Zirconia Beads VS Glass Beads: Which Sandblasting Media Are Better for Your Needs?
October 9, 2024
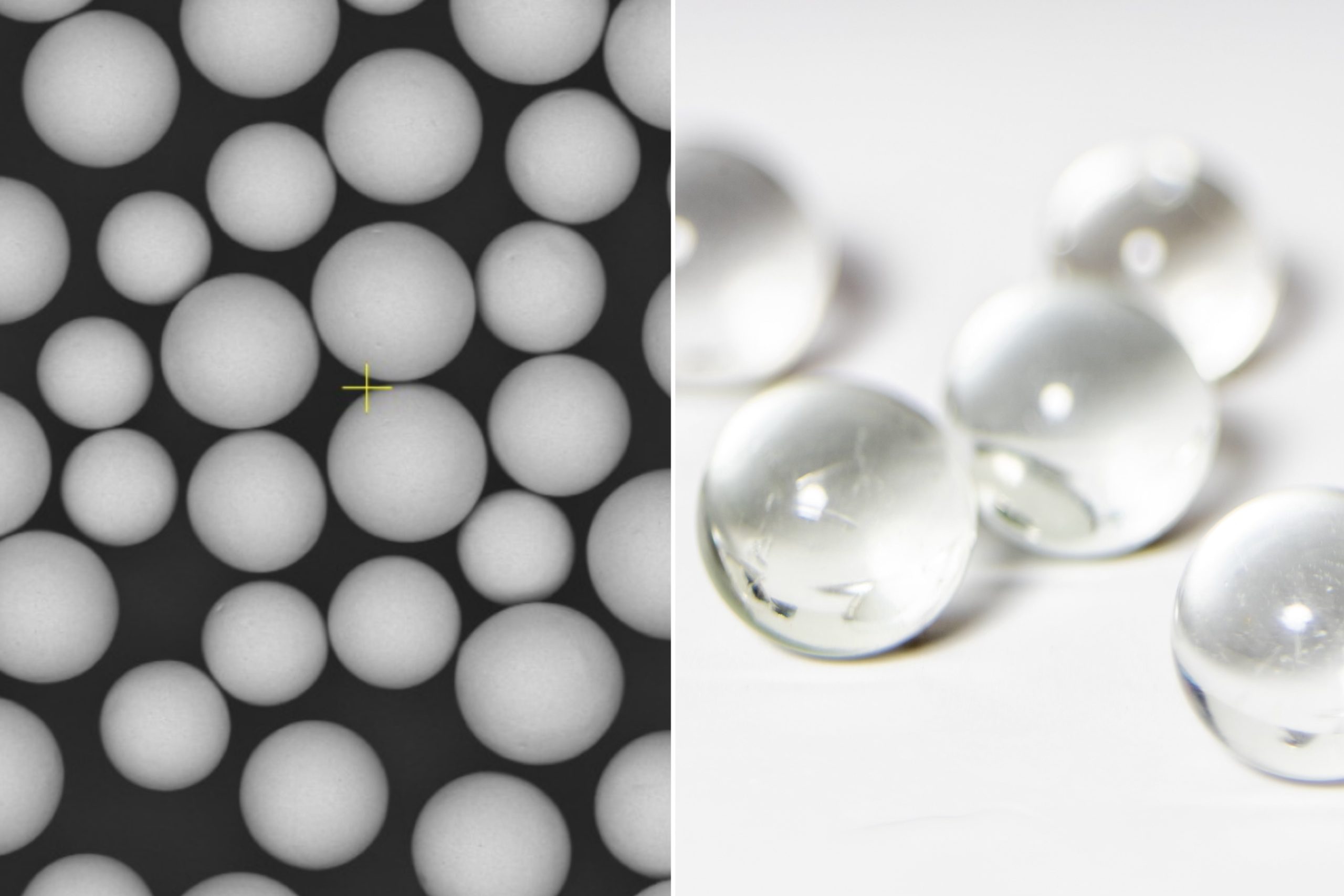
In modern industrial processing, choosing the right sandblasting media is essential to ensure fine surface treatment of the product, increase the life of the workpiece, and reduce subsequent processing steps. The characteristics of different sandblasting media make them have significant differences in their effects when processing different materials. This article focuses on zirconia blasting beads and glass beads, two widely used sandblasting media. As two common but very different materials, zirconia blasting beads are often used for high-intensity sandblasting operations due to their excellent hardness and durability, while glass beads are known for their gentle surface treatment effects and are suitable for fine processing and surface beauty treatment. Through an in-depth comparison of the two materials in terms of workpiece material, surface treatment purpose, economy, and environmental protection, this article will help you choose the most suitable sandblasting media according to specific needs to ensure the efficiency and safety of the processing process.
Introduction to Zirconia Beads and Glass Beads
When choosing sandblasting media, it is particularly important to understand the material composition, performance characteristics, advantages, and disadvantages of different media. Zirconia blasting beads and glass beads each have unique chemical properties and application scenarios, suitable for different sandblasting needs.
Zirconia beads(Click here for details)
Zirconia blasting beads are sandblasting media made of high-purity zirconium oxide (ZrO₂) material. Due to its high hardness and high wear resistance, zirconium oxide has excellent surface impact performance and can provide long-term stability and efficiency in high-intensity sandblasting processes. Zirconia blasting beads are usually white or off-white, high-temperature resistant, and chemically stable, and they are not easily affected by oil or chemicals on the workpiece.
- Advantages
- High hardness: Mohs hardness 8-9, capable of handling hard materials, suitable for large-area cleaning and roughening.
- Strong durability: high material density, impact resistance, wear resistance, long service life, reducing the cost of frequent replacement.
- Chemical stability: Able to maintain performance under high temperatures and strong acid and alkali environments, suitable for use in chemical and special environments.
- Good consistency: uniform particle size, not easy to break, ensuring consistent sandblasting effect.
- Reduce dust: less dust is generated during use, reducing workshop pollution and improving operator safety.
- Applicable scenarios
Zirconia beads are often used in processing processes that require high impact and wear resistance and are suitable for processing hard materials such as steel, cast iron, stainless steel, etc. They can effectively remove heavy contamination layers and oxides, so they are widely used in the following industries:
- Automobile manufacturing: used to remove scale and oil stains on the surface of engine parts and transmission system parts to ensure the adhesion of subsequent coatings.
- Aerospace: suitable for high-precision sandblasting of key components such as turbine blades to ensure their reliability in extreme environments.
- Mold manufacturing: roughen the surface of the mold to increase the service life of the mold.
- Heavy equipment maintenance: such as cleaning and anti-corrosion layer removal of ships and steel structures to ensure long-term use of equipment.
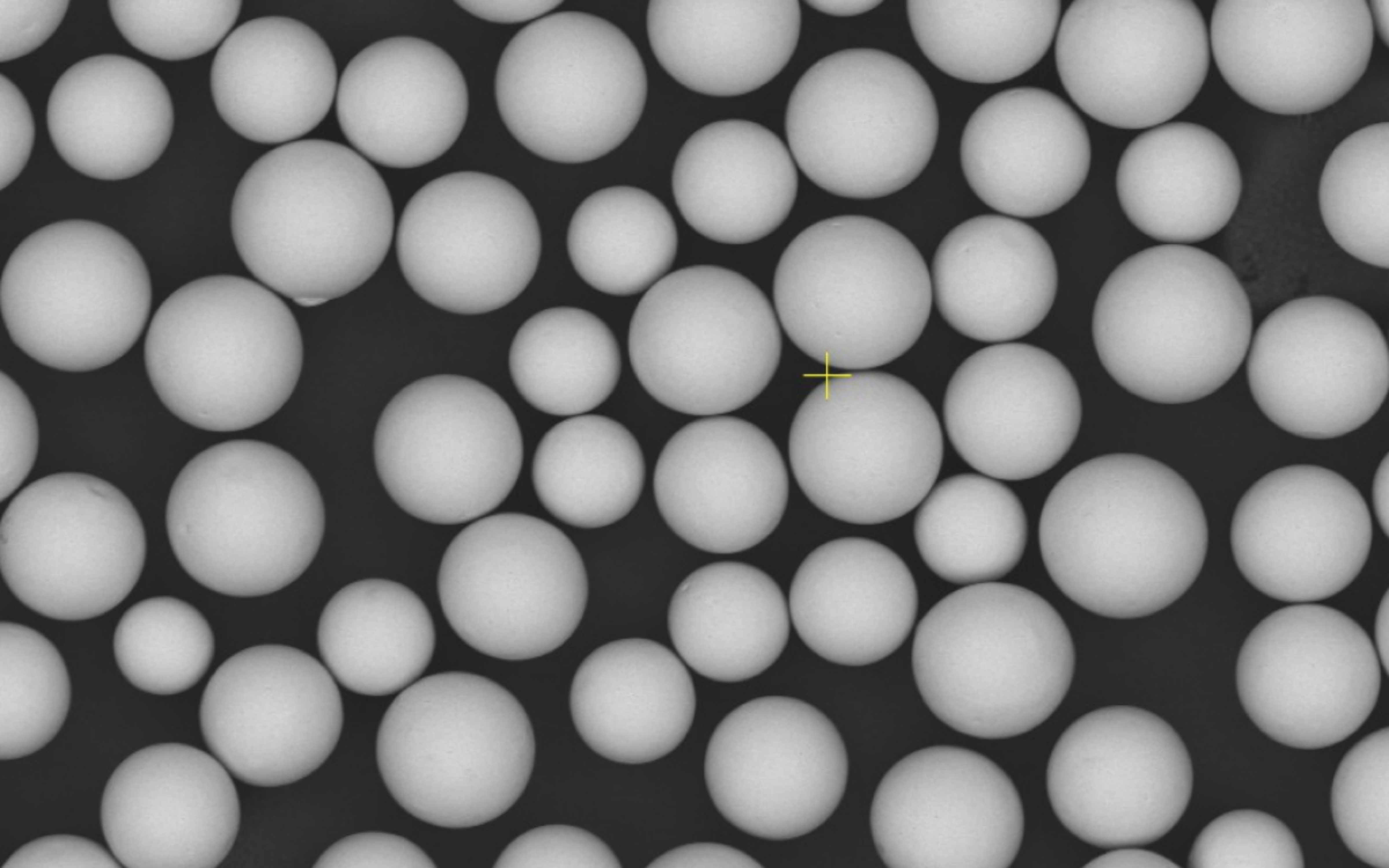
zirconia blasting beads
Glass beads
Glass beads are sandblasting media made of high-quality glass materials through high-temperature melting and molding. The chemical composition is mainly silicon dioxide (SiO₂). Glass beads have a relatively mild texture, moderate hardness, and density, and can effectively clean the surface of the workpiece without damaging its internal structure. It is usually translucent and smooth in appearance, suitable for processes with high requirements for surface smoothness and gloss.
- Advantages
- Gentle surface treatment: Due to the low hardness of glass beads (Mohs hardness 5-6), the material surface will not be damaged during the cleaning process, which is suitable for processing more fragile workpieces.
- Keep the workpiece smooth: It can keep the surface of the workpiece smooth and bright while removing the surface oxide layer and contaminants.
- Good environmental protection: Glass beads can be reused, and it is not easy to generate a lot of dust, reducing pollution to the environment.
- No iron pollution: Glass beads do not contain iron elements, which is suitable for processing workpieces with strict iron-free requirements on the surface to avoid secondary pollution.
- Good polishing effect: The surface can be lightly polished and polished to improve the appearance quality of the workpiece.
- Applicable scenarios
The wide application of glass beads is mainly concentrated in processing scenarios with high surface accuracy requirements but no severe impact. It is often used for fine cleaning and surface treatment of metals and non-metals, and is suitable for the following applications:
- Aerospace and medical devices: Used to clean the surface of aviation parts and medical devices without destroying the dimensional accuracy of parts, such as the surface polishing of aircraft engine blades and medical devices.
- Precision electronic equipment: Cleaning and micro-processing of chips and semiconductor components to ensure that the surface is not damaged.
- Decoration and surface beautification: used for surface polishing and beauty treatment of crafts, jewelry, and artistic decorations to enhance appearance and texture.
- Light metal cleaning: suitable for surface cleaning of softer metal materials such as aluminum and copper to prevent deformation or damage of materials.
Key factors affecting the selection of sandblasting media
When deciding whether to use zirconia blasting beads or glass beads for sandblasting, various factors need to be evaluated from multiple angles, including the material of the workpiece, the purpose of surface treatment, and economic conditions. These factors not only determine the efficiency of the sandblasting operation but also directly affect the final treatment effect.
Workpiece material
Different workpiece materials require different sandblasting media to ensure that the surface treatment goal can be achieved without causing unnecessary damage or changes to the workpiece. In this regard, zirconia blasting beads and glass beads are each suitable for different types of materials.
- Applicable materials of zirconia blasting beads
Zirconium beads are suitable for processing some harder workpiece materials due to their high hardness and impact resistance, such as:
- Metal materials: such as stainless steel, cast iron, alloy steel, etc. Zirconia blasting beads can deeply remove stubborn contaminants such as oxide layers, corrosion products, oil stains, etc. on these materials without causing significant damage to the substrate.
- High-strength alloys: Especially suitable for high-strength alloy parts used in aerospace and heavy industries. They require higher impact force and wear resistance to ensure that the quality of the workpiece surface is not damaged while ensuring the cleaning effect.
- Suitable materials for glass beads
Glass beads are more suitable for materials with lower hardness and gentle treatment. Due to its lower hardness, glass beads can clean and polish the following materials without damaging their surfaces:
- Aluminum and its alloys: Glass beads can effectively remove slight oxides on the surface while maintaining the smoothness and dimensional accuracy of the material. Aluminum products are widely used in aerospace, automotive, and electronics industries, so glass beads play an important role in surface treatment in these fields.
- Plastics and resins: For some high-precision plastic parts or resin products, glass beads can gently remove surface impurities without causing cracking or deformation of the surface due to excessive impact force.
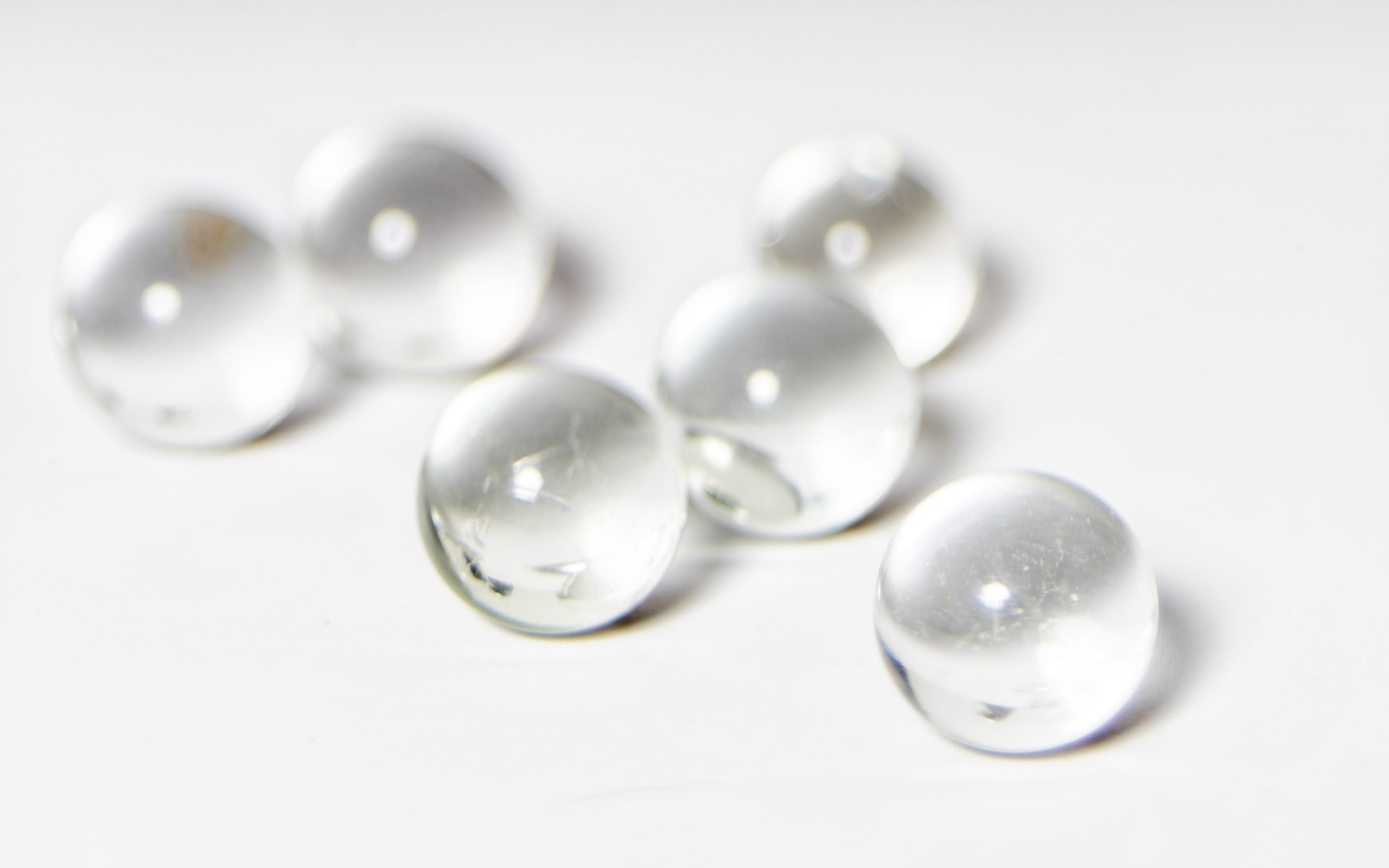
Glass beads
Purpose of surface treatment
Another key consideration in selecting sandblasting media is the purpose of the sandblasting operation. Different surface treatment requirements will determine which media is more suitable.
- Treatment goals of zirconia blasting beads
Zirconia beads are mainly suitable for the following surface treatment purposes:
- Roughening: The high hardness of this material makes it very suitable for processes that require surface roughening, especially before coating or electroplating, to provide a high adhesion surface for the substrate. Ceramic beads can etch deeply into the surface of the workpiece, providing an excellent adhesion foundation for subsequent processes.
- Large area cleaning: When cleaning large areas of stubborn contaminants, such as scale on steel or heavy dirt on high-strength alloys, zirconia blasting beads can do the job efficiently and thoroughly. They can remove heavy oxide layers with rapid impact force, saving time.
- Treatment goals of glass beads
Glass beads are often used for more delicate surface treatments, especially in situations where surface smoothness and gloss need to be maintained. Its typical applications include:
- Polishing and surface smoothing: Glass beads can gently polish the surface of the workpiece to give it a smoother and glossier appearance. This is particularly important in decorative surface treatments and processes that require high aesthetics.
- Surface cleaning and residue removal: For some workpieces that require gentle cleaning, glass beads can effectively remove minor contaminants (such as dust, and mild corrosion) remaining on the surface, but will not affect the appearance or size of the workpiece. This is very common in the cleaning of precision instruments and medical device surfaces.
Economic conditions and cost-effectiveness
Whether it is industrial manufacturing or small-scale operations, cost is always an important factor that cannot be ignored when choosing sandblasting media. There is a clear difference between zirconia blasting beads and glass beads in terms of cost and economic benefits.
- Economics of zirconia blasting beads
Zirconia beads have a higher initial cost, but their durability and long life add to their economic benefits in long-term operations. The following are its economic considerations:
- Long life and reduced replacement frequency: Although zirconia blasting beads are more expensive, their high wear resistance means that the frequency of media replacement is low in long-term use. This can significantly reduce downtime maintenance time and save labor costs for large-scale industrial production lines.
- Suitable for high-intensity operations: Due to their high density and impact resistance, zirconia blasting beads can withstand repeated impacts from high-pressure sandblasting equipment. This makes them particularly suitable for processing hard workpieces, such as large-scale industrial materials such as cast iron and steel. In terms of durability, they are not only not easy to break but also can maintain their grinding effect for a long time, which is particularly suitable for manufacturing industries that require large-scale processing.
- Reduce downtime maintenance: Due to the high durability of zirconia blasting beads, their use reduces the number of equipment downtimes and reduces production interruptions caused by frequent media changes. This is especially important for factories or high-efficiency production lines that require 24-hour uninterrupted operation.
- Economics of glass beads
In contrast, glass beads are cheaper and suitable for operations with limited budgets and milder surface treatment requirements. The following are the economic considerations of glass beads:
- Low price, suitable for small-scale operations: Glass beads have a low procurement cost, so they are very suitable for sandblasting operations of small and medium-sized enterprises or single projects, especially those light processing areas that do not require high-strength media.
- Reusability: Glass beads also have a certain degree of reusability, but due to their lower hardness, their service life is shorter than that of zirconia blasting beads. Therefore, in large-scale long-term operations, glass beads may need to be replaced frequently, increasing operating costs.
- High maintenance requirements: Glass beads are prone to breakage and wear, so sandblasting equipment needs to be cleaned regularly to avoid equipment failure caused by debris accumulation. Frequent media replacement also means that operators need more maintenance time, which may bring certain cost and efficiency issues in large-scale production.
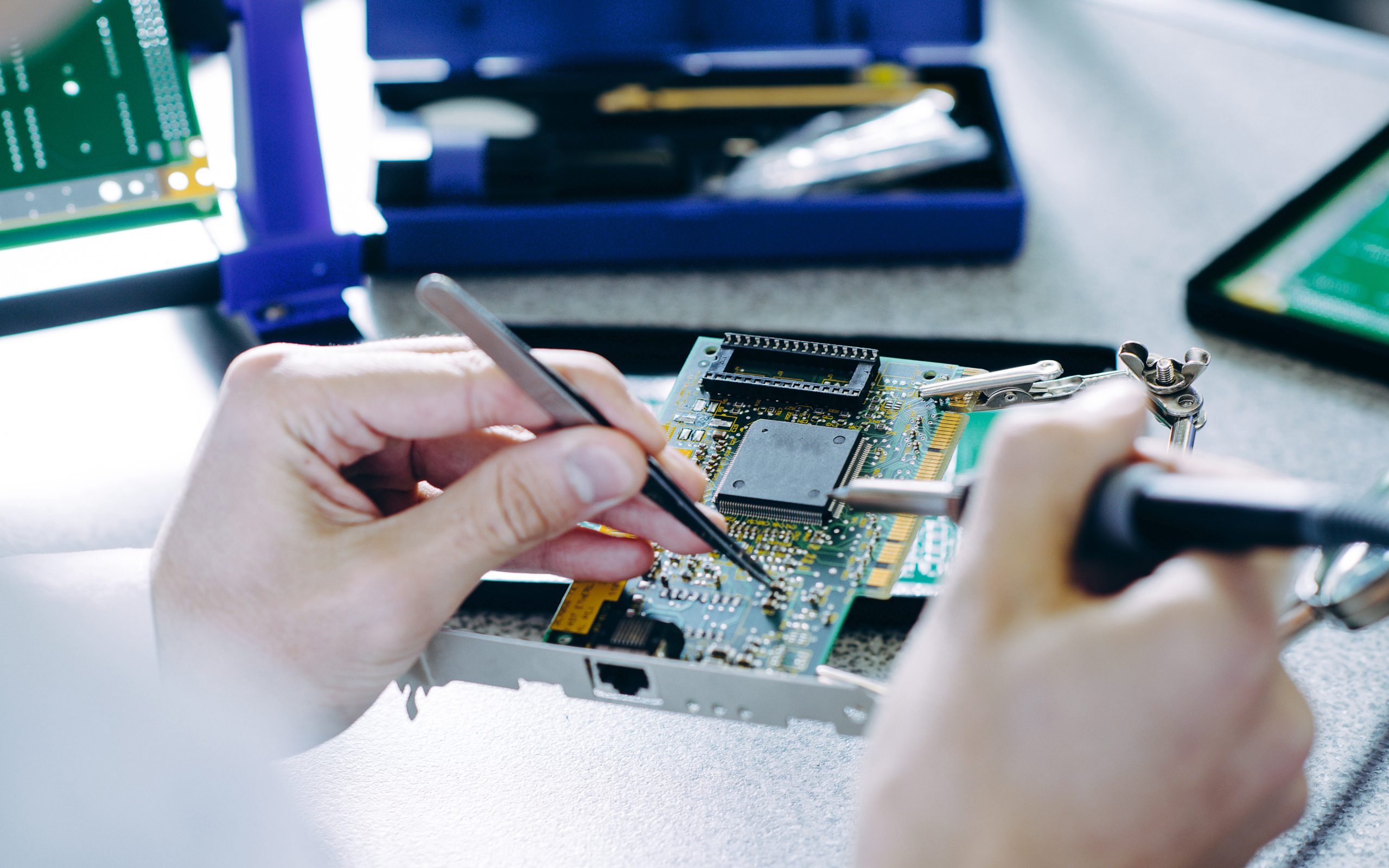
Precision Instruments
Summary: Comparison of the cost-effectiveness of the two media
- Zirconia beads
- High initial investment: The purchase cost of zirconia blasting beads is relatively high, especially compared with glass beads. Due to its complex manufacturing process and rare materials, the single purchase cost of zirconia blasting beads is often several times higher than that of glass beads.
- Significant long-term benefits: Despite the large initial investment, the high wear resistance and low loss rate of zirconia blasting beads in long-term use make them more economical in long-term large-scale production. From the perspective of replacement frequency and operation and maintenance, ceramic beads not only save human resources but also reduce equipment downtime, thereby improving the overall efficiency of the production line.
- Suitable for large-scale production: For industrial enterprises that require high-intensity and continuous processing, zirconia blasting beads can provide better cost-effective performance. Especially in the fields of aviation, automobiles, and metallurgy, enterprises tend to pay more attention to long-term production efficiency, so choosing more durable zirconia blasting beads can effectively reduce long-term costs.
- Glass beads
- Low initial cost: The single purchase cost of glass beads is significantly lower than that of zirconia blasting beads, which makes it an ideal choice for small and medium-sized enterprises with limited budgets or short-term projects. The availability and relatively simple manufacturing process of glass beads determine its price advantage.
- High-frequency replacement increases long-term costs: However, due to the low hardness and short service life of glass beads, enterprises need to frequently replace the medium, which leads to the gradual accumulation of material costs in long-term use. Although the initial cost is low, due to frequent medium replacement and equipment maintenance, the long-term cost performance of glass beads is not as ideal as that of zirconia blasting beads.
- Suitable for small-scale operations: For some short-term projects or light workpiece processing, glass beads are undoubtedly a more cost-effective choice. Especially in application scenarios with tight budgets or low surface treatment requirements, glass beads can quickly complete the task without excessive investment.
In sandblasting, zirconia blasting beads and glass beads each have their advantages and disadvantages. No matter which sandblasting media you choose, you should consider it comprehensively based on the material of the workpiece, the purpose of surface treatment, and long-term economic benefits. Only by comprehensively analyzing these factors can you ensure that the sandblasting operation achieves the best results while taking into account cost-effectiveness and production efficiency.
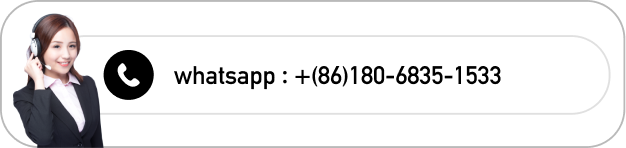