A Detailed Explanation of Ultrafine Aluminum Oxide Blast Media
August 21, 2024
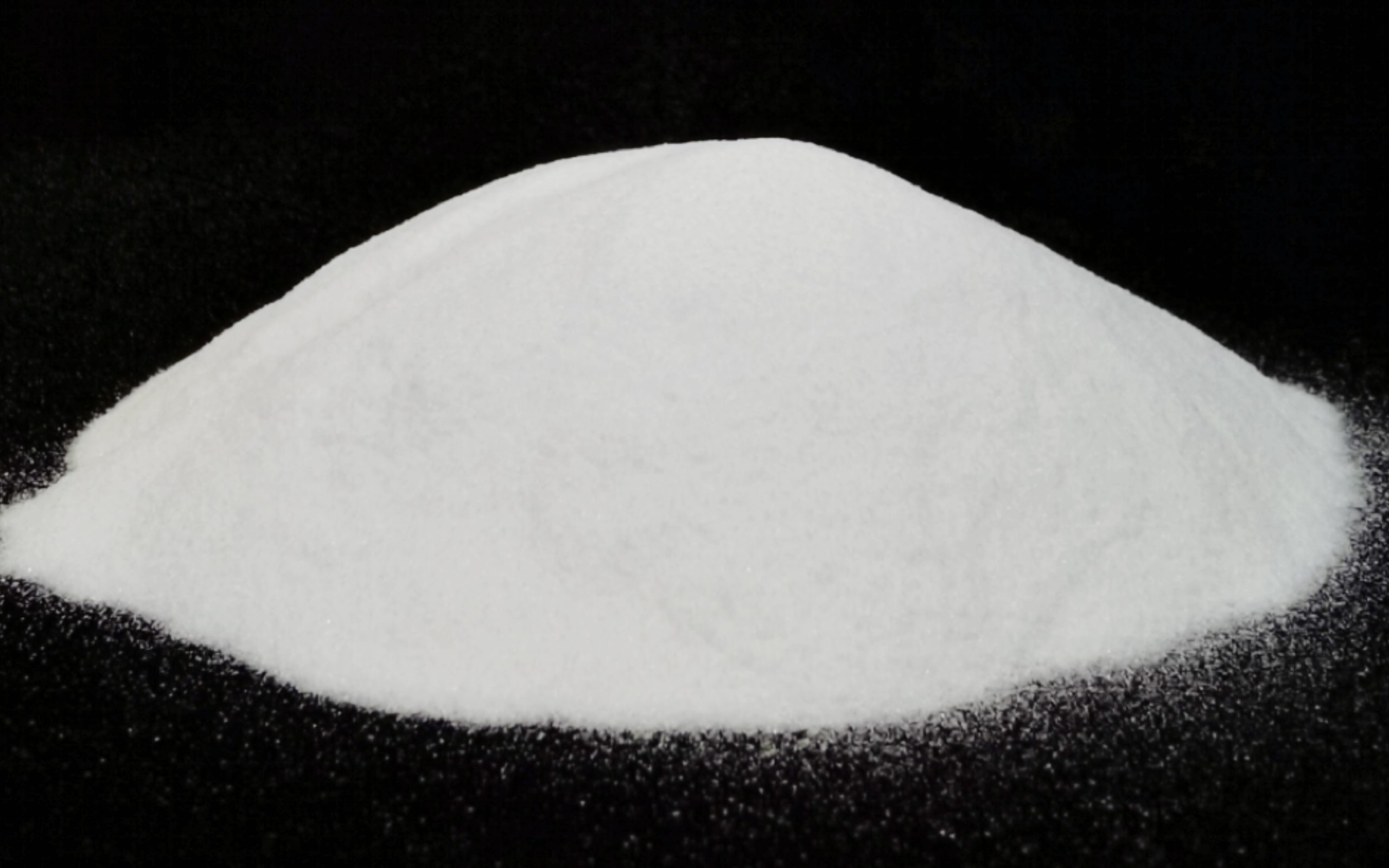
In modern manufacturing, advancements in surface treatment technology have significantly impacted various industries, most notably through quality improvement and increased production efficiency. Among these advancements, sandblasting technology, as a common surface treatment method, has seen continuous diversification. Ultrafine aluminum oxide blast media, with its unique properties and advantages, has gradually become the material of choice in many high-precision manufacturing fields.
This article will introduce you to six key aspects, including “What is Sandblasting?”, “What is Ultrafine Aluminum Oxide blast Media?”, “Characteristics and Advantages of Ultrafine Aluminum Oxide blast Media”,”Economic Benefits and Environmental Friendliness”,”Specific Functions and Application Areas” and “Current Technology and Future Prospects” helping you fully understand its importance in industrial applications and its future potential.
What is Sandblasting?
Sandblasting originated in the late 19th century, with its patent filed by American inventor Jesse H. Stevens in 1893. He invented the first sandblasting machine designed for cleaning and processing metal surfaces, marking the official birth of sandblasting technology.
The principle of sandblasting involves using high-pressure air to propel fine abrasive particles onto the surface of the object being treated. This process uses strong mechanical force to remove impurities or defects from the surface, while also adjusting the surface roughness and improving the adhesion of coatings or adhesives. The technique achieves purposes such as cleaning, deburring, polishing, or strengthening the surface.
From the late 19th century to the early 20th century, sandblasting technology began to be applied in various industrial fields, including construction, automotive, and aerospace. In 1905, a patent was granted for an improved design of sandblasting technology, making the sandblasting process more convenient and economical. Another 30 years later, high-speed sandblasting technology began to be used for precision machining and metal surface treatment. The application areas of sandblasting gradually expanded to include casting, mold making, and the automotive industry.
In the late 20th century, with advancements in materials science, sandblasting technology started to use various new abrasives, such as glass beads and ceramic particles. By the early 21st century, sandblasting technology entered the era of intelligence and automation. Modern sandblasting equipment is equipped with advanced control systems that precisely adjust sandblasting parameters and optimize the process. Automated sandblasting systems increased production efficiency and reduced labor intensity. With the development of nanotechnology, new materials such as sand blasting aluminum have been applied to high-precision surface treatments, meeting higher industrial demands.
What is Ultrafine Aluminum Oxide blast Media(Click)?
Ultrafine aluminum oxide blast media is a type of sandblasting material with high-purity alumina as its main component. It is characterized by extremely fine particles, usually ranging from 1 to 5 microns in diameter.
Compared to traditional sandblasting media (such as glass beads, quartz sand, etc.), ultrafine alumina has higher hardness and chemical stability, allowing it to quickly cut and etch the hardest materials, especially excelling in the treatment of precision pre-treated objects and surfaces with high requirements.
You can choose different sandblasting sizes to achieve different effects. Larger grains will etch faster and leave a rougher surface, while finer grains will leave a smoother surface but take longer to process.
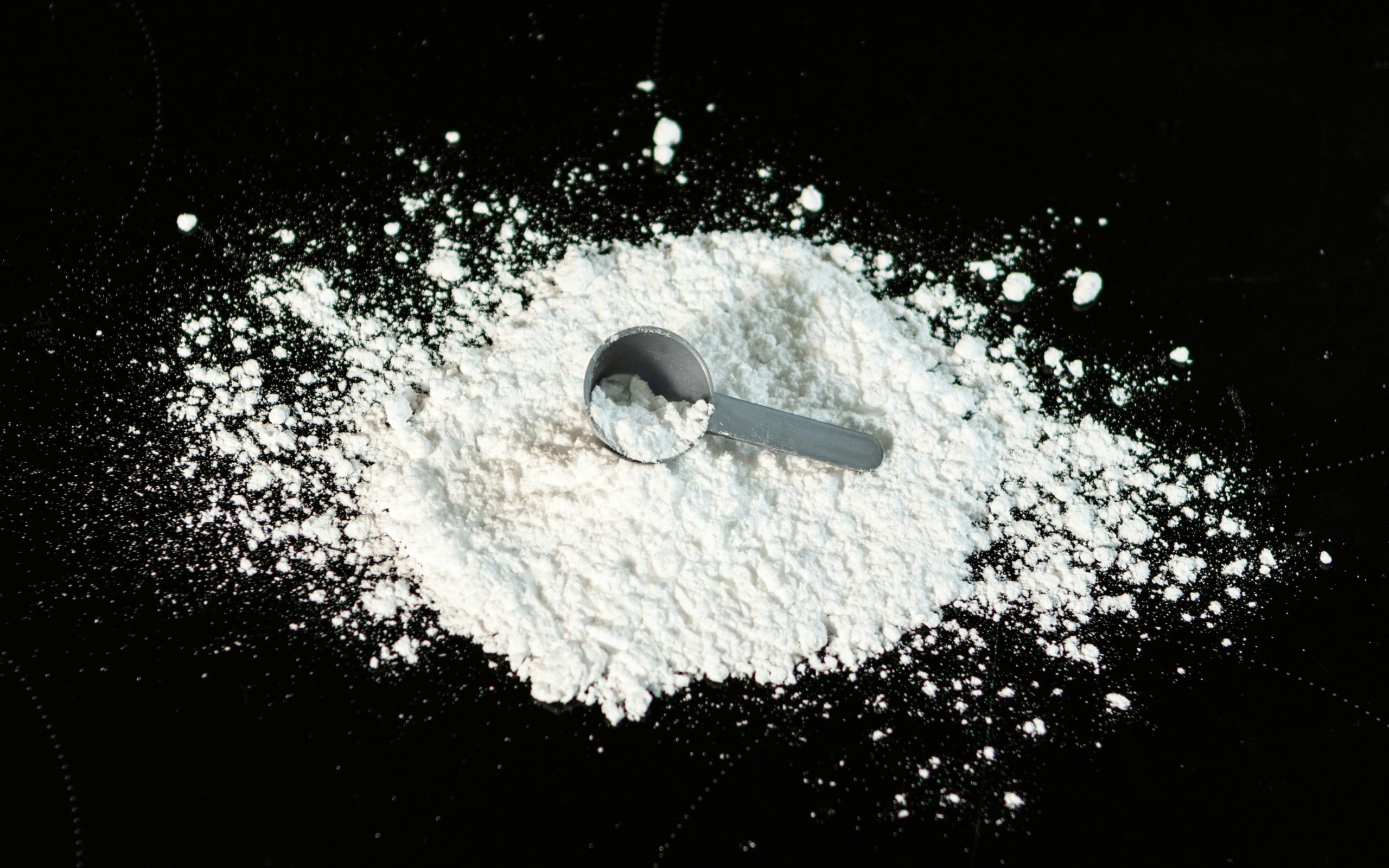
Ultrafine Aluminum Oxide blast Media
Characteristics and Advantages of Ultrafine Aluminum Oxide blast Media
High Purity, Low Pollution
The main component of aluminum oxide sandblasting is high-purity alumina (Al₂O₃), with a purity typically reaching over 99%. This high purity ensures that no impurities or pollutants are generated during use, which is particularly important for industrial applications requiring high cleanliness (such as semiconductors, optical devices, etc.), ensuring that pre-treated objects maintain extremely high surface quality after processing.
Fine Processing Capability
Ultrafine aluminum oxide blast media typically takes the form of small crystalline particles, which may appear as polyhedral, near-spherical, or other irregular shapes. Due to the extremely small particle size, it can penetrate small recesses or complex structures of pre-treated objects, achieving uniform surface treatment, especially suitable for complex structures or precision components.
High Hardness and Wear Resistance
Ultrafine aluminum oxide blast media has extremely high hardness and wear resistance, with a Mohs hardness second only to diamond and silicon carbide. This enables it to effectively remove burrs, oxide layers, or other impurities from the surface of pre-treated objects without damaging them. Additionally, it maintains its shape and performance stability during high-pressure jetting, significantly extending its lifespan and reducing the need for frequent replacements.
Chemical Inertness
Due to the chemical inertness of alumina, it will not chemically react with the material of pre-treated objects during processing, allowing it to maintain stable physical and chemical properties in harsh environments such as high temperatures, strong acids, and strong alkalis, without affecting the material properties.
Economic Benefits and Environmental Friendliness
High Reusability
The high hardness and wear resistance of ultrafine aluminum oxide blast media give it a long service life. In practical applications, this media can be reused multiple times, greatly reducing the material cost of sandblasting operations.
Lower Production Costs
Thanks to the high efficiency and long lifespan of ultrafine sand blasting aluminum, companies can reduce material loss and downtime during sandblasting operations, thereby lowering equipment maintenance and replacement frequencies, enhancing overall production efficiency. Moreover, due to its high purity and low pollution properties, the surface of pre-treated objects requires no complex cleaning procedures after treatment, indirectly saving time and resources.
Environmental Friendliness
Ultrafine aluminum oxide blast media does not generate harmful dust or toxic substances during use, meeting strict environmental standards. Additionally, its high reusability reduces the generation of waste. Compared to traditional sandblasting media, it better meets modern industrial requirements for sustainable development.
Specific Functions and Application Areas
Deburring
Ultrafine sand blasting aluminum, with its small and hard particles, effectively removes burrs and irregular edges from the surface of pre-treated objects, ensuring a smooth and even surface, which is especially important for components requiring high precision and quality, such as electronic components and medical devices.
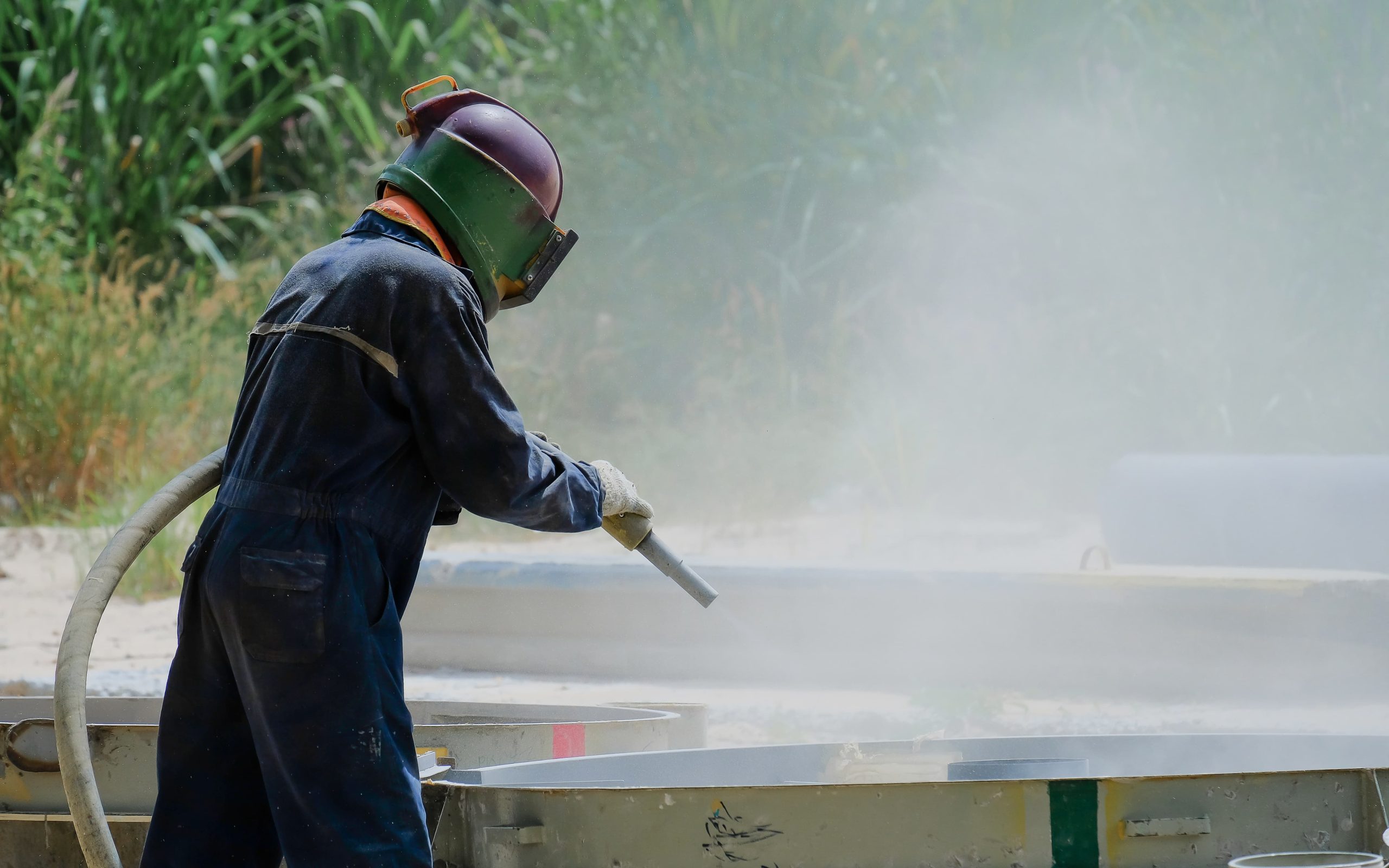
Sandblasting process demonstration
Cleaning
Removes oxide layers, rust, or other contaminants from surfaces, ensuring the cleanliness of pre-treated objects. For example, in the processing of automotive engine components and aerospace parts, ultrafine aluminum oxide blast media can remove surface deposits, providing a cleaner surface for subsequent coatings or processing.
Polishing
Suitable for industries aiming to enhance surface smoothness, it is widely used in optical devices and aerospace components, helping to improve the visual effects and performance of products.
Surface Strengthening
By utilizing its high-hardness particles, ultrafine aluminum oxide blast media can strengthen the surface of pre-treated objects, a common treatment in automotive components and aircraft structural parts, enhancing product wear resistance and corrosion resistance under extreme conditions, thereby improving reliability and lifespan.
Detail Processing
Due to the extremely small particle size, ultrafine sand blasting aluminum can finely process complex details, ensuring high precision and consistency. In the processing of precision molds and small optical components, it performs exceptionally well, effectively removing minor defects and enhancing detail quality.
In addition to the five main conventional functions, aluminum oxide blasting media can also be applied in the fields of art and design. Through precise sandblasting, artists can create unique textures and patterns on materials such as metal, glass, and ceramics. This technique is widely used in sculptures, decorative furniture, and architectural design, giving works a distinctive texture and visual appeal. In high-end watchmaking and jewelry manufacturing, aluminum oxide blasting media is also used for fine processing and surface treatment, creating luxurious matte finishes or unique textures. This meticulous surface treatment enhances the aesthetic value and durability of products, helping them stand out in a competitive market. Similarly, in the field of cultural heritage preservation and restoration, aluminum oxide blasting media can be used to clean and restore the surfaces of ancient stone carvings, metal artifacts, and other cultural relics, removing oxidation layers and dirt while preserving their original appearance as much as possible.
Note: Due to the high hardness of aluminum oxide (Mohs hardness 7-9), it may cause surface damage, scratches, or excessive wear when processing softer materials, such as plastic, wood, or certain metals.
Current Technology and Future Prospects
Current Technological Development
Currently, many companies are dedicated to the research and production of aluminum oxide abrasive media, particularly in high-precision manufacturing and surface treatment fields. Below is an introduction to some well-known companies that have made significant contributions to the research and production of aluminum oxide media:
- Saint-Gobain
Saint-Gobain is a global leader in high-performance materials manufacturing. They offer a wide range of abrasive products, including sand blasting aluminum. Their products are known for their high purity and stability, and they are widely used in aerospace, automotive, electronics, and other fields.
- HLH
HLH, based in China, has been focusing on the technological research, production, application, and sales of new surface treatment abrasive materials for 20 years. All their products, including ultra-fine aluminum oxide abrasive media, have passed the IS09001:2008 International Quality System Certification, EU CE and RoHS Certification, CCC Certification, and CQC Certification, earning widespread recognition both domestically and internationally.
- Washington Mills
Washington Mills is an established American abrasive manufacturing company specializing in the production of various types of abrasives. Their aluminum oxide products are renowned in the market for their superior wear resistance and hardness.
- Imerys Fused Minerals
Imerys, headquartered in France, is a mineral materials company with several high-performance aluminum oxide production lines. Their aluminum oxide abrasive media are primarily used in high-precision manufacturing and surface treatment fields, with products covering multiple industries globally.
- Almatis
Almatis is a company specializing in the production of high-performance aluminum oxide products, offering various forms of aluminum oxide, including ultra-fine powders suitable for abrasive applications. Their aluminum oxide products are widely used in refractory materials, abrasives, and industrial ceramics.
- Fujimi Corporation
Fujimi, a Japanese company, specializes in the production and research of ultra-precision abrasives, including high-purity aluminum oxide abrasive media. Their products are known for their high precision and uniformity, widely used in electronics, semiconductors, and optical devices.
- 3M
3M is a multinational technology company involved in various industry sectors, including abrasives and surface treatment. They offer a range of abrasive solutions, with aluminum oxide abrasive media being one of their core products, widely used in industrial cleaning, surface preparation, and coating applications.
These companies continue to innovate in aluminum oxide sandblasting research by continuously improving production processes and product features to meet the demands of different industrial applications. In recent years, with advancements in nanotechnology and materials science, the manufacturing process of ultra-fine aluminum oxide abrasive media has seen significant improvements. Modern technology allows for precise control of particle size and shape, ensuring consistent quality and performance in every batch. This precise control has enabled the widespread adoption of ultra-fine aluminum oxide abrasive media in a,n increasing number of high-precision applications, meeting the stringent requirements of various complex processes in surface treatment.
Furthermore, the introduction of automated equipment and intelligent control systems has greatly improved the efficiency and accuracy of abrasive operations, saving companies more time and costs.
Future Prospects
Looking ahead, the development of aluminum oxide sandblasting will continue to move towards high precision, high efficiency, and environmental friendliness. In terms of manufacturing technology, as emerging technologies such as 3D printing and additive manufacturing become more widespread, the demand for surface treatment will become more complex and diverse, and ultrafine aluminum oxide blast media will continue to optimize its properties to meet the requirements of these emerging applications.
In the current global context, manufacturing industries in different regions will face unique challenges and needs. In the future, ultrafine aluminum oxide blast media will further refine its product lines to meet the customized needs of different markets. For example, parts working in high-temperature, high-pressure environments may require sandblasting media with stronger heat resistance and wear resistance, while the trend toward miniaturization and high integration in electronic components may lead to the development of finer alumina particles for more precise surface treatment.
Moreover, as artificial intelligence and big data technologies are widely applied, future sandblasting processes may become more intelligent and automated. Real-time monitoring and feedback systems can instantly adjust sandblasting parameters, optimizing media usage efficiency and treatment effects. This not only enhances production stability and consistency but also creates higher economic benefits for companies.
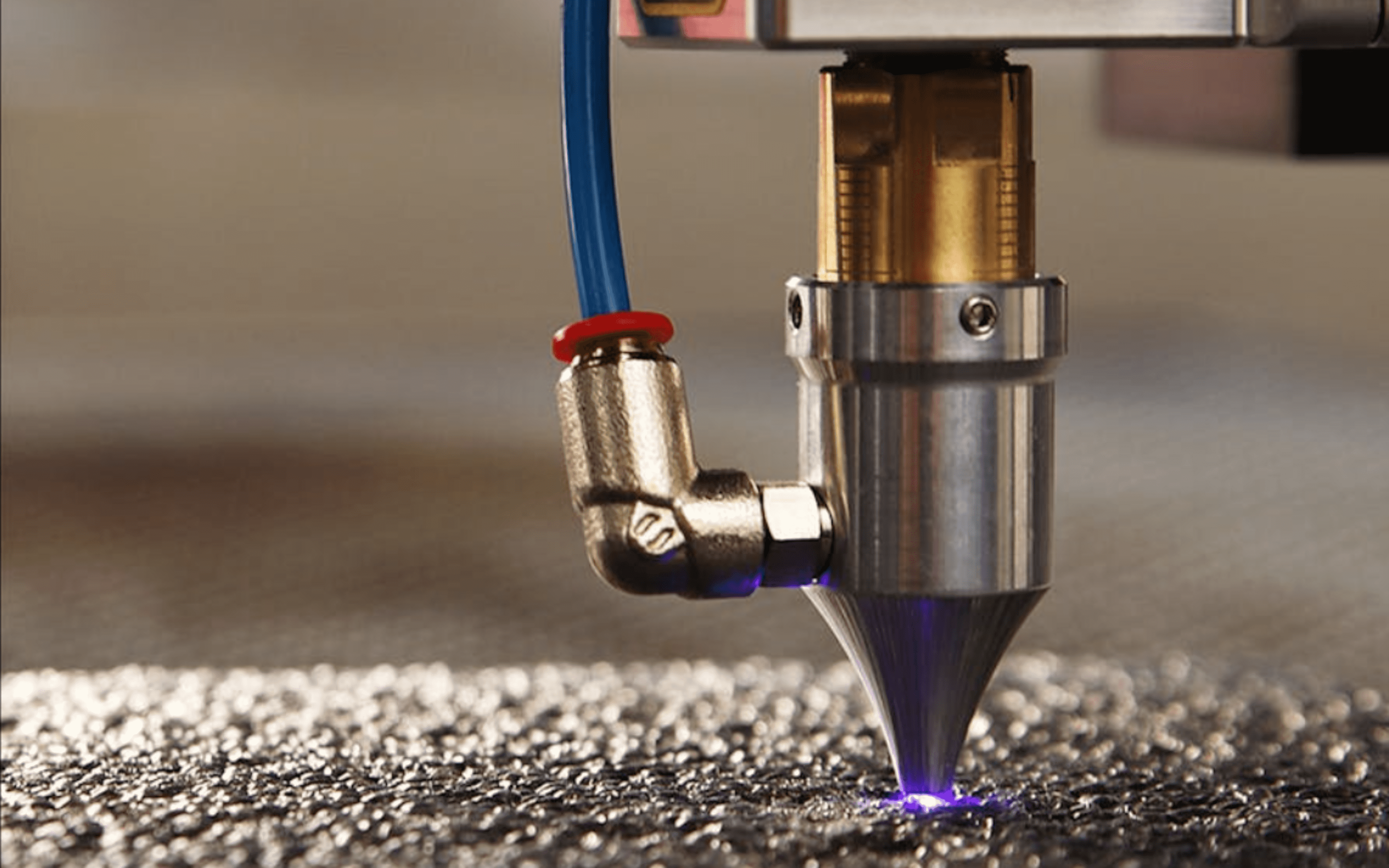
Sand blasting equipment at work
In conclusion, ultrafine aluminum oxide blast media, with its unique properties and broad application prospects, will continue to occupy an important position in modern manufacturing. As technology advances and market demands change, it will also play a role in a wider range of fields, driving manufacturing toward higher precision, efficiency, and environmental standards.
Filters