Ceramic beads vs garnet sand: Which is the best metal rust removal medium?
January 8, 2025
The formation of rust and scale on the metal surface not only affects the appearance, but also may weaken the material performance and increase the risk of equipment failure. Finding efficient rust removal methods has become a core demand in many industries. Among the many rust removers for metal, ceramic sandblasting beads and garnet sand are widely used due to their respective characteristics. However, with the advancement of industrial technology, ceramic sandblasting beads have gradually become the representative of the best rust remover. This article will compare these two sandblasting media to help companies choose a rust removal solution that better suits their needs.
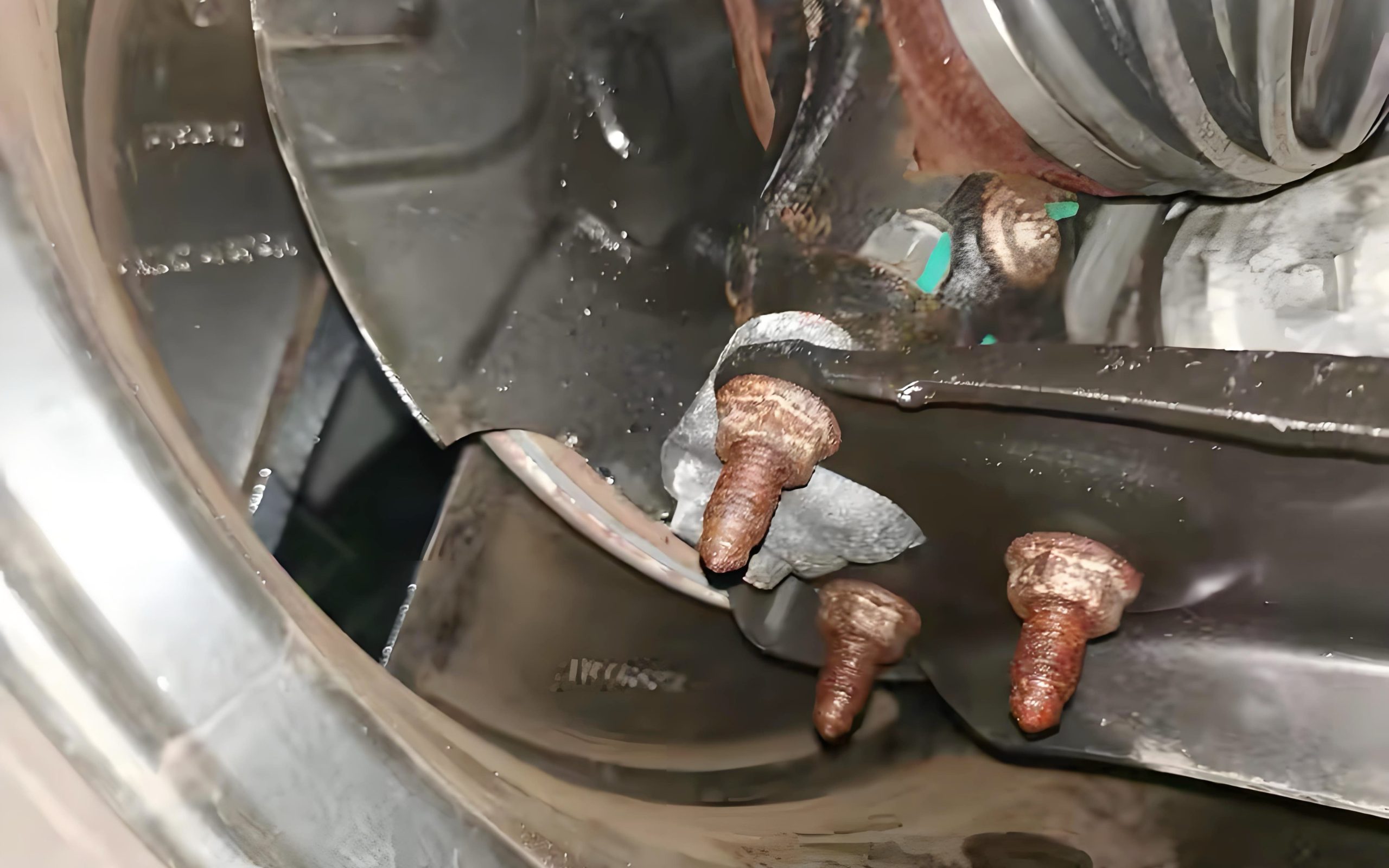
Media Introduction
Ceramic Sandblasting Beads
Ceramic beads are advanced media made of high-purity zirconium oxide and aluminum silicate through high-temperature sintering. Its unique properties make it excel in the field of rust removal:
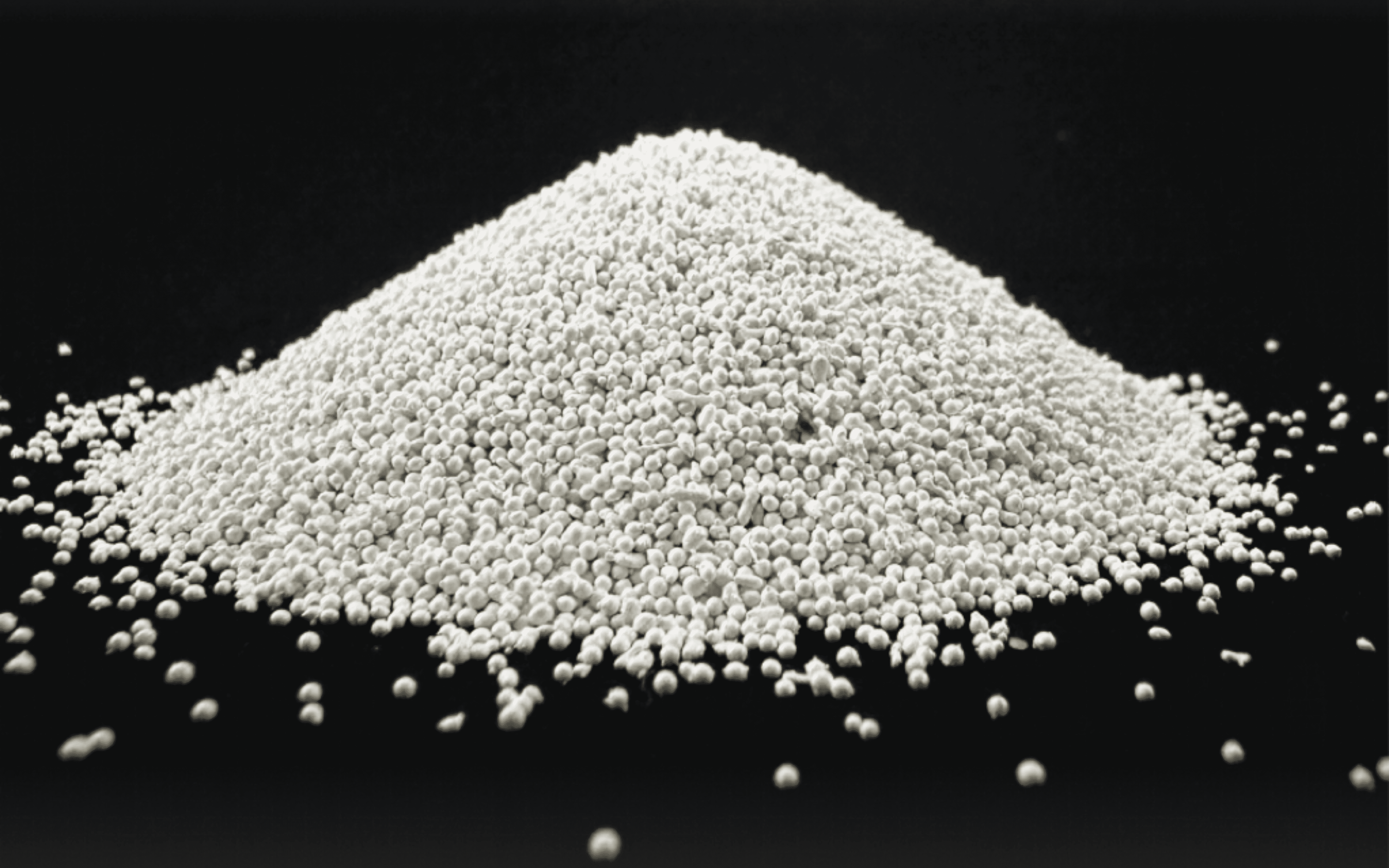

- High strength and wear resistance: The hardness of ceramic blasting beads is close to 9 (Mohs hardness), which can maintain stable performance in high-intensity sandblasting and is not easy to break.
- High recycling rate: Experimental data show that ceramicblasting media can be reused 150-200 times in standard sandblasting equipment, which is 30-40 times that of traditional garnet sand, significantly reducing the replacement frequency.
- Low dust generation:Compared with garnet sand, ceramic blasting beads reduce dust by 80%-90%, which is conducive to improving the working environment and reducing the health risks of operators.
- Precision rust removal ability:Ceramic blast media are not easy to damage the metal surface due to their rounded and uniform particle shape, and are suitable for precision parts with extremely high surface quality requirements.
- Outstanding environmental protection: Due to their high durability and low waste generation, ceramic beads are more in line with the requirements of modern industry for sustainable development.
Disadvantages:
- High initial cost: The unit cost of ceramic beads is usually 3-4 times higher than that of garnet sand, which may be prohibitive for small and medium-sized enterprises with limited budgets.
- Higher equipment requirements: Ceramic sandblasting media need to be equipped with sandblasting equipment with higher wear resistance due to their higher density and hardness; otherwise, they will accelerate equipment wear.
Garnet sand
Garnet sand is a natural mineral medium with irregular particles and sharp cutting edges, which is widely used in traditional sandblasting processes.
- High cutting force: The sharp edges of garnet sand can quickly remove stubborn rust and scale, making it an efficient tool for treating large areas of metal surfaces.
- Low cost: Compared with ceramic sandblasting beads, garnet sand has a lower procurement cost and is suitable for projects with limited budgets.
- Wide range of applications: Its versatility allows it to be used in many industries, especially in shipbuilding, building steel structures, and other fields.
Disadvantages:
- Short service life: It can usually only be reused 3-5 times and needs to be replaced frequently, which increases the overall cost of use and operational complexity.
- High dust volume: Since the particles are easily broken, the dust generated during sandblasting is large.
- Risk of surface damage: Because its particles are sharp, it is easy to cause fine scratches on the metal surface, making it unsuitable for cleaning high-precision or precision parts.
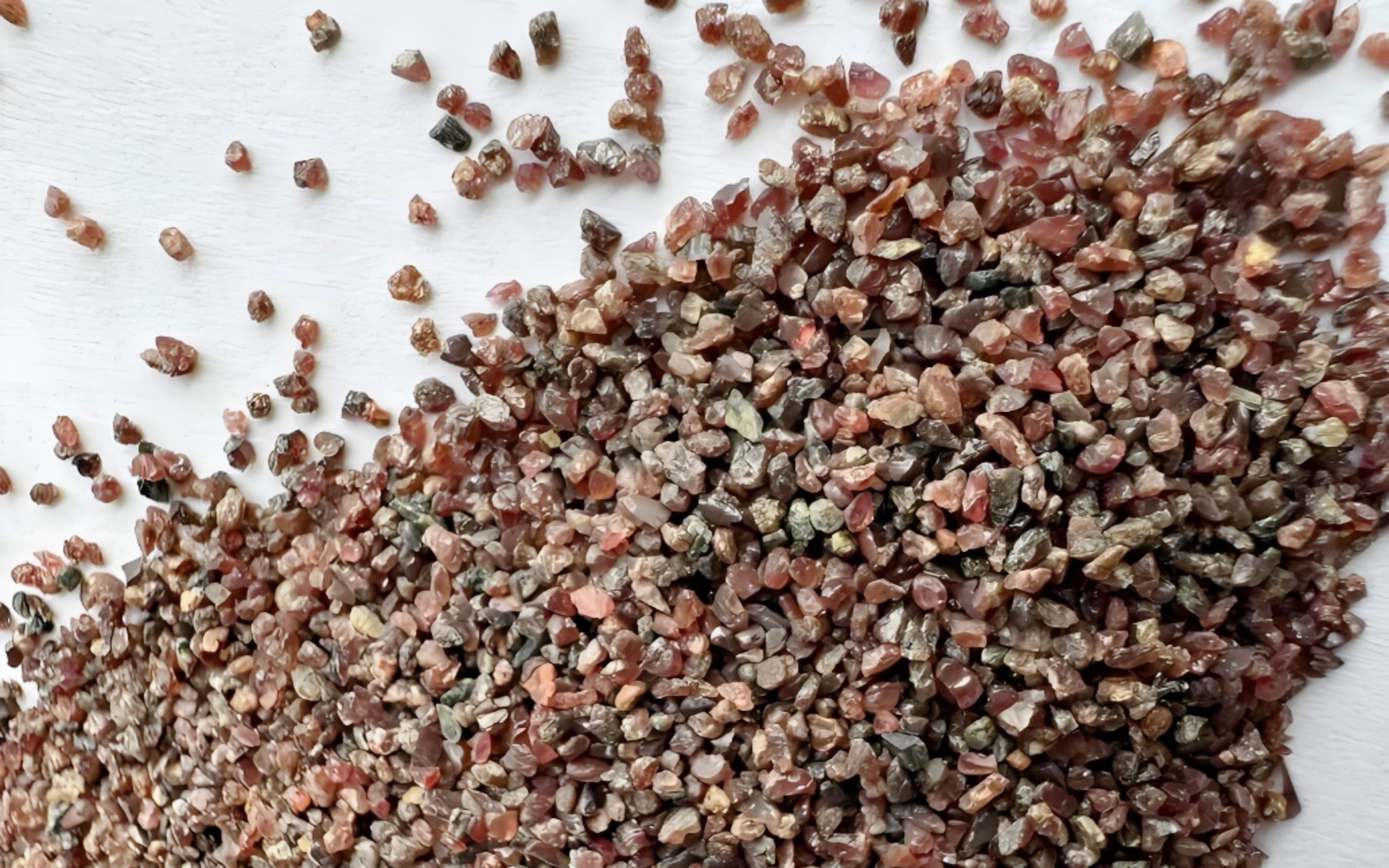
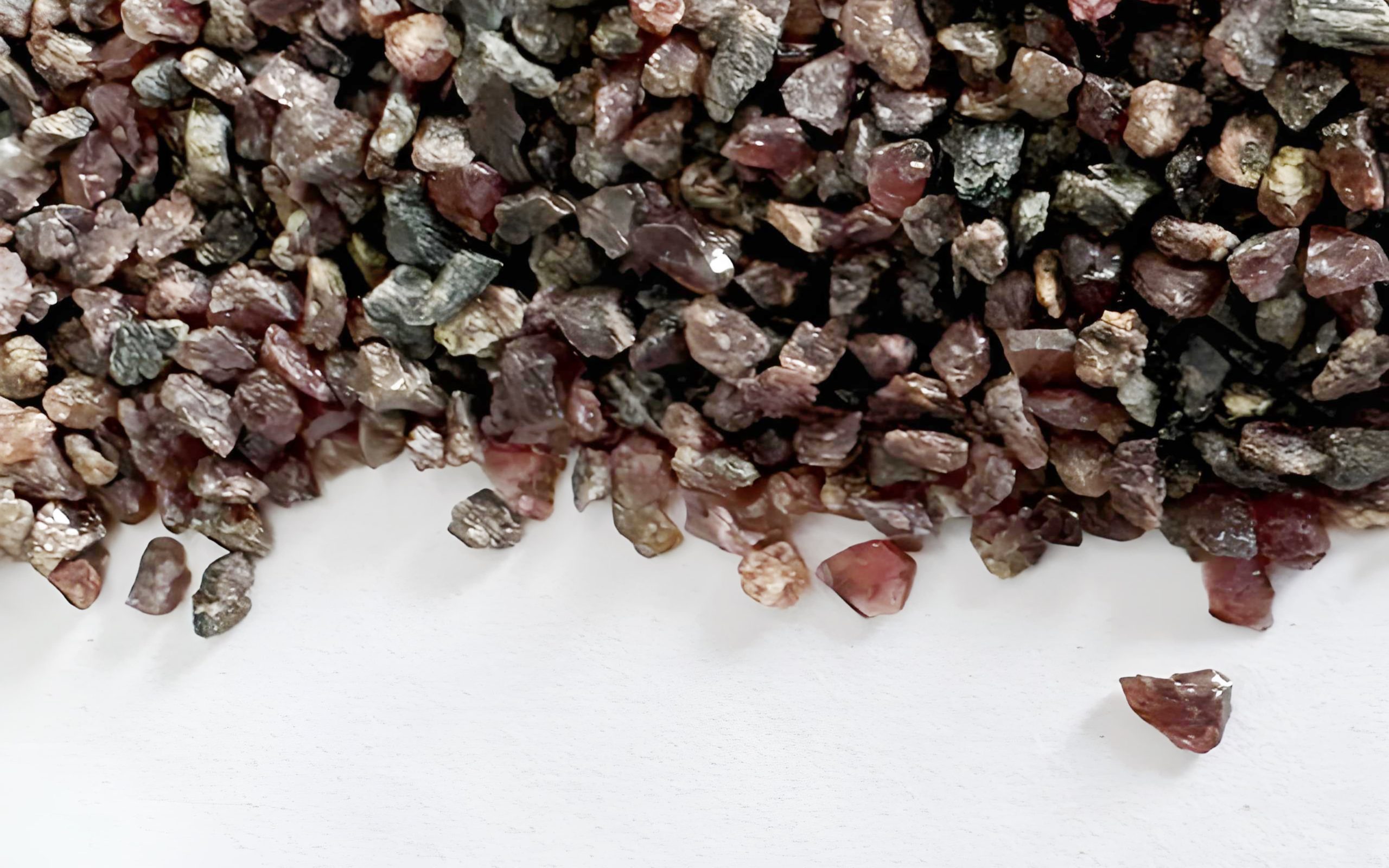
Commonly suitable rust removal industries
Although ceramic blasting media and garnet sand have different properties, they are both widely used in the following industries to undertake the task of rust removal on metal surfaces:
Electronic components industry
Metal parts used in electronic components, such as connectors, conductive connectors, and heat sinks, are often affected by oxidation and micro-rust, which will reduce their conductivity and mechanical strength.
- circuit board brackets
- battery contacts
- high-precision connectors
- radiators or metal housings

Auto parts industry
Parts in automobile manufacturing, such as engine blocks, brake discs, and chassis parts, will produce rust or scale due to exposure to humid environments or long storage times.
- engine parts (such as pistons, cylinder blocks)
- brake discs and wheels
- chassis support structures
- exhaust system components
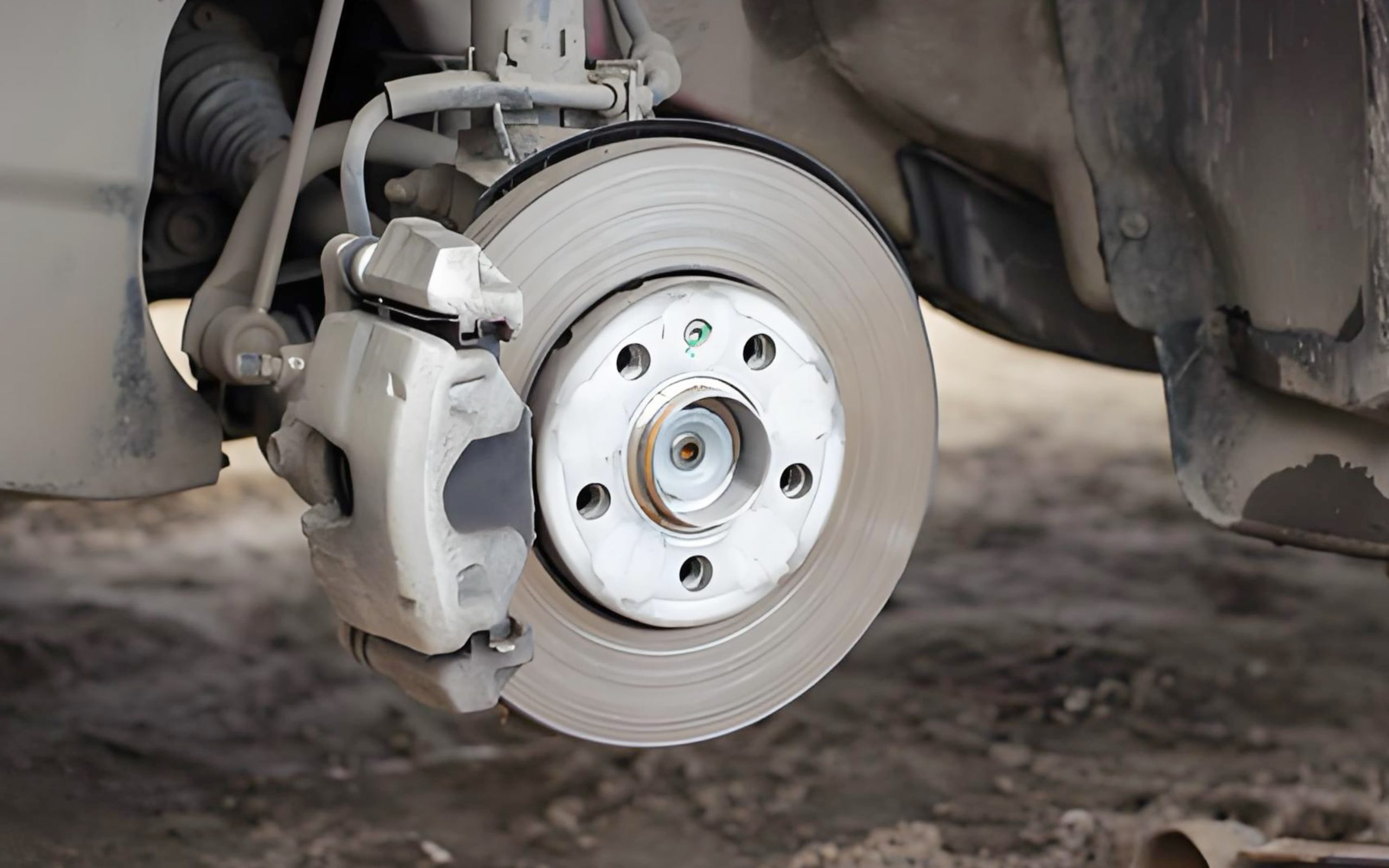
Medical devices and implants
Surface treatment of medical devices and implants requires extremely high cleanliness and pollution-free processes, especially during rust removal, it is necessary to ensure that the metal material is not damaged.
- surgical instruments (such as scissors, pliers)
- titanium alloy implants (such as joint prostheses, and dental implants)
- Medical equipment parts (such as pump housings, and stainless steel catheters)
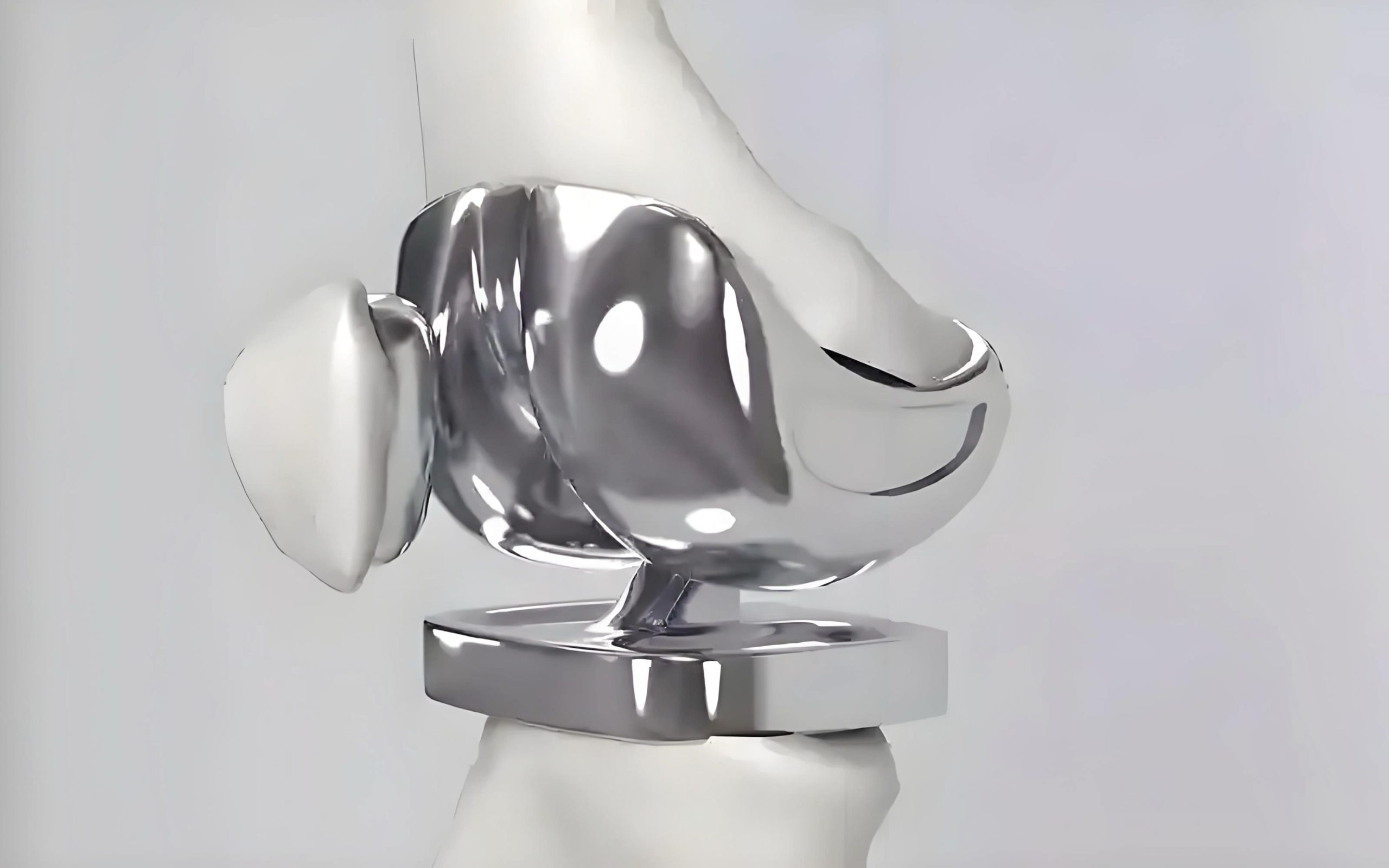
Mold industry
Long-term use of molds will lead to the formation of surface oxide layers and rust, affecting the appearance and precision of the product.
- plastic injection molds
- cold punching molds
- die casting molds
- thermoforming molds
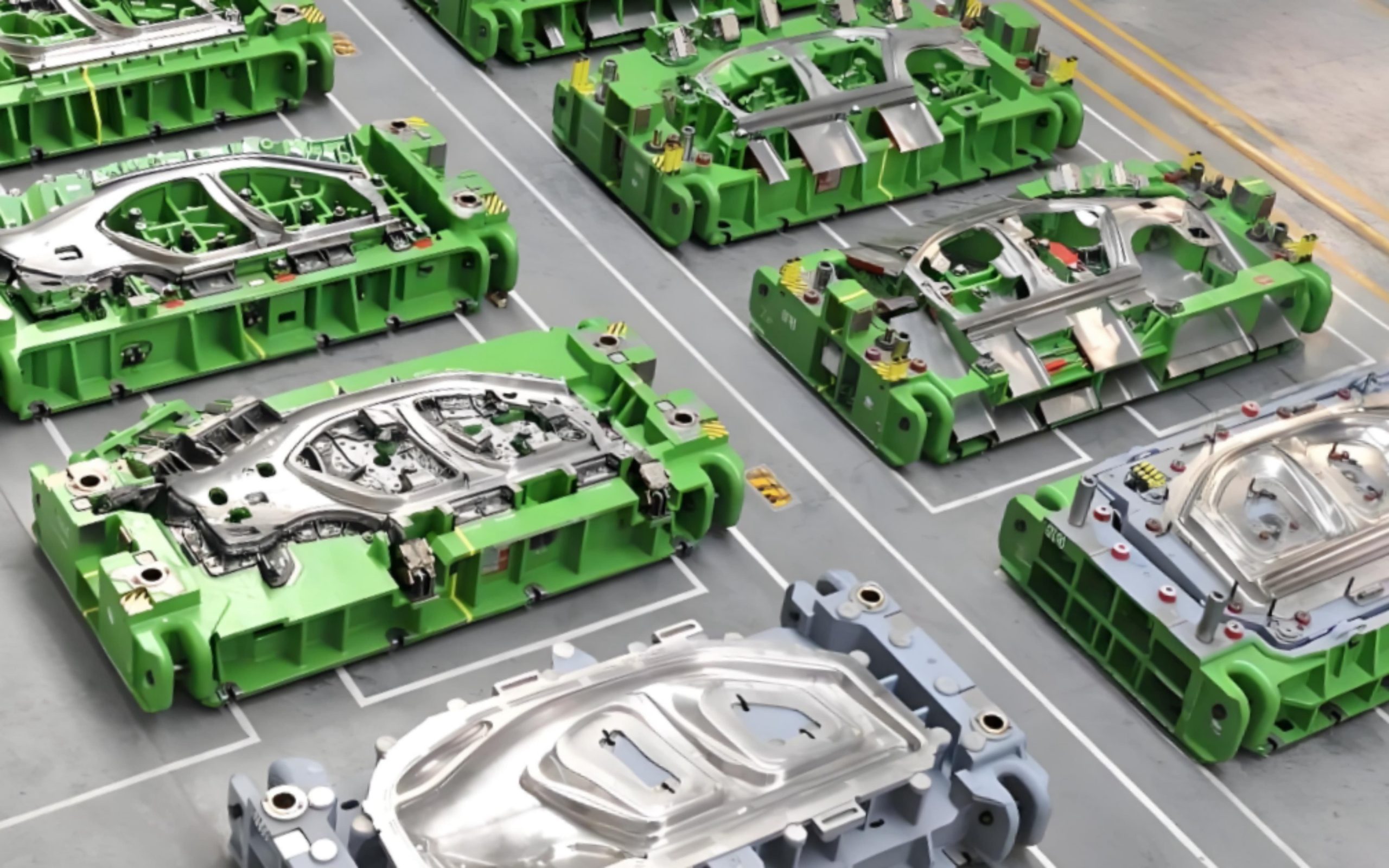
Aerospace industry
Aerospace parts have extremely high requirements for material strength and surface quality. Any rust will have a serious impact on their service life and safety.
- lAluminum alloy fuselage plates
- lTitanium alloy parts (such as turbine blades)
- lAircraft engine parts
- lLanding gear components
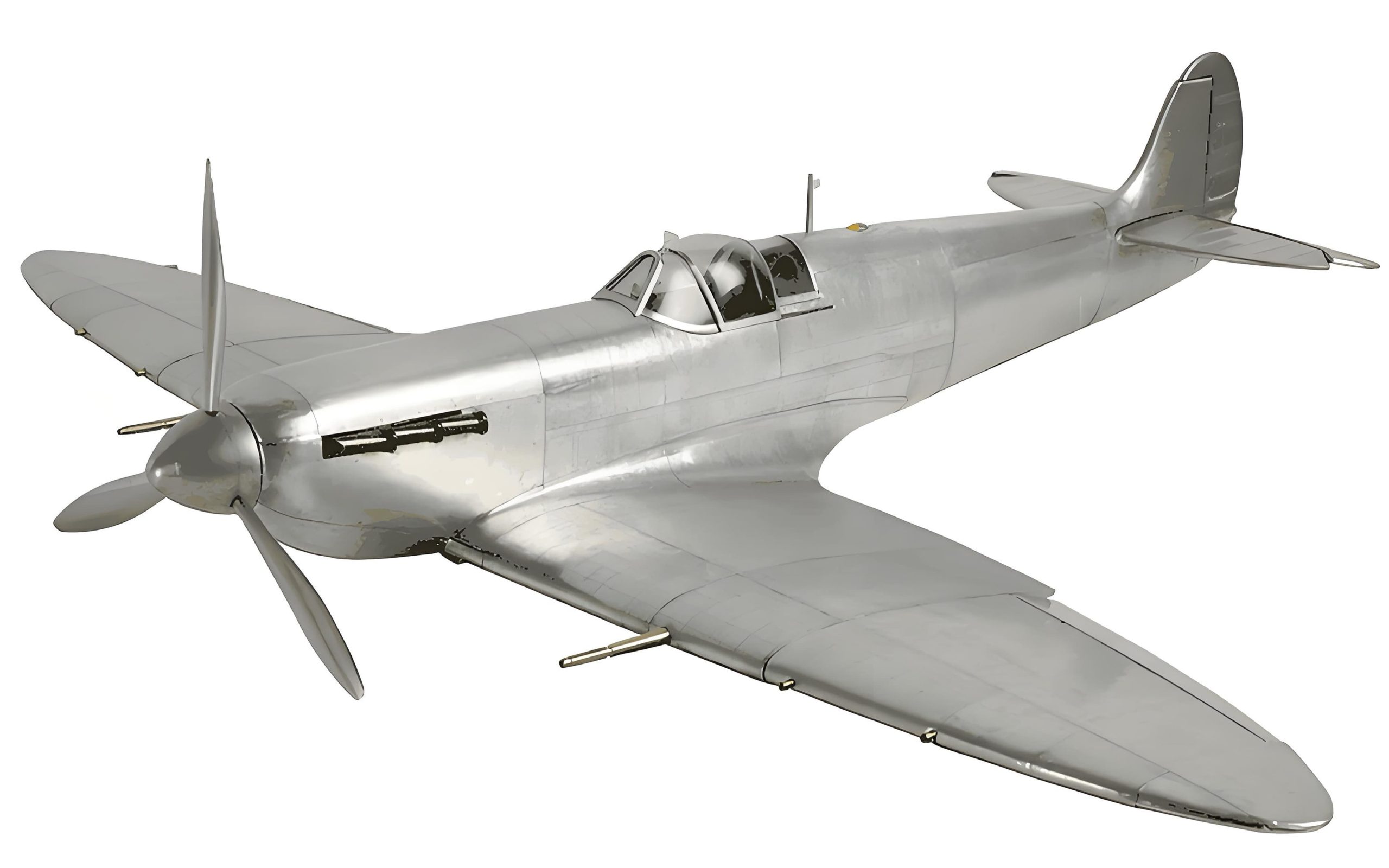
Performance data comparison: Finding the best rust remover for metal
Number of cycles
Ceramic sandblasting beads have been verified by many industrial experiments and can be recycled 150-200 times under normal operating conditions, while the edge structure of garnet sand will lose its cutting ability due to wear after 3-5 uses and needs to be replaced frequently. This means that the use of ceramic blasting beads can significantly reduce the frequency of consumable replacement, saving time and cost.
Dust generation
The dust generated during the sandblasting process not only affects the working environment, but also poses a threat to the health of operators. Data shows that the dust generation of ceramic sandblasting beads is 80%-90% less than that of garnet sand, which not only improves the safety of operations, but also reduces the dependence on dust removal equipment.
Material damage rate
When processing thin-walled metal or precision parts, the high hardness and sharpness of garnet sand can easily cause up to 30% damage to the workpiece surface. In contrast, due to its rounded particle shape and moderate hardness, the material damage rate of ceramic beads is only less than 5%, which is particularly suitable for applications with high surface quality requirements.
Environmental impact
The waste emission of ceramic blast media is 70%-80% less than that of garnet sand. This advantage is particularly prominent in today’s environmentally friendly industry. At the same time, due to its high durability, ceramic beads greatly reduce the consumption of natural mineral resources in the production process.
Long-term economic efficiency
Although the initial purchase cost of ceramic blasting media is relatively high, their high number of recycling times and low waste disposal costs make them save 30%-50% of the total cost over the long-term use compared with garnet sand. This economic efficiency is particularly important for large industrial projects that require efficient rust removal.
Overall, ceramic blasting beads are superior to garnet sand in terms of durability, environmental protection, and precision processing capabilities. For companies with high budgets and high requirements for processing precision, ceramic sandblasting beads are undoubtedly the best rust remover for metal.
If you need a rust removal solution that can provide excellent performance, improve the working environment, and reduce long-term costs, ceramic sandblasting beads are your first choice!
FAQ
The initial cost of ceramic beads is relatively high. Are they suitable for small businesses?
Although the single purchase cost of ceramic sandblasting beads is relatively high, the long-term use cost is significantly reduced due to the much higher number of recycling times than garnet sand, which is especially suitable for small and medium-sized enterprises with stable demand.
Is garnet sand eliminated? What scenarios are still suitable for use?
Garnet sand is still competitive in large steel structures or ship hull surface cleaning with extremely limited budgets and low surface quality requirements, but the hidden costs of frequent replacement need to be considered.
If my metal workpiece has a complex geometry, which medium is more suitable?
For workpieces with complex geometries, ceramic sandblasting beads are more suitable. Its rounded particles can remove rust more evenly when cleaning grooves, edges, and hard-to-reach areas while avoiding damage to delicate surfaces.
How to determine which medium is more suitable for my project?
You can consider the following aspects:
- Budget: If the initial budget is low, you can choose garnet sand; if you focus on long-term costs, ceramic sandblasting beads are more advantageous.
- Surface accuracy: Ceramic sandblasting beads are preferred for precise processing; garnet sand is suitable for rough processing.
- Environmental requirements: Ceramic blast media are recommended for projects that are sensitive to waste emissions and resource consumption.
- Equipment conditions: If the equipment is older or the wear resistance requirements are not high, garnet sand can be given priority.
Can the two media be mixed?
It is not recommended to mix them. The particle shape, density, and performance of these two media are quite different. Mixing them may lead to reduced sandblasting efficiency, uneven surface treatment, and increased equipment wear.
Filters