Surface finishing solutions for different materials
October 24, 2024
Surface finishing is an important process in modern manufacturing, which can not only improve the appearance and quality of products but also enhance their functionality and durability. In today’s various industries, surface finishing technology is widely used for different materials, such as metals, plastics, and glass. Still, ther are significant differences in surface treatment processes for various materials because their different physical and chemical properties determine the other challenges and requirements encountered during the processing. Therefore, when choosing a finishing method, the specific characteristics of the material must be considered to ensure that the process can meet its requirements in terms of wear resistance, corrosion resistance, and enhanced aesthetics. This article will explore surface finishing solutions for three common materials: metal, plastic, and glass, and discuss their differences and specific application scenarios.
Differences and challenges between materials
Overview of material properties
- Metal: Metal materials are known for their high strength and hardness. Common problems include surface oxidation, rust, and mechanical damage. Especially in harsh environments, metal surfaces are prone to oxidation reactions, which affect their service life and aesthetics.
- Plastic: Plastic materials have good flexibility and chemical stability, but are prone to scratches and static electricity accumulation on the surface. Plastics are sensitive to temperature during processing, as high temperatures can cause the material to deform and affect its performance.
- Glass: Glass is both hard and brittle, so it is easy to break, so it needs to be processed with extreme care to prevent microcracks. The transparency of the glass is also an indicator that needs to be focused on during processing, as any flaws may affect its appearance and function.
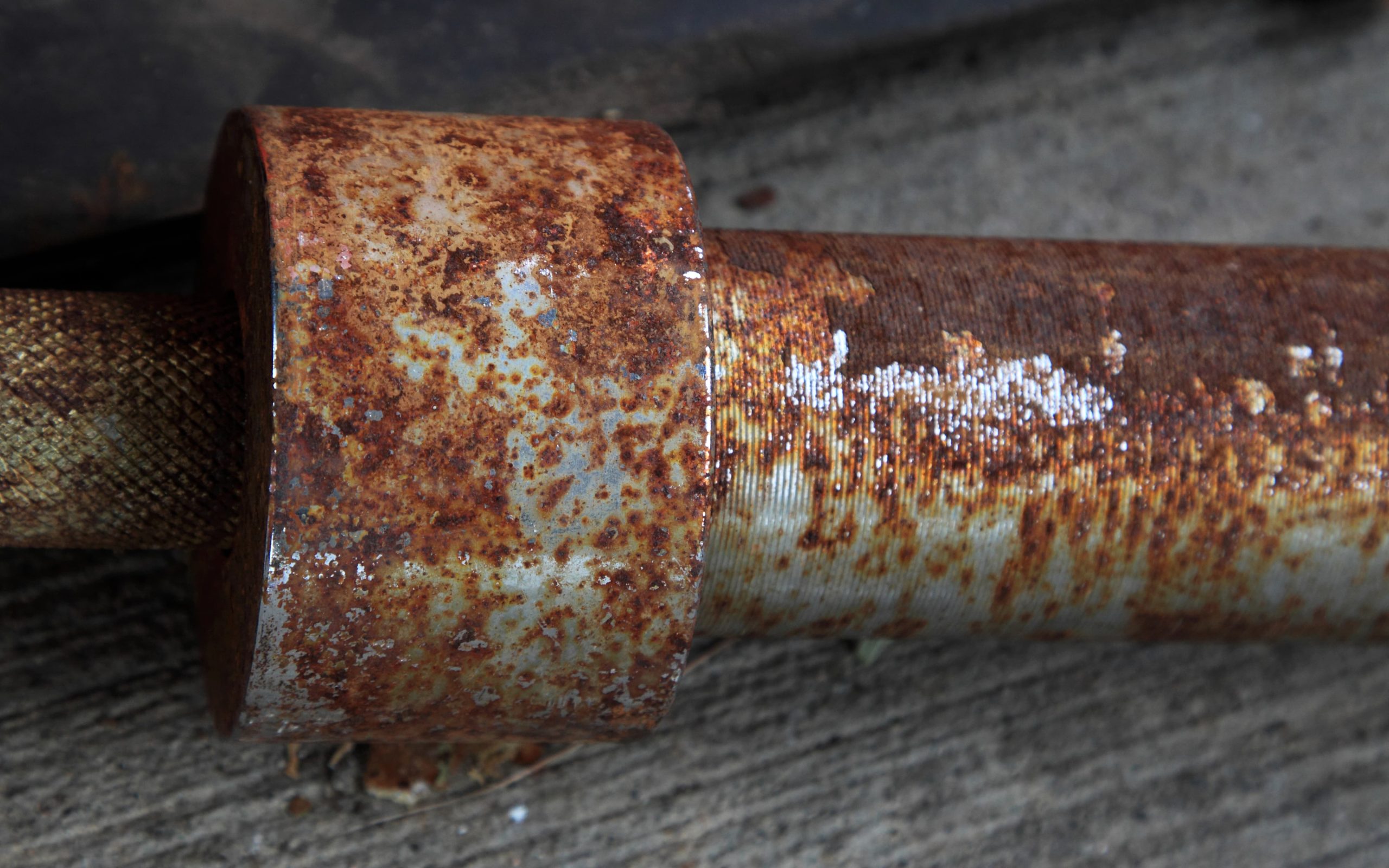
Metal oxidation is a common problem
Surface treatment challenges
- Metal: When removing scale and rust, how to ensure the smoothness and structural integrity of the surface is a key issue. If the treatment method is not selected properly, it may cause damage to the metal surface, which will affect subsequent painting and use.
- Plastics: Surface damage caused by high temperature, chemicals, or mechanical processing needs to be avoided, especially for brittle materials. Choose the appropriate finishing process to reduce the thermal impact and mechanical stress on the plastic.
- Glass: During the treatment of the glass surface, it is necessary to avoid microcracks, and scratches and ensure that the transparency is not affected. For different types of glass, it is necessary to choose the appropriate finishing method to ensure the quality of the final product.
The needs and goals of finishing
Finishing is not only to improve the aesthetics of the product but also to improve the functionality of the material, such as wear resistance, corrosion resistance, and impact resistance. By rationally selecting processing methods and materials, multiple goals of the product can be achieved, providing customers with better services.
- Metal: Finishing needs in different industries
- Automobile manufacturing industry
In the automotive industry, finishing technology is required to enhance the wear resistance, corrosion resistance, and impact resistance of the material to ensure the long-term use of the vehicle under harsh conditions. Especially in coastal areas or high-humidity environments, corrosion resistance is essential. The steel of the body and chassis usually needs to be sandblasted, polished, and coated to prevent corrosion caused by long-term exposure to the environment. In addition, the smoothness of the metal surface will also affect the aerodynamic performance, so in the manufacture of high-end cars such as sports cars, there are also very high requirements for the accuracy of surface treatment.
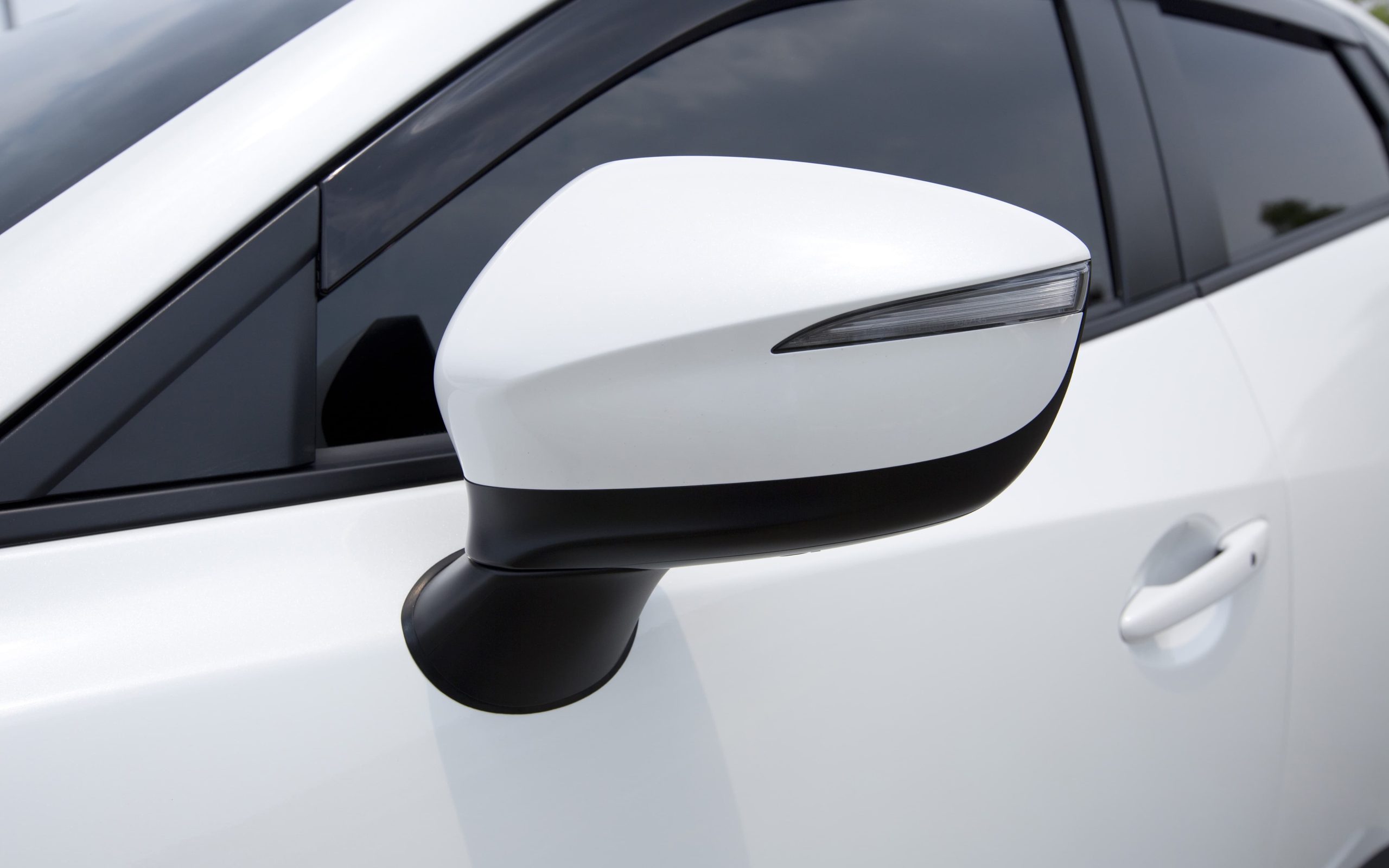
Car body surface after finishing
- Construction and infrastructure
In the construction industry, especially in structures such as high-rise buildings and bridges, metals are often used to construct frames, curtain walls, and exterior decorations, so more attention is paid to the anti-rust treatment of the steel surface. The metal panels on the exterior walls of buildings must not only be resistant to weathering but also have to increase their antioxidant properties through fine surface processing, thereby reducing the cost of long-term maintenance. To enhance the visual effect and functionality of the materials, anodizing and sandblasting are widely used in the construction industry.
- Aerospace
Aerospace has extremely stringent requirements for metal materials. Aircraft fuselages are usually made of lightweight aluminum alloys or titanium alloys, which must have extremely high oxidation resistance and strength while ensuring lightweight. To this end, the aerospace field often uses anodizing and precision sandblasting to ensure the wear resistance and corrosion resistance of the fuselage surface, thereby extending its service life. In addition, the surface after finishing must be smooth and uniform to reduce wind resistance during flight and improve fuel efficiency.
- Plastics: Finishing requirements in different industries
- Electronics industry
With the rapid development of consumer electronics, the widespread use of plastic materials has brought advantages such as lightness and strong plasticity to products. However, consumers’ high requirements for product appearance make the finishing of plastic surfaces particularly important. For the shells of electronic products such as mobile phones and laptops, technologies such as sandblasting and chemical treatment can effectively improve the smoothness, wear resistance, and anti-fingerprint properties of the surface, ensuring that the product can maintain a high finish and high-quality feel after long-term use. At the same time, since plastics have certain flexibility and shock resistance, the surface treatment method also needs to adapt to its material properties to prevent plastic deformation due to high temperature or excessive friction.
- Medical equipment
Plastic parts in medical equipment usually require extremely high surface finish and antibacterial properties. Especially in the processing of shells for surgical instruments or medical devices, the surface must be smooth and flawless to reduce the risk of bacterial attachment. Sandblasting and low-temperature deburring technology can effectively remove tiny burrs and ensure the surface accuracy of medical devices while maintaining the non-toxicity and sterility of the material. In addition, plastic finishing in the medical industry also needs to meet strict regulatory standards to ensure that the equipment can maintain stable performance during frequent disinfection and cleaning.
- Automotive interior parts
In the manufacture of automotive interior parts, plastic materials need to meet the requirements of wear resistance, durability, and beauty at the same time. For example, parts such as door handles and dashboards must not only remain intact under high-frequency use but also present a high-quality appearance and feel. Sandblasting can give plastic interior parts a high-quality surface texture, improve their aesthetics, and enhance the adhesion of subsequent coatings. Low-temperature deburring technology effectively ensures the accuracy of parts and avoids deformation or defects during processing that affect the service life of the product.
- Glass: Finishing requirements of different industries
- Decorative arts and home furnishing industry
In decorative arts and high-end home furnishing design, the aesthetics and customization of glass are very high. Through fine sandblasting etching technology, complex patterns can be engraved on the surface of the glass to create a unique decorative effect. At the same time, physical polishing can give glass products a high mirror effect, making them exude a sense of luxury and artistic atmosphere in interior decoration.
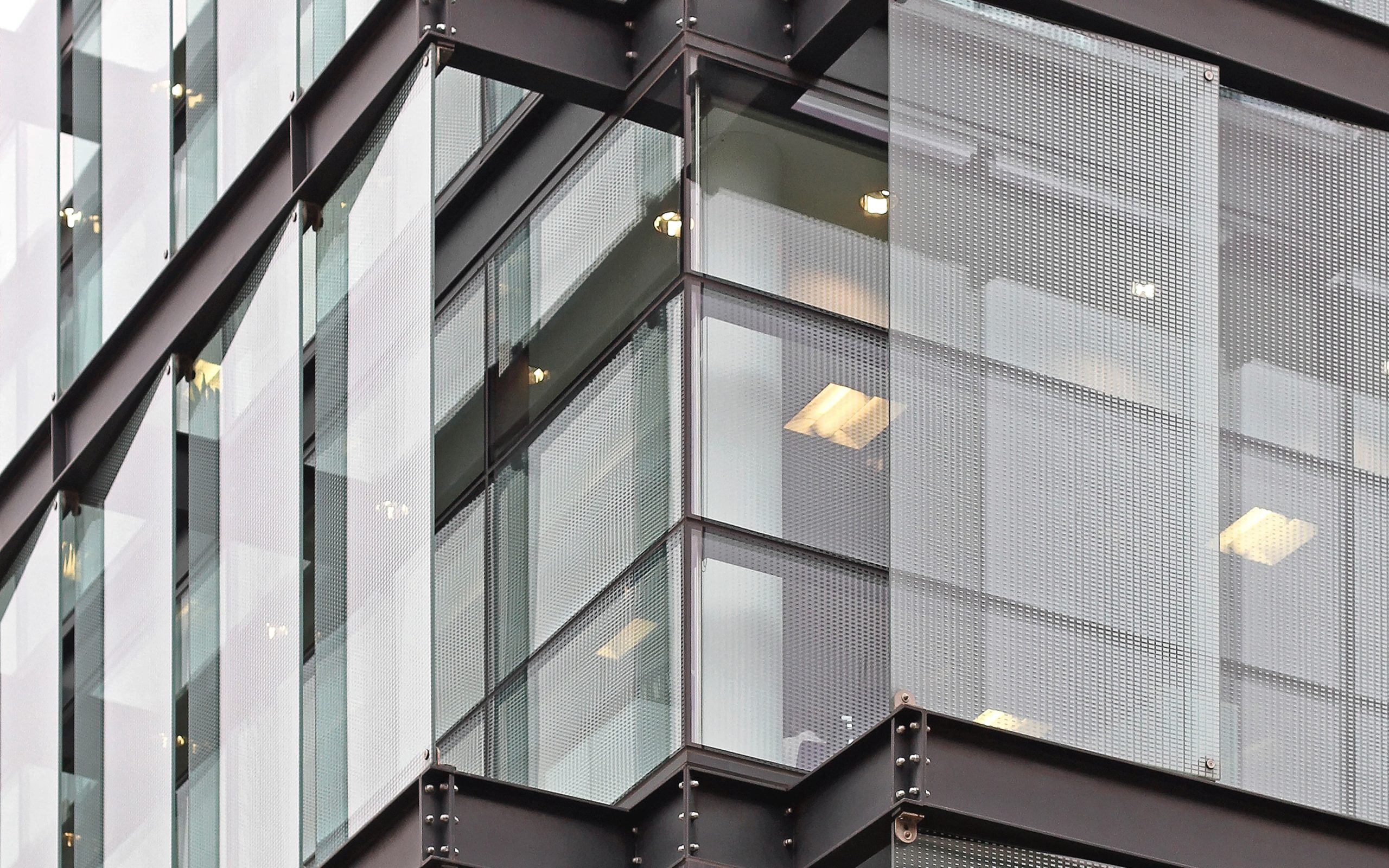
Etched architectural glass curtain wall
- Automobile industry
The requirements for glass in the automotive industry are mainly focused on safety and optical performance. Windshields and windows must have high impact resistance and scratch resistance, so these properties need to be improved through physical polishing and chemical treatment. At the same time, the transparency and optical consistency of the glass needs to be guaranteed during the finishing process to ensure the driver’s clear vision and driving safety. In addition, in the decoration and functional design of automotive glass, sandblasting etching is also widely used for the customized processing of brand logos or personalized designs.
- Construction industry
In modern buildings, glass curtain walls and windows are widely used. The surface treatment requirements of glass materials are not only aesthetic design requirements but also functional considerations. Architectural glass usually needs to be sandblasted, etched, or chemically polished to enhance its scratch resistance, UV resistance, and impact resistance to ensure its service life in various environments. At the same time, the transparency and finish of the glass must also be consistent to ensure that the lighting effect and visual effects of the building are not affected.
Surface finishing methods of metals
Metal surface characteristics and processing requirements
The finishing of metal surfaces usually requires oxide removal, anti-corrosion treatment, and improved finish. Common metal materials include steel, aluminum, copper, and stainless steel. For different metals, it is particularly important to choose the right processing method.
Common finishing methods
- Mechanical polishing: Improve the surface smoothness by mechanical means, suitable for most metals. Mechanical polishing can effectively remove surface defects and improve the appearance of the product.
- Sandblasting: Use high-pressure sand flow to clean the surface and remove rust, an oxide layer, or burrs. The sandblasting process can be selected according to different sand materials, such as ceramic beads, glass beads, aluminum oxide, etc., to achieve the best effect.
- Electroplating: Form a protective layer on the metal surface by chemical or electrochemical means to prevent corrosion. Electroplating can not only improve the gloss of the metal surface but also enhance its corrosion resistance.
- Anodizing: Especially suitable for aluminum, it enhances wear resistance and corrosion resistance by forming an oxide film on the surface. After anodizing, the oxide film formed on the aluminum surface is not only beautiful but also effectively prevents further oxidation.
Application scenarios
- Automotive industry: Anti-corrosion treatment and polishing of car body steel to ensure smooth, beautiful, and durable. The finishing of the car surface not only improves the appearance quality but also enhances the service life.
- Construction industry: Anti-rust treatment of steel structure parts of building exterior walls to extend the service life. The application of finishing technology makes building materials more durable.
- Aerospace: Lightweight and high-strength processing of aluminum alloy for aircraft fuselage, combined with anti-oxidation treatment. For aerospace products, surface finishing is the key to ensuring structural safety and performance.
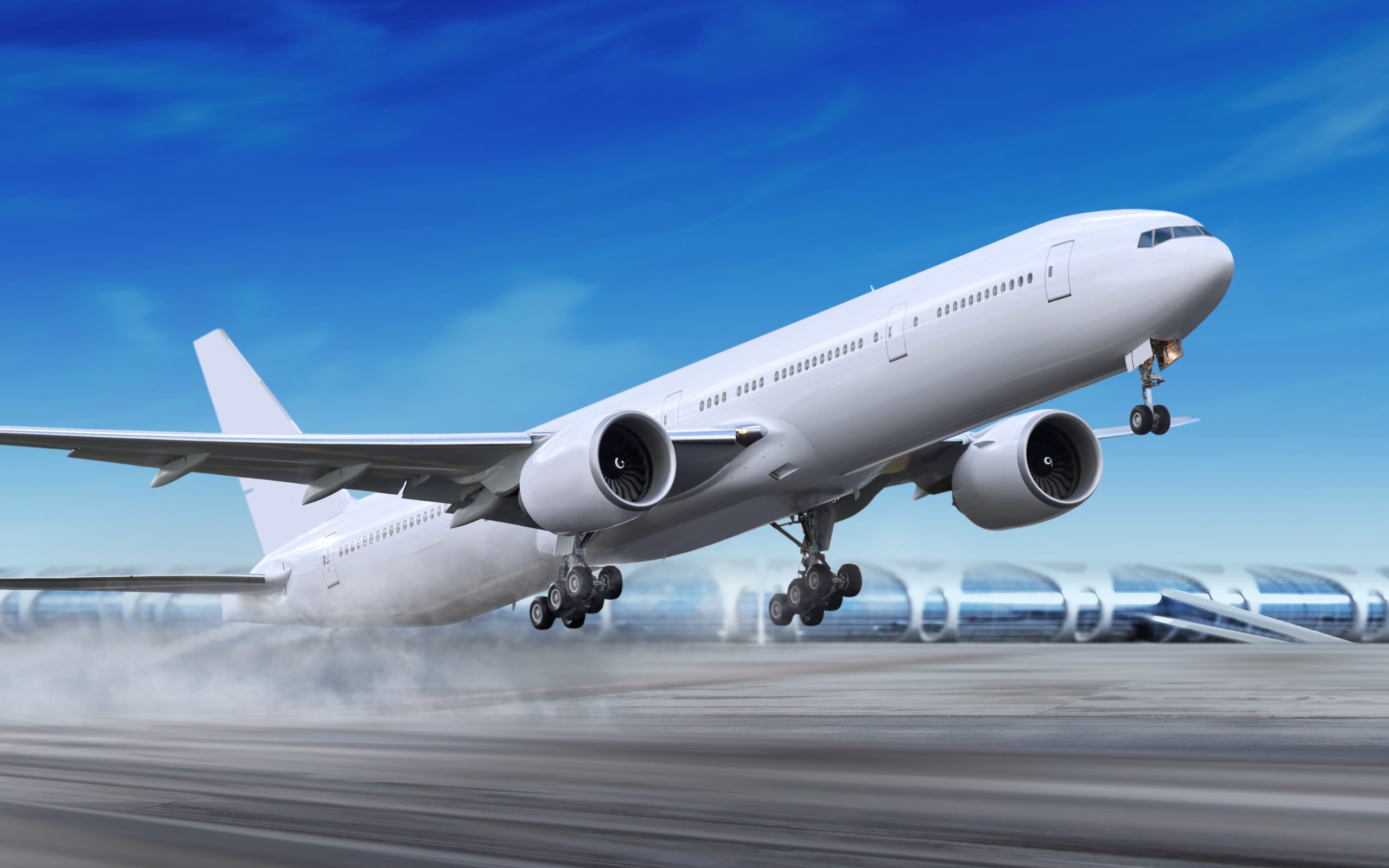
Anti-oxidation-treated aircraft fuselage
Surface finishing methods for plastics
Plastic surface characteristics and processing requirements
Common plastic materials include ABS, nylon, polypropylene, and polyethylene. The surface of plastic is relatively soft and susceptible to mechanical damage or chemical erosion, so high temperature or excessive friction should be avoided.
Common finishing methods
- Low-temperature deburring: Use a low-temperature environment to harden plastics, remove excess burrs, and ensure the accuracy of parts. It is often used for injection molded parts. Low-temperature deburring can effectively prevent the material from deforming due to heat.
- Sandblasting: Mild sandblasting can be used to roughen the surface of plastics to improve subsequent coating or bonding. By selecting appropriate sandblasting materials, the adhesion of the plastic surface can be optimized.
- Chemical treatment: By using chemical solvents to treat the surface, the adhesion of plastics is enhanced. It is common in plastic parts that need to be sprayed or plated. Chemical treatment can effectively improve surface properties, but the amount of chemical agents used must be carefully controlled.
Application scenarios
- Electronic product shells: such as mobile phone and laptop shell processing, pursuing high gloss and comfortable feel. The application of surface finishing technology makes the shell of electronic products beautiful and durable.
- Medical devices: The finishing of surgical instruments and shells must be smooth and flawless, sterile and easy to clean. For medical devices, strict standards for surface finishing are the key to ensuring safety and hygiene.
- Automotive interior parts: Such as door handles and dashboards, which require wear resistance and durability while maintaining beauty. The finishing of automotive interiors not only improves the riding experience but also enhances the market competitiveness of products.
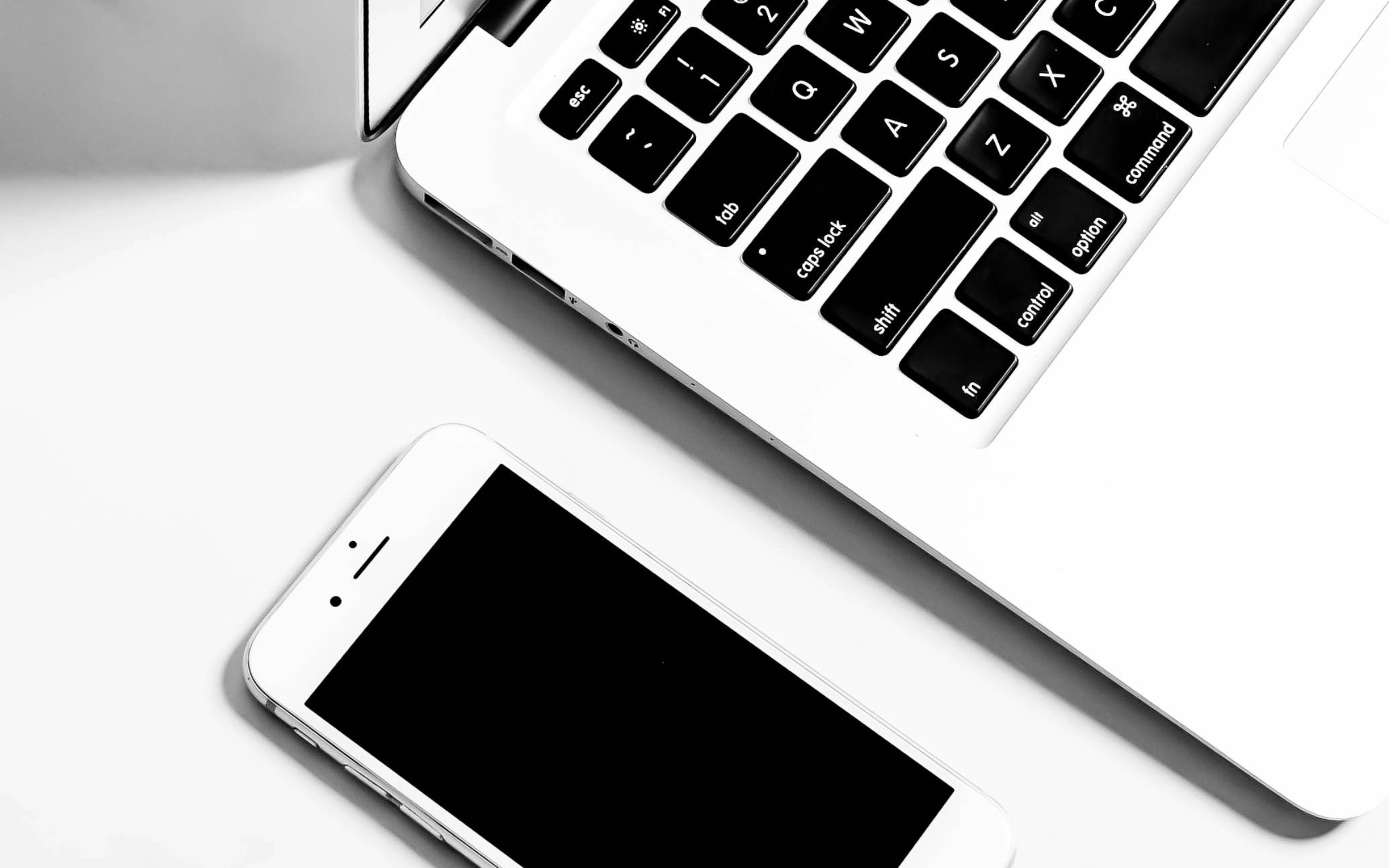
Electronic product shell
Surface finishing methods of glass
Glass surface characteristics and processing requirements
Common types of glass include ordinary flat glass, tempered glass, and low-iron glass. Glass has high hardness but high brittleness. Its fragile nature requires that the integrity and smoothness of the surface be ensured during finishing while avoiding cracks and scratches.
Common finishing methods
- Sandblasting and etching: used for processing customized patterns or logos, widely used in architectural decoration, artwork processing, etc. Sandblasting and etching can achieve delicate pattern effects and enhance the artistic value of glass products.
- Chemical polishing: Chemical solvents are used to remove surface defects, improve transparency and surface smoothness, and are commonly used in optical glass. Chemical polishing is an effective means to improve the quality of optical glass.
- Physical polishing: Mechanical means are used to finely polish the glass surface to achieve a mirror effect. Physical polishing is widely used in high-end glass products to ensure the optical performance of the product.
Application scenarios
- Architectural glass: Such as windows and partition glass, often requires scratch-resistant surface treatment and maintain transparency. The finishing of architectural glass directly affects the beauty and performance of the building.
- Automotive glass: Windshields and windows require impact and scratch resistance to ensure driving safety. The finishing of automotive glass ensures driving safety and passenger comfort.
- Decorative art glass: In interior design or architectural decoration, glass etching is used to achieve customized decorative effects. The finished art glass not only enhances the uniqueness of the design but also adds a romantic atmosphere to the space.
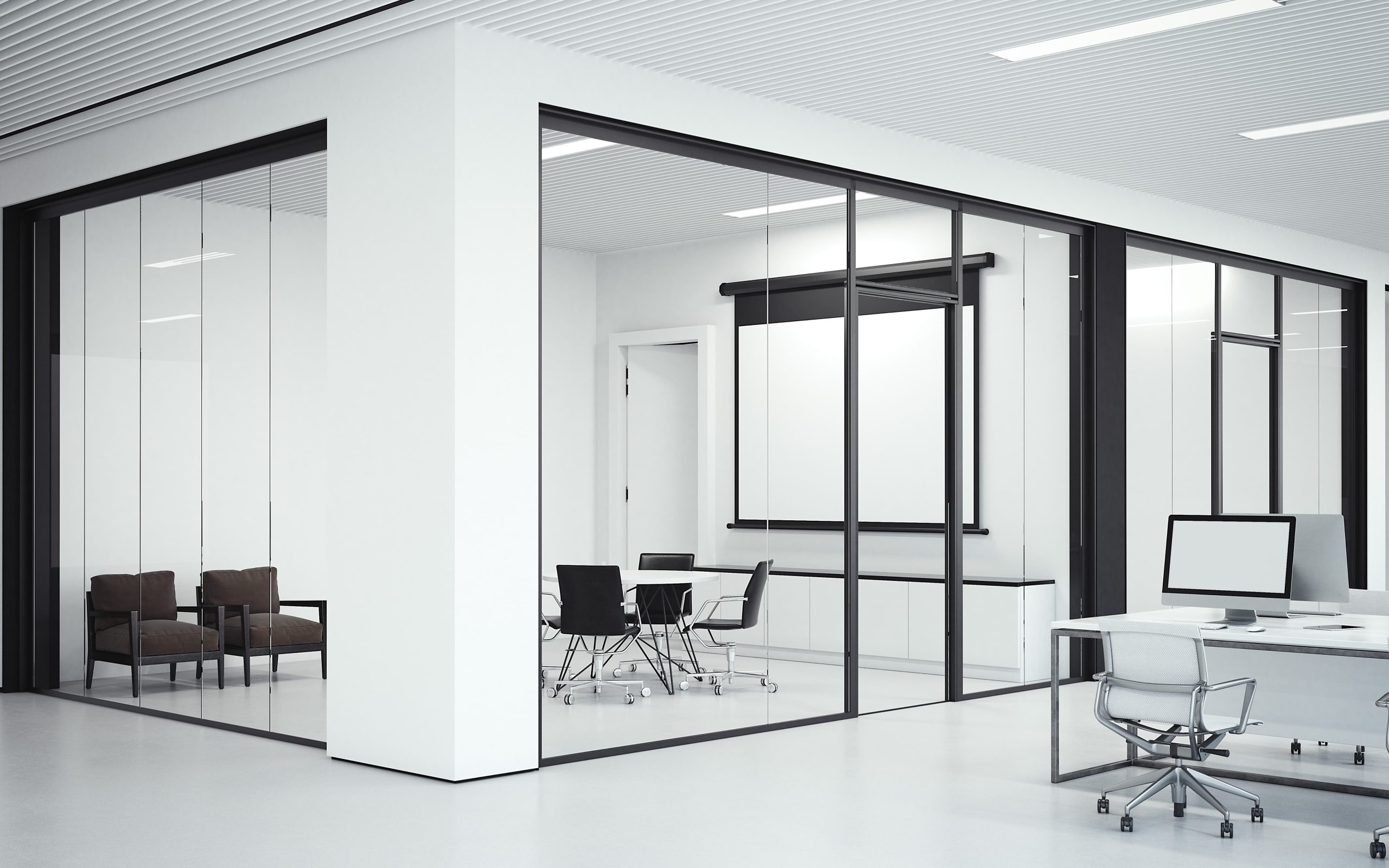
Partition glass
Material selection in surface finishing
Different sandblasting materials are suitable for different substrates and processing requirements. The following are four common sandblasting materials: ceramic beads, glass beads, aluminum oxide, and plastic abrasives.
- Ceramic beads
Ceramic beads are a high-performance sandblasting medium, usually made from bauxite sintered at high temperatures. They are hard and wear-resistant and are suitable for deburring, polishing, and cleaning metal surfaces.
The main advantage is that their uniform particle size can effectively improve the smoothness and gloss of the surface. In addition, ceramic beads have a long service life, reducing the cost of frequent replacement.
Ceramic beads are suitable for industries such as aerospace, automobile manufacturing, and mechanical processing that have particularly strict requirements for surface treatment.
- Glass beads
Glass beads are a relatively soft sandblasting material, mainly made from recycled glass after grinding. Its characteristics make it excellent in polishing and surface smoothing, and it is suitable for fine processing of metal, plastic, and glass surfaces.
The advantage of glass beads is that they can effectively remove surface dirt and oxide layers while maintaining surface finish. Especially in the processing of electronic product housings and decorative glass, the use of glass beads can significantly improve the appearance and quality of the product. In addition, glass beads cause less damage to the substrate during sandblasting, which is suitable for the processing of delicate and sensitive materials.
- Aluminum Oxide
Aluminum oxide is a high-hardness sandblasting material that is usually used for rougher surface treatment. Its excellent cutting performance makes it an ideal choice for removing rust, oxides, and other surface defects.
Aluminum oxide is widely used in metal processing, automotive repair, and construction industries. Due to its strong wear resistance and long service life, aluminum oxide can reduce operating costs in the long run.
- Plastic Abrasive
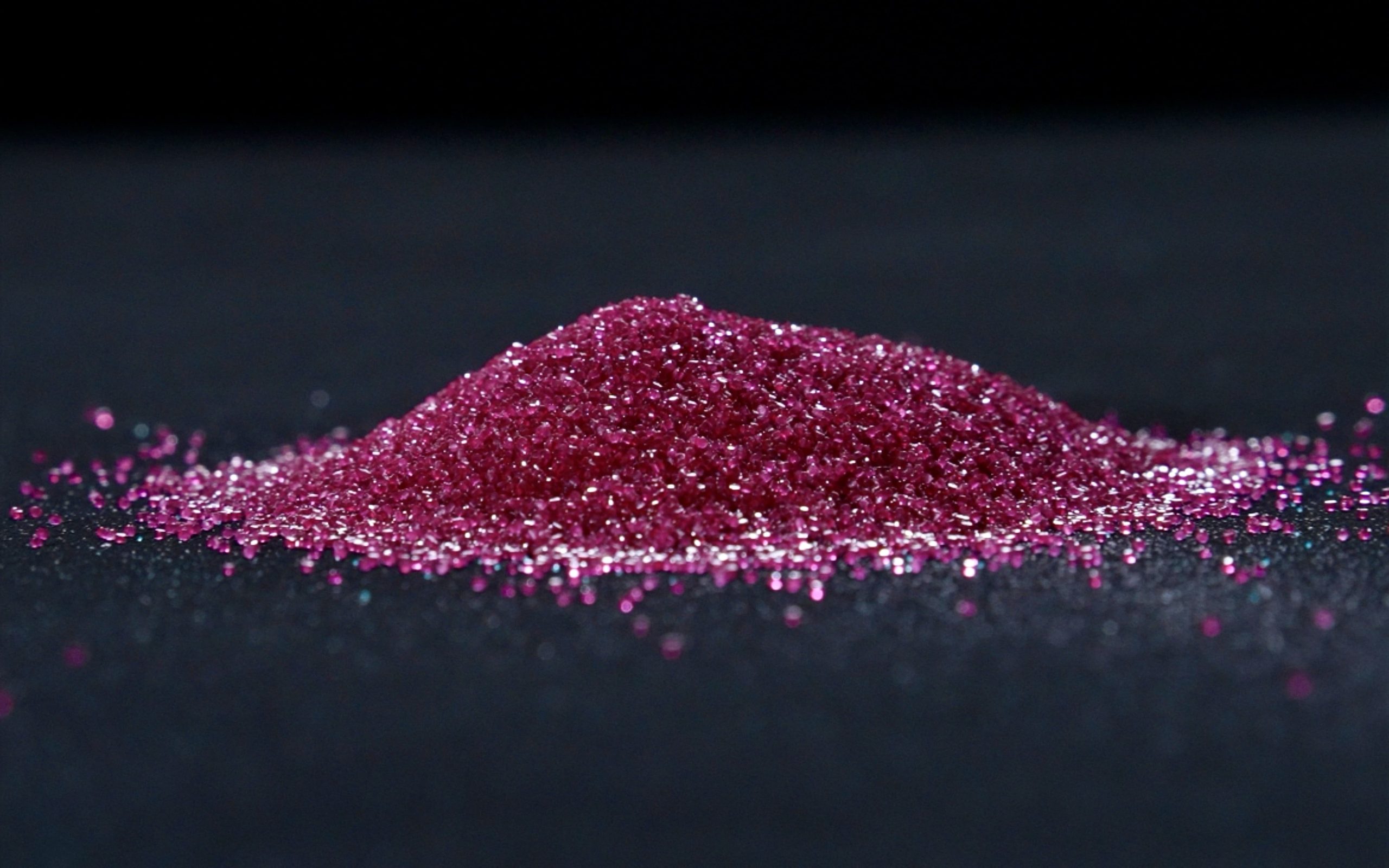
Plastic media-nylon sand
Plastic abrasive is a relatively new sandblasting material. It is economical, lightweight, non-toxic, and has minimal damage to the substrate during the sandblasting process. It is particularly common in the processing of medical devices, electronic products, and automotive accessories because it can ensure the accuracy and beauty of the finished product.
Plastic abrasive is suitable for the surface treatment of materials such as plastics, aluminum alloys, and stainless steel. It can effectively remove surface burrs and impurities while maintaining the original characteristics of the material.
As mentioned above, surface finishing plays a vital role in modern manufacturing. Whether it is metal, plastic, or glass materials, it can be improved through this process. Its appearance and functionality. With the help of sandblasting media such as aluminum oxide and ceramic sand, not only can precise surface treatment be achieved, but also significant effects can be achieved in rust removal, descaling, and coating removal. In the future, with the continuous advancement of surface treatment technology and the diversified demand for materials, the selection and application of sandblasting media will become more sophisticated and extensive, further promoting the innovation and development of various industries.
Filters