Ceramic peening beads: efficient surface strengthening
September 6, 2024
With the rapid development of modern manufacturing, the requirements for surface treatment technology are constantly increasing. From improving the aesthetics of materials to enhancing their durability, corrosion resistance and overall performance, shot peening technology plays a vital role. As a commonly used media in shot peening technology, ceramic peening beads have gradually become a popular choice in the industry due to their unique material properties and high efficiency. This article will explore the characteristics, advantages, economic benefits and industry applications of ceramic peening beads in depth, and analyze their actual performance in multiple fields through real cases.
What are ceramic peening beads?
Ceramic peening beads are a type of shot blast media made of high-strength ceramic materials, mainly used in surface treatment processes. Shot peening technology uses high-speed projectiles of tiny particles to impact the surface of the workpiece, thereby producing plastic deformation and enhancing the fatigue strength and wear resistance of the material surface. Compared with other shot blast media, ceramic peening beads have the advantages of high hardness, good durability and environmental protection, so they are widely used in multiple industrial fields.
Features
- Material composition
The main components of our ceramic peening beads are zirconium oxide (60–70%), silicon dioxide (28–33%) and a small amount of aluminum oxide. These high-strength ceramic materials are extremely wear-resistant and chemically stable. Zirconia not only has excellent hardness, but also remains stable under extreme temperature conditions. Aluminum oxide is often used for standard industrial needs due to its wide availability and cost-effectiveness.
- Hardness
Ceramic peening beads have a very high hardness, ranging from 7 to 9 on the Mohs hardness scale, which is much higher than traditional steel and glass beads. This high hardness allows ceramic peening beads to exert strong impact forces on the workpiece surface during application, thereby improving the material’s wear resistance and fatigue resistance.
- Particle shape
Ceramic peening beads are usually spherical in shape. This shape allows the beads to produce uniform impact forces during blasting, avoiding uneven wear or excessive material erosion. The smooth surface also helps to reduce micro cracks on the workpiece surface caused by excessive impact.
- Durability
Ceramic peening beads have superior durability compared to other shot peening media. With a hardness range of 643-780HV, ceramic peening beads can maintain stable performance in long-term high-intensity operations, so they are not easy to break during multiple cycles. In industrial applications, the long life of ceramic peening beads not only reduces material costs, but also improves the efficiency of peening operations.
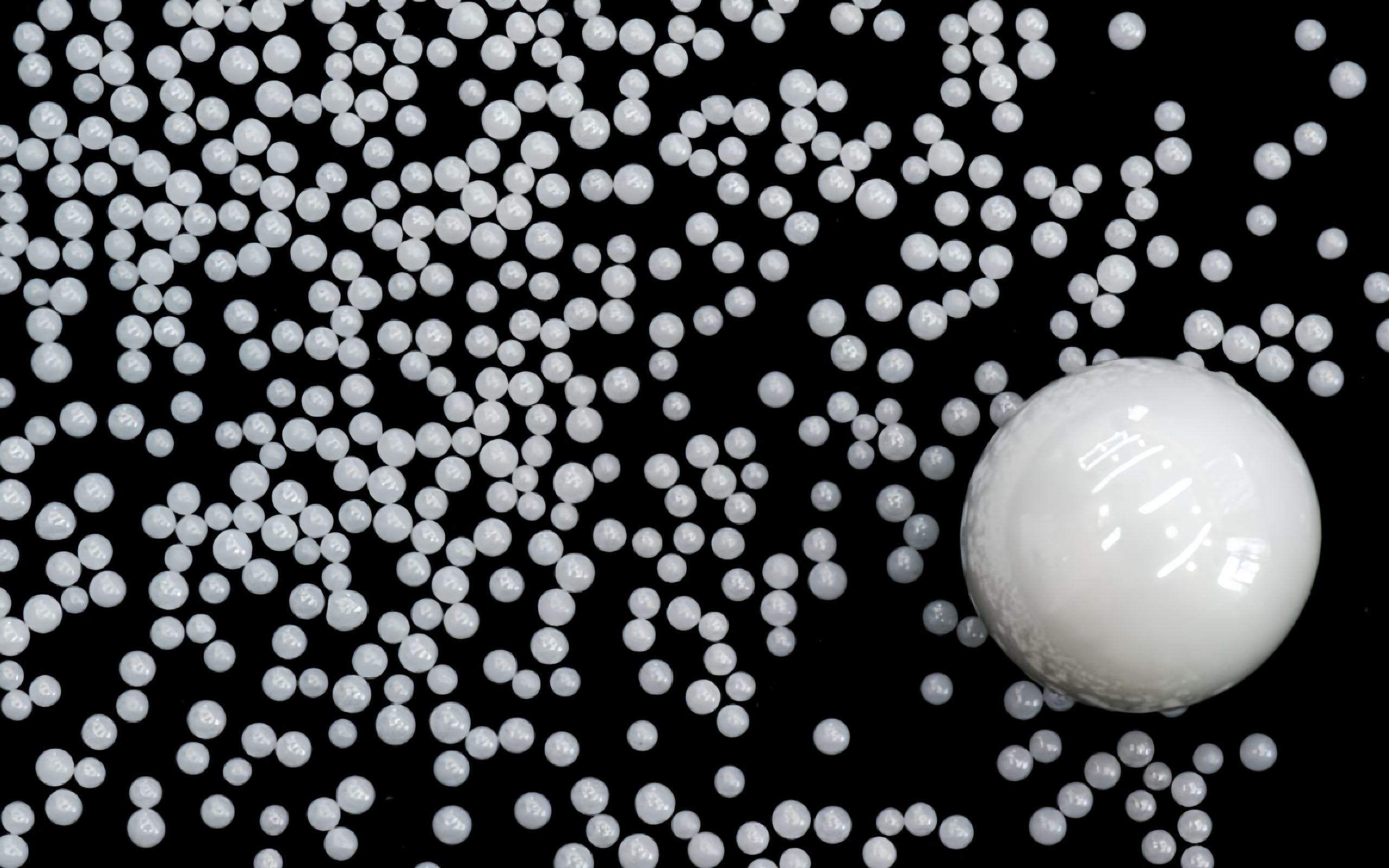
Our live shot products
Advantages and Challenges
Advantages
- High efficiency: The high hardness and wear resistance of ceramic peening beads enable them to provide high-quality surface treatment results in a continuous and stable manner during the shot peening process. Due to their low breakage rate, the frequency of particle renewal in the peening operation is greatly reduced, thereby improving the economic benefits of the process.
- Environmental protection: Ceramic peening beads do not contain toxic substances and can be recycled many times, reducing the generation of waste. Compared with some peening media containing metal components, ceramic peening beads have a lower environmental impact and are suitable for industrial applications with high environmental requirements.
- Consistency: Due to the spherical particles and high hardness of ceramic peening beads, the peening effect is highly consistent and can provide uniform surface treatment results, especially suitable for processing occasions requiring high precision.
Challenges
- High initial cost: Compared with other peening media, ceramic peening beads have a relatively high purchase cost. Although its long life can partially offset this cost, the initial investment may be a challenge for some small and media-sized enterprises.
- Limited applicability: The high hardness of ceramic peening beads is particularly suitable for surface strengthening of large parts, but on the contrary, it is not suitable for soft metals, plastics, wood and other materials or applications that require gentle surface treatment.
Economic benefits and environmental protection
Although the initial cost of ceramic peening beads is high, given the extremely high wear resistance and cycle life of ceramic beads, enterprises can obtain less particle loss, less material replacement frequency, longer service life and lower waste disposal costs, which together reduce the overall operating costs, so its long-term economic benefits are obvious.
On the other hand, with the increasingly stringent environmental protection regulations of various countries, the demand for environmentally friendly materials in industrial production is increasing. The environmental protection of ceramic peening beads is mainly reflected in the fact that they do not contain any toxic and harmful substances, will not pollute the surrounding environment, are also friendly to the health of workers, and can be recycled many times, greatly reducing the generation of industrial waste. These two advantages not only meet the sustainable development goals of modern enterprises, but also meet customers’ needs for green manufacturing.
Industry Application and Case Analysis
Ceramic peening beads are widely used in multiple industrial fields. The following is an application case analysis of three typical industries.
- Aerospace Industry
- Background: Aerospace is a field with extremely high requirements for materials and processes. Aircraft and spacecraft components often need to work under extreme temperatures and pressures. Ceramic peening beads are mainly used for surface strengthening treatment of aircraft turbine engines, gas turbine blades, fuselage structural parts and key connecting parts.
- Case: Rolls-Royce is one of the world’s leading aircraft engine manufacturers. Its turbine blade manufacturing process uses ceramic shot peening technology. The application of this process effectively enhances the fatigue resistance and corrosion resistance of the blades and extends the service life. Through shot peening, Rolls-Royce’s engine components can reduce stress concentration under extreme temperature and pressure conditions, avoid surface crack propagation, run longer, and reduce maintenance frequency, which not only improves the safety and reliability of the aircraft, but also saves long-term maintenance costs. According to data provided by the company, the life of turbine blades treated with ceramic shot peening has increased by 15%-20%.
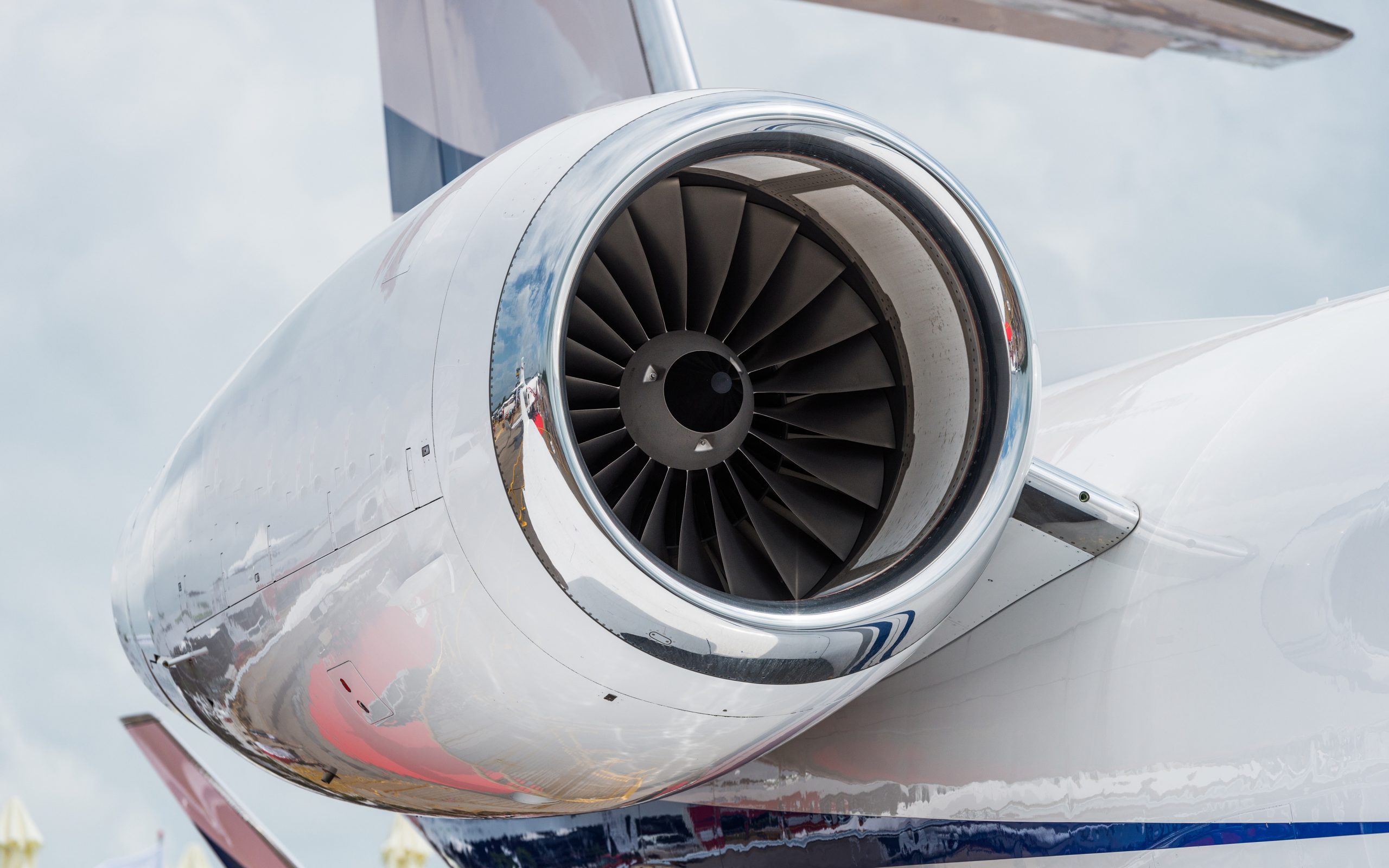
Aircraft turbine blades
- Automobile Manufacturing
- Background: In automobile manufacturing, especially for high-performance sports cars and commercial vehicles, the strength and reliability of components are crucial. Ceramic peening beads are widely used for surface treatment of key components such as automobile transmission systems, gears and suspension systems. By spraying onto the surface of metal parts, core components such as gears, crankshafts, connecting rods in the transmission system can be effectively strengthened. The high hardness and wear resistance of ceramic beads also ensure that the shot peening process improves its surface structure and increases the fatigue resistance and crack resistance of components without damaging the components.
- Case: BMW widely uses ceramic peening beads for surface treatment of gears and transmission systems of its high-performance sports cars. BMW’s M series models are known for their excellent performance and precise control, and ceramic shot peening technology helps improve the durability of core components of these vehicles. BMW fully applies this technology in its production line, making the stress distribution on the gear surface more uniform, reducing component wear, and thus improving the performance of the vehicle under high load. Data shows that the durability of gears after ceramic shot peening is increased by about 30%, allowing BMW to further improve the reliability and safety of its sports cars.
- Medical equipment
- Background: The medical industry has extremely high requirements for surface treatment technology, especially when manufacturing implants and surgical tools. The quality of surface treatment directly affects the biocompatibility and service life of the material. The application of ceramic peening beads in medical devices is mainly concentrated in the treatment of bone nails, heart stents, and joint implants (such as artificial hip joints and knee joints) to improve their wear resistance and biocompatibility. Ceramic peening beads can not only optimize the surface roughness, but also enhance the fusion effect between the implant and human tissue and reduce postoperative friction and wear. At the same time, ceramic shot peening technology is used to treat the surface of surgical instruments to enhance the durability and corrosion resistance of the instruments.
- Case: Stryker is a world-renowned medical device manufacturing company that focuses on the production of high-end medical implants such as artificial joints. They also use ceramic peening beads to treat the surface of artificial hip joints, which significantly improves the wear resistance and biocompatibility of the joints. The company’s research report data shows that the life of hip implants treated with ceramic shot peening in clinical use has been extended by more than 20%, effectively reducing the risk of secondary surgery for patients.
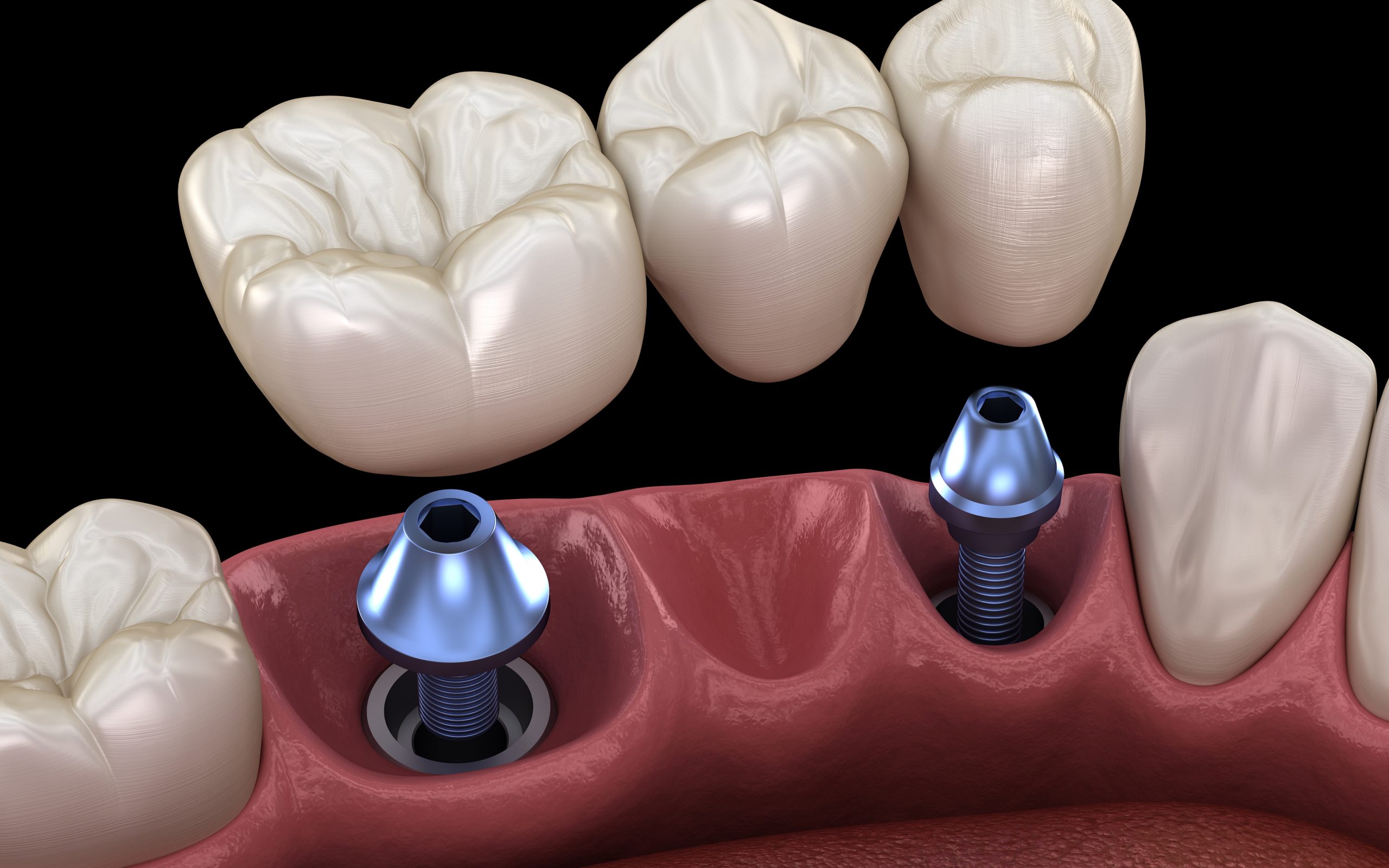
Dental bridge supported by implants
- Molds
- Background: Mold strengthening is to improve its durability and crack resistance, reduce failures and downtime, reduce wear and fatigue, and thus extend its service life. This not only improves production efficiency, but also reduces maintenance costs and ensures the consistency and stability of product quality. By strengthening molds, companies can maintain the continuity and efficiency of production under high-intensity working conditions, and ultimately achieve higher economic benefits.
- Case: According to sources such as technical white papers, research reports and market research data released by various companies, it can be seen that: after shot peening, Bosch’s mold life was extended by 30%, the defect rate in the production process was reduced by 25%, and the overall production efficiency was improved by 20%; Apple used ceramic peening beads in the surface treatment of aluminum alloy molds to improve the finish and durability of the molds, and the final mold appearance quality was improved by 15%, production defects were reduced by 20%, and mold maintenance costs were reduced by 25%; Volkswagen reported that the mold life was increased by 25%, the mold maintenance frequency was reduced by 30%, and the production line downtime was reduced by 20%; GE Aviation used ceramic shot peening technology in molds for aircraft engine components to cope with high temperature and high pressure conditions. The service life of the treated molds was extended by 40%, and the mold’s high temperature resistance was improved by 35%.
Applications of different sizes
- Z100 (0.100–0.150 mm)
- Application: Mainly used for delicate treatments with extremely high surface finish requirements, such as shot peening of precision molds, electronic components and micro-mechanical parts. Ceramic peening beads of this size are suitable for processing extremely small surface defects and fine surface textures. They are widely used in the manufacture of high-precision electronic devices and micro-components, such as surface treatment of mobile phone screens and deburring of precision mechanical parts.
- Features: Small particles can provide high-quality surface smoothness and precision, suitable for processing fine surface defects. In some industries with particularly high requirements for surface finish, such as high-end electronic products and micro-mechanical fields, Z100-sized shot peening beads can significantly improve the appearance and functionality of the finished product.
- Z150 (0.150–0.210 mm)
- Application: Used for media-precision surface treatment, such as molds for consumer electronics, precision castings, and plastic molds. Shot peening beads of this size can effectively remove minor surface defects and provide appropriate treatment intensity while maintaining surface smoothness. They are often used to improve the surface quality of precision castings and enhance the service life of molds.
- Features: The particles are slightly larger than Z100, but they can still provide a high level of surface treatment effect, suitable for processing workpieces with media precision requirements. It can provide stronger surface strengthening effect while maintaining high surface smoothness, and is the first choice of many consumer electronics manufacturers.
- Z210 (0.250–0.425 mm)
- Application: Used for media-strength surface treatment, such as pretreatment of automotive parts and aerospace components and removal of surface oxide layers. This size of shot peening beads is suitable for removing thick oxide layers or surface impurities, while enhancing the surface roughness and improving the adhesion of parts.
- Features: The particles are larger and suitable for applications where large surface defects or oxide layers need to be removed, especially in the pretreatment stage of automotive parts and aerospace components. It can effectively handle relatively thick surface impurities and provide better surface conditions for subsequent processing.
- Z300 (0.300–0.425 mm)
- Application: Suitable for surface treatment of media and large molds, especially when the mold surface needs to improve wear resistance. This size of shot peening beads can take into account both removing surface defects and enhancing surface strength, and is suitable for the treatment of large mechanical parts and industrial molds.
- Features: The particle size is moderate, which can provide strong surface treatment effect while avoiding excessive wear and damage to the workpiece. It is very suitable for treating large surface areas and can effectively improve the service life and performance of molds.
- Z425 (0.425-0.600 mm)
- Application: Used for rougher surface treatment, such as casting molds, engineering machinery parts, or removing larger rust and impurities. Shot peening beads of this size can provide efficient treatment effects in rougher surface treatment.
- Features: The particles are large and can effectively treat rough or damaged surfaces. It is suitable for applications that require strong shot peening, such as surface treatment of large engineering machinery or cleaning of casting molds. It can quickly remove rust and impurities on the surface and improve the surface quality and durability of parts.
- Z600 (0.600-0.850 mm)
- Application: Used for rough surface treatment or high-strength surface strengthening, such as shot peening of large castings and heavy structural parts. Shot peening beads of this size are suitable for treating large areas and high-strength surfaces.
- Features: Large particle size, capable of processing heavy surface layers, enhancing surface roughness, suitable for large-scale and high-intensity processing needs. It can complete relatively rough surface processing in a shorter time, suitable for surface strengthening of large structural parts and industrial components.
- Z850 (0.850–1.180 mm)
- Application: Used for extremely rough surface treatment, such as surface pretreatment of large molds, decontamination and strengthening of large mechanical parts. This size of shot peening beads is suitable for processing extremely rough surfaces and can effectively remove heavy surface layers.
- Features: The largest particle size, suitable for processing extremely rough surfaces, can quickly remove heavy surface layers and improve surface durability. It is suitable for surface treatment under extreme conditions, such as pretreatment of large molds or surface strengthening of large mechanical parts, and can complete high-intensity processing work in a shorter time.
Ceramic peening beads are gradually becoming the preferred media for surface treatment in various industries due to their excellent material properties, economic benefits and environmental advantages. Whether in the fields of aerospace, automotive manufacturing or medical equipment, ceramic peening beads have demonstrated their unique advantages. Although its initial cost is relatively high, from the perspective of long-term application, its high efficiency, durability and environmental friendliness can bring significant cost savings and environmental benefits to enterprises. With the continuous advancement of technology and the changing needs of the industry, ceramic peening beads are expected to be promoted and applied in more fields and play a more important role in promoting the development of green industry. In the future, we expect ceramic peening beads to further break through the limitations of application and become an important force in promoting the sustainable development of modern manufacturing industry.
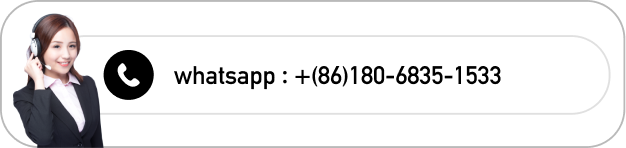