What is a descaling process
October 16, 2024
In the field of metal processing, the descaling process is an important step to ensure material quality. Scale is an oxide formed by metal under high temperature or humid environment, which often adheres to the metal surface and affects the subsequent processing and coating process. Especially in the steel manufacturing industry, scale not only reduces the strength and toughness of the metal but also may cause adverse effects in the subsequent processing process, such as poor coating adhesion and reduced welding quality. Therefore, it is essential to deeply understand the formation of scale and its removal process.
Formation of scale
Scale is usually formed when the metal is exposed to high temperature, oxygen, and moisture. When the metal surface comes into contact with oxygen in the air, especially in the molten state, an oxidation reaction will occur on the metal surface. Over time, these oxides will accumulate to form a hard shell called scale. Specifically, in the steel manufacturing process, scale mainly comprises iron oxide, manganese oxide, and other components. The reasons for its formation include:
- High-temperature heating: During heat treatment or welding, the metal temperature rises and the surface oxidation reaction intensifies.
- Humid environment: The metal surface is exposed to humid air for a long time, causing moisture to combine with oxygen and accelerate oxidation.
- Improper storage: Lack of proper protection during storage of metal materials may lead to surface oxidation.
Oxide scale not only affects the finish of the metal surface but may also cause defects in subsequent processes. For example, during welding, an oxide scale may cause insufficient strength of the weld; and during the coating process, the presence of an oxide scale will prevent the coating from adhering well, thus affecting the anti-corrosion effect.
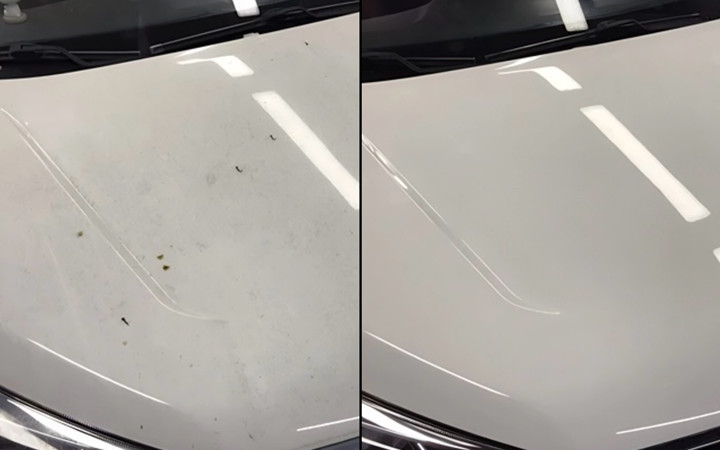
Repair comparison of oxidized cars
Descaling process
The process of removing oxide scale mainly includes mechanical removal, chemical removal, and sandblasting removal. Each method has its unique advantages and applicable scenarios, which will be introduced in detail below.
Mechanical removal
- Method overview
Mechanical removal is to remove oxide scale physically by manual or mechanical equipment such as grinders and scrapers. This method is suitable for small workpieces or local removal.
- Advantages
- High precision: It can accurately remove oxide scale without damaging the substrate, which is suitable for workpieces with high surface finish requirements.
- Easy operation: The equipment for mechanical removal is relatively simple, easy to operate, and suitable for various work occasions.
- Applicable scenarios
- Small parts: Small metal parts such as molds and tools need to be finely processed to ensure the subsequent processing effect.
- Local repair: Mechanical removal can effectively achieve targeted treatment for local oxide removal on large equipment.
Chemical removal
- Method overview
Chemical removal uses acidic solutions (such as hydrochloric acid, sulfuric acid, etc.) to dissolve the oxide. Chemical removal methods are suitable for large workpieces and can effectively remove oxide layers that are difficult to clean mechanically.
- Advantages
- Significant removal effect: Chemical agents can quickly and thoroughly remove oxide layers, especially thick oxide layers.
- Wide applicability: Suitable for workpieces of various complex shapes, not limited by physical contact.
- Applicable scenarios
- Large structural parts: For large metal components such as bridges, ships, and steel structures, chemical removal can effectively clean the oxide on their surfaces.
- Workpieces with complex shapes: For metal parts with irregular shapes or complex details, chemical removal can ensure thorough cleaning.
Sandblasting removal
- Method overview
Sandblasting removal removes oxides by spraying granular media (such as aluminum oxide, sand, etc.) with physical impact force. This method can quickly remove large areas of oxide and has a wide range of applications.
- Advantages
- High efficiency and speed: Sandblasting can process a large number of workpieces in a short time, with high efficiency and suitable for industrial production.
- Strong adjustability: According to the material and requirements of the workpiece, different sandblasting media and spray pressure can be selected to achieve personalized processing.
- Applicable scenarios
- Steel manufacturing: In the steel processing industry, sandblasting is often used to remove rust and oxide layers to prepare for subsequent painting or welding.
- Automobile and aviation industry: Sandblasting of automobile bodies, aviation parts, etc. to ensure their surface finish and improve product quality.
- Oil and gas industry: Used for surface treatment of oil and gas pipelines and equipment to remove oxides and impurities, prevent equipment corrosion, and extend service life.
After comprehensively considering the three processes of mechanical removal, chemical removal, and sandblasting removal, we can find that each method has its advantages, but in modern industrial manufacturing, the process that can simultaneously meet the requirements of efficiency, adaptability, and surface quality in large-scale production is undoubtedly sandblasting. The main reasons are as follows:
- High efficiency and speed: Sandblasting removal can process large areas of workpieces in a short time, greatly improving production efficiency. This is particularly important for modern industries that pursue production speed and efficiency.
- Strong adaptability: Sandblasting equipment can be adjusted according to different workpiece materials and oxide layer thickness to meet diverse production needs. This flexibility makes it suitable for a variety of industrial applications, including steel manufacturing, automobiles, and aviation.
- Surface quality: Sandblasting can not only effectively remove oxide scales, but also improve the surface finish of workpieces, creating a good foundation for subsequent coating and processing.
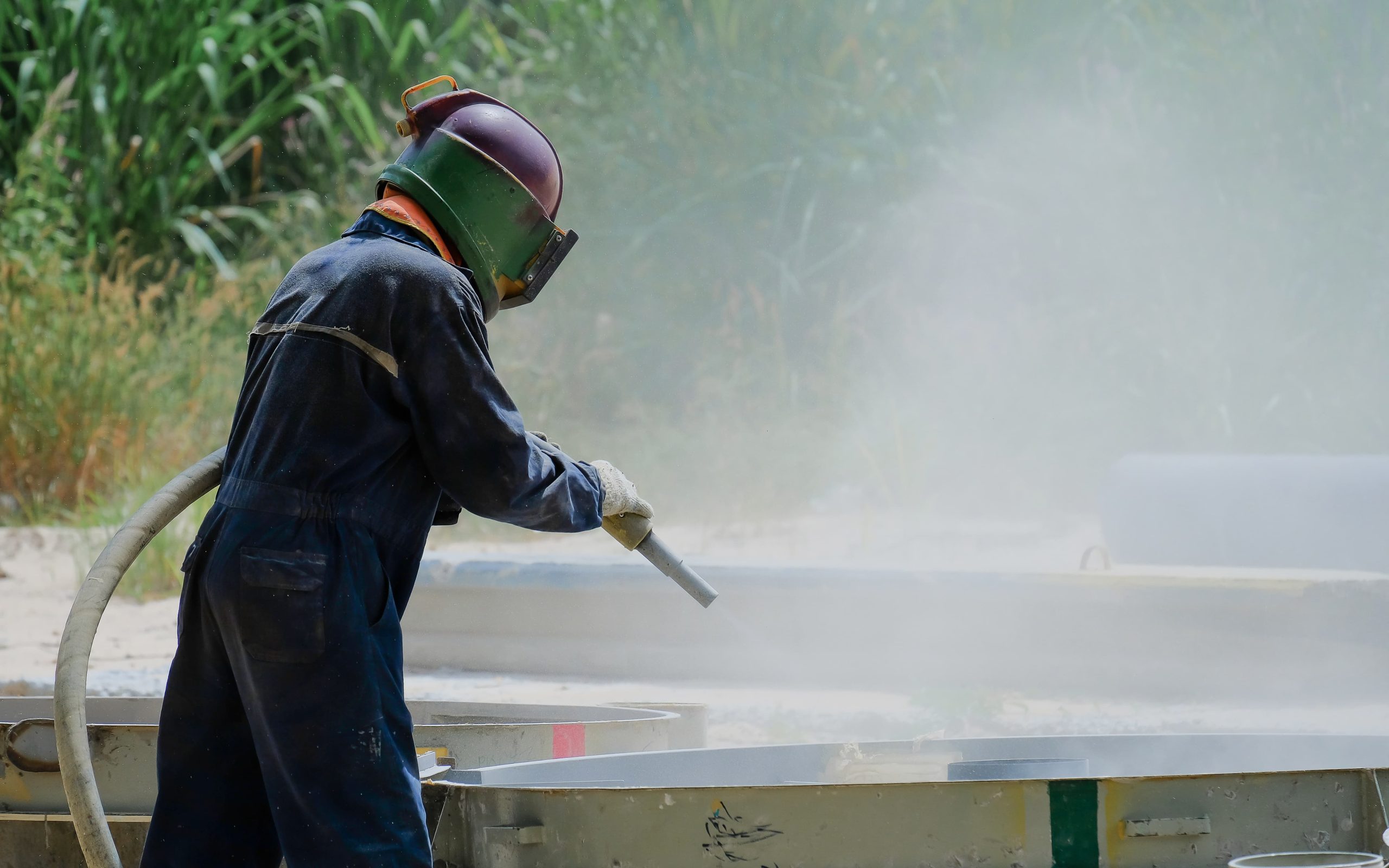
Sandblasting Demonstration
Equipment and materials for the descaling process
In the descaling process, it is crucial to choose the right sandblasting equipment. The following are three commonly used sandblasting equipment, namely high-pressure sandblasting machine, pressure sandblasting machine, and turbine sandblasting machine, each of which has different advantages and disadvantages and applicable scenarios.
- High-pressure sandblasting machine
A high-pressure sandblasting machine uses high-pressure air to accelerate and spray the sandblasting medium onto the surface of the workpiece, which is suitable for occasions requiring high-intensity impact force. Widely used in large-scale industrial production and the processing of heavy workpieces.
Advantages:
- High efficiency: It can quickly remove thick oxide layers and dirt and improve work efficiency.
- Wide range of applications: It can be used for surface treatment of various materials and is suitable for different process requirements.
Disadvantages:
- High equipment cost: Compared with other types of sandblasting equipment, the investment in high-pressure sandblasting machines is relatively large.
- High maintenance requirements: The maintenance and management of high-pressure systems are relatively complex and require professional operation.
- Pressure sandblasting machine
The pressure sandblasting machine controls the intensity and effect of sandblasting by adjusting the pressure and flow rate of the medium, which is suitable for medium-intensity cleaning needs. Suitable for smaller workpieces and surface treatment.
Advantages:
- Relatively low cost: Compared with high-pressure sandblasting machines, pressure sandblasting machines have lower purchase and maintenance costs and are suitable for use by small and medium-sized enterprises.
- Easy operation: The equipment operation is relatively simple and easy to use.
Disadvantages:
- Limited removal effect: For thick oxide scales and dirt, the cleaning effect may not be as good as that of high-pressure sandblasting machines.
- Not suitable for large-area treatment: Suitable for small-scale or fine operations, but not suitable for large-scale industrial production.
- Turbine sandblasting machine
The turbine sandblasting machine uses high-speed rotating turbine blades to accelerate the sandblasting medium to form a powerful jet, which is suitable for surface treatment. It is mainly used in surface treatment processes with high requirements.
Advantages:
- Good uniformity: The sandblasting medium is sprayed evenly, which can achieve better surface treatment effects.
- High efficiency and low energy consumption: Compared with other equipment, turbine sandblasting machines are more efficient in energy consumption.
Disadvantages:
- High initial investment: The purchase cost is relatively high, which is suitable for companies with sufficient budgets.
- High technical requirements: Operation and maintenance require certain technical support.
When choosing the right sandblasting equipment, factors such as the characteristics of the workpiece, the thickness of the oxide scale, and the budget need to be considered. Understanding the characteristics and applicable scenarios of various types of sandblasting equipment can help your company achieve the best results in the oxide scale removal process. Of course, in the process of oxide scale removal, it is also crucial to choose the right sandblasting material. The following are four commonly used sandblasting media. I will explain in detail their respective advantages and disadvantages and applicable scenarios. According to the needs and budget of specific workpieces, you can choose the most suitable material to achieve the best removal effect.
- Steel grit
Advantages:
- High hardness: Steel grit has high hardness and can effectively remove stubborn oxide scales and dirt.
- Economical: Compared with other sandblasting media, steel grit has a lower cost and is suitable for large-area applications.
Disadvantages:
- Easy to rust: Steel grit is easy to oxidize during use and may leave rust on the surface.
- Dust generation: More dust may be generated during the blasting process, and ventilation and safety measures need to be strengthened.
Applicable scenarios:
Steel grit is often used for surface treatment of industrial manufacturing and heavy machinery, especially for removing oxide scale and welding residues on the surface of large workpieces.
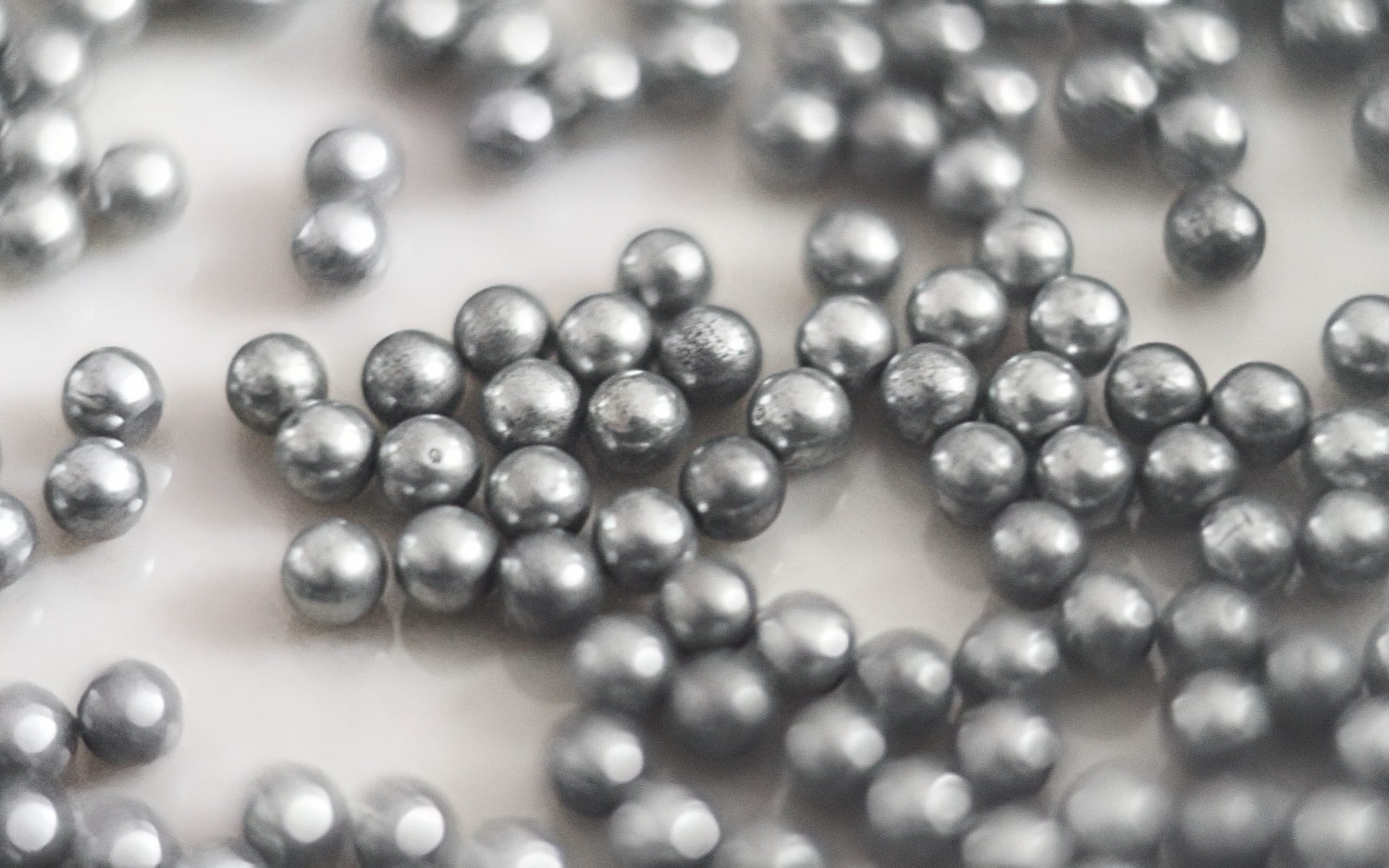
Steel Ball
- Brown corundum
Advantages:
- Strong wear resistance: The hardness and wear resistance of brown corundum make it excellent in removing oxides.
- No pollution: Its chemical properties are stable and will not cause pollution to the surface of the workpiece.
Disadvantages:
- Higher cost: Compared with steel grit, brown corundum has a higher price and may not be suitable for projects with limited budgets.
- Large brittleness: During use, it may break and generate dust.
Applicable scenarios: Brown corundum is suitable for fine surface treatment and cleaning, such as the requirements for high surface quality in the aerospace and automotive industries.
- Steel shot
Advantages:
- Smooth surface: Steel shot can form a smooth surface without damaging the substrate during the spraying process.
- Long service life: Due to its wear resistance, steel shot can be reused many times and is economical.
Disadvantages:
- Limited cleaning effect: For a thick oxide scale, the cleaning effect of steel shot may not be as good as steel grit and brown corundum.
- Heavier: Compared with other media, steel shot is heavier and requires more energy when spraying.
Applicable scenarios: Steel shot is mainly used for surface polishing and strengthening, and is widely used in the surface treatment of automobiles, machinery manufacturing, and metal products.
Advantages:
- Excellent cleaning effect: Aluminum oxide has high hardness and can effectively remove oxide scale without causing too much damage to the substrate.
- Environmental protection: Its non-toxic and harmless characteristics give it an advantage in environmental protection.
Disadvantages:
- High cost: Aluminum oxide is relatively expensive compared to other sandblasting media and is not suitable for large-scale, low-budget projects.
- Not suitable for heavy oxide layers: Aluminum oxide may require a long processing time when dealing with thick oxide layers.
Applicable scenarios:
Aluminum oxide is suitable for industries with high requirements for surface finish, such as surface treatment of electronic devices and precision machinery.
Industry application cases
Oxide scale removal is widely used in various industries. Here are some specific case studies:
Steel manufacturing
In the steel manufacturing industry, an oxide scale is usually formed during the heat treatment and welding of steel. Sandblasting or chemical cleaning can effectively remove the oxide layer and improve the quality of subsequent treatments (such as coating and welding). Steel manufacturers have successfully reduced the shedding rate of subsequent coatings and improved the surface quality and durability of products by using aluminum oxide.
Aerospace
In the aerospace field, oxide scale removal is key to ensuring component performance. High-temperature alloy parts are prone to forming oxide layers during manufacturing and welding. Using an ultrasonic cleaner to remove them can maintain the geometric accuracy and surface finish of the components, which is crucial to improving the reliability of aircraft components.
Oil and Gas Industry
In the oil and gas industry, equipment surfaces are often contaminated by oxides and deposits, especially in high-temperature and high-pressure environments. For example, key equipment such as drill bits and valves will form an oxide layer during operation. Using a sandblaster to treat it can effectively extend the service life of the equipment and improve its working efficiency.
Best practices for the descaling process
To ensure the efficiency and safety of work, you can pay attention to the following key operating suggestions during the oxide scale removal process:
Standardize the operating process
Ensure that the operating process is standardized, including pre-treatment, main treatment, and post-treatment. Operators need to be familiar with the requirements of each link to ensure the integrity of the oxide scale removal.
Safety Precautions
- Personal protective equipment: Operators should wear appropriate protective equipment such as protective glasses, masks, gloves, and earplugs to avoid injury during operation.
- Ventilation and exhaust: When using chemical cleaning agents or sandblasting equipment, ensure that the work area is well-ventilated to reduce the accumulation of harmful gases and dust.
Operator Training
Strengthen the training of operators to ensure that they understand the use of equipment, hazards, and emergency response measures. Conduct safety drills regularly to deal with emergencies.
Equipment maintenance
Maintain and service the equipment for descaling regularly to ensure its normal operation. For sandblasting machines, the condition of the nozzle, air pressure, and abrasive should be checked regularly to ensure the consistency of the removal effect.
Descaling is of great significance in the metal surface treatment process, which is directly related to the quality and production efficiency of the product. Choosing appropriate removal methods and materials can not only improve the effect of surface treatment but also reduce production costs and environmental impact. In the future, with the continuous advancement of technology, the descaling process will be more efficient, environmentally friendly, and intelligent. People in the industry should pay attention to the descaling process to ensure the high quality and performance of metal products to meet the needs of modern industry.
Filters