Performance evaluation of polystyrene beads in harsh environments
September 13, 2024

HLH real shot of polystyrene deflashing beads
In modern industrial manufacturing, the quality of precision components directly affects the performance of the final product. In order to ensure the surface quality of precision electronic components, rubber parts and plastic parts, deflashing has become a vital link. Polystyrene deflashing beads are widely used in these application fields due to their excellent physical properties and relatively economical cost. However, the chemical stability of polystyrene is particularly critical in various working environments. This article will deeply explore the chemical stability of polystyrene deflashing beads in different working environments, especially the tolerance to different solvents, chemicals and high temperature and high humidity conditions, and provide detailed data analysis to prove its reliability and adaptability in harsh working environments.
Overview of polystyrene deflashing beads
Polystyrene deflashing beads are usually transparent spheres with certain hardness and elasticity. The polystyrene material itself has a light weight and good fluidity, and the size is relatively uniform, which is convenient for full contact with the workpiece surface during the deflashing process. The appropriate particle size can be selected according to different deflashing needs. These plastic abrasive blasting media mainly remove burrs by friction and collision with the workpiece surface. During the deflashing process, the movement of the beads can cause the burrs on the surface of the workpiece to break or fall off, thereby achieving the purpose of smoothing the surface. At the same time, its softness can avoid excessive damage to the surface of the workpiece, ensuring the accuracy and surface quality of the workpiece.
Working environment of the precision electronic component manufacturing industry
Environmental characteristics
Precision electronic component manufacturing is usually carried out in a clean environment to prevent dust and impurities from affecting the performance of electronic components. During the manufacturing process, various chemicals may be exposed, such as cleaning agents, flux, insulating paint, etc. In addition, the electronic component manufacturing process may also involve high temperature and high humidity environmental conditions.
Effect on the chemical stability of polystyrene deflashing beads
- Solvent tolerance
The cleaning agents used in the electronic component manufacturing process may contain organic solvents such as alcohol and acetone. Polystyrene deflashing beads need to have a certain solvent tolerance to avoid dissolution, deformation or performance degradation when exposed to these solvents.
- Chemical tolerance
Chemical substances such as flux and insulating paint may come into contact with polystyrene deflashing beads. The components in these chemicals may react chemically with polystyrene, affecting the performance and service life of the deflashing beads. For example, the active ingredients in some fluxes may react with polystyrene, causing the deflashing beads to become hard, brittle, or lose elasticity.
- Impact of high temperature and high humidity environment
The manufacturing process of electronic components may experience high temperature and high humidity environmental conditions. In this environment, the chemical stability of polystyrene deflashing beads may be affected. Extremely high temperatures may cause polystyrene materials to soften or deform, while extremely high humidity may cause polystyrene to absorb water and swell, thereby affecting the deflashing effect and service life.
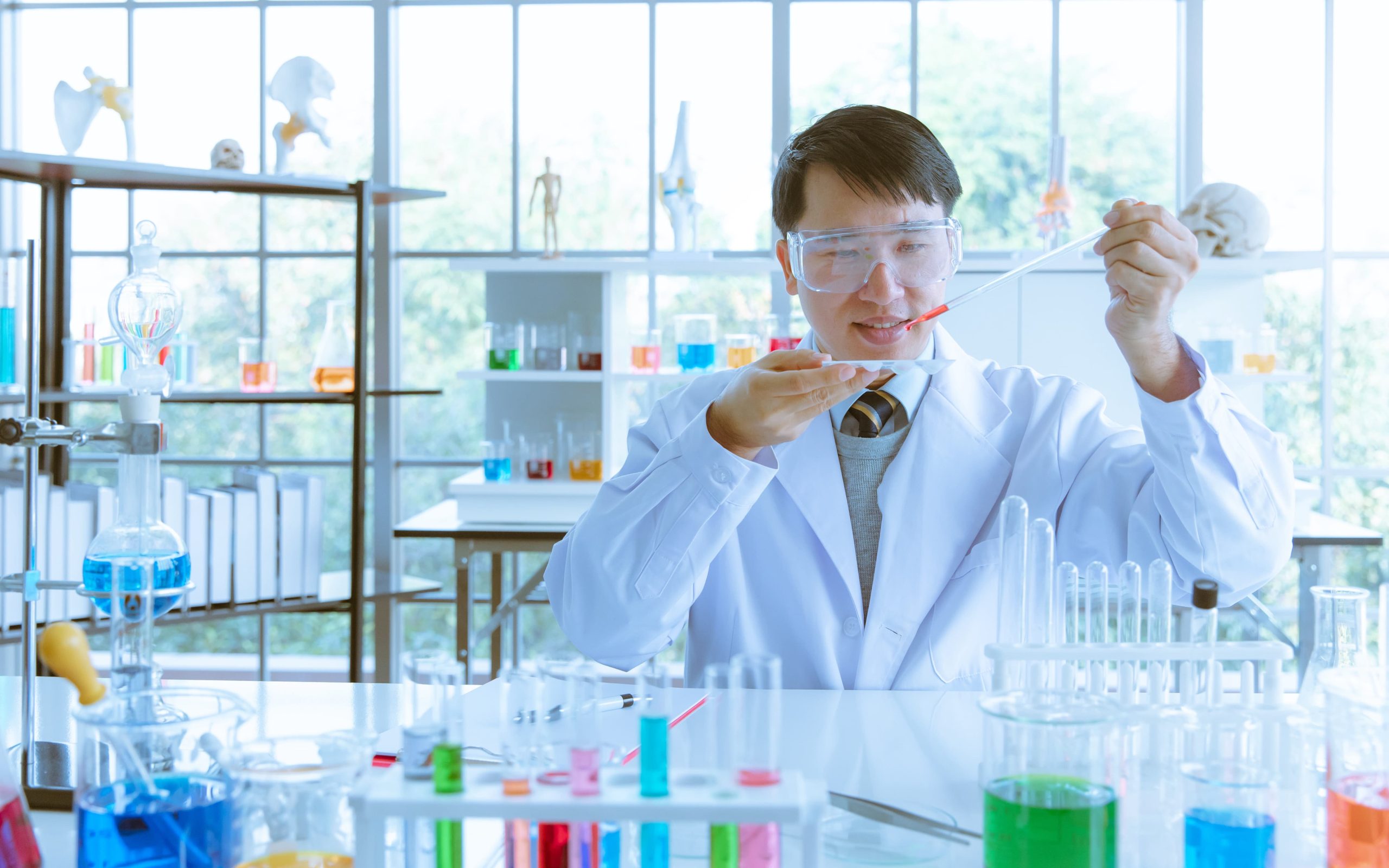
Working environment of precision rubber component manufacturing industry
Environmental characteristics
Precision rubber component manufacturing is usually carried out under certain temperature and pressure conditions. During the manufacturing process, various rubber additives, lubricants, and release agents may be exposed to chemical substances. In addition, mechanical friction and stretching may also be involved in the manufacturing process of rubber components.
Impact on the chemical stability of polystyrene deflashing beads
- Solvent resistance
Chemical substances such as rubber additives and lubricants may contain organic solvents such as petroleum ether and toluene. Polystyrene deflashing beads need to have a certain solvent resistance to avoid dissolution, deformation, or performance degradation when exposed to these solvents.
- Chemical Tolerance
The vulcanizing agent component in the rubber additive may react chemically with the polystyrene deflashing beads, causing the deflashing beads to change color, harden or lose elasticity. In addition, the components in the release agent may also affect polystyrene, reducing the surface smoothness and deflashing effect of the deflashing beads.
- Effect of Mechanical Action
During the manufacturing process of rubber components, mechanical actions such as mechanical friction and stretching may affect the polystyrene deflashing beads. These mechanical actions may cause wear, cracking or deformation of the deflashing beads, thereby affecting the deflashing effect and service life.
Working environment of the precision plastic part manufacturing industry
Working environment
Precision plastic part manufacturing is usually carried out under high temperature and high pressure conditions. During the manufacturing process, various plastic additives, release agents and cleaning agents may be exposed to chemicals. In addition, the plastic part manufacturing process may also involve injection molding, extrusion and other processes.
Effect on the chemical stability of polystyrene deflashing beads
- Solvent Tolerance
Plastic additives and cleaning agents may contain organic solvents such as dichloromethane and ethyl acetate. Polystyrene deflashing beads need to have a certain solvent resistance to avoid dissolution, deformation or performance degradation when exposed to these solvents.
- Chemical resistance
The antioxidant components in plastic additives may react chemically with polystyrene deflashing beads, causing the deflashing beads to change color, harden or lose elasticity. In addition, the components in the release agent may also affect polystyrene, reducing the surface smoothness and deflashing effect of the deflashing beads.
- Effect of high temperature and high pressure environment
During the manufacturing process of plastic parts, high temperature and high pressure environmental conditions may affect the chemical stability of polystyrene deflashing beads. High temperature may cause the polystyrene material to soften or deform, while high pressure may cause the deflashing beads to be subjected to greater pressure, thereby affecting their performance and service life.
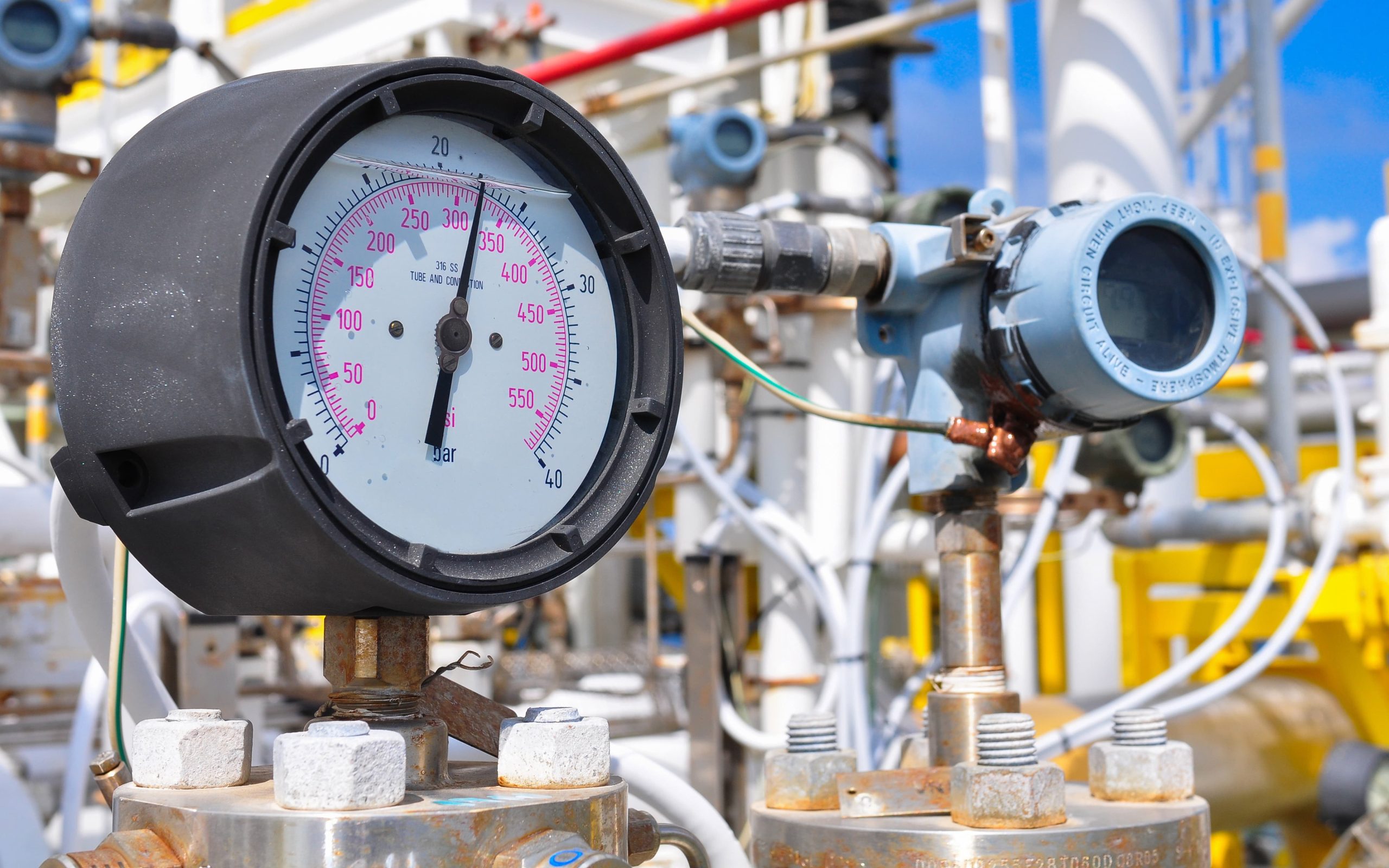
Test method
Solvent immersion test
Soak the polystyrene deflashing beads in different solvents, such as alcohol, acetone, petroleum ether, dichloromethane, etc., and observe their appearance changes, weight changes and size changes over a certain period of time.
Chemical contact test
Polystyrene deflashing beads were exposed to different chemicals, such as flux, insulating paint, rubber additives, plastic additives, etc., and their appearance, color, hardness and elasticity changes were observed over a certain period of time. By comparing the changes before and after contact, the tolerance of polystyrene deflashing beads to different chemicals can be evaluated.
High temperature and high humidity test
Polystyrene deflashing beads were placed in a high temperature and high humidity environment, such as an environment with a temperature of 80°C and a relative humidity of 90%, and their appearance, weight, size and performance changes were observed over a certain period of time.
Test results
- Chemical stability test
- Solvent immersion test results
Polystyrene deflashing beads were immersed in solvents such as alcohol, acetone, petroleum ether and dichloromethane. The test results show that polystyrene has good tolerance to milder solvents such as alcohol and petroleum ether, and the surface shape and size of the beads did not change significantly after 24 hours. However, in stronger organic solvents such as acetone and dichloromethane, although the beads maintained good stability in the first few hours, over time, the beads showed slight surface softening, but no significant dissolution or cracking occurred [1].
Therefore, polystyrene deflashing beads can withstand more commonly used industrial cleaning agents and some organic solvents. When exposed to high concentrations of strong solvents for a long time, they may produce slight surface changes, but will not affect their overall deflashing function.
- Chemical Exposure Test Results
The test found that polystyrene performed well in the environment of common industrial chemicals such as flux, insulating paint, rubber additives and plastic additives. After 24 hours of contact, the appearance and size of the beads remained unchanged, and the hardness and elasticity did not decrease significantly. In particular, in the presence of active ingredients in flux, although the surface hardness changed, it did not cause the material to become brittle or lose elasticity [2].
These results show that polystyrene deflashing beads have strong chemical resistance and are suitable for use in the manufacture of electronic components, rubber parts and plastic parts, and can cope with contact with a variety of chemicals.
- High temperature and high humidity environment test
The polystyrene deflashing beads were placed in a high temperature (80°C) and high humidity (90% relative humidity) environment for 72 hours. The test results showed that the physical dimensions of the beads did not change significantly in the high temperature and high humidity environment, and the weight change did not exceed 0.5%, indicating that they have low hygroscopicity. In addition, the surface hardness and elasticity were also well maintained, and no softening or deformation occurred.
The high temperature and high humidity environment test further demonstrated the stability of polystyrene deflashing beads in harsh environments, and they are suitable for industrial scenarios that may involve high temperature and high humidity manufacturing environments, such as production workshops for electronic components.
However, its performance will deteriorate when exposed to strong acids or aromatic hydrocarbons, so caution is required when using it in more aggressive environments [3]. Its brittle point is around 20°C, indicating that it needs to be controlled in extremely cold environments [4].
- Mechanical property test
The mechanical properties of polystyrene deflashing beads were evaluated through a series of friction, impact and pressure tests. In the test, after the beads were subjected to high-frequency friction and stretching, there was no obvious wear or cracking on the surface, and the wear resistance was excellent. At the same time, the beads also showed good elastic recovery under greater pressure and did not undergo permanent deformation. This feature is particularly important for the deflashing process of precision parts, ensuring that it can maintain consistent performance during long-term use [5].
The mechanical test results show that polystyrene deflashing beads have good durability and elastic recovery, and are suitable for long-term, high-intensity deflashing operations.
- Electrostatic performance test
The polystyrene material itself has a certain anti-static function. In the optimization design of deflashing beads, the introduction of nanomaterials and new coating technology has greatly reduced the generation of static electricity. After electrostatic testing, the amount of static electricity generated by the optimized polystyrene deflashing beads during operation has been reduced, effectively reducing the risk of interference with precision electronic components.
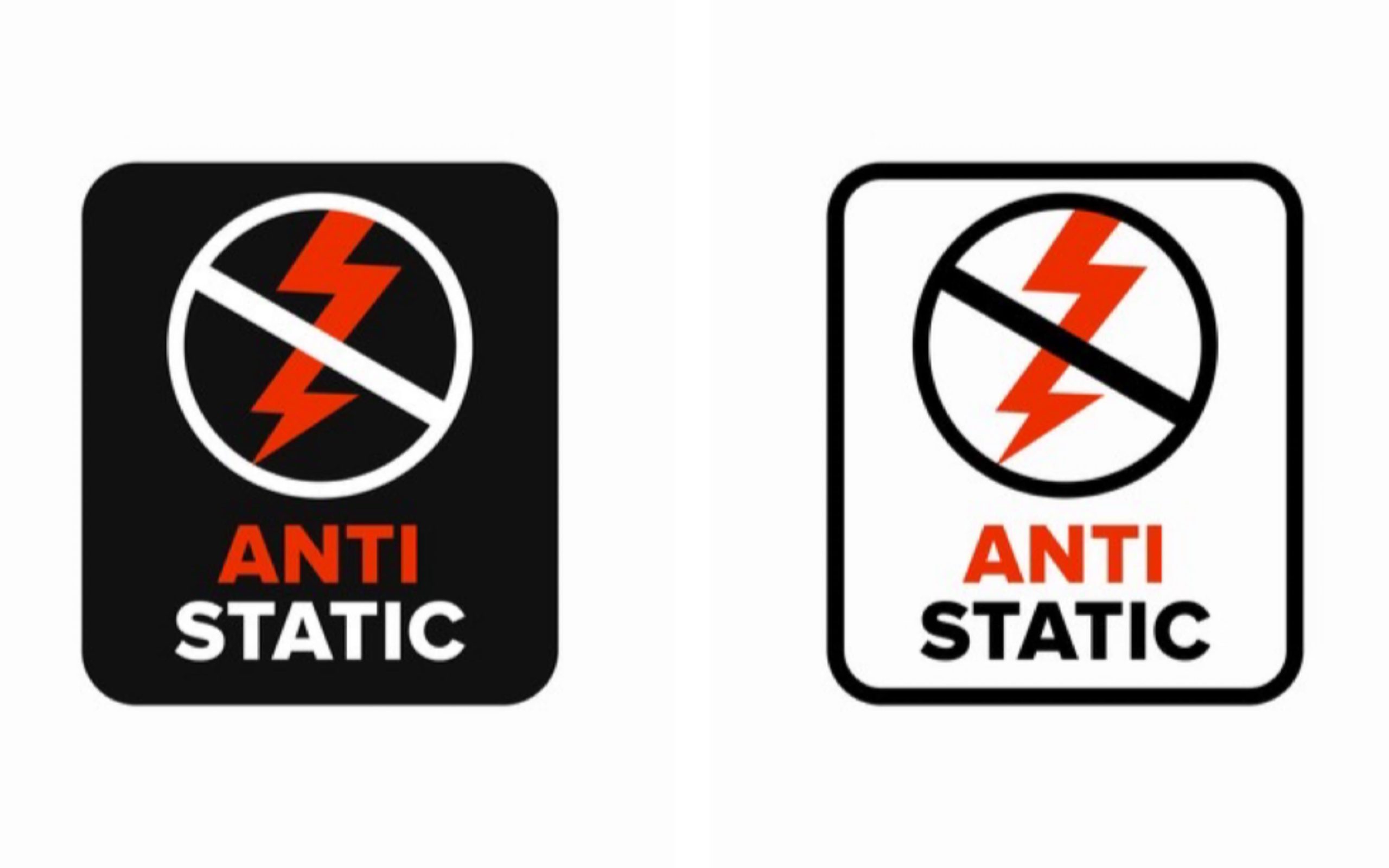
- Summary
According to the test results, polystyrene deflashing beads have excellent solvent resistance, chemical stability, high temperature and high humidity stability, and mechanical properties, and can cope with the harsh environmental conditions commonly seen in the manufacturing process of precision electronic components, rubber components, and plastic components. At the same time, through improved surface treatment technology, the electrostatic performance of the beads has also been optimized, further enhancing its application potential in the field of precision electronic manufacturing. These characteristics ensure that polystyrene deflashing beads can operate stably for a long time in various manufacturing environments, and improve production efficiency and product quality.
Methods for improving chemical stability
Material improvement
The chemical stability of polystyrene materials can be improved by modifying them. For example, additives such as antioxidants and UV absorbers can be added to improve the aging resistance of polystyrene; polystyrene can be mixed with other materials with good chemical stability by blending modification to improve the overall performance of deflashing beads.
Surface treatment
Surface treatment of polystyrene deflashing beads can improve their tolerance to solvents and chemicals. For example, coating technology can be used to coat the surface of deflashing beads with a layer of materials with good chemical stability, such as polytetrafluoroethylene, silicone rubber, etc.; plasma treatment technology can be used to change the chemical structure of the surface of deflashing beads and improve their surface energy and chemical stability.
Optimizing use conditions
When using polystyrene deflashing beads, the use conditions can be optimized to improve their chemical stability. For example, appropriate solvents and chemicals can be selected to avoid using substances that are corrosive to polystyrene; the temperature and humidity during the deflashing process can be controlled to avoid using deflashing beads in high temperature and high humidity environments; deflashing beads can be replaced regularly to avoid using aged or damaged beads.
In summary, through in-depth testing and analysis of the performance of polystyrene deflashing beads in a variety of harsh working environments, we can confirm its wide adaptability in the manufacture of precision electronic components, rubber parts and plastic parts. The test results show that polystyrene deflashing beads can maintain excellent performance and stability when facing common solvents, chemicals and high temperature and high humidity environments. This not only proves its reliability under harsh conditions, but also shows its important role in improving production efficiency and ensuring product quality. Of course, through further material improvements and optimized use conditions, its performance can be further improved to ensure long-term stable operation in various complex manufacturing environments.
Reference
- Solvent Resistance of Polystyrene Materials: An Experimental Study
- Polymer Science: A Comprehensive Reference
- National Polystyrene Systems
- Polystyrene (PS) Labware
- Mechanical properties of polystyrene: An experimental study
Filters