Surface finishing for 3D printing parts
October 18, 2024
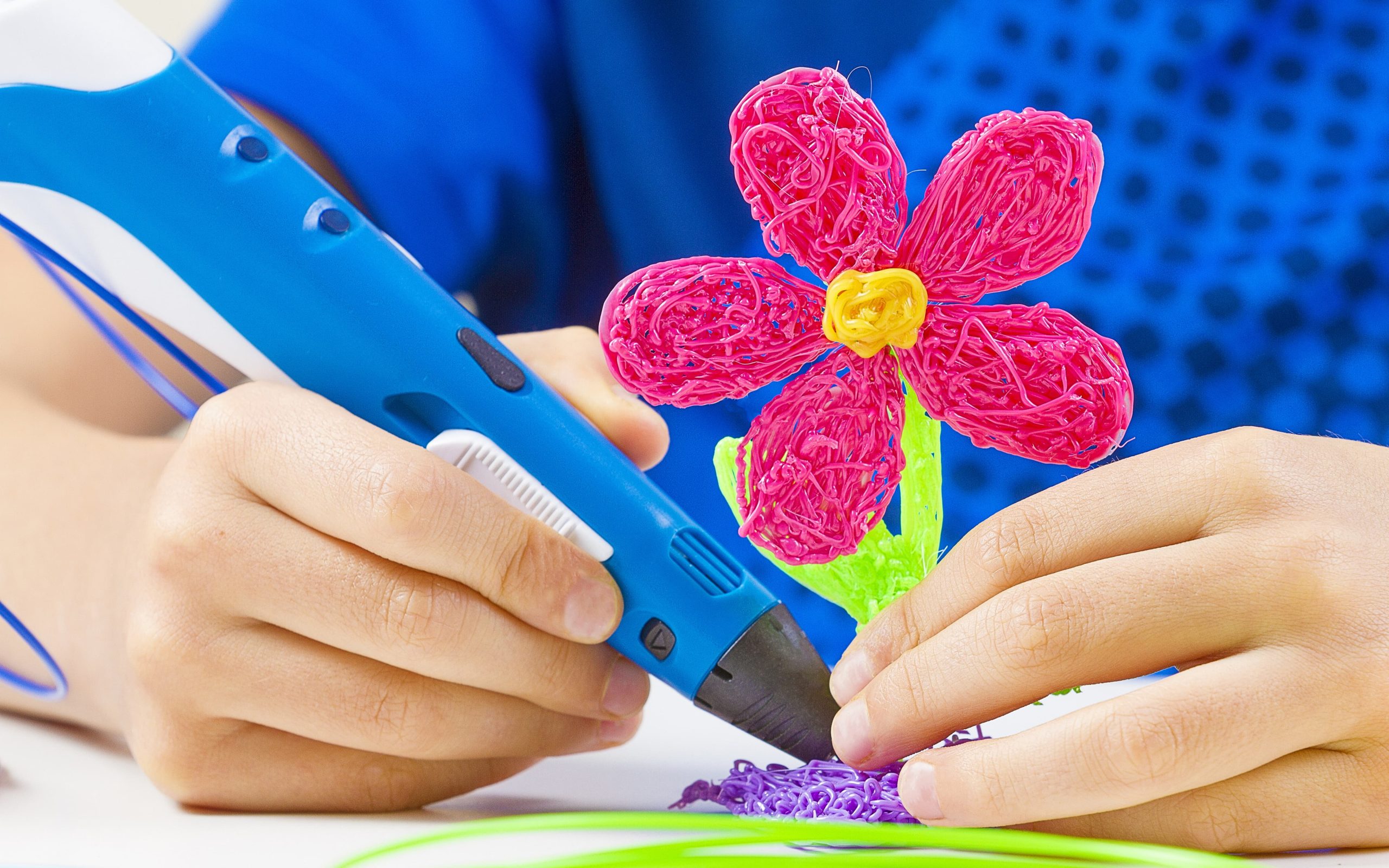
With the continuous advancement of 3D printing and additive manufacturing (AM) technology, this cutting-edge manufacturing method has gradually become an important part of modern manufacturing. According to research by MarketsandMarkets, by 2026, the global 3D printing market is expected to reach nearly US$34.8 billion, with a compound annual growth rate of 22.5%. [1] 3D printing is widely used in high-precision fields such as aerospace, medical devices, and automobiles, but has also found its place in mass markets such as consumer goods, construction, and electronics.
However, although 3D printing provides manufacturers with unprecedented design freedom and efficiency improvements, the surfaces of its products are often imperfect. The layered stacking structure during the printing process (called print layer pattern) leads to uneven surface roughness, affecting the parts’ aesthetics, durability, and functional performance. Therefore, surface finishing has become an important link that cannot be ignored in the 3D printing process. It is not only a modification of the appearance but also can improve the mechanical properties of the parts and improve their functionality.
Industry experts agree that surface finishing has a key impact on the function and application of 3D-printed parts. For example, materials engineer John Barnes said: “3D printed parts without finishing are not competent in certain key applications. Finishing not only improves the appearance but also significantly enhances its service life and performance.” Therefore, understanding and mastering the surface finishing technology of 3D printed parts is the key to achieving widespread application of additive manufacturing technology.
The necessity of 3D printing surface finishing
The unique molding method of 3D printing determines that the surface finish of its parts is often not as good as traditional processing methods. This is due to the layer-by-layer construction method, which forms an irregular layer structure at the micro level. Specifically, whether it is through fused deposition modeling (FDM) technology, selective laser sintering (SLS) technology, or stereolithography (SLA) technology, the surface of 3D printed workpieces will have a certain degree of roughness, and may even leave unfused material particles. This phenomenon not only affects the appearance of the product but also hurts the mechanical properties of the parts in some cases, such as reducing wear resistance, increasing friction coefficient, or affecting sealing.
The influence of printing layer texture and roughness
Take consumer electronics as an example. If the 3D-printed plastic mobile phone case is not surface treated, its surface may be rough and uneven, with a poor hand feel, which does not meet the user’s usage habits and aesthetic needs. In addition, for medical devices, especially implants, untreated rough surfaces may cause biocompatibility issues and increase the risk of bacterial growth. Therefore, surface treatment not only affects the appearance but is also closely related to the functionality of the product.
In addition, the surface roughness of 3D printing will also affect the mechanical properties of parts. For high-performance products such as automotive parts, excessive surface roughness will reduce the fatigue life of parts and increase the risk of wear. Through surface finishing, the fatigue resistance and durability of these parts can be significantly improved, thereby extending their service life.
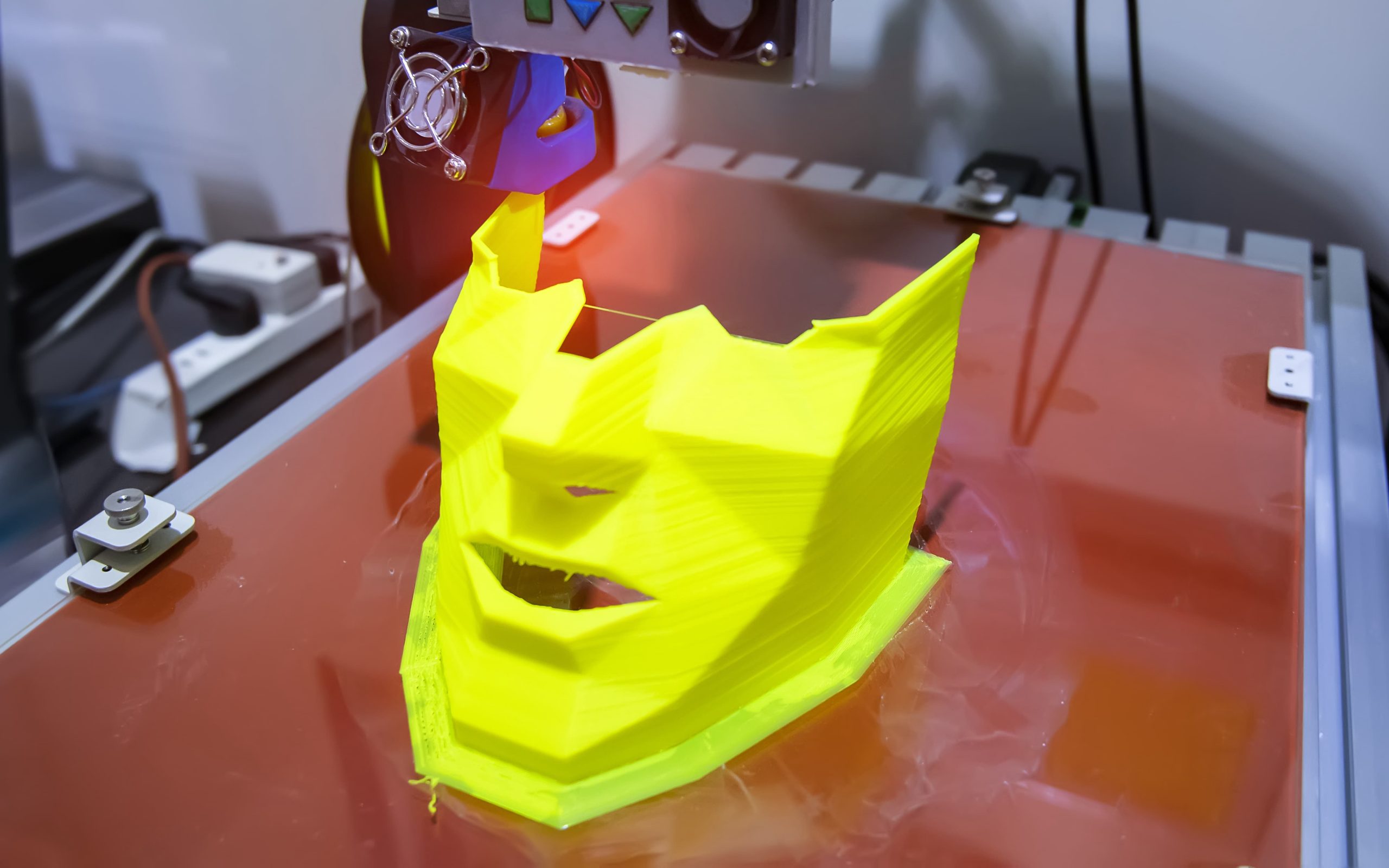
3D printing has obvious burrs and defects
Improvement of functionality by surface treatment
3D printed parts must not only be beautiful but also have various functionalities. Taking the aerospace field as an example, the surface of printed metal turbine blades must be smooth to reduce air resistance and improve engine efficiency. Without surface finishing, the roughness of these metal parts will increase resistance and affect fuel efficiency. Therefore, surface treatment is crucial in improving the functionality of 3D-printed parts.
In practical applications, surface finishing can significantly improve the conductivity, wear resistance, sealing, and other properties of 3D-printed products. For example, in the production of electrical components, metal parts after surface treatment can conduct electricity better and extend their service life. For seals, the improvement of surface finish can effectively reduce the risk of air leakage and improve the reliability of parts.
Common 3D printing post-processing methods
3D printed parts often need to be post-processed to improve surface finish, enhance functionality, and meet the requirements of specific applications. Different 3D printing materials and printing methods determine that the required post-processing processes will be different. Common 3D printing post-processing methods can be divided into two categories: physical treatment and chemical treatment. Each treatment method has its unique advantages and applicable scenarios.
Physical treatment methods
Physical treatment methods mainly rely on mechanical or electrical equipment to smooth the surface, remove layer patterns, and finally achieve a fine finish through grinding, polishing, sandblasting, and other methods.
- Manual grinding and polishing
This is the most traditional physical treatment method, suitable for parts with smaller or simple geometric shapes. The operator polishes the parts with a grinding tool, using sandpaper of different coarseness and fineness to gradually remove the uneven parts of the surface, and finally polishes the parts to a smooth surface. The advantages of this method are low equipment cost, flexible operation, and the ability to process very small areas. However, manual grinding and polishing are time-consuming and inefficient, especially when dealing with complex geometric structures.
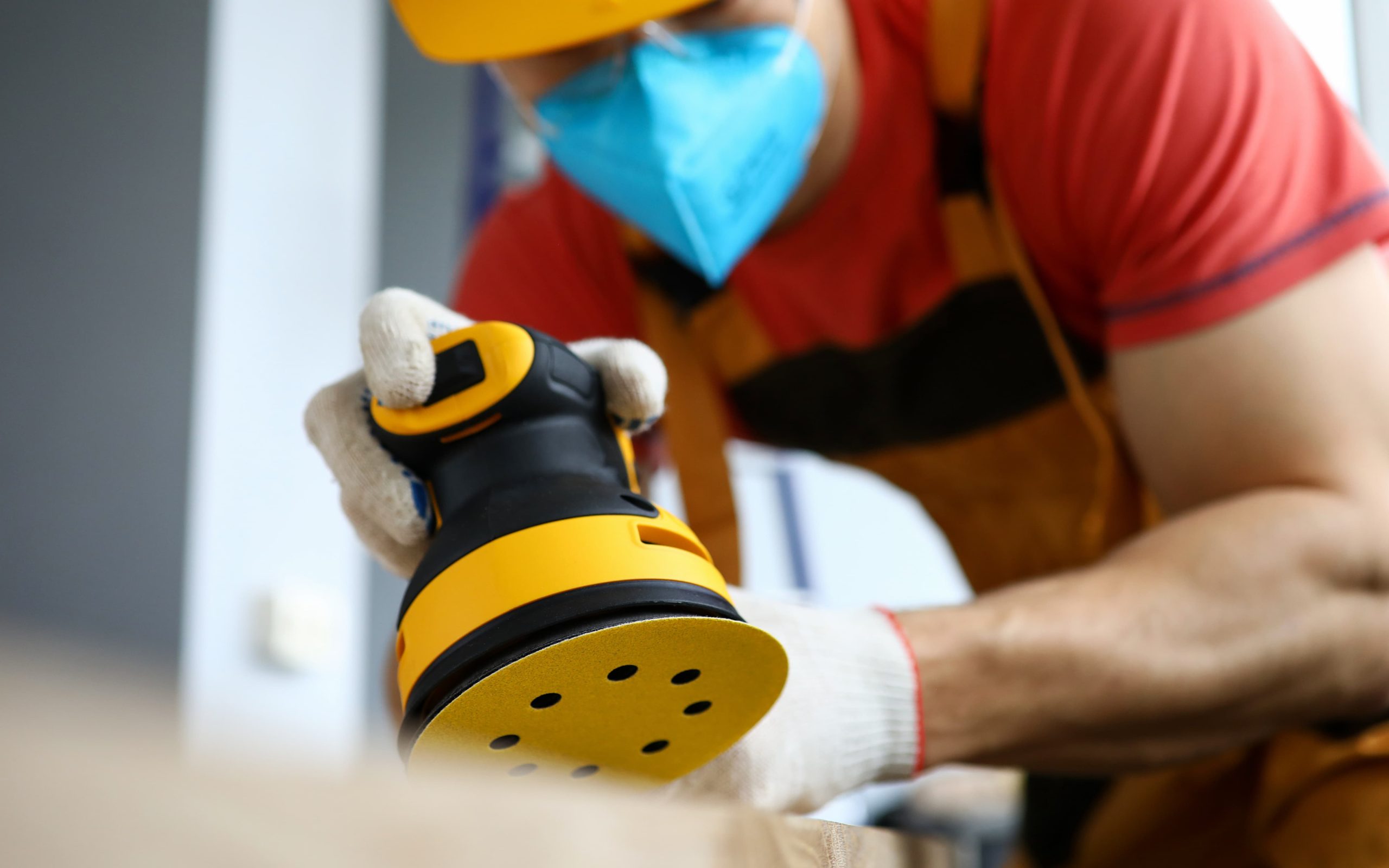
Hand sanding with sanding tools
- Sandblasting
Sandblasting is a common surface finishing method that is suitable for removing residual materials and layer patterns on the surface of parts. Sandblasting is to polish the surface of 3D printed parts by spraying abrasive particles at high speed to achieve the effect of deburring and removing surface roughness. The media used can be selected from aluminum oxide, glass beads, ceramic beads, etc. according to different materials. Its advantage is that it can quickly process large surfaces and can also be applied to parts with complex geometric structures. Sandblasting is widely used in plastic and metal parts, especially for surface treatment of automotive parts and electronic housings.
- Support removal and laser polishing
In 3D printing technologies such as FDM and SLA, supports are inevitable in printing auxiliary structures. To remove supports, shearing tools or mechanical equipment are often used to remove them. At the same time, laser polishing has become an increasingly popular surface treatment method, especially for metal parts. The laser melts the rough areas on the surface of the part by precisely controlling the energy input so that it re-solidifies into a smooth surface. Compared with traditional polishing, laser polishing can handle more complex shapes and details, and has advantages in efficiency and precision.
Chemical treatment method
Chemical treatment methods use chemical reagents such as solvents, acids, and alkali liquids to dissolve or corrode the surface of the part to achieve a smooth effect. Common chemical treatment methods include chemical polishing and surface coating.
- Chemical polishing
Chemical polishing is the use of specific solvents to dissolve the uneven tiny particles on the surface of 3D printed parts under controlled conditions, thereby smoothing the surface. This method is suitable for a variety of printing materials, such as plastics and metals. For example, PLA and ABS plastics, which are commonly used in FDM printing, can dissolve the rough layer on the surface through ethanol or acetone to achieve a smooth effect. The advantage of this treatment method is that it can quickly process large quantities of parts, especially suitable for small parts in industrial production.
- Electroplating and coating treatment
Electroplating and coating treatment is often used for 3D-printed metal parts to enhance their corrosion resistance, wear resistance, or aesthetics by depositing a thin film on their surface. For example, 3D-printed titanium alloy parts can be electroplated with nickel or chromium to enhance their corrosion resistance, which is suitable for parts used in high-temperature and high-pressure environments in the aerospace field. In addition, metal parts can also be surface treated with powder coating or liquid coating, which is widely used in the housing of consumer electronic devices to enhance their aesthetics and touch.
Differences in surface treatment of different materials in additive manufacturing
In the field of 3D printing and additive manufacturing, the diversity of materials determines that the needs and methods of surface finishing are also significantly different. Common 3D printing materials include plastics, metals, and resins, and different materials face different challenges during post-processing. Therefore, to optimize the performance and appearance of 3D printed parts, it is particularly important to select appropriate surface finishing technology for different materials.
Surface treatment of plastics
Plastics are one of the most common materials in 3D printing, such as PLA, ABS, nylon, etc. Since plastic printed parts are often accompanied by delamination marks and large surface roughness, surface finishing mainly focuses on improving their smoothness and enhancing aesthetics. There are many different surface treatment techniques for plastic parts, and the following methods are particularly common:
- Sandpaper grinding and sandblasting
Plastic parts are often physically sanded or sandblasted to remove surface texture and roughness. For example, in the consumer goods field, plastic mobile phone cases such as 3D printed are usually sanded to achieve a smooth touch and then sandblasted to enhance their aesthetics and durability.
- Chemical polishing
Chemical polishing is widely used in FDM-printed plastic parts, especially for thermoplastics such as PLA and ABS. Acetone dissolves the rough parts of the ABS surface to form a smooth surface, which is often used in toy manufacturing or prototyping to ensure that the parts are smooth and visually attractive.
Surface treatment of metals
Compared with plastics, the surface treatment of metal parts has higher requirements, especially in terms of functionality and durability. Common metal materials include titanium alloys, stainless steel, aluminum alloys, etc. The surface treatment of metal parts usually requires a complex multi-step process to meet the stringent requirements in industrial applications.
- Machining and electroplating
The surface treatment of metal parts is often improved through machining, polishing, and electroplating processes to improve their wear resistance and corrosion resistance. For example, in the aerospace field, 3D-printed titanium alloy turbine blades are mechanically polished and nickel-plated to ensure stable performance in high-temperature and high-pressure environments.
- Laser polishing and heat treatment
Laser polishing is also a common choice for metal surface treatment, which can quickly remove surface layers of metal parts and improve their finish. In addition, the heat treatment process enhances the hardness and fatigue resistance of metal parts by changing the microstructure of the material and is widely used in key components such as automotive drive shafts or gears.
Surface treatment of resin
Resin materials are widely used in high-demand fields such as medical equipment and jewelry design due to their high precision and delicate surface quality. However, the surface of resin parts is prone to forming curing marks or tiny unevenness, so post-processing is also required before the finished product.
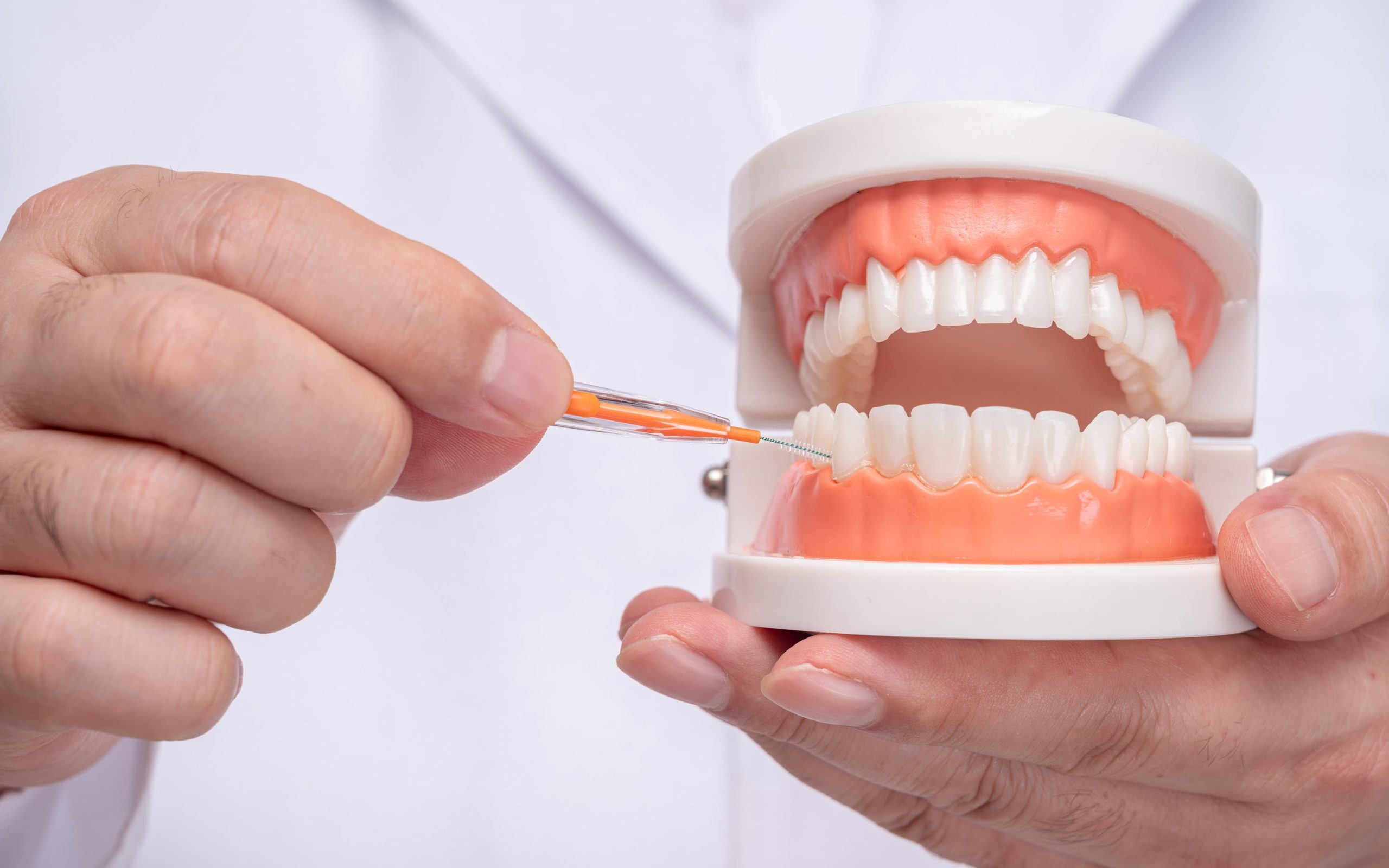
Polished tooth model
- UV curing and spraying
Resin parts are usually further enhanced by UV curing to enhance their surface hardness and then sprayed to improve aesthetics and functionality. For example, in the medical industry, resin 3D-printed dental models are often subjected to subsequent spraying and polishing processes to ensure that their surfaces are smooth and easy to disinfect.
- Grinding and coating
Grinding and coating are common choices for resin parts that require high finish and details. For example, in jewelry design, resin jewelry that has been ground and coated not only looks beautiful but also has the characteristics of wear resistance.
Application Cases
The importance of surface finishing in 3D printing lies in its ability to significantly improve the performance, appearance, and functionality of printed parts. The following will explore specific application cases in multiple industries to show how surface finishing can solve practical problems for specific workpieces and bring significant benefits.
Aerospace Industry
- Fuel Nozzle
In the aerospace field, the fuel nozzle is a key component, and its design must take into account both lightweight and high performance. 3D printing technology can produce complex geometric structures and significantly reduce the weight of parts. Surface finishing is essential to improve the airflow control and injection performance of the nozzle. Through laser polishing or plasma treatment, the surface roughness can be effectively reduced, thereby improving the uniformity and efficiency of fuel injection.
- Fuselage Parts
Aircraft fuselage parts usually require extremely high corrosion resistance and fatigue resistance. Surface-treated 3D-printed metal parts can not only reduce surface defects but also improve surface hardness and oxidation resistance. For example, the application of CVD technology to form a protective coating on fuselage structural parts effectively extends the service life of parts and improves the safety of aircraft.
Medical Industry
- Medical Implants
In the medical industry, 3D-printed implants (such as bone implants and dental restorations) have strict requirements on surface finish. Through fine surface finishing, the biocompatibility of implants can be improved and postoperative complications can be reduced. For example, titanium alloy implants that have been surface-treated can effectively improve the bonding with biological tissues, thereby promoting healing and stability.
- Surgical Tools
3D-printed surgical tools often need to have good corrosion resistance and antibacterial properties. Through chemical vapor deposition (CVD) technology, an antibacterial coating is applied to the surface of the tool, which can not only prevent bacterial growth but also improve the wear resistance and service life of the tool, thereby improving surgical efficiency and safety.
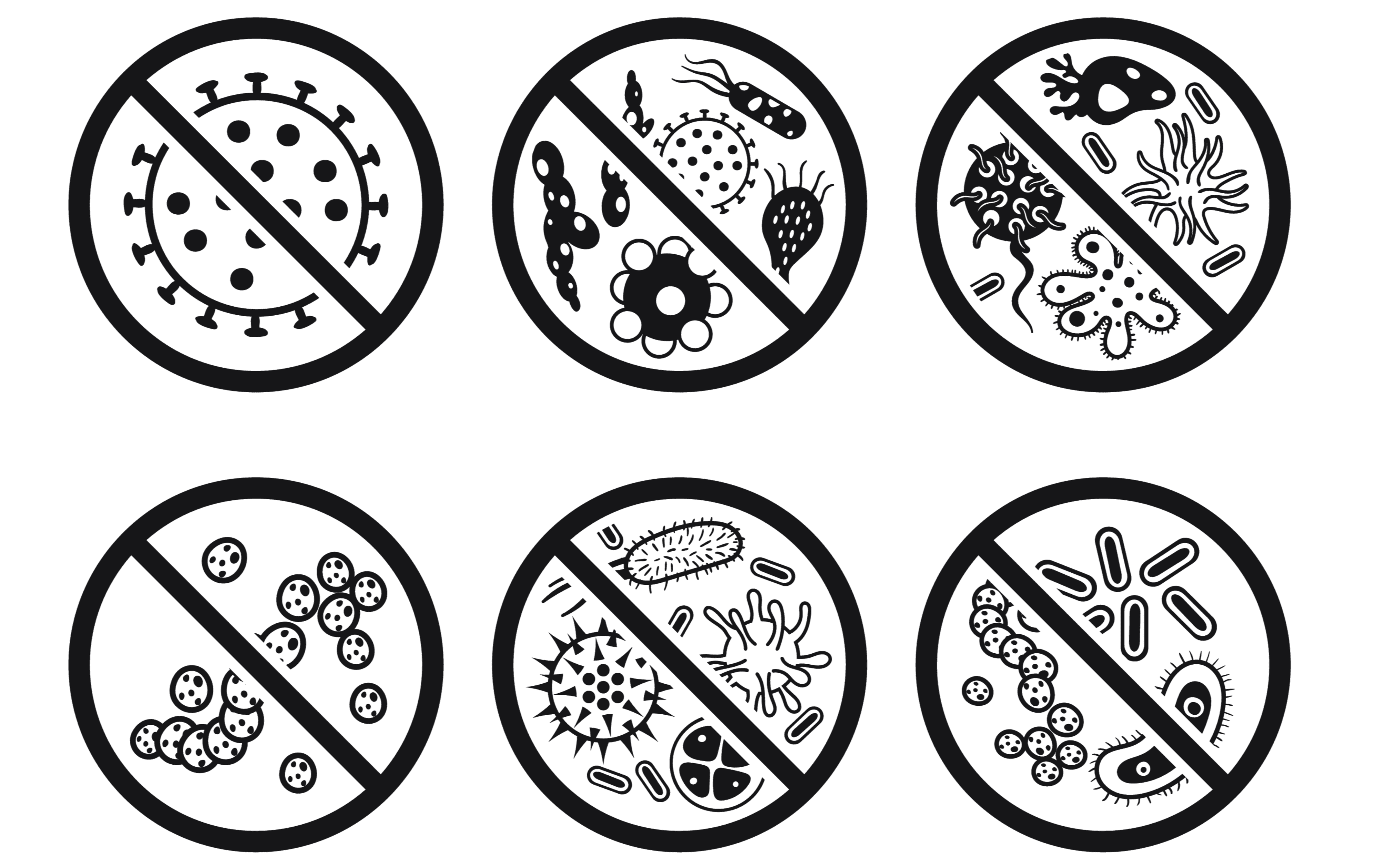
Antibacterial icon
Automotive Industry
- Engine Parts
In automobile manufacturing, the high-temperature resistance and wear resistance of engine parts is crucial. Metal parts manufactured by laser melting 3D printing technology can significantly improve their thermal stability and wear resistance after subsequent surface treatment. For example, after spraying ceramic coating, engine parts can effectively withstand higher temperatures, extending the service life of parts.
- Body components
3D printing technology is increasingly used in the production of body components, especially in the design of complex shapes. Body components that have undergone surface finishing can not only improve the appearance quality but also improve aerodynamic performance. Through airflow-optimized surface treatment technology, air resistance can be significantly reduced, thereby improving the fuel efficiency of the vehicle.
Electronics industry
- Radiator
In electronic products, radiators are key to ensuring the stable operation of equipment. 3D printing technology can be used to produce radiators with complex shapes, and surface finishing helps to improve their heat dissipation performance. For example, fine treatment of the radiator surface through micro-jet technology can increase the surface area and thus improve heat dissipation efficiency.
- Housing and bracket
3D-printed electronic housings and brackets often need to achieve lightweight and good visual effects. After surface treatment, these parts can not only improve wear resistance but also obtain better appearance smoothness, enhancing the consumer’s experience.
With the development of 3D printing and additive manufacturing technology, the importance of surface finishing has become increasingly prominent. Through effective post-processing methods, manufacturers can significantly improve the surface quality and functionality of printed parts to meet the stringent requirements of various industries. This article analyzes the necessity, common methods, and application cases of surface finishing in aerospace, medical, automotive, and other fields, demonstrating its key role in improving product performance and aesthetics.
In the future, with the advancement of technology, surface finishing will play a more important role in 3D printing and promote the sustainable development of the manufacturing industry. Manufacturers should continue to explore new technologies to meet market demands and environmental challenges and further exert the unique value of surface finishing.
[1] 3D Printing Market worth $34.8 billion by 2026 – Exclusive Report by MarketsandMarkets
Filters