Wie gehen Zirkoniumdioxidperlen mit Oberflächenfehlern von Glasprodukten um?
4. September 2024
Auf dem heutigen Markt für Heimdekoration und Kunst sind mundgeblasene Glasprodukte mit ihrer einzigartigen Handwerkskunst, ihrer zarten Textur und ihrem individuellen Design zu einem Highlight der modernen Heimdekoration geworden und erfreuen sich wachsender Beliebtheit bei den Verbrauchern. Diese Art von Glasprodukten spiegelt nicht nur die exquisiten Fähigkeiten der Handwerker wider, sondern beinhaltet auch eine Vielzahl von künstlerischen Stilen, die jedes Produkt zu einem einzigartigen Kunstwerk machen. Die Werke von Künstlern wie Matsuto Koichi und Reto ZÜND beispielsweise haben nicht nur ein exquisites und elegantes Aussehen, sondern regen die Menschen auch zum Nachdenken über die Natur, die Ästhetik, die Zukunft, soziale Beziehungen und andere Dinge an.
Trotz der unvergleichlichen Schönheit und des künstlerischen Wertes mundgeblasener Glaserzeugnisse werden ihre Oberflächen jedoch häufig einer komplexen Bearbeitung unterzogen. Während des Herstellungsprozesses kann sich feiner Schmutz auf der Glasoberfläche ansammeln oder eine ungleichmäßige Oxidschicht bilden, was nicht nur das Aussehen des Produkts beeinträchtigt, sondern auch seine Lebensdauer und Qualität beeinträchtigen kann. Um zu gewährleisten, dass jedes mundgeblasene Glasprodukt die beste optische Wirkung und das beste Finish erzielt, ist es daher besonders wichtig, eine fortschrittliche Oberflächenbehandlungstechnologie einzusetzen.
Unter den zahlreichen Technologien zur Oberflächenbehandlung haben sich Zirkoniumdioxid-Perlen aufgrund ihrer hervorragenden Leistung zu einer idealen Wahl für handgefertigte Glasprodukte entwickelt. Mit diesem Medium lassen sich feine Schmutz- und Oxidschichten gut entfernen. Sie können Glasoberflächendefekte wirksam reinigen und dabei den ursprünglichen Glanz und die Textur des Glases erhalten. Als Nächstes werde ich die Anwendung von Zirkonoxidkugeln bei der Oberflächenbehandlung von mundgeblasenen Glaswaren im Detail besprechen und analysieren, wie sie die Qualität und den visuellen Effekt von Glasprodukten verbessern können. Ich werde auch die Verwendungsmöglichkeiten und Vorteile von Zirkoniumdioxidperlen in verschiedenen Größen auflisten, um Ihnen zu helfen, diese besser zu verstehen und auszuwählen.
Der Herstellungsprozess von mundgeblasenen Glaswaren umfasst in der Regel zunächst die folgenden Schritte:
- Glasschmelze vorbereiten: Rohstoffe (wie Quarzsand, Natriumcarbonat, Kalkstein usw.) in einem Hochtemperaturofen zu einer Glasschmelze schmelzen.
- Blasen: Das Personal nimmt das geschmolzene Glas mit einer Blasrohrflöte auf und bläst es in Form. Bei diesem Verfahren muss die Glasbläserpfeife ständig gedreht werden, damit sich das Glas gleichmäßig ausdehnt.
- Vorläufige Formgebung: Mit handwerklichem Geschick bläst der Handwerker das Glas in eine grobe Form. Die in diesem Stadium geformten Werke sind oft grob und müssen nachbearbeitet werden.
- Abkühlung: Das geformte Glas wird allmählich abgekühlt, um Risse zu vermeiden, die durch zu schnelles Abkühlen entstehen.
- Oberflächenbehandlung:In diesem Schritt kann die Glasoberfläche mit Zirkoniumdioxid-Strahlperlen behandelt werden. Durch Sandstrahlen werden feine Verschmutzungen, Oxidschichten oder Unebenheiten auf der Glasoberfläche entfernt, wodurch die Oberfläche und der optische Effekt verbessert werden. Durch die Einstellung von Parametern wie der Größe der Sandstrahlpartikel und des Sandstrahldrucks können verschiedene Oberflächeneffekte erzielt werden, z. B. eine glatte Oberfläche oder ein mattierter Effekt.
- Detaildekoration: Weitere Dekoration oder Feinbearbeitung von Glaswaren, wie Schleifen, Gravieren usw.
- Endgültige Abkühlung und Prüfung: Die behandelten Glaswaren werden schließlich abgekühlt, auf Mängel geprüft und verpackt.
Sandstrahlen spielt bei der Glasherstellung vor allem in der Phase der Oberflächenbehandlung eine Rolle, da die Oberfläche von handgefertigten Produkten nicht so gleichmäßig ist wie die von maschinell hergestellten Produkten. Das Sandstrahlen erzeugt durch Hochgeschwindigkeitsspritzen Reibung auf der Glasoberfläche, entfernt Schmutz, Oxidschichten und andere Defekte auf der Oberfläche, macht die Oberfläche glatter und gleichmäßiger und trägt zur Verbesserung des Aussehens und der Textur des Endprodukts bei. Dieses Verfahren ist besonders wichtig für mundgeblasene Glaswaren.
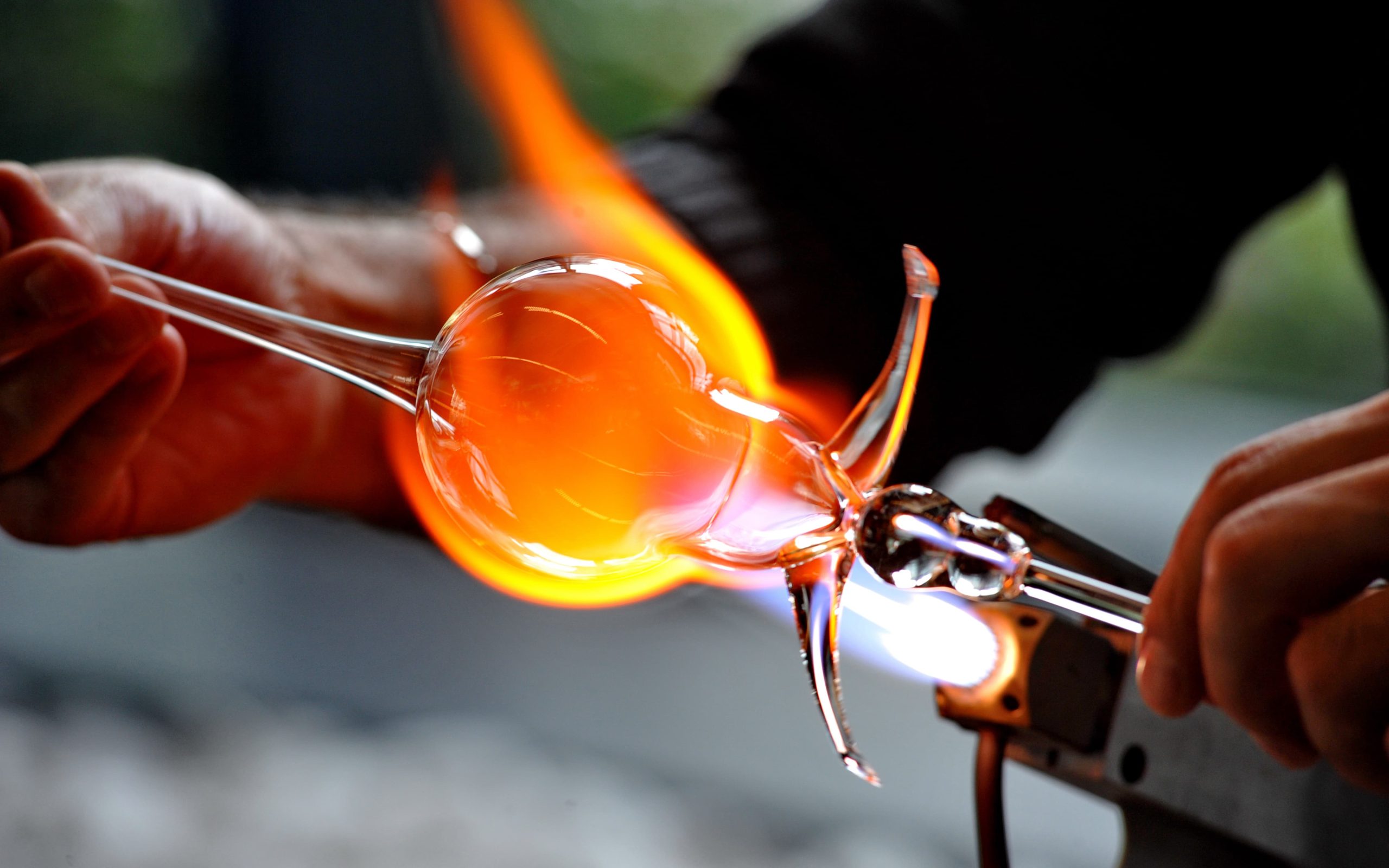
Brennvorgang
Warum Zirkoniumdioxid-Strahlperlen?
Im Vergleich zu anderen Sandstrahlmitteln haben Zirkoniumdioxid-Strahlkugeln große Vorteile. Spezifische Untersuchungen finden Sie in dem von Smith, L. et al. verfassten Papier: "Abrasives Strahlen von Glasoberflächen: Eine experimentelle Studie". In dieser Studie werden die Auswirkungen verschiedener Sandstrahlpartikel auf die Behandlung von Glasoberflächen, einschließlich Zirkoniumdioxid-Strahlkugeln, untersucht. Der Artikel enthält detaillierte experimentelle Daten und vergleichende Analysen, die Ihnen helfen, die Leistung verschiedener Sandstrahlmittel bei der Behandlung von Glasoberflächen zu verstehen.
Im Folgenden werden die grundlegenden Eigenschaften von Zirkoniumdioxid-Strahlkugeln beschrieben:
- Ausgezeichnete Verschleißfestigkeit: Zirkoniumdioxid-Strahlmittel werden aus hochreinem, sehr verschleißfestem Zirkoniumoxid hergestellt und haben eine sehr hohe Verschleißfestigkeit. Dies ermöglicht eine lange Lebensdauer während des Behandlungsprozesses und reduziert die Notwendigkeit, Sandstrahlmittel häufig zu ersetzen.
- Effiziente Reinigungsfähigkeit: Zirkoniumdioxid-Strahlperlen haben eine hohe Härte und können feine Schmutz- und Oxidschichten auf der Glasoberfläche wirksam entfernen, ohne den Glaskörper zu beschädigen, was für die Qualitätskontrolle hochwertiger handgefertigter Glasprodukte von entscheidender Bedeutung ist.
- Gleichmäßige Sprengwirkung: Da Zirkoniumdioxid-Strahlkugeln einheitliche Partikel und eine stabile Größe haben, können sie eine gleichmäßige Strahlwirkung erzielen und die Glätte und das Aussehen der behandelten Oberfläche gewährleisten.
- Verringerung der Sekundärverschmutzung: Zirkoniumdioxid-Strahlperlen hinterlassen keine Verunreinigungen auf der behandelten Oberfläche, was besonders wichtig ist, um die Reinheit und hohe Transparenz von Glasprodukten zu erhalten, vor allem bei Anwendungen, bei denen hohe optische Effekte erforderlich sind.
Unsere Zirkonia-Strahlperlen sind in 5 Größen erhältlich (Produktinformation herunterladen)entsprechend den verschiedenen Verwendungszwecken. Aufgrund seiner einzigartigen Leistungsvorteile und Behandlungsanforderungen ist YZ150 (150-200 Mikrometer) die am besten geeignete Partikelgröße für die Oberflächenbehandlung von Glas. Im Folgenden wird näher erläutert, warum diese spezielle Partikelgröße ausgewählt wurde.
Vorteile der YZ150
- Mäßige Partikelgröße: Feine Partikel von 150-200 Mikrometern können feinen Schmutz aufnehmen und eignen sich für hochpräzise Anwendungen. Zu große Partikel verursachen eine raue Oberfläche, während zu kleine Partikel den Schmutz möglicherweise nicht wirksam entfernen. Diese Größe kann einen gleichmäßigen Strahlungseffekt erzielen, der Schmutz entfernt und gleichzeitig eine glatte Oberfläche erhält.
- Entfernt wirkungsvoll feinen Schmutz: Bei handgefertigten Glasprodukten sind feine Fehler oft hartnäckig. YZ150 verfügt über eine ausreichende Abtragskapazität, ohne die Glasoberfläche übermäßig zu verschleißen oder zu beschädigen, und ist daher ideal für die Behandlung solcher subtilen Probleme.
- Verbesserung der Oberflächengüte: Mit dem YZ150 lassen sich feine Sandstrahleffekte erzielen, die zur Verbesserung der Oberfläche und Transparenz von Glasprodukten beitragen. Durch die präzise Steuerung des Sandstrahlprozesses können Sie sicherstellen, dass die Glasoberfläche den besten visuellen Effekt und Glanz erzielt.
- Optimieren Sie Sandstrahlarbeiten: Durch die ausgezeichnete Verschleißfestigkeit und chemische Stabilität können die Strahlzeit und der Verschleiß während des Sandstrahlprozesses effektiv reduziert werden, wodurch der Betrieb effizienter wird und die Lebensdauer der Sandstrahlanlage verlängert wird, was für die Verbesserung der Produktionseffizienz und die Senkung der Verarbeitungskosten von großer Bedeutung ist.
Zusammenfassend lässt sich sagen, dass Zirkoniumdioxid-Strahlmittel aufgrund ihrer hervorragenden Verschleißfestigkeit, ihrer effizienten Reinigungsfähigkeit, ihrer gleichmäßigen Sandstrahlwirkung und ihrer geringeren Sekundärverschmutzung ideal für die Bearbeitung von mundgeblasenen Glaswaren geeignet sind. Die Partikelgröße von YZ150 (150-200 Mikrometer) bietet einzigartige Vorteile bei der effektiven Entfernung von Feinschmutz, der Verbesserung der Oberflächengüte und der Optimierung von Sandstrahlarbeiten.
Anwendung und Vorteile der verschiedenen Größen
YZ300 (250-300 Mikrometer)
- Anmeldung: Geeignet für die Grobbearbeitung großer Werkstücke und Konstruktionsteile, z. B. im Brücken- und Schiffsbau.
- Vorteile:
- Entfernt effizient große Flächen von Oxidationsrückständen und Rost.
- Geeignet für große Reinigungsarbeiten und zur Verbesserung der Reinigungseffizienz.
- Bildet eine grobe Oberflächenrauhigkeit, die eine gute Haftung für nachfolgende Beschichtungen gewährleistet.
- Fallstudie: Die Florence Steel Company in den Vereinigten Staaten verwendet Zirkoniumdioxid-Perlen der Größe YZ300 zur Behandlung großer Stahlteile, um Rost und Oxidhaut zu entfernen. Dadurch wird die Oberflächenqualität der Bauteile verbessert und eine gute Haftung für nachfolgende Beschichtungen erzielt. 1
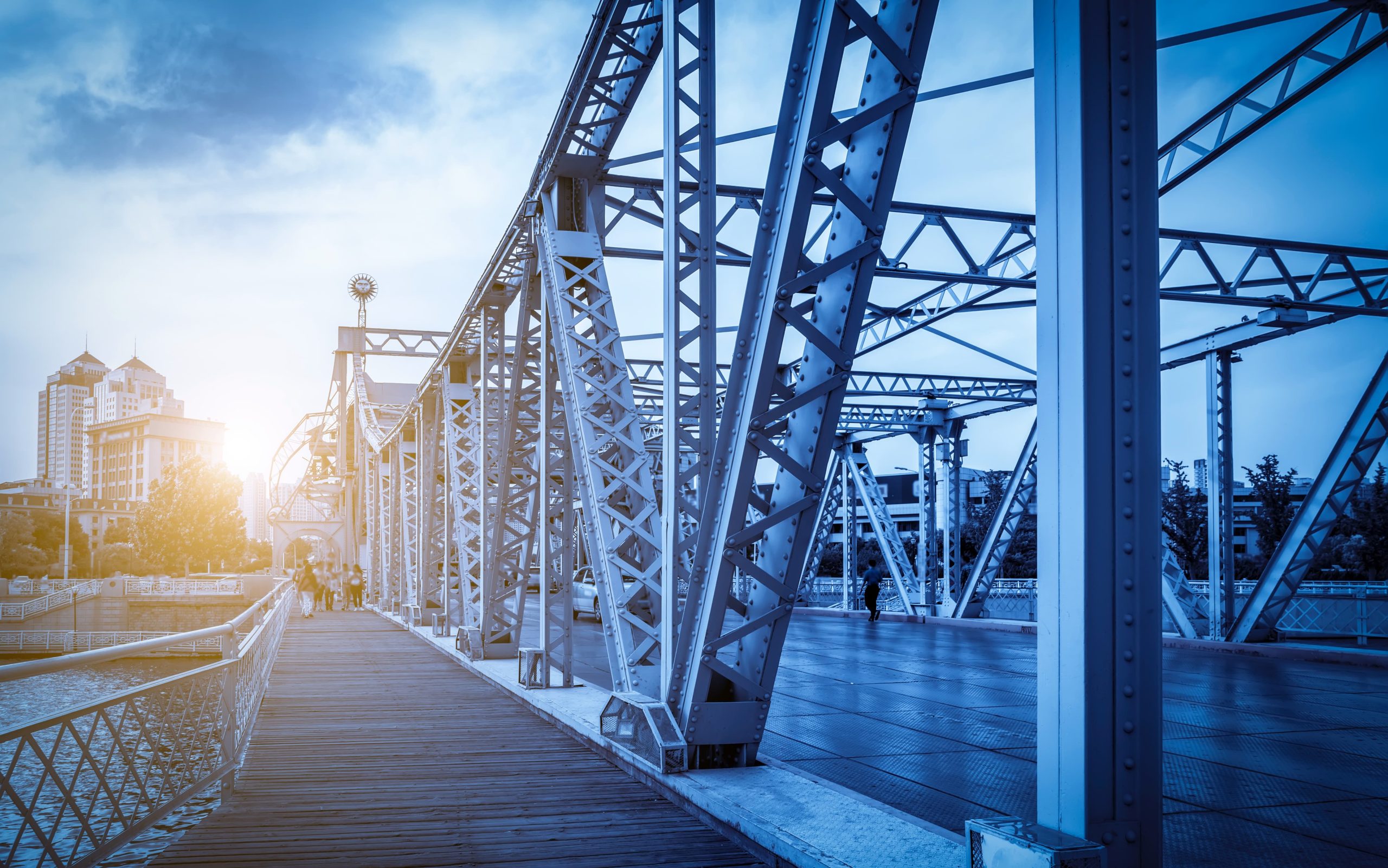
Stahlbrücke
YZ200 (200-250 Mikrometer)
- Anwendung: Geeignet für die Oberflächenbehandlung von mittelgroßen mechanischen Teilen und Gussteilen.
- Vorteile:
- Entfernt wirkungsvoll mittelstarke Oxidschichten und Schmutz.
- Bietet eine gute Oberflächenrauhigkeit, geeignet für die Weiterverarbeitung bei mittleren Anforderungen.
- Hohe Verschleißfestigkeit, wodurch der Verbrauch von Sandstrahlmitteln reduziert wird.
- Feine Partikel können feine Verschmutzungen aufnehmen und sind für hochpräzise Anwendungen geeignet.
- Beschreibung des Falls: Schneider Electric in Deutschland verwendet YZ200-Zirkonoxidkugeln in seinem Maschinenbauprozess, um mittelstarke Oxidschichten und Schmutz zu entfernen. Diese Behandlung verbessert die Oberflächenrauhigkeit mechanischer Teile und eignet sich für die anschließende Endbearbeitung. 2
YZ100 (80-125 Mikrometer)
- Anwendung: Geeignet für kleine Präzisionsteile und anspruchsvolle Oberflächenbehandlung.
- Vorteile:
- Entfernen Sie feinen Schmutz und Grate mit hoher Präzision.
- Erzeugt einen gleichmäßigen Oberflächenglanz und verbessert die Qualität des Aussehens des Produkts.
- Geeignet für den Einsatz in High-Tech-Bereichen wie optische Geräte und elektronische Komponenten.
- Beschreibung des Falls: Nikon verwendet YZ100-Zirkonoxidkugeln zur Behandlung optischer Linsen, um feine Verunreinigungen und Grate zu entfernen und so die optische Leistung und die Qualität des Aussehens zu gewährleisten. Dieses Verfahren spielt eine wichtige Rolle bei der Feinbearbeitung von optischen Geräten. 3
YZ50 (45-90 Mikrometer)
- Anwendung: Wird für ultrapräzise Teile und Gelegenheiten mit extrem hohen Anforderungen an die Oberflächenbehandlung verwendet.
- Vorteile:
- Kann extrem feine Verunreinigungen entfernen und eine makellose Oberflächenbehandlung bewirken.
- Geeignet für Anwendungen mit extrem hohen Anforderungen an die Oberflächenqualität, wie z. B. medizinische Geräte und hochwertige Elektronikprodukte.
- Moderater Preis, hohe Leistung.
- Beschreibung des Falls: Mettler-Toledo verwendet YZ50-Zirkonoxidkugeln für die ultrapräzise Oberflächenbehandlung bei der Herstellung seiner medizinischen Geräte, um extrem feine Verunreinigungen zu entfernen und die Qualität und Sicherheit der Produkte zu gewährleisten. 4
Grundsätze für die Auswahl von Zirkoniumdioxid-Perlen
- Auswahl nach der Größe des Werkstücks
- Bei großen Werkstücken sollte man Sandstrahlperlen mit größeren Partikeln wählen, um die Reinigungswirkung zu verbessern.
- Bei kleinen Werkstücken sollten Strahlmittel mit kleineren Partikeln gewählt werden, um eine übermäßige Belastung des Werkstücks zu vermeiden.
- Auswahl nach den Anforderungen an die Oberflächenqualität
- Bei Werkstücken mit hohen Anforderungen an die Oberflächenqualität sollte man Sandstrahlperlen mit kleineren Partikeln wählen, um eine höhere Oberflächengüte zu erzielen.
- Für Werkstücke, die eine hohe Reinigungsleistung erfordern, können Sandstrahlperlen mit größeren Partikeln gewählt werden.
- Auswahl nach Materialhärte
- Bei Materialien mit höherer Härte sollten Sie Sandstrahlperlen mit größeren Partikeln wählen, um die Reinigungswirkung zu verbessern.
- Bei Materialien mit geringerer Härte wählen Sie Sandstrahlkugeln mit kleineren Partikeln, um eine Beschädigung des Werkstücks zu vermeiden.
- Auswahl nach Produktionskosten
- Sandstrahlperlen mit kleineren Partikeln sind in der Regel teurer, und die entsprechenden Spezifikationen sollten je nach Budget ausgewählt werden.
- Sandstrahlperlen mit größeren Partikeln sind relativ billig und eignen sich zur Kostensenkung in der Großserienproduktion.
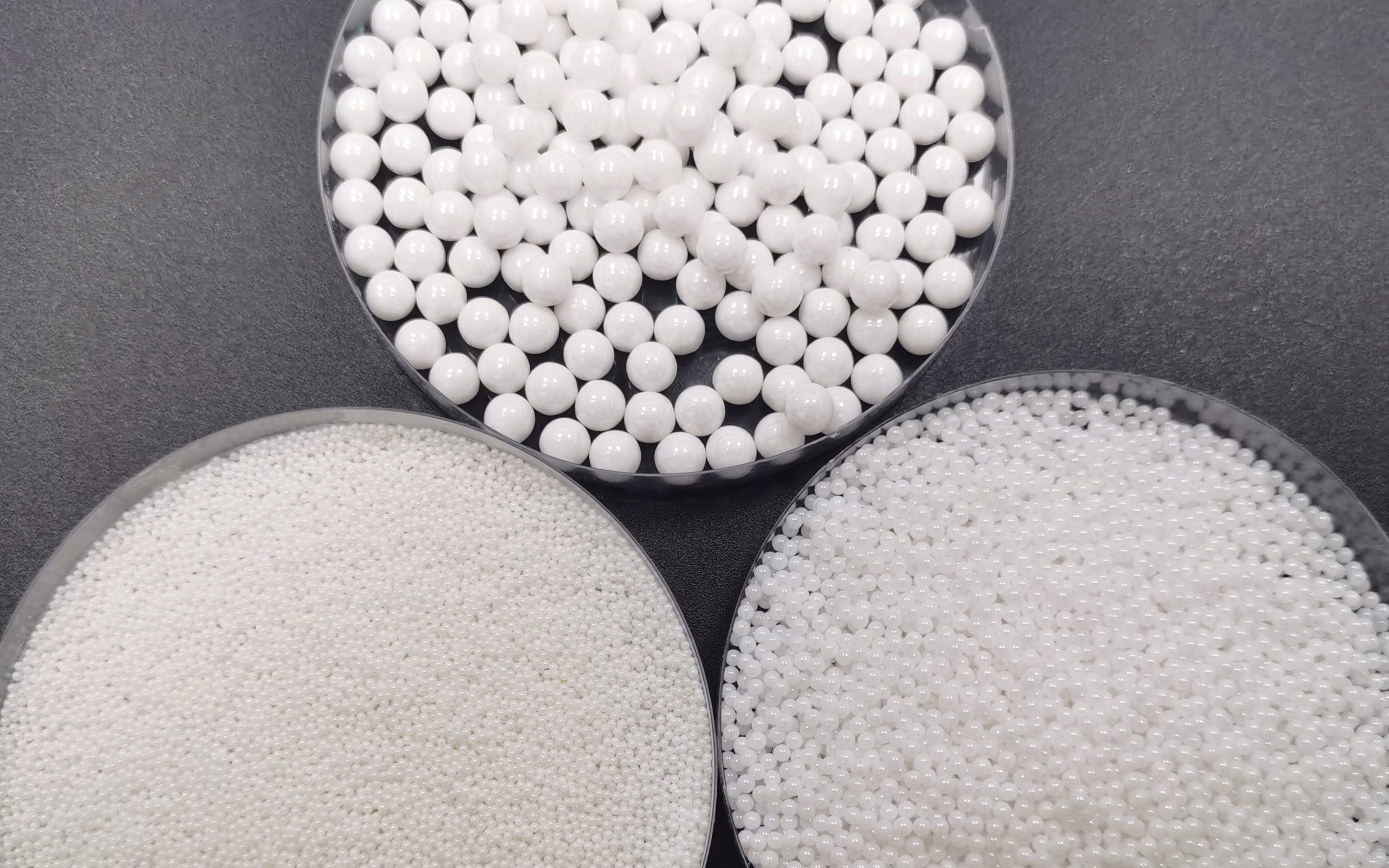
Verschiedene Größen von Zirkoniumdioxid-Strahlkugeln
Tatsächlicher Betrieb und Vorsichtsmaßnahmen
- Abstimmung von Ausrüstung und Prozessbedingungen
Die Auswahl der Sandstrahlausrüstung sollte auf die Partikelgröße des Sandstrahlmittels, den Einspritzdruck und die Düsengröße abgestimmt sein. Eine vernünftige Abstimmung der Ausrüstung kann die Konsistenz und Stabilität des Sandstrahleffekts gewährleisten.
Kontrollieren Sie die Temperatur und die Luftfeuchtigkeit der Sandstrahlumgebung, um zu vermeiden, dass eine zu hohe Luftfeuchtigkeit zu einer Agglomeration des Sandstrahlmittels führt und dadurch die Sandstrahlwirkung beeinträchtigt.
- Management von Sandstrahlmitteln
Überprüfen Sie das Sandstrahlmittel regelmäßig und tauschen Sie es aus, um zu vermeiden, dass der Verschleiß des Mittels während des Gebrauchs die Sandstrahlwirkung beeinträchtigt.
Lagern Sie das Sandstrahlmittel angemessen, um das Eindringen von Feuchtigkeit und Verunreinigungen zu verhindern.
- Beherrschung der Betriebstechnik
Die Bediener sollten mit der Sandstrahltechnologie und dem Prozessablauf vertraut sein, um sicherzustellen, dass der Sandstrahleffekt den Erwartungen entspricht.
Führen Sie regelmäßig Schulungen durch und verbessern Sie Ihre Fähigkeiten, um die Sicherheit und Effizienz der Sandstrahlarbeiten zu gewährleisten.
Allgemeine Probleme und Lösungen
- Ungleichmäßiges Sandstrahlen
Beschreibung des Problems: Beim Sandstrahlen kommt es zu einer ungleichmäßigen Oberflächenbehandlung, die das Aussehen und die Qualität des Endprodukts beeinträchtigen kann.
Lösung:
-
- Überprüfen Sie die Düse: Prüfen Sie, ob die Düse verstopft oder abgenutzt ist. Prüfen und reinigen Sie die Düse regelmäßig und tauschen Sie sie bei Bedarf aus, um ein gleichmäßiges Strahlen zu gewährleisten.
- Wartung der Sandstrahlausrüstung: Führen Sie regelmäßig eine umfassende Inspektion der Sandstrahlausrüstung durch, um sicherzustellen, dass alle Komponenten normal funktionieren, einschließlich der Sandstrahlkammer, des Luftversorgungssystems und der Durchflussregelung.
- Stellen Sie die Sandstrahlparameter ein: Stellen Sie den Sandstrahldruck und den Mediendurchfluss angemessen ein, um sicherzustellen, dass der Sandstrahlmodus des Sandstrahlgeräts mit den Verarbeitungsanforderungen übereinstimmt.
- Überprüfen Sie den Sandstrahlabstand und -winkel: Stellen Sie sicher, dass der Sandstrahlabstand und der Düsenwinkel einheitlich sind, um eine ungleichmäßige Bearbeitung aufgrund von Winkelproblemen zu vermeiden.
- Der Sandstrahleffekt ist nicht ideal
Beschreibung des Problems: Die Oberfläche erreicht nach dem Sandstrahlen nicht die erwartete Sauberkeit oder Rauheit.
Lösung:
-
- Stellen Sie den Sandstrahldruck und den Durchfluss ein: Stellen Sie den Druck und die Durchflussmenge entsprechend den spezifischen Anforderungen des Sandstrahlens ein, um sicherzustellen, dass Schmutz und Oxidschichten effektiv entfernt werden können.
- Wählen Sie die geeigneten Spezifikationen für Sandstrahlkugeln aus: Wählen Sie die geeigneten Spezifikationen für Zirkoniumdioxid-Strahlmittel je nach Art des Materials und der Verarbeitungsanforderungen, um die erwartete Wirkung zu erzielen.
- Optimieren Sie die Prozessparameter: Optimieren Sie den Prozess entsprechend der tatsächlichen Bearbeitungssituation und passen Sie die Einstellungen der Sandstrahlmaschine an die Bearbeitungsanforderungen an.
- Das Sandstrahlmittel verschleißt zu schnell
Beschreibung des Problems: Das Sandstrahlmittel nutzt sich während des Gebrauchs zu schnell ab, was zu einer verminderten Sandstrahleffizienz führt.
Lösung:
-
- Reduzieren Sie den Sandstrahldruck: Eine Verringerung des Sandstrahldrucks kann die Verschleißrate des Sandstrahlmittels verringern und seine Lebensdauer verlängern.
- Reduzieren Sie die Aufprallkraft: Stellen Sie die Sandstrahlausrüstung so ein, dass die Aufprallkraft zwischen dem Strahlmittel und dem Werkstück reduziert wird, um so den Verschleiß zu verringern.
- Tauschen Sie das Strahlmittel regelmäßig aus und füllen Sie es auf: Überprüfen Sie regelmäßig die Abnutzung des Sandstrahlmittels und wechseln Sie es rechtzeitig aus oder füllen Sie es auf, um einen guten Sandstrahleffekt zu erzielen.
- Beim Sandstrahlen entsteht Staub
Beschreibung des Problems: Beim Sandstrahlen entsteht eine große Menge Staub, der die Arbeitsumgebung und die Gesundheit des Bedienpersonals beeinträchtigt.
Lösung:
-
- Sorgen Sie für eine gute Belüftung: Installieren Sie ein wirksames Belüftungssystem im Sandstrahlraum, um die Luftzirkulation aufrechtzuerhalten und die Staubkonzentration zu verringern.
- Installieren Sie ein Filtersystem: Das Gerät ist mit einem effizienten Luftfiltersystem ausgestattet, das Staub auffangen und die Arbeitsumgebung sauber halten kann.
- Reinigen Sie den Sandstrahlraum regelmäßig: Reinigen Sie den Sandstrahlraum und die umliegenden Bereiche regelmäßig, um Staubansammlungen zu vermeiden.
Tipps und Vorschläge zur Verbesserung der Sandstrahlergebnisse
- Optimieren der Sandstrahlparameter
- Druck und Durchfluss einstellen: Stellen Sie den Sandstrahldruck, den Durchfluss und den Düsenwinkel je nach Materialtyp, Verschmutzungsgrad und Sandstrahlanforderungen ein. Die besten Einstellungen der Sandstrahlparameter können den Bearbeitungseffekt und die Effizienz verbessern.
- Sandstrahlwinkel und -abstand: Die Wahl des richtigen Sandstrahlwinkels und -abstands trägt dazu bei, ein gleichmäßiges Sandstrahlen zu gewährleisten und den gewünschten Oberflächeneffekt zu erzielen.
- Halten Sie die Ausrüstung sauber
- Reinigen Sie die Ausrüstung regelmäßig: Reinigen Sie die Sandstrahlausrüstung, Düsen und Rohre regelmäßig, um zu verhindern, dass Staub und Verunreinigungen die Qualität des Sandstrahlens beeinträchtigen.
- Pflegen Sie den Sandstrahlraum: Reinigen Sie das Innere des Sandstrahlraums regelmäßig, um zu verhindern, dass Staub und Rückstände den Sandstrahlprozess beeinträchtigen.
- Wählen Sie die Medien vernünftig aus
- Wählen Sie das Strahlmittel entsprechend den Bearbeitungsanforderungen: Wählen Sie je nach Art des zu bearbeitenden Materials, der Oberflächenanforderungen und des Verschmutzungsgrads die geeigneten Zirkonoxid-Sandstrahlperlen aus, um konsistente und zufriedenstellende Sandstrahlergebnisse zu gewährleisten.
- Bewerten Sie die Leistung des Strahlmittels: Wählen Sie Sandstrahlmittel mit hoher Verschleißfestigkeit und Stabilität, um den Verschleiß zu verringern und die Effizienz des Sandstrahlens zu verbessern.
- Kontrolle der Sandstrahlumgebung
- Halten Sie eine trockene Umgebung aufrecht: Kontrollieren Sie die Luftfeuchtigkeit in der Sandstrahlumgebung, um die Auswirkungen einer zu hohen Luftfeuchtigkeit auf das Sandstrahlmittel zu vermeiden und die Stabilität des Sandstrahleffekts zu gewährleisten.
- Sorgen Sie für gute Belüftung: Sorgen Sie für eine gute Belüftung der Sandstrahlumgebung, um die Auswirkungen von Feuchtigkeit und Staub auf das Sandstrahlmittel und die Wirkung zu verringern.
Diese detaillierten Vorschläge und Lösungen tragen dazu bei, den Sandstrahleffekt zu verbessern und sicherzustellen, dass Probleme im Sandstrahlprozess effektiv gelöst werden, wodurch die Produktionseffizienz und die Produktqualität verbessert werden.
Durch ein tiefes Verständnis der Sandstrahltechnologie können wir feststellen, dass Zirkoniumdioxid-Strahlkugeln mit ihren ausgezeichneten Eigenschaften bei der Entfernung von feinem Schmutz und Oxidschichten gute Dienste leisten. Gleichzeitig können Sandstrahlkugeln verschiedener Größen eine Vielzahl von Anforderungen erfüllen, von der Grobbearbeitung bis zum Feinschliff, wodurch sichergestellt wird, dass verschiedene Oberflächen den idealen Zustand und die ideale Qualität erreichen können. Durch wissenschaftliche und vernünftige Arbeitsweise und Verwaltung kann die kontinuierliche Erforschung und Anwendung fortschrittlicher Sandstrahltechnologie nicht nur die Produktqualität verbessern, sondern auch den Fortschritt und die Entwicklung verwandter Industriezweige fördern und den verschiedenen Märkten weitere aufregende Innovationen und Durchbrüche bringen.
Referenzen:
- Florence Steel Corporation - Oberflächenbehandlung
- Schneider Electric - Oberflächenbehandlung
- Nikon Corporation - Optische Oberflächenbehandlung
- Mettler-Toledo - Präzisionsoberflächenbehandlung
Filter