October 18, 2024
Surface polishing is a key technology widely used in the manufacturing industry. Its purpose is not only to make the product more beautiful but also to improve product performance, extend service life, and other goals. For many customers, the quality of surface polishing directly determines the market value and user experience of the product. Whether it is electronic products, automotive parts, aviation equipment, or medical equipment, polishing technology plays an important role. From the smoothness of the surface to the precise fit between parts, surface polishing not only improves the appearance of the product but also has significant optimization in terms of functionality and safety. This article will focus on the multiple purposes of polishing, starting from the actual needs of customers, deeply explore why surface polishing is crucial to products in various industries, and specifically explain its application examples in multiple industries.
How does polishing improve the aesthetics of products?
Surface polishing is a key process to improve the appearance of products, especially in high-end consumer products and industrial design. For customers in industries such as automotive manufacturing, electronics, and luxury goods, polishing can bring great visual improvement. Taking the automotive industry as an example, a finely polished car body can not only present a streamlined mirror effect but also reflect the high-end brand’s pursuit of quality and details. After polishing, the car paint shows a bright color, reduces the scattering of light, and gives people the ultimate visual enjoyment.
For the consumer electronics industry, surface polishing makes the shells of mobile phones, laptops, and other devices smoother and glossier, improving the user’s tactile experience and increasing the wear resistance and scratch resistance of the equipment. The luxury industry also relies on polishing technology. After fine polishing, jewelry, watches and other products can better show the texture and gloss of metal materials and enhance their market appeal. In addition, surface polishing can also cover up minor defects that may occur during the product’s manufacturing process, making the product’s overall appearance more unified and smooth.
Through fine polishing, the product is not only more attractive during the exhibition, but also conveys a high-end and professional brand image to customers. Especially in the luxury industry, such as watches, jewelry, and leather goods, the polished metal surfaces and decorative parts show a charming luster, greatly enhancing the product’s added value and attractiveness.
Extension:
- After polishing, the panels of refrigerators and washing machines in the home appliance industry not only improve the overall aesthetics but also enhance their anti-fingerprint and anti-fouling properties, which are convenient for cleaning and daily use.
- The metal parts in high-end furniture are polished to make the furniture more shiny and elegant, which enhances its appeal in the high-end market.
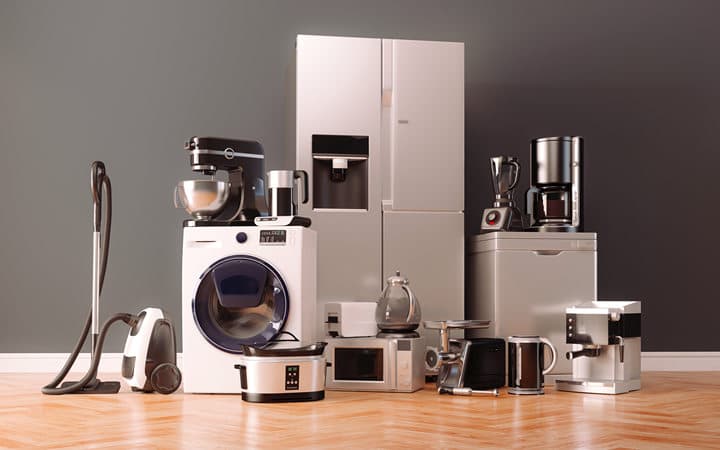
Polishing makes household items more beautiful
How does polishing improve the functionality of the surface?
Polishing is not only for appearance, functional improvement is also an important purpose of polishing. By removing surface roughness, polishing can reduce the friction coefficient of the product, improve wear resistance and fatigue resistance, and thus extend the service life of parts. For example, after polishing, the friction of transmission shafts and gears in the field of mechanical manufacturing is greatly reduced, making the operation smoother, thereby reducing energy consumption and improving mechanical efficiency.
Aerospace and energy equipment also rely on the support of polishing technology. After precision polishing, the turbine blades of aircraft engines can greatly improve the efficiency of airflow and reduce the energy loss of the engine. Similarly, in wind power generation and petroleum equipment, surface polishing can significantly reduce the friction and wear of parts during operation, extend the service life of equipment, and reduce maintenance costs.
In the manufacture of optical instruments with high precision requirements, the surface polishing of key components such as lenses and prisms can greatly reduce the scattering of light, greatly improve the clarity and transmittance of optical devices, and provide users with clearer and more accurate images.
Extension:
- After polishing, the internal parts of the automobile engine reduce the energy loss during engine operation and improve fuel efficiency.
- After polishing, the wind turbine blades are polished to improve the smoothness of the surface, reduce wind resistance, and improve energy conversion efficiency.
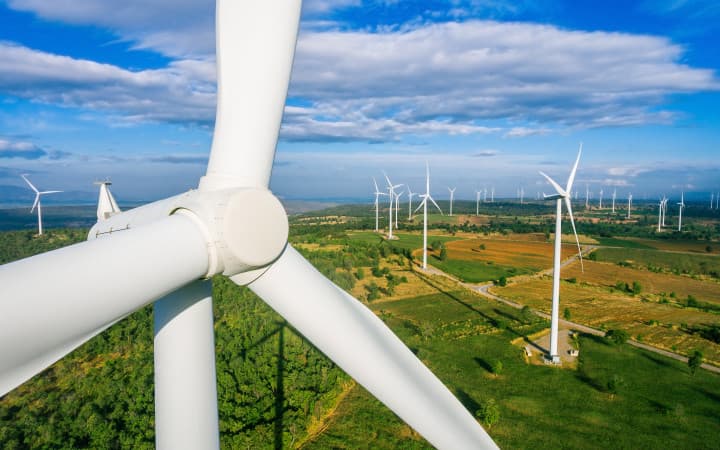
Wind turbine blades
How does polishing eliminate surface defects?
During the product manufacturing process, tiny burrs, scratches, or other surface defects are inevitable, and these subtle defects may cause problems during the use of the product. Polishing is one of the best ways to eliminate these surface defects. For example, the surface of metal parts in the machining industry is prone to burrs during production. These burrs not only affect the assembly of parts, but also generate additional friction during operation, and even cause component failure. Through polishing, surface defects can be completely removed and product quality can be significantly improved.
Polishing not only plays a role in metal products but also in the manufacturing process of plastic parts and composite materials. Polishing can also remove tiny defects remaining on the surface and make the surface smoother and flatter. For example, in the manufacturing process of medical devices, surface polishing can ensure that the surface of the product is free of any burrs, reduce friction and irritation that may be caused when in contact with patients, and improve product safety.
Extension:
- Aircraft engine turbine parts are polished to remove tiny manufacturing defects on the surface to ensure stable operation under high pressure.
- Plastic injection molding products are polished to eliminate minor defects left by the mold to ensure a smooth surface and improve appearance and performance.
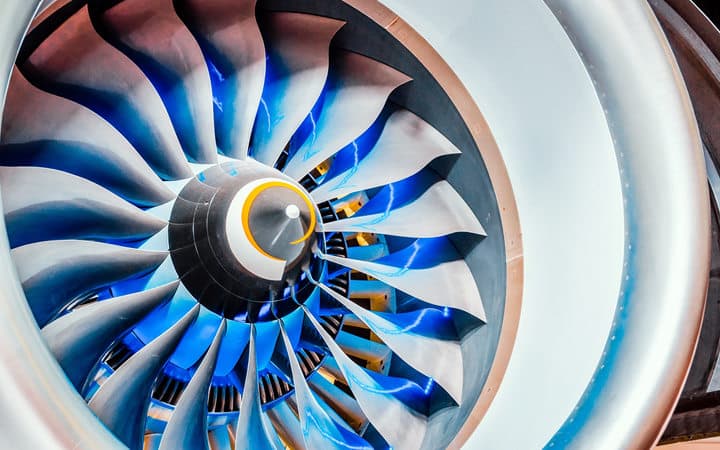
Engine Turbine
How does polishing improve the protectiveness of the surface?
Surface polishing can also effectively improve the corrosion resistance and oxidation resistance of the product. Especially for equipment exposed to harsh environments for a long time, polishing is an essential process. In the oil and gas industry, pipelines, valves, and other equipment need to have strong corrosion resistance on their surfaces because they work in high temperature, high pressure, and chemical corrosion environments all year round. Through polishing, the metal surface is denser and it is difficult for corrosive substances to enter the material, thereby extending the service life of the equipment and reducing downtime and maintenance costs.
The shipbuilding industry is also highly dependent on polishing technology, especially the polishing of the hull shell, which can effectively improve its ability to resist seawater corrosion and reduce wear and damage during long-term operation in seawater. In addition, surface polishing can also improve the hygiene standards of food processing equipment and medical devices to ensure that the surface will not breed bacteria and pollutants due to long-term use.
Extension:
- After polishing, chemical equipment can better resist the erosion of various chemicals, extend the service life of equipment, and reduce enterprise maintenance costs.
- After polishing, the hull of the ship significantly enhances its corrosion resistance, ensuring safe operation in harsh marine environments for a long time.
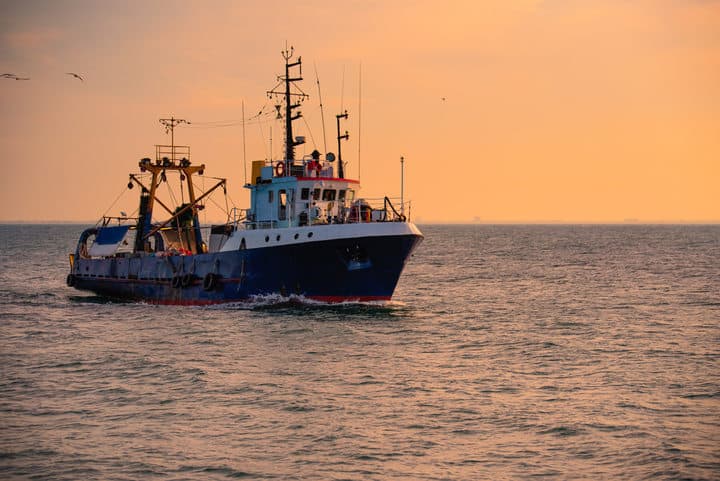
The hull needs to withstand various harsh environments
How does polishing ensure precision fit?
In the precision manufacturing industry, especially in the fields of electronics, optics, aerospace, etc., surface polishing not only affects the smoothness of the product surface but also directly determines the precision fit between parts. Customers want the fit between parts to be accurate and correct, reducing the risk of loosening or jamming during use. Polishing ensures that the fit between parts reaches micron-level precision by accurately removing the excess part of the material surface.
For example, in the production of medical devices, artificial joints can perfectly match human tissues after fine polishing, reducing friction and wear, thereby improving patient comfort and the life of artificial joints. In the field of optical instruments, the surface polishing of lenses can improve their transparency and optical performance, making them play a more stable role in high-precision measurements.
Extension:
- After polishing, the movement parts of precision watches ensure the precise fit between gears, improving the durability and accuracy of the product.
- Polishing reduces light scattering and improves image quality and observation accuracy.
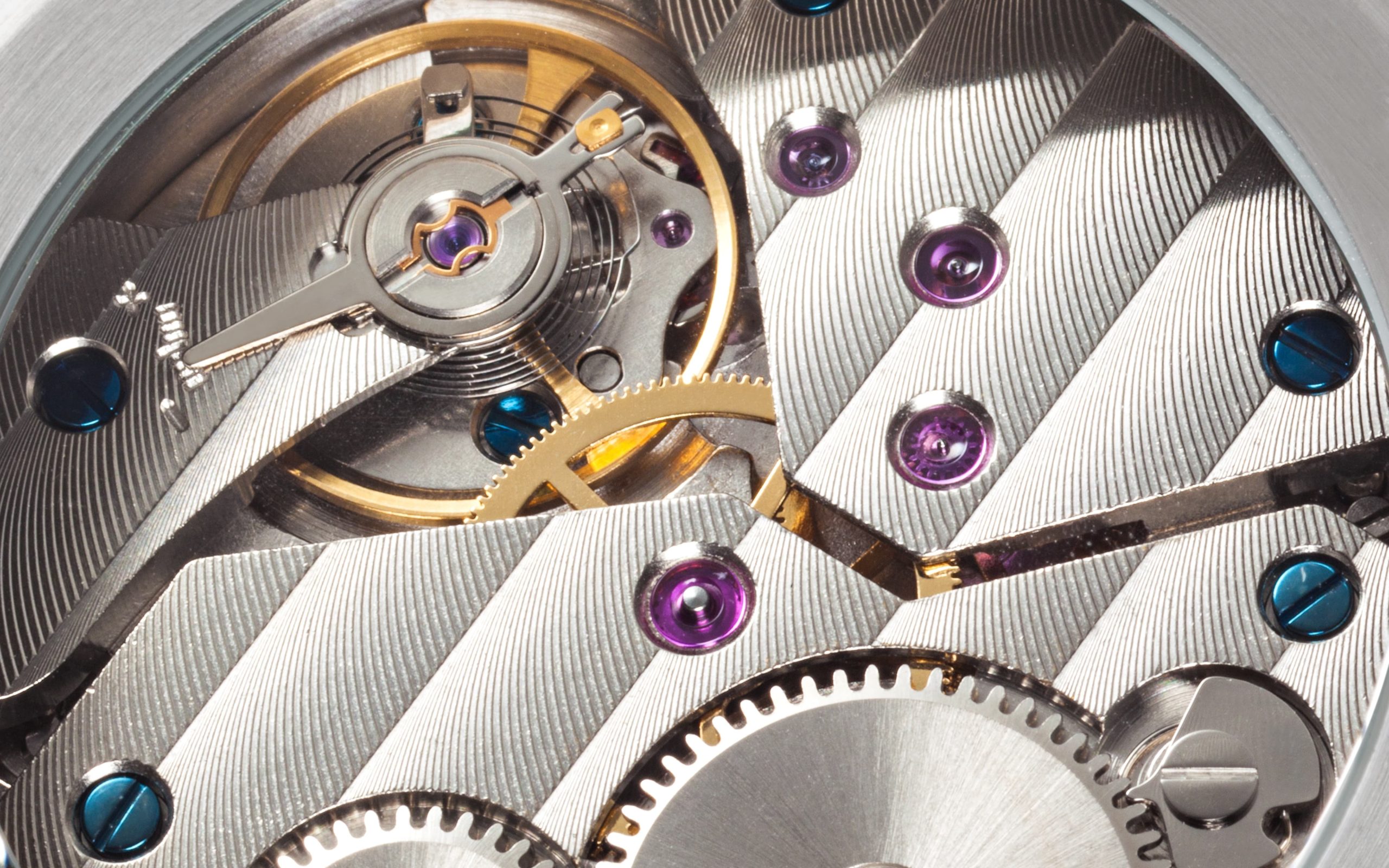
Precision fit between gears
How does polishing improve cleanliness and hygiene requirements?
In the pharmaceutical equipment and food processing industries, surface polishing is not only for aesthetics but also for improving hygiene standards – this is crucial for many industries, especially the pharmaceutical and food processing industries! Because surface polishing can significantly improve cleanliness and hygiene levels. Equipment with smooth and non-porous surfaces can prevent the accumulation of bacteria, dirt, and chemical residues, ensuring qualified hygiene conditions. Food processing equipment is polished to avoid the adhesion of food residues, thereby reducing the possibility of bacterial growth and meeting strict hygiene standards.
Polishing also plays an important role in medical device manufacturing. For equipment such as surgical instruments, implants, and catheters, the smoothness of the surface determines whether it can safely and effectively contact human tissue. Polished surgical tools reduce the chance of bacterial adhesion and reduce the risk of infection.
Extension:
- After polishing, the surface of pharmaceutical production equipment is smoother and flatter, reducing the risk of contamination in drug production and meeting the hygiene requirements of drug production.
- After polishing, dairy processing equipment prevents the adhesion of fat and residues in dairy products, making it easier to clean and disinfect.
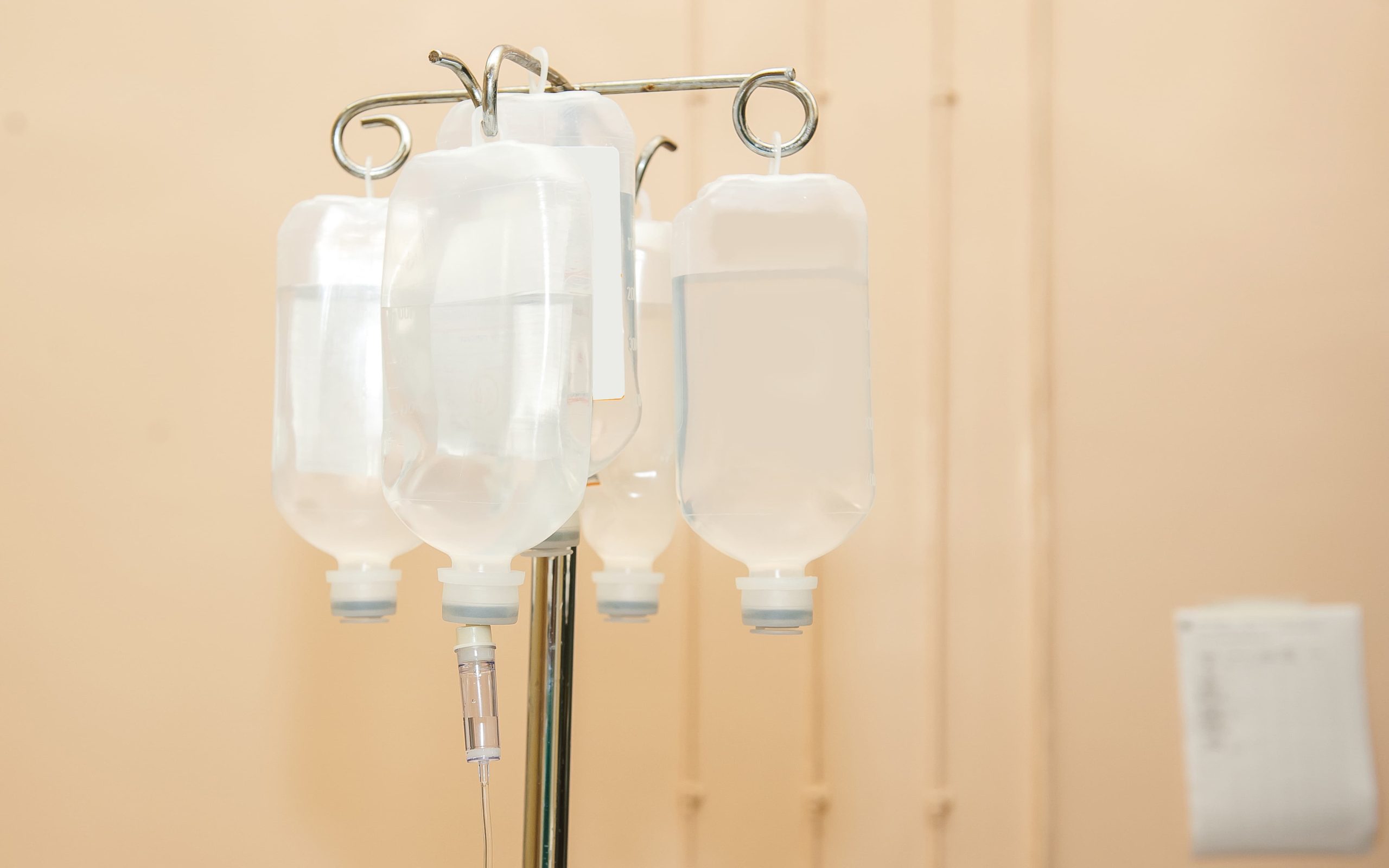
Clean catheters must be maintained
In summary, the benefits of polishing are as follows:
- Improve product appearance
- Improve surface performance
- Extend equipment life
- Reduce energy consumption and friction
- Meet strict hygiene standards
- Improve safety and reliability
It is worth mentioning that in today’s manufacturing industry, the demand for customization is constantly increasing, and customers’ personalized requirements for products are becoming increasingly obvious. Whether it is home appliances, auto parts, or luxury goods, consumers hope that the products not only have excellent performance but also reflect their unique personality and style. In this context, surface polishing, as a key surface treatment technology, can meet these customized needs.
Customization needs and surface polishing
- Diversity of customization
Different industries have their standards for surface finish, texture effects, and colors. For example, in the jewelry industry, consumers want products with high gloss and perfect light reflection effects, which requires a fine polishing process to achieve. In the automotive industry, different models of automotive parts may have different requirements for surface treatment. For example, sports cars may prefer smooth surfaces to improve performance, while SUVs may require more wear-resistant surfaces to adapt to off-road environments. There are also key aircraft components such as turbine blades, which often require highly customized polishing to reduce aerodynamic drag and improve fuel efficiency. Manufacturers use different polishing techniques based on the characteristics of each component to ensure optimal performance.
- Adaptability and flexibility
The adaptability and flexibility of the surface polishing process make it an ideal choice to meet the personalized needs of customers. Polishing equipment can be adjusted according to the characteristics of different materials (such as metal, plastic, glass, etc.) to achieve the best polishing effect. For example, the polishing process of aluminum alloy parts and stainless steel parts is different. Using different surface polishing tools and techniques for different materials can effectively improve the surface quality.
- Improve market competitiveness
With the intensification of market competition, companies need to continue to innovate to meet the customized needs of customers. By optimizing the polishing process, companies can not only improve product quality but also shorten production cycles and reduce production costs, thereby gaining an advantage in competition. Customized surface polishing services can attract more customers, improve customer satisfaction, and promote repeat purchases.
- Application of advanced technologies
The application of emerging technologies has also brought more possibilities for customized surface polishing. For example, new technologies such as laser polishing and ultrasonic polishing can not only achieve higher precision and efficiency but also meet the processing needs of complex shapes and microstructures. The application of these advanced technologies enables producers to provide customers with more sophisticated and personalized polishing solutions.
Through the above analysis, the close connection between customized needs and surface polishing has brought new opportunities and challenges to the manufacturing industry. Enterprises must continue to innovate and optimize processes to meet the growing personalized needs of customers and maintain their advantages in the fierce market competition.
Surface polishing is not only a link in the surface treatment process, but also the key to improving the overall quality of products. It can significantly improve the appearance of products, enhance the functionality of the surface, increase the service life of equipment, and ensure reliability in harsh environments. Especially in the fields of precision manufacturing, food processing, medical equipment, etc., polishing technology not only affects product performance but also directly relates to safety and hygiene standards. Through precise polishing technology, enterprises can meet customers’ needs for high quality, high performance, and safety of products, thereby improving market competitiveness. Whether in industrial manufacturing or daily life, the application of polishing technology is everywhere, and its value far exceeds our expectations.
Filters