Avantages et applications du traitement de surface par sablage
15 octobre 2024
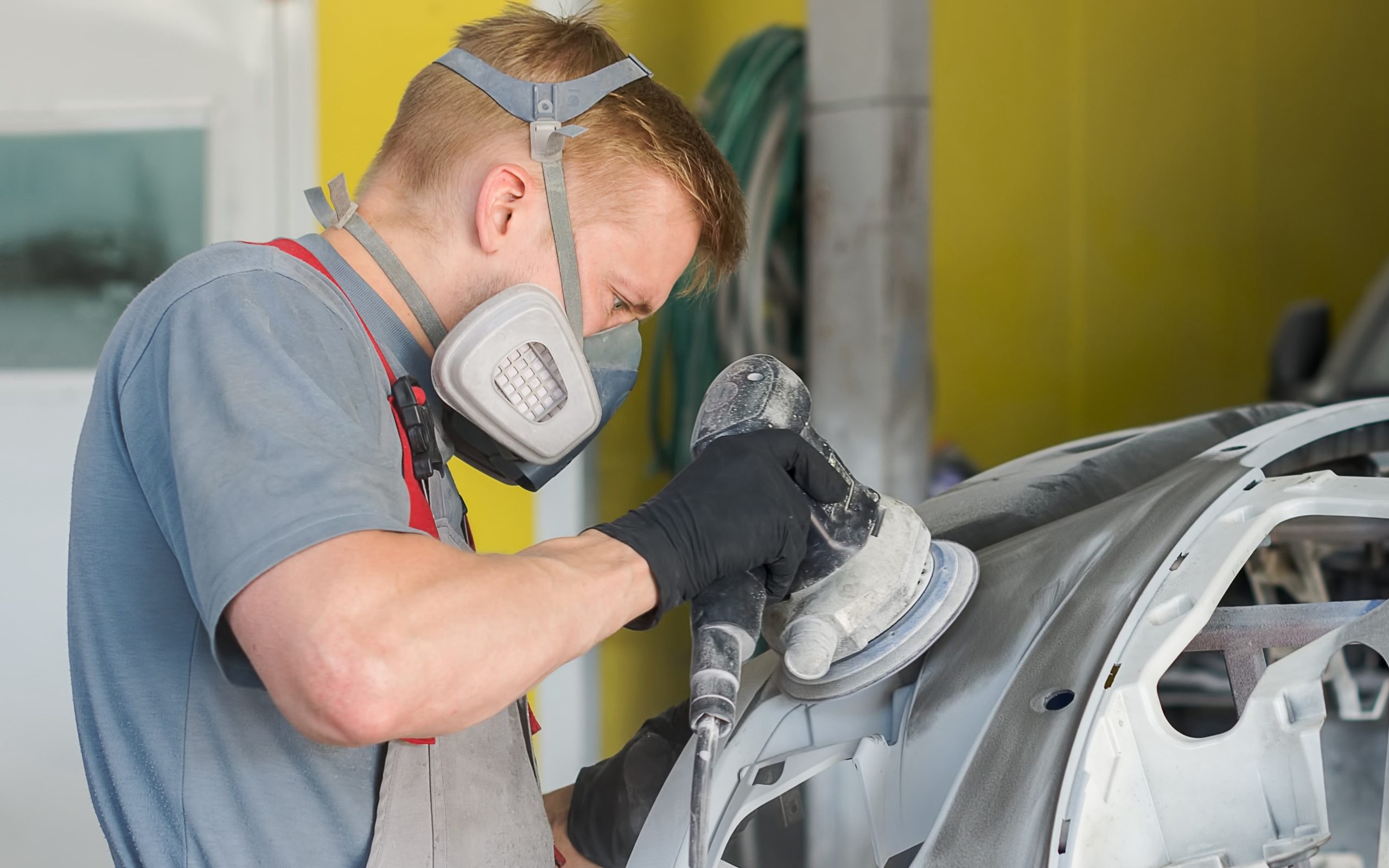
Dans l'industrie moderne, le prétraitement des surfaces est considéré comme un maillon essentiel du processus de fabrication des produits. Il affecte non seulement l'apparence et les performances du produit, mais aussi directement sa durée de vie et sa fiabilité. En éliminant les impuretés, les oxydes et les taches d'huile à la surface, le prétraitement de surface établit une base solide pour le revêtement ou le traitement de surface ultérieur. Le prétraitement de surface a un large éventail d'applications dans différents domaines industriels, notamment l'aérospatiale, l'automobile, l'équipement électronique et les appareils médicaux. Dans ces domaines, le traitement de surface n'est pas seulement une question d'esthétique, mais aussi de sécurité et de fonctionnalité. Pour répondre à des besoins différents, la technologie du sablage a également évolué de manière flexible en ce qui concerne la sélection des matériaux et les méthodes de traitement. Par conséquent, la compréhension des concepts de base du prétraitement des surfaces par sablage et de ses applications spécifiques peut aider les entreprises à choisir le plan de traitement le plus approprié, améliorant ainsi la qualité et la compétitivité des produits.
Qu'est-ce que le prétraitement des surfaces ?
Le prétraitement de la surface désigne le processus de traitement du matériau par des moyens physiques ou chimiques avant l'application d'un revêtement sur la surface du matériau. L'objectif de ce processus est d'améliorer l'adhérence du revêtement et de s'assurer qu'il ne se décolle pas facilement ou que ses performances ne se dégradent pas au cours d'une utilisation à long terme. Les étapes du prétraitement de la surface comprennent le nettoyage, la rugosité et l'activation de la surface afin que le revêtement puisse adhérer fermement au matériau.
Parmi elles, le sablage est une méthode de prétraitement de surface courante et largement utilisée. En utilisant des particules abrasives à grande vitesse pour frapper la surface du matériau, il permet d'éliminer la couche d'oxyde, la rouille et les revêtements anciens, et de créer un profil de surface idéal. Comparé aux méthodes de traitement chimique telles que le décapage, le sablage présente de grands avantages en termes d'efficacité, de sécurité et de protection de l'environnement.
Outre le sablage, d'autres méthodes courantes de prétraitement des surfaces sont utilisées :
- Marinade : L'acide est utilisé pour éliminer les oxydes et les contaminants à la surface du matériau, mais le processus de traitement produit des déchets liquides et des gaz nocifs, qui doivent être strictement contrôlés.
- Polissage : Principalement utilisé pour éliminer les petites bavures ou les défauts de la surface, souvent utilisé pour le traitement des matériaux qui nécessitent une surface très lisse.
- Broyage mécanique : Utiliser un équipement mécanique pour poncer et aplanir la surface, adapté au traitement de surface de grandes surfaces, en particulier sur les structures en acier.
Comparé à ces méthodes, le sablage permet de créer plus efficacement une rugosité microscopique à la surface du matériau, d'améliorer l'adhérence du revêtement au substrat et constitue l'un des choix les plus courants dans les applications industrielles.
Le principe scientifique du prétraitement des surfaces
Le principe scientifique du prétraitement des surfaces consiste principalement à éliminer les impuretés, la rouille ou le revêtement sur la surface, tout en créant une morphologie de surface appropriée pour les processus de revêtement ou de collage ultérieurs. Le sablage permet d'obtenir un effet de nettoyage et de décapage en frottant et en impactant la surface de la pièce avec le produit de sablage éjecté à grande vitesse. Ce processus fait intervenir les facteurs clés suivants :
- Formation de la rugosité de la surface
La rugosité de la surface est due à la force d'impact du produit de sablage. Le produit de sablage percute la surface de la pièce à grande vitesse, éliminant non seulement les taches de rouille, les revêtements, etc. mais formant également des bosses microscopiques uniformes sur la surface. Cette structure de bosses contribue à augmenter la zone d'adhérence de la surface, améliorant ainsi l'adhérence des revêtements ultérieurs.
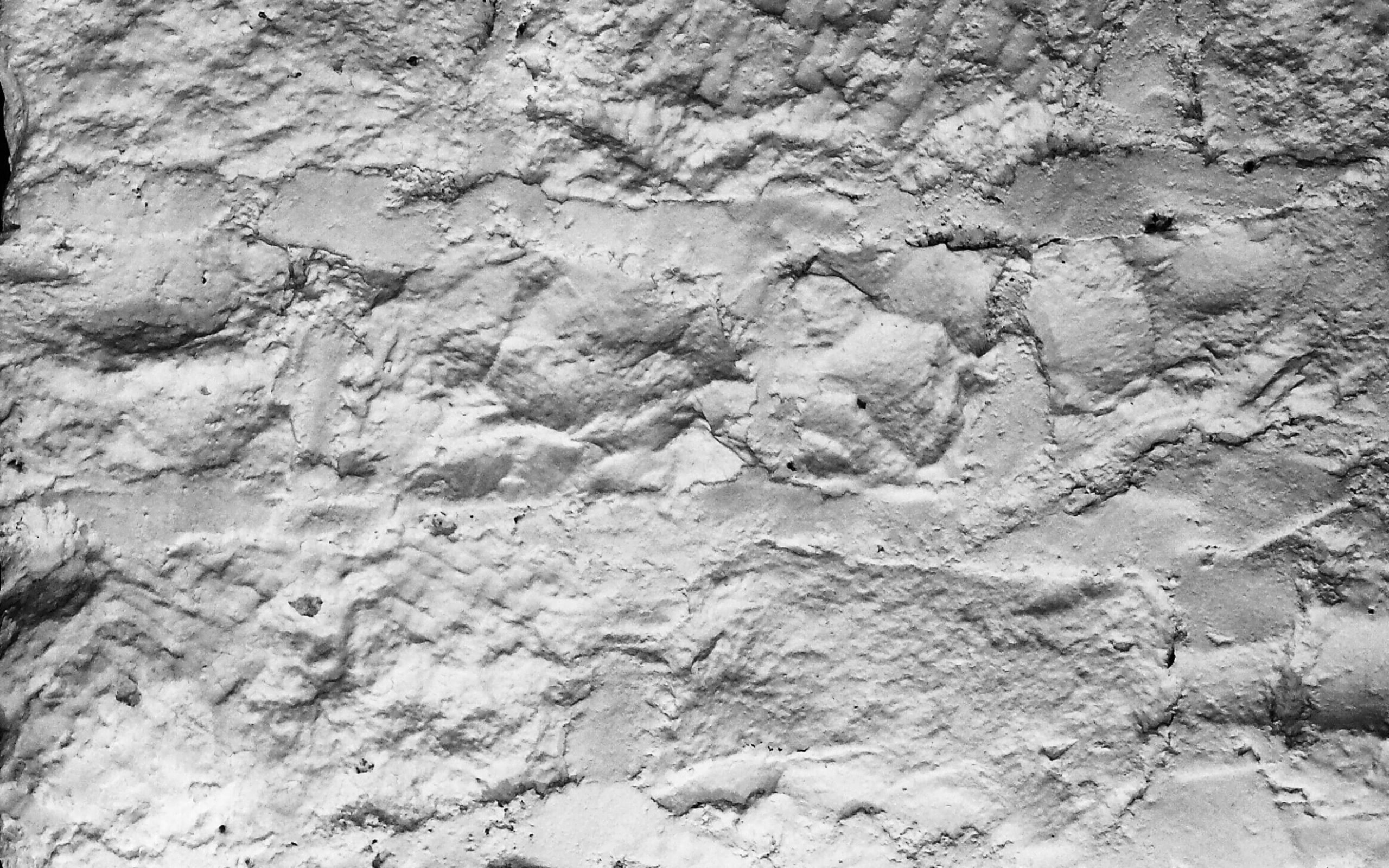
La rugosité de la surface est liée à l'adhérence du revêtement ultérieur.
- L'énergie cinétique des matériaux de sablage
Au cours du processus de sablage, la taille des particules, la densité et la vitesse du produit de sablage déterminent son énergie. Lorsque la taille et la densité des particules sont modérées et que la vitesse de pulvérisation est élevée, le matériau peut éliminer efficacement les salissures de surface et les taches de rouille et obtenir l'effet désiré. En raison de sa dureté et de sa densité élevées, le sable d'oxyde d'aluminium présente une bonne efficacité de conversion de l'énergie cinétique et est particulièrement adapté au traitement des couches de rouille et des revêtements durs ou épais.
- L'effet de la morphologie des particules sur le prétraitement
La morphologie des particules des différents matériaux de sablage influe également sur l'effet du prétraitement de la surface. Les particules de sable d'oxyde d'aluminium présentent des arêtes relativement vives, ce qui permet d'éliminer les salissures et les taches de rouille difficiles à enlever. Les matériaux tels que les billes de verre conviennent au polissage et au traitement de surface fin en raison de leur forme arrondie. Par conséquent, en fonction de l'objectif du traitement de surface, il est nécessaire de sélectionner le matériau de sablage approprié.
- Effet de l'électricité statique
Au cours du processus de sablage, l'électricité statique générée par la friction entre le matériau et la surface de la pièce affectera également l'effet du traitement. Pour les revêtements et les adhésifs, l'électricité statique peut provoquer l'adsorption de poussières et affecter la qualité des processus ultérieurs. Par conséquent, dans les applications à forte demande, l'électricité statique doit être contrôlée ou des matériaux de sablage antistatiques doivent être utilisés pour garantir la qualité de la surface.
Problèmes résolus par le prétraitement des surfaces
Le prétraitement de la surface est important car la surface non traitée du matériau présente généralement les problèmes suivants, qui peuvent empêcher le revêtement d'adhérer complètement, ce qui affecte la durabilité et la fonctionnalité du produit :
Rouille et couche d'oxyde
Lorsque les matériaux métalliques sont exposés à l'air, ils réagissent avec l'oxygène pour former une couche d'oxyde, dont la plus courante est la rouille sur la surface du métal. La rouille n'affecte pas seulement l'apparence du métal, mais surtout, elle érode davantage le matériau et affaiblit sa résistance structurelle. Le sablage permet d'éliminer rapidement et efficacement ces couches d'oxyde et ces taches de rouille, en redonnant au métal une surface brillante et en posant une base solide pour le processus de revêtement ultérieur.
Résidus de revêtement et contaminants
Lorsqu'il faut repeindre, l'ancien revêtement et les résidus de graisse, de saleté, etc. affectent gravement l'adhérence du nouveau revêtement. Le sablage peut nettoyer en profondeur divers résidus de surface grâce à l'impact de particules abrasives à grande vitesse, ce qui garantit la stabilité et la durabilité du nouveau revêtement.
Finition de surface irrégulière
Les surfaces non traitées sont souvent irrégulières, en particulier les matériaux qui ont été utilisés pendant longtemps ou exposés à des environnements difficiles. Le sablage permet non seulement d'éliminer uniformément les impuretés à la surface, mais aussi d'affiner la rugosité de la surface en ajustant le type et la taille des particules de l'agent de sablage afin d'obtenir les meilleures conditions d'adhérence pour différents types de revêtements.
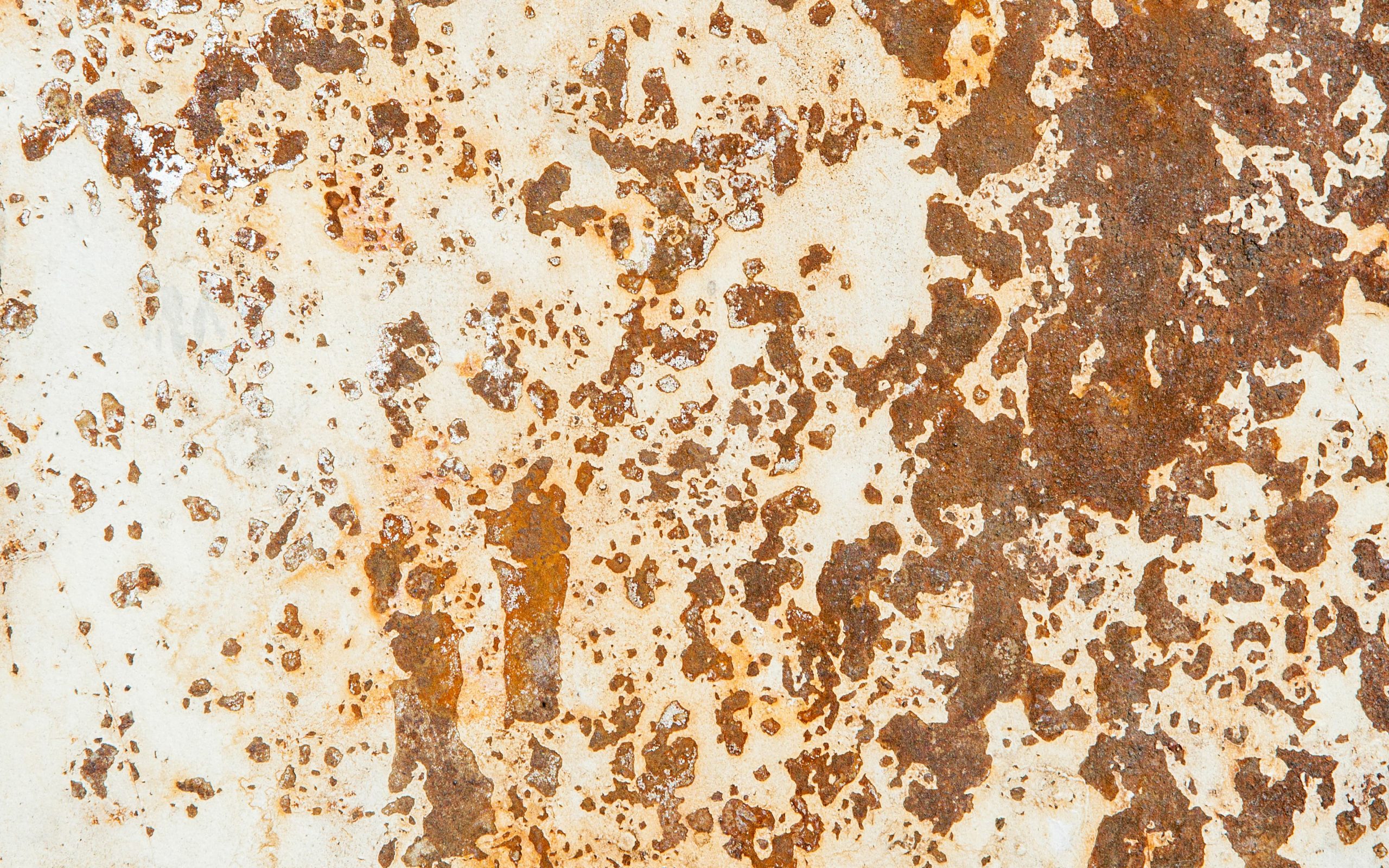
corrosion
Application du prétraitement des surfaces dans diverses industries
Le prétraitement de surface est un processus clé largement utilisé dans de nombreuses industries. Les exigences en matière de traitement de surface peuvent varier d'une industrie à l'autre, en fonction des caractéristiques du matériau et des exigences en matière de revêtement. Ce qui suit est une introduction à plusieurs applications industrielles typiques :
Industrie automobile
Le prétraitement des surfaces est essentiel dans le processus de fabrication et de réparation des automobiles. Les surfaces des pièces clés telles que les carrosseries, les composants du moteur et les roues doivent souvent être sablées pour éliminer les anciens revêtements, les taches de rouille et les impuretés, ce qui permet une meilleure adhérence pour l'application des apprêts et des couches de finition. Par exemple, avant que la carrosserie ne soit pulvérisée, la surface doit présenter une rugosité uniforme pour éviter que le revêtement ne s'écaille et que des bulles ne se forment. En outre, le sablage peut également être utilisé pour polir et découper la surface des pièces afin d'améliorer la finition générale et la durabilité.
Industrie aérospatiale
L'industrie aérospatiale a des exigences extrêmement élevées en matière de performance des matériaux, en particulier pour les pièces qui travaillent dans des environnements à haute température et à haute pression, comme les aubes de turbines, les composants de moteurs d'avion, etc. Après une certaine période d'utilisation, ces pièces formeront une couche d'oxyde ou une défaillance du revêtement en raison de l'oxydation à haute température ou de l'usure. Le sablage permet d'éliminer rapidement les résidus présents sur la surface afin de garantir l'adhérence des revêtements ultérieurs et de prolonger la durée de vie des pièces. En outre, le sablage peut également être utilisé pour renforcer la surface pendant le traitement afin d'améliorer la résistance à la fatigue des matériaux.
Métallurgie et sidérurgie
Les industries métallurgiques et sidérurgiques nécessitent souvent le sablage de grandes structures en acier. Le sablage permet non seulement de nettoyer la rouille en surface, mais aussi d'améliorer la résistance à l'usure de la surface métallique afin d'éviter la concentration des contraintes et la propagation des fissures lors de l'utilisation ultérieure. Dans le traitement des matériaux alliés à haute température, le sablage peut également ajuster la rugosité de la surface pour la rendre plus résistante à la corrosion à haute température. En contrôlant finement la taille des particules et la vitesse des matériaux de sablage, il est possible d'améliorer efficacement les performances de ces matériaux afin de répondre aux exigences d'utilisation d'environnements complexes.
Industrie pétrolière et gazière
Les équipements de l'industrie pétrolière et gazière sont exposés à des environnements extérieurs difficiles tout au long de l'année et sont sujets à des problèmes de corrosion et d'usure. L'application de la technologie de sablage dans l'industrie du pétrole et du gaz se reflète principalement dans le prétraitement de la surface d'équipements clés tels que les pipelines, les équipements de forage et les réservoirs de stockage. Par exemple, lors de l'utilisation du trépan, des boues épaisses et de la rouille sont souvent attachées à la surface. Les méthodes traditionnelles de nettoyage mécanique sont difficiles à éliminer efficacement, tandis que le sablage peut nettoyer rapidement ces impuretés difficiles à éliminer, garantissant ainsi une surface lisse du trépan, ce qui prolonge sa durée de vie.
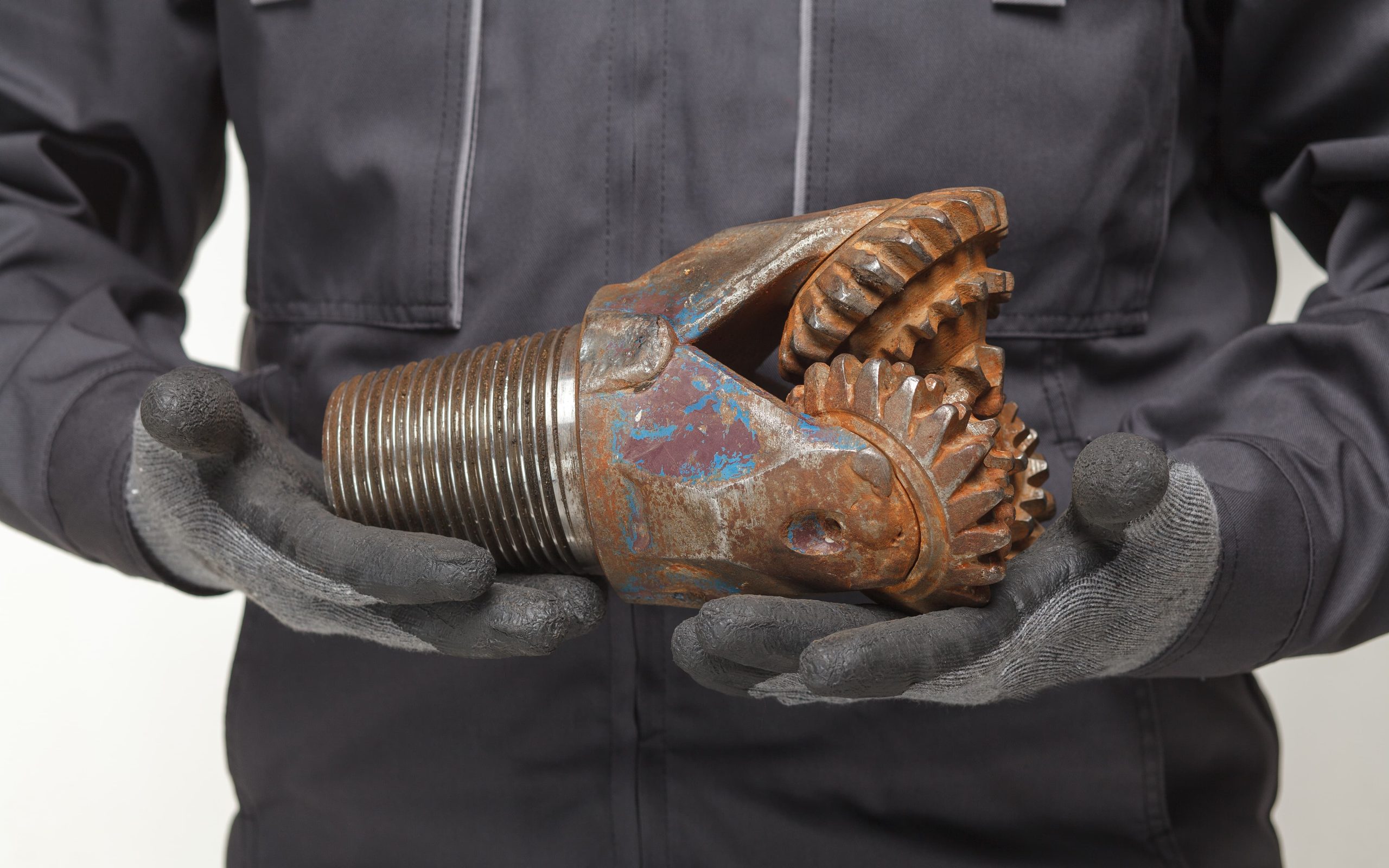
Tenir une perceuse rouillée
Introduction aux matériaux de sablage
Le choix des matériaux de sablage joue un rôle essentiel dans l'effet du prétraitement de la surface. Les différents matériaux ont des caractéristiques différentes et conviennent à des scénarios d'application différents. Dans le processus de prétraitement des surfaces, l'oxyde d'aluminium est l'un des matériaux de sablage les plus courants, mais d'autres matériaux tels que les billes de verre et les billes de céramique ont également leurs propres scénarios d'application.
Sable alumineux
Le sable d'alumine est devenu l'un des matériaux préférés pour le prétraitement des surfaces en raison de sa grande dureté et de sa densité élevée. Grâce à sa forte capacité de coupe, il peut éliminer efficacement la rouille et les vieux revêtements sur les surfaces métalliques. Ses particules sont uniformes et durables, et conviennent à une utilisation répétée à long terme. En outre, le sable d'alumine convient à une variété de matériaux métalliques et non métalliques et peut ajuster la rugosité de la surface en fonction de la taille des particules. Il est largement utilisé dans les tâches de traitement de surface très exigeantes telles que l'automobile, l'aérospatiale, etc.
Perles de verre
Les billes de verre sont principalement utilisées dans les cas qui nécessitent un traitement délicat, comme le polissage de la surface des produits en acier inoxydable et en aluminium. La dureté des billes de verre est relativement faible et elles n'endommagent pas la surface de la pièce lors de leur utilisation. Elles conviennent donc au traitement de matériaux dont les exigences en matière de finition de surface sont élevées. Il est largement utilisé dans le nettoyage et l'ébavurage des dispositifs médicaux et des boîtiers de produits électroniques.
Perles en céramique
Les billes de céramique ont une densité et une résistance à l'usure élevées, ce qui en fait un choix idéal pour le traitement des matériaux à haute résistance, en particulier pour le nettoyage et le renforcement de la surface des matériaux résistants aux hautes températures. Les billes de céramique sont principalement utilisées pour les pièces nécessitant un traitement de surface de précision, telles que les pales de turbines et les alliages à haute température. Ses caractéristiques sont qu'elles peuvent maintenir la stabilité dans des environnements à haute température et garantir la qualité de la surface.
Comment choisir le bon matériel de sablage
Il est essentiel de choisir le bon matériau de sablage en fonction des besoins de prétraitement de la surface. Les différents scénarios d'application ont des exigences de performance différentes pour les matériaux, de sorte que la sélection des matériaux de sablage doit être basée sur les facteurs suivants :
Matériau de la pièce
Les exigences en matière de matériaux de sablage varient en fonction du matériau de la pièce à traiter. Par exemple, les pièces métalliques nécessitent généralement un produit de sablage plus dur pour le nettoyage, tandis que les pièces en plastique ou en alliage léger nécessitent un produit plus doux pour éviter de rayer ou d'endommager la surface.
Objectifs du traitement de surface
Si l'objectif est d'éliminer rapidement la rouille ou les revêtements, le sable d'oxyde d'aluminium sera un choix idéal en raison de sa forte force de coupe. Si la surface doit être lissée ou renforcée, d'autres types de matériaux de sablage tels que les billes de verre ou les billes de céramique peuvent être plus appropriés.
Efficacité économique
Dans les grands projets industriels, l'efficacité économique des matériaux de sablage doit également être prise en considération. Le coût initial des matériaux de sablage à l'oxyde d'aluminium peut être élevé, mais leur longue durée de vie et leur excellente capacité de nettoyage les rendent très rentables à long terme.
En résumé, le sablage est une méthode efficace de prétraitement des surfaces, avec d'excellents effets de nettoyage et des avantages en termes d'adhérence, et il est largement utilisé dans divers domaines industriels. Des matériaux et des besoins différents peuvent conduire à des différences dans le meilleur processus de sablage, de sorte que le choix de la technologie de sablage la plus appropriée est crucial pour obtenir le meilleur effet de traitement de surface. Dans des applications spécifiques, le support et le procédé de sablage appropriés doivent être soigneusement sélectionnés en fonction du matériau de la pièce et des objectifs du traitement afin d'en maximiser les avantages.
Annexe :
Normes et spécifications pour le prétraitement des surfaces
Pour garantir la qualité et la sécurité du prétraitement des surfaces, diverses industries disposent de normes et de spécifications correspondantes, en particulier dans les applications de haute précision telles que l'aérospatiale et l'automobile. Voici quelques normes internationales courantes :
- ISO 8501-1 : Norme de propreté des surfaces
La norme ISO 8501-1 est une norme internationale relative à la propreté des surfaces métalliques, qui sert à évaluer le degré d'élimination de la rouille et des revêtements en surface. Le sablage, en tant que méthode de nettoyage mécanique, est souvent utilisé pour répondre aux exigences de cette norme. Les différents niveaux de propreté ont des exigences différentes en ce qui concerne la rugosité de la surface, l'adhérence du revêtement et l'environnement d'utilisation. La taille des particules et le choix des matériaux utilisés pour le sablage ont une incidence directe sur la réalisation du niveau de propreté.
- Série ISO 11124 : Spécifications pour les matériaux de sablage
La série de normes ISO 11124 réglemente spécifiquement les exigences de qualité des matériaux de sablage, y compris la morphologie des particules, la composition chimique et la dureté des matériaux courants tels que le sable d'alumine et les billes de verre. Ces normes garantissent que les matériaux de sablage ont des performances constantes dans les applications pratiques, assurant ainsi la stabilité et l'effet du prétraitement de la surface.
- Norme SSPC : Spécifications pour le nettoyage et le revêtement des surfaces
L'American Society for Steel Structure Coatings (SSPC) a également élaboré des normes pour la préparation des surfaces, en particulier pour le nettoyage par sablage des revêtements anticorrosion sur les structures en acier. La norme SSPC fournit une classification détaillée des différents niveaux de nettoyage, et les opérations de sablage doivent suivre les spécifications correspondantes en fonction des exigences du projet afin d'obtenir le meilleur effet d'adhérence du revêtement.
Filtres