October 27, 2024
In modern industrial manufacturing, surface preparation, as an important basic process, is directly related to the quality and performance of products. The standardization of surface preparation not only improves the adhesion of coatings and bonding materials, but also effectively extends the service life of workpieces. With the enhancement of environmental awareness, the continuous advancement of technology and the advancement of international standardization, surface preparation standards are moving towards a more stringent, meticulous and sustainable direction. This article will explore in depth the development trend of current surface preparation standards, future changes, and the impact of these changes on various industries.
What is surface preparation?
Definition of surface preparation
Surface preparation refers to a series of cleaning, roughening, deoxidation or other physical and chemical treatments on the surface of workpieces or materials to lay the foundation for subsequent processing or coating processes (such as painting, electroplating, bonding, etc.). This process is widely used on different materials such as metals, plastics, composite materials, etc., with the aim of improving the cleanliness and roughness of the workpiece surface, thereby enhancing the adhesion and durability of subsequent processes.
The core role of surface preparation
As a core step in industrial manufacturing and processing, surface preparation is important in the following three aspects:
- Improving the adhesion of coatings and bonding: Surface treatment can improve surface roughness and cleanliness, thereby greatly improving the adhesion of coatings, adhesives, etc.
- Enhancing the corrosion resistance of material surfaces: Removing surface oxides or impurities during pretreatment can delay or prevent corrosion of materials in specific environments.
- Improving surface flatness and aesthetics: Through sandblasting, polishing, etc., the surface of the material is made smoother, which is convenient for further decorative treatment.
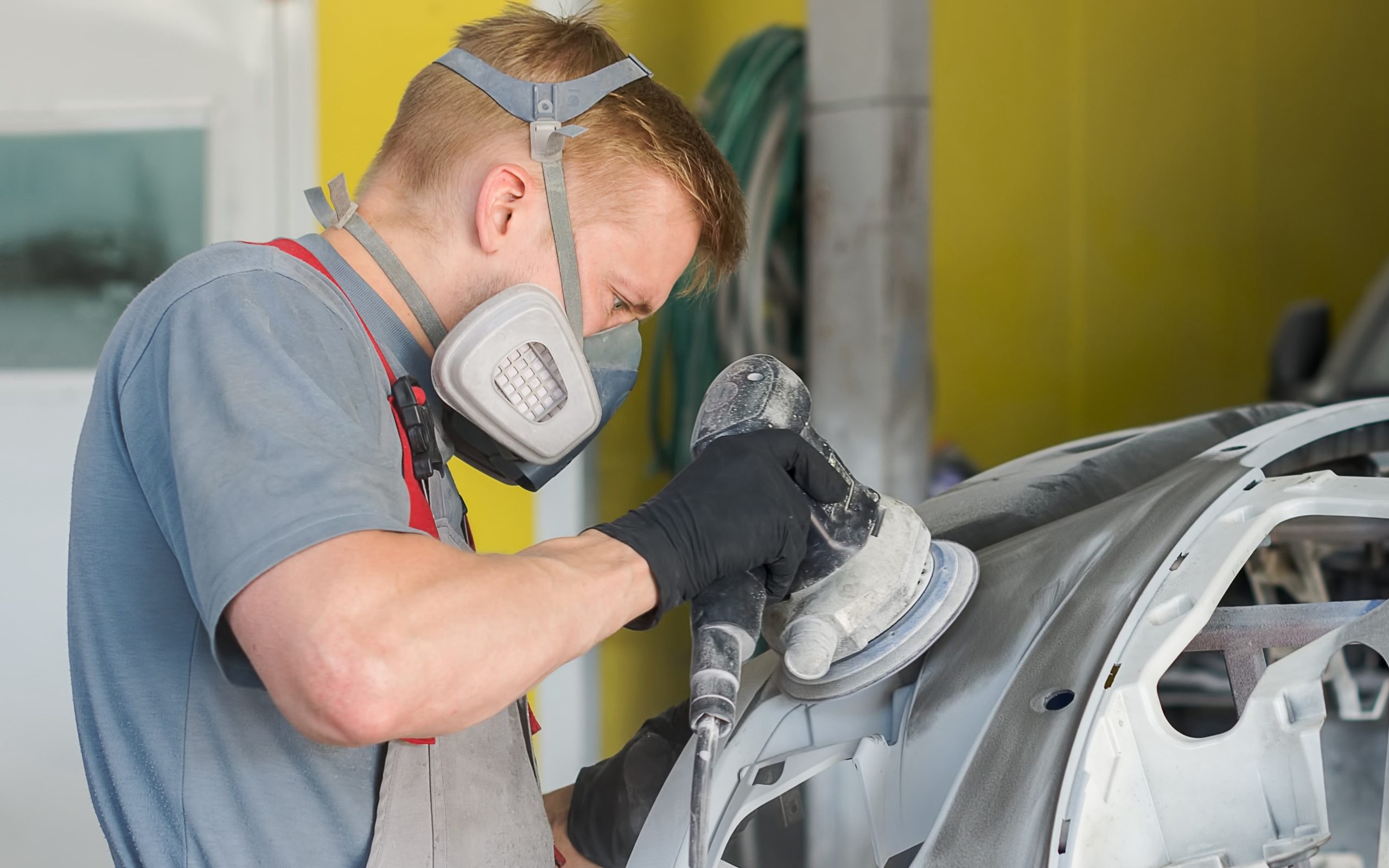
Standards for surface preparation
Why standards are needed for surface preparation
The establishment of surface preparation standards aims to ensure that each workpiece can achieve a consistent quality level after preparation by standardizing process flow and quality control requirements. The benefits of standardization are mainly reflected in the following three aspects:
- Improving production efficiency: Through standardized operating procedures, trial and error time and material waste are reduced, thereby improving the efficiency of the entire production process.
- Ensure product quality consistency: If workpieces from different batches and by different operators follow the same standards, it will help ensure product quality consistency and avoid quality fluctuations caused by differences in operation or materials.
- Extend workpiece service life: Strict surface preparation standards help improve the stability and durability of the coating or bonding layer, thereby extending the life of the workpiece in harsh environments.
Requirements for surface preparation in different application fields
Surface preparation is widely used in various industries, but the requirements of different application fields are also different. For example:
- Automotive and aviation fields: High-strength adhesion and durability are required to ensure that parts maintain stable performance in high temperature, corrosive environments, etc.
- Shipbuilding and oil and gas industries: Equipment and structures are exposed to corrosive environments such as moisture and salt for a long time, and the anti-corrosion performance requirements of surface treatment are particularly strict.
- Medical devices and electronics: Such applications have extremely high requirements for surface cleanliness. Surface preparation must not only ensure strong adhesion, but also avoid factors such as chemical residues that affect the biocompatibility or electronic performance of the material.
Through standardized surface preparation, each industry can obtain a more reliable and specific workpiece surface, thereby ensuring the final performance of the product.
Common international standards
Globally, many countries and regions have developed their own surface preparation standards. Here are some of the common standards:
- ISO standards: The International Organization for Standardization (ISO) has published several standards on surface preparation, covering specifications for different materials and processes. For example, ISO 8501 defines different levels of rust removal on metal surfaces, and ISO 11124 regulates the quality and performance of abrasive materials.
- ASTM standards: The American Society for Testing and Materials (ASTM) has developed many standards related to surface preparation, especially for the pretreatment of metals and composites. For example, ASTM D4417 specifies the measurement method for the surface roughness of coated substrates, while ASTM B322 is a general specification for metal surface cleaning.
- SAE standards: The Society of Automotive Engineers (SAE) provides special standards for metal surface treatment in the automotive and aviation fields, such as SAE J400 for measuring the surface roughness of automobile bodies. Such standards are crucial in ensuring the consistency of the quality of vehicles and aviation parts.
- European standard EN, Japanese standard JIS: Europe and Japan have EN standards and JIS standards respectively, for example, EN 13788 regulates the cleanliness of metal surfaces, and JIS G3141 defines the surface treatment requirements for steel. These standards play an important role in ensuring product quality and market consistency in their respective regions.
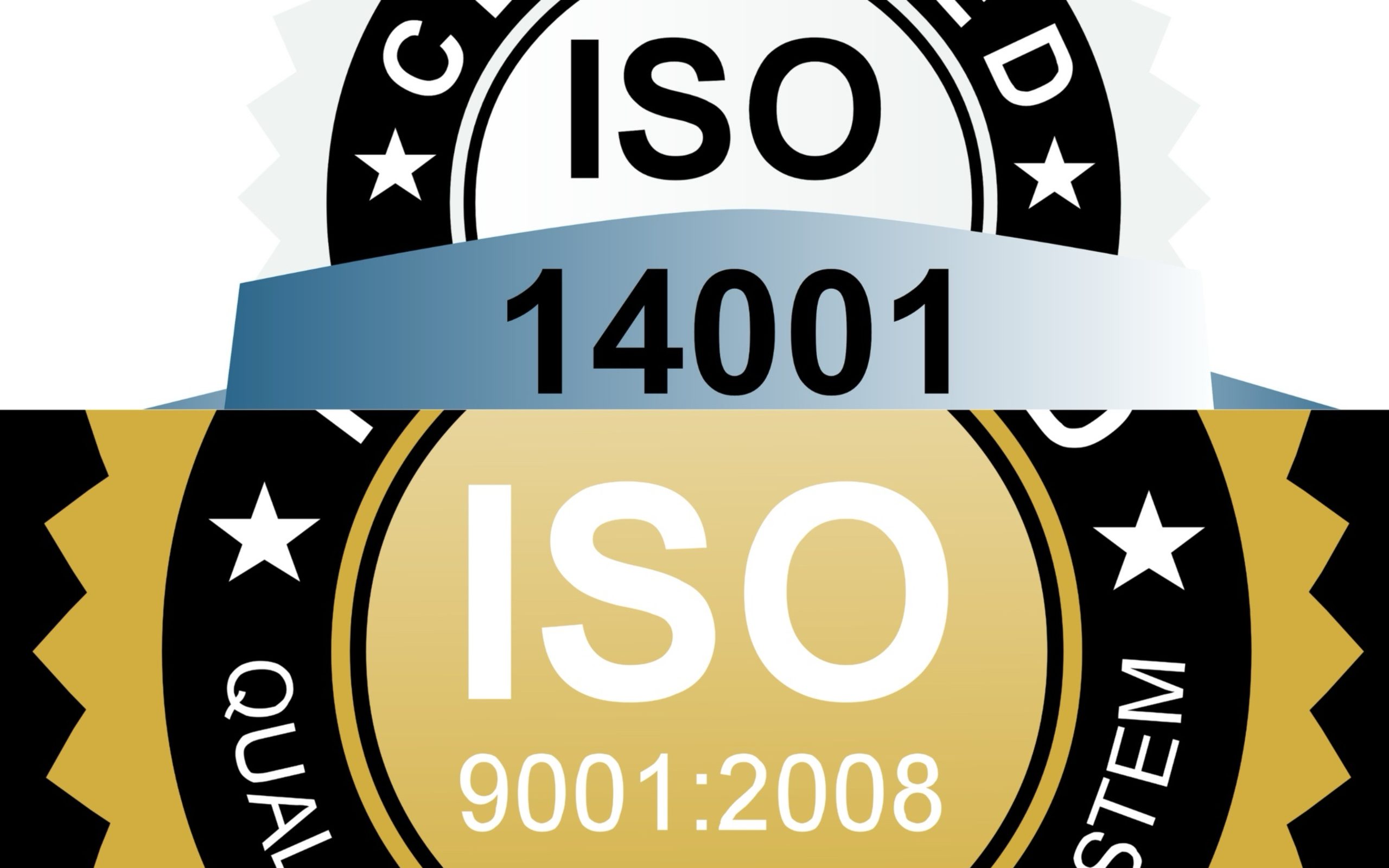
Regional differences and reasons for standards
There are certain differences in standards between different countries and regions, and this difference usually comes from the following three aspects:
- Environmental regulations: Europe and Japan have higher requirements for environmental protection, so their standards may be more inclined to reduce the use of hazardous substances, while some countries may have more relaxed requirements in this regard.
- Industry maturity: The manufacturing industry in some countries started earlier, so the standards are more mature and detailed, while emerging markets may have relatively limited coverage of standards.
- Adaptation needs of export products: Many manufacturers pay special attention to the standards of the target market when exporting products to ensure that the products can pass the inspection smoothly and obtain market access qualifications.
Impact of standardization
International surface preparation standards provide a common language for global manufacturers. By following these standards, parts or equipment produced in various countries can meet unified quality requirements, thereby simplifying barriers to cross-border trade and cooperation. For example, manufacturers can produce and test according to the cleanliness standards of ISO 8501, making products more universal worldwide.
Surface preparation standards for different workpieces and materials
Due to the differences in materials, application environments and functional requirements, different materials and workpieces have different standards for surface preparation. According to these differences, the technical means and standardization requirements for preparation will vary. The following are the preparation standards for several common workpiece materials and their applicability.
Metallic materials
Metallic materials are widely used in machinery, construction, automobiles, aviation, and other fields, and the preparation standards are particularly strict. Different metal materials have different pretreatment technologies. The following are 3 typical metal material preparation requirements.
- Steel: Steel is one of the most widely used metal materials in industrial applications, and the common surface treatment standard is Sa 2.5 (ISO 8501). This standard requires the surface to reach a certain level of rust removal and roughness to ensure the adhesion and durability of subsequent coatings.
- Aluminum alloy: Aluminum alloy is widely used in fields with high lightweight requirements such as aviation, automobiles, and construction. Aluminum surface treatment standards usually involve the removal and roughening of the surface oxide layer to increase coating adhesion. Common preparation methods include sandblasting, pickling, and phosphating.
- Copper and its alloys: Copper alloys are mainly used in the electronics, electrical, and plumbing industries. Due to their good electrical and thermal conductivity, surface preparation standards emphasize cleanliness and non-destructive surface conductivity.
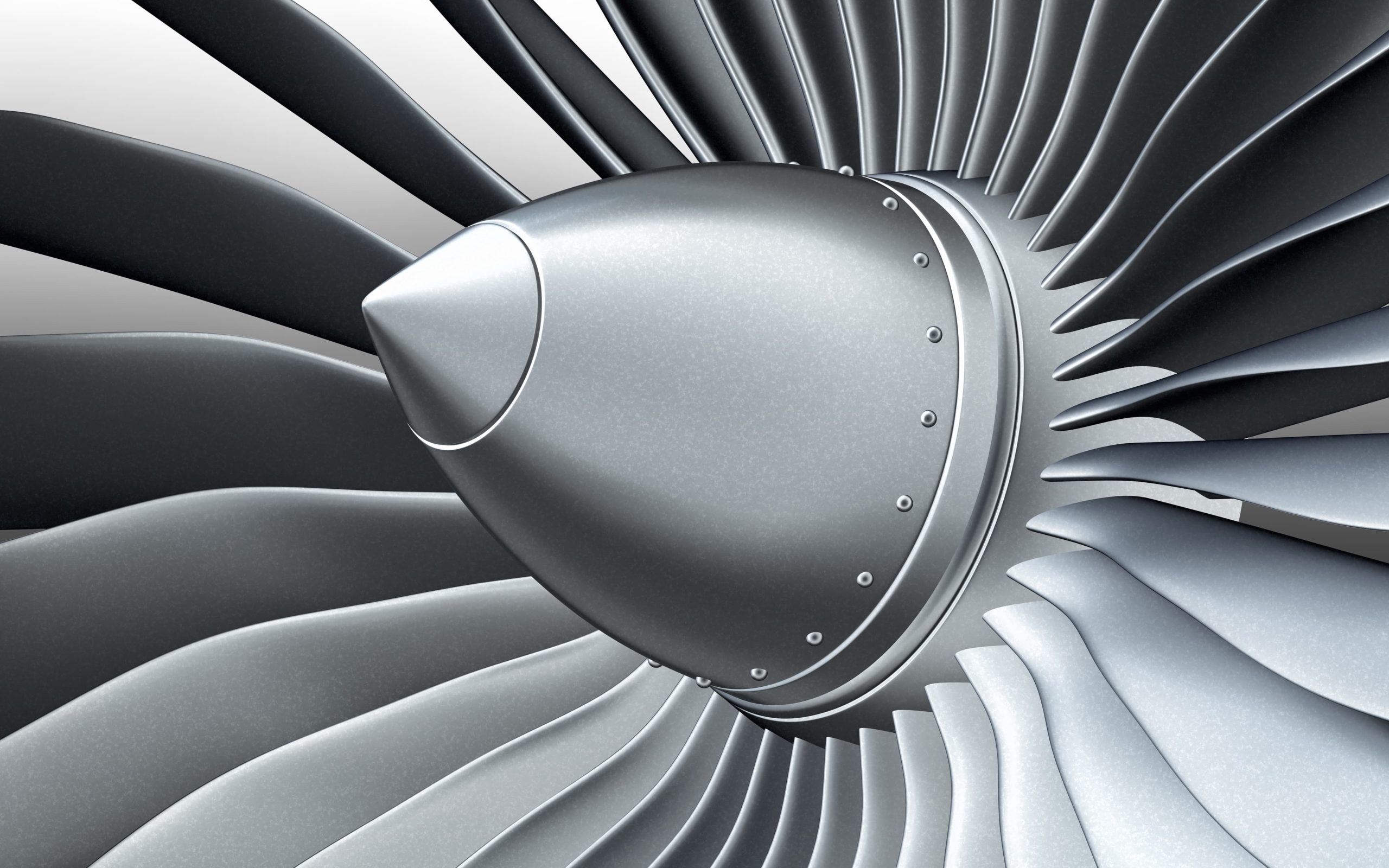
Non-metallic materials
Non-metallic materials such as plastics, ceramics and glass are widely used in the automotive, electronics, construction and other industries. Due to different material properties, the focus of surface treatment is on the control of cleanliness and roughness.
- Engineering plastics (such as ABS, PC, etc.): In the automotive, electronics and other industries, engineering plastics such as ABS and PC are often used for housings and structural components. In order to ensure the adhesion of the coating, the plastic surface usually needs to be cleaned and slightly roughened.
- Ceramics and glass: Ceramics and glass are widely used in medical equipment, electronic product housings and other fields, and their preparation standards usually focus on surface cleanliness and wear resistance.
Composite materials
Composites (such as carbon fiber reinforced composites, CFRP) have important applications in high-end industries such as automobiles, aviation and energy. The pretreatment standards for such materials usually focus on surface roughness and cleanliness to ensure the adhesion of adhesives and coatings.
- Carbon fiber composites (CFRP): CFRP is widely used in the aviation and automotive fields and is favored for its lightweight and high strength. However, the surface treatment of CFRP should be carried out with extreme care to avoid damaging the structure of the material itself.
- Glass fiber composites (GFRP): Glass fiber is widely used in industries such as shipbuilding and construction, and its surface treatment standards focus on roughness and cleanliness.
Precision electronic components and medical devices
In the field of precision electronic components and medical devices, the standards for surface preparation have extremely high requirements for cleanliness and surface residue-free to ensure equipment performance and biosafety.
- Electronic components: The requirements for surface preparation of precision electronic components are mainly dust-free and residue-free
- Medical devices: The surface preparation standards for medical devices, especially surgical instruments, are more stringent, which must ensure the biocompatibility of the material and avoid any harmful substances remaining on the surface.
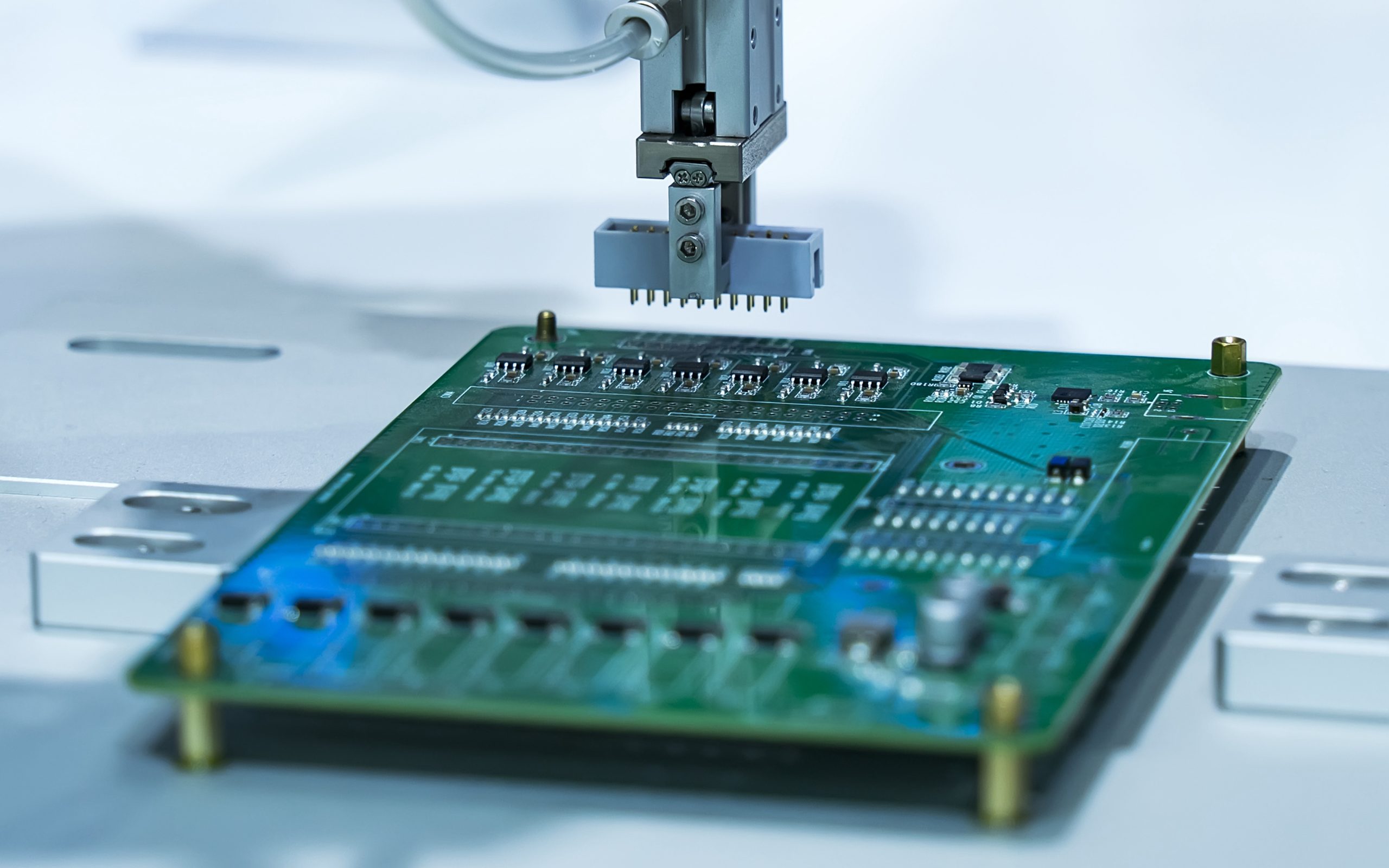
Adjust the pretreatment standards according to the application environment.
In different application environments, the standards for surface preparation will be adjusted. Environmental factors (such as temperature, humidity, and chemical corrosiveness) and the needs of the final use of the workpiece have different requirements for preparation. According to the differences in the environment, the depth of pretreatment, material selection, and quality control methods also need to be adjusted accordingly.
- Preparation requirements for different working conditions
- High-temperature environment: When the workpiece is used in a high-temperature environment, the surface preparation standard usually requires the workpiece to have high-temperature resistance and oxidation resistance. Sandblasting preparation is one of the effective surface modification methods.
- Chemical corrosion environment: Corrosive environments (such as marine, oil, and gas industries) can cause rapid oxidation or damage to the metal surface. Therefore, the pretreatment standard usually requires that the surface be free of oxides and other impurities and have a certain degree of roughness so that the coating can adhere more firmly.
- Environment with drastic humidity changes: In an environment with large humidity fluctuations (such as outdoor buildings, and port equipment), the coating of the workpiece is prone to peeling, blistering, and other problems. Therefore, the preparation standard has strict control over cleanliness and roughness to ensure the stability of the coating in a dry and wet alternating environment.
- The impact of end-use on standards
The end use of the workpiece largely determines the standard of surface preparation. Different industries need to put forward special requirements for pretreatment in terms of aesthetics and functionality.
- Industries with high aesthetic requirements (such as consumer electronics and home appliances): In these fields, the appearance quality, and durability of the surface are particularly important. The pretreatment standards have high requirements for surface finish and removal of fine burrs.
- Fields with high functional requirements (such as military industry and aerospace): The surface preparation standards of high-demand industries such as military industry and aerospace are more stringent, requiring the surface to be wear-resistant and corrosion-resistant to ensure the adhesion and functionality of the coating under extreme conditions.
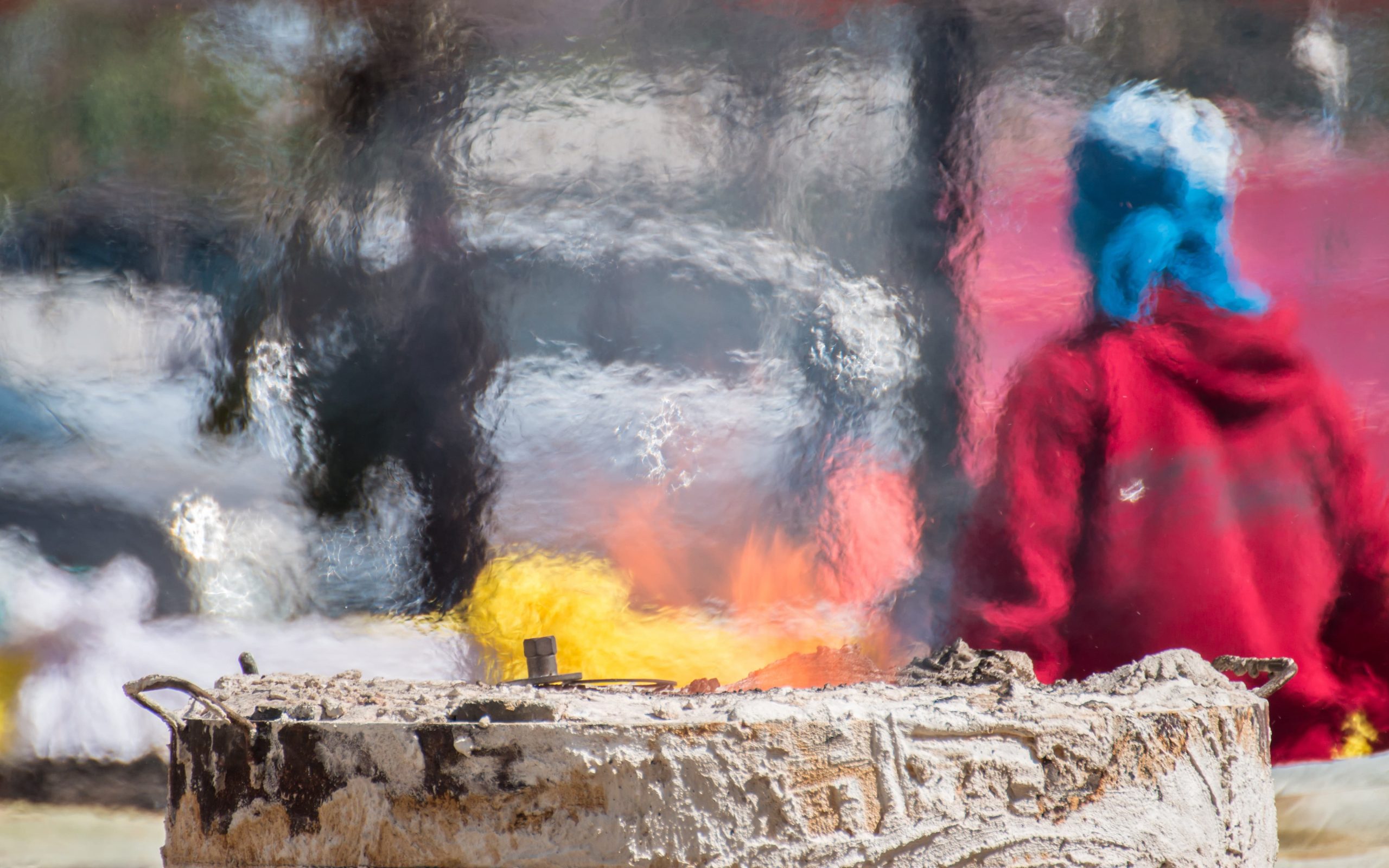
Quality control and evaluation standards for the surface preparation process
In the industrial production process, quality control of surface preparation is crucial. Through strict measurement and evaluation methods, it can be ensured that the pretreated workpiece meets various performance requirements, providing a good foundation for subsequent coating and protective treatment.
Measurement method of surface cleanliness
Surface cleanliness is one of the important indicators in the surface preparation process, which is related to the adhesion, corrosion resistance, and overall quality of the coating. Commonly used surface cleanliness evaluation methods include the following 3 types:
- Visual inspection: Visual inspection is the most basic cleanliness evaluation method, through professional observation to see whether there are obvious pollutants, oil stains, oxide scale, etc. on the surface. However, visual inspection is subjective and is usually used as a preliminary evaluation method.
- Wipe test: The wipe test can detect whether there are residual tiny contaminants on the surface of the workpiece. Cleanliness is evaluated by wiping the surface with a white cloth or wiping tool and then checking whether it is contaminated. This method is suitable for workpieces with higher requirements, such as aviation or electronic products.
- Microscope inspection: Microscope inspection can magnify the surface and detect tiny impurities or contamination residues. This method is suitable for workpieces that require high-precision pretreatment, such as high-purity metals and precision parts. HLH sandblasting materials can provide efficient and residue-free cleaning treatment to ensure that microscopic inspection is qualified.
Common cleanliness classification standards: Cleanliness classification standards are used to clarify cleanliness requirements, such as the Sa standard of ISO 8501-1 and the SP level in the American standard. HLH sandblasting materials can meet cleanliness levels such as Sa 2.5 or Sa 3, so that the workpiece reaches a uniform and residue-free state. 、
Measurement of surface roughness
Roughness is another important indicator after surface preparation. Surface roughness has a direct impact on coating adhesion and corrosion resistance, so the measurement of roughness is crucial. Commonly used roughness measurement tools include stylus roughness meters and optical roughness meters. Stylus instruments measure by contacting the surface with a probe, while optical instruments use the reflection and scattering of light to evaluate surface roughness.
Specific requirements for roughness in different industries: Roughness requirements vary from industry to industry. For example, the automotive and aviation fields usually require medium roughness to provide stronger adhesion for the coating, while the home appliance or electronics fields may require lower roughness to ensure beauty and feel.
Testing of coating adhesion
Coating adhesion is one of the final manifestations of the surface preparation effect. Good surface preparation can enhance the bonding between the coating and the substrate, thereby extending the service life of the workpiece. Common adhesion test methods include:
- Cross-cut test: The cross-cut test is one of the common methods for testing coating adhesion. By scratching a grid on the surface coating, observe its peeling under the action of external force.
- Shear strength test: The shear strength test evaluates the coating’s adhesion in the vertical direction and is usually used to test thicker coatings or functional coatings.
Surface preparation standards play a vital role in improving product quality, reducing production costs and protecting the environment. Standardized pretreatment not only brings long-term economic value, but also gives companies an advantage in the fierce market competition. For companies and practitioners, flexibly selecting appropriate standards according to the characteristics of different markets and workpieces is the key to achieving sustainable development. Only by constantly adapting to industry changes and paying attention to environmental protection and technological progress can we be invincible in the future market.
Filters