Aluminum Oxide Blasting Process Operation Issues and Solutions
August 27, 2024
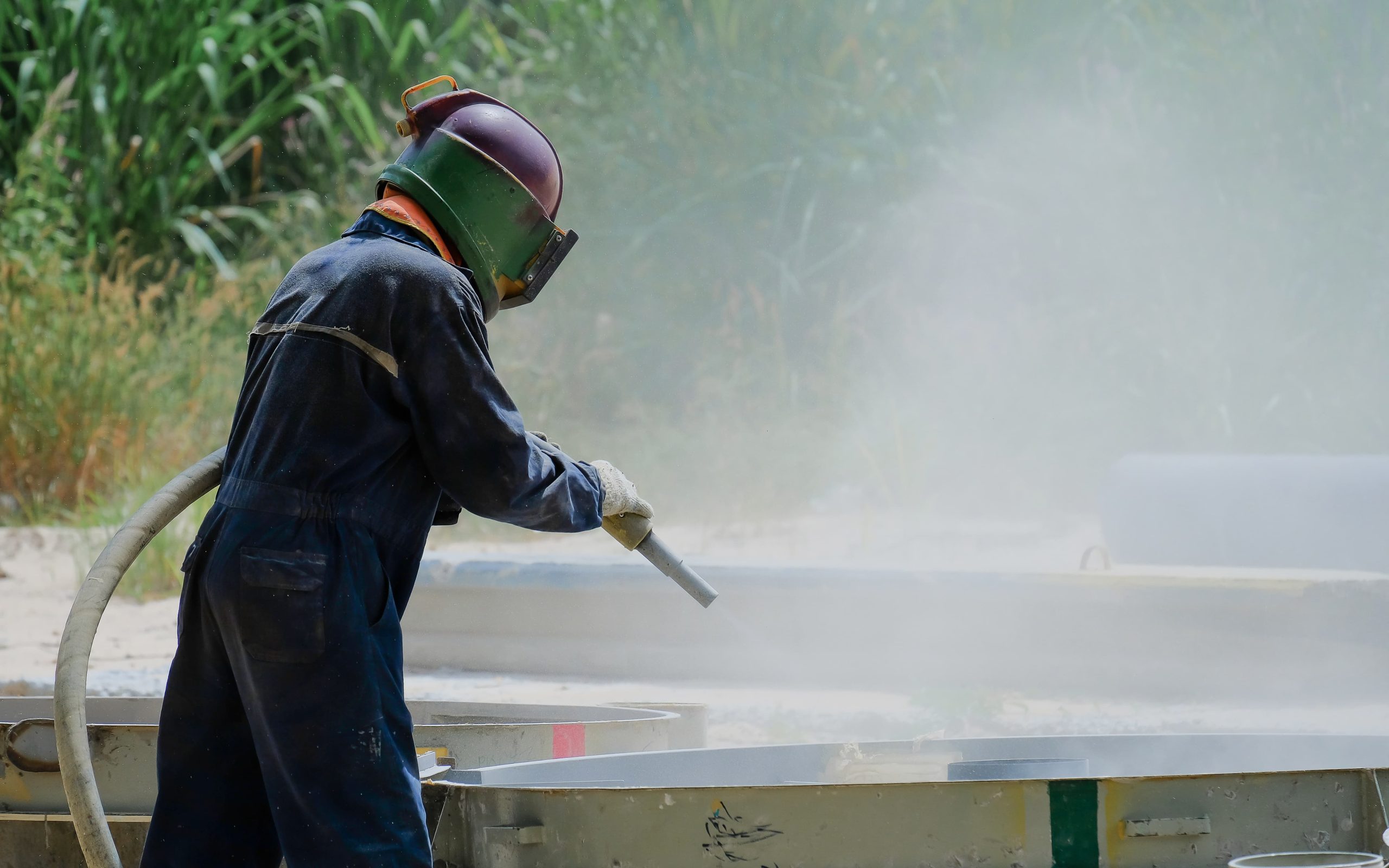
Aluminum oxide blasting media, as a surface treatment technology, has been widely used in various industries. However, despite the significant advantages of alumina sandblasting technology, various issues may arise during actual operation due to the complexity of equipment, materials, and operating conditions. If not properly handled, these issues can directly affect the final processing effect and may even lead to a decline in product quality. This article will explore 18 of these issues in detail, provide corresponding solutions and improvement measures, and conclude with some tips for optimizing the alumina sandblasting effect to help you better utilize this technology.
Issue 1: Equipment Wear
- Description: Due to the high hardness of alumina, sandblasting may cause accelerated wear of sandblasting equipment (especially nozzles and pipes).
- Solution: Choose nozzles and pipes made from high-wear-resistant materials such as tungsten carbide or ceramics to significantly reduce equipment wear.
- Improvement Measures: Regularly monitor equipment wear; maintain and replace worn parts; adjust sandblasting pressure and media flow in a timely manner; avoid excessive use of the same equipment.
Issue 2: Dust Handling Problems
- Description: A large amount of dust generated during sandblasting may affect the health of operators.
- Solution: Install efficient dust removal equipment to reduce dust emissions, such as pulse dust collectors or electrostatic precipitators. Operators should also be equipped with appropriate personal protective equipment, such as respirators and protective clothing.
- Improvement Measures: Optimize the ventilation system in the working environment, regularly inspect and maintain dust removal equipment to ensure its normal operation. Wet sandblasting technology can also effectively reduce dust generation.
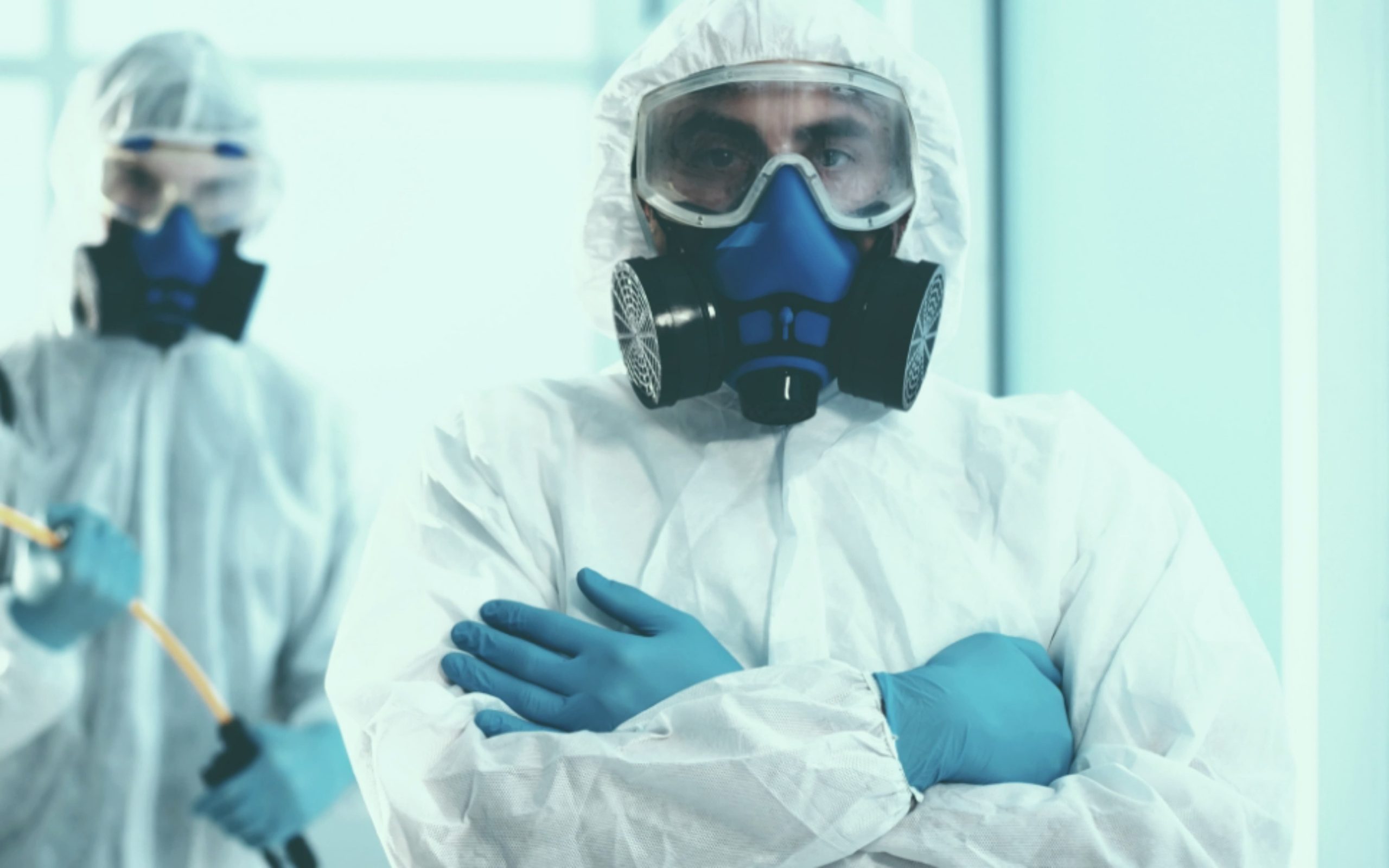
Protective dress demonstration
Issue 3: Uneven Sandblasting Pressure
- Description: Uneven pressure during sandblasting may lead to uneven surface treatment, affecting the final surface quality.
- Solution: Use high-quality pressure control equipment to ensure pressure stability. Regularly calibrate and maintain pressure control equipment to ensure accuracy.
- Improvement Measures: Experiment to determine the optimal sandblasting pressure, adjust pressure settings according to different materials and process requirements, and achieve the best effect.
Issue 4: Media Recovery and Reuse Issues
- Description: Used aluminum oxide blasting media may become contaminated or mixed with impurities, leading to a decline in sandblasting effect.
- Solution: Set up a dedicated media recovery system with separation and cleaning devices to remove impurities and ensure media purity. Media that is significantly worn or contaminated should be replaced promptly.
- Improvement Measures: Regularly check the condition of the media, use microscopes or other detection methods to assess media quality, and ensure it remains efficient during reuse.
Issue 5: Surface Roughness Not Meeting Standards After Sandblasting
- Description: The surface roughness of the workpiece after sandblasting may not meet the expected requirements, possibly being too rough or too smooth, affecting subsequent processing.
- Solution: Adjust the particle size and distribution of the media according to the desired surface roughness. Appropriately shorten or extend sandblasting time to control surface roughness.
- Improvement Measures: Adjust the nozzle angle so that the sandblasting media impacts the surface at the optimal angle, gradually achieving the desired roughness. For high-precision parts, determine the best sandblasting parameters through small batch tests.
Issue 6: Difficulty Controlling Media Flow Rate
- Description: Under different operating conditions, it may be challenging to precisely control the flow rate of aluminum oxide blasting media, affecting the sandblasting effect.
- Solution: Use high-precision flow control valves and sensors to monitor media flow in real-time and ensure a stable sandblasting process.
- Improvement Measures: Implement an automated control system to achieve precise control of media flow rate, and regularly inspect and calibrate flow control equipment to ensure proper operation.
Issue 7: Material Overheating Leading to Deformation or Damage
- Description: In high-intensity sandblasting, excessive heat generated from friction may cause deformation or damage to the treated material.
- Solution: Control sandblasting time and pressure to avoid prolonged, high-intensity operations. Intermittent sandblasting can be used to give the material time to cool down.
- Improvement Measures: Introduce a cooling system or use cold sandblasting technology to reduce the heat generated during processing and minimize the risk of thermal deformation of the material.
Issue 8: Excessive Consumption of Alumina Media
- Description: Frequent sandblasting operations may lead to excessive consumption of alumina media, increasing production costs.
- Solution: Optimize process parameters, such as adjusting sandblasting pressure, flow, and time to reduce media waste. Additionally, recycling and reusing uncontaminated media can also reduce overall consumption.
- Improvement Measures: Regularly monitor media usage, use intelligent sandblasting systems to automatically adjust the quantity based on actual needs, and improve efficiency.
Issue 9: Chemical Reactions Between Media and Materials
- Description: Under certain conditions, alumina media may chemically react with the treated material (though this is rare), leading to a decline in surface quality or the formation of undesirable surface films.
- Solution: Choose suitable sandblasting media and working environments to avoid adverse reactions with materials. If necessary, consider using media with stronger chemical inertia.
- Improvement Measures: Conduct chemical stability tests on materials before sandblasting to ensure no adverse reactions occur between media and materials. Additionally, consider using inert gas environments or controlling environmental humidity to reduce the occurrence of chemical reactions.
Issue 10: Cleaning Issues After Surface Treatment
- Description: Residual alumina powder or debris may remain on the material surface after sandblasting, affecting subsequent surface treatments such as coating or plating.
- Solution: Implement dedicated cleaning processes, such as ultrasonic cleaning or high-pressure air cleaning, to thoroughly remove surface residues and ensure smooth subsequent processes.
- Improvement Measures: Improve cleaning equipment and processes to shorten cleaning time, increase efficiency, and reduce environmental impact during cleaning.
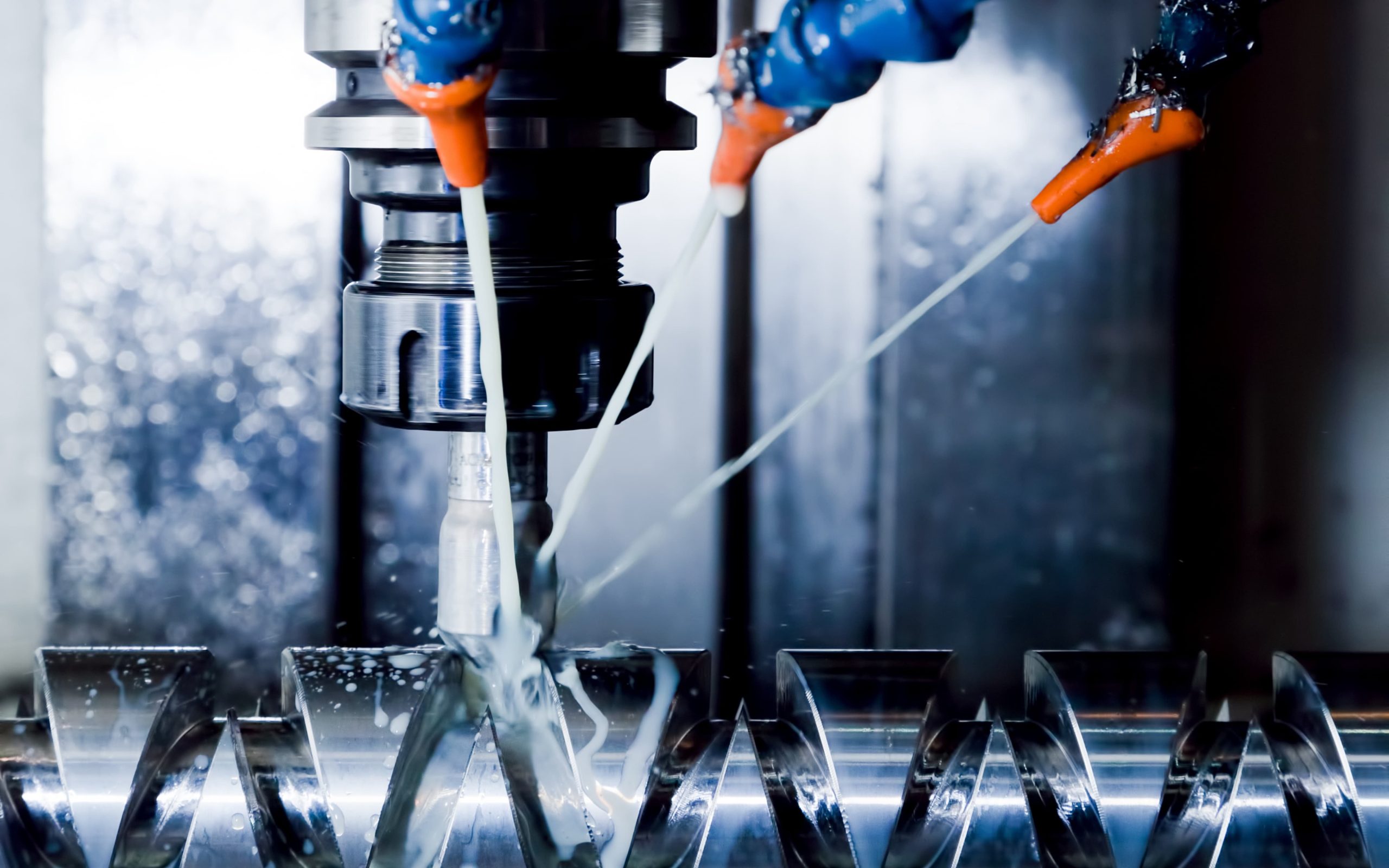
cleaning machine
Issue 11: Static Electricity Accumulation in Media
- Description: In dry sandblasting operations, static electricity may accumulate in the sandblasting media due to friction, affecting the sandblasting effect.
- Solution: Install static elimination equipment, such as ion blowers or grounding devices, to reduce the risk of static accumulation.
- Improvement Measures: Implement wet sandblasting processes to effectively reduce static electricity generation, and use conductive materials, such as conductive pipes or nozzles, in the sandblasting system to dissipate static electricity and reduce media accumulation.
Issue 12: Vibration Effects During Sandblasting Operation
- Description: During the processing of thin-walled or precision parts, vibrations generated by the sandblasting equipment may affect the fixture and the uniformity of surface treatment.
- Solution: Design or install shock-absorbing devices on sandblasting equipment and worktables to reduce the impact of vibrations on operations. Ensure that the workpiece is securely fixed during sandblasting to avoid displacement or loosening due to vibrations.
- Improvement Measures: Adjust equipment operating parameters, such as sandblasting pressure and flow, to reduce vibration sources and stabilize the sandblasting effect.
Issue 13: Media Storage Problems
- Description: Alumina media may be affected by oil, moisture, or other contaminants during storage or operation, reducing the sandblasting effect.
- Solution: Store alumina media in a dry, clean environment to prevent contamination or moisture absorption. Clean the media before use to remove surface contaminants and ensure media purity.
- Improvement Measures: Regularly check media for contamination or degradation and replace with new alumina media as needed to ensure sandblasting quality.
Issue 14: Oxidation of Workpieces After Sandblasting
- Description: If not promptly processed after sandblasting, the surface of the treated workpiece may rapidly oxidize, affecting final surface quality.
- Solution: Immediately perform subsequent treatments after sandblasting, such as coating, passivation, or protective coating, to prevent surface oxidation.
- Improvement Measures: Use inert gas coverage on the workpiece surface after sandblasting to prevent oxidation when high surface quality is required. Regularly monitor oxidation using surface inspection instruments to ensure timely subsequent processing.
Issue 15: Noise Pollution from Sandblasting Operations
- Description: High noise levels generated during sandblasting may damage operators’ hearing and cause noise pollution in the working environment.
- Solution: Install noise isolation equipment, such as soundproof panels or windows, outside the sandblasting chamber; or provide operators with earplugs or noise-canceling earmuffs.
- Improvement Measures: Choose sandblasting equipment with low noise design or modify existing equipment to reduce operational noise.
Issue 16: Difficulty Ensuring Consistency of Sandblasting Effects
- Description: In mass production, especially with multiple batches, consistency issues may arise.
- Solution: Develop strict operating procedures and standards to ensure each operation follows uniform process parameters. Implement batch management to label and record each batch, tracking sandblasting parameters and effects to ensure consistency.
- Improvement Measures: Use automated surface inspection systems to monitor and adjust sandblasting effects in real-time to ensure consistency for each workpiece.
Issue 17: Complexity of Sandblasting Equipment Operation
- Description: High-precision sandblasting equipment may have complex operating procedures, requiring specialized training for correct use, affecting production efficiency.
- Solution: Provide systematic training for operators to ensure they can master the equipment operation skills proficiently.
- Improvement Measures: Introduce automated control systems to reduce human intervention, simplify the operation process, and improve efficiency.
Issue 18: Control of Sandblasting Environment Temperature
- Description: Excessive high or low temperatures in the sandblasting environment may affect sandblasting effects or media performance.
- Solution: Install temperature control systems in the sandblasting workshop to maintain suitable operating temperatures and regularly monitor environmental temperatures to ensure they remain within a reasonable range.
- Improvement Measures: Adjust sandblasting parameters according to different seasons to ensure stable sandblasting effects. Use temperature-resistant sandblasting media to reduce the impact of environmental temperatures on performance.
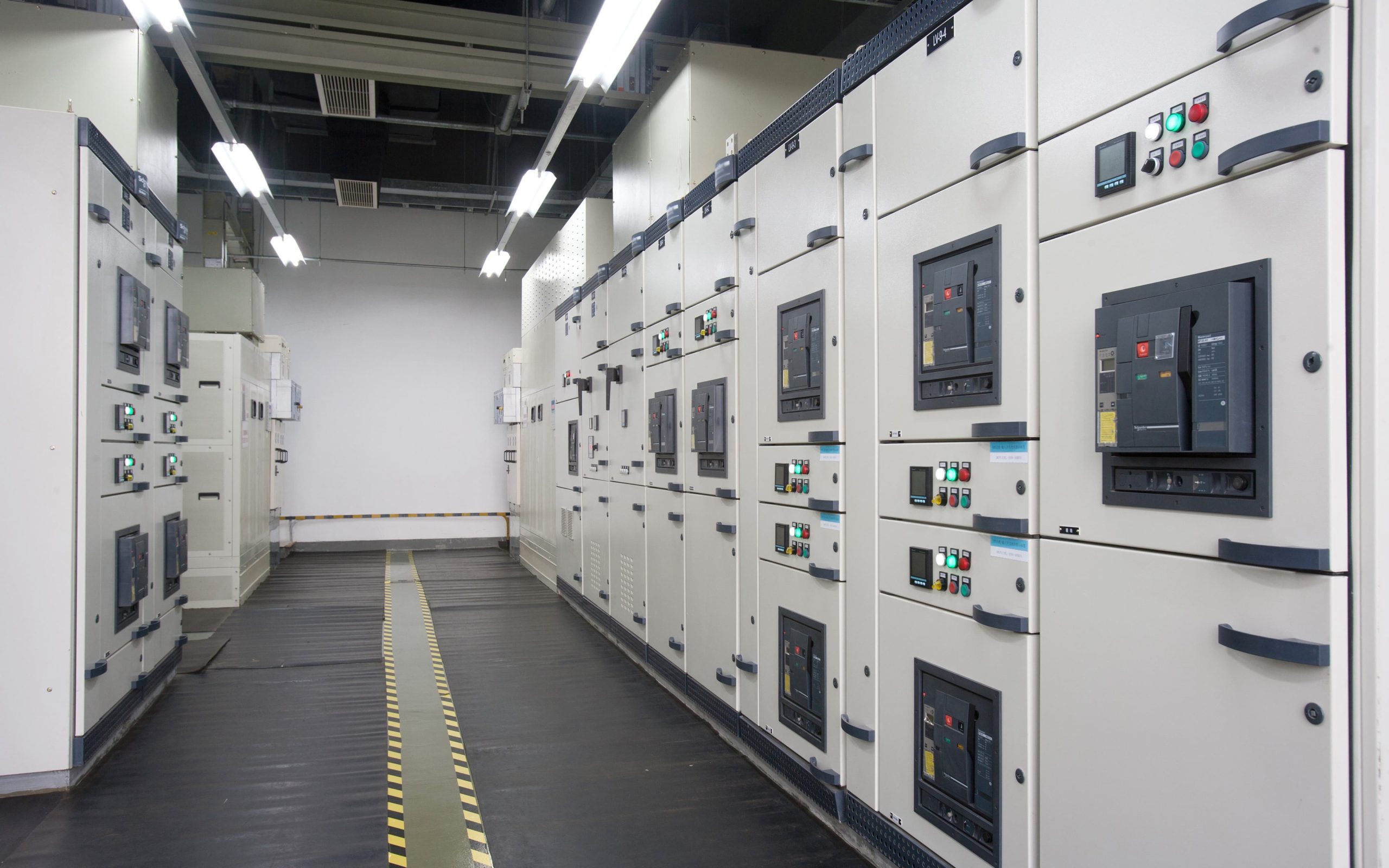
temperature control system
Summary of Tips for Optimizing Alumina Sandblasting Effects:
- Choose appropriate particle size and nozzles: Different nozzle shapes and particle sizes affect sandblasting results; selecting suitable media and equipment can effectively enhance efficiency and surface quality.
- Optimize sandblasting parameters: Adjust sandblasting pressure, flow, distance, and angle precisely based on material characteristics and sandblasting requirements for the best surface effect.
- Use high-quality media: High-purity, high-quality alumina sandblasting media can improve the sandblasting effect, extend media lifespan, and reduce equipment wear. However, timely replacement of unsuitable media (severely worn, contaminated, etc.) is essential!
- Regular equipment maintenance: Equipment performance is crucial for sandblasting effects. Regularly inspect and maintain equipment to ensure it operates at its best.
- Implement automation control: Use intelligent sandblasting systems to monitor and adjust process parameters in real-time, ensuring consistency and efficiency. Pay attention to operational timing and arrange staggered operations.
- Small batch testing: Conduct small batch tests before large-scale production to verify process parameters and equipment suitability, ensuring smooth production.
- Train operators: The skills and experience of operators directly affect sandblasting results. Provide regular training to improve their operation level and adaptability.
- Record and analyze data: Record parameters and results of each sandblasting operation, continuously optimize sandblasting processes through data analysis, and improve product quality.
- Control the working environment: Install efficient dust removal systems to ensure a clean and stable sandblasting environment, reduce dust and impurities interference, and maintain appropriate temperature and humidity to avoid material impact from environmental conditions.
By thoroughly analyzing the above 18 issues, we not only understand the causes of these problems but also find feasible solutions and improvement measures. These strategies can effectively address current operational challenges and provide references for future process optimization. With reasonable equipment maintenance, parameter optimization, and advanced technology application, coupled with proper technical guidance and training for relevant personnel, we can significantly enhance sandblasting effects and ensure product quality consistency and stability. Looking forward, with the continuous exploration and application of new technologies, alumina sandblasting technology will undoubtedly unlock greater potential, bringing more possibilities for surface treatment across various industries.
Appendix:
Safety Measures in Sandblasting Process
There are certain safety risks associated with operating aluminum oxide blasting media, such as dust exposure, noise, and mechanical hazards. Here are some key safety measures:
- Personal Protective Equipment (PPE) Operators should wear protective clothing and gloves to prevent skin contact with sandblasting media or equipment. Additionally, appropriate personal protective equipment, including safety goggles, face shields, dust masks, or respirators, should be worn to prevent inhalation of dust or eye injuries. Earplugs or noise-canceling earmuffs are also necessary to prevent hearing damage from prolonged exposure to high noise levels.
- Dust Ventilation System Installing an efficient dust ventilation system in the sandblasting operation area is crucial. It can effectively reduce dust concentration and improve air quality in the work environment. Modern sandblasting rooms typically feature dust collection systems that collect and filter dust to prevent its spread to other work areas.
- Operator Training Regular safety training for operators is essential to enhance their safety awareness and emergency handling capabilities. Training content should include proper use of protective equipment, safety operating procedures, equipment maintenance, and emergency measures for handling accidents, helping to reduce safety incidents caused by improper operation.
- Emergency Preparedness A well-developed emergency plan should be in place in the sandblasting operation area, including measures for handling fires, explosions, or other emergencies. Ensure that adequate fire extinguishing equipment and first aid supplies are available on-site and conduct regular emergency drills to improve operators’ response capabilities.
Filters