Polishing Comparison – Ceramic Beads and Glass Beads
December 17, 2024
Surface finishing is an indispensable part of modern manufacturing, aiming to treat the surface of workpieces to achieve specific smoothness, aesthetics, and functional requirements. This process not only improves the appearance of the product but also plays a key role in functionality, such as:
- Improve wear resistance
- Enhance corrosion resistance
- Improve part matching
Performance comparison between ceramic beads and glass beads
In the above classification of polishing media, ceramic polishing beads and glass beads belong to non-metallic polishing media. In surface finishing, the performance difference of the media directly affects the final processing effect. This article will conduct a detailed comparative analysis of ceramic blasting beads and glass beads from five dimensions: hardness and density, polishing effect, service life, environmental protection, and cost efficiency.
Hardness and density
Key factors that determine the performance of polishing media. Directly affect processing efficiency, polishing depth, and applicable materials.
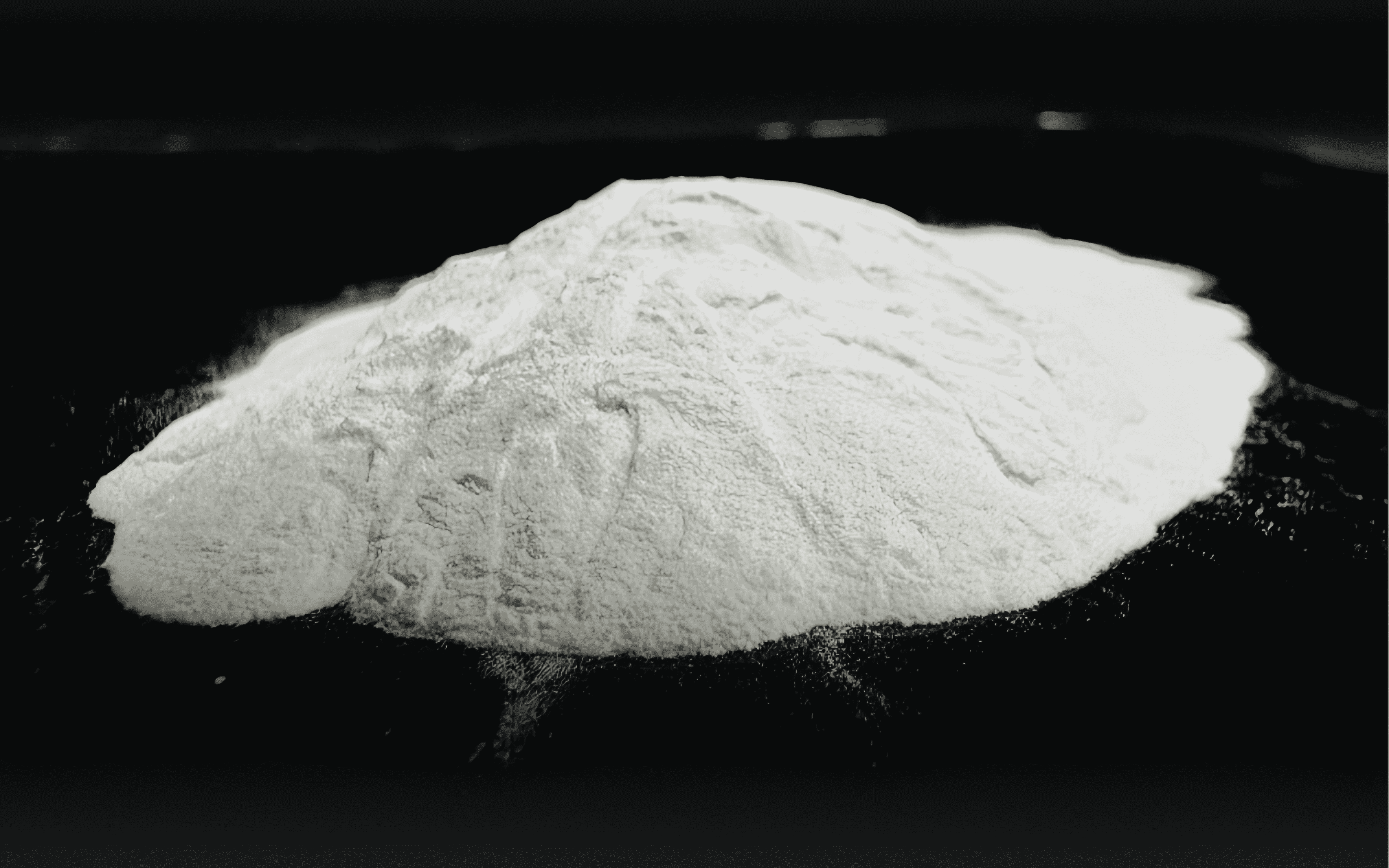
Ceramic beads:
- Hardness: Mohs hardness can reach 7~8.5, close to the hardness level of corundum (aluminum oxide), and performs well in processing high-hardness materials (such as stainless steel and titanium alloy).
- Density: About 3.8~4.0 g/cm³, about 30%-40% higher than glass beads. High density means that ceramic blasting beads have a greater impact when spraying, which can achieve deeper surface polishing and deburring.
Glass beads:
- Hardness: The Mohs hardness of glass beads is generally between 5.5 and 6.0, which limits its applicability on high-hardness materials.
- Density: About 2.4~2.6 g/cm³. The lower density makes its impact force smaller, suitable for light polishing and cleaning.
Polishing effect and precision
The polishing effect is an important indicator for evaluating the performance of the medium, which is mainly reflected in the surface finish, polishing depth, and processing consistency.
Ceramic beads:
- Due to its high density and hardness, it can achieve deep surface finishing, remove micro-concave and convex, and make the surface smoother.
- Uniform spherical particles can ensure the consistency of surface treatment during the polishing process and avoid local excessive wear or insufficient wear.
- Especially suitable for workpieces that require high-precision surface treatment.
Glass beads:
- Suitable for light polishing with low surface requirements to remove surface dirt and oxide layer.
- Due to its low hardness and density, it is difficult for glass beads to achieve deep surface treatment, and the treatment effect is not as good as ceramic blasting beads in terms of precision and finish.
Service life and stability
The service life of polishing media directly affects production costs and work efficiency.
Ceramic beads:
- It has high wear resistance and can maintain stable performance even after long-term use. According to actual usage data, the service life of ceramic blasting beads is usually 2~3 times that of glass beads.
- During repeated use, the particle morphology and polishing effect remain stable and do not need to be replaced frequently.
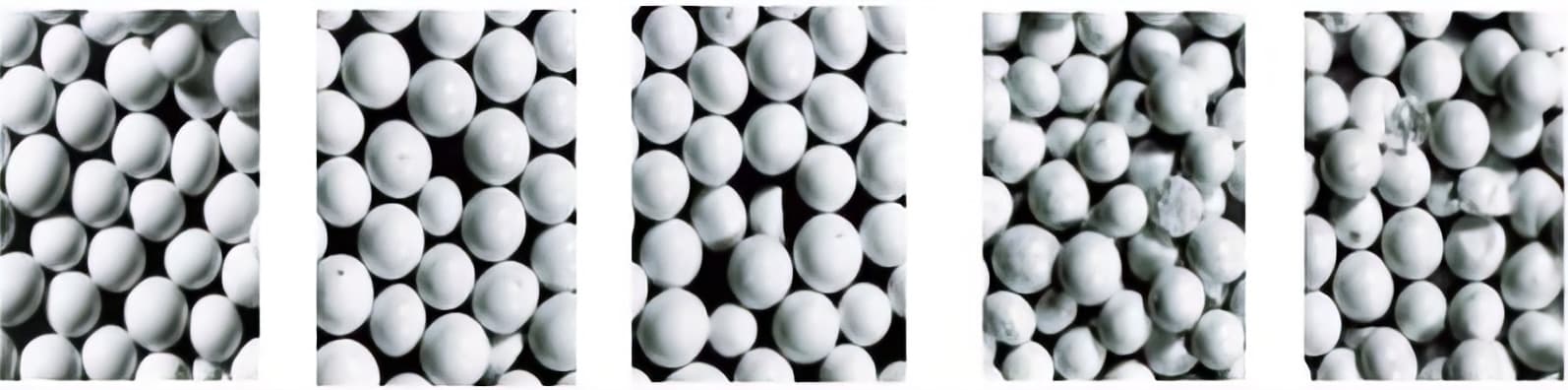
Glass beads:
- Glass beads are easy to break during use, especially when handling high-hardness workpieces, the breakage rate is higher.
- The service life is relatively short and materials need to be replenished frequently.
Environmental protection and dust emission
Environmental protection is increasingly valued in modern manufacturing, and low dust emission and sustainability have become important factors in selecting polishing media.
Ceramic beads:
- The amount of dust generated is extremely low, which helps to improve the working environment.
- Due to its stability and long life, ceramic polishing beads can be recycled and reused repeatedly to reduce material waste.
Glass beads:
- Glass beads are fragile and easily generate a lot of dust during use.
- Broken particles are difficult to recycle, which increases the pressure on solid waste treatment.
Cost efficiency
Cost is one of the important factors affecting the selection, and it is necessary to comprehensively consider the material price, service life, and operating efficiency.
Ceramic beads:
- The unit price of ceramic blasting beads is high, and the initial cost is high.
- In high-demand processing, ceramic blasting beads can reduce the frequency of replacement, improve production efficiency, and reduce long-term operating costs.
Glass beads:
- Low initial cost, suitable for production needs with limited budgets.
- Because glass beads are fragile and have a short life, they need to be replaced frequently, and the long-term use cost is high.
Summary
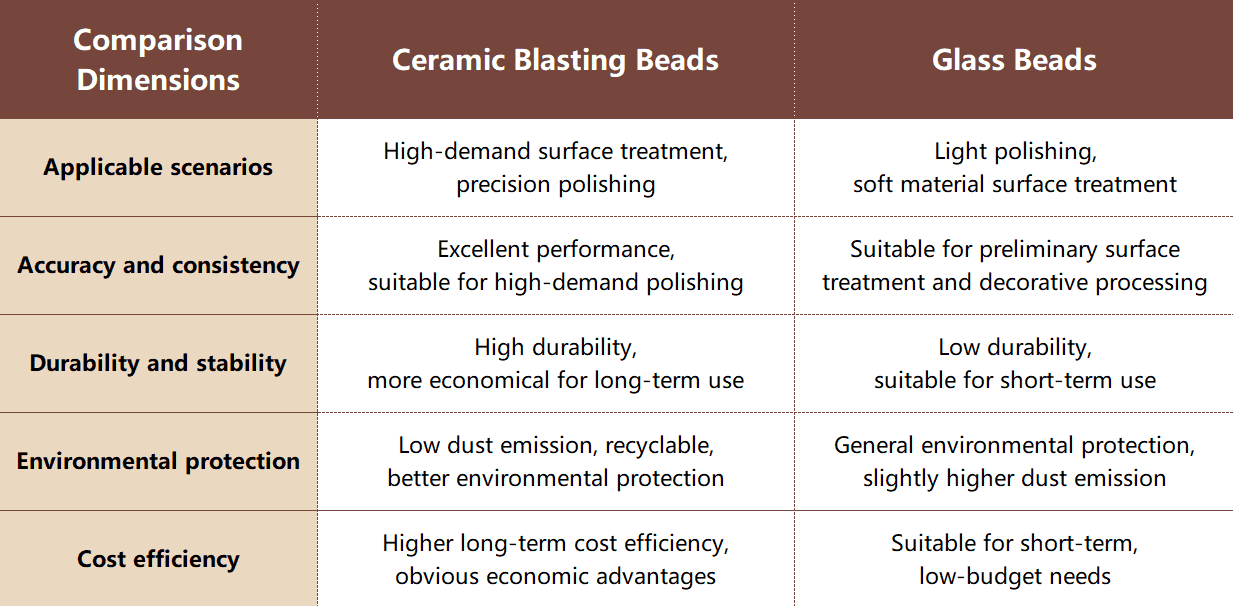
- Ceramic beads: Due to its high hardness and high density, it is suitable for high-demand, deep-level surface finishing scenes. Its uniform spherical particles make the surface treatment more consistent and reduce micro-damage, and are widely used in high-end metals (such as stainless steel, and titanium alloy) and composite material processing.
- Glass beads: The hardness and density are relatively low, and it is mainly suitable for light polishing and surface cleaning. Although the treatment effect is not as deep as that of Ceramic beads, its economic practicality and wide applicability make it widely used in light industry and general decorative processing.
Practical application and case analysis
Ceramic polishing beads and glass beads have their characteristics in the field of surface finishing, and different application scenarios have different requirements for the selection of polishing media. This section will combine actual industry cases to explore the application performance of both in high-end metal processing, non-metallic surface treatment, and specific fields.
High-end metal processing: deep polishing advantages of Ceramic beads
In the field of high-strength and high-precision high-end metal surface treatment, such as stainless steel, aluminum alloy, and titanium alloy processing, the requirements for surface finish and consistency are extremely high. Ceramic blasting beads have become a more ideal choice with their deep polishing effect and consistency advantages.
Application scenarios:
- Stainless steel kitchenware and decorative panels:
Stainless steel products are widely used in modern home and architectural decoration, and the surface needs to have good gloss and flatness. Ceramic blasting beads can remove tiny surface defects with high hardness and uniform spherical particles, achieve a mirror-like smooth effect, and meet the high standards of decorative polishing.
- Aluminum alloy parts:
In the automotive and electronics manufacturing industries, aluminum alloy parts often need to be deburred and surface optimized. Ceramic polishing beads can achieve fine polishing without damaging the surface of the material, which helps to improve the functionality and appearance quality of parts.
Case:
After a high-end stainless steel kitchenware manufacturer introduced ceramic polishing beads for surface polishing, its production efficiency increased by 25% and the surface defect rate decreased by 30%.
Compared with glass beads, the stability of ceramic blasting beads in high-strength workpiece processing has been fully verified.
Non-metallic surface treatment: light polishing performance of glass beads
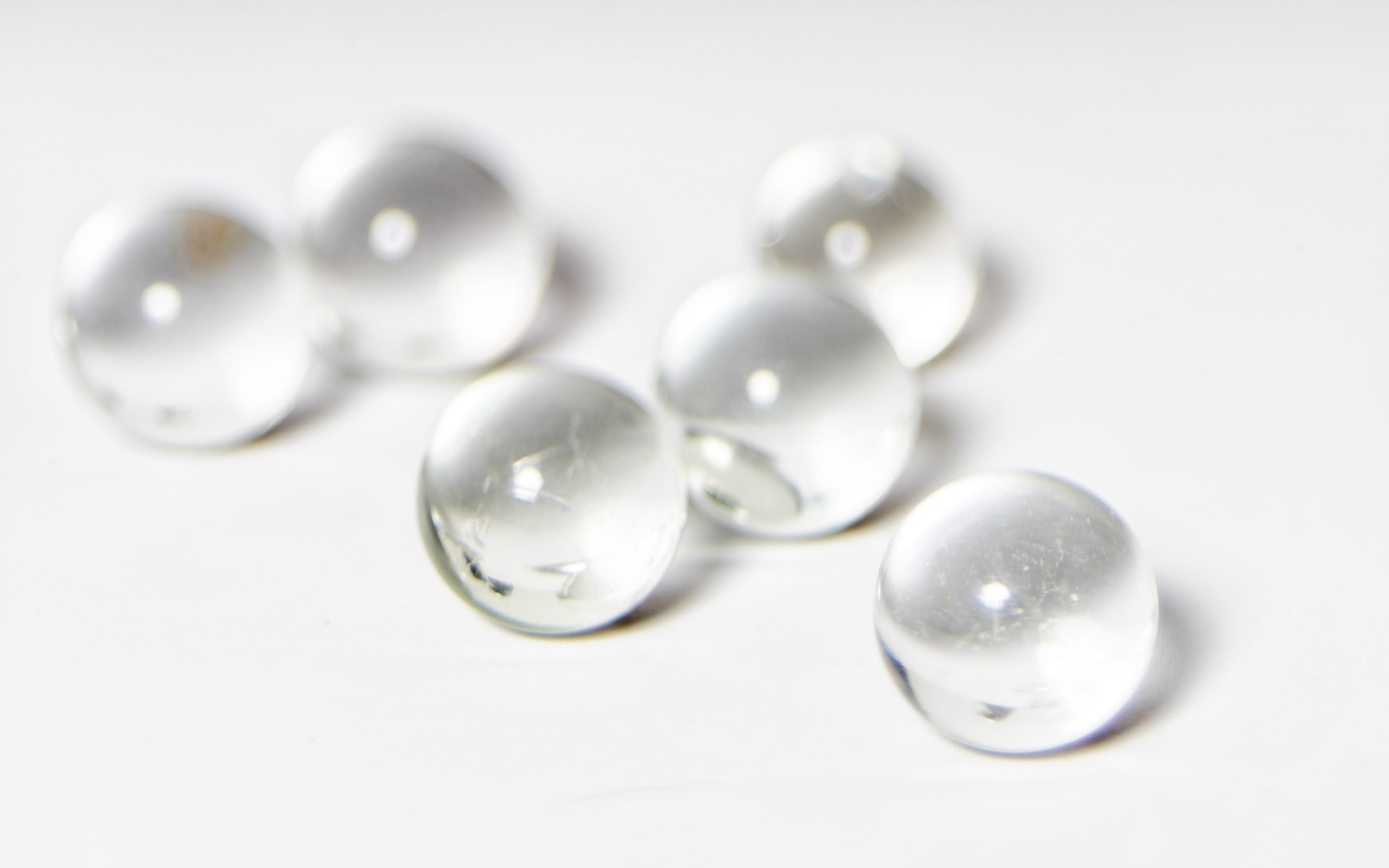
For non-metallic light polishing and cleaning applications such as plastics and composite materials, glass beads have more obvious advantages due to their lower hardness and gentle impact force, which can not only meet the processing needs but also effectively control costs.
Application scenarios:
- Plastic mold cleaning:
Plastic molds are prone to accumulate dirt and mold-release agent residues during long-term use. The low hardness of glass beads enables them to clean dirt without damaging the mold surface, thereby extending the service life of the mold.
- Composite material deburring:
In the aerospace and automotive fields, composite structural parts often need to be deburred. Glass beads can effectively remove slight burrs on the surface and avoid material damage due to excessive polishing.
Case:
A composite material manufacturer successfully reduced the material scrap rate by 15% and the overall cost of the polishing process by 10% after using glass beads for surface treatment.
Aerospace field: Precision processing of Ceramic beads
The aerospace field has extremely strict requirements on the accuracy and consistency of the surface of parts. Ceramic blasting beads perform well in this field and are the best choice for high-precision surface treatment.
Application scenarios:
- Polishing of titanium alloy parts:
Titanium alloy is widely used in the aerospace field due to its high strength and lightweight characteristics. However, its surface treatment is difficult. Ceramic polishing beads can achieve fine polishing and microstructure optimization while ensuring the integrity of the material.
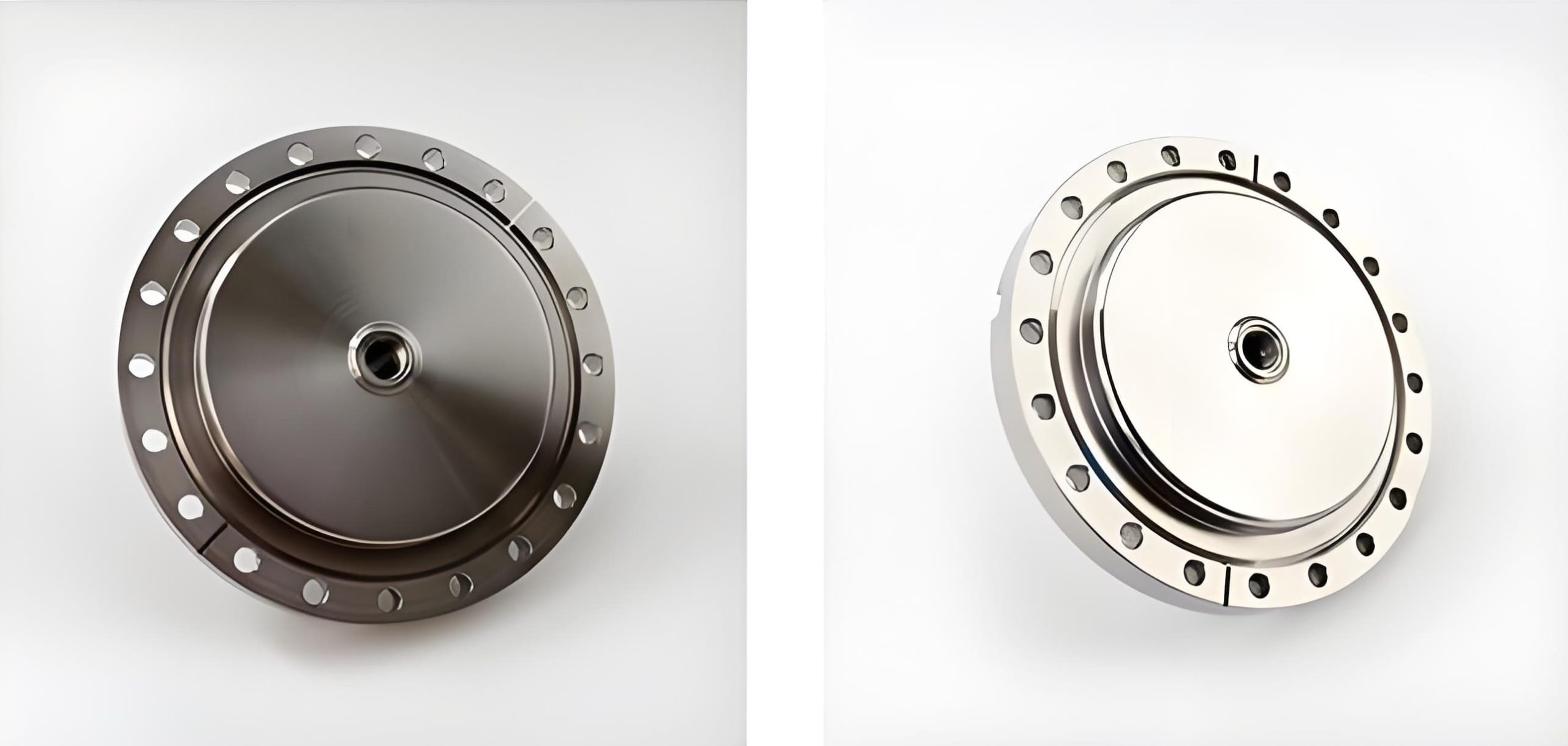
- Deburring of engine blades:
Engine blades need to have an extremely high finish to reduce air resistance. Ceramic blasting beads can effectively remove micro burrs on the blade surface and improve processing accuracy with their uniform spherical particles.
Case:
After an aircraft engine manufacturer introduced ceramic polishing beads for blade surface treatment, the polishing efficiency increased by 20%, and the roughness of the blade surface was reduced to Ra 0.2μm, meeting strict quality standards.
Medical device field: combined application of ceramic beads and glass beads
The surface treatment of medical devices needs to take into account both the polishing effect and material safety. Ceramic blasting beads and glass beads are often used in combination to achieve a perfect balance between high precision and gentle processing.
Application scenarios:
- Polishing of surgical instruments:
Surgical instruments (such as scalpels and forceps) have extremely high requirements for surface smoothness to ensure operational accuracy and safety. Ceramic polishing beads can achieve deep polishing and remove microscopic surface defects.
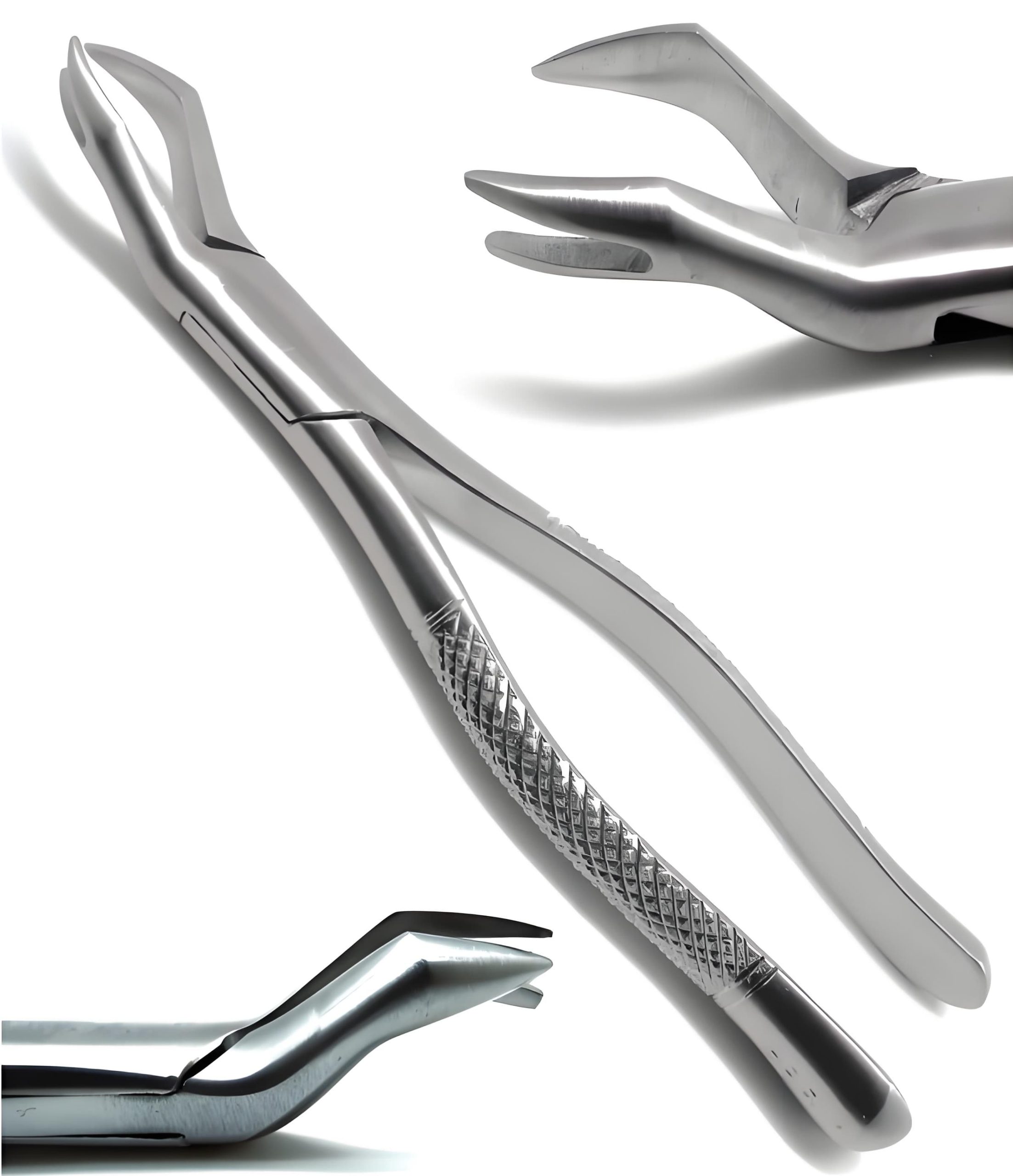
- Deburring of injection molded medical parts:
Medical injection molded parts (such as catheter connectors) are prone to burrs during the production process. Glass beads can be used for light polishing to ensure that the surface is burr-free while ensuring the integrity of the material.
Case:
A medical device manufacturer uses a combination of ceramic polishing beads and glass beads to successfully improve the surface finish of the product and reduce the surface defect rate by 40%, meeting strict medical safety standards.
How to choose a suitable polishing medium?
Ceramic blasting beads and glass beads each have their advantages. When choosing, factors such as material properties, processing goals, process costs, and environmental requirements need to be considered. This section will analyze in detail how to choose the appropriate medium under different working conditions.
Select by material type
Workpieces of different materials have different requirements for the hardness and particle size of polishing media.
- Metal workpieces (such as stainless steel, aluminum alloy, titanium alloy):
Metal materials need to withstand a certain impact force during the polishing process. Ceramic blasting beads with higher hardness are more suitable for deep polishing and surface optimization.
- Non-metal workpieces (such as plastics, and composite materials):
For plastic and composite surfaces, glass beads with lower hardness are more suitable. The gentle impact of glass beads can remove minor burrs and dirt while ensuring that the surface of the material is not damaged.
Select according to the processing target
Different surface processing targets determine the selection of polishing media:
- Deburring:
For removing tiny burrs on the surface of the workpiece, the high hardness of ceramic polishing beads can achieve more efficient deburring effect, especially in the processing of complex parts and high-hardness materials, such as aircraft engine parts and medical device parts.
- Improve surface finish:
If the goal is to improve surface smoothness and aesthetics, glass beads can be used for light polishing, while ceramic blasting beads are suitable for deeper polishing with higher requirements.
- Surface cleaning:
In terms of surface dirt removal and mold maintenance, glass beads can avoid secondary damage to the material surface with their gentle impact force, and the effect is better.
Choose according to process cost
Cost is an important consideration for enterprises when choosing polishing media, including material replacement frequency, consumption, and environmental treatment costs.
- Ceramic beads:
Although the initial purchase cost is slightly higher, ceramic blasting beads have a longer service life due to their high hardness and stability, which can reduce the replacement frequency and overall cost in the long run. After a stainless steel processing company used ceramic polishing beads instead of glass beads, the material replacement frequency was reduced by 40%, and the overall polishing cost decreased by 15%.
- Glass beads:
Glass beads have a low purchase cost and are suitable for light polishing and large-scale surface cleaning, but their consumption is large and they need to be replaced frequently, so the long-term cost may be high.
Comprehensive comparison and decision-making suggestions
Combined with the above factors, enterprises can refer to the following decision-making suggestions when choosing ceramic blasting beads and glass beads:
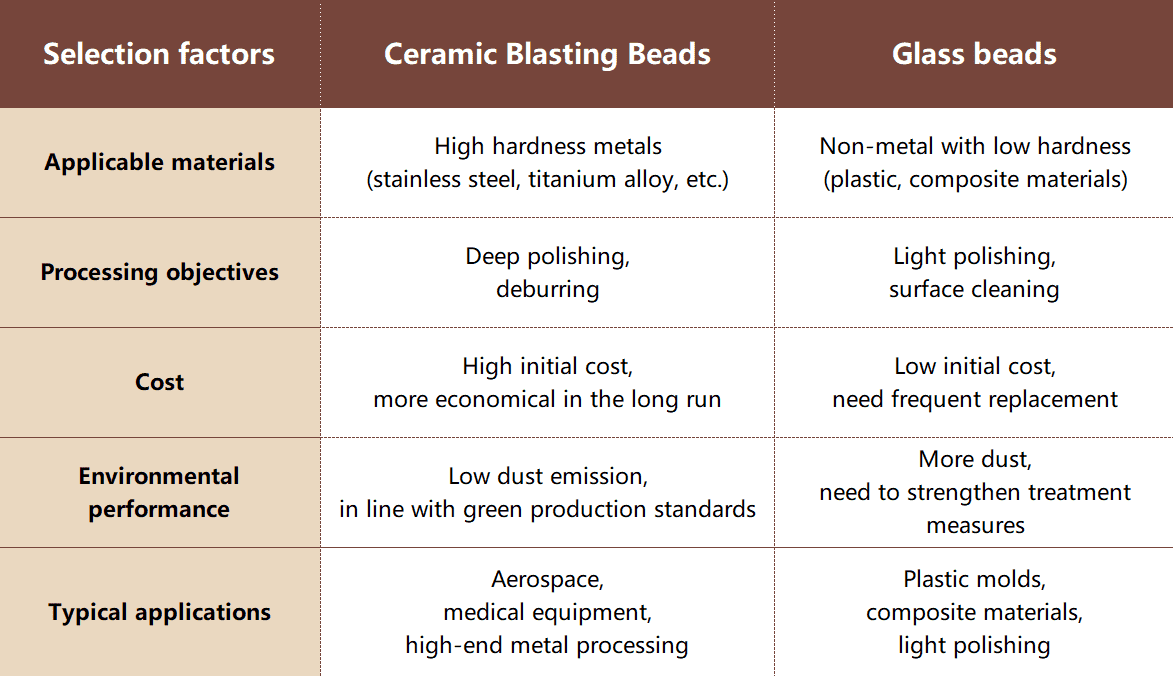
Selection process in actual operation
To help enterprises make better choices, the following is a standardized polishing medium selection process:
- Clarify the workpiece material and polishing target: Determine the material of the object to be processed, the required finish, and the polishing depth.
- Evaluate process requirements: Combine production efficiency, precision requirements, and process stability.
- Cost analysis: Calculate short-term and long-term material costs and consumption.
- Environmental protection and safety review: Confirm that the polishing medium complies with environmental protection regulations and ensures the safety of workers.
- Small batch test verification: Test the polishing effect through actual operation and select the best solution.
Filters