October 10, 2024
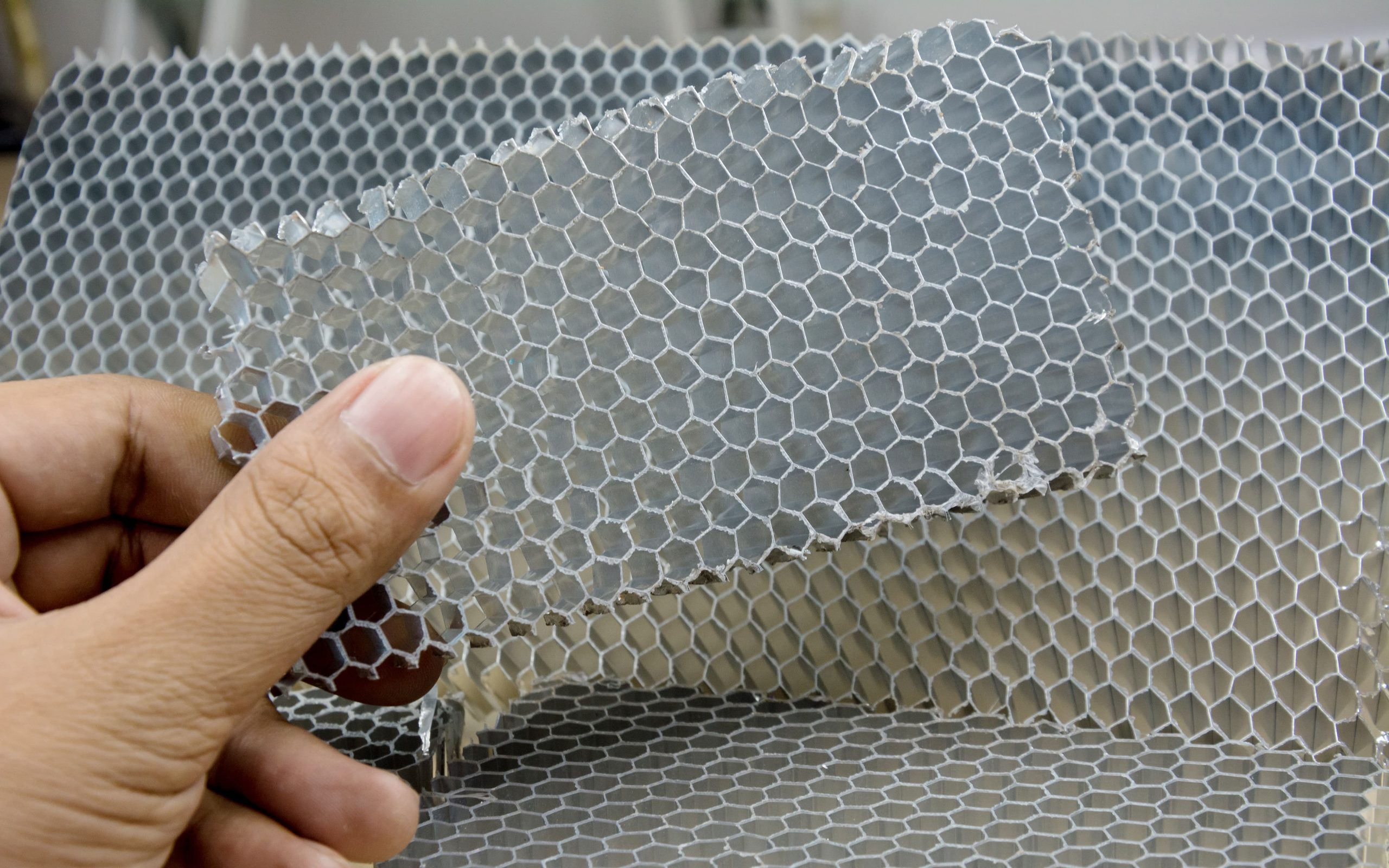
In modern industrial manufacturing, burrs are almost everywhere. Whether through cutting, welding, casting, or molding, burrs will appear on the edge of parts, around holes, or in complex geometric areas. If these small and sharp material residues are not handled in time, they will affect the performance and appearance of the product, and even bring safety hazards. Therefore, the deburring process has become an indispensable step in industrial production.
This article will discuss “Deburring solutions for industrial applications”, starting from different types of burrs, analyzing the importance of deburring, and deeply exploring various deburring methods and corresponding sandblasting media and equipment to help you improve production efficiency and product quality in modern industry.
What is a burr?
A burr is a tiny material residue generated during material processing due to processes such as cutting, punching, casting, or welding. The appearance of burrs may be inevitable, but they have a vital impact on the quality, durability, and safety of the final product. There are many types and forms of burrs, which can be classified into the following main types according to the way they are generated:
- Cutting burrs
Cutting burrs are local deformation or residue of materials caused by friction and shearing between the tool and the material during machining. This type of burr usually occurs in the cutting, drilling, and turning processes of metals, plastics, and composite materials. Cutting burrs are one of the most common types of burrs because this process is widespread in modern manufacturing.
For example, in precision machining, tool wear or improper operation may produce excessive burrs, especially in hard materials. Such burrs are often located at the edge of the workpiece and may interfere with the assembly or further processing of the parts.
- Stamping burrs
Stamping burrs occur during the stamping, shearing, and die-forming processes of metal sheets or other materials. The stamping process itself is to cut or form the material through the pressure of the die, so if the die is worn, the material is too hard or the stamping parameters are set improperly, burrs are easy to appear on the edge.
Stamping burrs are characterized by rough and irregular edges, which affect the assembly accuracy and surface quality of the workpiece. Especially in automobile manufacturing, stamping burrs may cause parts not to fit tightly together, affecting the performance and safety of the vehicle.
- Casting burrs
During the casting process, casting burrs may form at the mold joints due to uneven liquid metal fluidity or excessive mold gaps. Such burrs are generally located at the casting mouth, edges, or corners of complex shapes of the workpiece, and are large and irregular in size.
Casting burrs are particularly common in large metal components, engine blocks, and other products, and need to be processed by grinding or other methods in subsequent processing, otherwise, the durability and surface quality of the parts will be affected.
- Welding burrs
During the welding process, welding burrs may be generated around the weld due to uneven welding current, heat, or improper operation. Such burrs usually appear in the form of small pieces of metal accumulation or welding slag, affecting the appearance and function of the welded parts, and may even harm the welding strength.
Welding burrs are not just cosmetic defects, they may interfere with subsequent surface treatment processes (such as coating or electroplating) and reduce the corrosion resistance of the product.
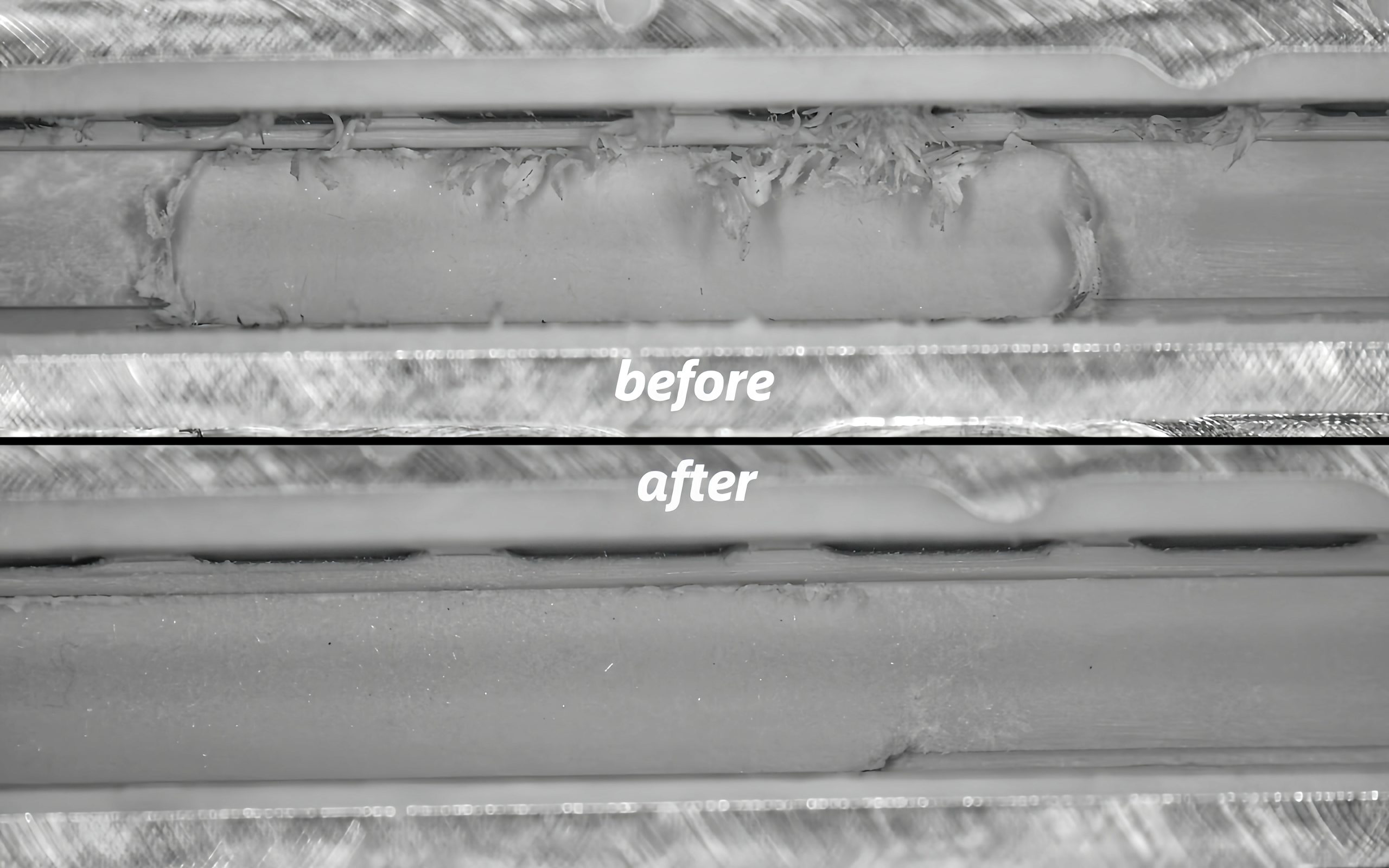
Comparison before and after deburring
Importance of Deburring
Burrs are not just a cosmetic problem; they have a profound impact on the performance, safety, and long-term use of products. Problems that may arise from burrs that are not removed promptly include:
- Safety hazards
The sharp edges of burrs may injure operators, especially during assembly, transportation, or maintenance. For example, sharp metal burrs may cut workers’ fingers, causing accidental injuries. For consumers, hidden burrs in products may also pose potential dangers during use.
- Functional failure
In precision machinery, burrs may cause poor assembly of parts or hinder the normal operation of moving parts. For example, if burrs remain on the turbine blades of aircraft engines, they may cause changes in aerodynamic properties and affect engine performance.
- Shortened product life
Burrs cause stress concentration and increase the risk of fatigue and wear of parts under high load conditions. Especially in metal parts, burr areas are more likely to become the starting point of cracks, ultimately leading to part failure.
- Appearance and quality issues
For some products that require high precision and beauty (such as mobile phone cases or automotive trims), burrs will affect the surface finish and reduce the market competitiveness of products. Especially in high-end consumer products, even small flaws can lead to customer dissatisfaction or complaints.
Cases:
- Aerospace: In aerospace manufacturing, burrs on wings and engine parts can cause uneven air flow, thereby increasing aerodynamic drag or affecting fuel efficiency.
- Medical devices: In implantable devices or minimally invasive surgical instruments, any unremoved burrs may damage patient tissue and increase surgical risks.
Methods of deburring in industrial applications
In different industrial scenarios, apropriate deburring methods need to be selected according to the type of burrs and the material of the workpiece. The following are several common deburring techniques:
- Mechanical deburring
Mechanical deburring is the removal of burrs by mechanical grinding, polishing, or grinding. Common equipment includes grinding wheels, grinders, and brushes. This method is suitable for larger or harder metal parts, especially metal parts in automotive and aviation manufacturing. However, for complex shapes or softer materials, mechanical deburring may not be ideal.
- Chemical deburring
Chemical deburring is the dissolution of burrs on the surface of the material through a specific chemical solution. This method is often used for precision parts with complex shapes or tiny burrs that are difficult to remove mechanically. Chemical deburring is particularly suitable for high-precision parts processing in aerospace and medical equipment.
- Cryogenic deburring
Cryogenic deburring makes the burrs brittle by freezing the material and then removes them by sandblasting or vibration. This method is often used to deburr rubber or plastic parts, especially for small parts with complex shapes. The advantage of cryogenic deburring is that it causes less damage to the surface of the workpiece and maintains the original shape of the workpiece.
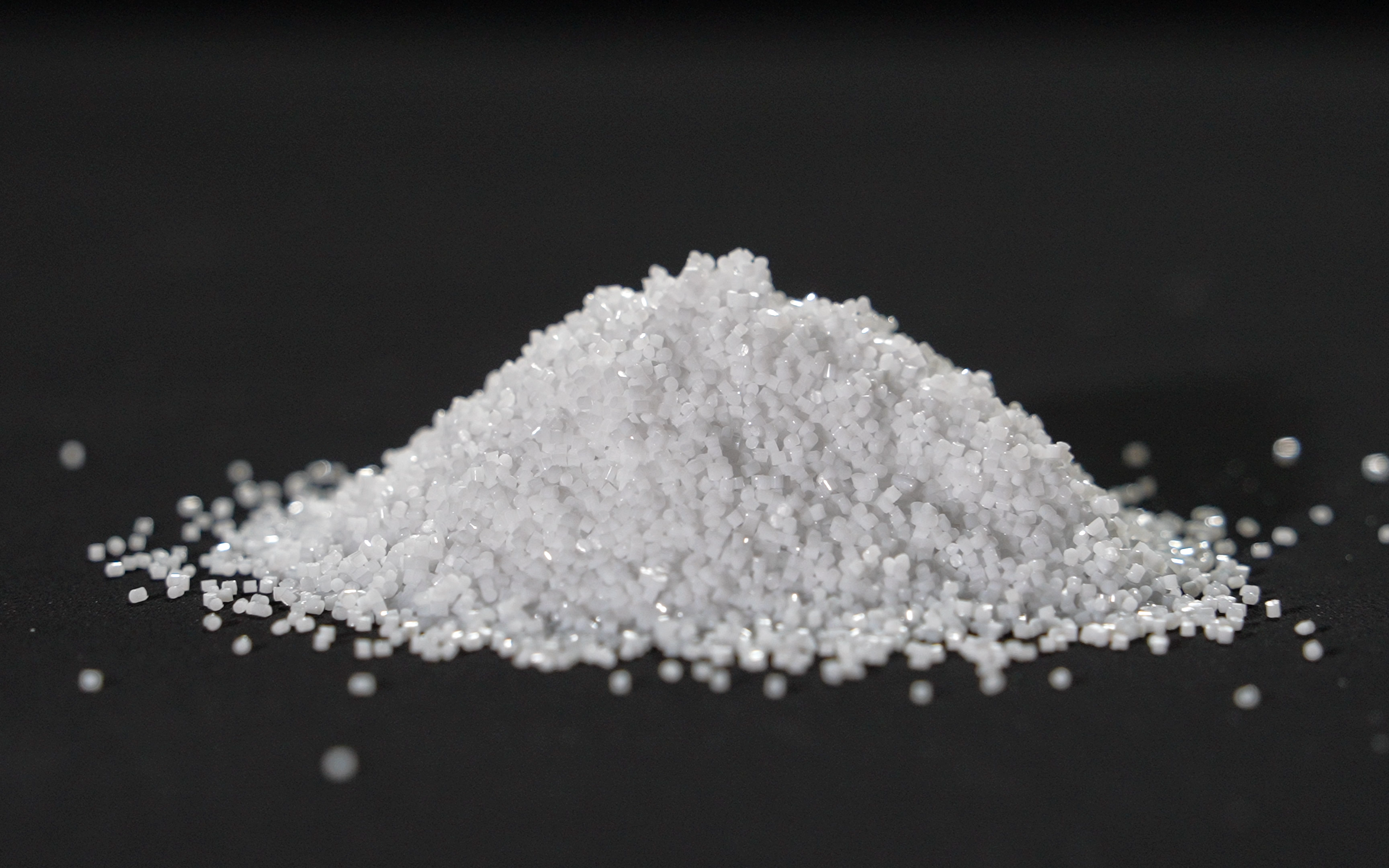
Cryogenic Deflashing Media
- Thermal deburring
Thermal deburring is an effective method for removing metal burrs by rapidly melting or vaporizing the burr area at high temperatures. It is suitable for the processing of metal parts in mass production, with high efficiency, but the equipment cost is high and has a certain impact on the surface quality of some materials.
- Manual deburring
In some scenarios with small batch production or high precision requirements, manual deburring is still an effective way. Workers use knives, files, or fine sandpaper to fine-process the workpiece, which is particularly suitable for deburring certain electronic components or medical devices that require extremely high precision.
Deburring media
In the industrial deburring process, it is crucial to choose the right media. Different media are suitable for different workpiece types and surface treatment requirements according to their material properties and shapes. The following are several common deburring media and their advantages, applicable scenarios, and industrial application cases.
- Basic introduction: Ceramic beads are a high-hardness sandblasting medium, mainly made of ceramic materials such as alumina or zirconia. Due to their high density, strong wear resistance, and high hardness, ceramic beads are often used for deburring, surface strengthening, and cleaning of metal and non-metal parts with high surface finish requirements. Ceramic beads are often used for the processing of precision parts, such as aerospace, automotive parts, and medical devices.
- Advantages:
- High hardness: It can effectively remove burrs on the surface of hard materials, especially suitable for the deburring process of metals and composite materials.
- Strong durability: Ceramic beads have a long service life and can be used repeatedly, suitable for large-scale production lines.
- Small surface damage: Less damage to the workpiece surface can ensure the finish of high-precision parts.
- Applicable scenarios: Ceramic beads are often used for surface treatment of precision engine blades in aerospace, deburring, and surface strengthening of engine parts in automobile manufacturing, especially when processing high-performance materials such as stainless steel, aluminum alloy, and high-temperature alloy.
Nylon Polyamide Deflashing Media
- Basic introduction: Nylon polyamide deflashing media are plastic sandblasting media commonly used for deburring plastic and non-metallic parts. They are soft but wear-resistant. Nylon polyamide deflashing media have a relatively mild texture and are particularly suitable for deburring materials that are not resistant to high temperatures or are easily scratched. They can also effectively handle flexible materials such as rubber products.
- Advantages:
- Gentle deburring ability: Suitable for processing fragile or easily deformed materials.
- No static effect: When processing electronic parts, nylon beads do not generate static electricity to avoid damaging sensitive components.
- Lightweight and environmentally friendly: Nylon beads can be recycled to reduce the impact on the environment.
- Applicable scenarios: Nylon polyamide deflashing media are very popular in the manufacture of electronic products and medical devices, especially when removing burrs from small electronic components and plastic housings. In addition, it is also suitable for the precision processing of plastic parts in the home appliance industry.
- Basic introduction: Cryogenic deflashing media are usually used to process flexible materials such as rubber and plastic. The core principle is to cool the material to a brittle state at low temperature, and then use the medium for deburring. This media type is suitable for high-precision workpiece deburring, especially for workpieces with complex shapes.
- Advantages:
- Low-temperature treatment without damage: The material burrs are brittle at low temperatures to ensure that the workpiece will not be damaged by high-temperature treatment.
- Suitable for workpieces with complex shapes: High deburring efficiency for parts with fine internal structures and complex geometric shapes.
- High precision: Especially suitable for workpieces with extremely high precision requirements.
- Applicable scenarios: Low-temperature deburring is widely used in the deburring of rubber seals and piping systems in automobile manufacturing, and is also used for surface treatment of medical devices such as catheters and injection molded parts.
Polystyrene Deflashing Beads
- Basic Introduction: Polystyrene deflashing beads are lightweight plastic media that are widely used for deburring flexible materials and lightweight parts. They have a low density and are suitable for industrial applications that require lightweight processing.
- Advantages:
- Lightweight and environmentally friendly: suitable for fragile materials, will not damage the surface, and has the environmental advantage of recycling.
- Efficient cleaning: It has a significant effect on the treatment of slight burrs on the surface of plastic parts, and can efficiently clean hard-to-reach details.
- No static electricity: Suitable for use when precision processing electronic products.
- Applicable scenarios: Polystyrene deflashing beads are widely used in the deburring of plastic housings and parts of electronic products and precision instruments. At the same time, it performs well in the deburring of automotive interior parts, especially in lightweight materials.
Garnet Sand
- Basic Introduction: Garnet Sand is a natural mineral medium with extremely high hardness and wear resistance. Due to its pure natural material characteristics, garnet sand is both efficient and environmentally friendly in deburring and surface treatment and is one of the most commonly used deburring materials in industrial applications.
- Advantages:
- High hardness and high efficiency: It can quickly remove burrs on hard surfaces without generating too much dust.
- Environmentally friendly and non-toxic: Garnet sand is a pure natural material, does not contain toxic substances, and is harmless to the environment after treatment.
- Wide applicability: It is suitable for the treatment of the surfaces of various materials, including metal and non-metallic materials.
- Applicable scenarios: Garnet sand is widely used for rust removal and deburring of steel surfaces in shipbuilding and marine engineering, and is also used for precision deburring and surface strengthening of metal parts in the aerospace industry.
Deburring machine
- Deburring equipment
In modern industry, there are many types of deburring equipment, and automated deburring equipment can greatly improve production efficiency. Common deburring equipment includes drum deburring machines, vibration deburring machines, and polishing deburring machines. These devices use vibration, rotation, or centrifugal force to act between the workpiece and the medium to achieve rapid deburring.
- Application case: In automobile manufacturing, deburring equipment is widely used to clean key parts such as engine blocks, valves, and drive shafts. With deburring equipment, factories can achieve mass production and ensure the stability of product quality.
- Manual sandblasting machine
The manual sandblasting machine is an ideal equipment for processing small batches or high-precision workpieces. It allows operators to precisely process specific areas, especially suitable for removing local burrs, and the equipment cost is relatively low and the flexibility is high.
- Application case: Manual sandblasting machines are often used in electronic product manufacturing, especially for fine deburring of mobile phone cases and computer cases. In addition, it is also used for local surface treatment of precision parts in medical device manufacturing.
Through the detailed introduction of this article, we can see the importance of the deburring process in industrial applications. Different types of burrs have a direct impact on product quality, production efficiency, and safety. Choosing the right deburring method and medium can effectively improve the efficiency of the production line and reduce the scrap rate. According to different industrial needs, the selection of deburring media and equipment should be combined with the workpiece material, shape, and surface quality requirements. No matter which medium is used, it can provide manufacturers with efficient and stable deburring solutions to help them gain a leading edge in the fiercely competitive market.
Filters