Surface finishing process | Comprehensive overview
November 7, 2024
Surface finishing is an indispensable process in many industries. Its main purpose is to improve the surface quality of materials or products, including their appearance, function, and durability. Whether in the automotive, aviation, architectural decoration, or consumer electronics industries, through fine processing, surface finishing can provide better solutions for various application scenarios and greatly enhance the value of products.
Types of Surface Finishing Processes
Surface finishing covers various processes, each with its unique characteristics, advantages, disadvantages, and applicable scenarios. Common finishing processes include mechanical polishing, electroplating, sandblasting, chemical treatment, and heat treatment. The following is a brief analysis of several major finishing processes:
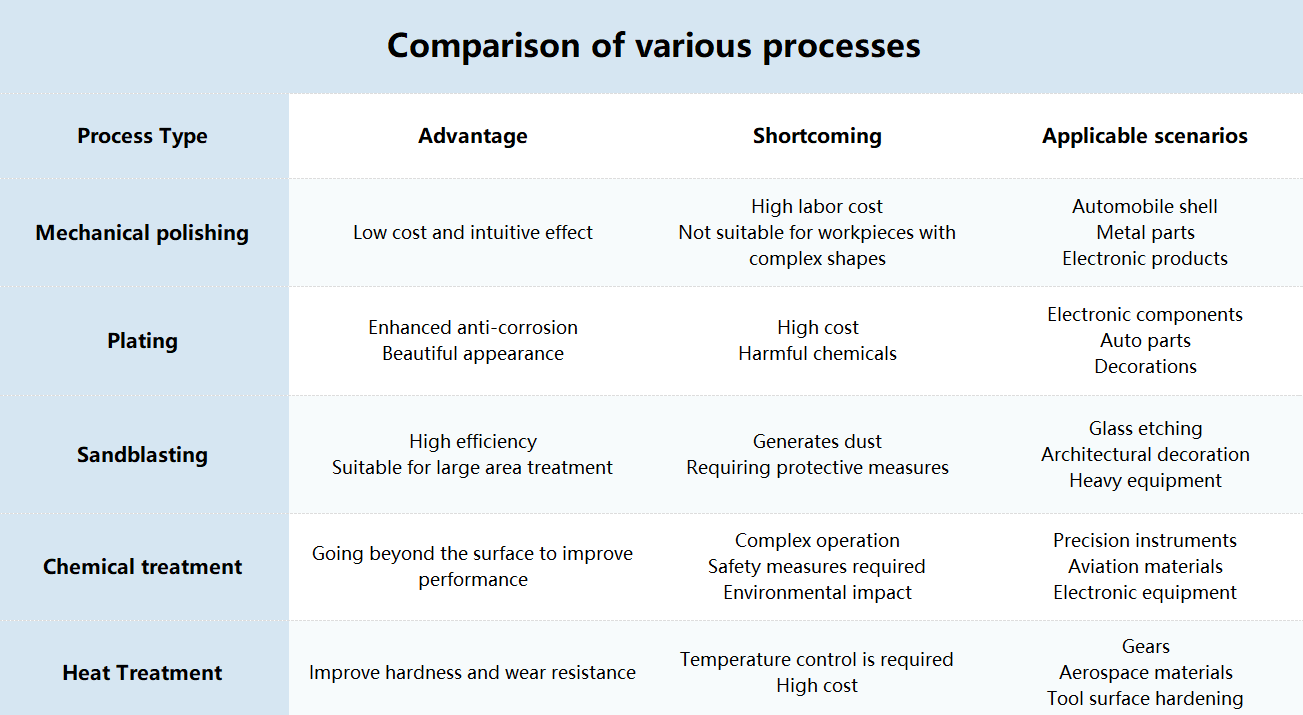
- Mechanical polishing
- Definition: Physical friction of the material surface through abrasives, sandpaper, etc. to achieve a smooth surface effect.
- Advantages: Low cost and intuitive effect; suitable for various materials, including metal, plastic, and glass.
- Disadvantages: High labor cost, not suitable for a large area or complex shape workpieces.
- Applicable scenarios: Polishing of automobile shells, modification of metal parts, and appearance finishing of electronic products.
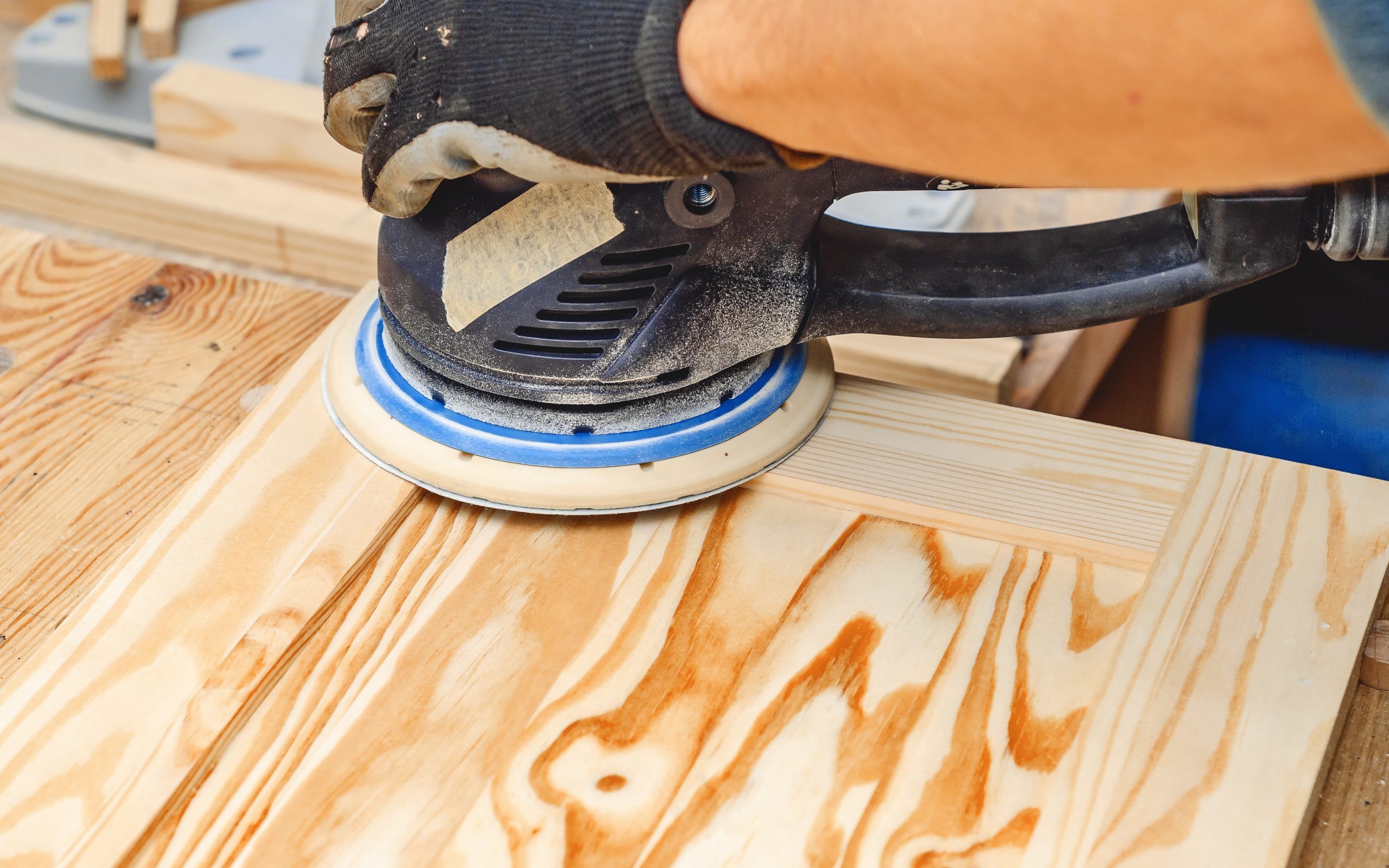
Mechanical polishing
- Electroplating
- Definition: Depositing a metal film on the surface of a material through an electrolytic reaction to enhance the corrosion resistance and aesthetics of the material.
- Advantages: Can significantly improve the corrosion resistance and aesthetics of metals; Applicable to different metal surfaces.
- Disadvantages: High cost, the treatment process involves harmful chemicals, and requires professional operation.
- Applicable scenarios: Anti-corrosion treatment of electronic components, surface modification of automotive parts, and processing of high-end decorative items.
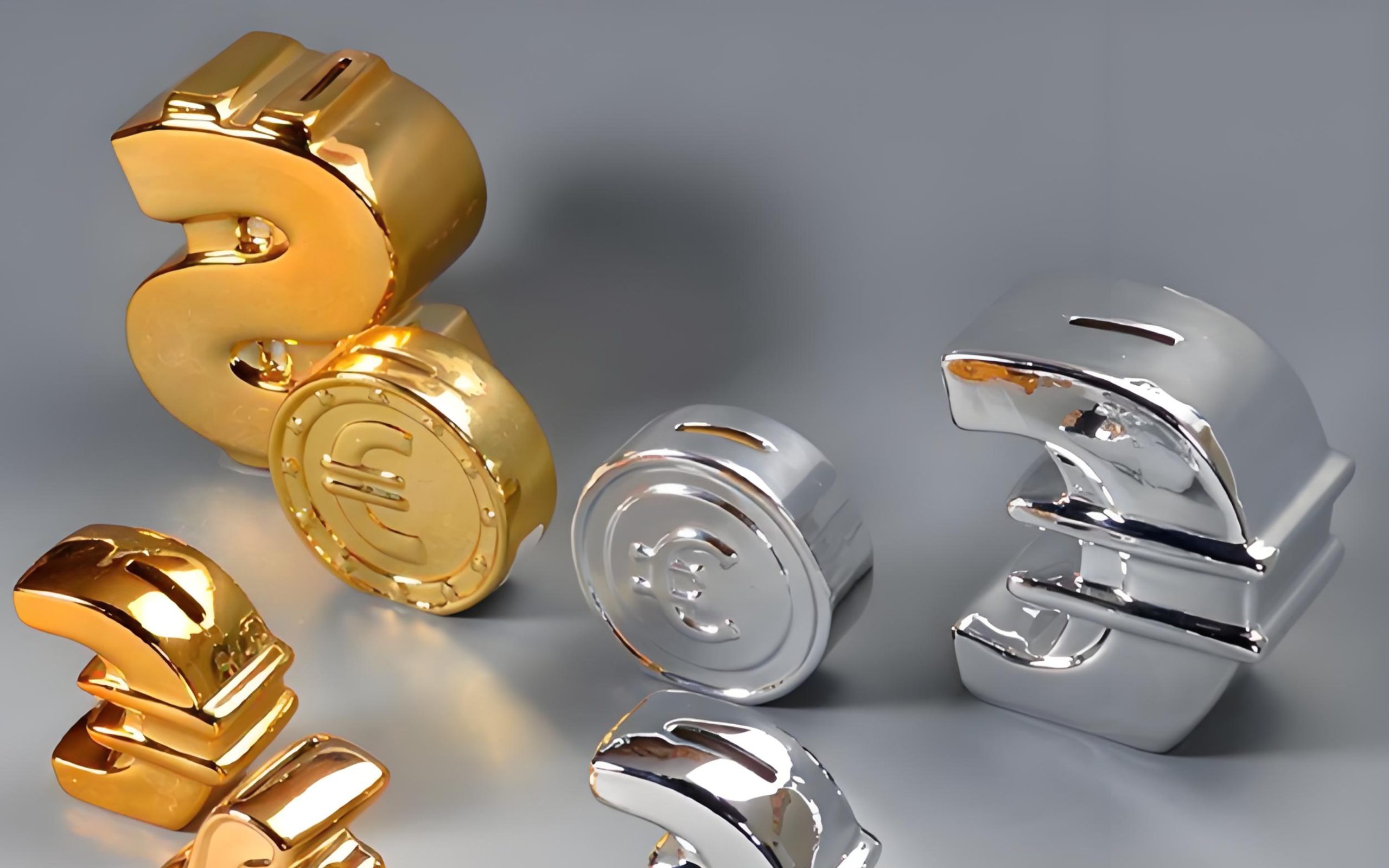
Electroplated products
- Sandblasting
- Definition: Grinding the surface of a material by high-speed jetting of abrasives to remove oxide layers or dirt, or to form a uniform surface texture.
- Advantages: Efficient and fast, suitable for a variety of materials, and ideal for large-area treatment.
- Disadvantages: Some materials will generate dust, and protective measures need to be taken. It is suitable for operation in a closed environment.
- Applicable scenarios: Glass etching, building decoration material processing, and surface cleaning of heavy industrial equipment.
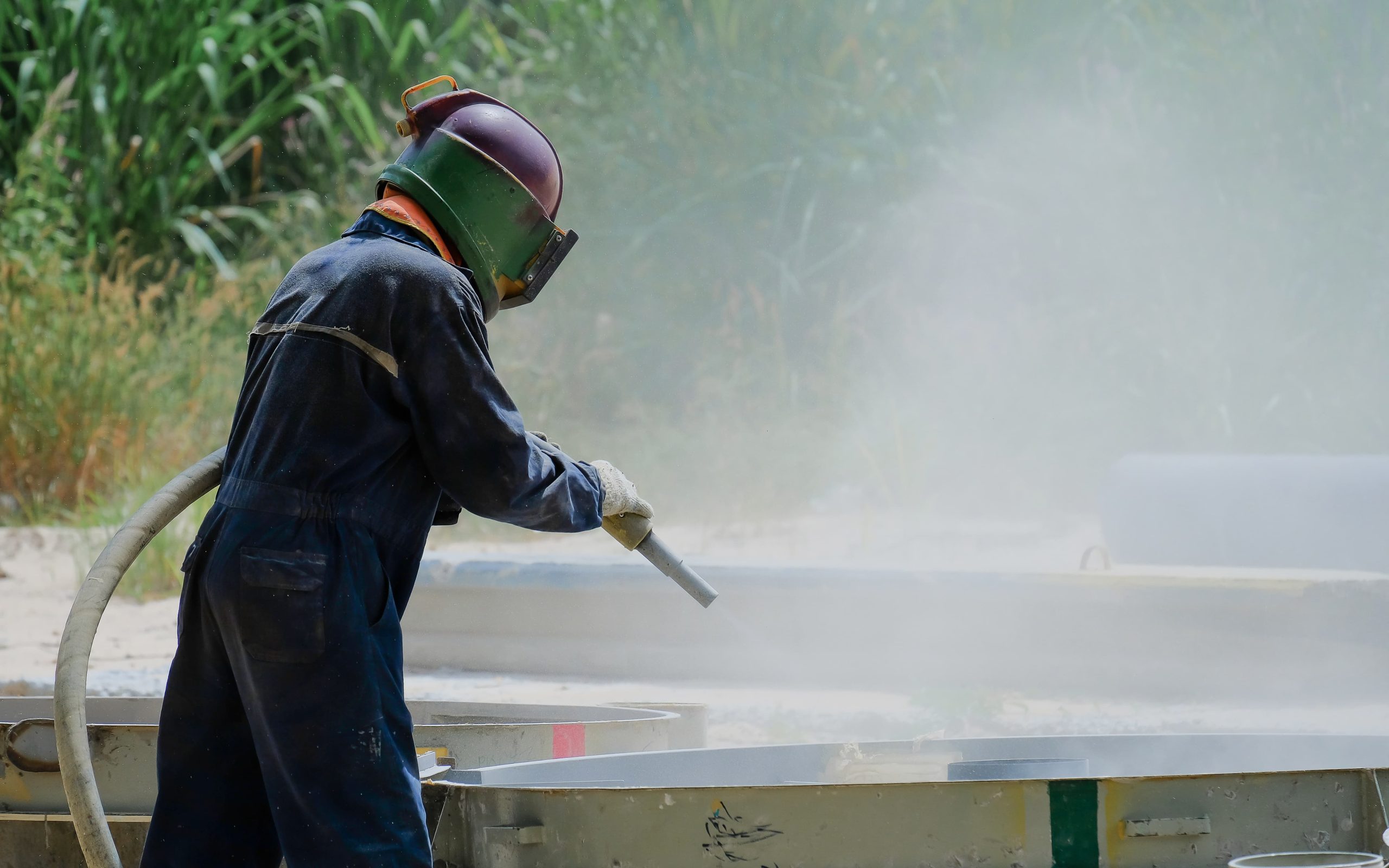
Sandblasting Demonstration
- Chemical treatment
- Definition: Removing oxides or impurities on the surface of the material through chemical reactions, or forming a protective film on the surface.
- Advantages: Able to penetrate the surface of the material and improve surface performance; Suitable for workpieces with complex shapes.
- Disadvantages: The operation requires chemical knowledge and strict safety measures, and improper handling may have an impact on the environment.
- Applicable scenarios: Surface finishing of precision instrument parts, anti-corrosion treatment of aerospace materials, and surface treatment of electronic equipment.
- Heat treatment
- Definition: Change the physical properties of the surface or the whole of the material, such as hardness and toughness, through thermal cycle processes such as heating and cooling.
- Advantages: Improve the surface hardness of the material, and enhance wear resistance and impact resistance.
- Disadvantages: The temperature and cooling rate needs to be controlled, and the cost is relatively high; it is mainly applicable to metals.
- Applicable scenarios: Strengthening treatment of mechanical parts such as gears, structural strengthening of aviation materials, and surface hardening treatment of tools.
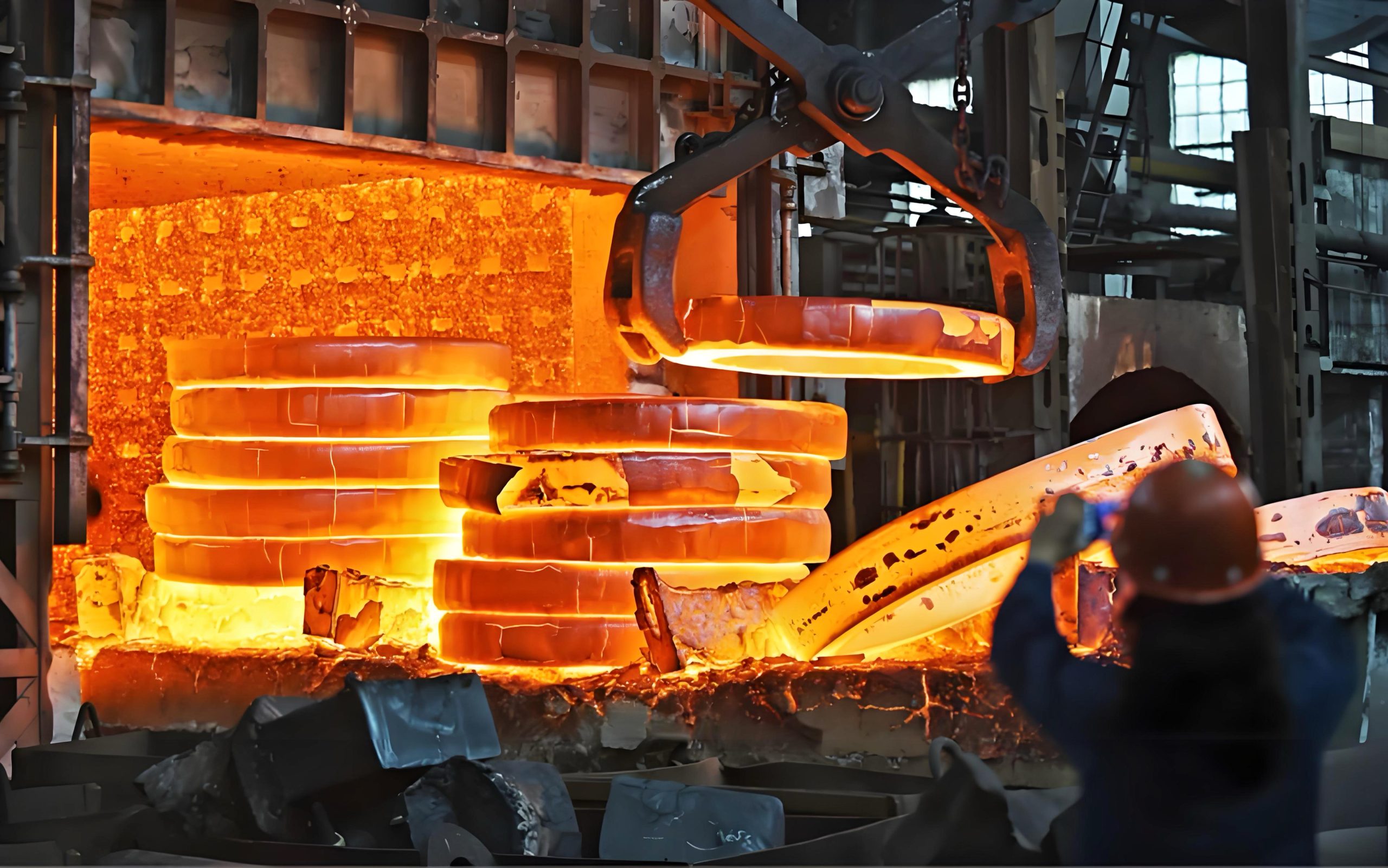
Heat treatment
Factors affecting surface finishing effects
The quality and effect of surface finishing are affected by many factors, from material selection to process execution details, which will have a significant impact on the final result. The following discusses these influencing factors in detail from four aspects: materials, processes, environmental conditions, and precision requirements.
- Material properties
Different materials show different reactions when surface finishing. Metals, ceramics, glass, and plastics have different hardness, thermal conductivity, and chemical properties, and need to choose an appropriate process.
- Hardness and wear resistance: For example, hard metals require stronger grinding materials, while soft metals are susceptible to over-grinding and uneven surfaces.
- Thermal conductivity: During heat treatment, the thermal conductivity of the material determines the cooling rate, which in turn affects the surface finish.
- Chemical reactivity: For reactive metals, chemical etching requires the use of special preservatives and process parameters to avoid excessive corrosion.
- Process parameters
The parameter settings of the finishing process directly affect the accuracy and effect of the surface treatment. Common influencing factors include grinding speed, pressure, and process duration.
- Grinding speed: During polishing or sandblasting, too high a speed will result in a rough surface, while too low a speed will affect efficiency.
- Applying pressure: For example, during sandblasting, too high a pressure may cause material damage, while too low a pressure may result in incomplete treatment.
- Process time: Extending the grinding or etching time usually improves the finish, but it may also cause material loss, so the time needs to be strictly controlled.
- Environmental conditions
Surface finishing has strict requirements on environmental conditions, and environmental factors such as temperature and humidity will affect the processing effect.
- Temperature: Heat treatment and chemical treatment processes are very sensitive to temperature. Too high or too low a temperature may cause surface defects.
- Humidity: A high humidity environment will accelerate oxidation reaction, which is not conducive to the smooth treatment of metal surfaces. Especially in chemical etching, special attention should be paid to moisture prevention.
- Cleanliness: Dust and impurities in the air may adhere to the surface of the workpiece, resulting in a poor treatment effect. Therefore, the cleanliness of the environment must be ensured during the finishing process.
- Accuracy and tolerance requirements
Different application scenarios have different requirements for surface accuracy and tolerance. In finishing, process parameters need to be adjusted according to specific uses.
- Finish requirements: For precision parts, such as aerospace parts or medical devices, the surface finish requirements are extremely high, and even a slight difference in roughness may affect their functionality.
- Tolerance control: Controlling tolerances during processing is the key to ensuring the accuracy of part assembly. Even in the same batch, each part may require specific process adjustments to meet strict tolerance requirements.
Application scenarios of surface finishing
Surface finishing has a wide range of applications in multiple industries, especially in automotive manufacturing, architectural decoration, aerospace, and consumer electronics. The following is an in-depth analysis of each application scenario, detailing the demand pain points, challenges faced, and solutions brought by surface finishing technology in various industries.
- Automobile Manufacturing
- Industry demand: In the automobile manufacturing industry, surface finishing is mainly used to improve the beauty and durability of the car body and parts. The car body needs a smooth appearance, while the engine, transmission, and other parts need corrosion and wear resistance.
- Common pain points: uneven surface after car body painting, performance degradation due to part wear, and corrosion of metal parts in harsh environments.
- Finishing process: Mechanical polishing and sandblasting are usually used to make the surface more shiny. Electroplating and heat treatment technologies are used to improve the corrosion resistance and hardness of parts.
- Typical case: Some high-end car brands use a combination of multi-layer sandblasting and polishing to ensure that the car body can present a uniform gloss effect under different light conditions and enhance visual impact.
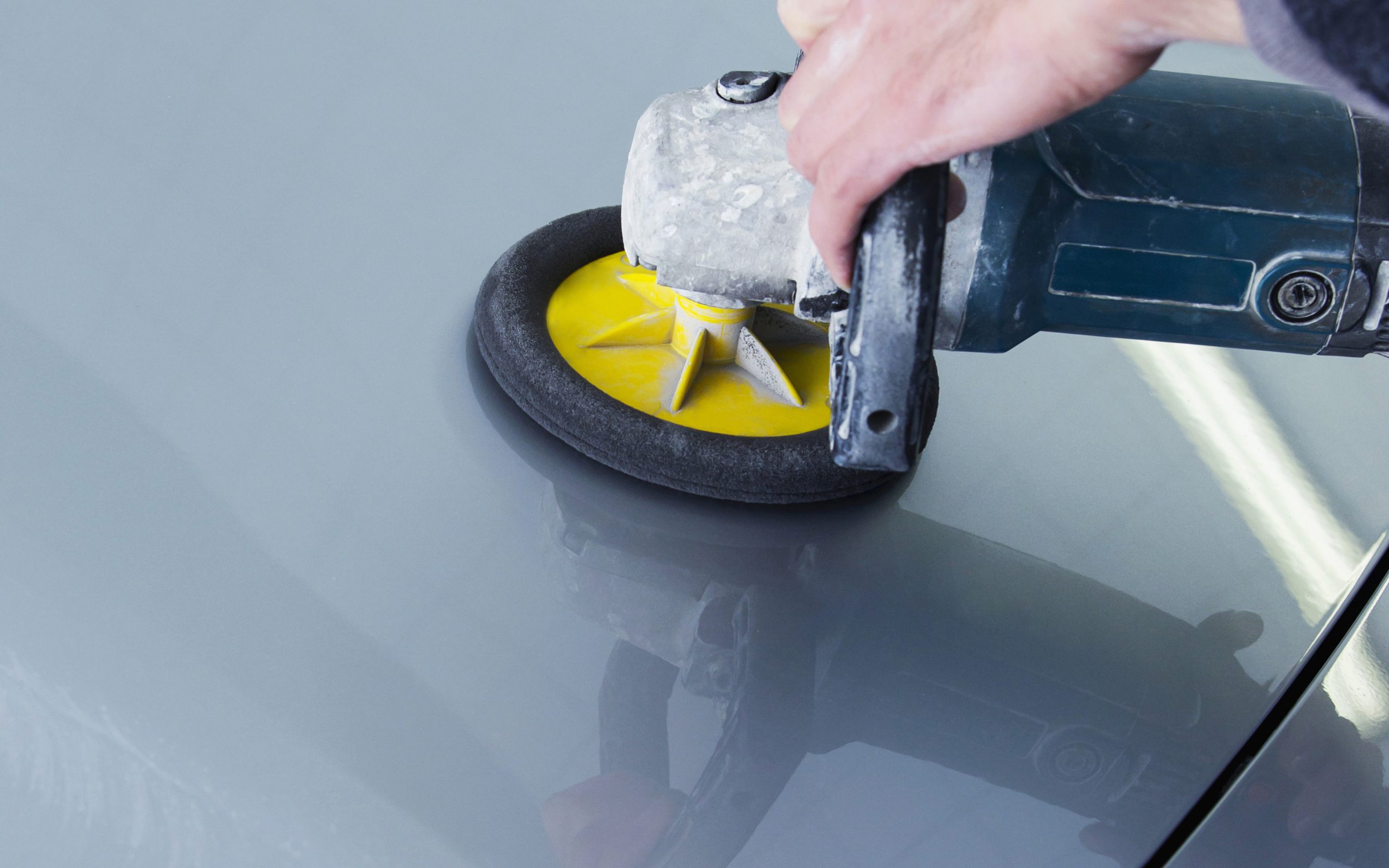
Cars being mechanically polished
- Building decoration
- Industry demand: The building decoration industry widely uses finishing technology on the surfaces of metal, glass, marble, and other materials to enhance the decorativeness and durability of the structure.
- Common pain points: Exterior wall materials are prone to corrosion under long-term sun and rain, the wind pressure resistance of glass materials in high-rise buildings needs to be improved, and interior decoration materials need to be stain-resistant.
- Finishing process: Sandblasting and chemical treatment technologies are widely used on the surface of building decoration materials to increase texture or enhance weather resistance. Mechanical polishing can be used for the surface treatment of decorative stones such as marble to give smoothness and aesthetic effects.
- Typical case: Many modern buildings use sandblasting and etching processes on the decoration of metal exterior walls to create a unique texture effect, making the building visually more layered.
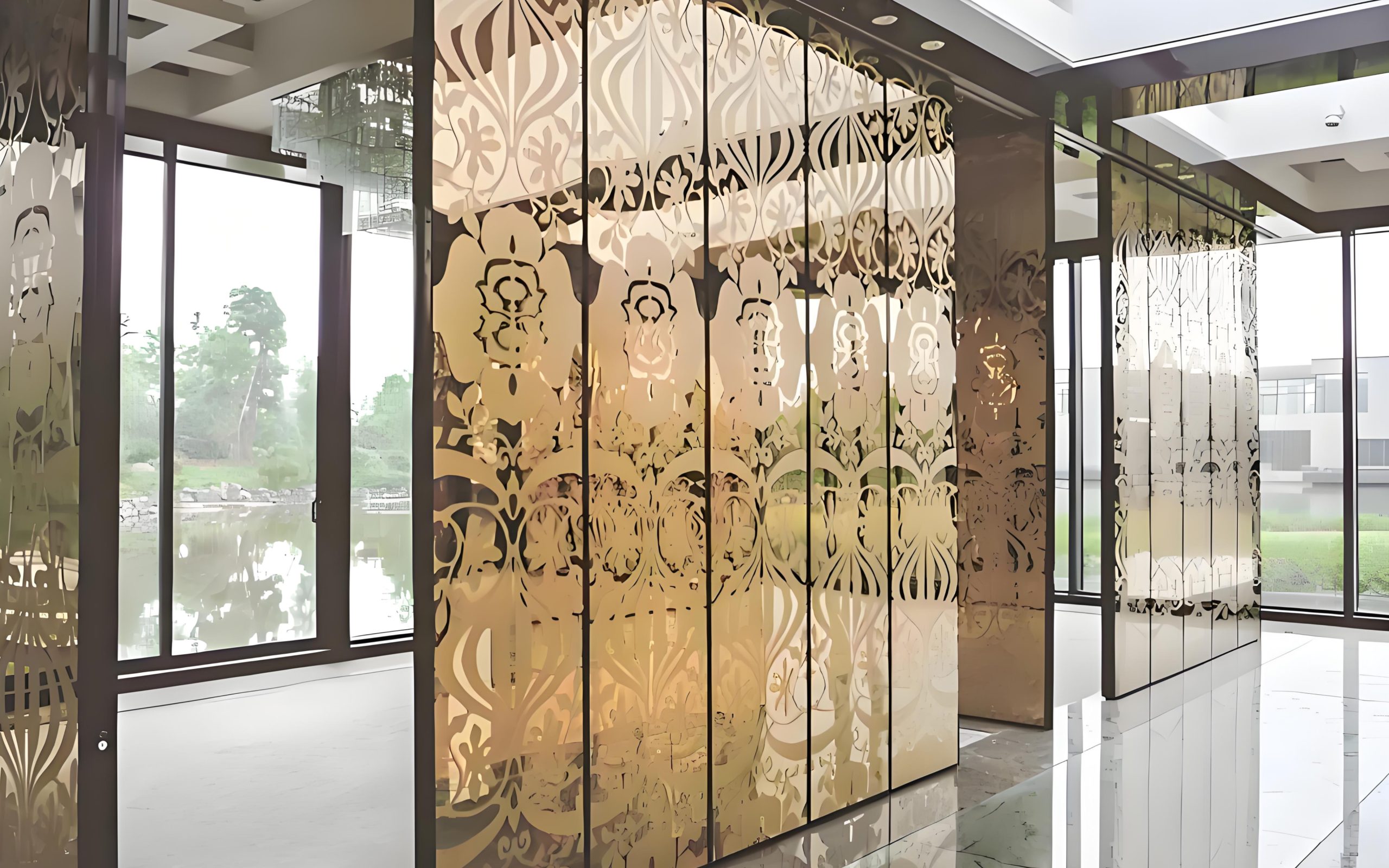
Etched glass partition
- Aerospace
- Industry demand: Materials in the aerospace industry require extremely high corrosion resistance and wear resistance, and surface finishing is used to extend component life and reduce maintenance costs.
- Common pain points: Aircraft shells are prone to oxidation and corrosion under extreme conditions at high altitudes, engine components are prone to wear at high temperatures, and the body metal needs to withstand strong winds and pressure.
- Finishing process: Heat treatment and chemical treatment are the main surface finishing methods, which can improve the hardness and high-temperature resistance of materials. In addition, sandblasting can remove surface impurities and improve corrosion resistance.
- Typical case: Boeing uses a special chemical nickel plating process to surface treat aircraft engine parts, which improves corrosion resistance and extends the service life of the parts.
- Consumer electronics
- Industry demand: The appearance and feel of consumer electronic products have a significant impact on user experience, so finishing processes are widely used in electronic housings, buttons, and internal parts.
- Common pain points: The housing is easy to scratch, the parts are easy to corrode after being damp, and the gloss of the plastic housing is uneven.
- Finishing process: Mechanical polishing can give the metal housing a glossy feel, sandblasting is used to enhance the touch and wear resistance of plastic or metal housings, and chemical treatment is used to enhance the UV resistance of plastics.
- Typical case: Apple’s product housing uses multiple surface finishing technologies such as anodizing and sandblasting during the production process, making its products excellent in both touch and appearance.
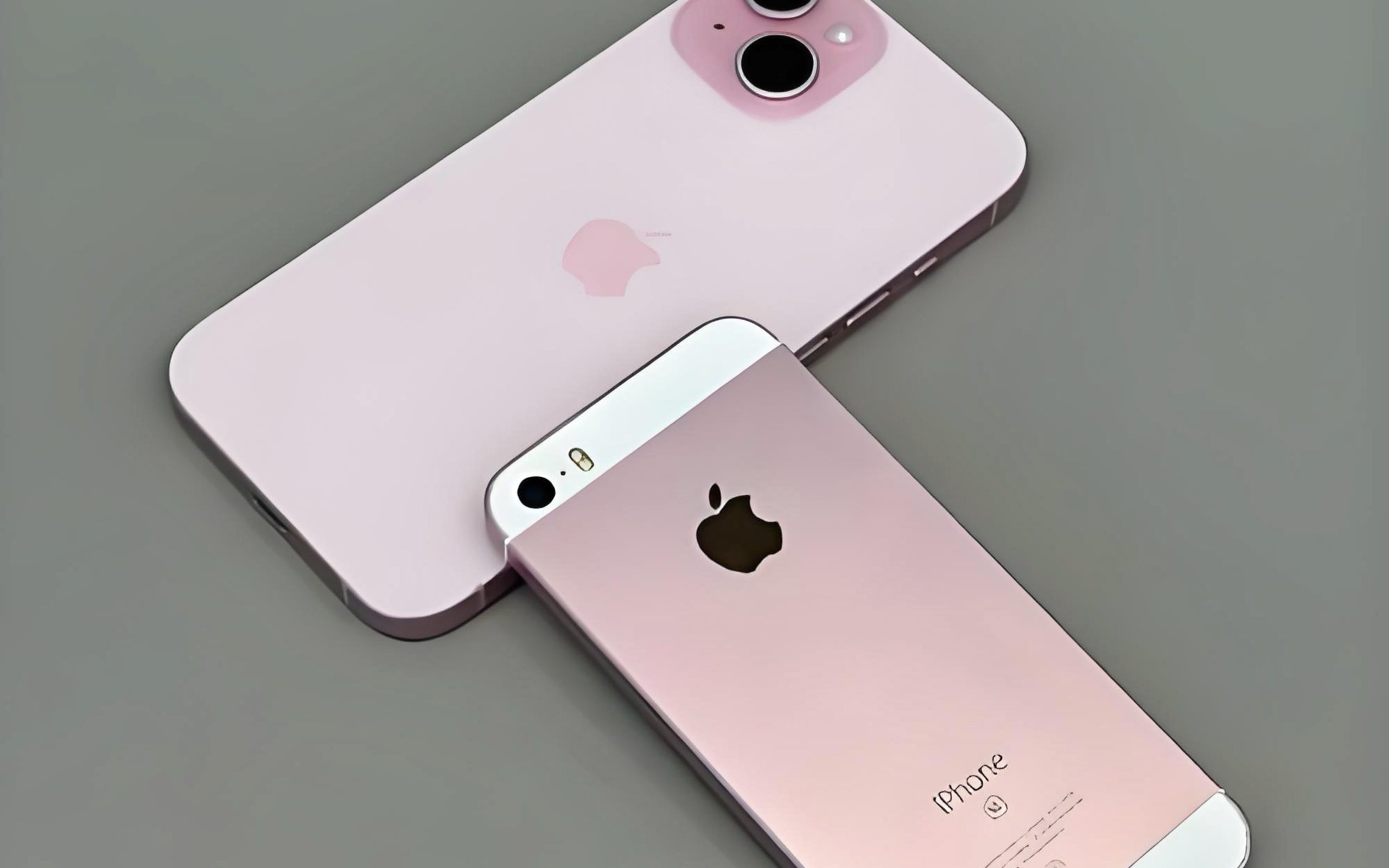
Anodizing process for mobile phone casing
Sandblasting media and equipment
In the surface finishing process, sandblasting is a widely used technology that can effectively improve the surface quality of the workpiece and meet various finish requirements. Selecting the right sandblasting media and equipment is essential to ensure efficient and high-quality surface treatment. The following introduces several commonly used sandblasting media and their application scenarios and recommends suitable sandblasting equipment.
Recommended sandblasting media
- Glass beads
Due to their smooth particle shape, glass beads cause fewer scratches on the surface during processing, and can produce a uniform matte effect, which significantly improves the surface finish.
Suitable for fine polishing and surface cleaning of metals and glass, usually used for decorative workpieces that require a higher finish.
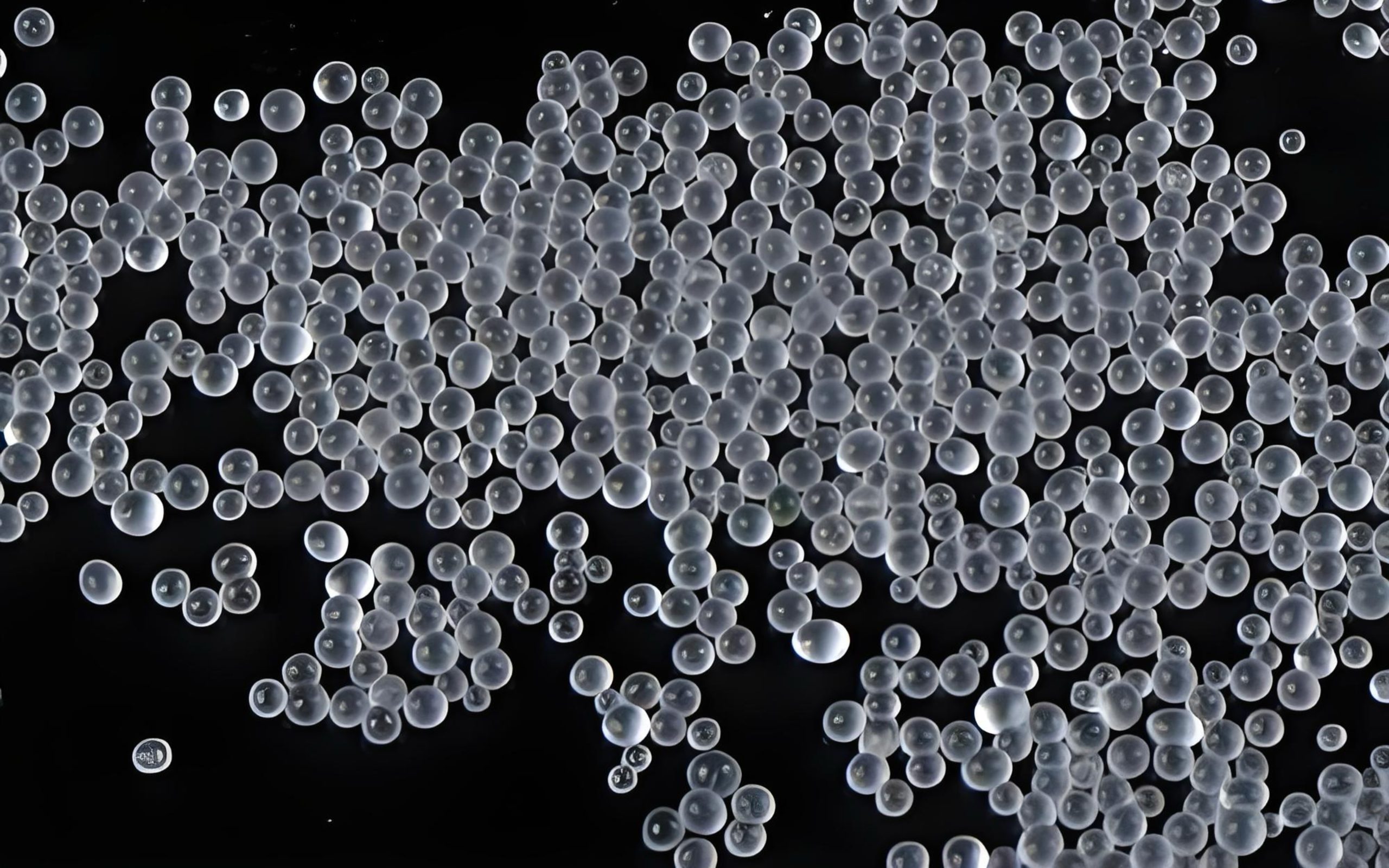
Glass beads
- Alumina
Alumina has high hardness and cutting force, can quickly remove surface defects, and produces good roughness, especially suitable for subsequent coating or bonding processes.
Suitable for surface roughening of high-hardness metals, ceramics, and stones, especially on workpieces that need to remove oxide layers and heavy dirt.
Alumina blasting media
- Silicon carbide
Silicon carbide has extremely high hardness and strong cutting force. It can effectively remove dirt and defects on the surface of hard materials and is often used for pretreatment before coating.
Mainly used for deep decontamination and roughening of ceramics, carbon fibers, and some metals.
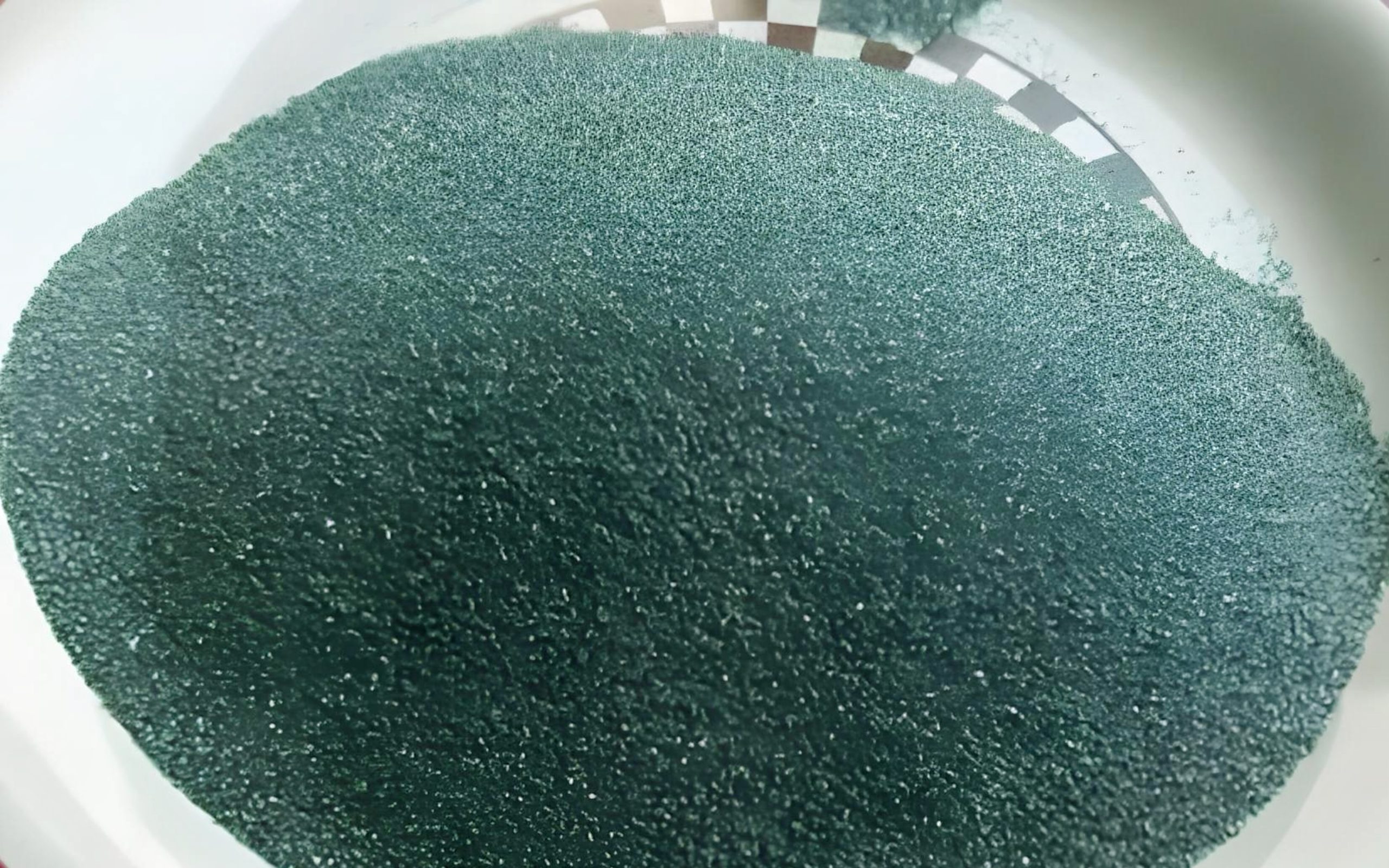
Silicon carbide
- Ceramic beads
Ceramic beads have high hardness and strong wear resistance. They are suitable for heavy-pressure sandblasting, can reduce micro scratches, and can form a uniform matte surface.
Suitable for surface treatment that requires high wear resistance and needs to maintain smoothness, commonly used in surface grinding of precision machinery and aviation parts.
- Plastic media
Due to its soft material characteristics, plastic sandblasting media hardly produces hard scratches on the surface of the workpiece and is suitable for fine surface treatment.
It is used for surface treatment of softer materials such as aluminum alloys and plastic parts, especially in scenes where surface damage is not allowed.
Recommended sandblasting equipment
- Press-in sandblasting machine
- Features: The pressure adjustable range of the press-in sandblasting machine is large, and suitable for processing materials of various hardness, especially widely used in sandblasting processes that require high precision and high efficiency.
- Applicable media: glass beads, ceramic beads, aluminum oxide, etc.
- Suction sandblasting machine
- Features: Simple operation, suitable for lightweight surface treatment needs, especially cleaning and polishing of small parts.
- Applicable media: glass beads, plastic media.
- Wet sandblasting machine
- Features: It uses a mixture of water mist and abrasives, suitable for operation in a dust-free environment, and is mainly used for workpiece processing with high precision and scratch-free surface requirements.
- Applicable media: glass beads, aluminum oxide.
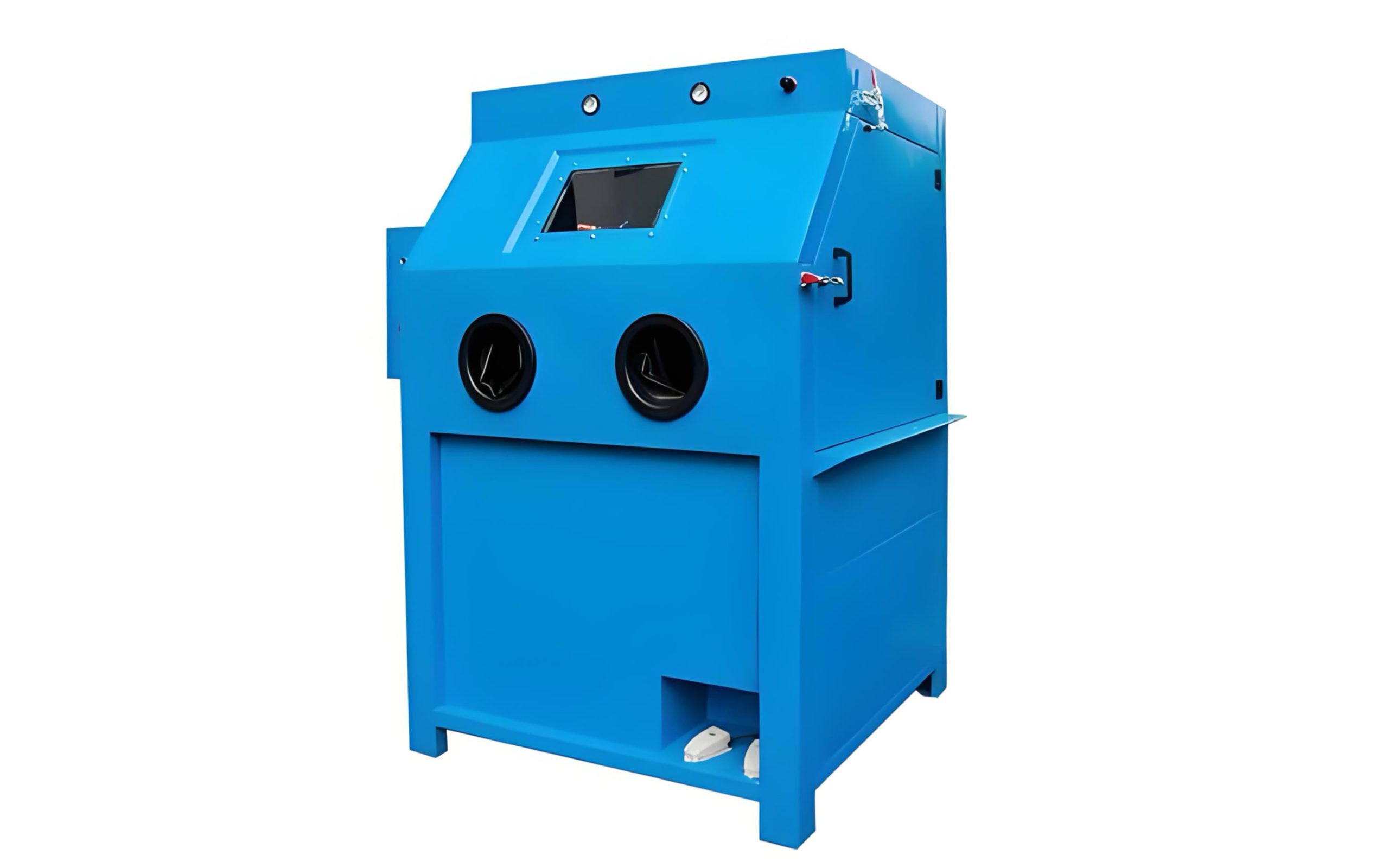
Wet sandblasting machine
- Mobile sandblasting machine
- Features: It is easy to move and operate, and suitable for large workpieces or scenes where it is difficult to operate in fixed places, such as surface treatment of large outdoor building components.
- Applicable media: aluminum oxide, silicon carbide.
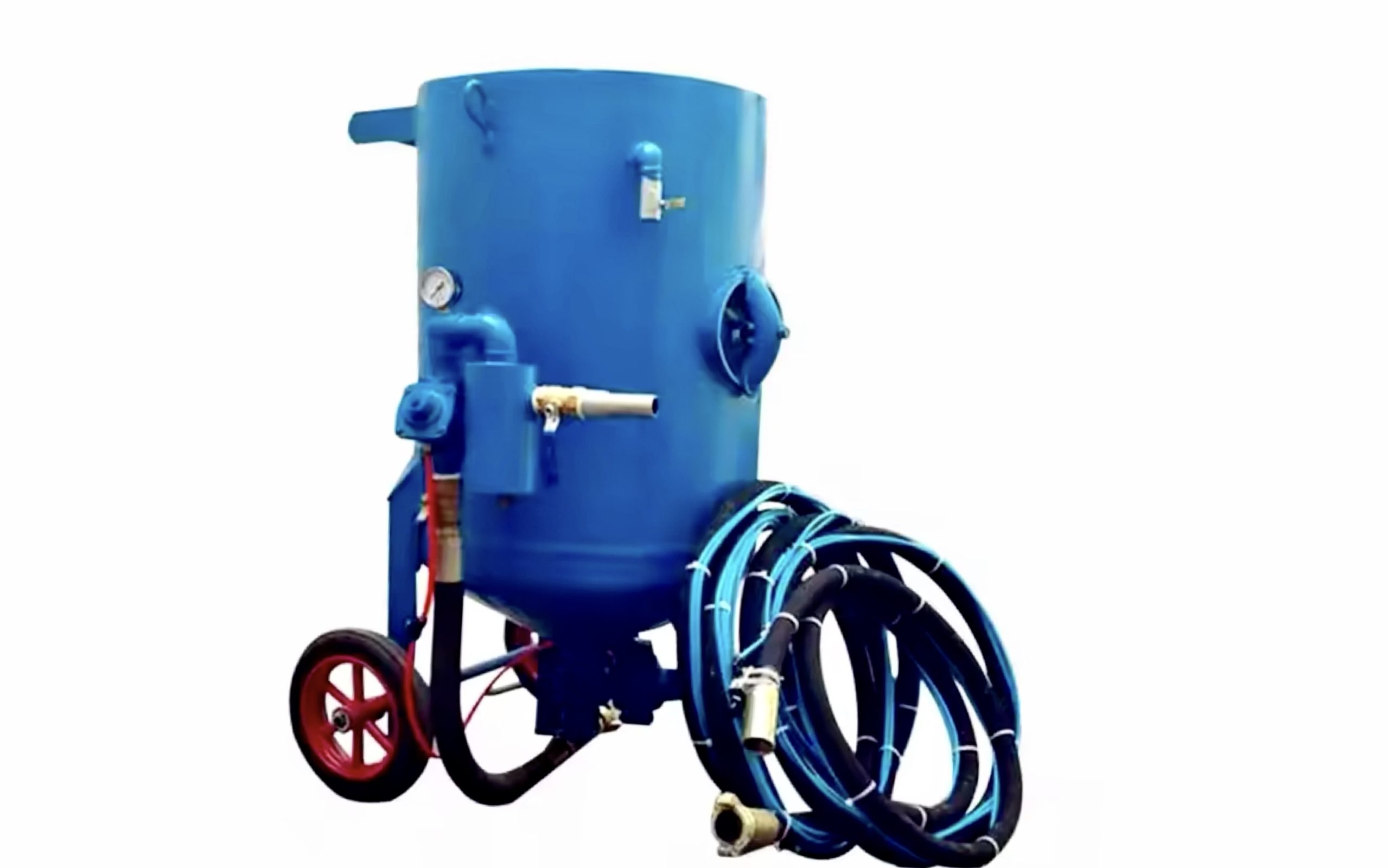
Mobile sandblasting machine
How to choose the right media and equipment
The selection of media and equipment in surface finishing requires a comprehensive evaluation based on the material of the workpiece, the required finish, and the processing target. In the case of hard materials and surface roughening, it is more appropriate to choose media with higher hardness such as aluminum oxide or silicon carbide. For workpieces with high finish and surface damage requirements, glass beads and ceramic beads sandblasting media combined with wet sandblasting machines can provide more ideal surface effects.
Common questions and solutions (Q&A)
Q: Which surface finishing processes are more environmentally friendly and safer?
A: Wet sandblasting, laser marking, and electrolytic polishing are relatively environmentally friendly. Wet sandblasting reduces dust through water mist, laser marking does not require chemical media, and electrolytic polishing does not involve the use of harmful substances. When choosing these processes, environmental pollution and operational risks can be minimized.
Q: How to choose a surface finishing method suitable for my workpiece?
A: Factors such as workpiece material, target surface effect, and economy need to be considered. For workpieces with high requirements for finish, polishing or electrolytic polishing can be selected; for workpieces with special requirements for surface roughness, sandblasting and laser etching may be more suitable.
Q: How to reduce the problem of metal surface oxidation?
A: Treat the metal with an anti-oxidation coating, select a suitable polishing process, and use anti-rust oil. Electrolytic polishing can effectively remove the oxide layer and form a smooth surface to reduce the occurrence of oxidation.
Q: What are the safety precautions in chemical treatment?
A: Operators should wear appropriate protective clothing, gloves, glasses, etc., and operate in a well-ventilated environment. For processes such as pickling, strictly follow the chemical use specifications and ensure that there are adequate emergency measures to deal with possible chemical leaks or human contact.
Q: How to avoid uneven effects during surface treatment?
A: The uniformity of surface treatment is affected by multiple factors, including process parameters, operator skills, and equipment stability. Choosing appropriate equipment and process parameters and regularly maintaining the equipment can effectively avoid uneven surface effects.
Q: What is the difference between sandblasting, polishing, and chemical treatment?
A: Sandblasting is suitable for removing surface oxides or treating rough surfaces, while polishing is used to improve surface finish. Chemical treatment (such as pickling) is mainly used to remove contaminants and oxide layers on the metal surface. The choice of each process should be determined based on the requirements and process characteristics of the workpiece.
Q: How to treat the surface of the workpiece after surface finishing?
A: The treated workpiece usually needs further protection. For metal surfaces, a protective layer (such as rust-proof oil) can be applied, while materials such as glass and plastic may need to be heated or polished to maintain the durability of the surface effect.
Q: How to ensure consistency in the surface treatment process?
A: To ensure consistency, process parameters (such as pressure, temperature, processing time, etc.) must be strictly controlled, and automated equipment must be used to reduce human errors. In addition, process inspections are performed regularly to ensure standardization of each treatment.
Q: Why is surface treatment required before painting?
A: Surface treatment removes impurities, oxides, and contaminants to make the surface of the workpiece smoother and cleaner, and enhance the adhesion and durability of the coating. For metal workpieces, surface treatment is a necessary step before painting to ensure the performance and life of the coating.
Q: Will the chemically treated surface be harmful to human health?
A: Safety should be taken into consideration during chemical treatment (such as pickling and phosphating). Reasonable operation and use of environmentally friendly chemicals can minimize health risks. Operators should wear appropriate protective equipment, avoid direct contact with chemicals, and ensure that the working environment meets safety standards.
Filters