys) require higher hardness media to achieve sufficient surface compressive stress.
Efficiency and economy of use
Customers’ choice of shot peening media is often constrained by efficiency and cost, which are specifically manifested in:
- Media life: Does the media have a long service life, thereby reducing the frequency of replacement and downtime?
- Cost control: Is the initial purchase cost and long-term use cost controllable, especially for large-scale production enterprises?
Specific application requirements
For industry customers who are shot peening, their needs may be very specific:
- Fatigue life extension: Customers want to significantly improve the fatigue life of parts, but are worried that the shot peening process is not enough to achieve the expected effect.
- Surface roughness requirements: Some industries (such as aerospace and medical devices) have strict requirements on the smoothness of the surface after shot peening, and any excess roughness may increase the subsequent processing costs.
- Enhanced corrosion resistance: Especially in the aerospace and energy industries, parts need to resist corrosion in harsh environments. Whether the surface compressive stress layer of shot peening can effectively prevent crack propagation.
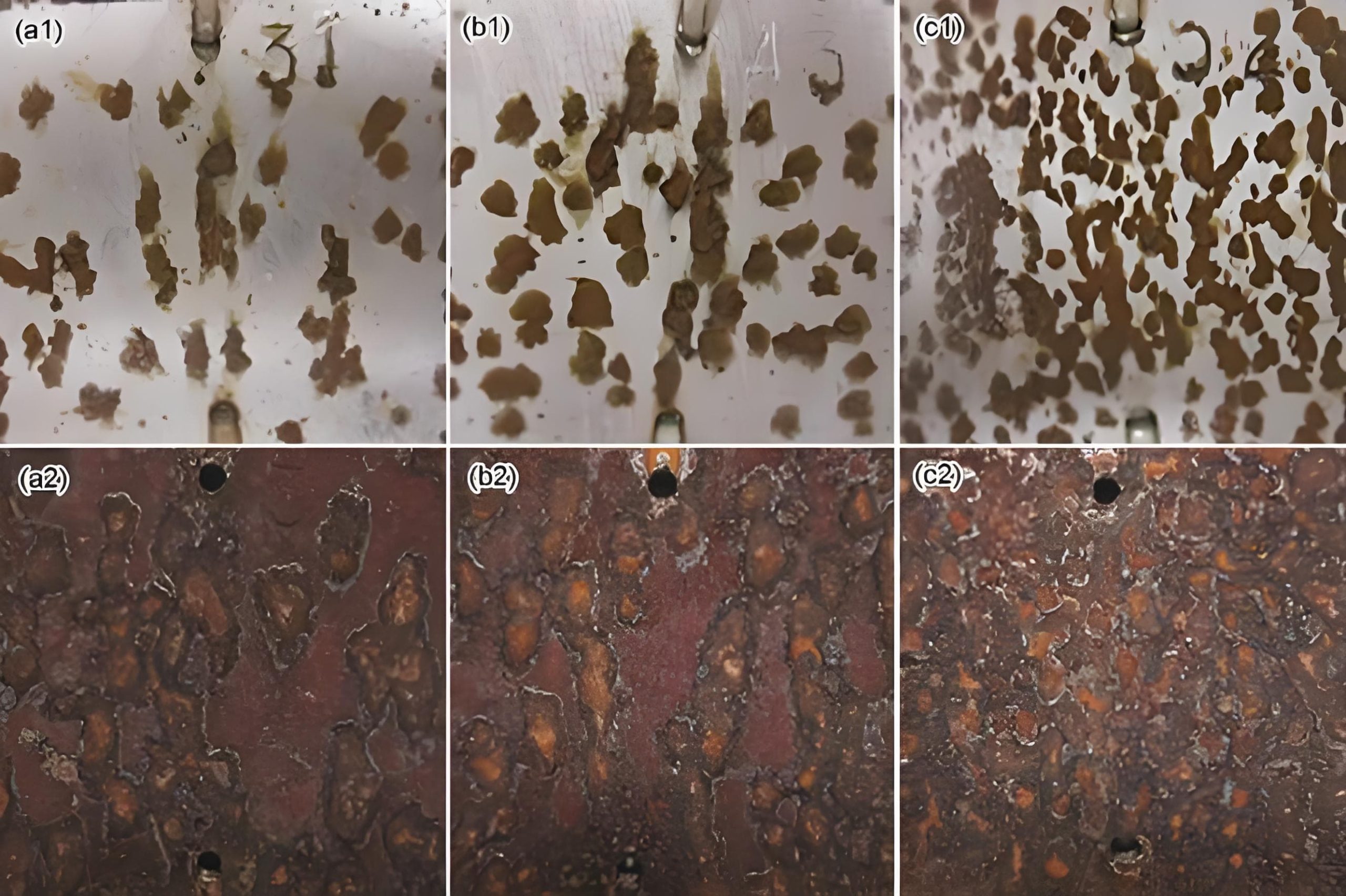
Environmental and health safety
As environmental protection requirements become increasingly stringent, customers will also pay attention to whether the shot-peening media has the following problems:
- Dust pollution: Low-quality or brittle media may generate a lot of dust, affecting the operating environment and personnel health.
- Sustainability: What is the recyclability of the media and whether the disposal cost of the waste is reasonable?
Technical and operational thresholds
Shot peening requires highly specialized technical support, but customers may face the following problems:
- Equipment compatibility: Is the shot peening equipment suitable for the new media, and does it require additional adjustments or upgrades?
- Operational complexity: Does the use of the media require special process conditions, increasing technical complexity, or training costs?
- Adaptability to new materials: Can new component materials (such as composite materials) be successfully applied to existing shot peening technology?
Ceramic shot peening VS glass beads: Who has more advantages?
Uniformity and stability of surface strengthening
Both media have a round and smooth appearance and can work evenly.
However, the crystal structure of ceramic shot peening has excellent compressive resistance and toughness and is not easy to break, especially suitable for high-intensity and repeated impact working environments.
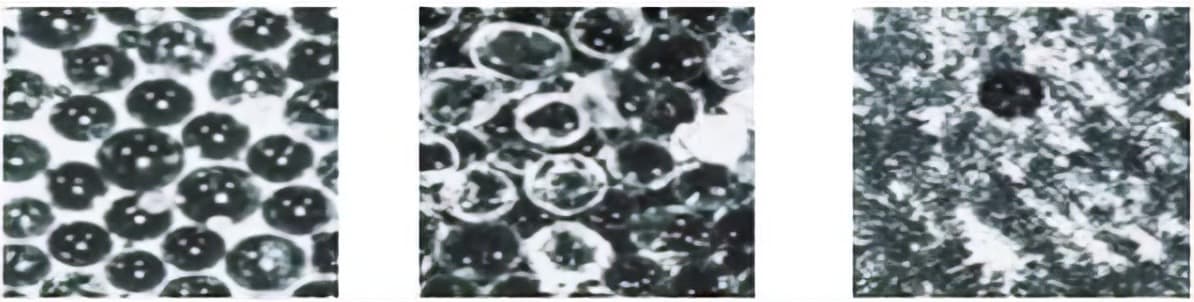
In contrast, glass beads are easy to break under high-intensity or frequent use, scratching the surface of the workpiece, and may also cause uneven thickness of the strengthening layer or unstable stress distribution.
When an aerospace manufacturing company was processing titanium alloy turbine blades, it originally used glass beads for shot peening. It was found that the thickness of the strengthening layer was uneven at the end of the blade, resulting in a decrease in the fatigue life of the blade. After switching to ceramic shot peening, the stability of the strengthening layer thickness increased by 15%, and the fatigue life of the blade increased by 20%.
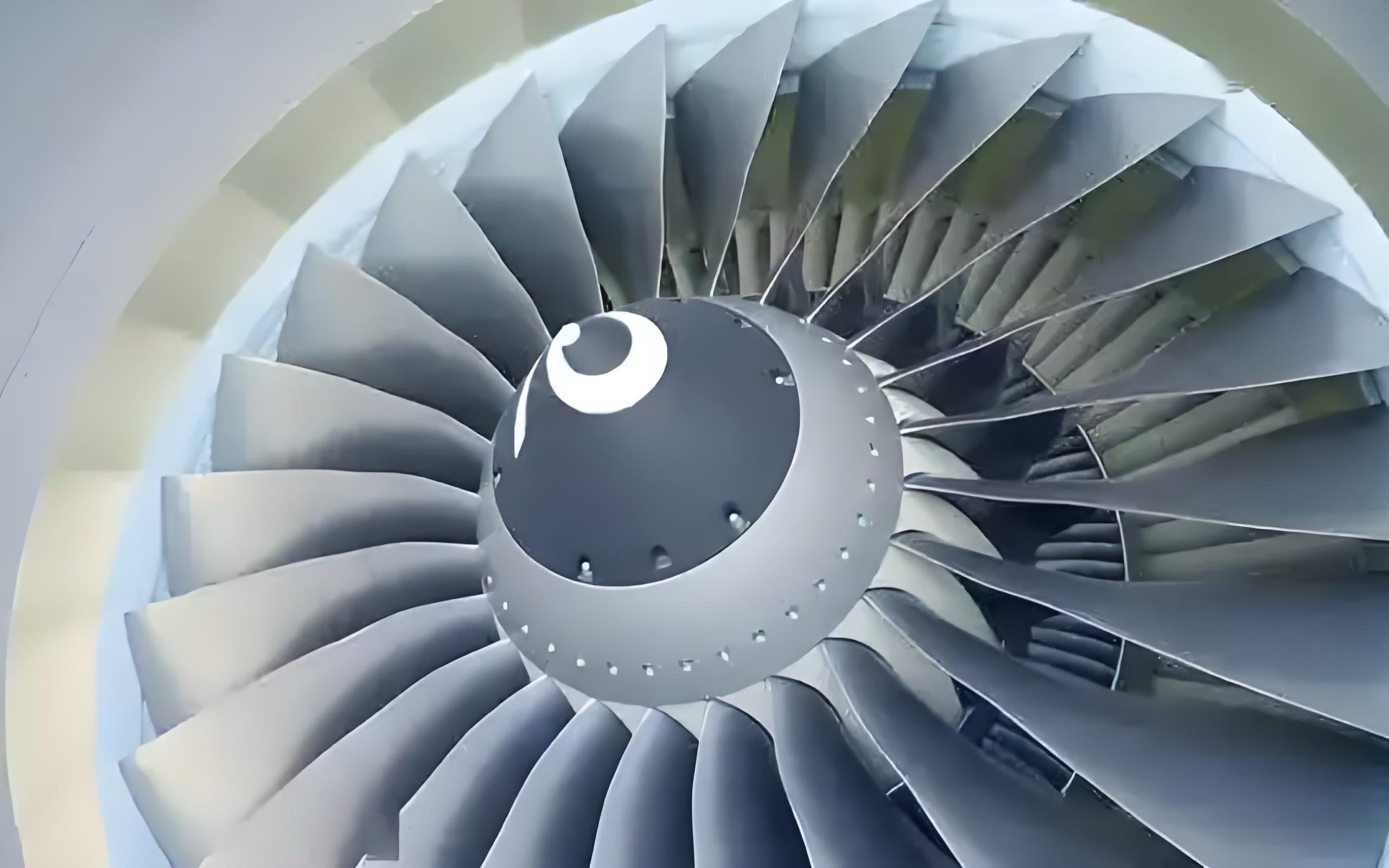
Material compatibility
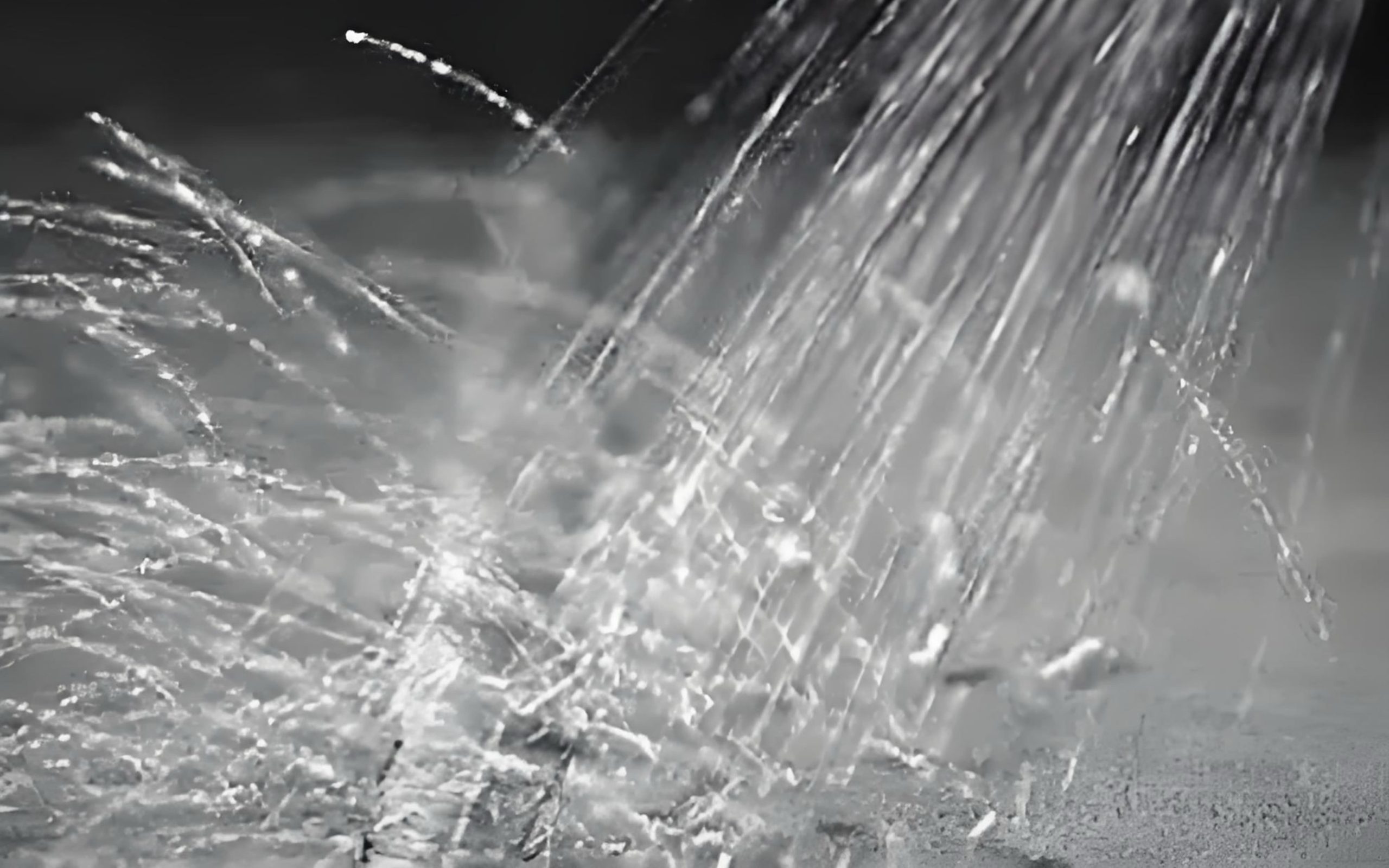
Glass beads are easy to break when strengthening high-strength materials, and may not generate sufficient surface compressive stress on flexible materials. However, ceramic shot peening is suitable for shot peening processes from flexible materials (such as aluminum alloys) to high-strength materials (such as stainless steel and titanium alloys) and has a large scheduling space.
Although ceramic shot peening has a high hardness, it can also handle soft materials well. This mainly depends on its particle size, shape, and the applied injection pressure.
As long as the appropriate particle size is selected and low-pressure injection is used, the intensity of the impact force concentration point can be reduced. In addition, the spherical design of ceramic shot peening also helps to disperse the impact force, which is similar to glass beads and can achieve a gentler surface treatment effect.
In the shot peening of aluminum suspension system parts, an automobile manufacturer failed to meet the depth of the compressive stress layer due to insufficient hardness of glass beads. After switching to ceramic shot peening, the depth of the surface compressive stress layer increased by 30%, and no scratches or pits appeared on the surface of the aluminum parts.
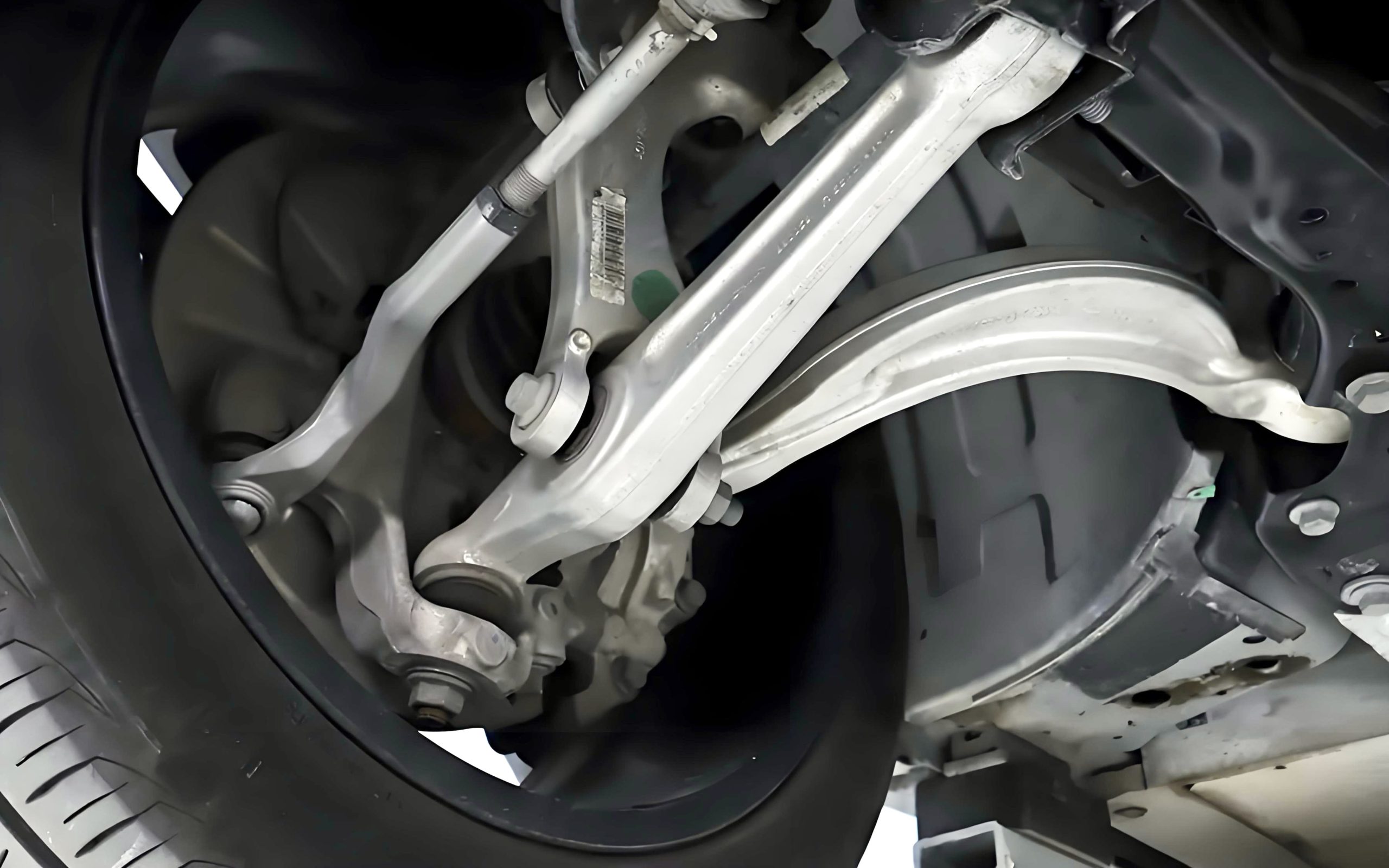
Efficiency and economy of use
First, ceramic shot peening has higher hardness and can apply greater surface compressive stress during shot peening, effectively improving the fatigue resistance and durability of the workpiece. Secondly, the density and durability of ceramic media are much higher than glass beads.
Although the initial purchase cost of ceramic shot peening is higher than that of glass beads, after multiple cycles of use, ceramic shot peening can still maintain a spherical shape and can be used repeatedly, while glass beads have a high breakage rate and need to be replaced frequently, increasing downtime and media procurement costs.
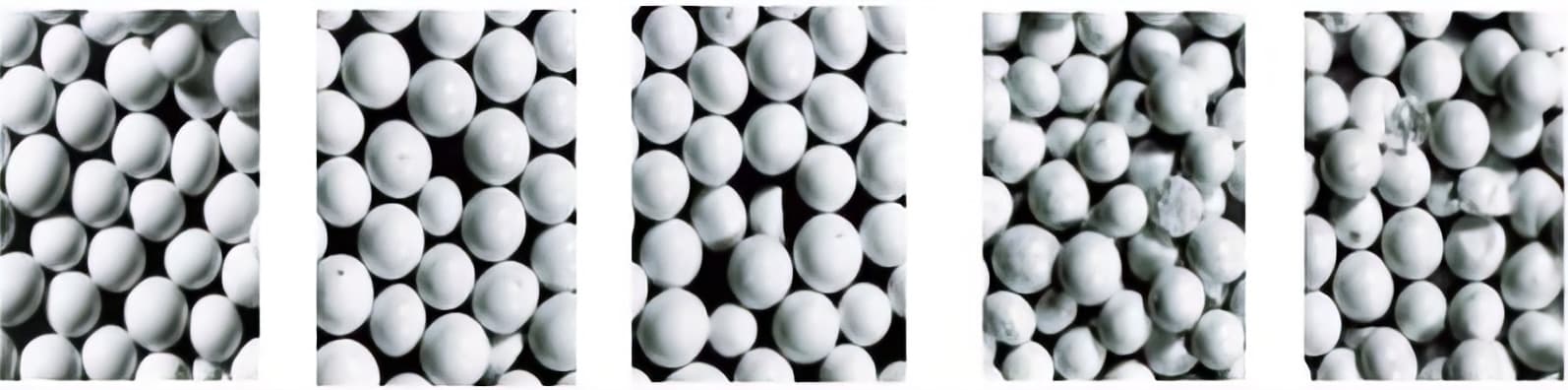
The ceramic media will wear but will not break into powder, so there is almost no dust, and the unbroken parts still maintain their original size, shape, hardness and smooth surface.
An automotive parts manufacturer switched to shot peening with ceramic shot peening when producing crankshafts. Although the procurement cost increased by about 30%, the number of times per kilogram of ceramic shot peening was used was 3-4 times that of glass beads, and the waste disposal cost decreased by 40%. Overall, the production cost decreased by 15% and the processing efficiency increased by 10%.
Specific application requirements
It is known that the fragility of glass beads will cause non-uniformity in shot peening, which will form weaknesses in the propagation of corrosion cracks, especially in harsh environments such as marine engineering and the nuclear energy industry.
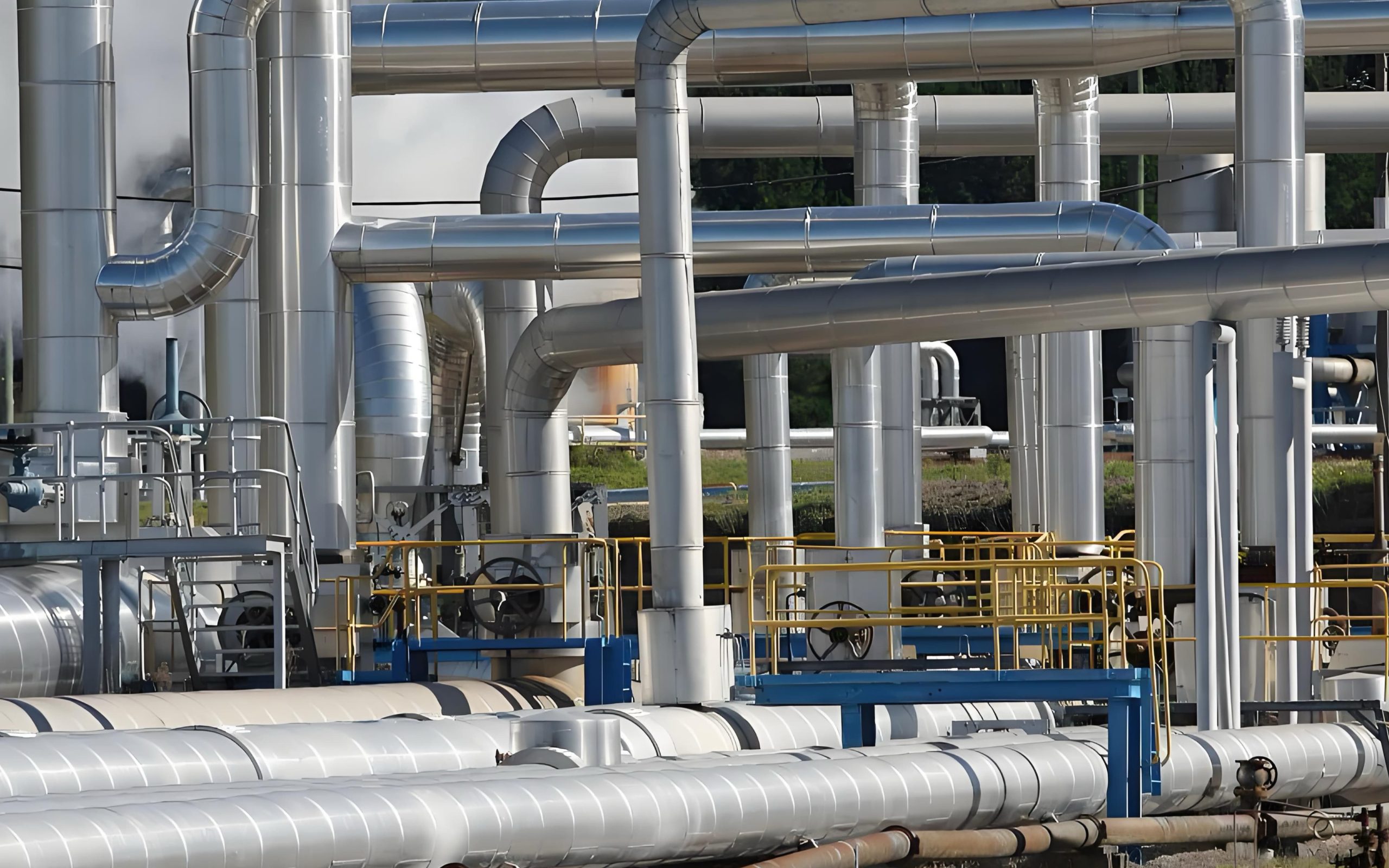
Broken fragments may also be embedded in the surface and become a potential source of corrosion. Ceramic media has a regular shape and is tenacious and strong. After shot peening, it can generate a uniform compressive stress layer, effectively preventing the expansion of corrosion cracks, and is more suitable for areas with high requirements for anti-corrosion performance.
A nuclear power plant maintenance project requires the shot peening of high-pressure steam pipes to extend their life. After using glass beads, the strengthening effect did not meet the standard, and the fatigue life of the pipes did not increase significantly. After replacing ceramic shot peening, the fatigue life of the strengthened pipes increased by 25%, and the crack propagation rate was significantly reduced.
Efficiency and economy of use
Ceramic shot peening does not easily generate dust during use, and the operating environment is cleaner, which helps reduce health risks for workers. Glass beads are easy to break, which may produce a large amount of tiny glass dust, affecting air quality and increasing environmental protection treatment costs.
In addition, the recyclability of ceramic media is much higher than that of glass beads, usually reaching more than 95%, and the amount of waste generated is also less, which is more easily accepted by environmental protection regulations.
After replacing glass beads, a spraying equipment supplier reduced industrial solid waste by about 20 tons per year, significantly reducing disposal costs. At the same time, the high availability of ceramic shot peening gives it extra points in green production certification, providing support for enterprises to open up the European and American markets.
Technical and operational thresholds
From the perspective of equipment compatibility, ceramic shot peening is highly compatible with modern shot peening equipment. Its regular shape and stable physical properties reduce the need for equipment adjustment, while glass beads are mainly easy to break, which increases the risk of clogging the nozzle and wearing the equipment.
Ceramic shot peening is also more tolerant of process parameters, such as more uniform injection pressure and particle size distribution, reducing the complexity of operating technology. At the same time, it can work under a wider range of temperature and humidity conditions, reducing the need for environmental control.
Due to its high hardness and regular shape, it can efficiently process emerging materials such as titanium alloys and composite materials, meeting the needs of the aerospace and medical industries for special surface strengthening.
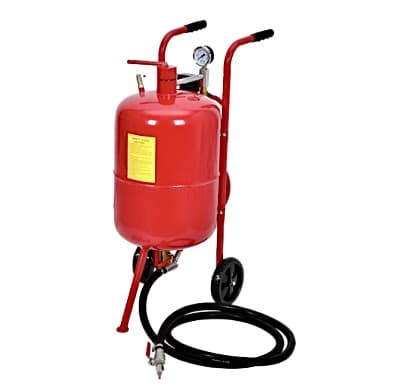
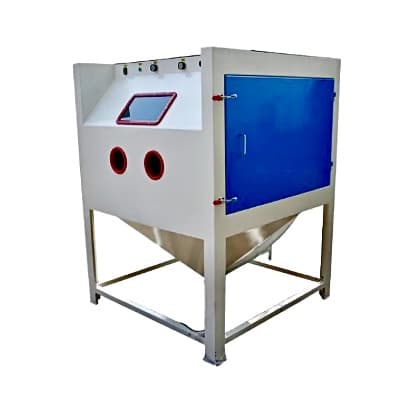
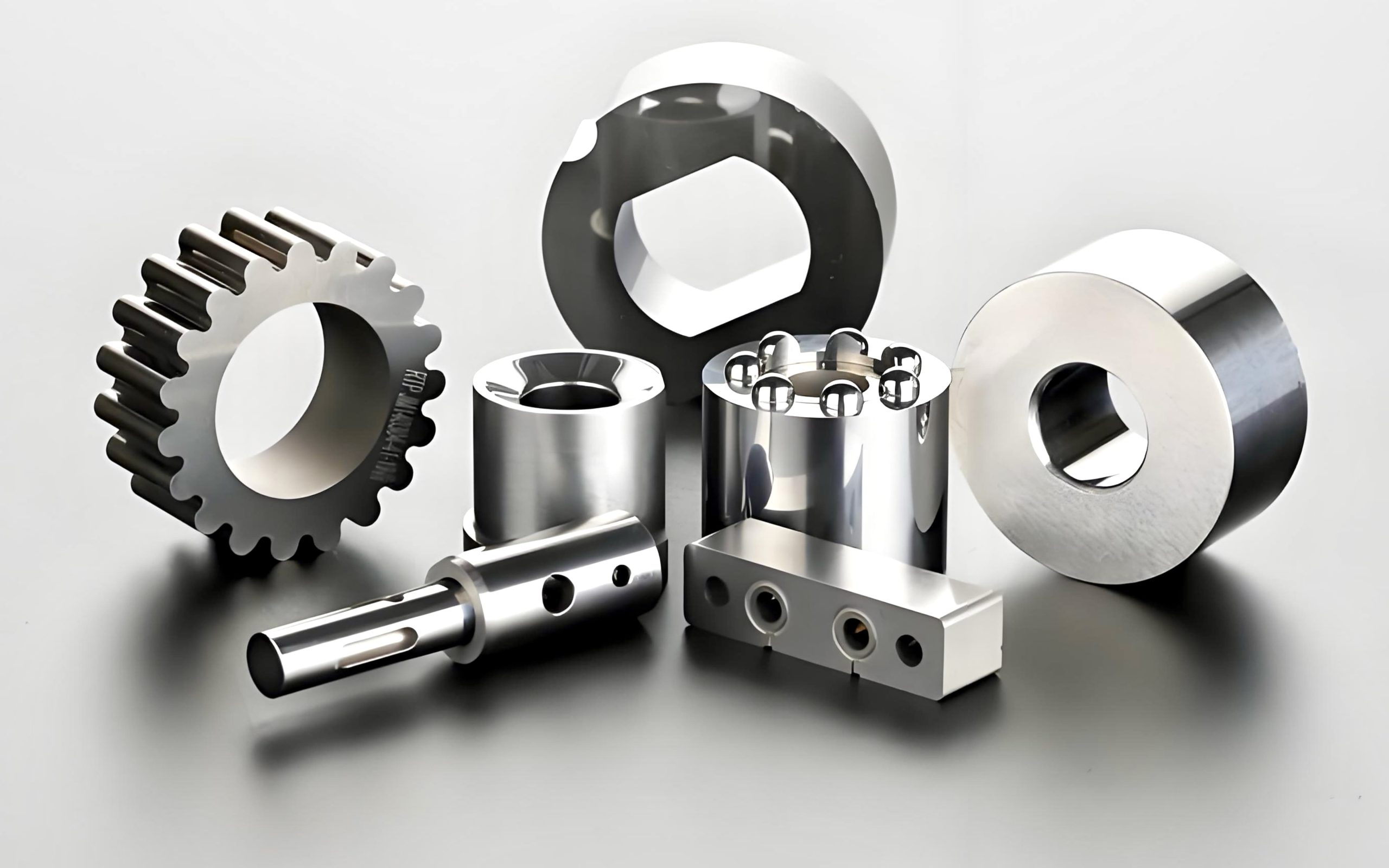
A precision mold manufacturing company found that frequent replacement of glass beads in the shot peening process led to increased equipment downtime. After replacing ceramic shot peening, the equipment operation time was extended by 25%, and the stability of the process was greatly improved.
In summary, we compared the performance of the two in terms of hardness and strengthening depth, life and efficiency, and environmental performance. It can be found that ceramic media has obvious advantages in these key dimensions. It is precisely with these advantages that ceramic shot peening is gradually replacing glass beads as a choice of high-performance shot peening media, bringing higher economic benefits and more sustainable production solutions to various industries.
Filters