Surface finishing: Sandblasting improves mold quality
November 8, 2024
The mold manufacturing industry widely serves the fields of plastics, automobiles, aviation, etc., and its product quality has a direct impact on the production efficiency and finished product performance of various industries. Although the mold undergoes multiple processing steps during the manufacturing process, it may still affect the service life and product quality due to problems such as rough surface, tiny burrs, and poor demolding. Surface finishing can effectively improve these problems, not only improving the finish and durability of the mold but also ensuring the consistency of mass-produced products, thereby helping the manufacturing industry achieve high-precision and high-quality production goals.
Mold production process
The mold manufacturing process is divided into multiple steps to ensure its accuracy, strength, and surface performance. The following are common mold production steps:
- Design and material selection: According to the functional requirements of the finished product, the designer defines the mold structure and size, and selects mold materials with high hardness and wear resistance (such as high-hardness steel or special alloys). The selection of materials is crucial because the mold needs to withstand high temperatures, high pressure, and repeated use.
- Rough processing: The mold material undergoes basic processing processes such as turning and milling to form a preliminary shape and size. The purpose of this stage is to process the mold to a close to the final contour so that subsequent fine processing can be carried out more efficiently.
- Heat treatment: In order to further improve the hardness and fatigue resistance of the material, the mold is often subjected to heat treatment (such as quenching and tempering). These processes reorganize the crystal structure inside the material under a high-temperature environment, making the mold more wear-resistant and compressive, and extending the service life.
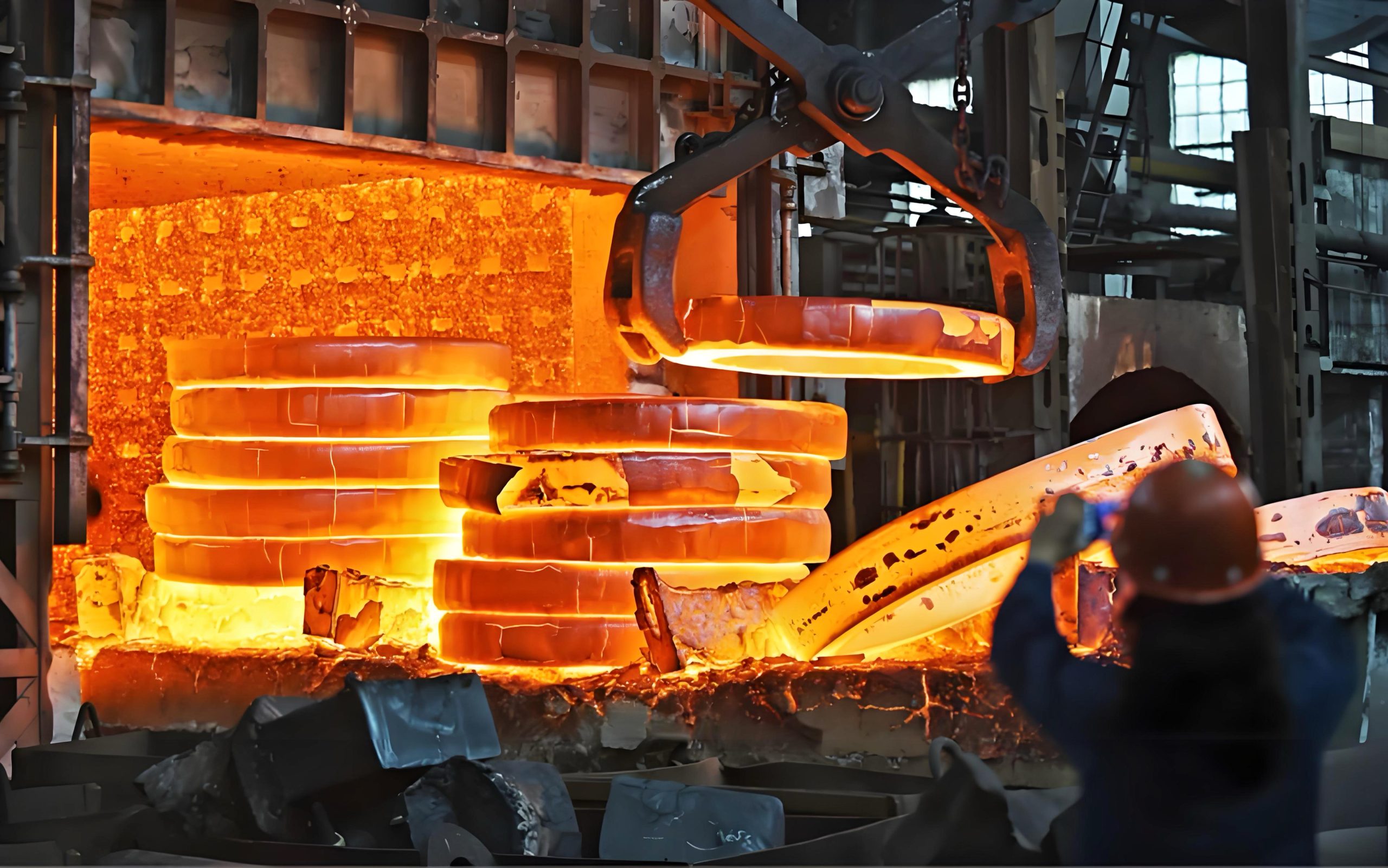
Heat treatment
- Finishing: The finishing stage mainly includes grinding, wire cutting, EDM, etc. to ensure that the dimensional accuracy and surface finish of the mold meets the use requirements. Although these processes can reduce the roughness, they may still leave tiny processing marks on the surface, which requires further treatment to meet higher finish requirements.
- Surface treatment (such as sandblasting surface finishing): After the mold is finally formed, surface treatment processes such as sandblasting are used to improve its surface properties. Through surface finishing, the mold surface can obtain ideal smoothness, wear resistance, and consistency, meeting the requirements of smooth molding and extended life.
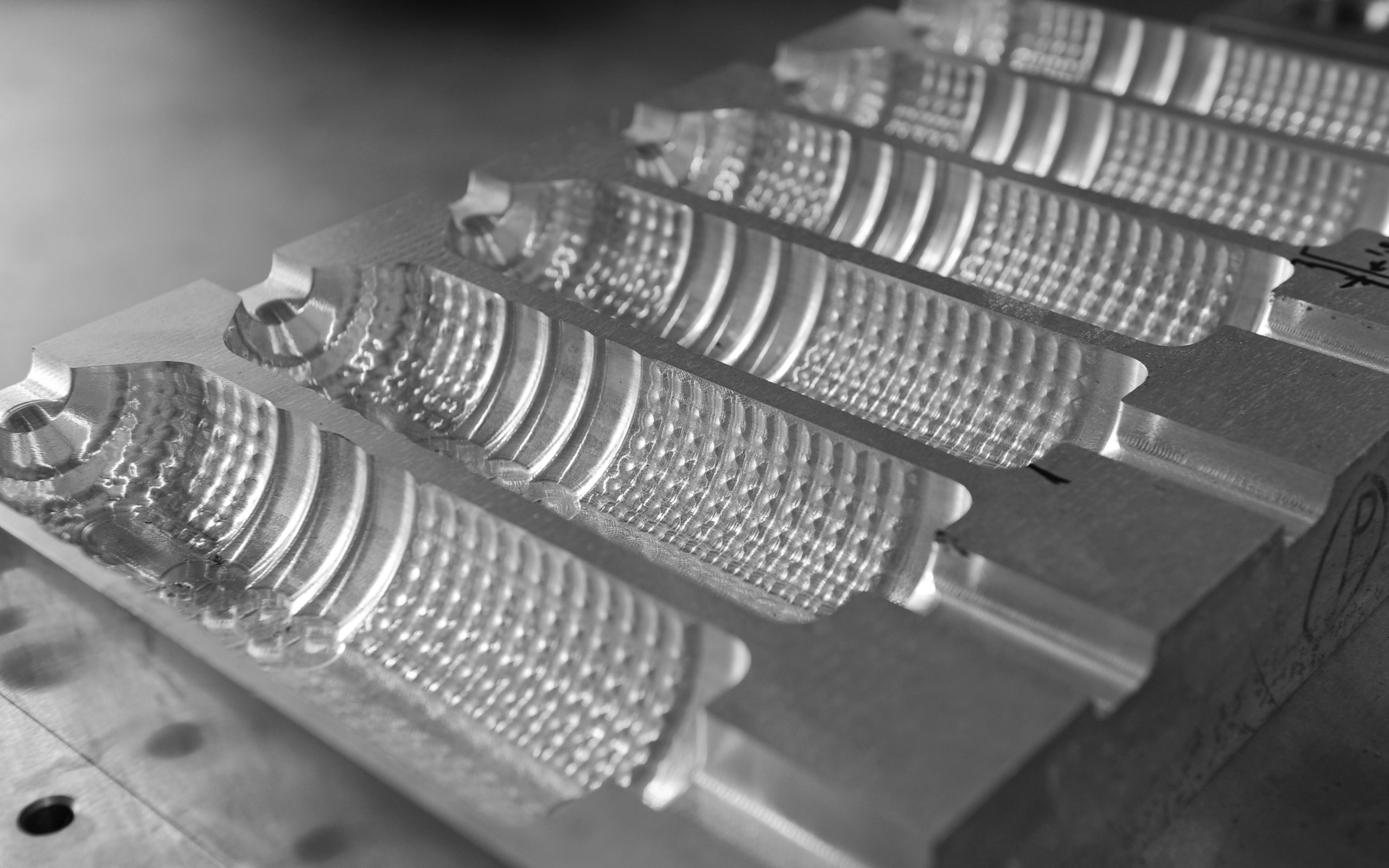
The final mold
Why is surface finishing needed?
Although mold manufacturing has gone through multiple steps, there are still some surface defects and functional requirements in actual use, which prompts the mold to be further finished before use. The following are the main pain points:
- Minor roughness and processing marks: Even if the surface finishing has significantly improved the flatness of the mold surface, due to process precision and material limitations, minor processing marks may remain on the surface. These minor irregularities will have an adverse effect on the wear resistance of the mold and may cause unstable product quality during the production process.
- Demolding performance requirements: The smoothness of the mold surface directly affects the demolding effect of the product. If the surface of some molds is not smooth enough, problems such as scratches or jamming may occur when the molded product is demolded. Proper surface finishing can make the mold surface smoother, which helps the product to be demolded smoothly and improves production efficiency.
- Surface hardening and wear resistance requirements: The mold needs to withstand high-frequency repeated use, so the surface must have good wear resistance. Through surface finishing, the hardness of the mold surface is further improved, which prolongs its service life and reduces the replacement frequency and maintenance cost.
- Consistent surface quality: The mold must ensure consistent surface quality of each batch of products during mass production. Finishing can eliminate minor processing errors and make the mold surface more uniform, thereby ensuring production stability and product consistency.
Effects that surface finishing can achieve
Improve mold durability
The mold surface after finishing is more wear-resistant, can cope with high-frequency production environments, and significantly extend the service life of the mold. Especially when producing high-precision and high-strength molds, surface finishing can effectively reduce the wear rate of the mold, thereby reducing the replacement frequency and reducing production costs.
Improve surface finish
Finishing can effectively eliminate minor defects and processing marks on the mold surface, making it smoother. The improvement of the surface finishing not only improves the demoulding performance of the mold but also makes the surface of the product more uniform and smooth. This is particularly important for automotive and electronic product molds, which can reduce the defective rate of the product and improve the quality of the appearance.
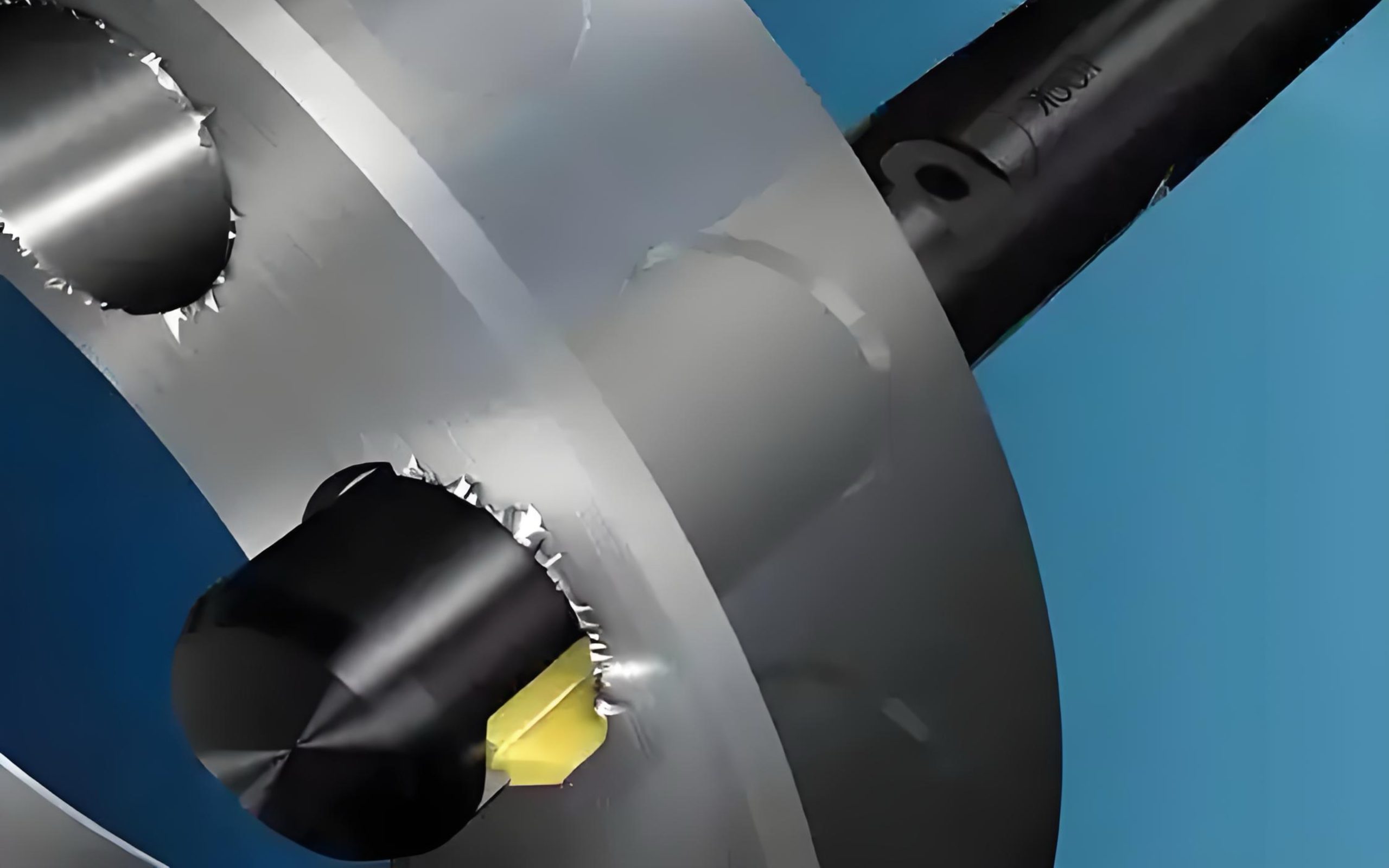
Unnoticeable rough edges
Enhance anti-corrosion performance
During use, the mold is easily corroded by moisture and acid-base substances in the environment, affecting its life and performance. Finishing can form a dense protective layer on the mold surface, improve its anti-oxidation and anti-corrosion properties, and is especially suitable for industries with high requirements for environmental tolerance, such as aviation and shipbuilding.
Ensure product quality consistency
The finished mold can achieve consistency in product surface quality in mass production, avoiding defects in finished products caused by differences in mold surface. For molds produced in large quantities, this consistency can greatly improve production efficiency, and reduce defective rates and rework times.
Advantages of sandblasting finishing
In the mold manufacturing industry, sandblasting surfac efinishing is widely used in surface treatment due to its low cost, high efficiency, and flexible control methods. The sandblasting process not only has advantages in cost and ease of operation but also can achieve detailed surface effect control.
- Fine control of surface roughness
Sandblasting can accurately control the surface roughness by selecting media with different particle sizes to achieve micron-level accuracy. For occasions where mold surface accuracy is high, sandblasting is an important process to achieve the ideal finish.
- Flexible surface effects
Through different combinations of sandblasting media (such as ceramic beads, alumina, etc.), sandblasting can achieve a variety of surface effects, such as matte, gloss, and fine textures, to meet the needs of different industries and products. For personalized needs in mold manufacturing, sandblasting can provide a more flexible surface treatment method.
- Low-cost and convenient operation
Compared with surface finishing processes such as laser and chemical treatment, sandblasting has lower costs and is suitable for mass production and surface treatment needs of large areas and complex structures. In the mold manufacturing industry, sandblasting not only improves processing efficiency but also reduces overall operating costs, which is especially suitable for cost-sensitive manufacturing companies.
Application scenarios
The wide application of sandblasting surface finishing in the mold manufacturing industry solves the surface treatment problems in many industries. The following are some common industries and application cases to show how sandblasting can improve mold performance and production efficiency for specific needs:
Plastic product molds
For molds of plastic products, sandblasting surface finishing can not only remove burrs and oxides remaining on the mold surface, but also reduce surface roughness, make the finished surface smoother, and enhance the aesthetics and user experience of the product.
Sandblasting can also achieve matte or high-gloss effects by selecting different media to meet the appearance requirements of different products.
Plastic product factories now usually use sandblasting technology to surface treat the injection molds they produce, which effectively reduces the roughness of the plastic product surface, improves the surface gloss, and reduces scratches, which improves the overall feel and visual effect of the plastic product.
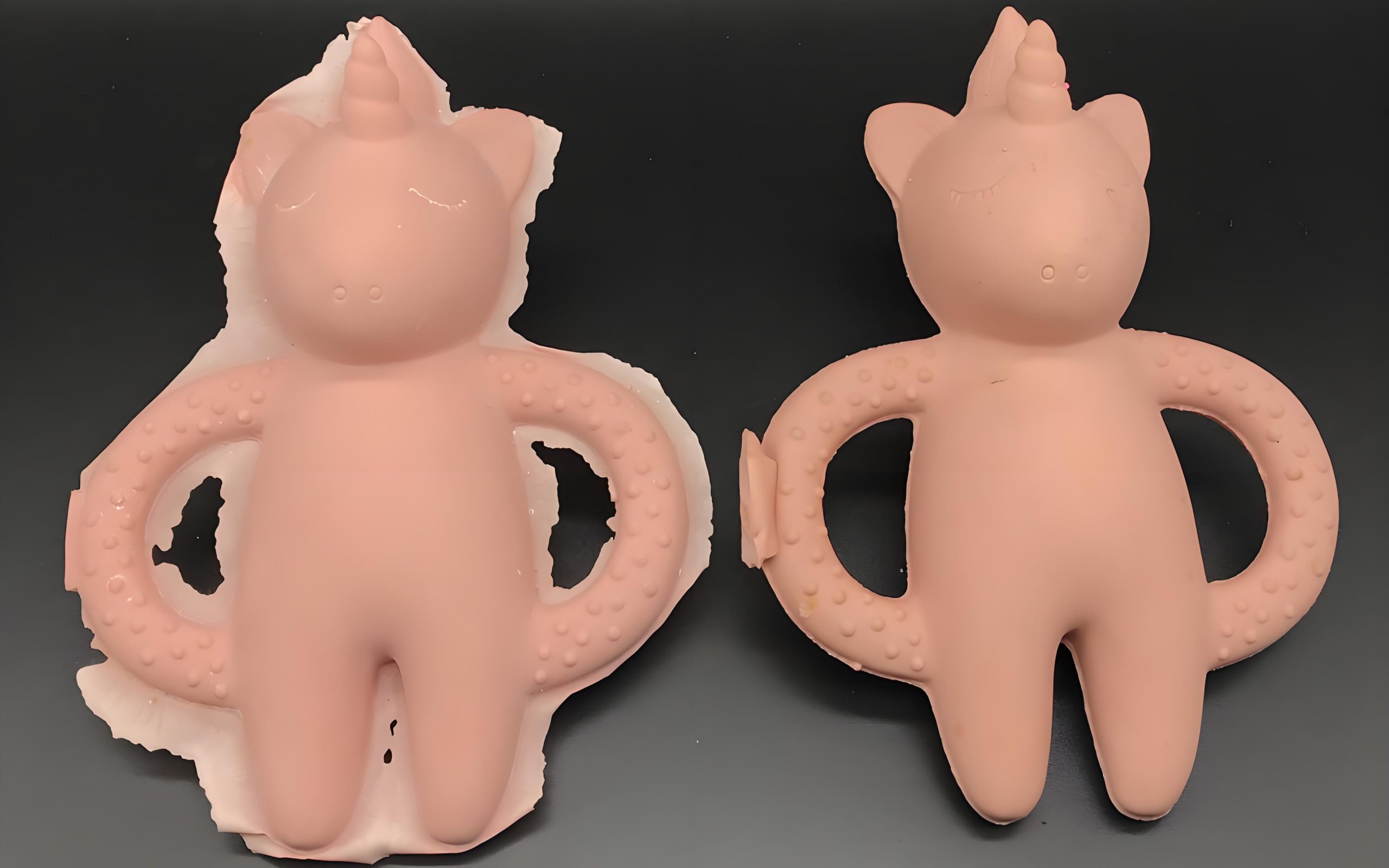
Effect comparison
Electronic product molds
The molds of electronic products require high surface quality, especially in the production of some precision electronic components (such as mobile phone housings, display screen frames, etc.), the smoothness and defect-freeness of the molds are crucial.
Sandblasting surface finishing can not only eliminate minor surface defects but also reduce friction between electrical components and improve the overall product appearance quality.
In the mold finishing process of electronic brands, sandblasting can be used to remove fine burrs on the mold surface and achieve a matte visual effect by selecting appropriate sandblasting media (such as ceramic beads). Not only can it increase the service life of the mold, but it also ensures the consistency of the appearance of each electronic component and avoids defects in the production process.
Automotive molds
In the automotive industry, molds need to meet the requirements of high precision, high finish, and durability, especially when producing appearance parts (such as body shells, bumpers, etc.).
Sandblasting finishing can not only remove fine burrs and oxides on the mold surface but also enhance the demolding performance of the mold, ensuring the smoothness of the product surface, thereby reducing defects and improving production efficiency.
When automobile manufacturers produce large quantities of plastic shell molds, they can use sandblasting to finish the mold, which can effectively reduce scratches during demoulding and improve the wear resistance and service life of the mold. Once the failure rate of the production line decreases, customer satisfaction will naturally increase significantly.
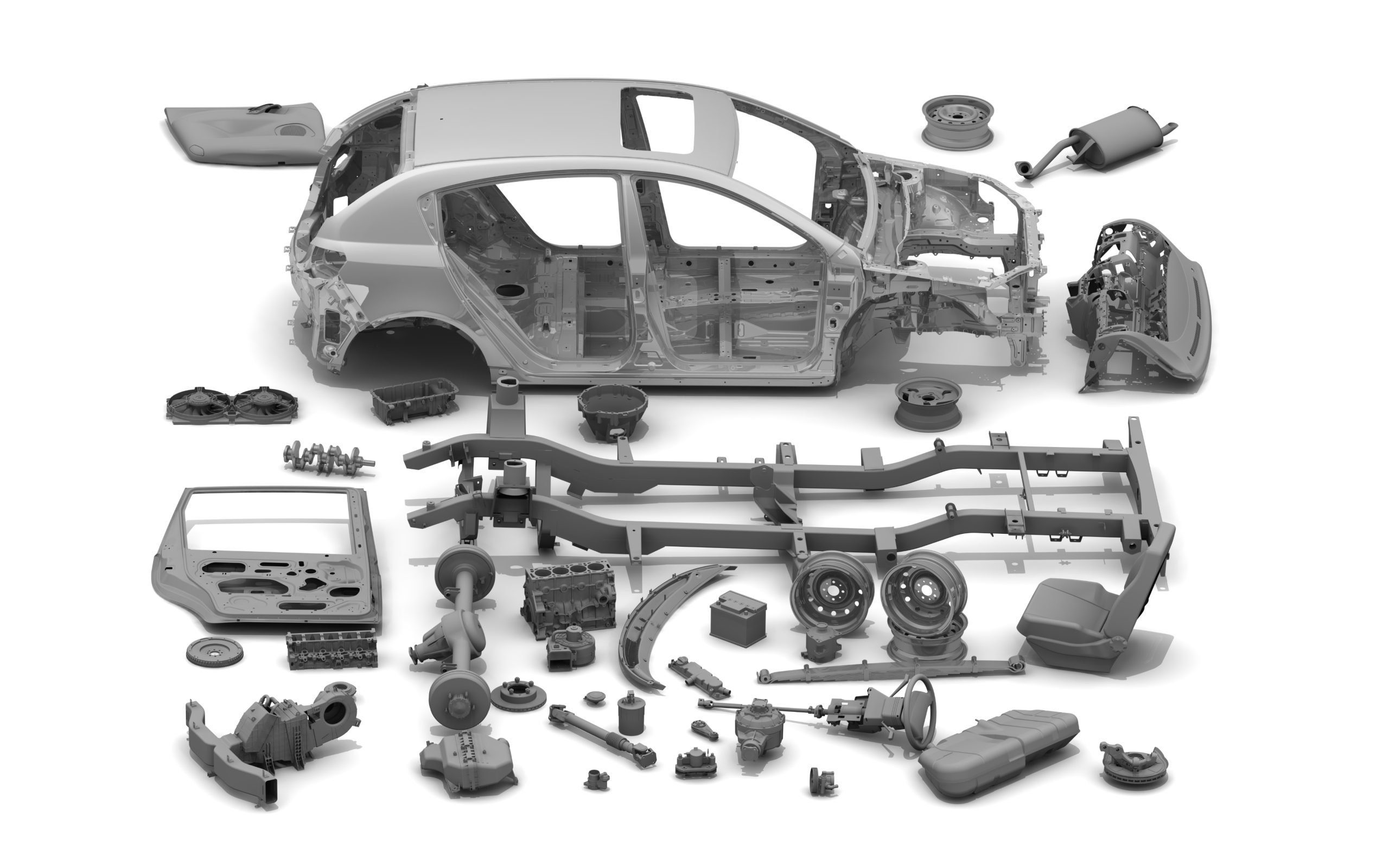
Requires highly refined and perfect car models
Aerospace device molds
The aviation manufacturing field has extremely strict requirements for the precision and durability of molds. Sandblasting surface finishing can enhance the wear resistance and corrosion resistance of the mold, especially in aviation device molds. Sandblasting can effectively improve the high-temperature resistance and corrosion resistance of the mold, extend the service life of the mold, and reduce the defective rate.
In aviation parts manufacturing companies, sandblasting technology is used for mold surface treatment to improve the wear resistance and corrosion resistance of the mold. Through sandblasting finishing, the performance of the mold in high-temperature and acidic environments has been significantly improved, which greatly extends the service life of the mold and improves the safety and reliability of production.
Recommended sandblasting media
The effect of sandblasting surface finishing is closely related to the selected sandblasting media. According to different mold materials, surface effect requirements, and durability requirements, it is very critical to choose the right sandblasting media.
- Applicable scenarios: Alumina medium has moderate hardness and is often used to remove oxide scale and burrs on the mold surface. It is particularly suitable for the surface treatment of durable molds, such as steel molds, to remove oxides and improve surface quality.
- Advantages: Alumina particles have strong cutting force and moderate hardness, which can effectively remove surface impurities without damaging the mold material. Suitable for high-frequency, wear-resistant molds.
Alumina blasting media
Ceramic beads
- Applicable scenarios: Ceramic beads are suitable for molds that require a high finish, commonly found in industries such as automobiles and electronic products, and can keep the mold surface consistent with a matte effect.
- Advantages: Ceramic beads are not easy to break, and the particles are uniform, which is suitable for molds that require high-precision and high-finish surface effects. It can produce a delicate surface treatment effect without affecting the hardness and strength of the mold material.
Glass beads
- Applicable scenarios: Glass beads are often used for the surface finishing of precision molds, which can remove subtle defects on the mold surface and provide a soft surface polishing effect. Applicable to industries such as precision electronics and medical devices.
- Advantages: Glass beads are softer and suitable for fine processing. They can provide a smooth surface polishing effect without causing excessive wear to the mold. Suitable for precision molds that require a high surface finish and no scratches.
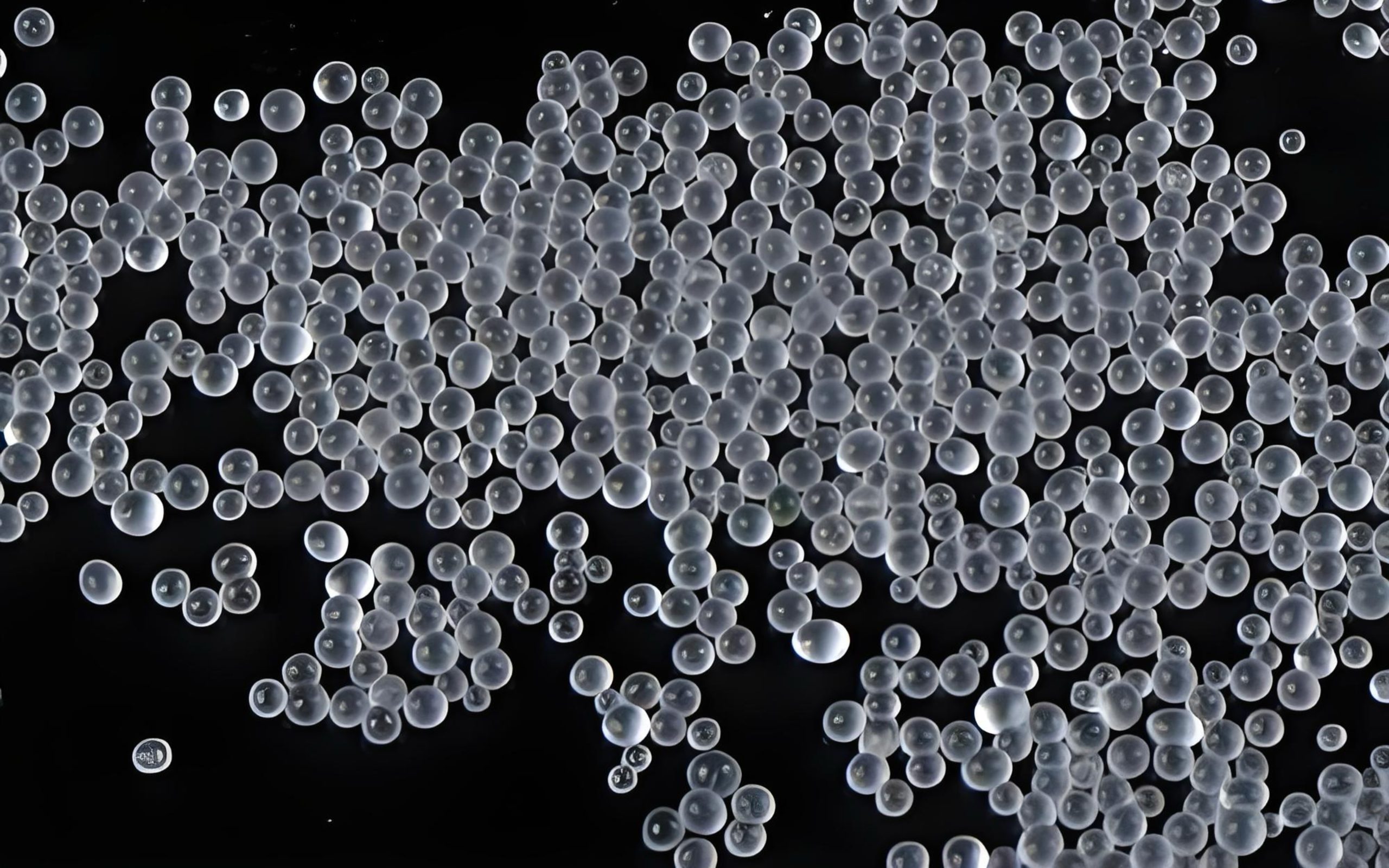
Glass beads
Stainless steel shot
- Applicable scenarios: A stainless steel shot is suitable for molds with higher hardness, especially molds that need to enhance surface strength, such as some aviation device molds or high-strength metal molds.
- Advantages: Stainless steel shot has a higher hardness and can enhance the durability of the mold while enhancing the surface strength of the mold. Its higher hardness makes it suitable for processing high-hardness molds and increasing the wear resistance of the mold surface.
Frequently Asked Questions
Q1: Can sandblasting finish process all kinds of mold materials?
A1: Sandblasting finish is suitable for most mold materials, including steel, aluminum, copper, plastic, etc. However, materials with higher hardness (such as titanium alloys and some high-strength steels) may require harder sandblasting media, such as stainless steel shot or alumina, to ensure the ideal surface effect.
Q2: Will the surface be scratched after sandblasting?
A2: If the appropriate sandblasting media is selected and the sandblasting pressure is controlled, scratches are usually not left. Choosing softer sandblasting media (such as glass beads) and lower sandblasting pressure can effectively avoid scratches on the mold surface.
Q3: What are the advantages of sandblasting compared to other finishing methods (such as grinding, and EDM)?
A3: Compared with grinding and EDM, sandblasting has higher processing efficiency and lower cost, especially suitable for mass production. Sandblasting can effectively remove surface burrs and oxide scales and is easy to operate. It is suitable for applications with high requirements for mold surface quality and large production volume.
Q4: How to choose the right sandblasting media?
A4: The selection of the right sandblasting media is mainly based on the mold material, the required surface effect (such as smoothness or matte effect), and the durability requirements of the mold. For example, ceramic beads are suitable for molds with high smoothness requirements, aluminum oxide is suitable for molds to remove oxides, and glass beads are suitable for polishing precision molds.
Filters