How do ceramic beads replace corundum to achieve efficient surface cleaning?
January 15, 2025
Traditional corundum abrasives have always been the mainstream choice in the industry due to their high hardness, strong cutting performance and wide applicability. However, with the increasing requirements for surface quality, environmental protection performance and economic benefits, ceramic blasting beads for blast cleaning have become the preferred material in the field of precision machining due to their superior characteristics.
Overview of corundum
Brown Fused Aluminum Oxide
Made from bauxite, iron filings and coke by high-temperature samelting, the main component is aluminum oxide (Al₂O₃), usually between 90% and 95%, and contains a small amount of iron oxide and silicon oxide.
Main characteristics
High hardness (Mohs hardness is about 9) and strong wear resistance.
Excellent toughness, suitable for heavy cutting and high-intensity cleaning processes.
Relatively low price, high cost performance.
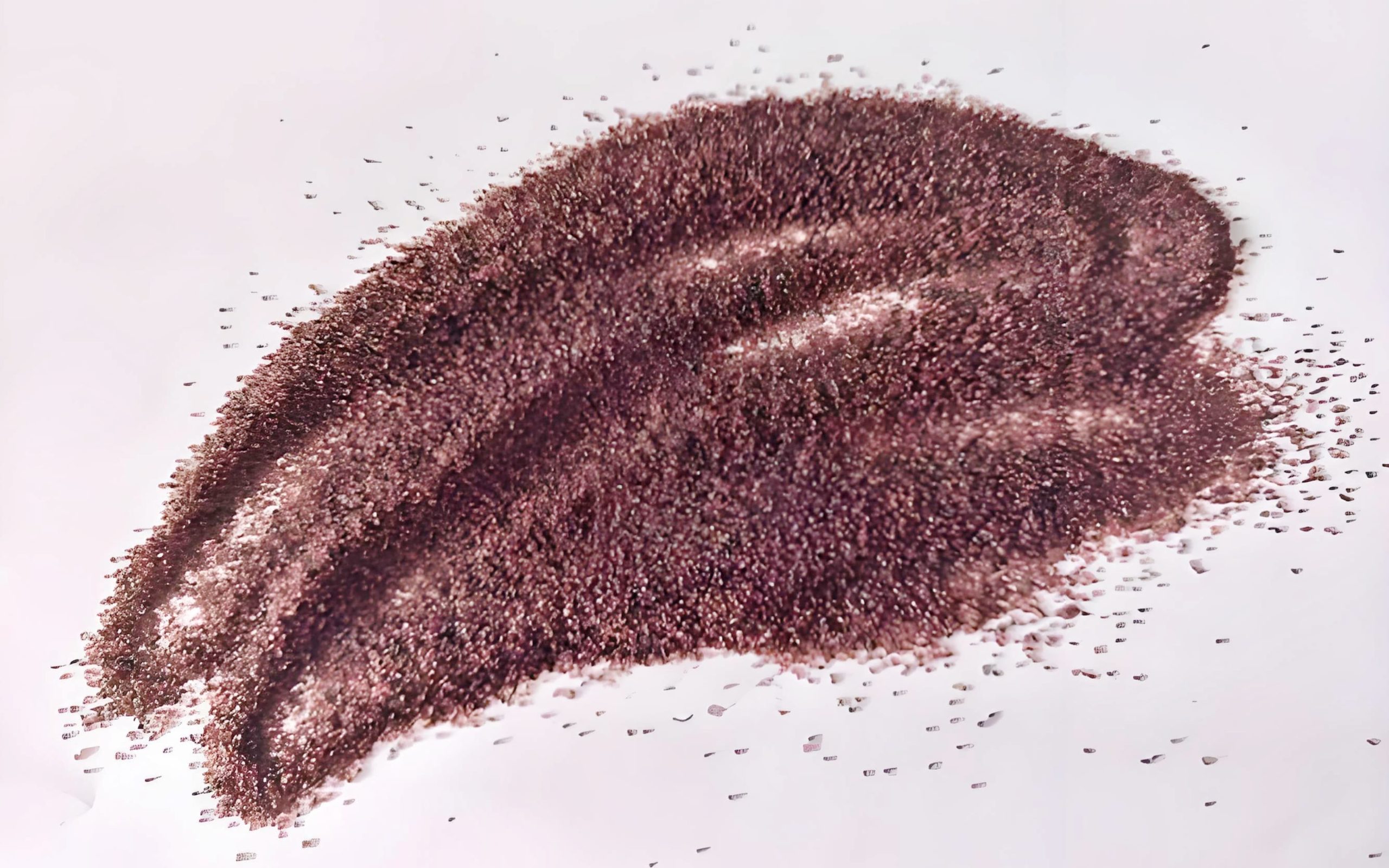
Typical applications
- Cleaning dirt from engine cylinders
- Removing rust and old coatings from chassis
- Removing oxide layers and coatings from engine turbine blades
- Preliminary cleaning of heavy equipment parts such as gears, bearing seats, etc.
- Removing burrs and oxides from cast iron parts
White Fused Aluminum Oxide
Made from high-purity alumina, it is smelted at high temperatures and cooled, with a purity of more than 99%.
Main features
High hardness (Mohs hardness is about 9) and strong cutting performance.
High purity, suitable for processing environments with strict requirements on material cleanliness.
Low toughness, not suitable for high impact processes.
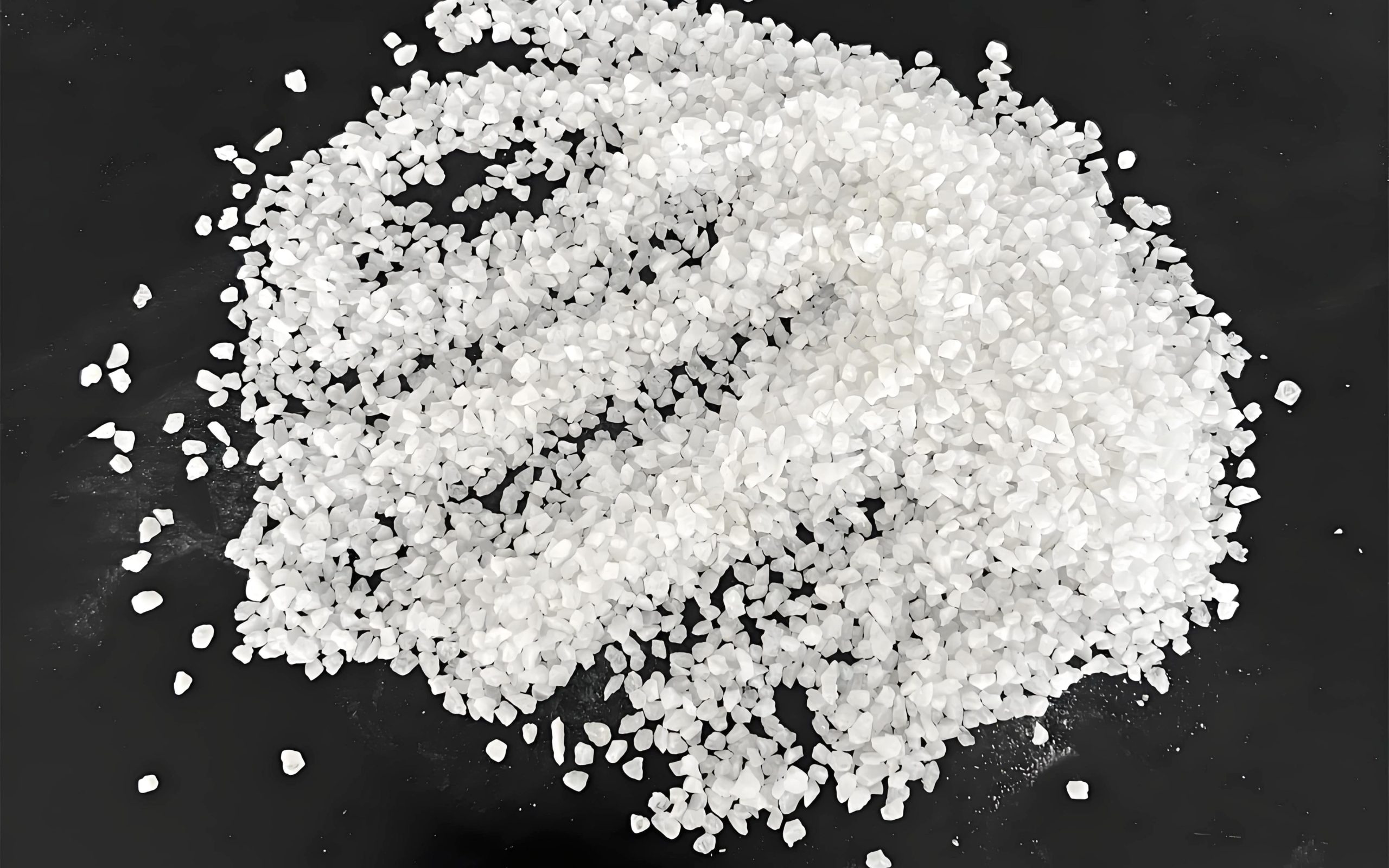
Typical applications
- Removing surface defects of high-end tools
- Improving the wear resistance and corrosion resistance of mold surfaces
- Fine cleaning and surface strengthening of landing gear components
Similarities and differences between brown corundum and white corundum
Similarities
High hardness and wear resistance, suitable for a variety of surface cleaning processes.
Strong resistance to high temperature and chemical corrosion.
Commonly used in sandblasting of materials such as metals, glass and ceramics.
Differences
White corundum has high purity and better cutting performance than brown corundum, suitable for fine processing.
Brown corundum has high toughness and is suitable for rough processing, while white corundum is more suitable for fine processing.
Limitations of Corundum Surface Cleaning
Although corundum media performs well in sandblasting, its performance in environmental protection, ease of operation, dust control, etc. needs to be improved, and it cannot fully meet the needs of high-precision and high-cleanliness processes.
Overview of ceramic beads
Zirconium oxide materials with a purity of more than 95% are used to make high-density, high-sphericity white spherical peening shots.
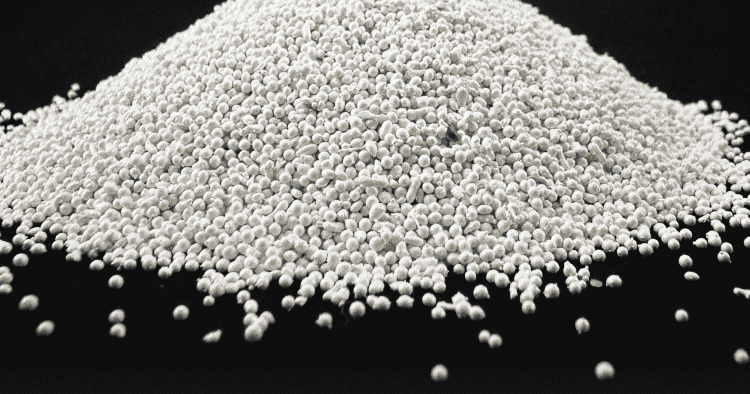
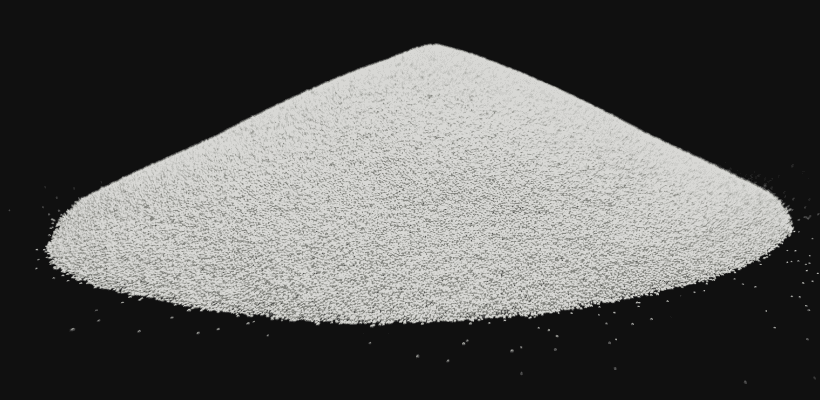
Main performance and advantages
- High-purity materials ensure the excellent quality and stability of the product, especially suitable for industries with extremely high requirements for material purity.
- White spherical design: reduce color pollution and improve product appearance quality.
- High density, higher energy transfer efficiency, and more significant sandblasting effect.
- High sphericity design: reduce uneven processing caused by irregular shapes and improve processing accuracy.
- Low wear rate: extend service life and reduce equipment maintenance costs.
- Environmentally friendly: non-toxic and harmless, in line with international environmental standards.
- Wide applicability: suitable for precision surface treatment of metal, ceramic, glass and other materials.
Typical application scenarios
Aerospace field
- Remove tiny impurities from the surface of gas turbine engine blades
- Enhance the fatigue resistance and corrosion resistance of landing gear components
- Ensure the integrity and balance of guide blades and fan impellers
Medical device manufacturing
- Ensure that the surface of surgical instruments is clean and flawless
- Prevent fine burrs from remaining on ducts and connectors
- Fine sandblasting of artificial joints and dental implants
Automotive manufacturing industry
- Cleaning and polishing fuel injectors
- Remove tiny burrs and dirt from cylinder heads and valve components
- Cleaning brake system components such as brake discs and brake pads
Electronic components and semiconductor processing
- Remove tiny particles from the surface of silicon wafers
- Make the surface of microprocessor heat sinks more uniform
- Ensure that the surface of precision connectors is clean and burr-free
Metal and glass processing industry
- Make the surface of stainless steel trims such as decorative panels and door handles smooth
- Frost treatment of glass curtain walls and lighting
- Achieve high-precision surface treatment of precision instrument housings
Comparison of surface cleaning between ceramic beads and corundum
Same function
- Coating and paint removal
Both ceramic sandblasting beads and molten alumina are good at removing solid coatings and old paints, and are suitable for coating cleaning of metal components.
- Surface cleaning and preparation of metal, plastic and ceramic parts
Both are suitable for processing a variety of materials, including metal castings, plastic molds and ceramic products.
- Deburring and surface hardening
Ceramic sandblasting beads can perform precision deburring due to their high density and spherical structure. Fused alumina is widely used for deburring large metal parts due to its hardness and strong grinding force. Both can significantly improve the surface hardness and fatigue resistance of parts.
Common characteristics
- Can handle hard materials, high temperature resistance and chemical inertness.
- Provide effective surface treatment solutions to improve product performance and life.
Differences
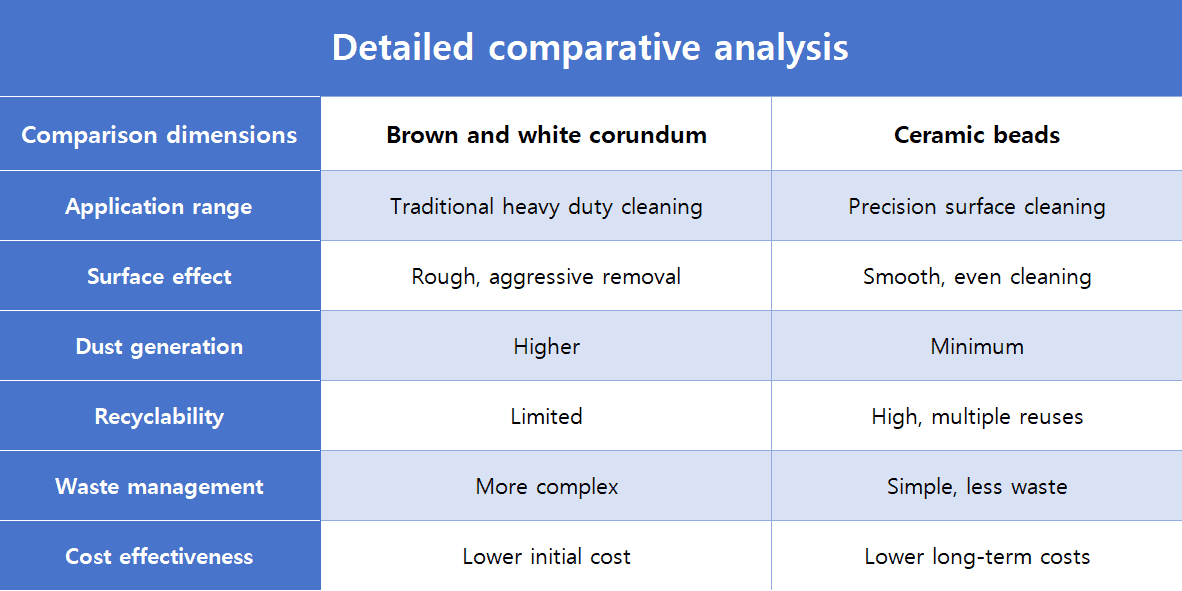
Application range
Brown fused aluminum oxide and white fused aluminum oxide are mainly used for traditional heavy cleaning tasks, suitable for processing scenes with low surface roughness requirements.
Ceramic blasting beads are widely used in high-precision part processing and surface treatment with their precision surface cleaning capabilities.
Surface effect
Brown fused aluminum oxide and white fused aluminum oxide provide strong and fast removal, and the surface after treatment is relatively rough.
Ceramic beads have a more uniform treatment effect and a smoother surface.
Dust generation
Corundum tends to generate a lot of dust during the blasting process, while ceramic blasting beads are almost dust-free.
Recyclability
Ceramic beads can be recycled more than 30 times, while corundum has a limited recycling rate and a high wear rate.
Waste management
Brown corundum and white corundum generate more waste, which is relatively complex to manage and handle.
Ceramic blasting media generate less waste, which helps save processing costs.
Cost-effectiveness
Brown fused aluminum oxide and white fused aluminum oxide have lower initial costs and are suitable for short-term use or mass production environments.
Ceramic blasting media have a slightly higher initial investment, but they have a long service life and high recyclability, which is economical in the long run.
Real case analysis
In order to improve cleaning efficiency and reduce maintenance costs, an aviation manufacturer conducted multiple rounds of cleaning project comparison tests on ceramic blasting beads and traditional molten alumina media in order to select the best solution.
Cleaning time
The high density and spherical structure of ceramic beads achieve a more uniform cleaning effect while avoiding the need for repeated blasting, thereby reducing cleaning time. Ceramic blasting media: cleaning time is reduced by 15%.
Corundum: Due to its high hardness but fast wear, continuous cleaning efficiency is low.
Abrasive consumption
Ceramic blasting beads: Abrasive consumption is reduced by 30%. The high wear resistance and reusability of ceramic beads significantly reduce the amount of abrasive used.
Fused aluminum oxide: Abrasives wear quickly after multiple uses, and the breakage rate is high, resulting in high consumption.
Post-cleaning pollution
Ceramic blasting beads: Post-cleaning pollution is significantly reduced, with very little residual dust, and the negative impact on the working environment is greatly reduced.
Corundum: The high wear rate leads to a large amount of dust pollution, which not only affects the cleaning effect, but also puts higher requirements on the environment and equipment maintenance.
Equipment maintenance requirements
Ceramic beads: Low equipment wear and reduced maintenance frequency.
Fused aluminum oxide: Due to its high breakage rate, it causes more severe wear on the equipment, increasing the maintenance and replacement frequency of the equipment.
Economic cost
The initial investment of ceramic blasting beads is higher than that of corundum, but the long-term cost is reduced by 25%. It can also provide higher production efficiency and stable cleaning effects, providing companies with significant competitive advantages.
Experience the excellent performance of ceramic blasting beads
In order to help customers more intuitively experience the high performance, economic benefits and environmental advantages of ceramic media in surface cleaning and treatment, we specially provide free trial opportunities.
Through the trial, you will be able to personally verify the following key advantages:
- Significantly shorten processing time and optimize production processes.
- Reduce abrasive consumption and reduce operating costs.
- Optimize surface quality and meet high-precision requirements.
- Environmentally friendly and dust-free operation improves the safety and cleanliness of the working environment.
Apply for a free trial now!
Welcome to contact us for professional application support and product recommendations to help you reach new heights in the field of surface treatment!
Filters