Qu'est-ce que le procédé d'ébavurage cryogénique ?
19 septembre 2024

Dans la fabrication moderne, l'ébavurage ou l'ébarbage est une étape importante pour garantir la précision et la qualité des produits. Qu'il s'agisse de pièces automobiles, de composants électroniques ou d'autres produits industriels, les fabricants ont toujours été confrontés à des problèmes de bavures. Les bavures n'affectent pas seulement l'apparence du produit, mais peuvent également entraîner un mauvais fonctionnement des dispositifs mécaniques et même raccourcir la durée de vie du produit. C'est pourquoi la question de savoir comment éliminer les bavures de manière efficace et économique est devenue un sujet d'attention dans l'industrie manufacturière. Avec les progrès constants de la technologie, une technique d'ébavurage innovante est progressivement apparue aux yeux du public : le procédé d'ébavurage cryogénique. Par rapport aux procédés d'ébavurage traditionnels, cette technologie est progressivement devenue un élément indispensable de l'automatisation industrielle et de la fabrication de précision en raison de sa grande efficacité et de sa précision. Dans cet article, nous présenterons en détail le procédé d'ébavurage cryogénique, nous étudierons son principe de fonctionnement, ses différences par rapport aux procédés traditionnels, les matériaux applicables et ses avantages dans la fabrication.
Qu'est-ce que le procédé d'ébavurage cryogénique ?
Définition
Comme son nom l'indique, le procédé d'ébavurage cryogénique est une technologie qui permet d'éliminer les bavures par des moyens physiques après avoir refroidi la pièce à une température extrêmement basse. Le principe consiste à refroidir le matériau jusqu'à ce qu'il devienne cassant, de sorte que les bavures à sa surface deviennent cassantes, et que ces bavures soient ensuite facilement éliminées par vibration mécanique ou d'autres méthodes physiques. Le moyen de refroidissement courant est l'azote liquide, qui peut rapidement refroidir le matériau à une température proche de moins 150°C, ce qui permet d'obtenir un effet d'ébavurage idéal.
L'ébavurage cryogénique est particulièrement adapté à certains matériaux sensibles à la chaleur, tels que les plastiques, les silicones et certains métaux tendres. Ces matériaux sont facilement déformés ou endommagés à haute température, et les méthodes traditionnelles d'ébavurage mécanique ou chimique sont difficiles à manier avec précision, alors que les procédés à basse température peuvent éviter ces problèmes et atteindre l'objectif de l'ébavurage tout en conservant la forme et les performances de la pièce à usiner.
Principe de fonctionnement
Elle comprend principalement trois étapes : le refroidissement, le durcissement et l'enlèvement mécanique :
- Refroidissement : Tout d'abord, la pièce prétraitée est placée dans un environnement à basse température, généralement un caisson de réfrigération à l'azote liquide, qui peut rapidement refroidir la pièce à une température proche de moins 150°C.
- Bavures de trempe : À basse température, les bavures du matériau deviennent fragiles, tandis que la structure principale reste relativement stable. En raison des coefficients de dilatation thermique différents d'un matériau à l'autre, la partie de la bavure située à la surface de la pièce devient souvent fragile avant le matériau principal, ce qui la rend plus fragile.
- Enlèvement mécanique : Les bavures fragilisées tombent naturellement sous l'effet de vibrations mécaniques ou d'autres stimulations physiques légères (telles que le grenaillage mécanique ou l'impact d'un flux d'air). Ce procédé est très précis et n'endommage pas la surface ou la forme de la pièce, ce qui convient particulièrement aux pièces présentant des exigences élevées en matière de finition de surface.
- Nettoyage et inspection : Après l'ébavurage, la surface de la pièce est à nouveau nettoyée pour éliminer les débris résiduels ou d'autres impuretés afin de garantir que la pièce atteigne la finition et la précision attendues.
- Contrôle de la qualité : Les méthodes d'inspection courantes comprennent l'inspection microscopique, l'inspection visuelle ou les instruments de mesure de la surface pour détecter la planéité et la finition de la pièce afin de s'assurer que toutes les bavures ont été éliminées et que la pièce n'a pas été endommagée d'une autre manière.
Objectif
L'objectif principal de l'ébavurage cryogénique est d'éliminer les bavures de manière efficace et non destructive afin de garantir la précision, l'état de surface et la durée de vie de la pièce. Un autre objectif important est d'économiser du temps et de l'argent. L'ébavurage cryogénique présente un degré élevé d'automatisation et peut traiter un grand nombre de pièces à la fois, ce qui lui confère une grande efficacité dans la production de masse. En outre, comme il n'y a pas d'usure excessive de la surface de la pièce ni de modification de la structure du matériau, les étapes de traitement ultérieures peuvent être simplifiées, ce qui permet de réduire encore les coûts de production.
Avantages
- Haute précision
Comme la technologie d'ébavurage cryogénique repose sur les différences de température pour fragiliser les bavures, elle n'endommage pas le corps de la pièce. Cela signifie que même les pièces très délicates (telles que les composants électroniques ou les appareils médicaux) peuvent conserver leur forme et leur taille. Cette technologie d'ébavurage de haute précision améliore considérablement le taux de qualification des produits.
- Convient aux géométries complexes
Par rapport à l'ébavurage mécanique traditionnel, l'ébavurage cryogénique peut facilement traiter certaines structures de pièces complexes, telles que les rainures, les fentes, les trous minuscules, etc. Ces pièces sont généralement difficiles à traiter avec les méthodes mécaniques traditionnelles, alors que le processus d'ébavurage cryogénique élimine les bavures par refroidissement à l'azote liquide et vibration, sans être limité par les formes géométriques.
- Forte adaptabilité des matériaux
L'ébavurage cryogénique convient au traitement d'une série de matériaux, en particulier les matériaux sensibles à la chaleur. Par exemple, les matières plastiques, les plastiques et certains métaux tendres sont facilement déformés ou endommagés à haute température ou sous une forte action mécanique, alors que le processus d'ébavurage cryogénique peut éliminer les bavures sans chauffer ou appliquer une pression mécanique trop importante, en conservant les propriétés physiques et chimiques d'origine du matériau.
- Efficace et automatisé
L'ensemble du processus d'ébavurage cryogénique peut être hautement automatisé. La pièce n'a besoin que de passer par quelques étapes dans la machine, telles que le refroidissement, la vibration et le nettoyage, pour terminer l'opération d'ébavurage. Un grand nombre de pièces peuvent être traitées en même temps, ce qui améliore considérablement l'efficacité de la production et convient particulièrement à la production de masse.
- Économies de coûts
Bien que l'investissement initial en équipement pour l'ébavurage cryogénique puisse être élevé, à long terme, le coût d'utilisation de cette technologie est faible. En raison du degré élevé d'automatisation du processus, aucune intervention manuelle importante n'est nécessaire, le temps de traitement est court et efficace, le coût unitaire de traitement de chaque pièce est faible.
- Forte protection de l'environnement
L'ébavurage cryogénique utilise de l'azote liquide, un matériau non toxique, inoffensif et recyclable, respectueux de l'environnement. Par rapport à certaines méthodes d'ébavurage chimique, il ne produit pas de gaz d'échappement nocifs, d'eaux usées ou d'autres polluants. Cette méthode est non seulement respectueuse de l'environnement, mais elle est également conforme aux réglementations de plus en plus strictes en matière de protection de l'environnement.
Différences par rapport aux procédés d'ébavurage traditionnels

La principale différence réside dans la température et les méthodes de traitement. Les procédés traditionnels reposent généralement sur le découpage mécanique, le meulage, le traitement chimique ou le traitement à haute température, qui fonctionnent bien pour les matériaux durs, mais ont souvent des limites lorsqu'il s'agit de traiter des matériaux souples ou à structure complexe.
L'ébavurage cryogénique durcit les bavures par refroidissement et les élimine ensuite en douceur. En revanche, il ne produit pas de contraintes thermiques ou mécaniques significatives et n'affecte donc pas les propriétés intrinsèques du matériau. En outre, le procédé d'ébavurage cryogénique convient également au traitement de pièces présentant des géométries complexes, telles que des rainures, des fentes et d'autres zones difficiles à ébavurer mécaniquement. Un autre avantage est que la vitesse et la précision du processus d'ébavurage cryogénique sont également supérieures aux processus d'ébavurage mécanique ou chimique traditionnels.
Types de procédés d'ébavurage traditionnels
- Ébavurage mécanique : Les bavures sont éliminées par des outils de coupe, de meulage ou de polissage manuels ou automatiques. Les avantages sont la simplicité de l'opération et le faible coût de l'équipement, mais pour les pièces de forme complexe, les méthodes mécaniques ne peuvent souvent pas couvrir toutes les zones. En outre, l'ébavurage mécanique peut provoquer un certain degré de rayures ou de déformation à la surface de la pièce.
- Ébavurage thermique : Les bavures sont fondues ou évaporées à haute température (généralement par combustion), ce qui convient à certains matériaux résistants aux températures élevées. Cette méthode convient au traitement des bavures de grande surface, mais la plage d'ébavurage ne peut pas être contrôlée avec précision et elle peut affecter les propriétés mécaniques du matériau lui-même.
- Ébavurage électrochimique (ECM) : Les bavures sont éliminées par un électrolyte et un courant électrique. Son avantage est que la profondeur de l'ébavurage peut être contrôlée avec précision et qu'il convient au traitement des matériaux métalliques à dureté élevée, mais l'équipement est coûteux et la vitesse de traitement est lente.
- Ébavurage chimique : Les bavures sont corrodées et éliminées à l'aide de solutions acides ou alcalines. Cette méthode convient pour certaines petites pièces de précision, mais la corrosivité de la solution peut avoir un effet néfaste sur le corps principal du matériau.
Comparaison de l'applicabilité avec d'autres processus
L'ébavurage cryogénique présente des avantages significatifs par rapport aux autres procédés d'ébavurage, en particulier pour le traitement de pièces de haute précision et de géométrie complexe. L'analyse comparative présentée dans le tableau suivant peut vous aider à comprendre leurs différences de manière plus intuitive.
Matériaux adaptés à l'ébavurage cryogénique
La particularité de la technologie de l'ébavurage cryogénique est qu'elle permet de traiter des matériaux difficiles à ébavurer par les procédés traditionnels, en particulier dans les applications exigeant une grande précision. Les matériaux suivants sont couramment utilisés dans l'ébavurage cryogénique :
Caoutchouc et élastomères
Le caoutchouc et les élastomères sont difficiles à traiter à l'aide des méthodes d'ébavurage mécanique traditionnelles en raison de leurs propriétés à la fois souples et résistantes. Ces matériaux sont généralement utilisés pour les bandes d'étanchéité automobiles, les joints d'équipement électronique, les pièces souples des appareils médicaux, etc.
- Propriétés physiques : Les matériaux en caoutchouc et en élastomère deviennent rapidement cassants à basse température, et les bavures sont plus faciles à enlever sans endommager la structure principale.
- Propriétés chimiques : Ces matériaux ne subissent pas de modifications chimiques dans des environnements à basse température et peuvent retrouver leur élasticité d'origine.
- Scénarios d'application : L'industrie automobile, l'industrie électronique, la fabrication d'équipements médicaux, etc. nécessitent des pièces de haute précision, qui sont généralement les principaux domaines d'application des procédés d'ébavurage cryogénique.
Thermoplastiques
Les thermoplastiques comprennent l'ABS, le polyéthylène (PE), le polypropylène (PP), etc., qui sont largement utilisés dans les produits de première nécessité, les appareils médicaux, les boîtiers électroniques, les accessoires automobiles et d'autres domaines. Ces matériaux sont généralement souples et produisent facilement de minuscules bavures au cours du processus de production.
- Propriétés physiques : Les thermoplastiques peuvent être rapidement refroidis dans des environnements à basse température, et les bavures deviennent cassantes, de sorte que les bavures peuvent être enlevées sans endommager la structure principale.
- Propriétés chimiques : Le traitement à basse température ne modifie pas les propriétés chimiques de ces matériaux, de sorte que la solidité, la résistance chimique, la résistance à la chaleur et d'autres propriétés des matériaux sont maintenues.
- Scénarios d'application : La technologie d'ébavurage cryogénique est largement utilisée pour les pièces en plastique, telles que les boîtiers de produits électroniques, les pièces intérieures d'automobiles, les emballages alimentaires, etc.
Métaux doux
Les métaux tendres tels que l'aluminium et le magnésium sont souvent utilisés dans l'aérospatiale, la construction automobile, les instruments de précision et d'autres domaines. Ces métaux étant sensibles à la température et aux contraintes mécaniques, les méthodes d'ébavurage mécanique traditionnelles peuvent facilement déformer ou endommager la pièce.
- Propriétés physiques : Les métaux doux ne deviennent pas cassants à basse température, mais la dureté de la bavure diminue, de sorte qu'elle peut être facilement enlevée par vibration mécanique ou impact du flux d'air.
- Propriétés chimiques : Les basses températures ne modifient pas les propriétés chimiques des métaux, de sorte que leurs propriétés de base, telles que la résistance à la corrosion et la solidité, restent inchangées.
- Scénarios d'application : Dans les industries de transformation des métaux à forte demande, telles que les pièces d'aviation, les pièces automobiles et les instruments de précision, les procédés d'ébavurage cryogénique sont généralement utilisés pour garantir la haute précision des pièces à usiner.
Matériaux composites
Les composites sont largement utilisés dans des secteurs tels que l'aviation, l'automobile et les équipements sportifs, en particulier pour certaines pièces présentant des exigences élevées en matière de résistance et de légèreté.
- Propriétés physiques : Les matériaux composites sont mélangés à d'autres matériaux et possèdent de solides propriétés mécaniques, mais leur structure complexe rend l'élimination des bavures difficile. Le processus d'ébavurage cryogénique peut traiter efficacement ces matériaux sans affecter leur résistance structurelle.
- Propriétés chimiques : Les basses températures n'affectent pas la stabilité chimique des matériaux composites, ce qui garantit leur résistance à la corrosion et à l'usure dans l'environnement d'utilisation.
- Scénarios d'application : Les applications de haute précision et de haute résistance telles que l'aérospatiale, la construction automobile et les équipements sportifs sont des domaines idéaux pour l'ébavurage cryogénique.
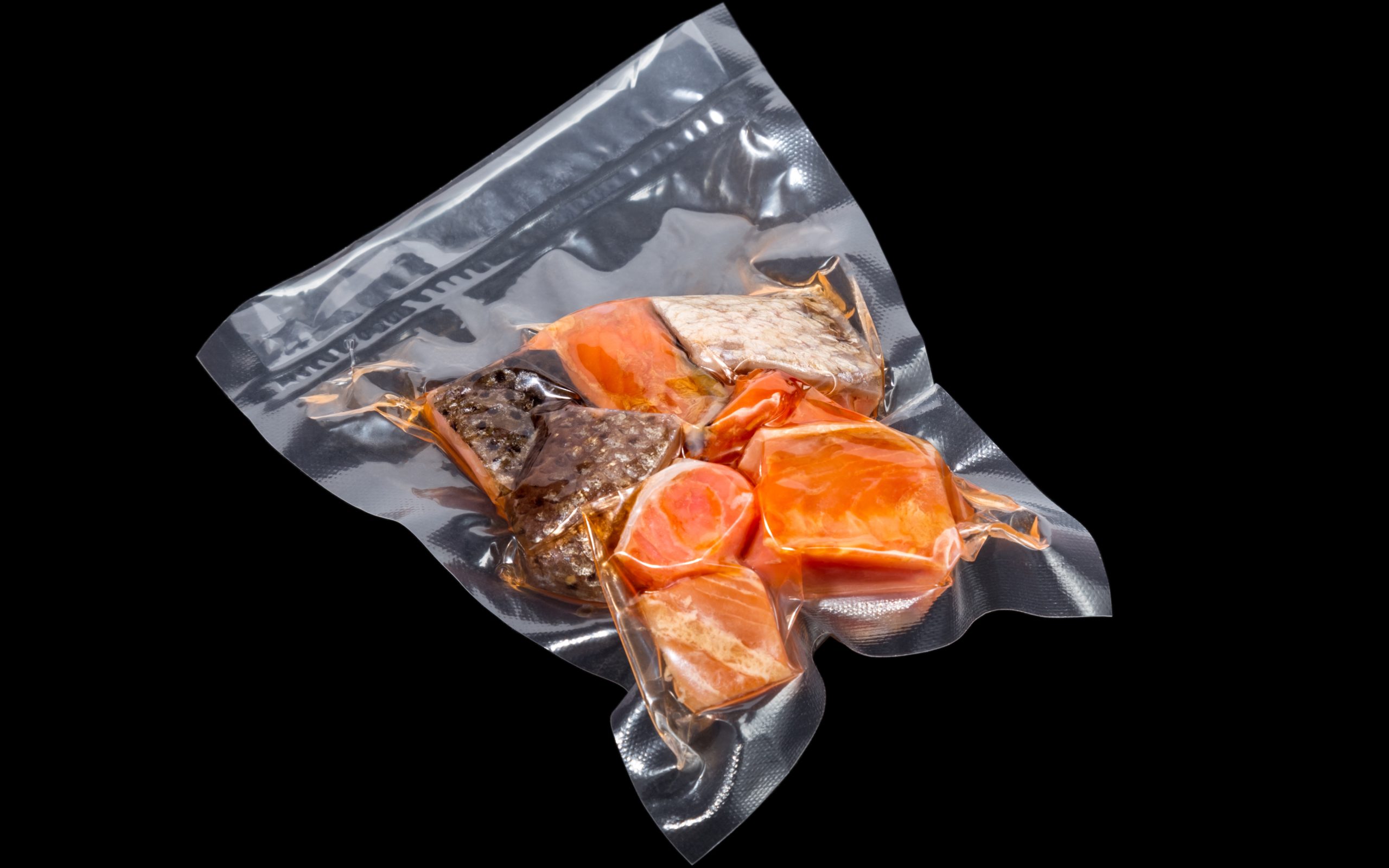
Tendances futures de l'ébavurage cryogénique
Innovation technologique continue
- Optimisation de la technologie de refroidissement
- Développer des moyens et des systèmes de refroidissement plus efficaces pour améliorer encore la vitesse et l'uniformité du refroidissement et réduire la consommation d'énergie. Par exemple, rechercher une nouvelle technologie d'injection d'azote liquide ou de mélange de gaz cryogéniques pour obtenir un contrôle plus précis de la température et un effet de refroidissement plus rapide.
- Explorer l'application d'autres sources de refroidissement cryogénique, telles que le dioxyde de carbone liquide ou l'azote cryogénique, pour répondre aux besoins de différents matériaux et processus.
- Amélioration des méthodes d'ébavurage
- Combiner les technologies avancées de vibration mécanique, d'ultrasons ou de laser pour améliorer l'efficacité et la précision de l'ébavurage. Par exemple, la vibration ultrasonique combinée au refroidissement cryogénique permet d'améliorer l'effet de fragilisation et de détachement des bavures ; ou l'ébavurage assisté par laser permet d'éliminer avec précision les bavures sur des pièces spécifiques.
- Développer des équipements d'ébavurage intelligents capables d'ajuster automatiquement les paramètres du processus en fonction du matériau, de la forme et de la taille de la pièce à usiner afin d'obtenir des solutions d'ébavurage personnalisées.
Extension du champ d'application
- Applications industrielles émergentes
- Avec le développement rapide des industries émergentes telles que les véhicules à énergie nouvelle, l'aérospatiale et l'information électronique, la demande de pièces de haute précision et de haute qualité augmente. La technologie d'ébavurage cryogénique sera de plus en plus utilisée dans ces domaines, tels que les composants des batteries des véhicules à énergie nouvelle, les pales des moteurs d'avion et l'emballage des puces électroniques.
- Dans les industries telles que les dispositifs médicaux et les instruments optiques, qui ont des exigences extrêmement élevées en matière de qualité de surface, la technologie d'ébavurage cryogénique jouera également un rôle important pour garantir la sécurité et la fiabilité des produits.
- Traitement des matériaux complexes
- Pour un nombre croissant de nouveaux matériaux composites, de nanomatériaux et de matériaux fonctionnels, les méthodes d'ébavurage traditionnelles ne peuvent souvent pas répondre aux exigences. La technologie de l'ébavurage cryogénique continuera d'élargir sa gamme de matériaux applicables, de développer des solutions d'ébavurage spéciales pour ces matériaux complexes et d'améliorer les performances de traitement et d'utilisation des matériaux.
Vert et durable
- Moyen de refroidissement respectueux de l'environnement
- Poursuivre la recherche et promouvoir l'application de moyens de refroidissement respectueux de l'environnement afin de réduire l'impact sur l'environnement. Par exemple, développer des réfrigérants cryogéniques biodégradables ou utiliser la technologie de refroidissement par circulation d'air pour réduire la dépendance à l'égard des moyens de refroidissement traditionnels tels que l'azote liquide.
- Renforcer le recyclage et la réutilisation des fluides de refroidissement, améliorer l'utilisation des ressources et réduire les coûts de production.
- Économie d'énergie et réduction des émissions
- Optimiser la consommation d'énergie du processus d'ébavurage cryogénique et atteindre l'objectif d'économie d'énergie et de réduction des émissions en améliorant la conception de l'équipement et l'efficacité de la conversion énergétique. Par exemple, utiliser des matériaux d'isolation efficaces pour réduire les pertes de chaleur, ou utiliser la technologie de récupération de la chaleur perdue pour réutiliser la chaleur générée pendant le processus d'ébavurage.
Développement en collaboration avec l'industrie
- Intégration de la chaîne industrielle en amont et en aval
- Le processus d'ébavurage cryogénique sera étroitement intégré aux industries en amont et en aval, telles que la recherche et le développement de matériaux, la fabrication d'équipements et le traitement des pièces, afin de former une chaîne industrielle de développement en collaboration. Grâce à la recherche et au développement conjoints et à l'innovation technologique, la compétitivité et la valeur ajoutée de l'ensemble de l'industrie seront améliorées.
- Renforcer la coopération avec les associations industrielles, les institutions de recherche scientifique et les entreprises concernées afin de promouvoir la normalisation et la standardisation du processus d'ébarbage cryogénique et de favoriser le développement sain et ordonné de l'industrie.
- Intégration intelligente de la fabrication
- Avec le développement continu de la technologie de fabrication intelligente, le processus d'ébarbage cryogénique sera profondément intégré à l'automatisation, à la numérisation et à la technologie intelligente. Il réalise des fonctions telles que le contrôle entièrement automatisé du processus de production, la surveillance et l'analyse des données en temps réel et le diagnostic des défauts à distance, et améliore l'efficacité de la production et la stabilité de la qualité.
- Utilisez les technologies de big data et d'intelligence artificielle pour optimiser et prévoir le processus d'ébavurage, découvrir à l'avance les problèmes potentiels et prendre les mesures correspondantes pour réduire les coûts de production et les risques.
À l'avenir, avec les progrès de la science et de la technologie et la croissance de la demande dans l'industrie manufacturière, la technologie de l'ébavurage cryogénique devrait jouer un rôle plus important dans un plus grand nombre de domaines. Elle permet non seulement d'améliorer la qualité du produit, mais aussi d'accroître l'efficacité de la production tout en garantissant la protection de l'environnement. Le développement de cette technologie aidera sans aucun doute l'industrie manufacturière à entrer dans une nouvelle ère de précision et d'efficacité accrues.
Filtres