Ceramic beads VS glass beads: the best choice for sandblasting cleaning
December 12, 2024
Sandblasting cleaning is an efficient and environmentally friendly surface treatment technology widely used in many industrial manufacturing fields. Its core goal is to remove dirt, scale, and welding residues on the surface while ensuring the integrity and precision of the workpiece.
In sandblasting cleaning, glass beads and ceramic blasting beads are two commonly used media materials. This article will conduct a comparative analysis of their cleaning efficiency, performance, scope of application, and cost, and deeply analyze the superiority of ceramic beads through real cases to help customers better choose suitable media products.
Customer pain point analysis
In the field of surface cleaning, customers usually face the following key pain points, which not only directly affect production efficiency, but may also significantly increase the operating costs of enterprises.
Cleaning efficiency and process stability: Enterprises need to complete large-area surface cleaning in a short time to ensure consistent cleaning effects.
Cost control and recovery rate: In mass production, the initial purchase cost and long-term use cost of sandblasting media directly affect the overall budget.
Working environment and dust control: The sandblasting process will generate a large amount of microparticles and dust, which will affect the cleanliness of the working environment and may endanger the health of the operator. Especially in closed or poorly ventilated environments, the dust problem is particularly serious.
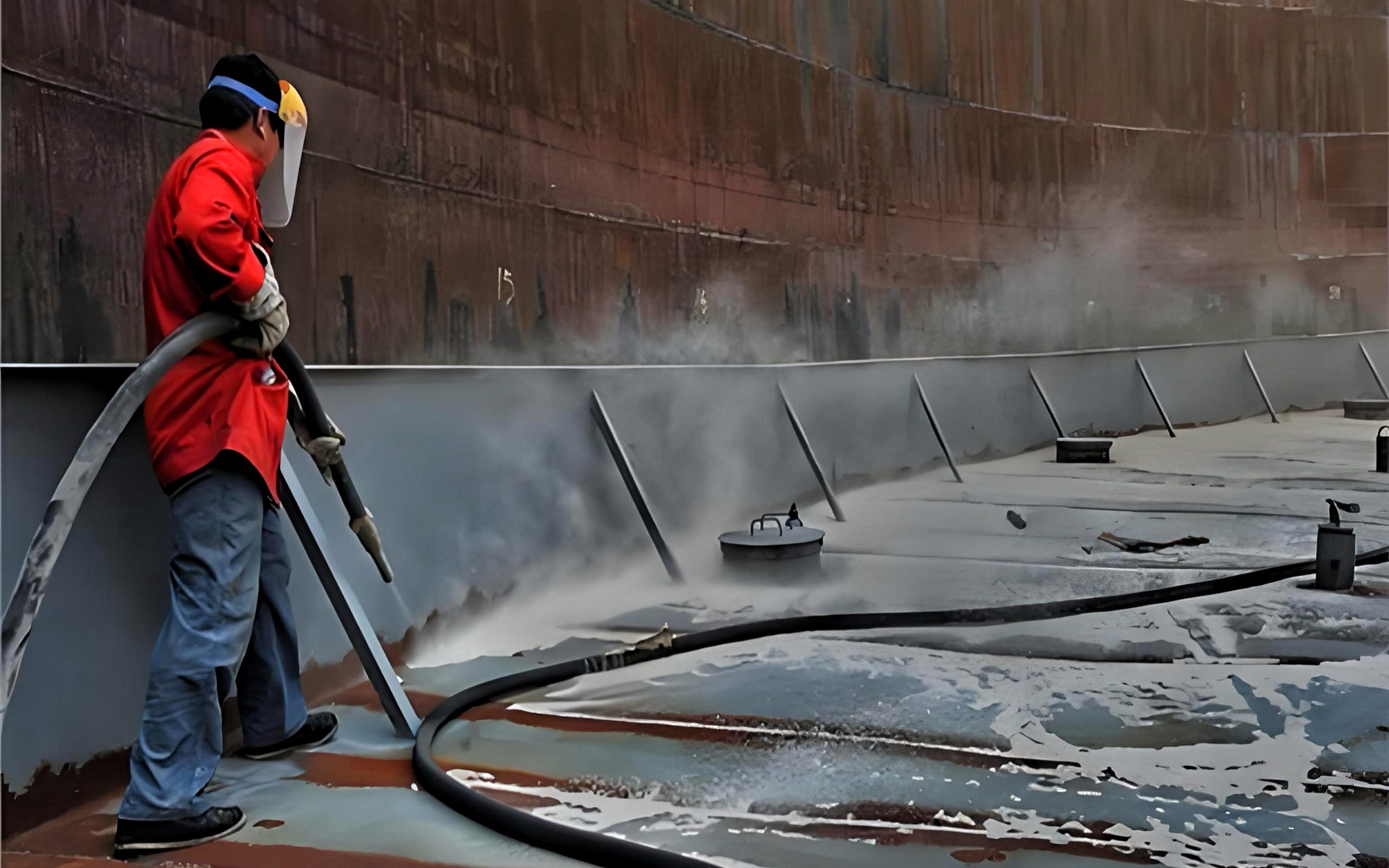
Material adaptability: Workpieces of different materials have very different requirements for sandblasting media.
Equipment compatibility and technical support: Replacing sandblasting media may require adjusting equipment settings, which increases technical complexity. At the same time, some media may cause wear to the equipment during long-term use.
Environmental and regulatory pressure: As global environmental regulations tighten, customers need more environmentally friendly sandblasting media while reducing the generation of industrial waste.
Performance comparison
Ceramic beads and glass beads have their characteristics in the field of sandblasting cleaning, and their performance differences make them suitable for different process requirements. This section will explore the advantages and disadvantages of the two media in five aspects: cleaning efficiency, particle stability, dust control, material compatibility, and long-term cost.
Cleaning efficiency
Ceramic blasting beads have excellent cleaning efficiency due to their high hardness (8-9 on the Mohs scale), especially when dealing with hard materials (such as stainless steel, and titanium alloy) or complex surfaces, they can quickly remove oxide scale and rust while maintaining the surface integrity of the workpiece.
Advantages: The combination of high hardness and regular rounded shape shortens its cleaning time by about 25%-40% compared with glass beads (the specific data depends on the material of the workpiece and the difficulty of cleaning).
Glass beads have a Mohs hardness of 5-6 and are suitable for medium and low-intensity cleaning tasks (such as plastic molds or aluminum parts). When cleaning high-hardness materials, the cleaning efficiency is significantly reduced and the particle breakage rate is significantly increased.
Disadvantages: Low cleaning efficiency and contaminants may remain on the surface of high-hardness materials.
Particle stability and life
Ceramic blasting beads have excellent toughness and pressure resistance, are not easy to break, and the particle life can reach 3-5 times that of glass beads. During long-term use, its physical shape and size remain stable, which helps to extend process consistency.
Advantages: A batch of ceramic beads can be recycled 50-70 times, significantly reducing the frequency of replacement.
Glass beads have a high breakage rate, and the particles become irregular in shape after 20-30 uses, and the cleaning efficiency gradually decreases.
Limitations: High breakage rate not only increases medium loss but may also lead to uneven surface strengthening.
(Click here to view the test content of the previous article)
Dust control and environmental performance
The low breakage rate of ceramic blasting beads directly reduces the amount of dust generated in the working environment, which is suitable for processes with high cleanliness requirements. In addition, its high recyclability (over 95%) makes waste management more environmentally friendly.
Advantages: Less particle decomposition during operation and low dust emissions help meet strict industrial environmental regulations.
Glass beads are prone to generate a lot of fine dust after being broken, and an additional air filtration system is required to reduce health risks. The cost of waste disposal is high and the environmental pressure is high.
Risks: The dust content may exceed industry standards, increasing the health risk of operators.
Material compatibility
Ceramic beads are suitable for a range of workpiece surface cleaning from flexible materials (such as aluminum alloy) to high-strength materials (such as titanium alloy, and stainless steel). Thanks to its hardness range and regular particle design, ceramic beads can achieve compatibility with different materials by adjusting the injection pressure.
Case: An automobile manufacturer uses ceramic blasting beads to clean aluminum suspension parts, and the depth of the compressive stress layer is increased by 30% without surface damage.
Glass beads are suitable for cleaning tasks of low-strength materials, but they may not clean enough on the surface of high-hardness workpieces, and may even cause microcracks or surface damage.
Limitations: Low compatibility, difficult to meet the needs of diversified materials.
Long-term cost analysis
The initial purchase cost of ceramic beads is usually higher than that of glass beads, but considering their high durability and low replacement frequency, the overall cost performance is better.
The following is an actual data analysis of an automotive parts manufacturer, showing the long-term cost-effectiveness of ceramic beads in actual production.
The company used glass beads for surface cleaning of aluminum alloy crankshafts, facing a high frequency of media replacement and high downtime, resulting in low production efficiency. After evaluation, the company decided to switch to ceramic beads for surface cleaning.
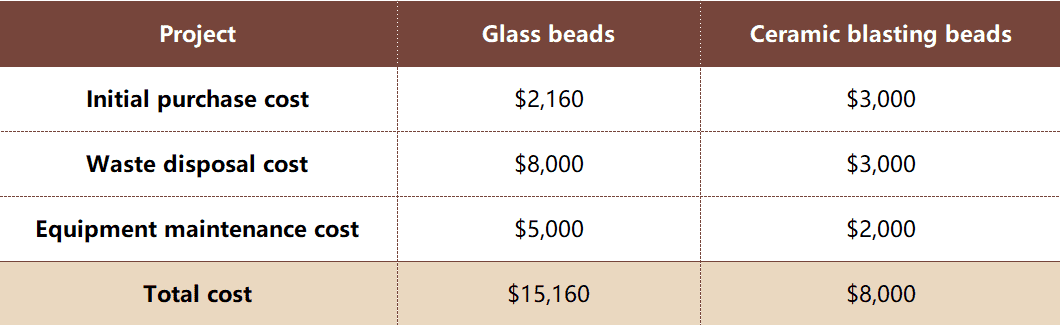
Through the above analysis, the overall cost of ceramic beads is 47% lower than that of glass beads. In addition, due to the high durability of ceramic beads, production efficiency has increased by 10%, and equipment downtime and maintenance costs have been greatly reduced.
Application Case Studies
Case 1: Automotive Parts Cleaning
Background:
An automotive manufacturer was faced with the challenge of cleaning aluminum engine parts. Due to the soft surface of aluminum alloys, welding residues, and oxide layers needed to be removed without causing surface damage. Initially, the manufacturer used glass beads for sandblasting cleaning.
However, the insufficient hardness of the glass beads resulted in a shallow surface compressive stress layer during the cleaning process, uneven cleaning in some areas, and even micro-cracks on the local surface. Due to the high breakage rate of glass beads, the sandblasting media needed to be replaced frequently, increasing production downtime and costs.
Solution:
The manufacturer decided to switch to ceramic beads for sandblasting cleaning. The high hardness and regular particle shape of ceramic beads ensured a uniform cleaning effect, while effectively removing oxides and welding residues, and a deeper surface compressive stress layer. Due to the durability of ceramic beads, the frequency of sandblasting media replacement is greatly reduced, reducing downtime and maintenance costs.
Results:
After using ceramic beads, the depth of the compressive stress layer on the surface of the parts increased by 30%, the cleaning efficiency increased by 25%, and no scratches or microcracks appeared on the surface. The overall production cost decreased by about 15%, and the production efficiency increased by 10%.
Case 2: Titanium Alloy Sandblasting Cleaning
Background:
An aerospace company needs to clean titanium alloy turbine blades to remove welding residues and oxide layers. This task requires high-precision cleaning of the surface without damaging the surface structure, while effectively removing contaminants. The company initially used relatively gentle glass beads for sandblasting cleaning.
However, when glass beads are used to process titanium alloys, they are not hard enough to fully remove surface residues. Especially at the end of the blade, the cleaning layer is uneven, resulting in a decrease in fatigue life, and the cleaning effect gradually weakens due to the crushability of the glass beads.
Solution:
After changing to ceramic beads, the high hardness and excellent particle stability of ceramic blasting beads can quickly and effectively remove oxide scale and welding residues without damaging the titanium alloy surface. Since the particles of ceramic beads are not easy to break, the cleaning effect is more durable, and there is less dust during the sandblasting process, which helps to maintain a clean operating environment.
Results:
After cleaning with ceramic beads, the compressive stress layer on the blade surface is uniform the depth is increased, and the fatigue life is increased by 20%. In addition, due to the durability of ceramic beads, the company has reduced the frequency of replacing sandblasting media by 50%, and the long-term maintenance cost has been greatly reduced.
Case 3: Nuclear Energy Pipeline Cleaning
Background:
When a nuclear power plant performs surface cleaning on high-pressure steam pipelines, it is required to clean the oxides and corrosive products on the surface, while increasing the corrosion resistance and fatigue life of the pipeline. Due to the harsh environmental conditions, the cleaning effect directly affects the safety and service life of the equipment.
When glass beads were used for sandblasting cleaning in the early stage, the cleaning effect was not ideal. Due to the high fragmentation rate of glass beads, the surface strengthening was uneven, and the expansion of corrosion cracks was not effectively suppressed, especially in the curved parts and welding points of the pipeline, where the corrosion problem was still serious.
Solution:
After replacement with ceramic beads, due to their high hardness and regular shape, ceramic beads can evenly apply surface compressive stress, significantly improving the corrosion resistance and fatigue resistance of the pipeline surface. At the same time, the plant was able to significantly reduce the frequency of blasting media changes due to the high recyclability of ceramic beads.
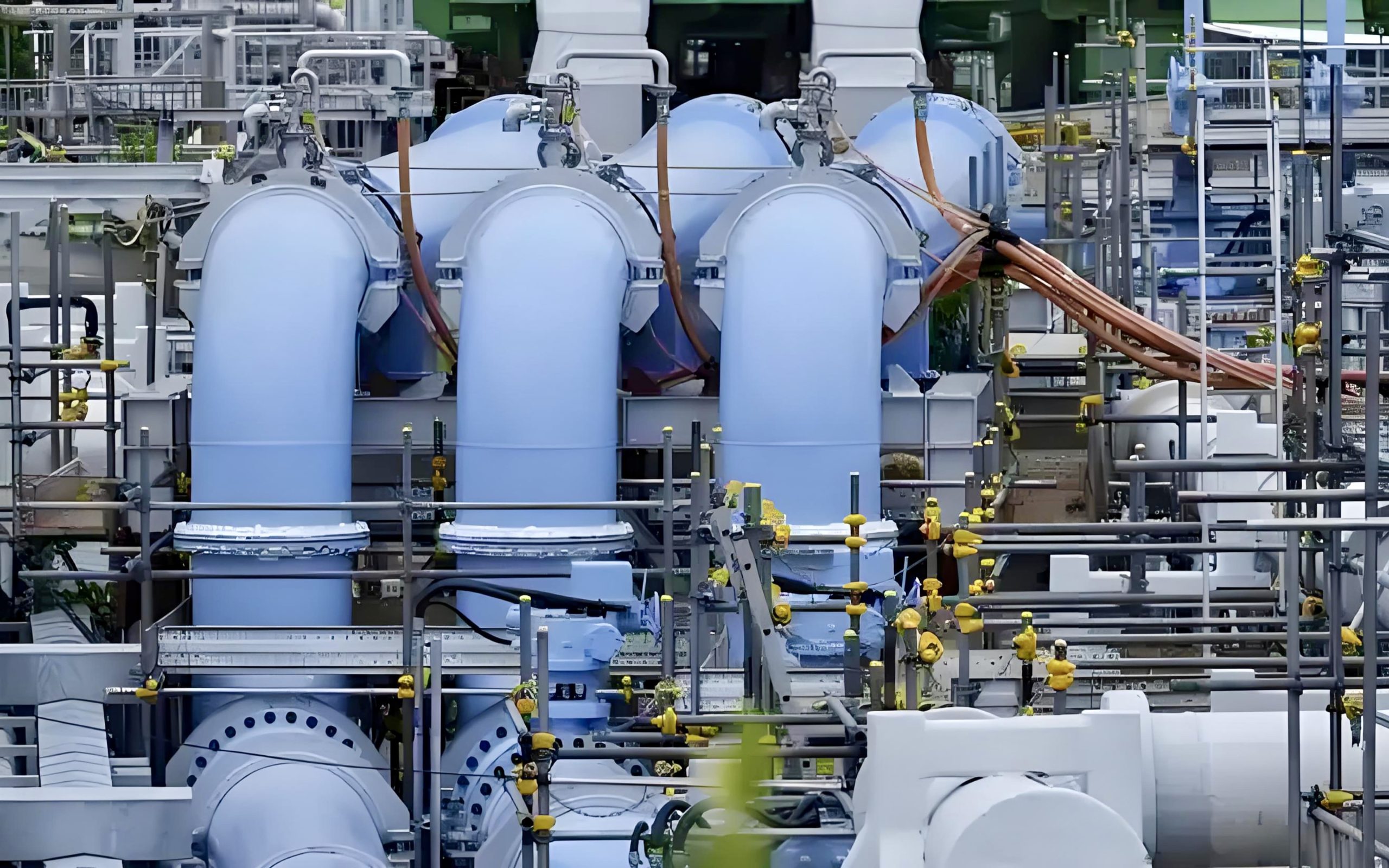
Results:
After using ceramic blasting beads, the fatigue life of the pipes was extended by 25%, the propagation rate of corrosion cracks was significantly slowed, and the overall cleaning effect was improved by 30%. In addition, due to the durability of ceramic beads, waste disposal costs were reduced by 40%.
FAQ
Are ceramic beads suitable for all types of materials?
Ceramic beads are generally suitable for most metals, alloys, and ceramic materials, especially in situations where high surface compressive stress is required.
For example, ceramic blasting beads perform well for high-hardness materials such as stainless steel, aluminum alloys, and titanium alloys. Ceramic beads can also adapt to soft materials such as aluminum alloys by adjusting the particle size and blasting pressure.
However, for some extremely soft materials such as plastics and wood, it may be necessary to choose ceramic beads with a smaller particle size or use plastic media.
Does the longer service life of ceramic beads mean a higher initial cost?
Yes, the initial purchase cost of ceramic blasting beads is generally higher than that of glass beads.
But it has significant durability and can be recycled many times. The hardness and wear resistance of ceramic beads allow them to withstand more repeated use, reducing the cost of frequent media replacement, thereby effectively reducing the long-term use cost.
Compared with glass beads, how do ceramic beads reduce dust in the working environment?
Ceramic beads are less likely to break during use, and even if it is worn, they will not be completely broken into powder, so their dust generation is low, which helps to keep the working environment clean.
Glass beads are easy to completely break during frequent use, generating more dust and may also damage the workpiece.
Is it necessary to make special adjustments to the sandblasting equipment to adapt to ceramic beads?
Ceramic beads are usually compatible with existing sandblasting equipment due to their regular spherical design and high hardness.
Compared with glass beads, the particle size distribution and physical properties of ceramic blasting beads make the equipment more adaptable and the sandblasting operation more stable. In most cases, only the injection pressure and particle size range need to be adjusted without complex modifications to the equipment.
What are the environmental advantages of ceramic beads?
The environmental advantages of ceramic beads are mainly reflected in their high recyclability.
Compared with glass beads, ceramic beads are not easy to break during use, and their recyclable ratio can be as high as 95%. This means that in most applications, ceramic beads can last much longer than glass beads, resulting in less waste, and are particularly suitable for industries that need to meet green production certification.
Filters