Type III Melamine: Efficient Stripping & Precision Cleaning
November 26, 2024
Are you still struggling to remove stubborn coatings from metal or composite surfaces?
Are you worried about damaging the underlying material or wasting time cleaning molds or precision electronic components?
Plastic sandblasting media provides an efficient, environmentally friendly, and safe solution for these common pain points. As a lightweight, angular material, plastic media can meet various needs from mold cleaning to complex surface treatment.
Of course, it is important to understand the problems customers face before providing them with solutions.
Source of pain points
Technical perspective: Why are traditional methods not effective?
Traditional surface cleaning methods, such as chemical rust removal and laser rust removal, generally have problems such as unstable cleaning effects, slow processing speeds, material damage, and high costs.
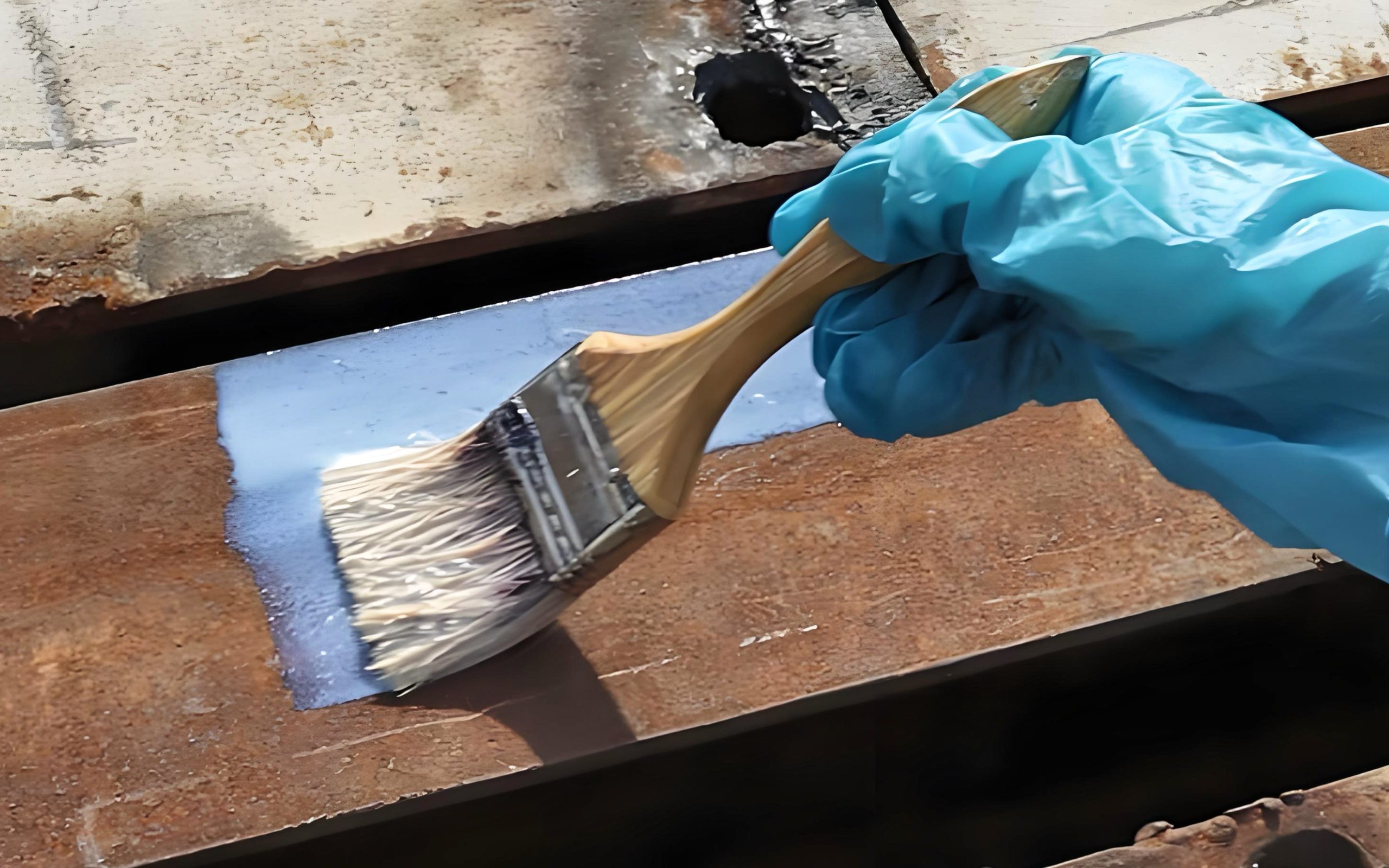
- Chemical rust removal: Relying on strong chemicals, which not only causes environmental pollution but may also damage sensitive parts. The use of chemicals also requires strict operating procedures and environmental control, which increases the difficulty of operation and safety hazards.
- Laser rust removal: The cost is high, and the surface cleaning effect is poor for large areas or complex geometries, and it may also cause thermal damage to some precision surfaces.
Economic perspective: How does it increase production costs?
- High material consumption and waste disposal: Chemical cleaning requires chemicals that generate a large amount of hazardous waste after use, which is expensive to deal with and affects environmental compliance.
- Time and labor costs: Laser equipment is expensive and complex to operate, and the cleaning speed is slow and requires more manual monitoring. In addition, the maintenance and operation costs of large equipment are also high.
- Frequent equipment failures: Frequent repairs and updates of cleaning equipment are also a cost that cannot be ignored.
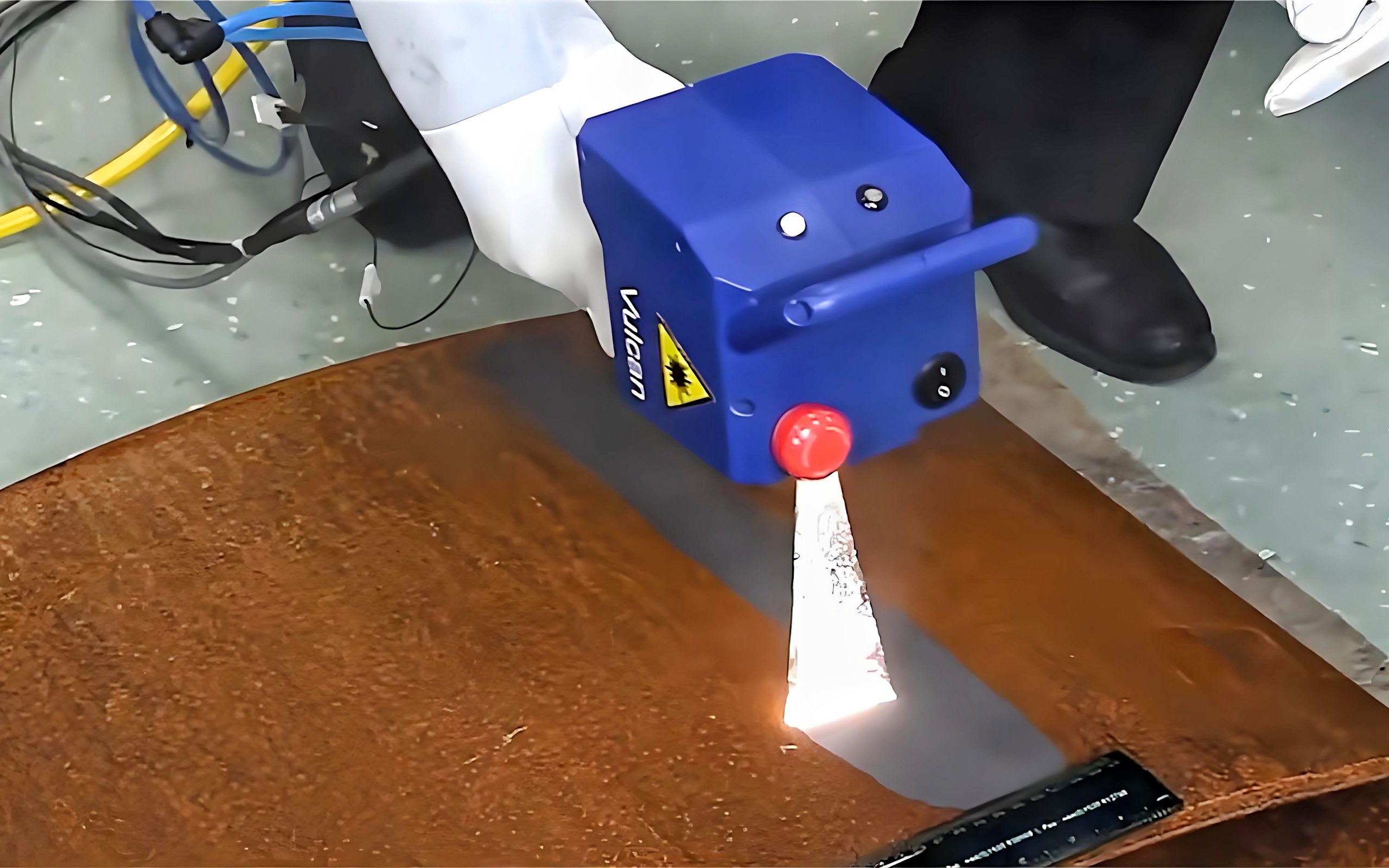
Industry trends: What are the imperfect existing methods on the market?
In the current surface treatment market, sandblasting is a common cleaning technology, but traditional abrasives such as ceramic particles and aluminum oxide sand have high hardness. Although they are suitable for cleaning rough surfaces or removing rust, they can cause physical damage to precision parts. When facing complex geometries or fine surfaces, they are prone to scratches and wear, or it is difficult to ensure thorough cleaning.
In this context, Type III melamine blasting media has gradually become the first choice for precision cleaning and surface stripping due to its low damage, high efficiency, environmental protection, and reusability. Whether it’s steel or aluminum molds, engine parts, or semiconductor components, it can quickly complete the toughest cleaning tasks while leaving the surface intact.
Next, I’ll take you to the Type III melamine, a highly efficient sandblasting media you can trust.
Key Performance
In surface preparation, efficiency and precision are often a contradiction. How can stubborn contaminants be quickly removed while avoiding damage to the underlying material? The unique properties of Type III melamine are the ideal answer to this dilemma.
1. Excellent hardness, easy to deal with stubborn coatings
With a Barcol hardness of 64-72, Type III melamine plastic media has a moderate hardness that makes it sharp enough to effectively strip stubborn primers, paints, hydrocarbon deposits, and hard coatings without scratching or deforming the surface. Compared with rougher abrasives (such as glass beads or metal media), it can achieve the perfect balance of cleaning power and protection.
Key Performance Benefits:
- Quickly remove contaminants from steel, aluminum, and other durable materials.
- Precise stripping without damaging the surface morphology of the substrate.
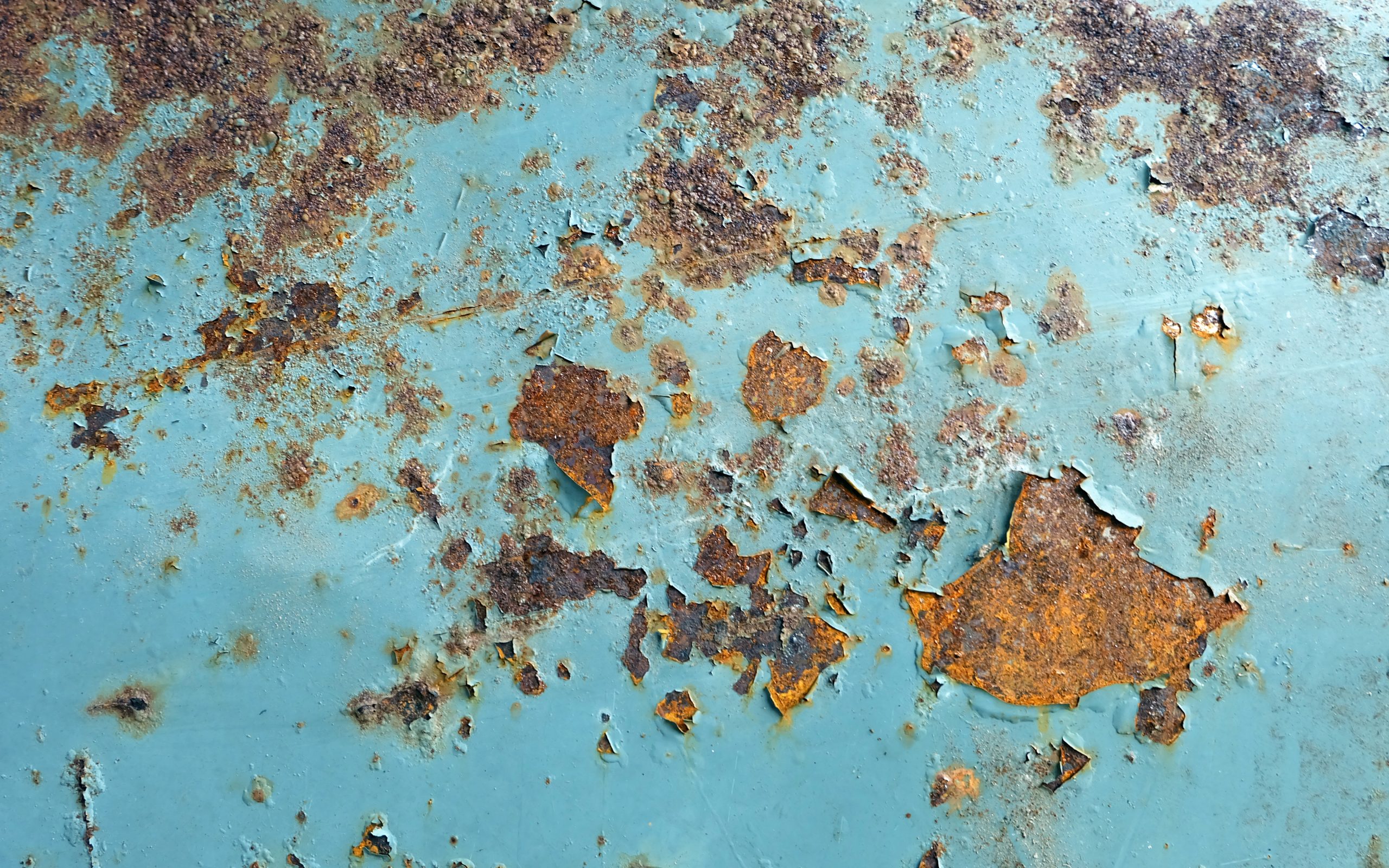
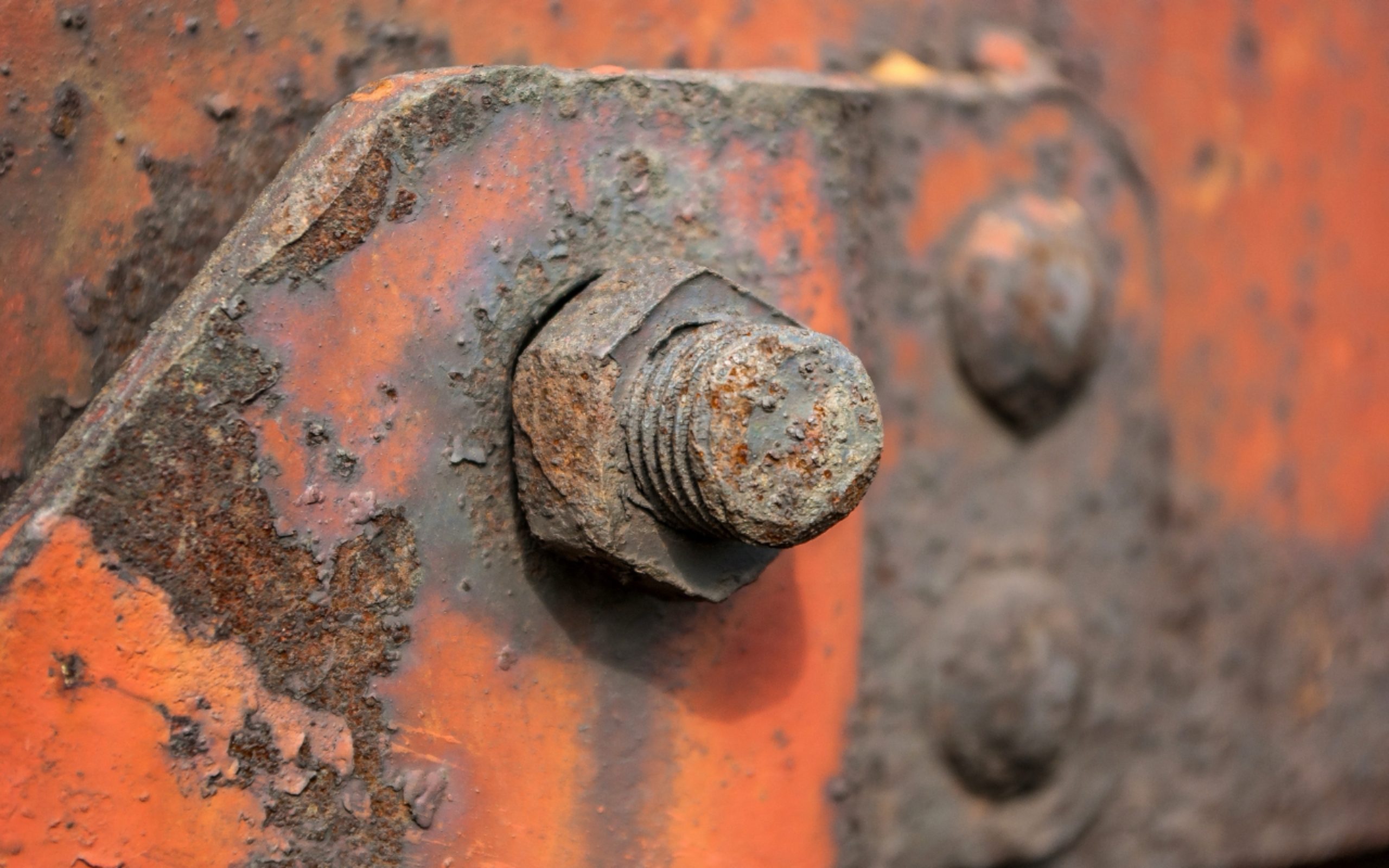
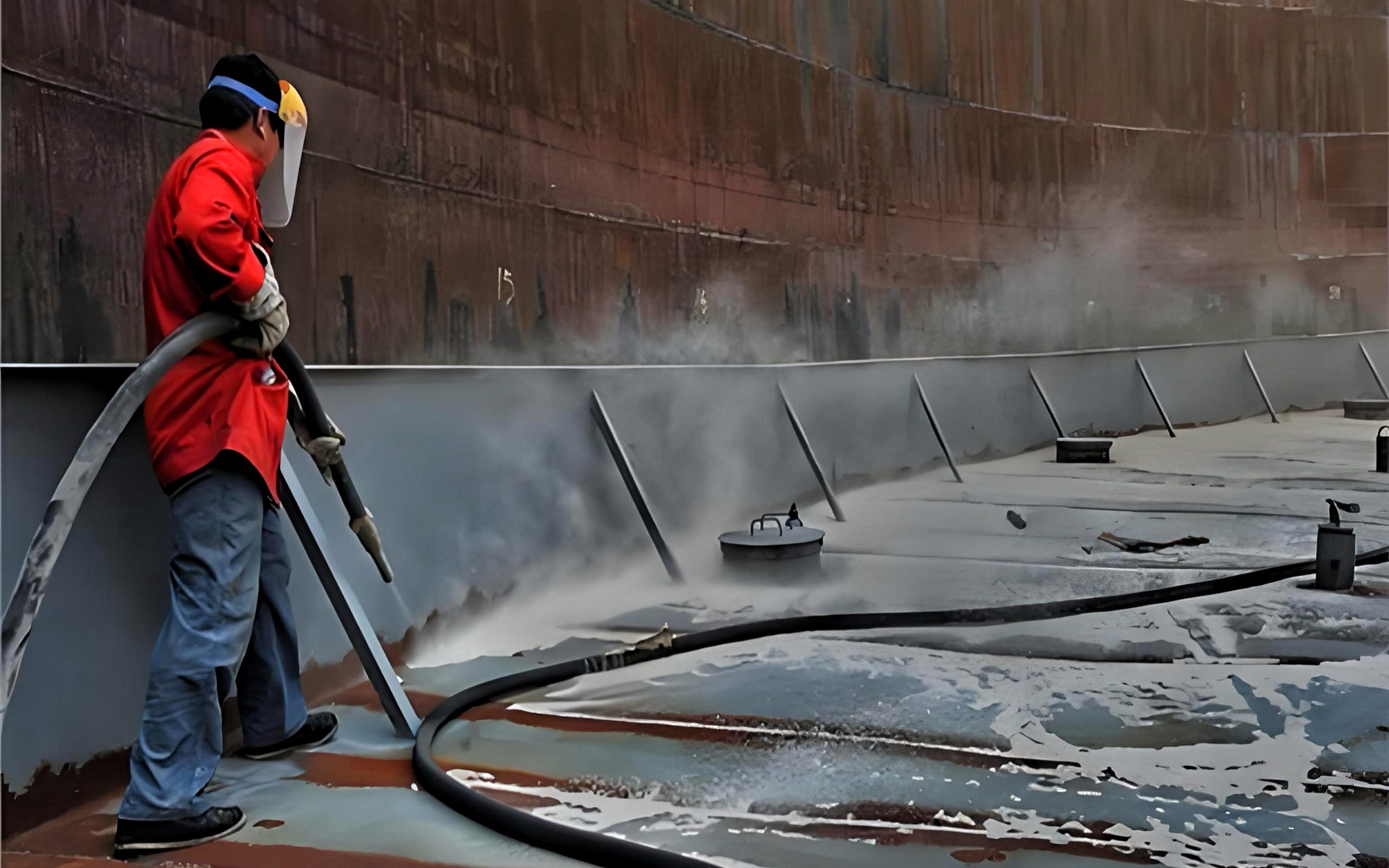
2. Environmental protection and safety: provide dual protection for operators and the environment
In modern industry, environmental protection and safety have become key indicators. Traditional chemical cleaning methods are often toxic or polluting, and some abrasives (such as glass beads or metal dust) produce tiny particles that pose a threat to operators’ health.
Type III melamine stands out for its chemical inertness. The sandblasting process does not produce dust, toxins, or residues, greatly reducing the safety hazards during operation and not polluting the environment.
Core features:
- Non-toxic and harmless, no harmful chemicals are released during use.
- Clean and environmentally friendly, avoiding secondary pollution in traditional sandblasting processes.
3. High efficiency and economy: Achieve a win-win situation in time and cost

At the same time, the consistent particle structure of Type III melamine blasting media ensures the stability of cleaning results, without the need for repeated treatments, which not only saves time but also significantly reduces energy and labor costs.
Specific advantages:
- Long-lasting and durable, reducing long-term procurement costs.
- Economical and efficient, finding the best balance between cleaning speed, effect, and media cost.
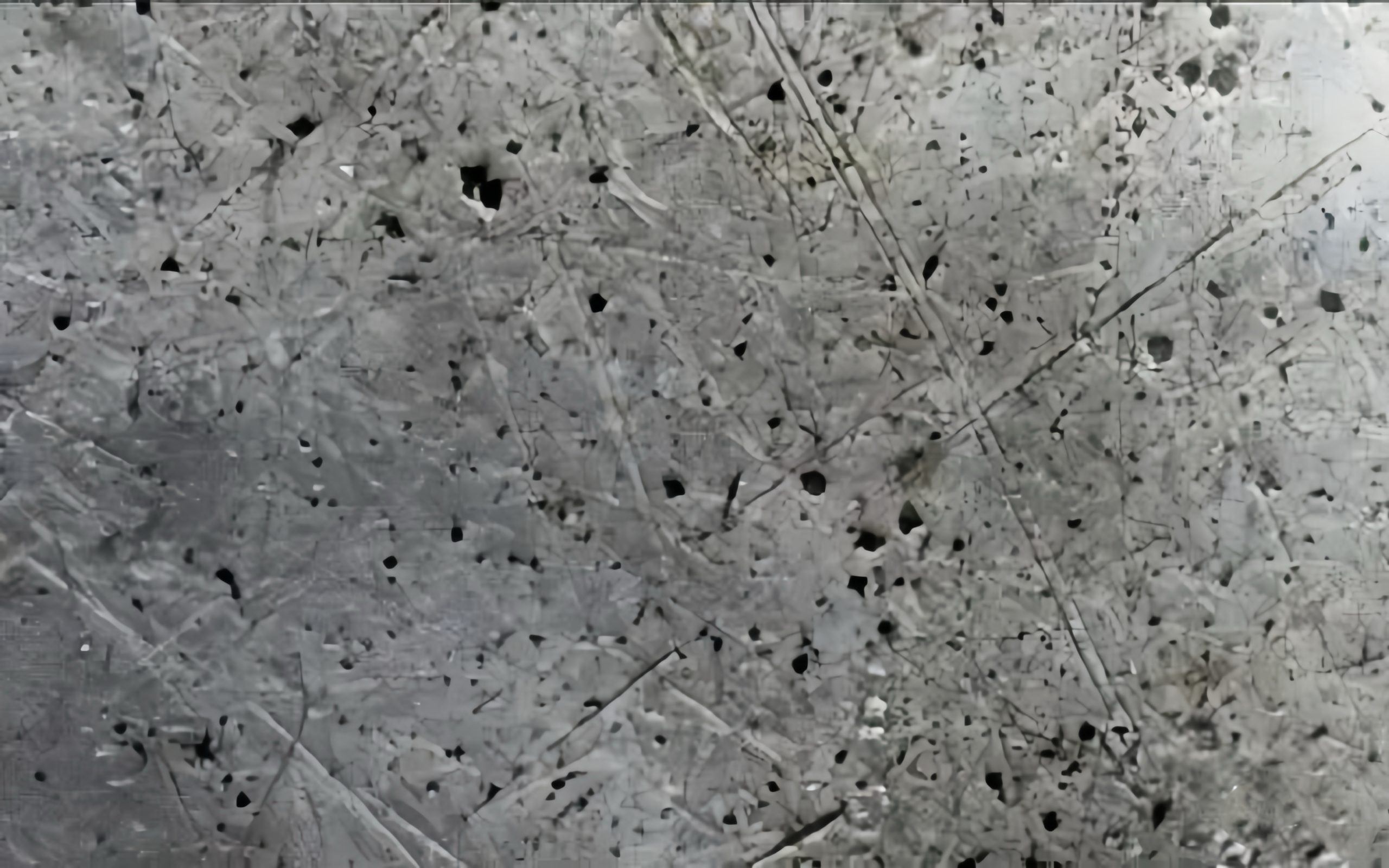
4. Protect the substrate and ensure that the surface is intact
Some precision parts, such as semiconductor components, aluminum molds, or automotive brake pads, have extremely high requirements for surface finish, and the slightest carelessness may cause irreversible damage. Traditional abrasives (such as metal sand or glass beads) often cause scratches or surface deformation due to excessive friction when processing these parts.
Type III melamine blasting media was originally designed to solve this pain point:
- Almost no heat is generated during sandblasting, avoiding bending, damage, or denting of the surface due to high temperature.
- Lightweight properties and moderate hardness are the best choices for protecting sensitive materials.
Application scenarios
The unique properties of melamine plastic media enable it to excel in the cleaning and surface treatment fields of multiple industries. The following are the main application scenarios to show how it can meet the specific needs of different fields.
Rubber and plastic industry
- Steel molds: used in the manufacture of rubber and plastic parts, removing stubborn carbides without damaging the fine structure of the mold.
- Chrome-plated molds: protect the integrity of the coating when removing coating deposits and extend the service life of the mold.
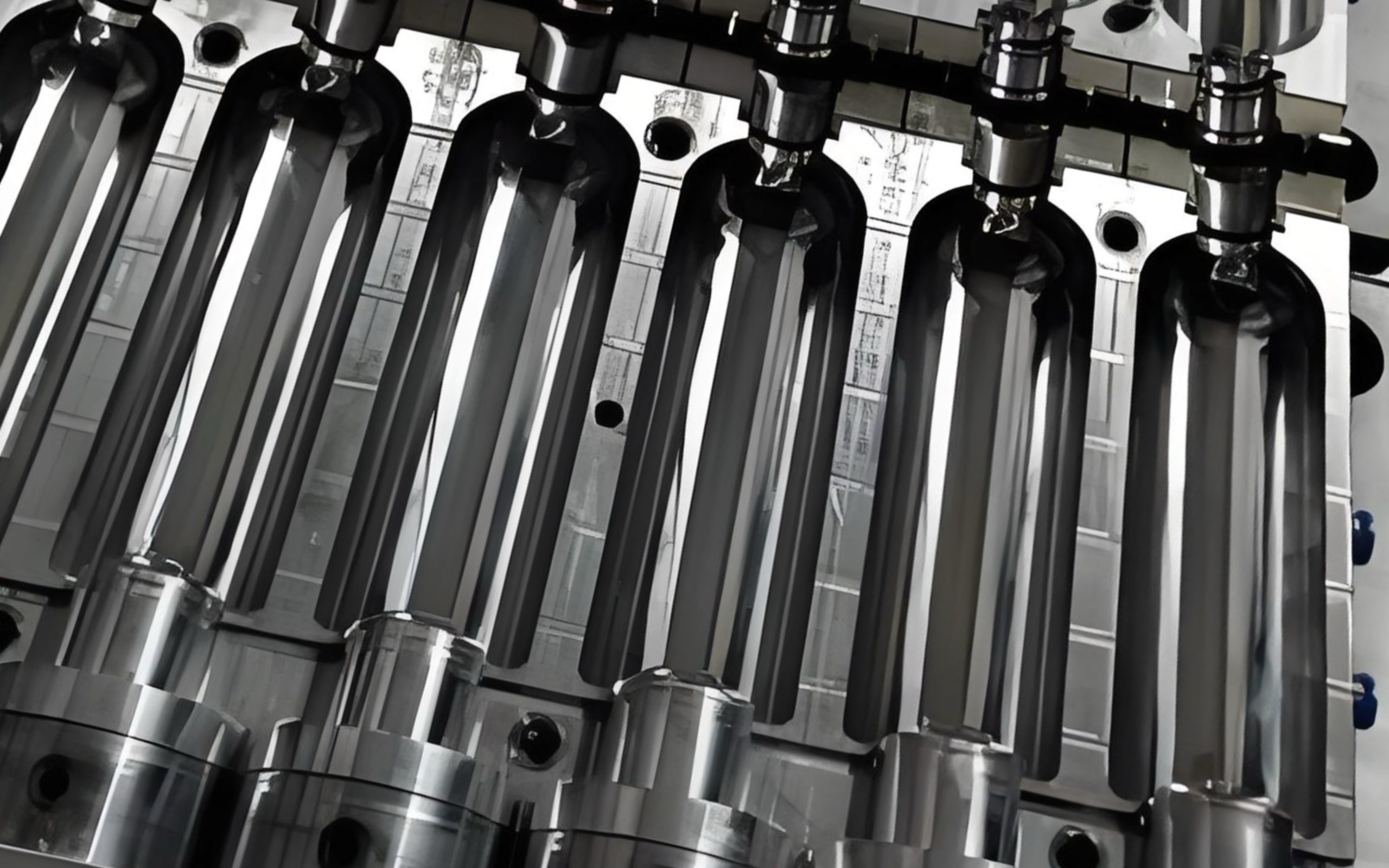
Foam plastic industry
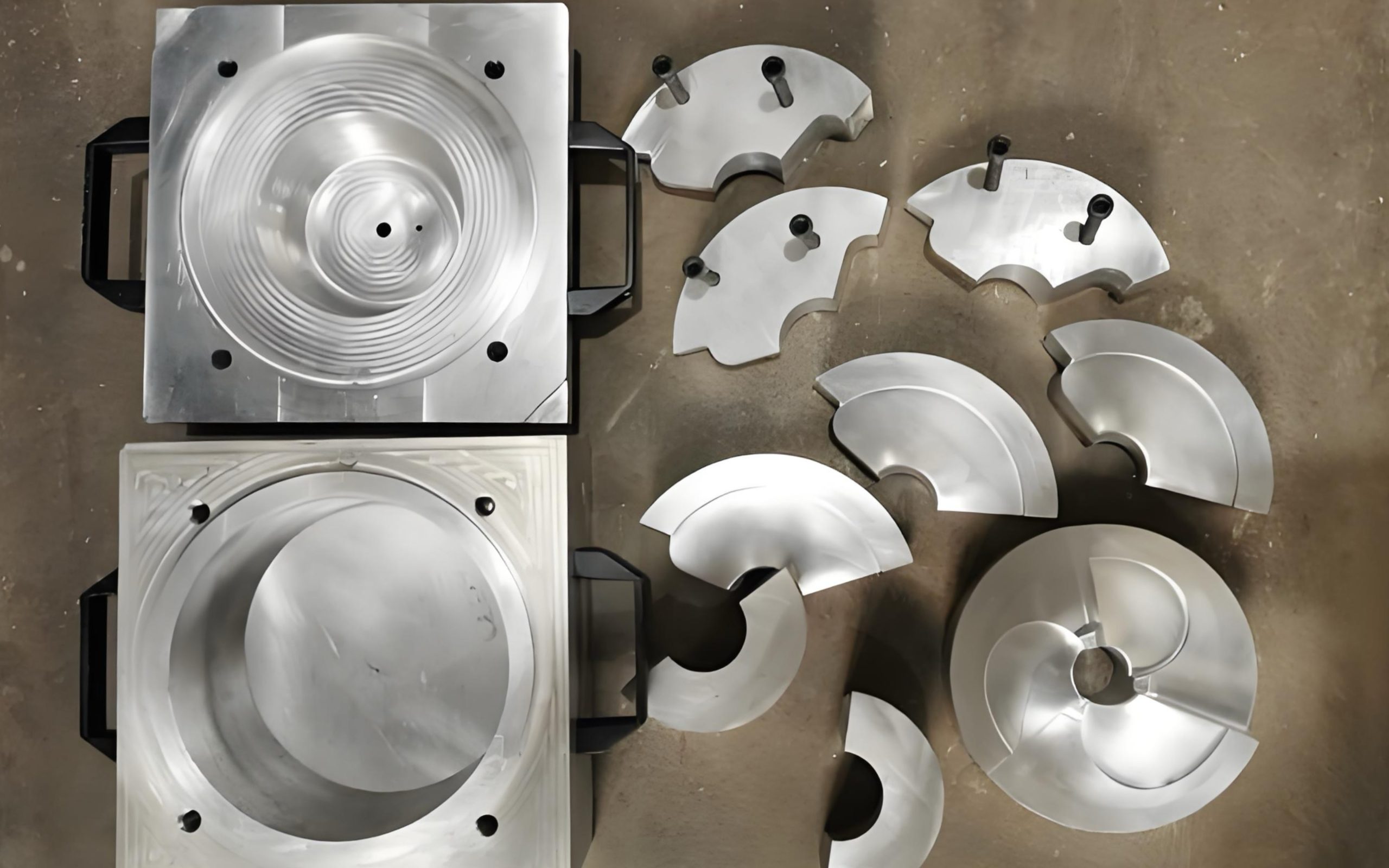
- Aluminum molds: suitable for lightweight aluminum molds in the production of foam products to avoid scratches or dents.
- Steel molds: stable performance when cleaning harder mold surfaces without risk of damage.
Electronics and semiconductor industry
- Electronic components: fine cleaning of surfaces such as circuit boards and contact pieces.
- Semiconductor components: used to remove stubborn deposits in miniature semiconductor devices.
Automotive industry
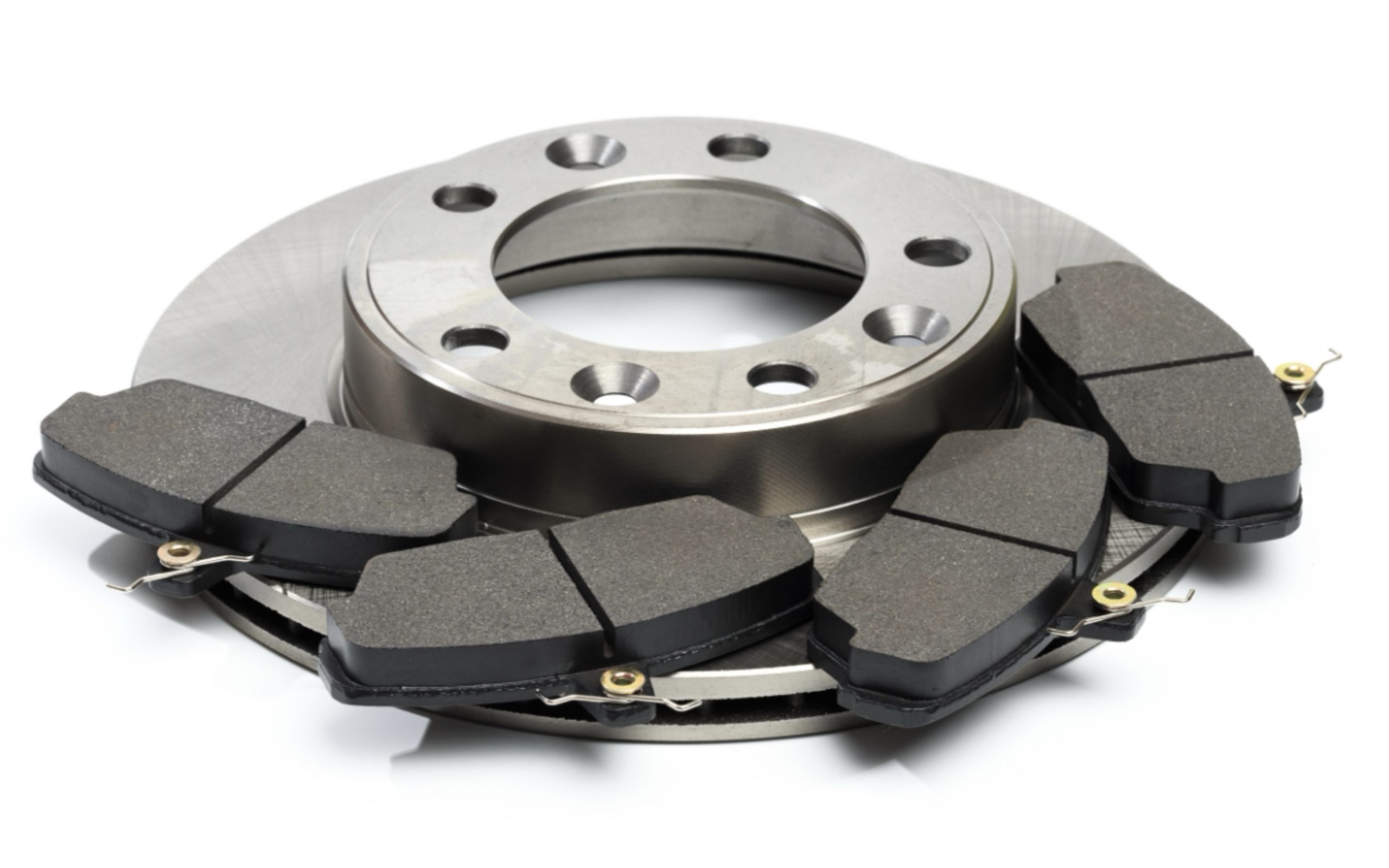
- Engine components: deep cleaning of surfaces such as cylinder blocks or crankshafts.
- Brake pads and composite materials: maintain the structural integrity of the material while removing surface deposits.
Special material cleaning

- Glass fiber: remove surface attachments without damaging the fiber structure.
- Copper/Brass: Protect the gloss and integrity of metal surfaces while cleaning oxide layers and deposits.
- Plastic/Rubber: Used to remove stubborn coatings or contaminants while protecting the material itself.
Practical Cases
To more intuitively demonstrate the superior performance of melamine plastic media in actual operations, this chapter will combine specific cases to elaborate on its application results in different fields. These data sources are based on real industry feedback and public reports to provide you with a reliable basis for decision-making.
Case 1: Cleaning car brake pads to improve performance and durability
Background issues
- Contaminant accumulation: The surface of brake pads is prone to coating residues, oil stains, and microparticles, which affect friction performance.
- Limitations of traditional methods: When traditional hard abrasives are used to clean brake pads, slight surface scratches are often caused, which shortens the service life of the product.
Solution
Introducing Type III melamine for surface treatment of brake pads, this material has moderate hardness and high impact efficiency, while protecting the integrity of the brake pads while removing stubborn residues. The final results are:
- Improved cleaning efficiency: Cleaning time was reduced by 30%, from an average of 10 minutes per piece to 7 minutes per piece.
- Extended product life: The durability of the brake pads was increased by 15%, greatly reducing the replacement frequency. [1]
- Customer satisfaction: Customer feedback shows that the performance of the brake pads after cleaning has improved, and the user complaint rate has dropped by 20%.
Case 2: Foam plastic mold cleaning to ensure high precision and quality
Background issues
- Aluminum molds are easily damaged: Traditional abrasives often leave scratches on the mold surface when cleaning stubborn residues, resulting in a decrease in the surface quality of the foam product.
- High mold replacement frequency: Aluminum molds are severely worn and need to be replaced every 3 months, increasing production costs.
Solution
The company used Type III melamine blasting media to clean aluminum molds and achieved non-destructive cleaning through its lightweight particles and moderate hardness, and finally obtained:
- Improved efficiency: The cleaning speed increased by 40%, from cleaning 5 sets of molds per hour to 7 sets of molds.
- Extended mold life: The service life of aluminum molds was extended from 3 months to 6 months, and maintenance costs were reduced by 50%.
- Improved product quality: The qualified rate of foam plastic products increased by 18%, and customer satisfaction was significantly improved.
Case 3: Cleaning semiconductor components to meet strict industry standards
Background issues
- Micro-particle contamination problem: Residual contaminants on the surface can easily affect component performance and reduce product yield.
- Traditional methods damage microstructures: Hard abrasives may cause surface microcracks when cleaning precision semiconductor equipment, which cannot meet industry standards.
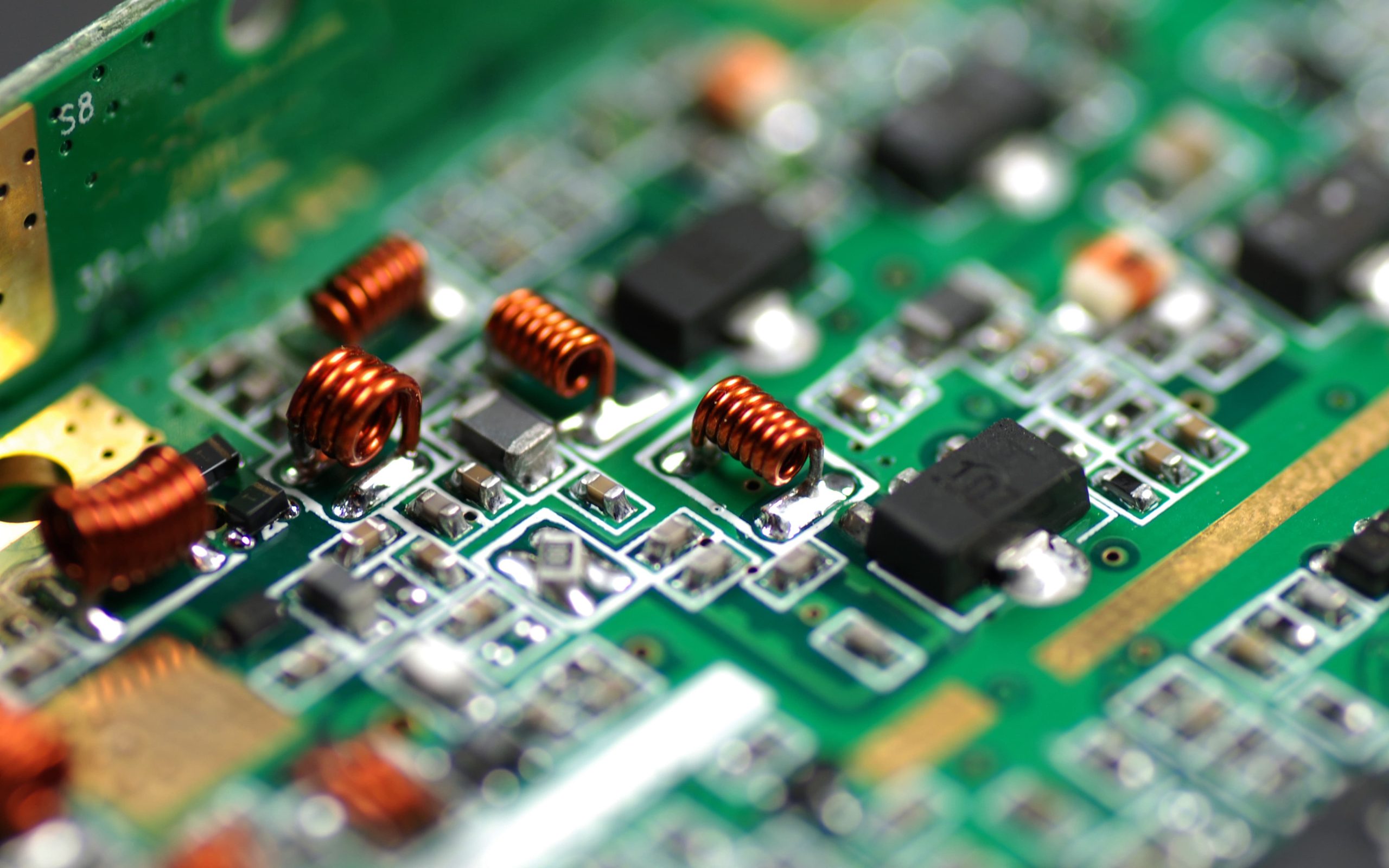
Solution
The factory introduced melamine blast media throughout the factory, using its high-impact force and lightweight properties to remove pollutants, and achieved satisfactory results:
- Pollutant removal rate: The removal rate reached 99.8%, higher than the industry average of 95%.
- Reduced defect rate: The product defect rate dropped from 5% to 2%, significantly improving production yield. [2]
- Precision surface protection: In multiple rigorous tests, no surface microcracks or structural damage were found, meeting the semiconductor industry standard (IPC-610E).
Case 4: Cleaning aviation composite materials to ensure flight safety
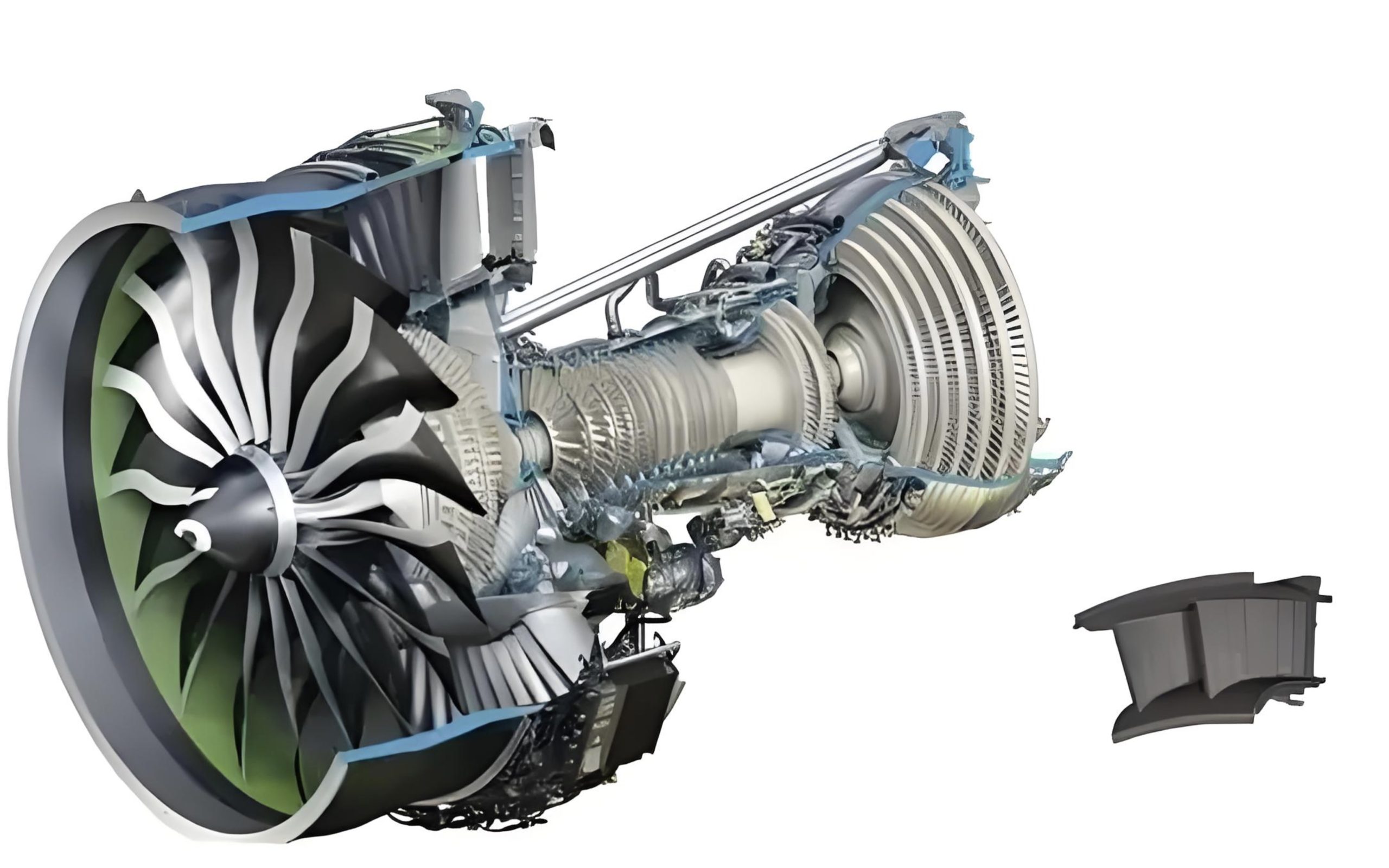
Background issues
- High requirements for surface integrity: Composite materials have strict requirements for strength and lightweight. Any surface damage will reduce component performance and even threaten flight safety.
- Disadvantages of traditional cleaning methods: Chemical cleaning methods are inefficient and may leave corrosive substances.
Solution
The company uses Type III melamine to clean composite parts, which meets the needs of the aviation industry with its environmentally friendly, safe, and non-destructive characteristics.
Actual results:
- Cleaning efficiency: Work efficiency has increased by 25%, and the cleaning time for each batch of parts has been reduced to less than 3 hours. [3]
- Surface integrity: Tests show that there are no microcracks or damage on the surface of the parts, and the mechanical properties remain intact.
- Environmental protection: No chemical residue, meeting the environmental protection standards of high-demand industries.
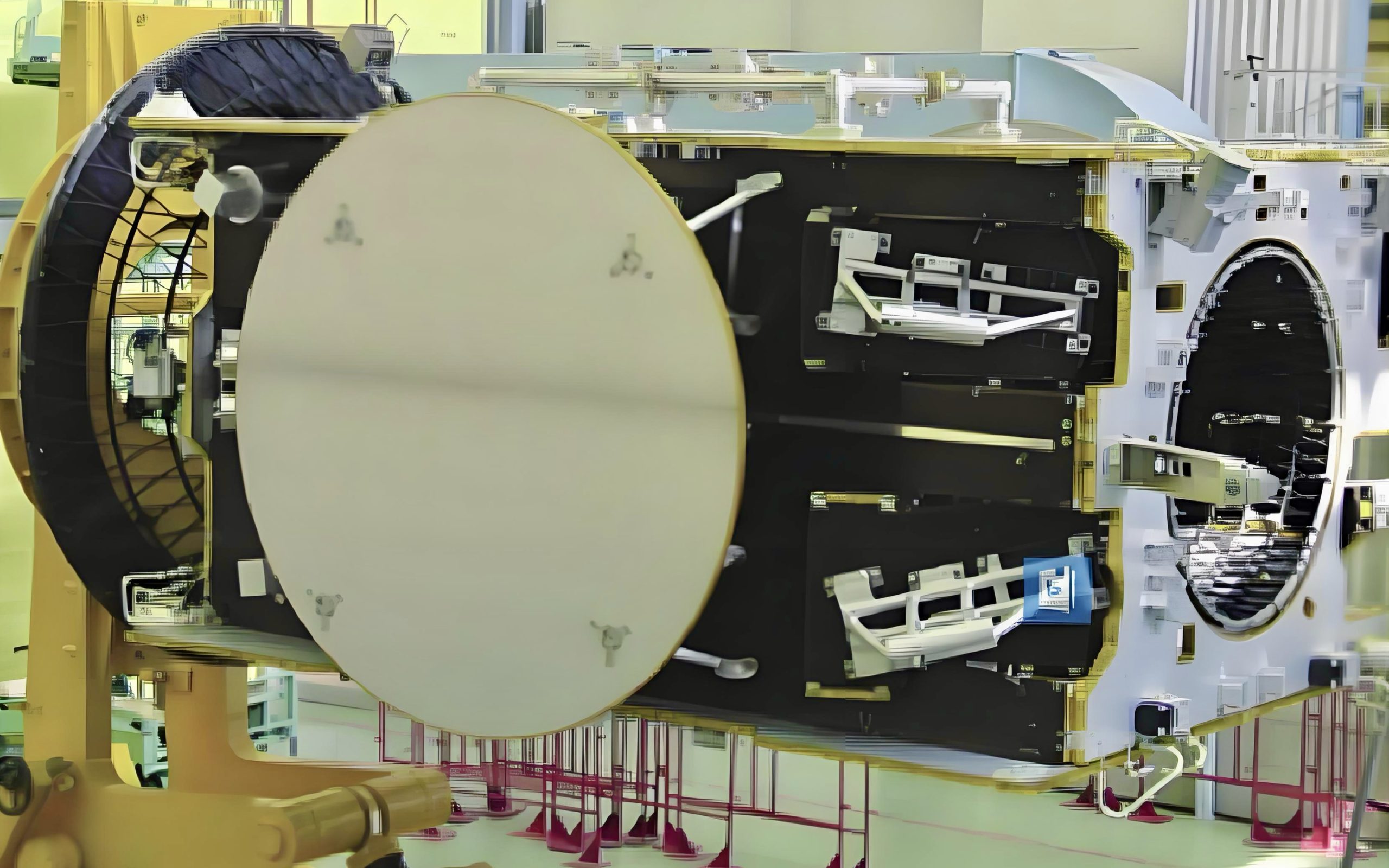
The above practical cases show the successful application of Type III melamine blast media in multiple industries. Whether it is automobiles, electronics, foam plastics, or aviation manufacturing, melamine abrasives have solved customer pain points with their high efficiency, precision, and environmental protection, while creating significant economic benefits.
Q&A: Frequently Asked Questions
Q1: Will plastic media damage precision parts?
A: No.
Type III melamine sandblasting media is designed for precision cleaning, with moderate and adjustable hardness. Its lightweight properties make it gentle and efficient during the cleaning process, suitable for processing high-precision parts or complex structure surfaces. Whether it is semiconductor components or steel molds, ideal cleaning effects can be achieved without damage.
Q2: How to evaluate the cost-effectiveness of plastic media?
A: The cost-effectiveness of Type III melamine comes from its durability and efficiency:
- Excellent durability: The media can be reused many times, greatly reducing the material consumption of a single cleaning.
- High processing speed: Due to the lightweight and strong impact of the particles, the cleaning efficiency is significantly improved, which can save time costs.
- Comprehensive cost advantage: Although the initial price may be slightly higher than traditional abrasives, its durability and efficiency significantly reduce the overall cost.
Q3: Does the product meet environmental standards?
A: Absolutely.
Type III melamine sandblasting media is an environmentally friendly material with the following characteristics:
- Dust and toxin-free: No harmful particles are generated during the sandblasting process, which is safer for operators and the environment.
- No chemical residue: No contaminants are left on the surface of parts or equipment, especially suitable for sensitive industries such as medical, aviation, and electronics.
- Recyclability: It can be reused many times to reduce waste generation.
- Industry certification: Type III melamine meets many international environmental standards, including ISO 9001:2015 and ISO 14001.
In general, Type III melamine blasting media has become the preferred choice for solving surface treatment problems in many industries due to its efficient cleaning, environmental safety, and non-destructive performance. Its wide range of application scenarios proves its applicability and economy. From automotive parts to precision semiconductor components, Type III can meet customer needs.
Contact us now to get customized solutions to make your production more efficient, safer, and more economical!
[1] China Automotive Parts Surface Treatment Industry Analysis (2022)
[2] Research on Cleaning Processes in the Electronics and Semiconductor Industry (2023)
[3] White Paper on Clean Technology for the Aviation Industry (2022)
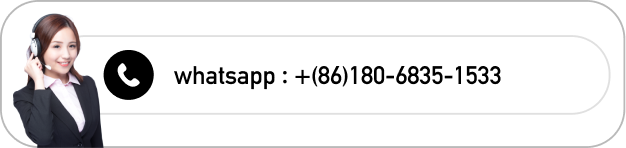