How does surface cleaning affect the performance of electronic products?
October 31, 2024
Electronic products are widely used in modern society, and their efficient operation depends on the stability of electronic components. In electronic manufacturing, environmental pollution, chemical residues, and electrostatic adsorption particles may affect component performance, so surface cleaning is crucial. This article explores the need for surface cleaning in electronic manufacturing, analyzes the impact on the performance of circuit boards and semiconductor components, introduces the role of ultrasonic cleaning, ion cleaning, sandblasting cleaning, and other technologies, and takes you to understand how surface cleaning controls pollution, improves reliability and improves user experience.
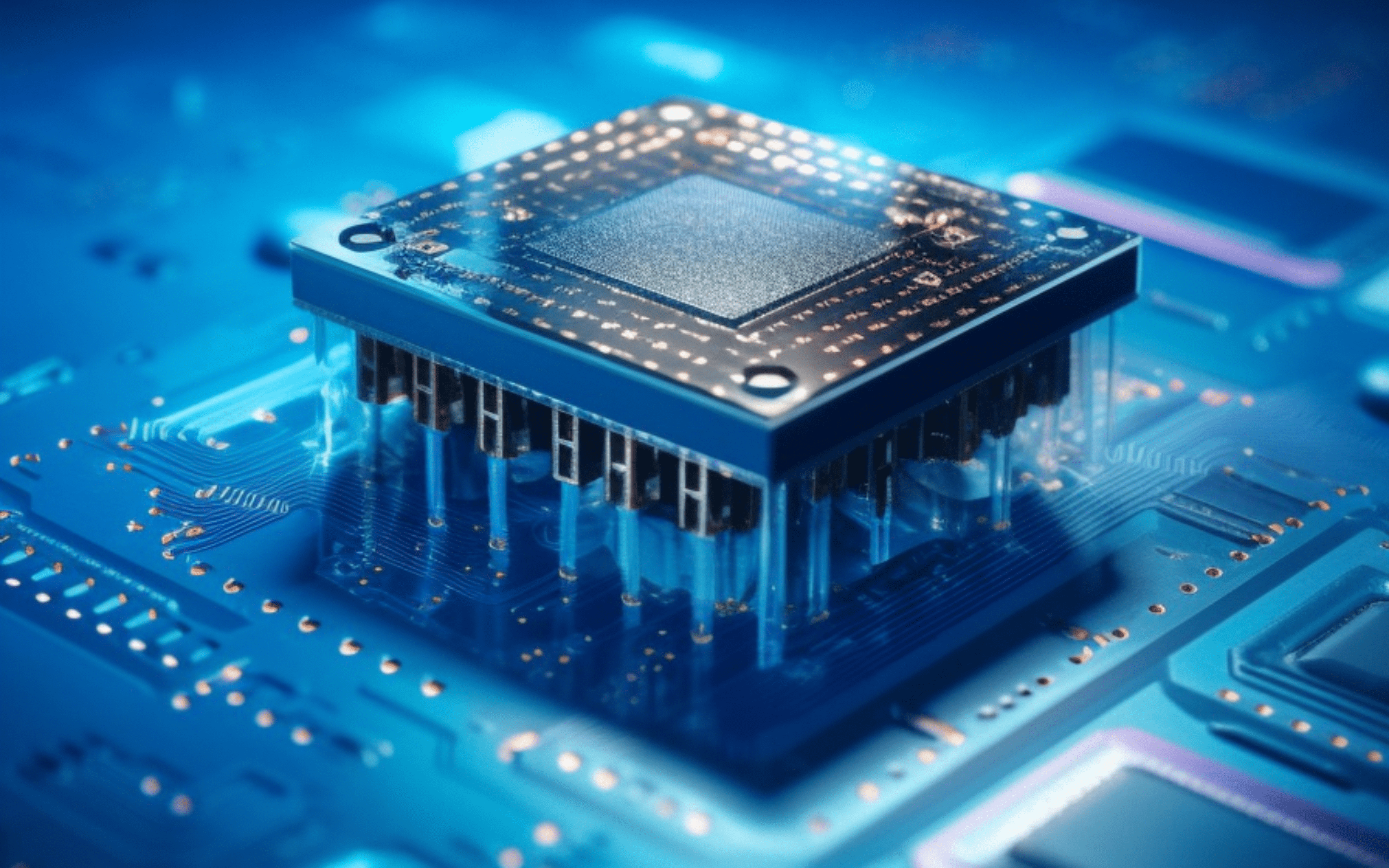
Surface Cleaning Requirements in Electronic Manufacturing
The need for surface cleaning during the manufacturing process of electronic products is directly related to the product’s stability and service life. The following are the main sources of pollution and their hazards.
- Sources of pollution
- Dust and particles
Dust and fine particles floating in the manufacturing environment will adhere to the surface of components, especially in miniaturized and high-precision production lines. These particles not only affect the electrical performance of components but may also cause short circuits or unstable conductivity of the entire circuit.
- Chemical residues
Flux, cleaning agents and other chemical solvents used in the process will leave residues on the surface of circuit boards and components. Even if these residues are not visually visible, the chemical composition may cause corrosion, hinder current transmission, or react at high temperatures.
- Impurities
The problem of static electricity is particularly prominent in electronic manufacturing, which easily adsorbs tiny particles of dust and cannot be removed by ordinary cleaning.
- Potential harm of pollution to electronic products
- Impact on the conductivity of circuit boards
Tiny particles and chemical residues will form an insulating layer in the conductive area, resulting in poor electrical connection and affecting the speed and quality of signal transmission. This has a potential impact on the overall performance of the circuit board and may even cause local failures.
- Reduce the reliability of semiconductor components
Semiconductor components have extremely high requirements for surface cleanliness because impurities and contaminants interfere with the essential properties of semiconductor materials. Contaminant particles may cause leakage, generate electromagnetic interference, or destroy the crystal structure, reducing the reliability of components.
- Increase product failure rate
The accumulation of contaminants increases the possibility of circuit short circuits and reduced conductivity, making electronic products more prone to failure during use. In the quality inspection of electronic products, the control of surface cleanliness has become an important guarantee to ensure product quality.
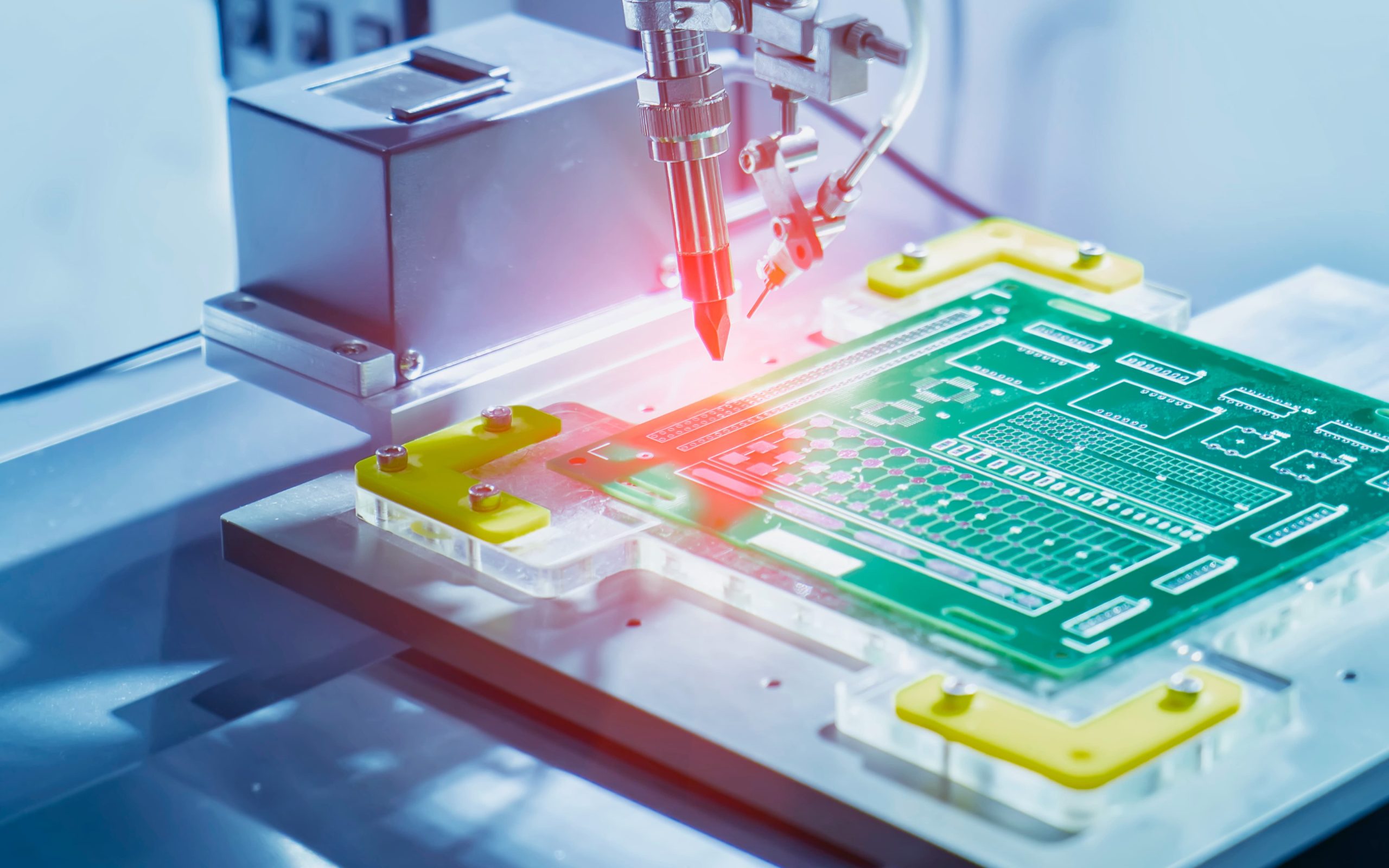
The key role of surface cleaning on circuit boards
Circuit boards are the core components of electronic products, and their surface cleanliness has a direct impact on electronic performance. In the process of circuit board manufacturing, cleaning is not only a key step to ensure product quality, but also a basic guarantee for improving product reliability.
- Ensure good electrical connection
- Remove solder slag and oxides to ensure solder joint quality
During the welding process, solder slag and oxides may remain on the surface of the circuit board or at the solder joint, resulting in poor contact, and increased resistance, thus affecting signal transmission. A high-quality cleaning process can effectively remove these residues to ensure the conductivity and durability of the solder joint.
- Improve the conductive stability of the circuit
Fine contaminants on the circuit will form an insulating layer, reduce the conductive effect, and may even cause a short circuit risk. Through high-precision cleaning methods, the conductive performance of the circuit can be guaranteed and the overall stability of the circuit board can be improved.
- The role of sandblasting in circuit board cleaning
In circuit board cleaning, sandblasting is widely used to remove stubborn surface contaminants and process complex surface structures. Its non-contact cleaning characteristics can avoid the potential damage to the fine lines of the circuit board by traditional cleaning and is suitable for various circuit board surface treatment needs.
- Effectively remove stubborn stains
The sandblasting process removes contaminants on the circuit board surface, including grease, dust, and slight oxides, by spraying media particles at high speed. These contaminants often reduce the conductivity of the circuit board and even cause short circuits or corrosion. Sandblasting can deeply clean irregular areas to keep the conductive path of the circuit board unobstructed.
- Improve surface flatness and adhesion
The sandblasting process can remove excess oxide layers and improve the microstructure of the surface, making the circuit board surface smoother and enhancing adhesion. For subsequent coating or welding operations, such surface optimization can effectively improve the firmness and durability of component adhesion, thereby improving the reliability and service life of the circuit board.
- Flexible process adaptability
By selecting different types and sizes of sandblasting media, the sandblasting process can be personalized for circuit boards of different materials. For example, when cleaning flexible circuit boards, softer dielectric particles can reduce mechanical stress on the material without affecting its electrical performance.
The role of surface cleaning on semiconductor components
Semiconductor components play a vital role in the performance and reliability of electronic products. However, due to the very delicate material structure of semiconductors, even tiny surface contamination can have a significant impact on their function. During the production and assembly process, dust, particulate matter, and chemical residues are inevitably introduced. If these contaminants are not effectively removed, they may cause unstable performance, poor heat dissipation, or even failure.
1. Improve performance stability
The presence of contaminants may change the surface charge distribution of semiconductor components, thereby interfering with the normal operation of the components. For example, tiny dust or chemical residues can affect sensitive transistors and electrodes, and even cause short circuits or leakage currents. By cleaning and removing these impurities, the electrical performance of the components can be effectively guaranteed, so that they can maintain stable conductive and insulating properties during operation and extend their service life.
2. Improve heat dissipation effect
Semiconductor components generate heat during operation. If the surface is covered with contaminants, the thermal resistance will increase, thereby affecting the heat dissipation performance. High-quality surface cleaning can remove the contamination layer that affects heat dissipation, allowing heat to dissipate more smoothly and reducing the risk of overheating. Good heat dissipation can not only protect components from thermal damage but also improve their long-term reliability.
3. Advantages of sandblasting
Sandblasting has significant advantages in semiconductor cleaning, especially when the contaminant particles are extremely small, sandblasting cleaning can more accurately control the degree of cleaning. Selecting fine aluminum oxide or glass beads as sandblasting media can achieve gentle and effective cleaning of the surface of semiconductor components:
- Accurate control of cleaning depth
Since the surface cleaning requirements of semiconductor components are extremely high, excessive cleaning may cause surface damage, while insufficient cleaning cannot completely remove contaminants. The sandblasting process can accurately control the sandblasting time and the strength of the medium particles, so that the cleaning depth is moderate, meeting the high requirements of semiconductors for cleaning accuracy.
- Removal of tiny particles and impurities
Sandblasting cleaning technology can effectively remove fine particles adsorbed by static electricity on the surface of semiconductors, and can also help eliminate potential static electricity sources.
Circuit board cleaning method
Circuit board cleaning is a key link in ensuring the reliability and performance of electronic equipment. The industry has developed a variety of cleaning methods for contaminants on circuit boards. Each method has its specific application scenarios, advantages and disadvantages, and applicability. The following will introduce several common circuit board cleaning methods in detail.
- Traditional cleaning methods
- Manual wiping
Manual wiping is a simple and direct cleaning method, usually performed with a special cleaning agent and a dust-free cloth. The advantages are simple operation and no need for complex equipment; it can be used to perform detailed cleaning on specific areas. However the disadvantages are low efficiency, the cleaning effect depends on the operator’s experience, there may be omissions, and the labor cost is also high.
- Solvent cleaning
Solvent cleaning is the use of chemical solvents to remove contaminants from the surface of circuit boards. It is widely used to remove welding residues and oil stains. Commonly used cleaning agents include isopropyl alcohol and ethanol. The advantages are that it can quickly and effectively remove organic dirt and grease, and is suitable for a variety of materials, with little residue after cleaning. The disadvantage is that the volatility of the solvent may pose a safety hazard, and for materials such as plastics, it may cause damage.
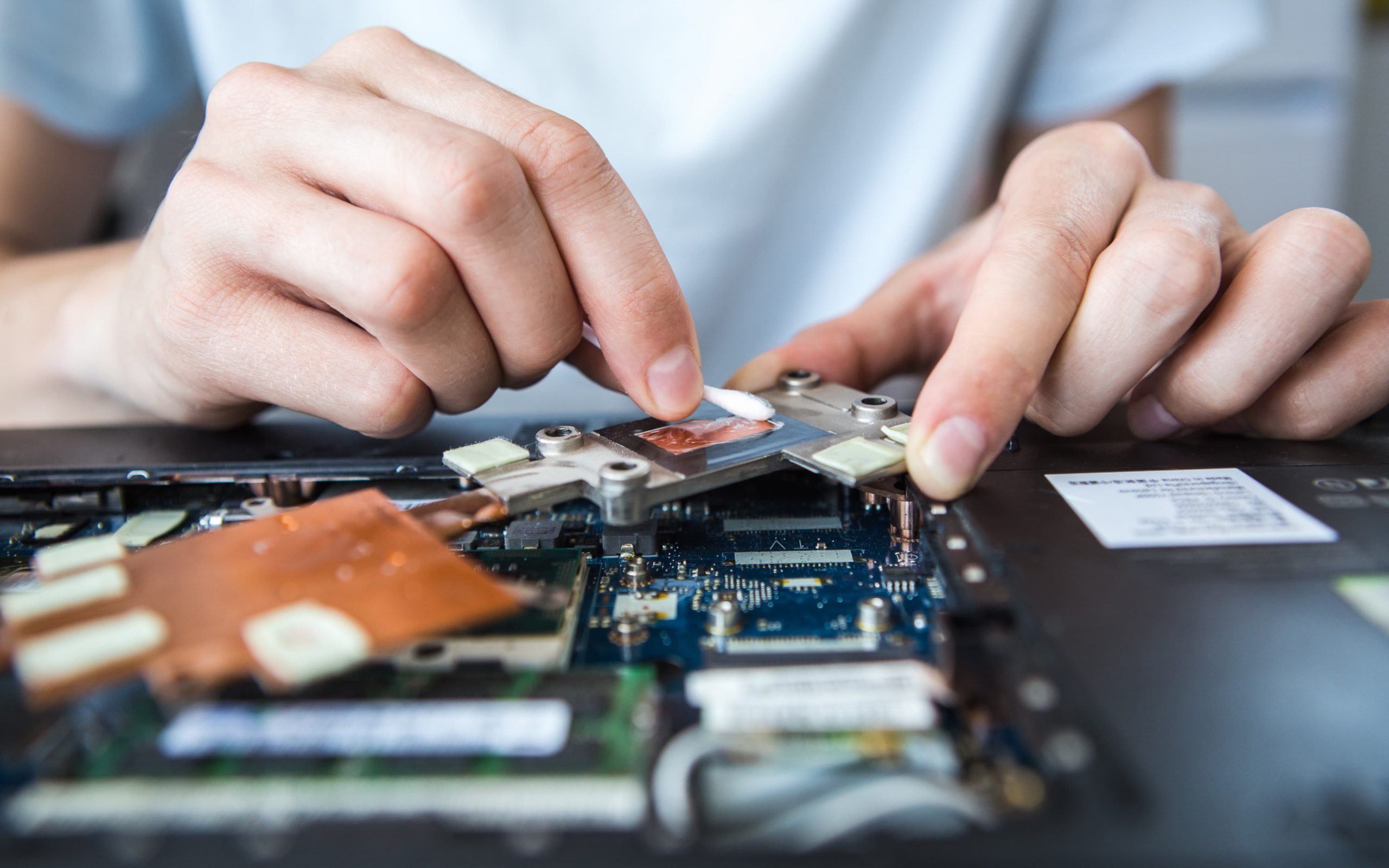
- Ultrasonic cleaning technology
Ultrasonic cleaning is a cleaning method that uses the cavitation effect generated by high-frequency sound waves in liquids. This technology shows unique advantages in cleaning precision components, especially for circuit boards with complex shapes.
- Working principles and advantages
Ultrasonic waves form tiny bubbles through the cleaning fluid. These bubbles explode under the action of pressure changes, generating strong impact force, which can penetrate every corner of the circuit board and remove stubborn dirt and impurities.
- Application cases
In practical applications, ultrasonic cleaning has been widely used for circuit board cleaning in fields such as medical equipment and aerospace. Studies have shown that ultrasonic cleaning can effectively remove solder and oxides, and improve the cleaning effect of the same type of pollutants with electrical performance. It is particularly effective in removing tiny particles, oil stains, and other organic pollutants, while the cleaning effect for solid particles depends on the properties of the cleaning fluid and the choice of ultrasonic frequency.
- Ion cleaning technology
Ion cleaning technology can remove dust and particles adsorbed by static electricity by using high-pressure gas to spray tiny ion particles onto the surface of the circuit board. This method is very important in the cleaning of semiconductors and high-precision electronic components.
- Principles and characteristics
Ion cleaning mainly relies on the electric field to accelerate the ions in the cleaning agent to a high speed, generating impact force to remove surface dirt. This technology can effectively avoid damage caused by physical friction and is suitable for cleaning sensitive components.
Ion cleaning can effectively remove fine particles generated by static electricity and maintain the cleanliness and functionality of the circuit board. After the circuit board is ion cleaned, the electrostatic charge on its surface is significantly reduced, which is crucial to prevent contamination in the subsequent manufacturing process.
- Importance in semiconductor component cleaning
In semiconductor manufacturing, ion cleaning is widely used to clean the surface of photomasks and chips to ensure stable electrical performance.
- Sandblasting cleaning technology
Sandblasting cleaning is a method of removing surface contaminants using high-speed sprayed granular media (such as ceramic particles or metal particles). This technology is particularly effective when stubborn dirt or impurities need to be removed.
- Principles and characteristics
Sandblasting uses compressed air to spray the cleaning medium at high speed onto the target surface, relying on impact force to remove contaminants. The advantage of this method is that it can handle surfaces with complex shapes, not just flat surfaces.
- Suitable types of contaminants
Sandblasting technology is suitable for removing oxides, solder residues, and other stubborn dirt. However, care should be taken to select the right medium to avoid physical damage to the circuit board.
- Comparative advantages with other cleaning methods
Compared with chemical cleaning and ultrasonic cleaning, sandblasting has a better effect in removing large or heavy dirt. At the same time, it has a fast operation speed and is suitable for large-scale production.
- Practical application
In some high-demand electronic manufacturing, sandblasting is used to remove contamination and prepare the surface to ensure the reliability and performance of the circuit board in the subsequent welding and assembly process.
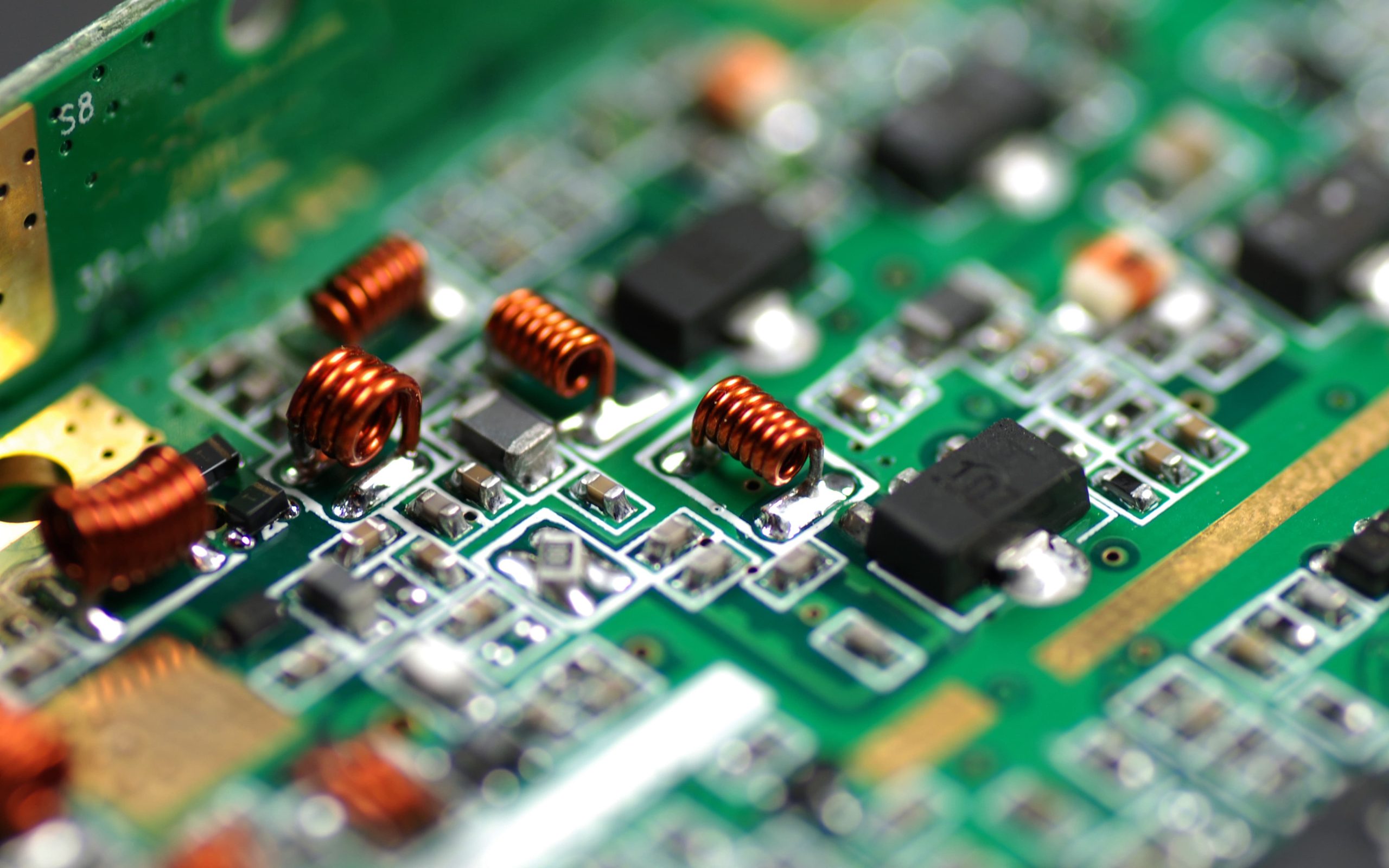
Application of sandblasting materials in electronic manufacturing
Sandblasting cleaning technology plays an important role in the electronic manufacturing industry, and choosing the right sandblasting material is the key to achieving efficient cleaning. Different types of sandblasting materials have different characteristics and application scenarios and are suitable for cleaning a variety of electronic components such as circuit boards and semiconductor components.
- Types of sandblasting materials
- Ceramic beads: Ceramic beads are widely used in cleaning circuit boards and semiconductor components because of their high hardness and low abrasiveness, which can effectively remove oxides and dirt on the metal surface. The diversity of its particle size and shape enables ceramic beads to meet different cleaning needs.
- Glass beads: Relatively soft, suitable for cleaning stainless steel and aluminum alloy surfaces, can effectively remove surface dirt without damaging the substrate. It can also be used to remove fine dust and pollutants in electronic products.
- Aluminum particles: With high hardness, it is suitable for removing stubborn dirt and coatings, and is often used for deep cleaning of circuit boards. Its stability under high-temperature conditions also makes it an ideal choice for cleaning.
- Polyester particles: It can effectively remove tiny particles adsorbed by static electricity while reducing damage to the substrate, and is suitable for use in electronic manufacturing.
- Characteristics and advantages of sandblasting materials
- Hardness and wear resistance: The hardness of sandblasting materials directly affects its cleaning effect. Materials with moderate hardness can effectively remove dirt while reducing wear on the substrate.
- Particle shape and size: Different particle shapes and sizes will affect the cleaning effect and speed. For example, larger particles are suitable for removing stubborn dirt.
- Environmental protection: Choosing environmentally friendly sandblasting materials can reduce the negative impact on the environment, which is in line with the current trend of sustainable development.
- Different cleaning needs
- Cleaning of circuit boards: For circuit boards, ceramic beads, and glass beads are usually the best choice because they can effectively remove solder slag and oxides while having minimal impact on the conductivity of the circuit board.
- Cleaning of semiconductor components: In the cleaning process of semiconductor components, polyester particles are an ideal choice because of their gentle characteristics and can effectively remove surface impurities without causing damage.
- Comprehensive evaluation: When selecting sandblasting materials, it is recommended to comprehensively consider cost, availability, and applicability to equipment to ensure a balance between cleaning effect and economy.
Pollution control strategy for electronic manufacturing
In the electronic manufacturing process, pollution control is an important part of ensuring product quality and performance. Through effective pollution control strategies, the negative impact of pollution on electronic products can be greatly reduced, and the reliability and life of products can be improved. Several major pollution control strategies will be discussed in detail below.
- Purify the production environment
- The role of air filtration system
Good air quality is to prevent pollution sources in the electronic manufacturing process. The use of efficient air filtration systems can significantly reduce the concentration of dust, particles, and other pollutants in the air. High-efficiency particulate air (HEPA) filters can remove 99.97% of particles with a diameter greater than 0.3 microns, which is essential for the purification of the electronic manufacturing environment.
- Static control measures
Static electricity is a common source of pollution in the production process of electronic components. It can absorb tiny particles and cause product performance to deteriorate. Taking static control measures, including the use of antistatic materials, grounding, and static dissipators, can effectively reduce the impact of static electricity on electronic components.
Electrostatic discharge (ESD) protection: Use ESD control equipment and clothing to reduce the accumulation and release of static electricity and protect sensitive components.
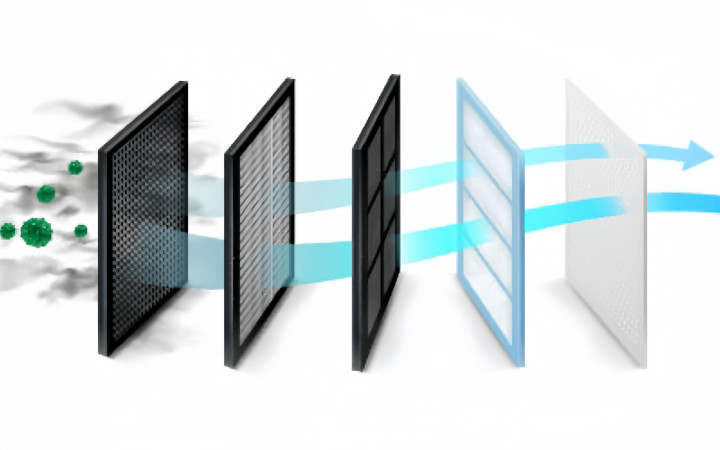
- Pollution control during sandblasting
During the sandblasting cleaning process, the dust and particles generated may become a new source of pollution. Therefore, it is very important to take effective pollution control measures.
- Dust treatment: Use local exhaust and dust collection devices to promptly handle the dust generated during sandblasting to ensure a clean and safe working environment.
- Cleaning process management: Before and after sandblasting, set cleaning and inspection standards to ensure that the sandblasting equipment and workpiece surface are not contaminated by secondary pollution.
- Strict process management
In electronic manufacturing, process management is an important link to ensure clean production. By formulating and implementing strict cleaning processes, the risk of pollution can be effectively reduced.
- Quality control of the cleaning process: Set clear cleaning standards and procedures, monitor and record the cleaning process, and ensure that every step meets the requirements.
- Employee training and operating specifications: Provide regular training for employees to enhance their awareness of the importance of cleaning and operating specifications, and ensure that every employee can master the cleaning process.
- Specifications and safety precautions for sandblasting operations
Sandblasting cleaning operations need to follow strict specifications to ensure safety and cleaning effects.
- Safety equipment: Operators should wear appropriate protective equipment, such as dust masks, goggles and protective clothing, to prevent the impact of particles generated during sandblasting on health.
- Operating procedures: Clarify the steps and precautions for sandblasting operations to ensure that every operator can perform cleaning tasks safely and effectively.
With the complexity and miniaturization of electronic products, the importance of surface cleaning has become increasingly prominent. In the future, sandblasting may be combined with other methods, and environmentally friendly sandblasting materials will become a trend. Enterprises should continuously update the control of electronic manufacturing pollution, pay attention to production environment purification, process management and employee training, ensure cleaning quality, and enhance the competitiveness of products in the market.
Filters