The Charm and Prospects of Zirconia Blasting Beads
September 2, 2024
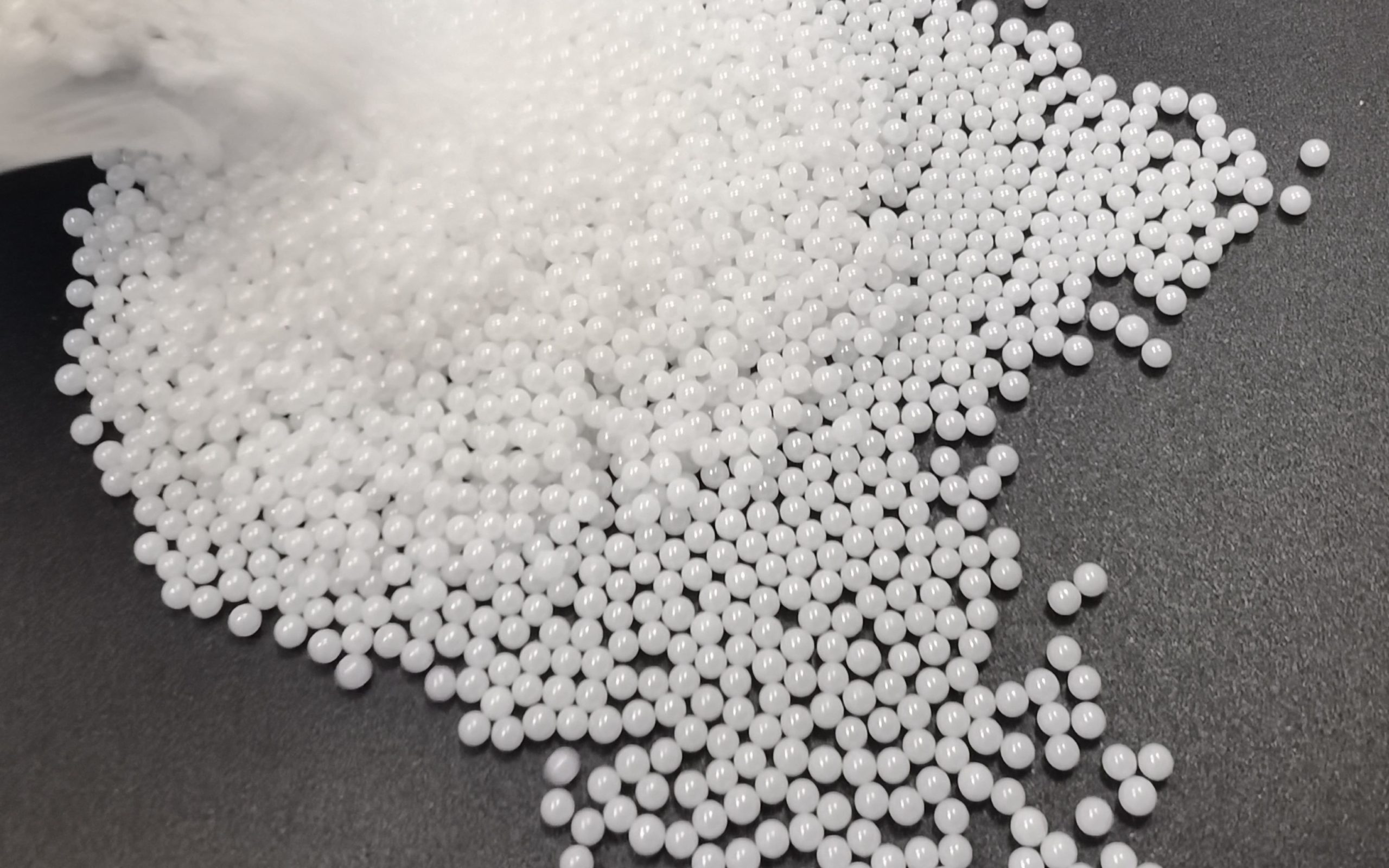
Zirconia blasting beads are a high-performance blasting media widely used in surface treatment, cleaning, and polishing fields. With the advancement of industrial technology and the increasing demand for high-quality processing, zirconia blasting beads have gradually gained favor in more and more industries due to their excellent performance, including emerging fields such as nanotechnology and 3D printing that are closely related to our daily lives. So, what makes this media so attractive? What characteristics make it dominant in various fields? This article will delve into the characteristics, advantages and challenges, economic benefits, environmental friendliness, industry applications, and future development trends of zirconia blasting beads, helping you gain a comprehensive understanding of the charm of this high-end blasting media.
What are Zirconia blasting beads(Click)?
Zirconia blasting beads are a blasting media made from high-purity zirconia (ZrO₂) mixed with stabilizers and processed through high-temperature sintering. Zirconia is a ceramic material with extremely high hardness and wear resistance. After high-temperature sintering, zirconia blasting beads exhibit extremely high hardness and chemical stability, allowing them to maintain their excellent performance in various harsh environments. Their application is widespread, ranging from surface treatment of precision machinery to polishing of aerospace components.
Characteristics
- Material Composition: Zirconia blasting beads are primarily composed of zirconia (ZrO₂), with a purity generally exceeding 95%. The chemical stability and hardness of zirconia allow it to maintain good performance even in high temperatures and corrosive environments.
- Hardness: The Mohs hardness of zirconia blasting beads ranges between 8.5 and 9.0, exceeding 1100 MPa, which is significantly higher than common blasting sand media such as steel shot (hardness of 7). This high hardness allows zirconia blasting beads to effectively remove surface dirt and oxides while being resistant to wear.
- Particle Shape: Typically presented as regular white spherical shapes, this shape helps achieve uniform impact force during blasting, ensuring consistency in treatment results.
- Durability: Due to its excellent hardness and wear resistance, zirconia blasting beads have a long service life, maintaining high-efficiency blasting performance for extended periods, reducing the frequency of media replacement, and lowering maintenance costs.
Main Functions
- Removing Surface Impurities: Effectively removes oxides, rust, dirt, and residues from the surface of metals, plastics, or other materials, preparing the surface for further processing or coating, ensuring the effectiveness of subsequent treatments.
- Polishing and Smoothing: Primarily used in surface treatment in jewelry processing, electronic products, etc., to enhance the high gloss surface of products during manufacturing, reducing surface roughness, and improving appearance quality.
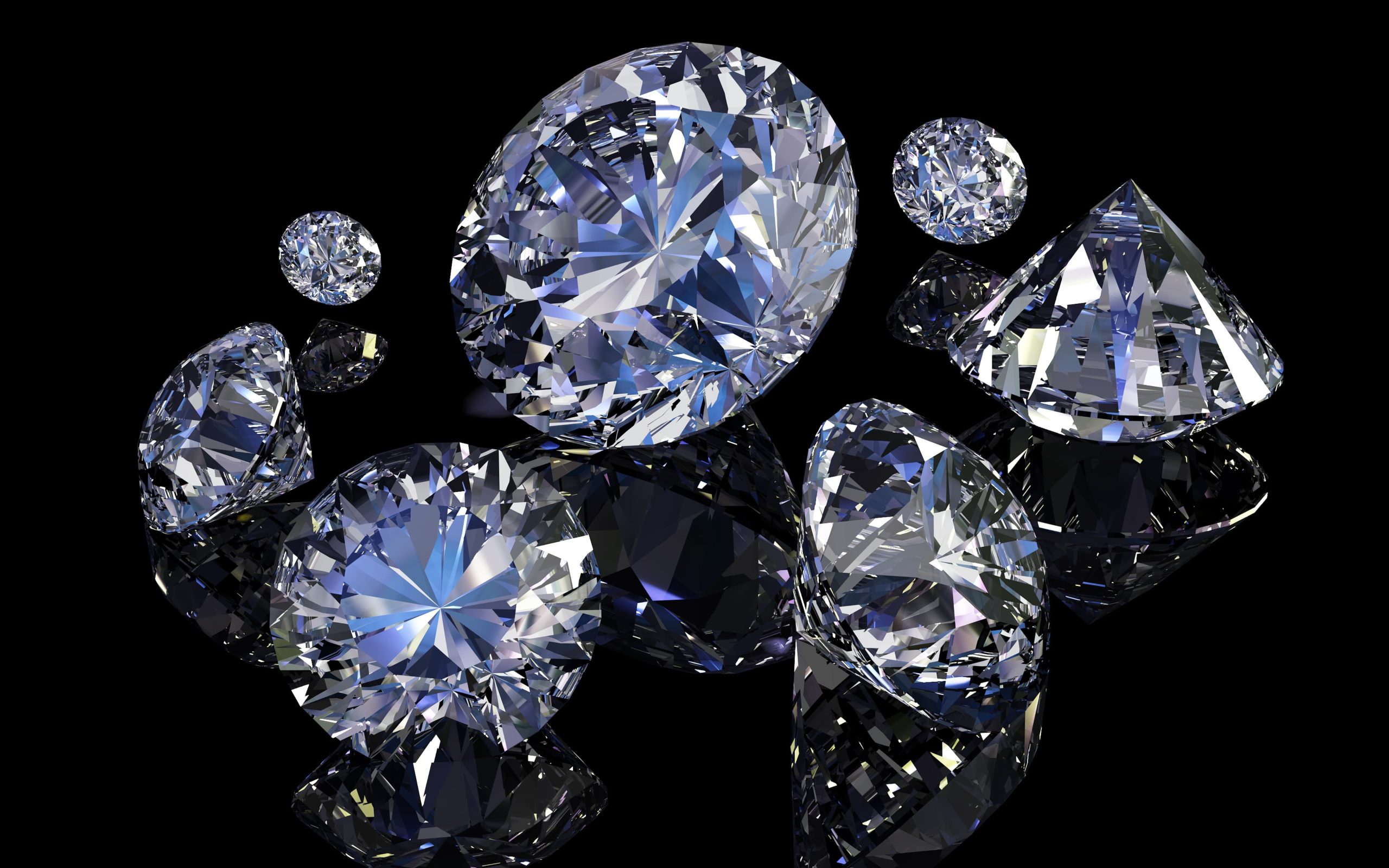
surface treatment of jewelry
- Deburring: Mainly used in mechanical processing and mold manufacturing processes to clean burrs from metal and plastic components, ensuring the safety and functionality of the parts.
- Increasing Surface Roughness: Used for surface treatment before coating, such as metal coatings and adhesive applications, to roughen the surface and increase its adhesion, providing a better foundation for subsequent coatings, adhesives, or other treatments.
- Cleaning Treatment: Used in repair and renovation processes to clean old equipment or various material surfaces, removing old coatings or corrosion, preparing for new treatment or repair.
- Enhancing Surface Hardness and Wear Resistance: Used in high-wear environments, such as industrial equipment and machine parts, to improve material hardness and wear resistance during surface treatment, extending the service life.
- Uniform Surface Treatment: Provides consistent and uniform treatment effects, ensuring the quality of surface treatment. In precision manufacturing processes, such as aerospace and automotive manufacturing, it ensures the uniformity and consistency of part surfaces.
Advantages and Challenges
- Advantages
- High Efficiency: Rapidly removes surface dirt and oxides, significantly improving production efficiency.
- Long Service Life: Due to its extremely high wear resistance, its service life far exceeds many traditional blasting media, which means it can save replacement and maintenance costs over the long term.
- Uniform Blasting Effect: The regular particle shape of zirconia blasting beads helps achieve a uniform blasting effect, thereby enhancing the surface gloss and consistency of the treated surface.
- Challenges
- High Cost: Due to the complex production process and high raw material costs, the market price of zirconia blasting beads is relatively high. This may limit their widespread use in cost-sensitive industries.
- Application Limitations: In some specialized blasting applications, zirconia blasting beads may need to be used in conjunction with other media to achieve the best results. For example, when processing some very hard materials, it may be necessary to adjust the combination of blasting media.
Economic Benefits and Environmental Friendliness
The economic benefits of zirconia blasting beads are primarily reflected in their long service life and high efficiency. Although the initial investment is higher, their strong wear resistance and long service life significantly reduce maintenance and replacement costs in the long run. This long-lasting feature makes zirconia blasting beads more cost-effective in high-frequency use industrial environments.
From an environmental perspective, zirconia blasting beads also perform well. They do not produce harmful waste during production and do not release toxic substances during use, meeting modern environmental requirements. Additionally, they can be recycled, further reducing their environmental impact. Compared to other blasting media, zirconia blasting beads have significant advantages in terms of environmental friendliness.
Industry Applications
- Aerospace
- Background: The manufacturing of aerospace engine components requires extremely high surface gloss and precision to ensure engine performance and safety. Traditional media often suffer from fast wear and uneven effects during processing.
- Application: Zirconia blasting beads are used for surface treatment of engine blades. Due to their high hardness and wear resistance, they can effectively remove oxides and impurities from the blade surface while maintaining surface gloss.
- Case Study: After using zirconia blasting beads to treat engine blades, GE Aviation observed a reduction in surface roughness of about 30%, an improvement in surface gloss of 20%, effectively reducing the failure rate. Additionally, the durability of the blasting beads improved by 50% compared to traditional materials, significantly lowering replacement frequency and maintenance costs.
- Automotive Manufacturing
- Background: The automotive manufacturing industry has strict requirements for the surface treatment of numerous components to ensure their appearance and performance.
- Application: In automotive manufacturing, zirconia blasting beads are used to remove oxides and dirt from aluminum alloy and steel parts, improving the gloss and adhesion of components.
- Case Study: BMW used zirconia blasting beads in the surface treatment of its body parts, improving the adhesion and durability of coatings. Tests showed that the corrosion resistance of the treated body parts increased by 25%, and the service life was extended by 20%.
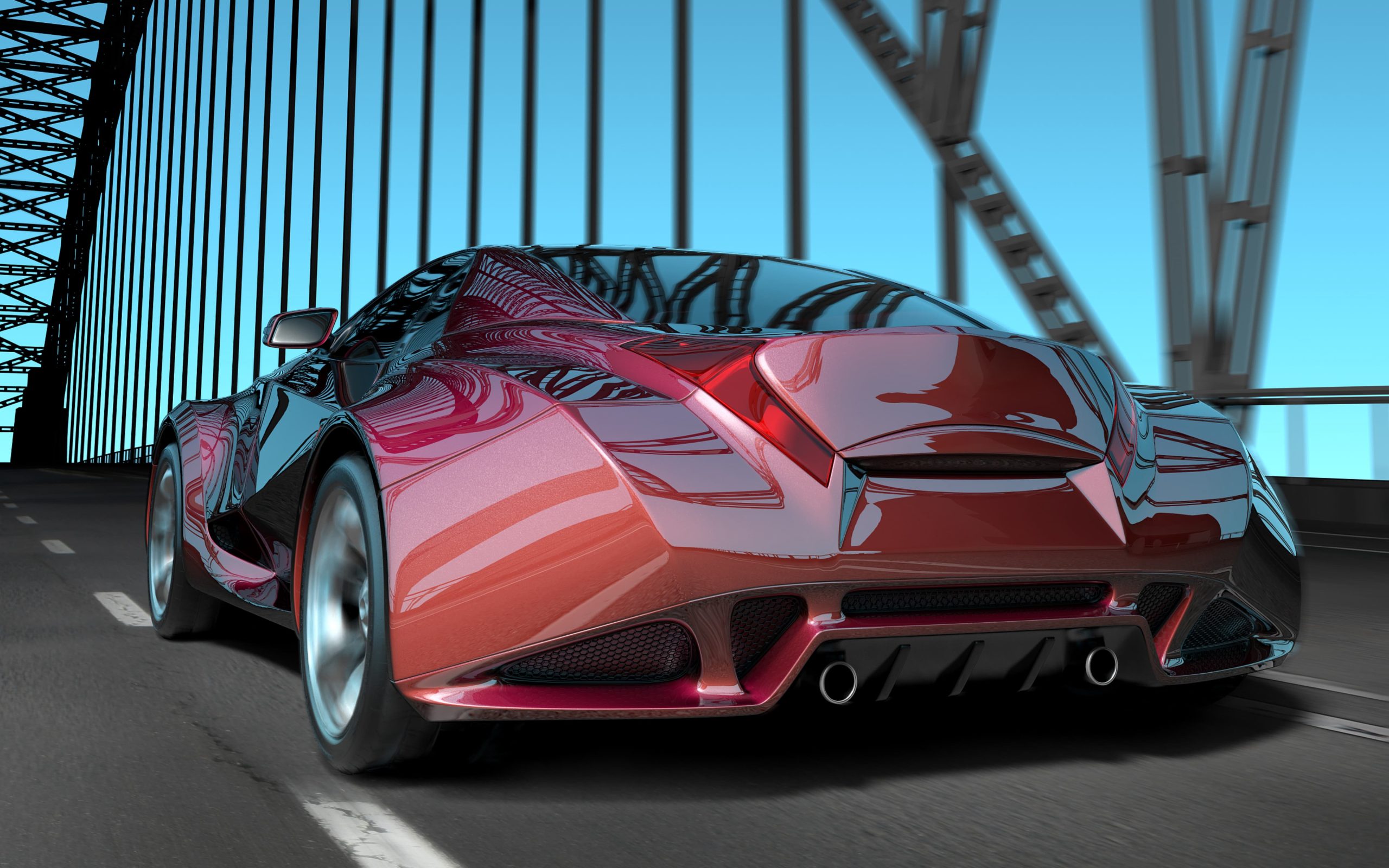
The appearance of the car is one of the factors that consumers consider
- Electronics
- Background: Surface treatment of electronic products, especially touch screens and other precision electronic components, requires high cleanliness and smoothness.
- Application: Zirconia blasting beads are used for surface treatment of touch screen glass, effectively removing tiny impurities and oxides from the surface, ensuring screen gloss and functional consistency.
- Case Study: Apple used zirconia blasting beads in the surface treatment of iPhone touch screens, significantly improving screen touch sensitivity and visual effects. The treated touch screens showed a 40% increase in gloss and a 15% reduction in touch response time.
- Industrial Manufacturing
- Background: The industrial manufacturing sector involves numerous complex mechanical components and equipment that typically require precise and uniform surface treatment to ensure accuracy, functionality, and durability.
- Application: Cleaning oxides and dirt from metal contact points on electrical equipment to ensure good electrical contact performance.
- Case Study: ABB, in producing electrical equipment, required precise treatment of metal contact surfaces. After using zirconia blasting beads, the cleanliness of electrical contact points increased by 25%, and the stability of electrical contact performance improved by 15%, significantly reducing failure issues caused by poor contact.
In addition to these mainstream industries, zirconia blasting beads are also starting to be used in the new energy sector, such as in the manufacturing of wind turbine blades and solar panels. Their excellent wear resistance and uniform blasting effect can effectively process these large-scale energy devices, enhancing their performance and service life. Moreover, with the continuous advancement of new energy technology, zirconia blasting beads are expected to play a greater role in improving equipment efficiency and reliability.
Latest Technological Innovations
- Application in Nanotechnology: Zirconia blasting beads have shown significant advantages in the field of nanotechnology. Due to the special properties of nanomaterials, their surface treatment requirements are extremely strict. The high hardness and chemical stability of zirconia blasting beads enable precise treatment of nano-level surfaces without damaging the nanostructure. This treatment not only maintains the high performance of nanomaterials but also enhances their wear resistance and thermal stability. In the future, with the continuous progress of nanotechnology, zirconia blasting beads are expected to play a more important role in the manufacturing and application of nanomaterials.
- Optimization in 3D Printing: In 3D printing technology, the application of zirconia blasting beads has also shown promising prospects. The 3D printing process often requires post-processing of printed parts to remove support materials and improve surface quality. Zirconia blasting beads can effectively remove excess material, and their uniform blasting effect can significantly improve the surface gloss of printed parts. Additionally, the high wear resistance of zirconia blasting beads ensures stable blasting performance in high-frequency use, thus enhancing the overall quality of 3D printed products. Future optimization of zirconia blasting beads for different types of 3D printing materials and processes is expected to further expand their application range in the 3D printing field.
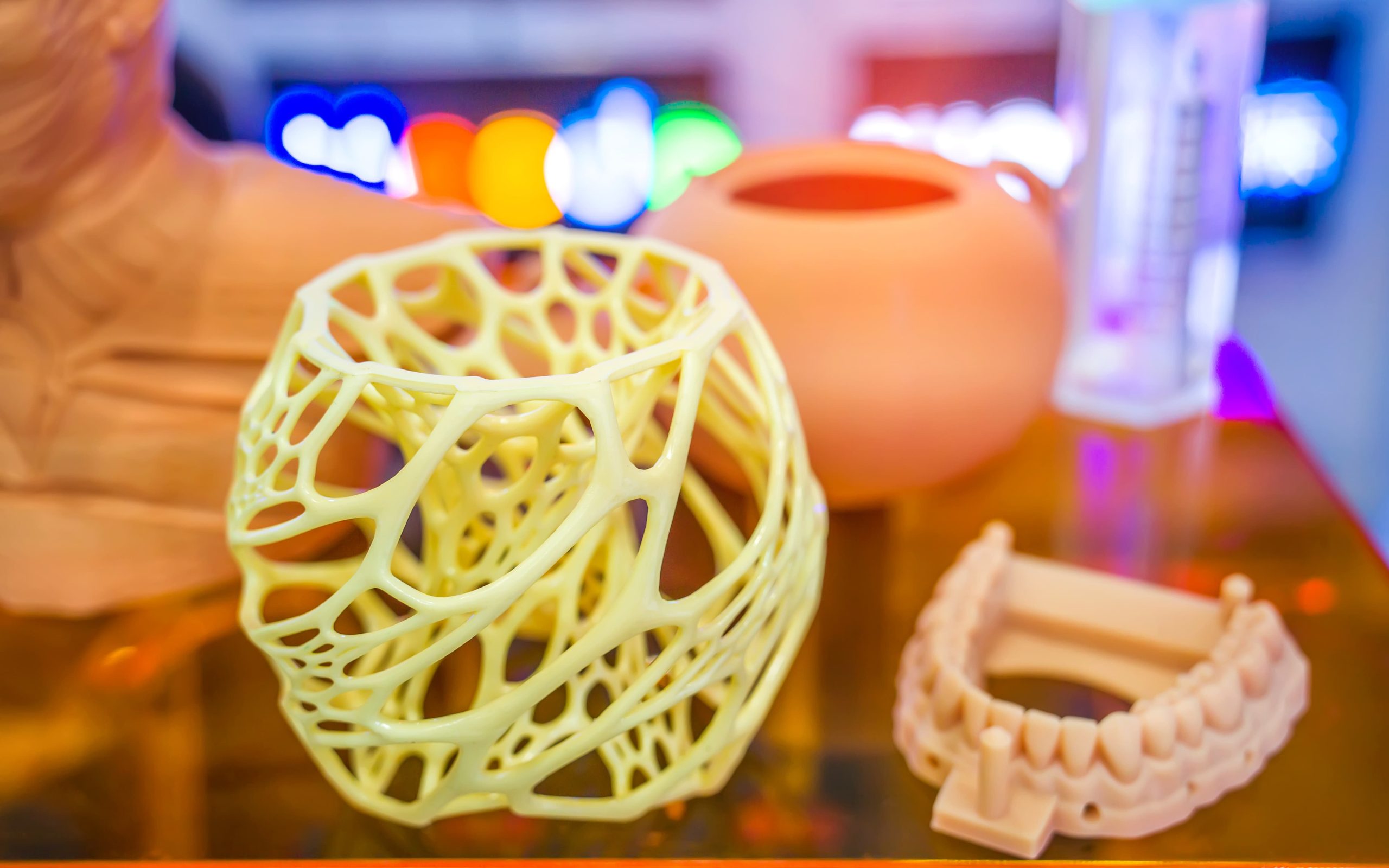
3D printed product
Comparison with Ceramic Beads Blasting Media
- Consistency: Both zirconia blasting beads and ceramic beads blasting media primarily consist of ZrO₂, resulting in high hardness and wear resistance for both. Additionally, both types of media have a relatively regular spherical shape, which facilitates uniform sandblasting results.
- Differences: Zirconia blasting beads have a significantly higher ZrO₂ content compared to ceramic beads blasting media, resulting in superior hardness and wear resistance. This enhanced durability makes zirconia blasting beads perform better in applications requiring high precision surface treatment. While ceramic beads blasting media generally have a lower cost, their performance and lifespan are relatively shorter compared to zirconia blasting beads.
Comparison with Other Media
- Steel Shot: Steel shot is a traditional blasting sand media known for its high hardness but is prone to rusting. In contrast, zirconia blasting beads offer greater hardness and environmental adaptability. Although the initial cost is higher, the long-term economic benefits are more apparent due to their durability.
- Alumina: While alumina sandblasting media have high hardness and wear resistance, they do not match the performance of zirconia blasting beads. Zirconia blasting beads provide a more uniform blasting effect and maintain stable performance with frequent use. Although alumina is less expensive, its performance and lifespan are inferior to those of zirconia blasting beads.
- Glass Beads: Glass beads are typically used for light polishing and cleaning and have lower hardness and wear resistance. Compared to glass beads, zirconia blasting beads offer higher hardness and longer lifespan, making them suitable for treating harder materials and more demanding industrial environments.
- Plastic Granules: Plastic granules are used for light surface treatments and lack the necessary hardness. Zirconia blasting beads provide higher processing efficiency and better wear resistance, making them suitable for more complex and demanding applications.
Future development trend
At present, the most important result is the combination of intelligent manufacturing, which can achieve more accurate sandblasting control and more efficient production processes. Intelligent manufacturing will further promote the application of zirconia blasting beads in surface treatment, and achieve automated and intelligent production management. In addition, environmental protection will also become an important direction of the development of sandblasting media. Advances in green technology for zirconia blasting beads will include more environmentally friendly production processes and material choices to reduce environmental impact. At the same time, improving the recycling rate and recycling capacity is also the future development trend, which will further promote its application in the field of environmental protection.
In the future, the technical development trend of zirconia blasting beads mainly includes the following aspects:
- Improve performance: Continuously improve the production process to improve the hardness and wear resistance of zirconia blasting beads for more demanding industrial applications.
- Cost reduction: By optimizing the production process and raw material procurement, the production cost of zirconia blasting beads is reduced, thereby improving its market competitiveness.
- New application exploration: Explore the application possibilities of zirconia blasting beads in more emerging fields, such as new energy, electronic manufacturing and other industries.
Zirconia blasting beads, as a high-performance blasting media, possess outstanding characteristics and advantages. Their excellent hardness, wear resistance, and uniform blasting effect make them ideal for use in surface treatment, cleaning, and polishing across various industries. Although they face some challenges such as high cost, their economic benefits and environmental friendliness are significant. With the continuous advancement of technology, zirconia blasting beads are expected to play an increasingly important role in emerging fields such as nanotechnology and 3D printing. By constantly optimizing their application technology and expanding their application range, zirconia blasting beads will continue to contribute to the development of high-quality and efficient manufacturing processes in the future.
Filters