Shot Peening and Laser Peening in Metal Finishing
October 25, 2024
In the world of metal finishing, improving fatigue resistance, enhancing surface hardness, and improving corrosion resistance are key factors in determining part life and performance. These performance improvements are achieved through a variety of processes designed to change the surface characteristics of metal parts. Among them, shot peening and laser shock peening are two of the most effective methods that can introduce beneficial compressive stresses in metals, thereby extending the service life of critical components.
However, despite the same goal, the two technologies have significant differences in penetration depth, accuracy, cost, and applicable applications. This article will provide an in-depth comparison of shot peening and laser shock peening, examining their technical differences, typical applications, and key factors that influence the choice between the two. Case studies from industries such as aerospace, automotive, and medical devices will be used to explore the advantages and limitations of each process.
Shot Peening Overview
Process Description
Shot peening is a cold working process that uses projectiles to impact a metal surface. These projectiles are usually made of spherical materials such as steel, glass, or ceramics. During the peening process, the spherical media is accelerated by air jets or centrifugal force to impact the surface at high speeds. Each impact creates a small dent in the surface, compressing the material underneath. This creates a compression layer that acts as a protective barrier against crack initiation and propagation, thus increasing the material’s fatigue strength and resistance to stress corrosion cracking.
The depth of compressive stress produced by shot peening typically affects the top 0.1 – 1 mm of the material surface, which is sufficient for many general applications. Its disadvantage is that it generally leaves a rougher surface that may require additional finishing. Of course, the roughness can vary depending on the material of the peening media used, and generally steel media will leave a rougher surface than ceramic or glass beads.
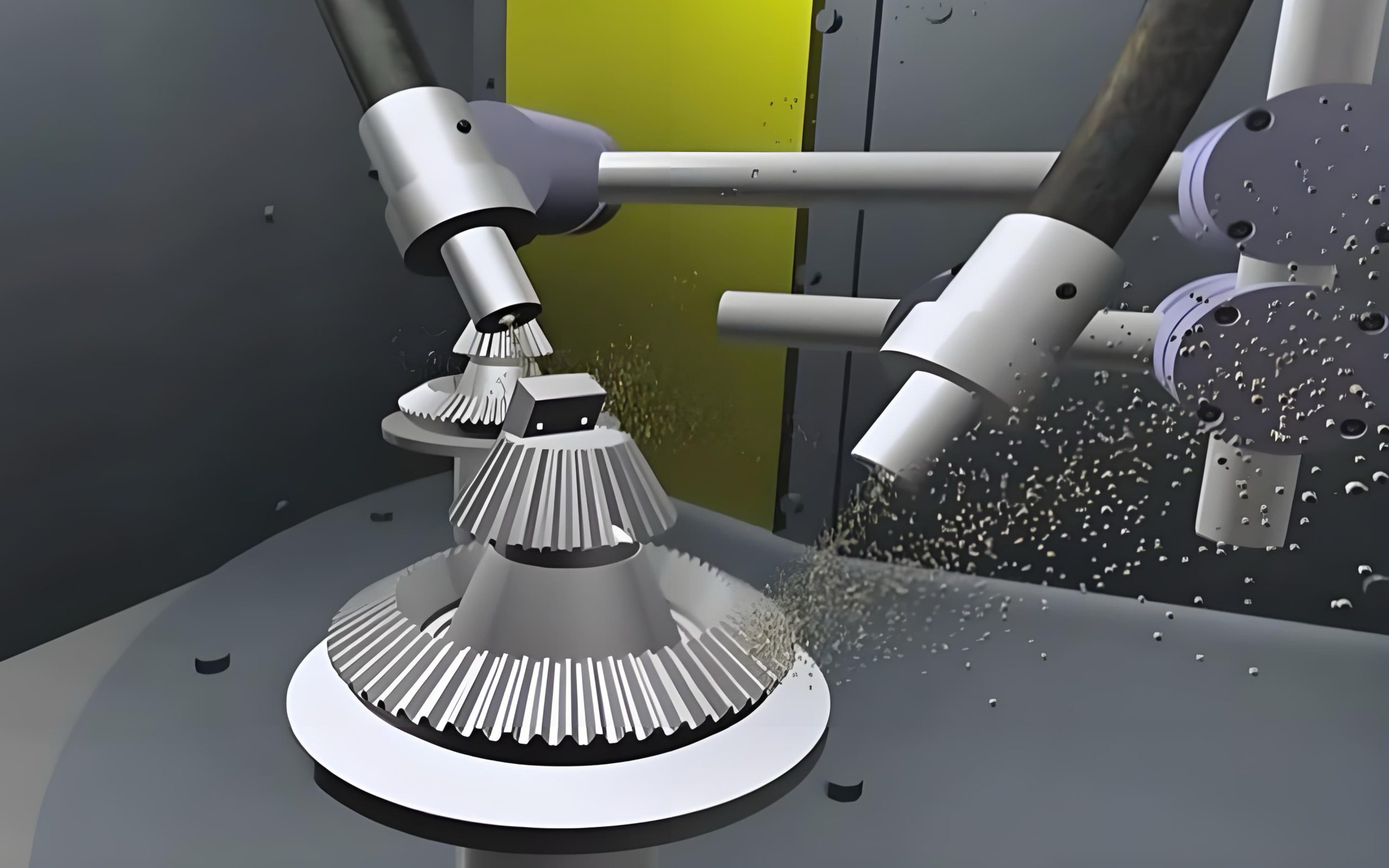
Schematic diagram of shot peening
Typical Applications
Shot peening is widely used in the automotive industry to strengthen components such as gears, coil springs and axles, which are subjected to repeated stresses during their service life. In the aerospace field, shot peening is applied to components such as landing gear and fuselage parts, where durability is critical to safety and these parts generally have simpler geometries that are well suited to the broader, less precise impacts of shot peening.
Laser shock peening overview
Process description
Laser shock peening is a more advanced technique that uses high-energy laser pulses directed at the metal surface, which is usually protected from direct ablation by a transparent cover layer such as water. The laser energy creates a shock wave that propagates through the material, creating deep compressive stresses deep below the surface. The process is more precise than shot peening and can produce a deeper compressive layer, making it ideal for high-stress applications to achieve fatigue and stress corrosion cracking resistance.
A key advantage of laser shock peening is its ability to produce compressive stresses much deeper than shot peening. In some cases, these stresses can penetrate up to 10 mm below the surface, providing enhanced protection for parts subjected to high fatigue loads. But unlike shot peening, laser shock peening leaves a smoother surface. This is particularly beneficial in applications that require both improved stress and surface finish quality, such as aerospace turbine blades and medical implants. The reduced surface roughness can eliminate the need for post-processing steps, saving time and cost.
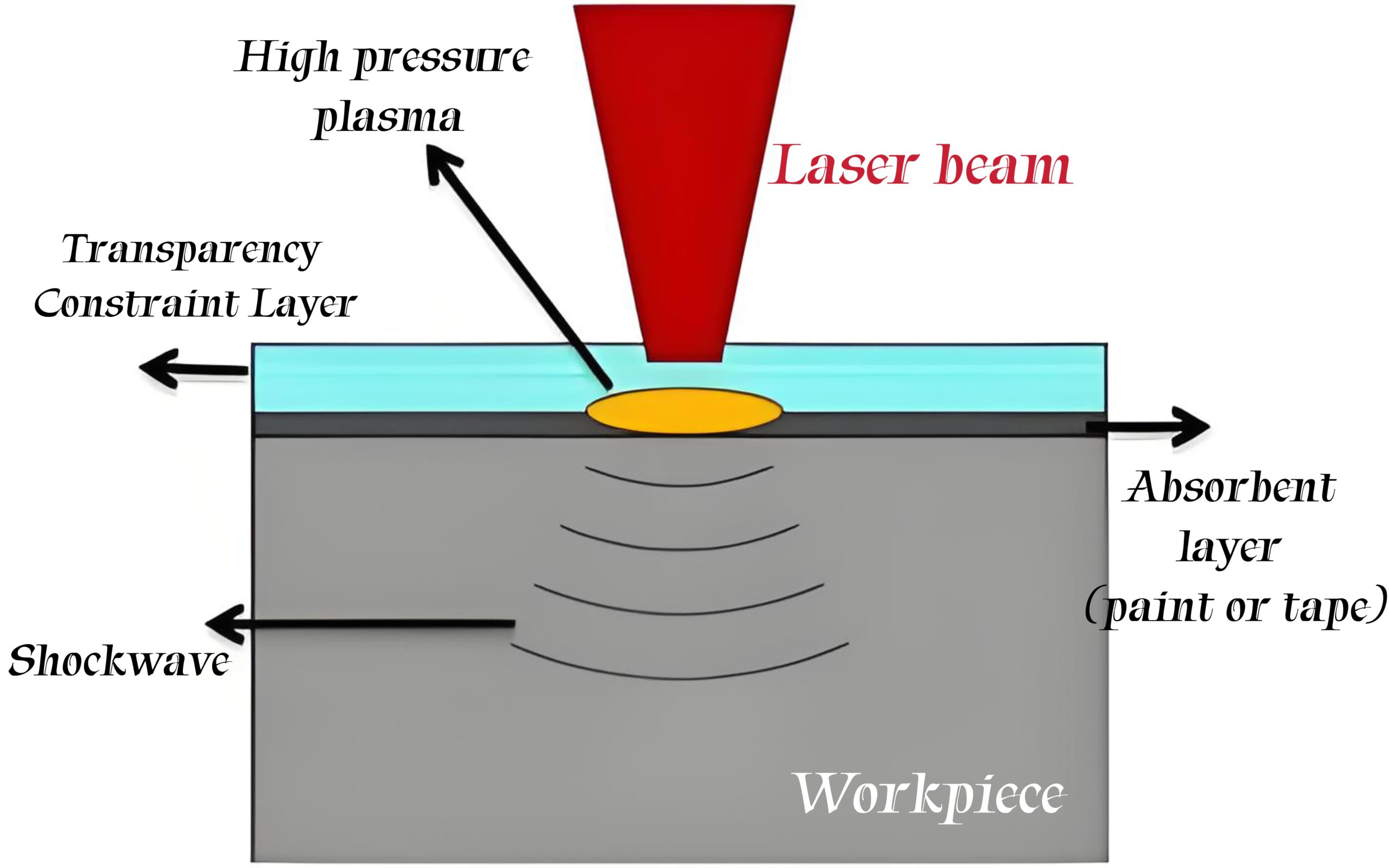
Laser shock peening
However, laser shock peening is significantly more expensive and requires specialized equipment. Its use is typically limited to critical, high-value components where the added cost is amortized through extended service life and improved performance. Although the initial cost can be high, the long-term benefits often outweigh the initial investment, especially in industries such as aerospace and energy where there is no room for potential failure.
Typical Applications
Laser peening is primarily used in industries where components face extreme thermal and mechanical stresses. For example, turbine blades in the aerospace and power generation industries are often laser peened to extend their service life under cyclic loading. Automotive components, such as highly stressed engine parts like pistons, also benefit from the deeper compressive stresses produced by laser peening. In the medical field, laser peening is used to extend the life of implants by improving their fatigue resistance and minimizing corrosion-related failures.
Differences between Shot Peening and Laser Peening
While shot peening and laser peening have the same basic goal of improving fatigue resistance, they differ in several key areas. Here are the key differences between the two methods:
Stress Application Method
Shot peening relies on the random impact of high-speed projectiles on the material surface. Mechanical impact produces compressive stresses, but the process is less precise. Laser peening, on the other hand, uses focused laser pulses to create controlled shock waves, allowing for more precise application of stress.
Depth of penetration
The depth of compressive stress is a key difference between the two processes. Shot peening typically produces shallow stresses (0.1 – 1 mm), while laser peening can penetrate up to 10 mm into the material. This deeper penetration makes laser peening more suitable for components subject to high levels of stress, such as turbine blades or high-performance automotive parts.
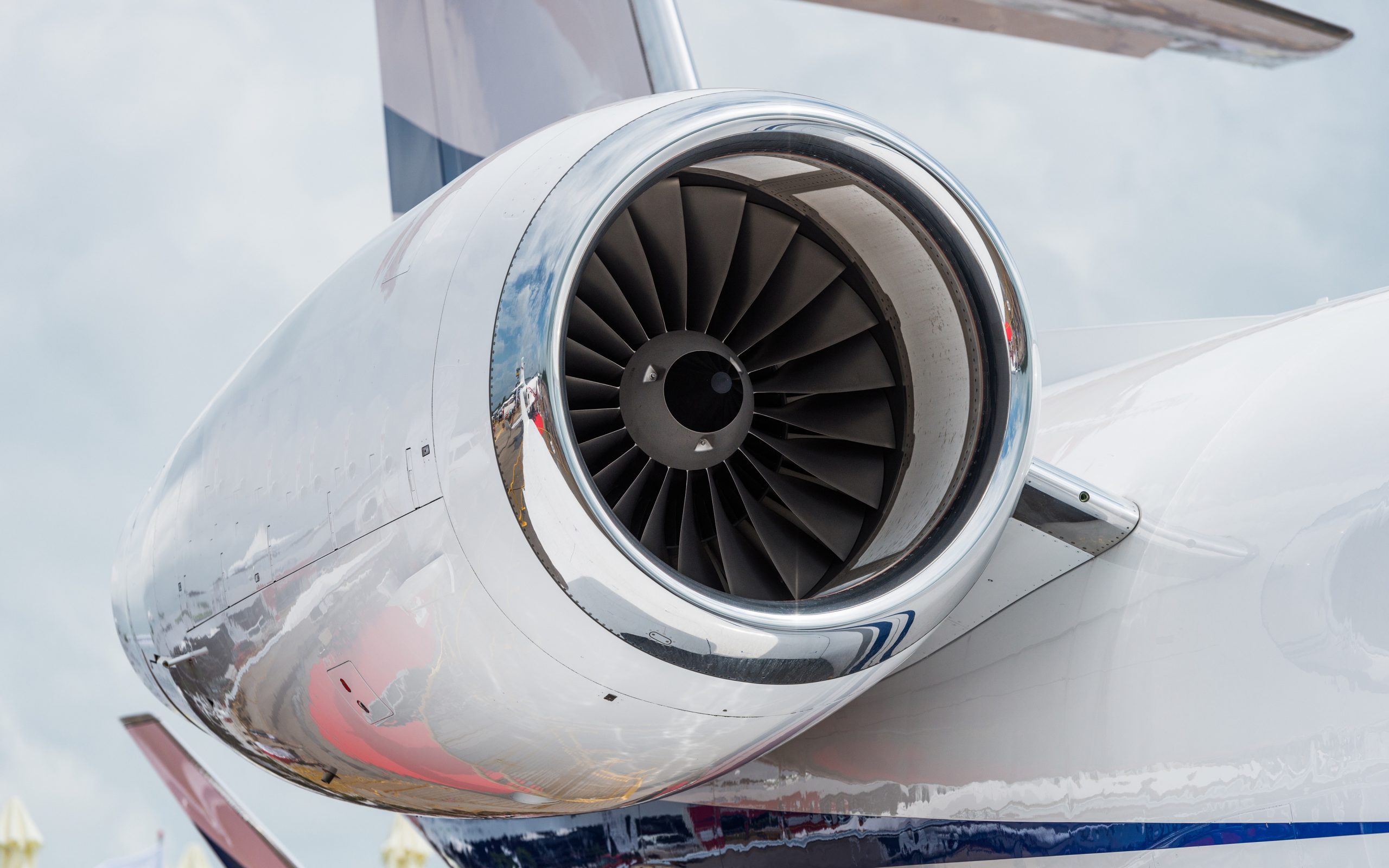
Turbine blades
Precision and control
Due to the nature of the projectile impact, shot peening offers less precision and is better suited for wider surfaces or simpler geometries. In contrast, laser peening allows for highly targeted applications, making it better suited for treating specific areas such as complex or delicate components.
Surface finish
Shot peening typically leaves a rough surface that may require additional finishing in sensitive applications. However, laser peening produces a smoother surface with fewer defects, reducing the need for further processing.
Cost and accessibility
In terms of cost, shot peening is more accessible due to its lower setup and operating expenses. It is widely used in industries such as automotive and construction where cost-effectiveness is a priority. Laser peening, on the other hand, is more expensive and is often used to improve critical component performance in industries such as aerospace and energy, providing long-term savings through extended component life and reduced maintenance.
Metal Type Determines Method
Different metals react differently to the stresses produced by shot peening and laser peening. Choosing the appropriate peening method depends on the metal’s characteristics, the application environment, and the desired performance results.
Steel
Steel is one of the most commonly treated metals in industrial applications, especially in the automotive and aerospace industries. Shot peening is commonly used for steel parts, especially those exposed to cyclic loading, such as springs, gears, and aircraft fuselage components. The shallow compressive stresses produced by shot peening are sufficient for these parts. However, for high-performance steel alloys used in aerospace or power generation, laser peening is more popular due to its ability to produce deeper stresses, improving fatigue resistance under extreme conditions.
Aluminum
Aluminum is widely used in industries such as automotive and aerospace where lightweight materials are critical. For general-purpose aluminum parts, shot peening is sufficient, while for aerospace-grade aluminum alloys, laser peening is more often used when fatigue resistance needs to be enhanced to cope with the high stresses of flight.
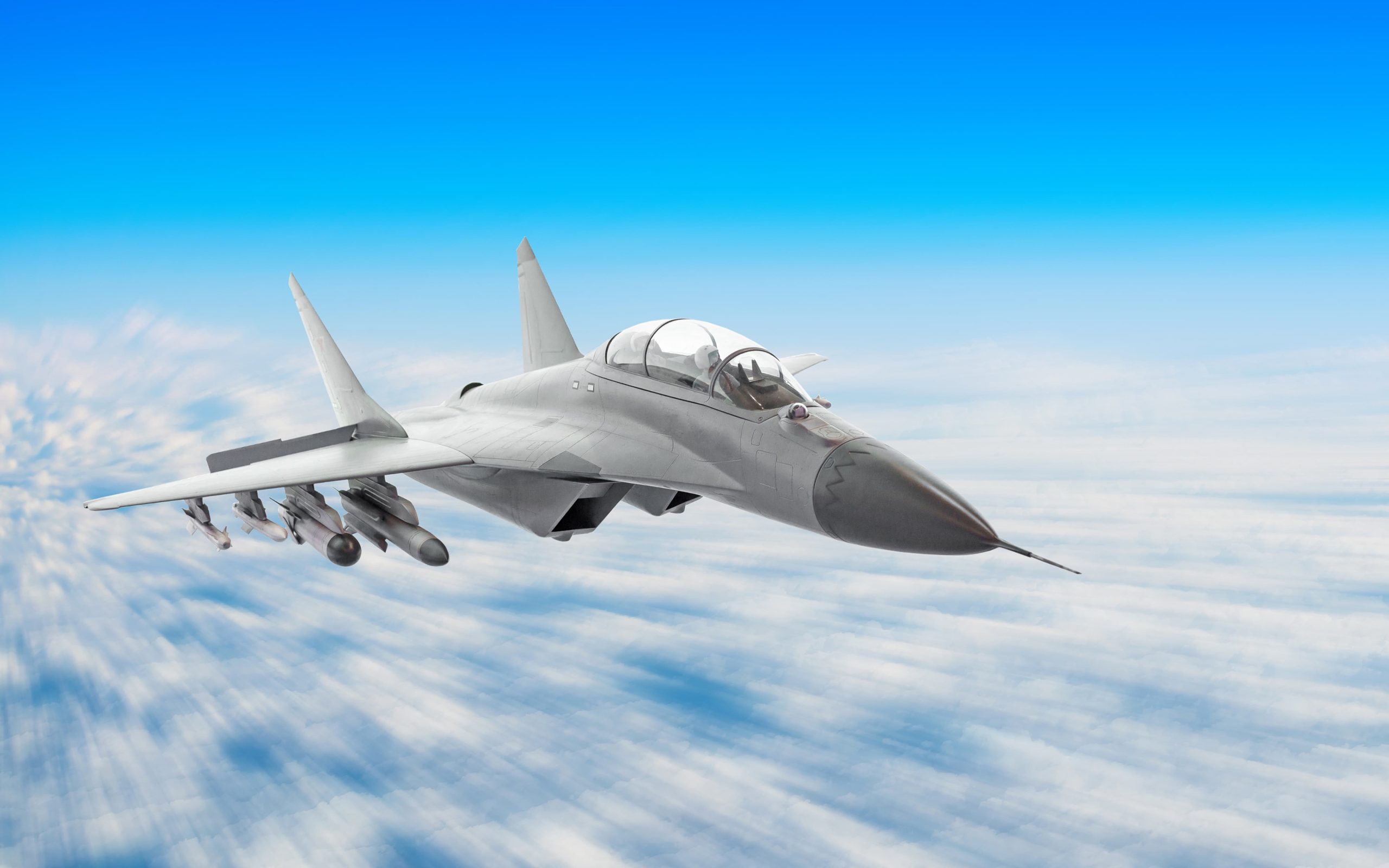
Aerospace-grade materials need to cope with more severe environmental stresses
Titanium
Titanium is known for its high strength-to-weight ratio and corrosion resistance, which makes it popular in aerospace and medical applications. Whether it is titanium fan blades that must withstand high mechanical stresses and increasing temperatures, or joint replacements or dental implants that must improve fatigue resistance and life, laser peening creates a deep compressive layer that improves fatigue life without compromising the material’s surface finish, and it can provide accurate precision and control.
Nickel Alloys
Nickel superalloys are often used in high-temperature environments such as gas turbines and other critical power generation applications. Due to their operating conditions, these alloys are susceptible to fatigue and thermal stresses, so surface treatment is critical to their performance. Laser peening is the preferred method for treating nickel alloy components because the deeper compressive stresses it produces protect turbine blades and other critical components from failure under cyclic loading and high temperature exposure, thereby extending the service life of these components.
Comparative Case Studies
Automotive Industry Cases
- Shot Peening of Gearbox Parts
Shot peening is commonly used in the automotive industry to enhance the fatigue life of gearbox components such as gears, shafts and housings. The high-speed impact of the metal projectile induces compressive stresses on the surface, effectively improving wear resistance and fatigue resistance. Research has shown that shot peening can improve the fatigue strength of gearbox parts by up to 30%. For components subject to cyclic loading, this enhancement helps prevent premature failure.
Shot peening is generally more cost-effective than laser peening and more suitable for large-scale automotive manufacturing production due to its lower setup cost and shorter processing time.
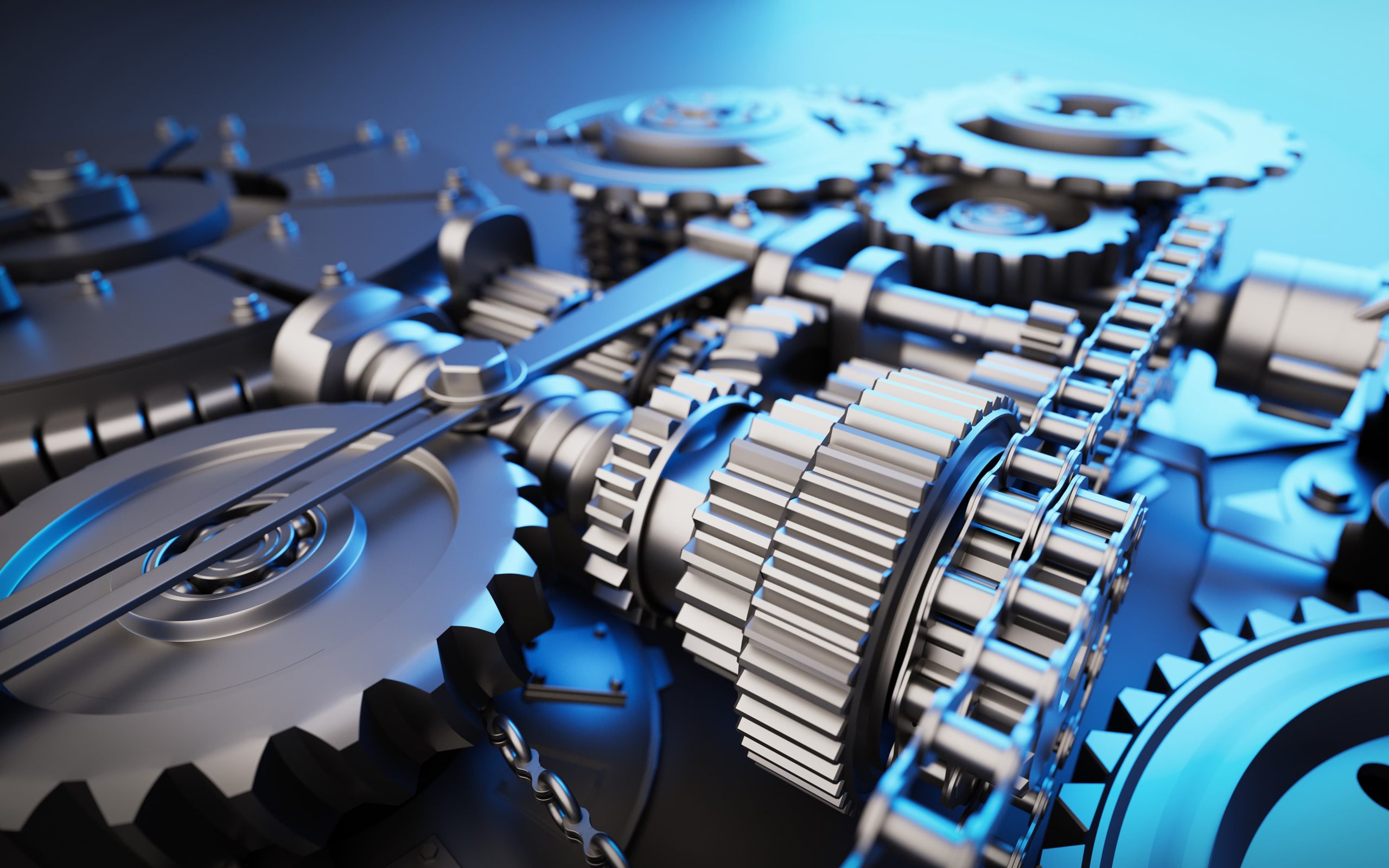
Gear structure
- Laser peening of engine components
Laser peening is increasingly being used for critical engine components such as pistons and crankshafts. The process involves focused laser pulses that produce deeper compressive stresses than shot peening. Improvements in fatigue life in high-stress areas with laser peening are typically more than 50%. This is particularly important for components exposed to extreme thermal and mechanical conditions.
Although laser peening is more expensive, its benefits in terms of life and performance are also significant, making it ideal for high-performance vehicles.
Aerospace Cases
- Shot peening of fuselage components
Shot peening is widely used for fuselage components, including structural elements such as fuselage skins and wing components. The process enhances the fatigue resistance of these components and can increase the fatigue life of fuselage materials by up to 200%, which is critical to maintaining structural integrity and safety.
The lower cost and simpler setup of shot peening make it a top choice for many airframe components, allowing manufacturers to implement it efficiently on a variety of parts.
- Laser shock peening of turbine blades
In contrast, laser shock peening is more commonly used for turbine blades in jet engines, where fatigue resistance and stress distribution requirements are critical. The deeper compressive stresses produced by laser shock peening significantly enhance the durability of turbine blades and can extend the life of turbine blades by up to 70%, which is critical for flight safety, especially in high-stress environments where blade failure can have catastrophic consequences.
Investments in laser shock peening can be justified by reducing the risk of failure and extending the service life of these critical components, making it a valuable process in aerospace engineering.
- Medical industry cases
Laser shock peening of medical implants
Laser shock peening is increasingly being used for orthopedic devices such as hip and knee implants. These implants face significant mechanical loads over time, and the method’s ability to effectively induce deep compressive stresses can extend the life of these implants. Medical implants that have been laser shocked have an average life increase of 100%. Compared to traditional surface treatments, laser peening offers a more effective solution for improving implant durability, reducing the risk of complications and the need for revision surgery.
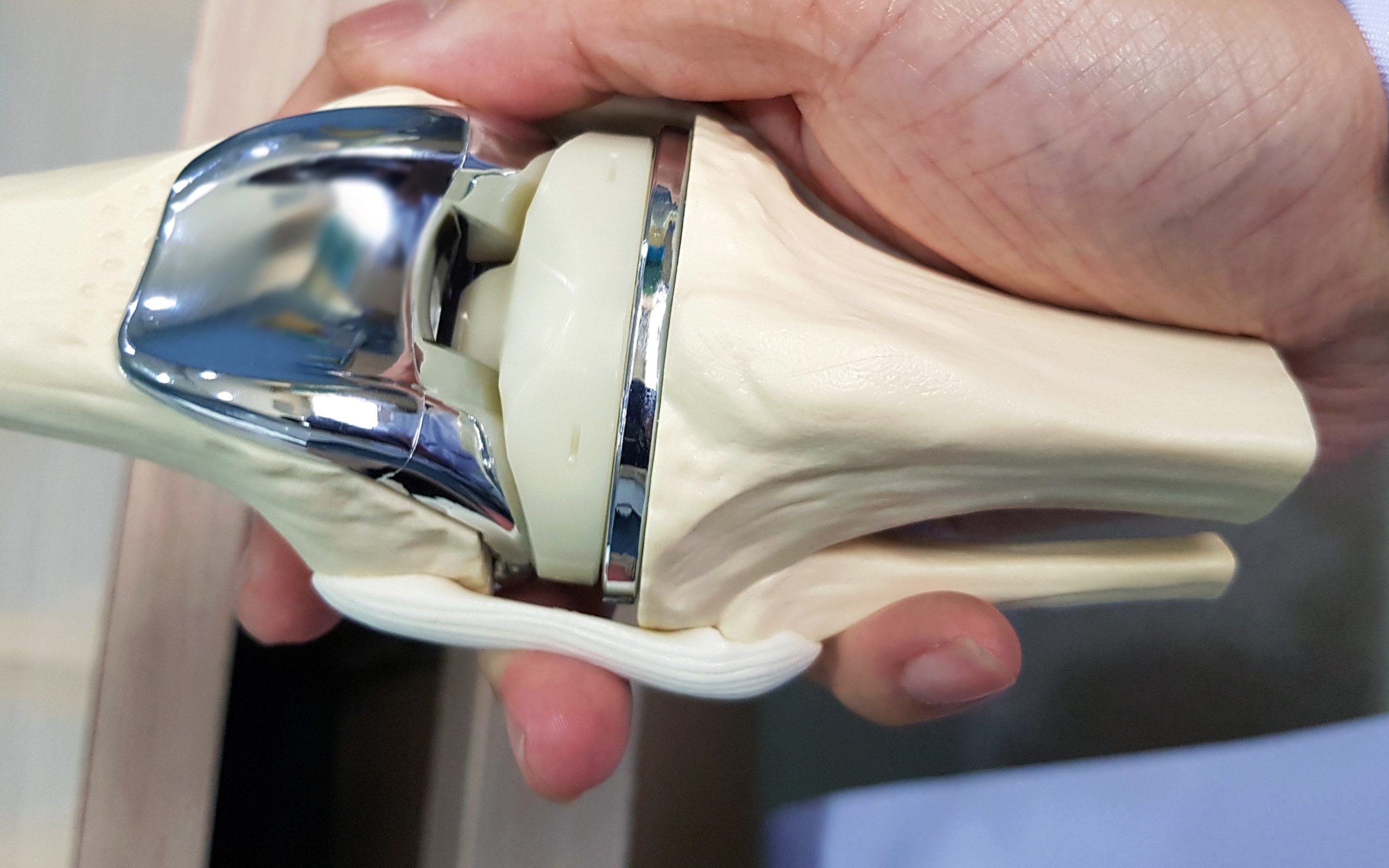
Joint implants
In summary, shot peening and laser shock peening have their own advantages and disadvantages in metal finishing.
The advantages of shot peening are low cost, low setup and operating costs, and are widely used in cost-effective industries such as automobiles. It can effectively improve the fatigue strength of materials and is often used for general steel parts and simple geometric parts such as automotive gears and springs. However, its disadvantages are that it will leave a rougher surface, which may require additional finishing, and the compressive stress generated is shallow.
The advantages of laser shock peening are obvious. It can produce deeper compressive stress, even penetrating 10 mm below the surface of the material, which is suitable for high-stress applications such as turbine blades; it has high precision and is suitable for processing complex or delicate parts; it can leave a smoother surface and reduce post-processing steps. However, it is expensive and requires specialized equipment. It is usually used for critical high-value parts such as aerospace.
In different metal applications, the two also have different choices due to metal properties and application environment. Overall, the two strengthening methods play an important role in their respective applicable fields and need to be considered comprehensively according to specific needs.
Reviewing the entire article, you will see that both shot peening and laser peening play a vital role in improving component performance and longevity in a variety of industries. Whichever method you choose, factors such as material type, part complexity, performance requirements, and cost impact must be considered. Understanding the unique advantages of each method will enable you to make an informed decision for your specific application.
Filters