Understanding Ceramic Beads blasting Media
August 27, 2024
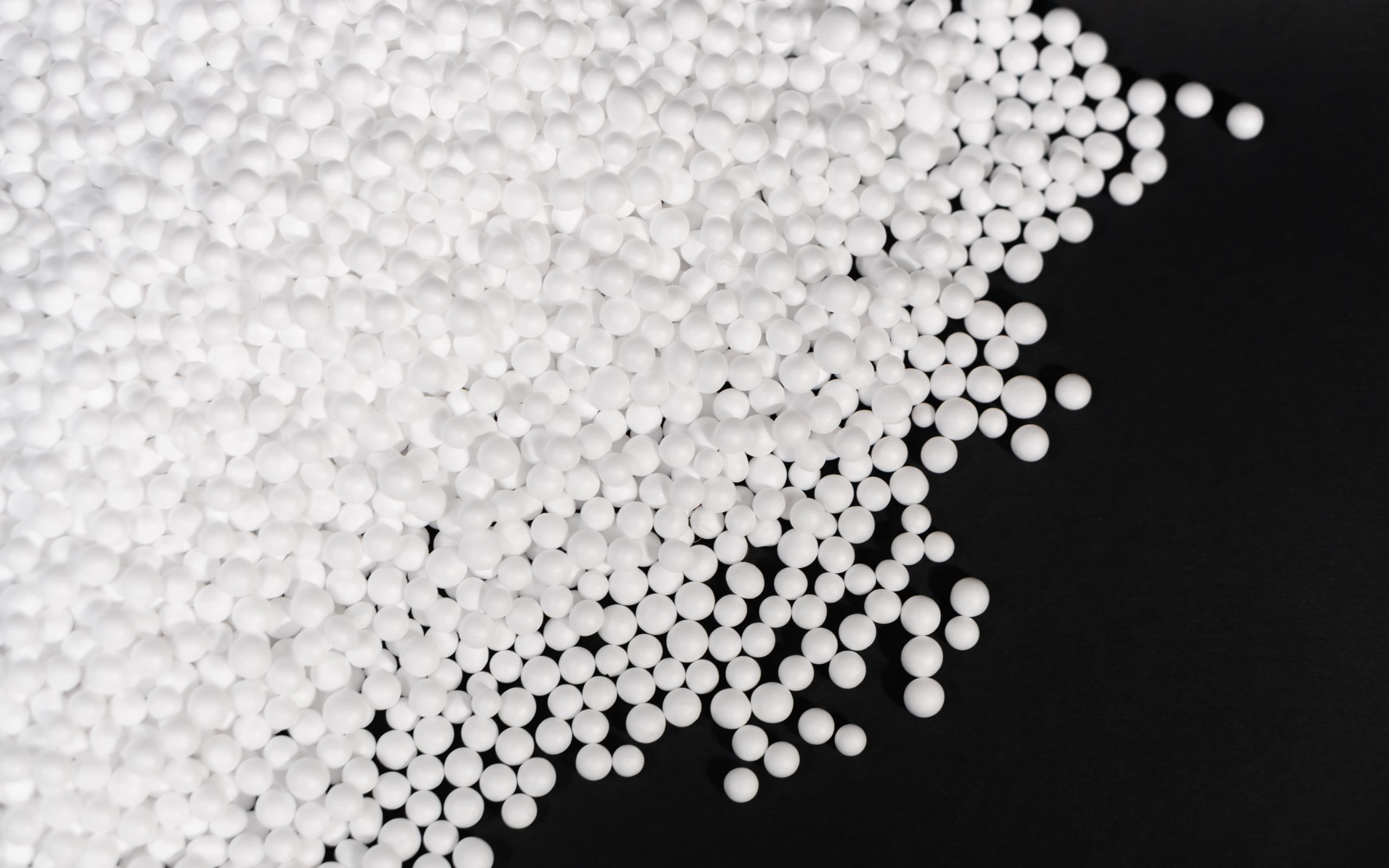
In the modern surface treatment field, ceramic beads, as an efficient and environmentally friendly sand blasting media, showcase excellent application effects in various industries due to their superior physical and chemical properties. Whether in metal processing or automotive manufacturing, ceramic beads blasting technology is continuously driving advancements and innovations. This article will introduce the basic information about ceramic beads blasting from aspects such as its characteristics and advantages, economic benefits and environmental friendliness, specific functions, and industry applications, helping you to gain an initial understanding of this media.
What is Ceramic Beads Blasting Media?
Ceramic bead sandblasting is a surface treatment technology that uses ceramic beads as the sand blasting media. Ceramic beads are small ceramic spheres made by high-temperature sintering, usually composed of materials like zirconium silicate, bauxite, and silicon dioxide. During the sandblasting process, ceramic beads are propelled onto the target surface by compressed air or other gases, achieving purposes such as removing surface dirt and roughening the surface. Ceramic bead sandblasting is widely used in the surface treatment of metals, plastics, glass, and other materials, characterized by a wide range of applications and notable effects.
Characteristics(Click to view details)
- Material Composition
Ceramic beads are made from high-temperature sintered ceramic materials, with the main component commonly being zirconium dioxide (ZrO₂). Additionally, other auxiliary materials such as aluminum silicate (SiO₂) and titanium dioxide (TiO₂) are included to further optimize the overall performance of the ceramic beads, enhancing their strength and wear resistance. After mixing these raw materials and sintering at high temperatures, the finished ceramic beads exhibit consistent physical and chemical properties.
- Hardness
The hardness of ceramic beads is one of their most important characteristics, typically ranging from 6 to 8 on the Mohs scale (a standard for measuring material hardness, with 1 being the softest and 10 being the hardest). High hardness allows them to effectively remove stubborn impurities from the workpiece surface, such as rust and oxidation layers. It also means they can maintain their shape and performance during the sandblasting process without excessive wear, ensuring high efficiency and consistency.
- Particle Shape
Typically spherical, this shape has significant advantages. Spherical particles distribute the impact force evenly during sandblasting, avoiding uneven wear or damage that sharp angles might cause. Spherical ceramic beads provide consistent surface treatment results and reduce potential flaws during the surface treatment process. Additionally, spherical particles flow smoothly in sandblasting equipment, greatly reducing blockages and equipment wear.
- Durability
Over long periods (not under high intensity), the shape and performance of ceramic beads remain stable. They can be reused multiple times, reducing the frequency of replacements.
In addition to the basic characteristics mentioned, ceramic beads sandblasting also offers the following performance advantages, which enable its widespread use in various complex industrial environments:
- Balance of Impact Energy and Abrasive Ability
The design of ceramic media finds a good balance between impact energy and abrasive ability. The spherical shape of the particles ensures that excessive wear is avoided while still providing enough impact force to remove surface dirt, oxides, or old coatings. This balance makes ceramic beads sandblasting suitable for both gentle surface treatments (such as precision components) and more intensive treatments.
- Excellent Chemical Corrosion Resistance
The chemical stability of ceramic media allows them to maintain performance stability in various chemical environments without easily corroding. Although their acid and alkali resistance is relatively limited, they still provide excellent sandblasting effects in neutral or weakly acidic and alkaline environments. This performance is especially suitable for surface treatments in complex chemical environments, such as chemical and pharmaceutical equipment.
- Wide Temperature Adaptability
Although ceramic beads have relatively low heat resistance, their performance at normal temperatures remains outstanding. Using ceramic beads for sandblasting in low or normal temperatures ensures a long service life and consistent treatment effects.
- Relatively Low Cost
After cleaning and screening, they can be reused under appropriate conditions, reducing material costs. They are suitable for large-scale production and cause minimal wear on equipment.
Economic Benefits
- Reducing Long-Term Usage Costs
Although ceramic beads wear out relatively quickly, their initial purchase cost is low and they cause minimal wear on equipment, leading to lower maintenance frequency and cost-effectiveness in the long run.
- Enhancing Production Efficiency
Ceramic beads sandblasting can quickly and evenly process workpiece surfaces, enabling faster completion of tasks on the production line, thus enhancing overall production capacity.
- Reducing Waste and Defect Rates
The uniformity and high efficiency of ceramic media reduces waste and defects caused by uneven sandblasting, further lowering production costs and improving resource utilization.
Environmental Friendliness
- Reducing Dust Emissions
Compared to other sandblasting media, ceramic media produces less dust during operation, helping to maintain indoor air quality and reduce negative environmental impacts.
- Non-Toxic and Harmless
Made from natural minerals, ceramic beads contain no toxic chemicals and are harmless to the environment and human health during use. This material is widely used in modern industry, meeting health and safety standards.
- Recyclability
Ceramic beads can be recycled after cleaning and screening, reducing waste and improving resource usage efficiency.
Specific Functions
- Removing Surface Rust and Oxidation Layers
Ceramic beads sandblasting is widely used to remove stubborn rust and oxidation layers from metal surfaces, restoring cleanliness and providing a good foundation for subsequent processing.
- Surface Polishing
Its uniform particle size and efficient processing ability significantly enhance the glossiness of the polished workpiece surface, improving the appearance and durability of the workpiece.
- Increasing Adhesion
Sandblasting with ceramic beads creates small roughness on the workpiece surface, increasing the adhesion of coatings or adhesives (which is especially important for spraying and bonding processes).
Industry Applications
- Automotive Manufacturing Industry
The automotive manufacturing industry has strict requirements for the surface quality of automotive parts. Ceramic beads blasting is widely used for processing body panels, engine components, and more, improving the appearance quality and durability of parts, enhancing coating adhesion, and ensuring the overall safety and quality of vehicles. Mercedes-Benz uses ceramic beads blasting technology to improve the appearance and surface quality of body panels and precision parts while enhancing paint adhesion. Volkswagen also uses this technology to improve the surface smoothness of body panels and engine components, ensuring reliability under high-load conditions.
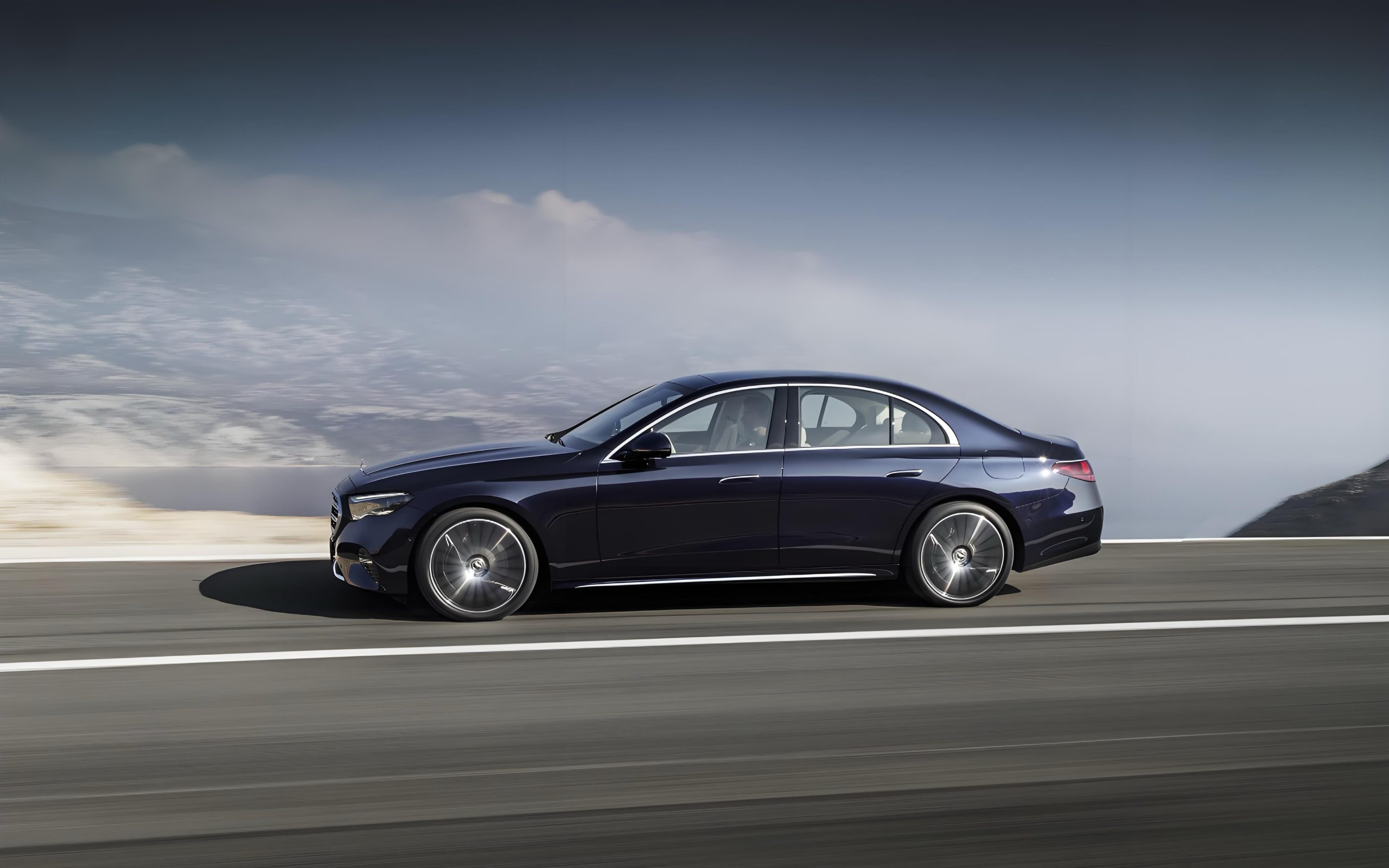
Benz
- Electronics Manufacturing Industry
The electronics manufacturing industry has strict requirements for the cleanliness and smoothness of product surfaces, especially in high-precision and high-reliability electronic components. Surface treatment processes play a crucial role in ensuring electronic product performance and longevity. Ceramic beads blasting is used to clean the surfaces of electronic components, removing solder residues and impurities from the production process. Its uniform processing effect ensures cleanliness and smoothness of electronic component surfaces, enhancing the performance and reliability of electronic products. Apple uses ceramic media technology for the processing of its device housings and internal components to achieve a uniformly smooth surface. For instance, the aluminum alloy housings of iPhones and iPads are often treated to provide a high-quality touch and aesthetic appearance.
- Petrochemical Industry
ln the petrochemical industry, equipment is often exposed to highly corrosive environments, necessitating high standards for surface corrosion protection. China National Petroleum Corporation (CNPC) has used ceramic media technology for the surface treatment of pipelines, storage tanks, and other equipment. After sandblasting, the surfaces become smoother, and coatings are evenly applied, providing a more stable protective layer, reducing weak spots in the coating, and improving corrosion resistance while lowering maintenance and replacement frequencies.
- High-Precision Machinery Manufacturing Industry
The surface smoothness of high-precision mechanical parts directly affects their final assembly quality and performance. Therefore, global renowned high-precision CNC machine tool manufacturers like DMG use ceramic media technology to polish the surfaces of precision parts during production to ensure surface quality and accuracy. The uniform particle size and efficient processing ability of ceramic beads make parts smooth and flawless, greatly enhancing product precision and reliability. In subsequent assembly processes, treated parts exhibit higher fitting accuracy and lower friction coefficients, significantly improving overall product performance.
- Medical Device Industry
The cleanliness and disinfection of medical device surfaces are crucial for the safety and effectiveness of the devices. Medtronic uses ceramic beads to clean and disinfect its surgical instruments. This method effectively removes small impurities from surfaces, enhances surface smoothness and consistency, and reduces bacterial adhesion. This processing method greatly improves the safety and durability of medical devices and has received high praise within the industry.
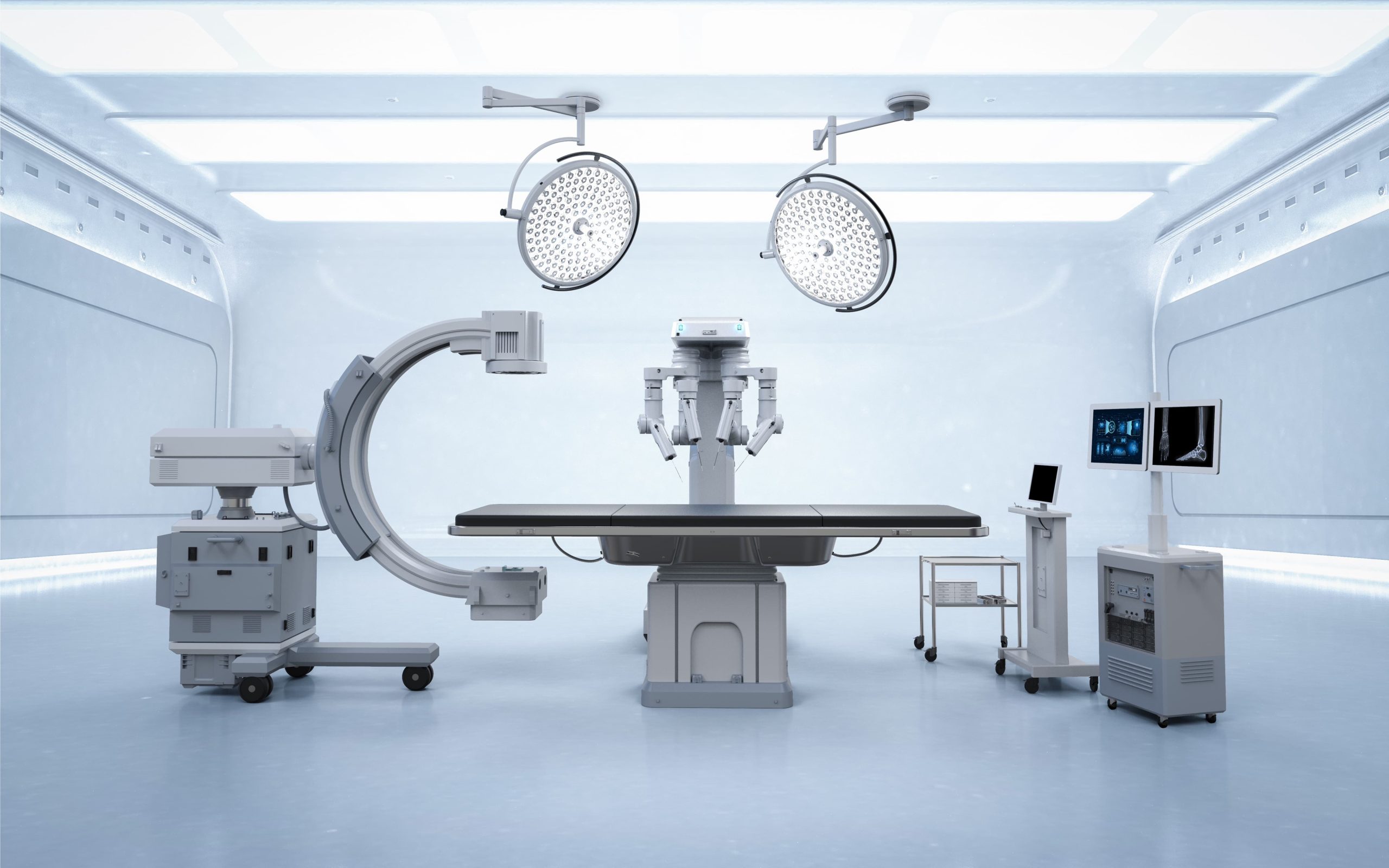
Medical devices with strict hygienic requirements
Comparison of Ceramic Beads Blasting with Other Sandblasting Media
The widespread popularity of ceramic media in industrial applications is due to both its superior performance and its comparative advantages over other sandblasting media. Here is a comparative analysis of ceramic bead sandblasting with other common sandblasting media:
- Comparison with Steel Shot
Steel shot is a common sandblasting media with high hardness and density, typically used for removing dirt or oxidation layers from hard surfaces. However, despite its high hardness, its density can produce significant impact force during sandblasting, potentially causing damage or excessive wear to the workpiece surface. In contrast, ceramic beads have a lower density and produce milder impact force during sandblasting, making them suitable for precision workpieces with higher surface requirements. Additionally, steel shot generates substantial metal dust during sandblasting, which can pollute the environment, whereas ceramic beads are more environmentally friendly due to their non-toxic and harmless properties.
- Comparison with Glass Beads
Glass beads are also widely used sandblasting media, known for their good chemical stability and smooth surface, performing well in removing surface dirt and polishing. However, glass beads have lower hardness compared to ceramic beads, limiting their effectiveness in removing stubborn surface contaminants. Ceramic beads, with their higher hardness, can better meet the requirements of surface treatment in more demanding industrial applications. Additionally, glass beads are more fragile and have a shorter service life than ceramic beads, making ceramic beads more cost-effective for long-term usage.
- Comparison with Aluminum Oxide
Aluminum oxide is an abrasive material with high hardness, commonly used in sandblasting for its excellent cutting ability and wear resistance. However, aluminum oxide can produce significant dust during sandblasting, which may affect the working environment. Ceramic beads, in comparison, generate less dust and offer a more uniform surface treatment effect. They are more suitable for applications requiring high surface quality and cleanliness.
- Comparison with Silicon Carbide
Silicon carbide is a highly abrasive material with high hardness and cutting ability, mainly used for more intensive sandblasting applications. Silicon carbide’s high abrasiveness can lead to excessive wear on equipment and the workpiece surface, resulting in increased maintenance costs. Ceramic beads offer a good balance between hardness and abrasive ability, making them suitable for a wider range of surface treatment applications and reducing equipment wear.
Future Development Trends of Ceramic Bead Blasting
More Environmentally Friendly Ceramic Bead Materials
In the future, as environmental regulations become increasingly stringent, the environmental friendliness of ceramic bead materials will become an important direction for their development. The development of more environmentally friendly, non-toxic, and biodegradable ceramic bead materials will help reduce the generation of industrial waste and further reduce the environmental impact of the blasting process.
Application of High-Performance Ceramic Beads
With advances in materials science, the research and application of high-performance ceramic bead materials (such as nano-scale ceramic beads and composite ceramic beads) will gradually become mainstream. These new types of ceramic beads will have higher hardness, stronger wear resistance, and better chemical stability, allowing them to play a greater role in more demanding industrial environments.
Development of Intelligent Blasting Equipment
With the popularization of industrial automation and intelligence, the development of intelligent blasting equipment will also bring new opportunities to ceramic bead blasting technology. By integrating advanced sensing technology, control technology, and data analysis technology, intelligent blasting equipment can achieve more efficient and precise surface treatment, further enhancing the application effectiveness and economic benefits of ceramic bead blasting.
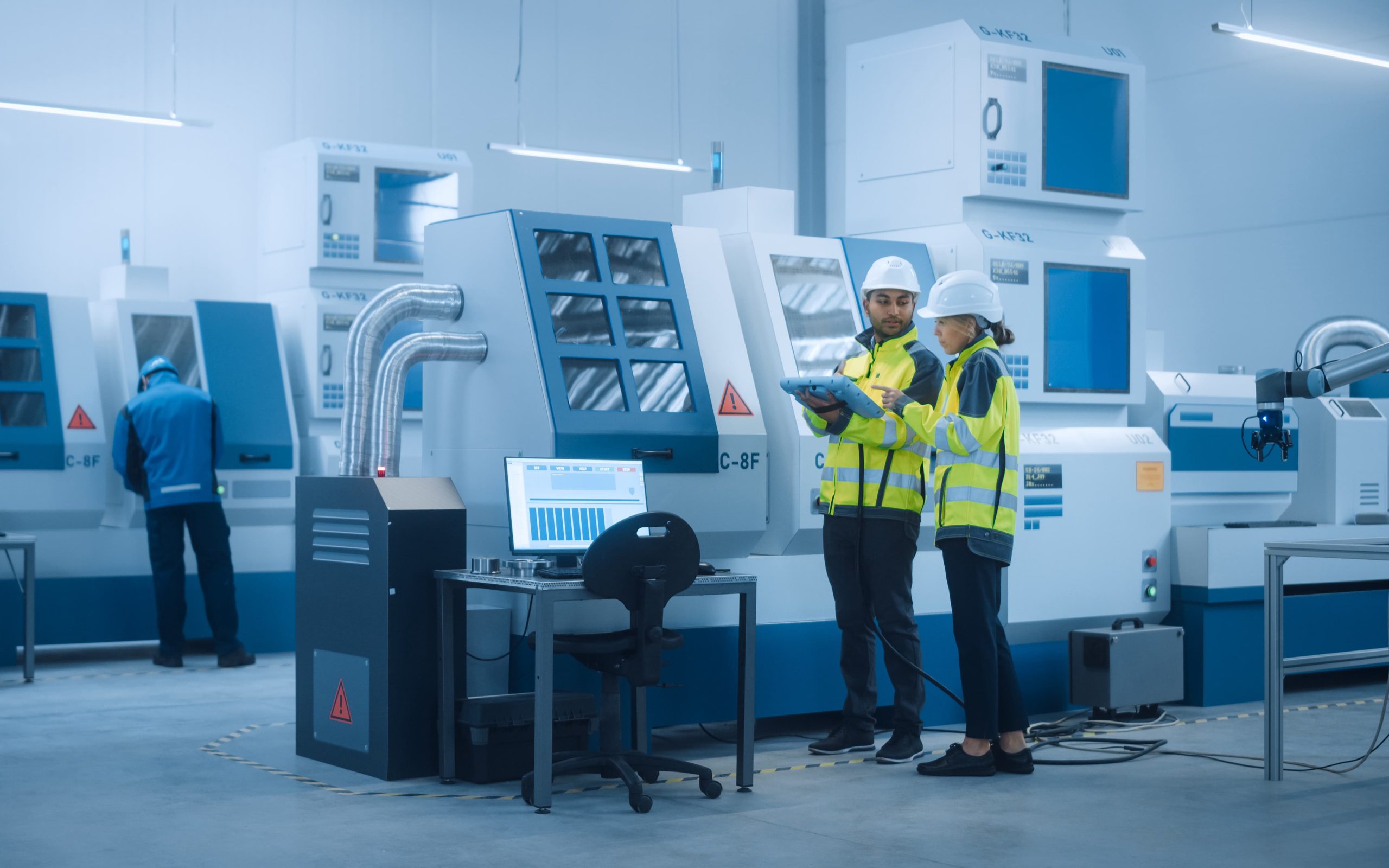
intelligent monitoring system
Ceramic beads blasting media has excellent physical and chemical properties, making it suitable for various industrial applications. Its high hardness, spherical particle shape, durability, and environmental benefits provide significant advantages in metal processing, automotive manufacturing, electronics, petrochemical industries, and high-precision machinery. By understanding its characteristics and comparing them with other sandblasting media, you can better utilize ceramic bead sandblasting technology in different surface treatment processes to achieve optimal results.
Filters