Avantages des billes de sablage en céramique : Des raisons qui dépassent les supports de sablage traditionnels
30 août 2024
Comparaison après l'utilisation de billes de sablage en céramique
Depuis son invention à la fin du XIXe siècle, la technologie du sablage est devenue un processus crucial pour le traitement et le nettoyage des surfaces. Elle consiste à utiliser des médias à haute pression pour éliminer la saleté, la rouille ou polir la surface d'un matériau afin d'obtenir la finition souhaitée. Avec les progrès constants de la technologie industrielle, les types et les performances des médias de sablage ont également évolué. Dans l'industrie moderne en particulier, le choix du bon produit de sablage est crucial pour améliorer l'efficacité de la production et la qualité du produit final. Ces dernières années, les billes de céramique se sont imposées comme l'un des meilleurs produits de sablage en raison de leurs performances exceptionnelles. Pourquoi les billes de céramique se distinguent-elles et deviennent-elles le choix préféré de nombreuses industries ? Pour répondre à cette question, nous devons analyser les avantages et les inconvénients des différents supports de sablage traditionnels sous différents angles et explorer les avantages uniques des billes de céramique.
Introduction aux moyens de sablage traditionnels
Sable de quartz
Le sable quartzeux a été l'un des premiers abrasifs largement utilisés pour le nettoyage et le ponçage des surfaces métalliques. Ses principaux avantages sont son faible coût et l'abondance de ses ressources, mais ses performances irrégulières ont conduit de nombreux utilisateurs industriels à passer à des produits de sablage plus performants. Les inconvénients du sable de quartz sont les suivants
- Dureté plus faible, ce qui le rend moins efficace pour le traitement des matériaux durs. La forme irrégulière des particules peut entraîner des effets de traitement de surface incohérents.
- La production de poussière est importante pendant l'utilisation, ce qui entraîne un environnement de travail difficile et des risques pour la santé des travailleurs.
- Taux de consommation élevé et durée de vie courte, ce qui augmente les coûts au fil du temps.
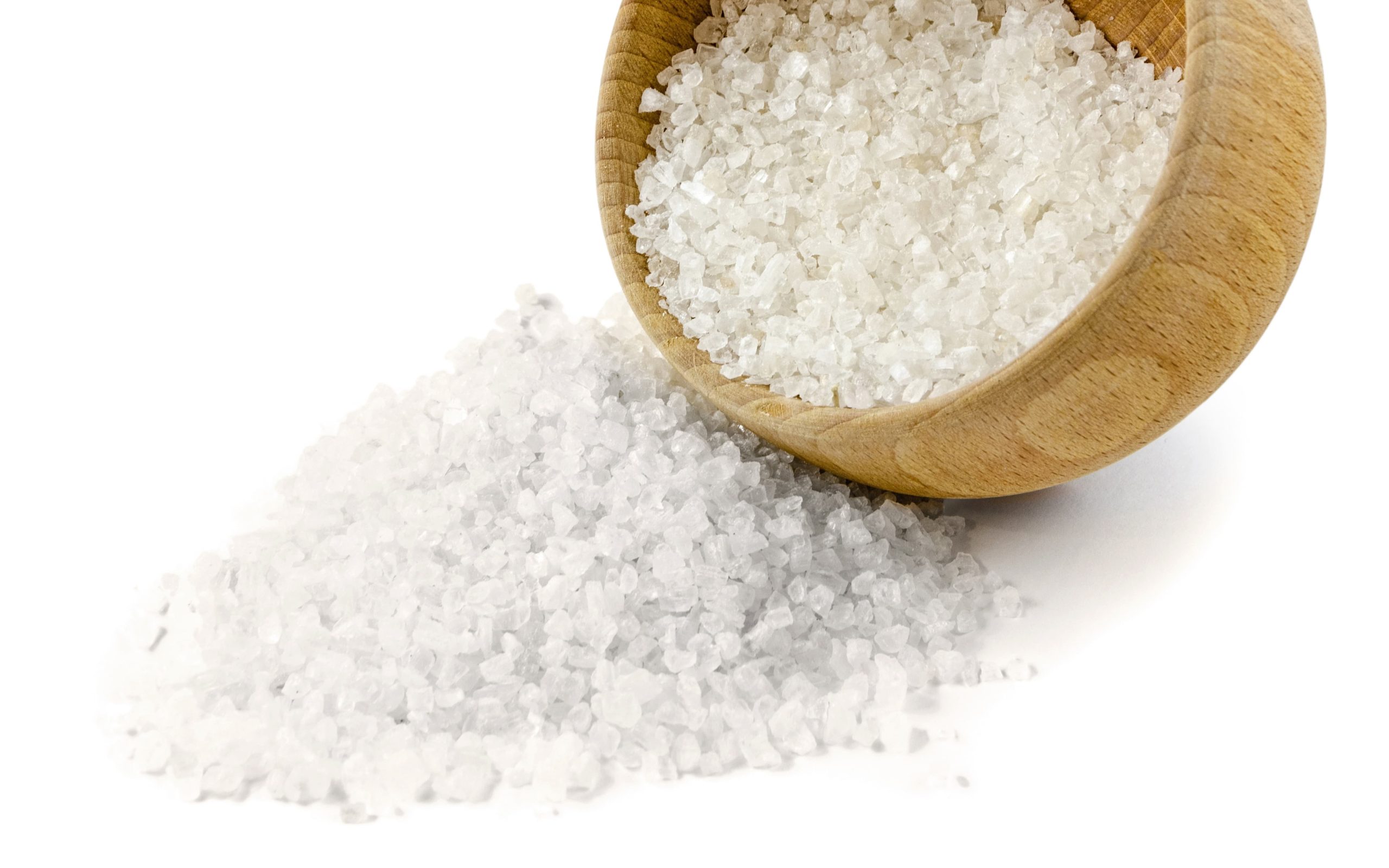
Sable de quartz
Grenaille d'acier
La grenaille d'acier, d'une dureté plus élevée, est généralement utilisée pour des scénarios de ponçage exigeants, en particulier pour éliminer la rouille et les revêtements tenaces. Ses principaux avantages sont sa grande dureté, sa réutilisation et ses excellentes performances sur de grandes surfaces. Cependant, ses inconvénients sont l'usure importante de l'équipement, les besoins fréquents de maintenance et le risque d'endommager des pièces délicates en raison de son poids.
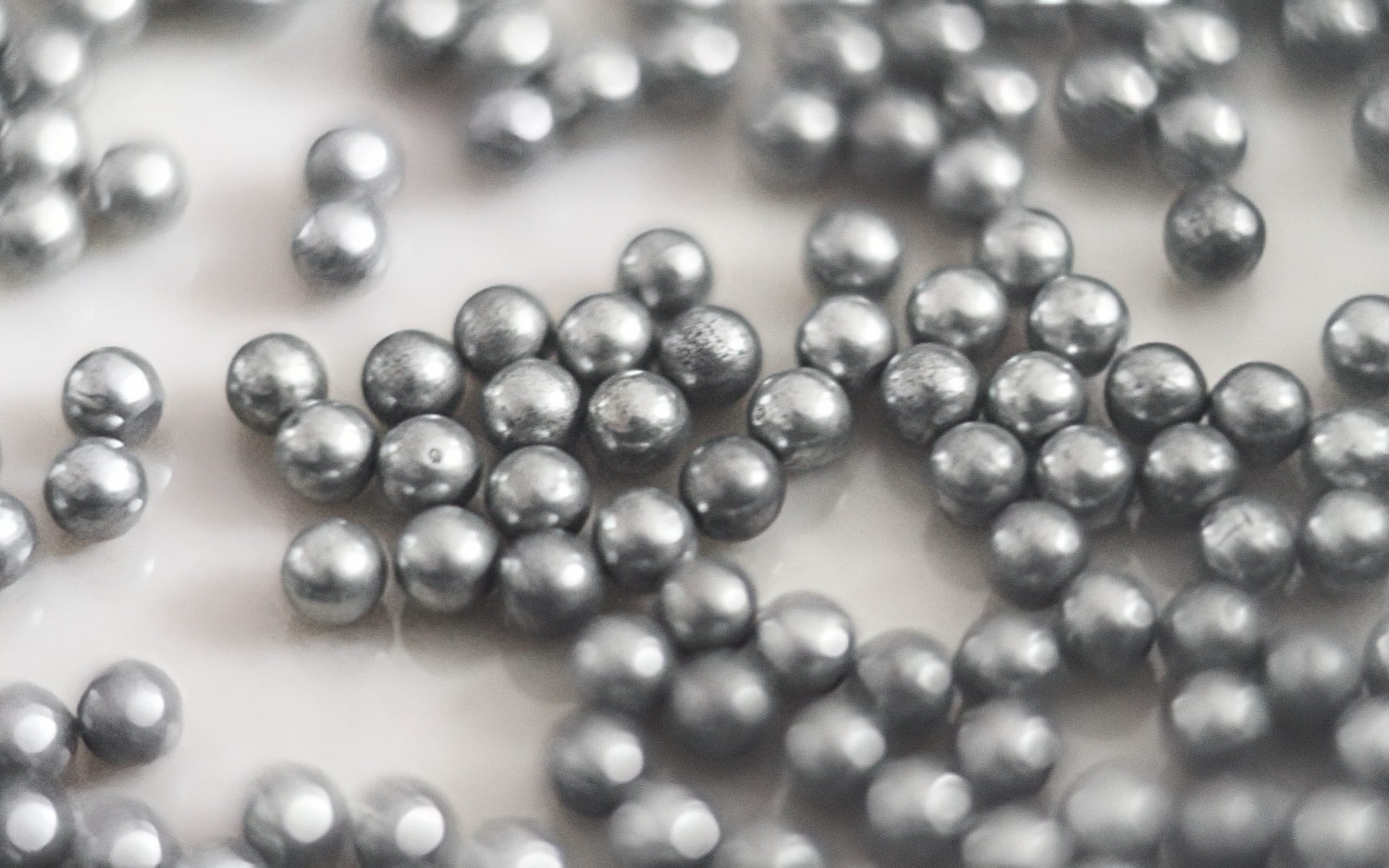
Grenaille d'acier
Perles de verre
Les billes de verre, un produit de sablage relativement doux, sont utilisées pour les applications nécessitant une grande précision, comme dans l'aérospatiale et l'électronique. Elles présentent l'avantage d'assurer un traitement de surface uniforme et de réduire le risque de rayer le matériau de base. Toutefois, leur faible dureté (dureté de Mohs de 5) et leur durabilité les rendent moins efficaces pour éliminer les contaminants tenaces et elles sont susceptibles de se casser, ce qui entraîne une augmentation des coûts due à des remplacements fréquents.
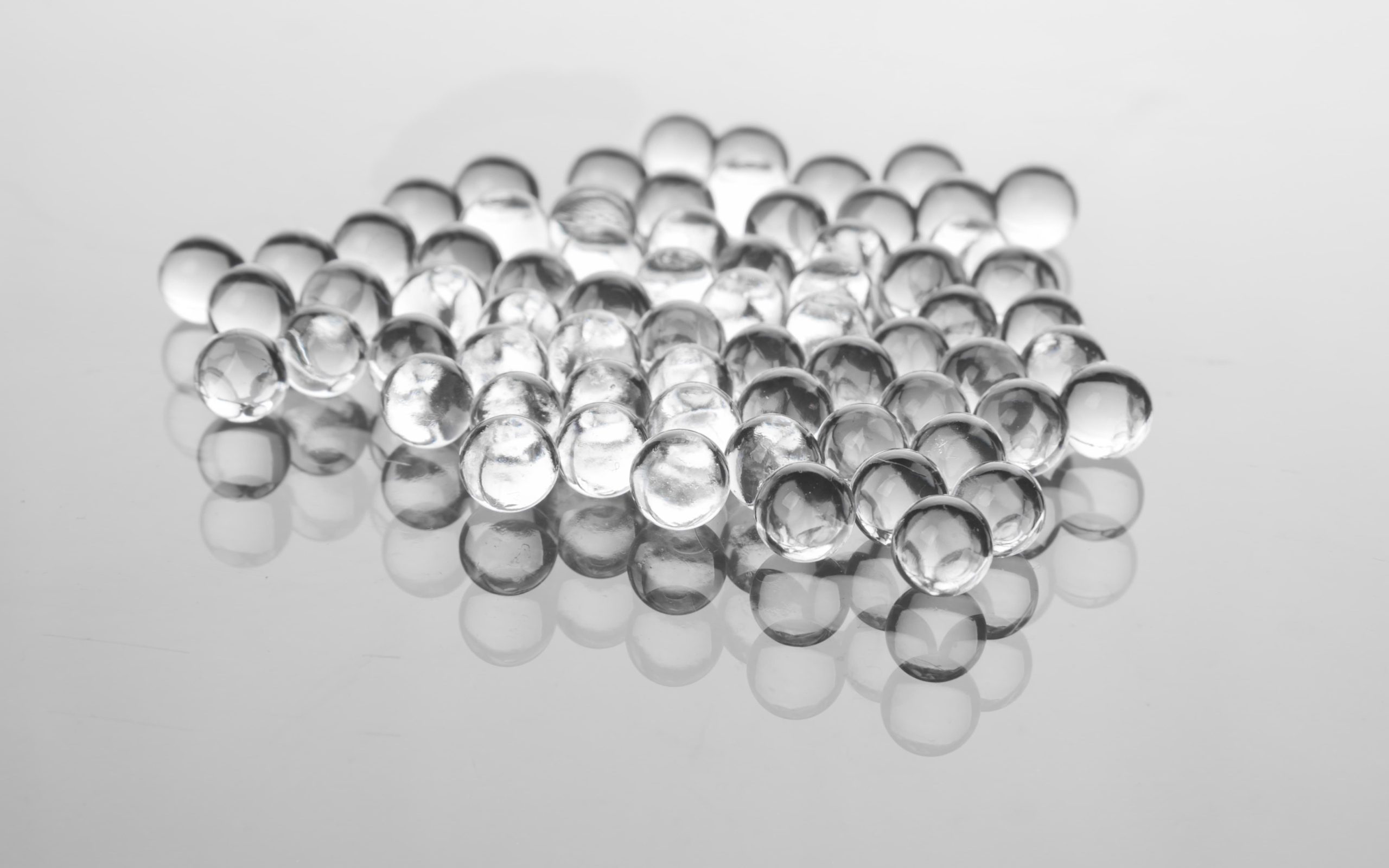
Perles de verre
Supports de sablage en oxyde d'aluminium
Comparé aux trois premiers médias, le grenaille d'oxyde d'aluminium excelle en termes de performances globales. Il est apprécié pour sa grande dureté et son excellente résistance à l'usure, et convient à divers traitements de surface, y compris l'ébavurage et le nettoyage. Toutefois, son coût plus élevé le rend moins compétitif pour certaines applications sensibles aux coûts, et ses billes acérées peuvent endommager les matériaux plus tendres.
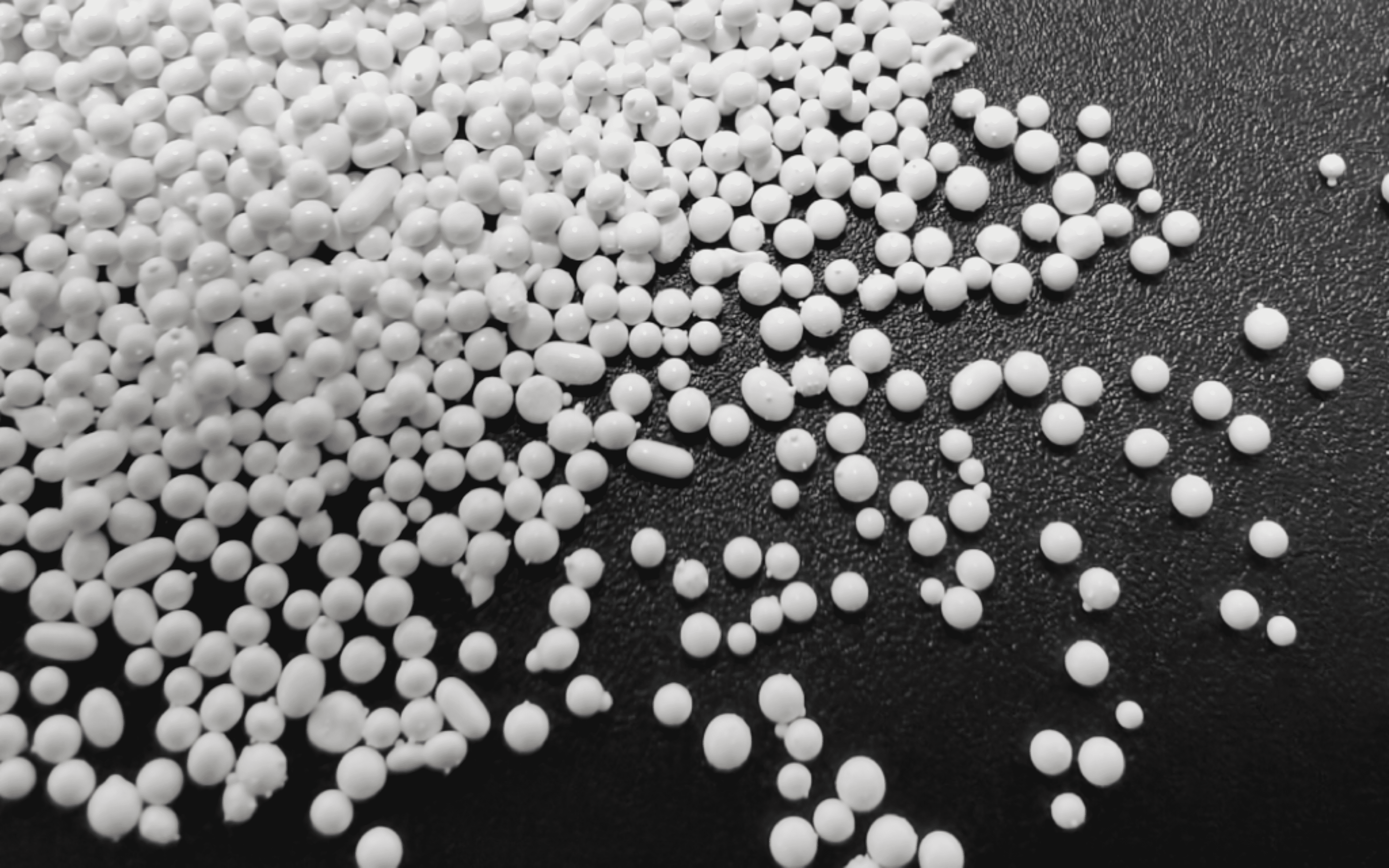
Supports de sablage en oxyde d'aluminium
Perles en plastique
Les billes de plastique, un type plus récent de support de sablage, sont utilisées pour des traitements de surface en douceur sur des matériaux tels que le bois et certains non-métaux. Leur principal avantage est de ne pas endommager la surface de la pièce, ce qui les rend adaptées aux matériaux délicats. Toutefois, leur faible dureté ne permet pas d'éliminer les contaminants plus coriaces ou de procéder à un ponçage en profondeur. En outre, les billes de plastique peuvent se déformer et se dégrader, ce qui réduit leur durée de vie et augmente les coûts d'exploitation.
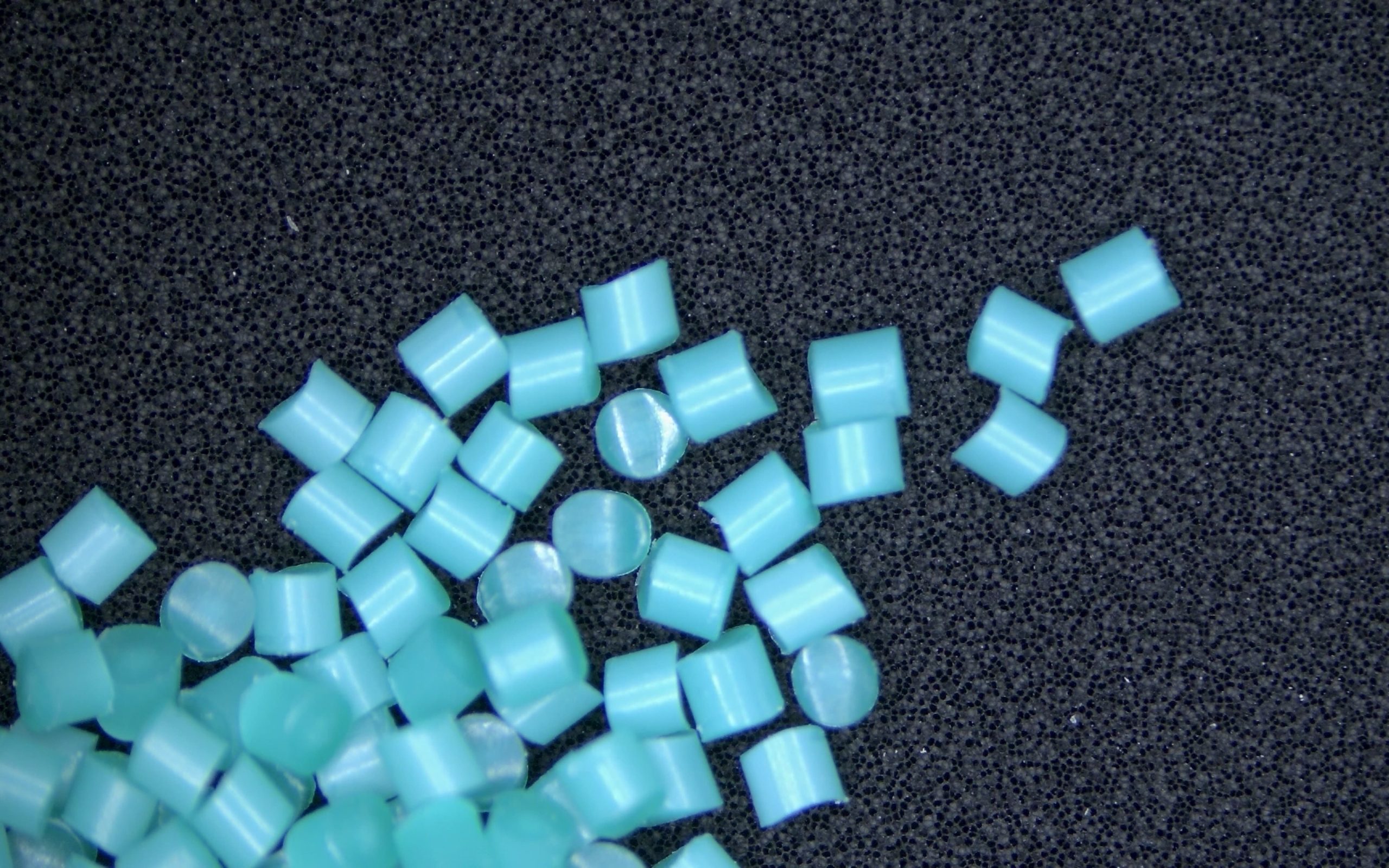
Perles en plastique
Avantages des billes de sablage céramique
- Dureté et durabilité élevées
Les billes de sablage en céramique, fabriquées à partir de zircone et de silice, présentent une dureté nettement supérieure à celle du sable de quartz, des billes de verre et des billes en plastique. Ce média traite efficacement les matériaux très résistants et conserve une longue durée de vie, ce qui réduit les remplacements fréquents. La durabilité des billes de céramique réduit considérablement les coûts d'exploitation et l'usure des équipements.
- Traitement de surface uniforme
Les billes de grenaillage en céramique permettent un traitement de surface stable et cohérent grâce à leur surface uniforme et tranchante. Cette régularité est cruciale pour les applications exigeant une grande précision, comme le traitement du verre des écrans tactiles. Les billes en céramique garantissent que chaque point de traitement produit l'effet désiré, évitant ainsi les défauts de surface causés par les médias traditionnels.
- Inertie chimique et non polluant
Les billes de grenaillage en céramique présentent une excellente inertie chimique, ce qui signifie qu'elles ne réagissent pas avec les matériaux traités et ne libèrent pas de substances nocives, ce qui les rend adaptées au traitement des matériaux sensibles aux réactions chimiques. Par rapport à certains supports traditionnels, les billes de grenaillage en céramique sont plus respectueuses de l'environnement et ne provoquent pas de pollution secondaire, ce qui les rend idéales pour les industries ayant des exigences élevées en matière de protection de l'environnement.
- Adaptabilité à divers environnements complexes
Les billes de grenaillage en céramique fonctionnent bien dans des environnements complexes, qu'il s'agisse de températures élevées, de températures basses ou de conditions d'humidité élevée. Cette adaptabilité les rend largement utilisées dans les industries ayant des exigences environnementales strictes, telles que l'aérospatiale et l'armée.
- Des avantages à long terme rentables
Bien que l'investissement initial dans les billes de grenaillage en céramique puisse être plus élevé, il permet de réaliser des économies significatives à long terme. Leur durabilité et leur efficacité réduisent la fréquence de remplacement et la durée d'utilisation, ce qui diminue les coûts d'exploitation globaux. En outre, les billes de sablage en céramique provoquent une usure minimale de l'équipement, ce qui prolonge sa durée de vie et réduit encore les coûts d'entretien.
Analyse comparative entre les supports céramiques et les supports traditionnels
- Durabilité et durée de vie
Par rapport au sable de quartz, aux billes de verre et aux billes de plastique, les billes de grenaillage en céramique ont une durée de vie plus longue. Les médias traditionnels tels que le sable de quartz et les billes de verre peuvent se casser ou s'user en cours d'utilisation, ce qui entraîne des remplacements fréquents. Grâce à leur grande dureté et à leur résistance à la rupture, les billes de grenaille céramique réduisent considérablement la fréquence de remplacement, ce qui permet de réduire les coûts des matériaux et de minimiser les temps d'arrêt.
- Traitement de surface Précision
La taille et la forme uniformes des billes de grenaille céramique garantissent un traitement de surface précis. En revanche, la taille inégale des particules de grenaille d'acier peut entraîner des effets de surface incohérents et des rayures potentielles. Bien que les billes de verre permettent un traitement de surface fin, leur dureté plus faible ne permet pas d'atteindre la précision des billes de grenaille de céramique.
- Impact sur les matériaux
Les billes de grenaille céramique ont un impact plus doux sur les surfaces des pièces, évitant les dommages par rapport aux médias traditionnels comme la grenaille d'acier. La conception des billes en céramique minimise l'impact pendant le traitement de surface, préservant ainsi l'intégrité et la précision de la pièce, ce qui est crucial pour la manipulation d'appareils de précision ou de produits nécessitant une surface très lisse.
- Considérations environnementales et de sécurité
Les médias traditionnels tels que le sable de quartz et la grenaille d'acier génèrent une quantité importante de poussière et de polluants, ce qui a un impact sur la santé des travailleurs et la sécurité de l'environnement. Les billes de grenaillage en céramique, avec leur faible teneur en poussière et leurs propriétés non toxiques, réduisent considérablement la pollution de l'environnement et les risques pour la santé, ce qui répond aux exigences de l'industrie moderne en matière de normes environnementales et de sécurité.
- Rapport coût-efficacité
Les avantages des billes de grenaille céramique en termes de durabilité, d'efficacité et de faible usure de l'équipement permettent de réaliser des économies significatives dans le cadre d'une utilisation à long terme. Par rapport au remplacement fréquent des médias traditionnels et aux interruptions de fonctionnement qui en découlent, les billes de grenaille céramique offrent une solution économiquement plus viable pour les entreprises, améliorant ainsi l'efficacité globale de la production.
Point de vue de l'utilisateur : Considérations sur les applications pratiques
- Qualité et efficacité
Les billes de grenaillage en céramique permettent un traitement de surface de haute qualité, réduisant les défauts et les incohérences dans le processus. Pour les industries exigeant une précision et une efficacité élevées, telles que la production de verre pour écrans tactiles, les billes en céramique excellent. Leur dureté et leur traitement uniforme garantissent que les produits finis répondent à des normes strictes.
- Durabilité et impact environnemental
Les caractéristiques écologiques des billes de grenaillage en céramique les rendent de plus en plus populaires dans les industries modernes. Leur nature non polluante et chimiquement inerte en fait un choix idéal dans le cadre des politiques de durabilité et d'environnement. Les produits de sablage traditionnels peuvent avoir un impact négatif sur l'environnement et la santé des opérateurs, ce qui nécessite des mesures supplémentaires en matière de protection de l'environnement et de sécurité.
- Comparaison des coûts et des avantages
Bien que les billes de grenaillage en céramique impliquent des coûts initiaux plus élevés, leurs avantages à long terme dépassent ceux des médias traditionnels. Leur longue durée de vie et leurs faibles exigences en matière d'entretien réduisent considérablement les coûts totaux. Pour les entreprises qui effectuent fréquemment des opérations de sablage, les billes de céramique constituent une solution plus rentable.
- Polyvalence et adaptabilité
La polyvalence et l'adaptabilité des billes de grenaillage en céramique garantissent d'excellentes performances dans diverses applications. Que ce soit dans l'aérospatiale, l'armée ou l'automobile, les billes de céramique assurent un traitement de surface stable et cohérent, offrant ainsi un large potentiel d'utilisation pour différents besoins.
- Compatibilité des équipements
- Machines de sablage à air comprimé
Compatibilité: Les billes de sablage en céramique sont généralement compatibles avec la plupart des machines de sablage à air comprimé. Ces appareils utilisent de l'air comprimé pour projeter l'agent de sablage sur la surface de la pièce. La dureté élevée et la forme uniforme des particules des billes de sablage en céramique leur permettent de bien fonctionner dans ce type d'équipement.
Considérations: Assurez-vous que les buses et les autres composants de la sableuse peuvent résister à la dureté élevée des billes de céramique. Des billes plus dures peuvent accélérer l'usure des buses, c'est pourquoi il est recommandé de les inspecter et de les remplacer régulièrement.
- Machines de sablage centrifuge
Compatibilité: Les machines de sablage centrifuge utilisent la force centrifuge pour projeter l'agent de sablage sur la pièce. Les billes de sablage en céramique, en raison de leur densité et de leur dureté élevées, s'adaptent bien aux exigences de ce type d'équipement.
Considérations: La forme et la taille des billes de céramique doivent correspondre aux exigences de conception de l'équipement. Veiller à ce que les billes ne provoquent pas une usure excessive des parois intérieures de l'équipement.
- Machines de sablage à jet de sable
Compatibilité: Les machines de sablage à roue utilisent des roues tournant à grande vitesse pour projeter l'agent de sablage sur la surface de la pièce. Les billes de sablage en céramique peuvent fournir un effet de traitement de surface uniforme dans ce type d'équipement.
Considérations: La dureté plus élevée des billes de céramique peut provoquer l'usure des roues et des garnitures de la sableuse à jet de sable, c'est pourquoi il convient d'utiliser des matériaux résistants à l'usure pour fabriquer ces composants.
Points de vue des experts de l'industrie
Les billes de grenaillage en céramique ont attiré l'attention de nombreux experts de l'industrie en raison de leurs performances et de leurs possibilités d'application supérieures. Selon le Dr. Emily Green, experte en revêtements et en traitement de surface, "La dureté élevée et l'uniformité des billes de grenaillage en céramique les rendent particulièrement remarquables dans les applications aérospatiales. Leur résistance à l'usure réduit la fréquence des entretiens, ce qui diminue les coûts à long terme."1 Cela reflète les avantages des billes de céramique dans les traitements de haute précision et de grande douceur de surface.
Un autre expert, l'ingénieur en mécanique John Smith, ne tarit pas d'éloges sur les billes de grenaillage en céramique, soulignant leur supériorité dans des applications industrielles spécifiques. Il note, "L'inertie chimique des billes de grenaillage en céramique est l'un de leurs plus grands avantages. Elles ne réagissent pas avec les matériaux traités, ce qui les rend idéales pour l'industrie alimentaire et pharmaceutique. En outre, leur excellente adaptabilité à l'environnement signifie qu'elles conservent des performances stables dans des conditions extrêmes."2
Jones et Robinson, qui examinent les avantages économiques des billes de grenaillage en céramique, soulignent, "Bien que le coût initial des billes de grenaillage en céramique soit plus élevé, leur durabilité et la réduction des coûts d'entretien se traduisent par des avantages économiques dans le cadre d'une utilisation à long terme. 3Ils discutent également de la nécessité d'utiliser des billes spécialement traitées dans des environnements extrêmes pour garantir des performances stables.
souligne Zhang, "Grâce à leur inertie chimique et à leur résistance à l'usure, les billes de grenaillage en céramique pèsent moins sur l'environnement. Ces billes ne libèrent pas de substances nocives et, en raison de leur durabilité, réduisent la production de déchets, ce qui témoigne d'une bonne performance en matière de développement durable."4
Roberts fait état des réactions des utilisateurs, "Les utilisateurs trouvent que les billes de grenaillage en céramique améliorent considérablement l'efficacité du traitement et la qualité du produit. Toutefois, certains ont rencontré des problèmes d'usure des particules dans des conditions extrêmes. Il est recommandé de choisir des billes de céramique spécialement traitées pour de telles applications et d'effectuer un entretien régulier de l'équipement".5
Les experts reconnaissent également les défis techniques liés à l'utilisation de billes de grenaillage en céramique. Par exemple, Lee discute, "Dans le cadre d'opérations à haute intensité et à haute pression, les billes de sablage en céramique peuvent provoquer l'usure de l'équipement. Les solutions efficaces consistent à optimiser les paramètres de sablage et à sélectionner des composants d'équipement très résistants à l'usure".6
En outre, les progrès de la technologie de production ont considérablement amélioré l'uniformité des billes de grenaille céramique, ce qui est essentiel pour améliorer les effets du traitement et réduire les déchets. M. Green ajoute : "Grâce aux progrès technologiques, la précision et l'uniformité de la production de billes de grenaillage en céramique se sont considérablement améliorées, ce qui les rend plus compétitives dans les applications haut de gamme."
En conclusion, les billes de sablage en céramique se distinguent des autres produits de sablage par leurs avantages significatifs dans plusieurs domaines clés. À l'avenir, avec les progrès technologiques et l'augmentation de la demande du marché pour des produits de sablage performants et respectueux de l'environnement, les billes de sablage en céramique devraient trouver davantage d'applications, ce qui orientera la technologie du sablage vers des directions plus efficaces et durables. L'innovation technologique et l'optimisation continues amélioreront encore leurs performances et leur applicabilité, ce qui en fera un choix indispensable pour les industries qui cherchent à améliorer la qualité et l'efficacité du traitement de surface.
Références:
- Green, E. (2022). Traitements de surface avancés pour les applications aérospatiales. Journal of Materials Processing Technology, 302, 120-135.
- Smith, J. (2023). Innovations dans le domaine du sablage abrasif : Une revue. Surface and Coatings Technology, 451, 187-203.
- Jones, A. et Robinson, L. (2024). Questions et solutions pratiques dans les opérations de sablage abrasif. Industrial Maintenance & Plant Operation, 58(2), 45-60.
- Zhang, Q. (2024). Impact environnemental et durabilité des matériaux abrasifs. Journal of Cleaner Production, 314, 142-156.
- Roberts, K. (2023). Expériences des utilisateurs avec les abrasifs Advanced Sand. Industrial Equipment Review, 29(3), 123-135.
- Lee, H. (2024). Les défis du grenaillage à haute performance. International Journal of Surface Engineering, 47(1), 56-69.
Filtres