Aluminum vs. Steel: Surface Preparation Strategies for Electric Vehicle Components
February 14, 2025
As electric vehicles (EVs) continue to evolve, aluminum and steel play crucial roles in manufacturing lightweight and durable components. Choosing the right surface preparation strategy is essential for optimizing performance, longevity, and adhesion in coatings.

Why Aluminum and Steel Matter in EV Manufacturing?
Both materials are used in different EV components due to their distinct properties:
Component | Common Material | Reason |
---|---|---|
Battery Enclosures | Aluminum | Lightweight, heat dissipation |
Chassis & Frame | Steel | High strength, crash resistance |
Suspension Components | Aluminum/Steel | Weight-to-strength balance |
Motor Housing | Aluminum | Corrosion resistance, thermal conductivity |
Structural Reinforcements | Steel | Impact resistance |
Understanding these material applications helps select the right surface treatment methods to enhance their durability and performance.
Surface Preparation Challenges for EV Components
Aluminum (Lightweight but Reactive)
Forms an oxide layer that hinders coating adhesion
Softer than steel, requiring gentler blasting techniques
Prone to galvanic corrosion when in contact with dissimilar metals
Steel (Strong but Corrosion-Prone)
Susceptible to rust without proper protection
Requires aggressive blasting to remove mill scale and contaminants
Needs additional coatings for enhanced longevity
Optimized Surface Preparation Strategies
For Aluminum Components:
1) Blasting Media:
- Fine Aluminum Oxide – Removes oxide layers without excessive erosion
- Ceramic Beads – Provides a uniform surface finish
2)Pre-Treatment:
- Chemical Etching – Enhances adhesion before painting
- Plasma Treatment – Cleans and activates the surface without damage
3)Coating Solutions:
- Anodizing – Creates a corrosion-resistant protective layer
- Powder Coating – Adds durability and visual appeal
For Steel Components:
1)Blasting Media:
- Garnet or Steel Grit – Effectively removes rust and mill scale
- Shot Peening – Increases fatigue resistance in structural parts
2) Pre-Treatment:
- Phosphating – Enhances corrosion protection before coating
- Solvent Cleaning – Removes oil and contaminants
3) Coating Solutions:
- Galvanization – Zinc coating prevents rust formation
- Epoxy Primer – Protects against harsh environments

Industry Innovations & Future Trends
Advantages of zirconia beads
Nanocoatings for Enhanced Protection:
Emerging ceramic-based nanocoatings provide superior corrosion resistance for both aluminum and steel without adding weight.
Laser Cleaning as an Alternative to Blasting:
New laser ablation technology offers a non-abrasive method to remove contaminants, improving coating adhesion with minimal environmental impact.
Hybrid Material Surface Engineering:
Combining advanced polymer coatings with traditional anodizing and galvanization techniques extends the lifespan of EV components.
Choosing the Right Method for EV Manufacturing
Aluminum: Needs gentle blasting, chemical treatments, and anodizing to enhance durability.
Steel: Requires aggressive blasting, phosphating, and protective coatings to prevent rust.
Selecting the optimal surface preparation strategy ensures EV components remain lightweight, durable, and corrosion-resistant, improving long-term performance.
Would you like specific case studies or a deeper comparison of surface roughness effects on coating adhesion?
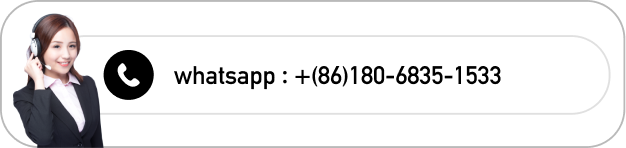