Zirconia beads for surface finishing
December 20, 2024
In modern industrial surface finishing, yttria-stabilized zirconia beads are widely used in many industries for their excellent hardness, density, and durability. Whether it is automotive parts cleaning, aerospace component strengthening, or glass product surface finishing, zirconia beads have become an important choice in the field of sandblasting with their high efficiency and environmentally friendly performance. Next, we will explore the unique value of zirconia blasting beads in industrial surface finishing based on their characteristics, advantages, and application areas.
What are Zirconia Beads
Yttria-stabilized zirconia beads are a high-performance sandblasting and surface finishing medium made by high-temperature sintering technology. The main component is zirconium oxide, which is stabilized by yttria to form high-density, uniform, and stable particles. This special process gives zirconium beads excellent hardness, density, and wear resistance, greatly extending their service life, while reducing the generation of breakage and fragments, ensuring the consistency of surface finishing effects.

Zirconia beads play a critical role in industrial surface finishing. As a sandblasting medium, it can not only effectively remove surface dirt and impurities, but also improve the surface hardness and smoothness of metals or other materials. Due to its high hardness and wear resistance, zirconia beads are particularly suitable for high-precision and high-intensity surface treatment, especially in industries such as aviation, automotive, electronics, and medical devices.
The main advantages of Zirconia Beads
High-purity material
HLH’s zirconia beads are made of zirconium oxide with a purity of more than 95%, ensuring that each bead has excellent stability and excellent performance. It is very suitable for surface finishing applications with strict requirements on material purity, such as medical devices, precision instruments, and other industries.
High wear resistance
Zirconium beads can maintain a longer service life during the surface treatment process, reduce the frequency of replacement due to wear, and significantly reduce operating costs, especially when processing large quantities.
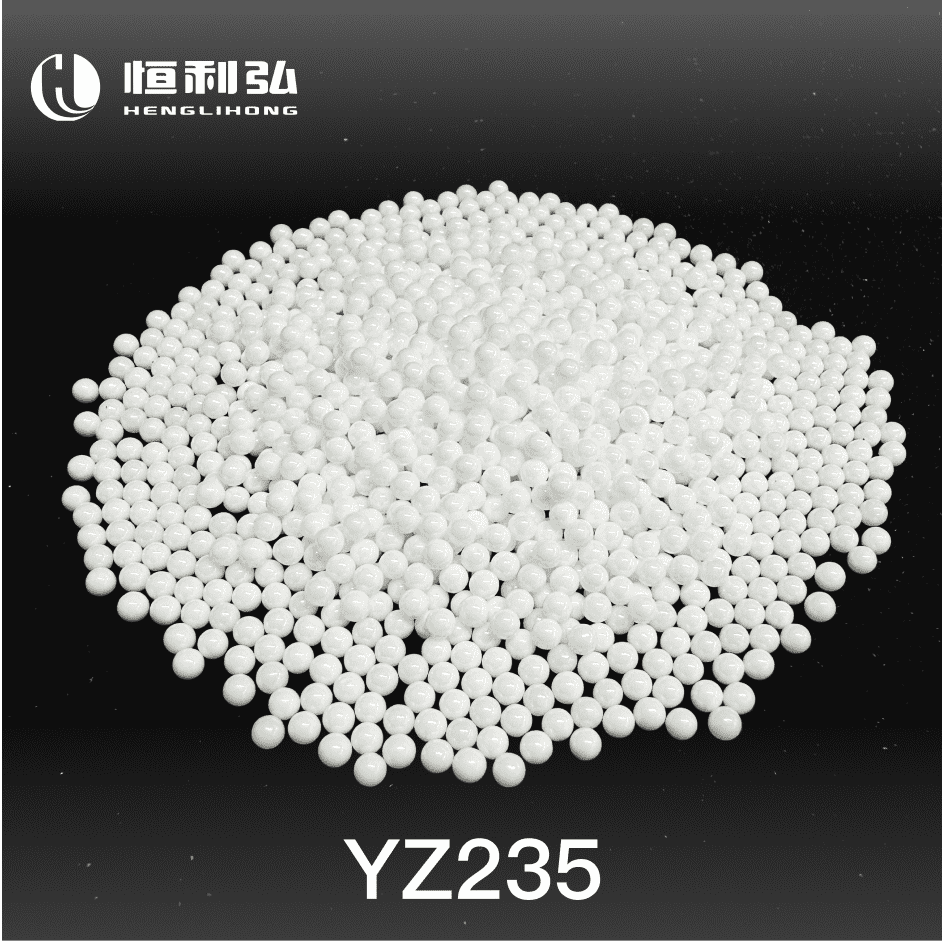
High-density properties
Due to the high density of zirconium oxide, HLH’s zirconia bead blasting can provide stronger impact and energy transfer efficiency during sandblasting or grinding, effectively remove dirt, oxide layers, or tiny flaws on the surface of parts, and improve the processing effect. They are especially suitable for surface strengthening of materials such as hard metals and alloys.
High-precision processing capabilities
Each HLH’s Yttria-stabilized zirconia beads is precision-manufactured to ensure that its shape is close to a perfect sphere. This design optimizes the uniformity and consistency of the sandblasting process, reduces surface damage that may be caused by irregular shapes, and is suitable for precision and high-demand surface treatment, especially for industries such as aerospace and automotive manufacturing.
Chemical stability
Zirconium beads have excellent chemical stability and can resist the erosion of acids, alkalis, and other corrosive substances. They can still maintain their performance under special environments (such as high temperature, high humidity, or highly corrosive environments), avoiding the contamination and degradation problems that may occur in traditional materials.
Multiple particle size options
The polishing effect is an important indicator for evaluating the performance of the medium, which is mainly reflected in the surface finish, polishing depth, and processing consistency.
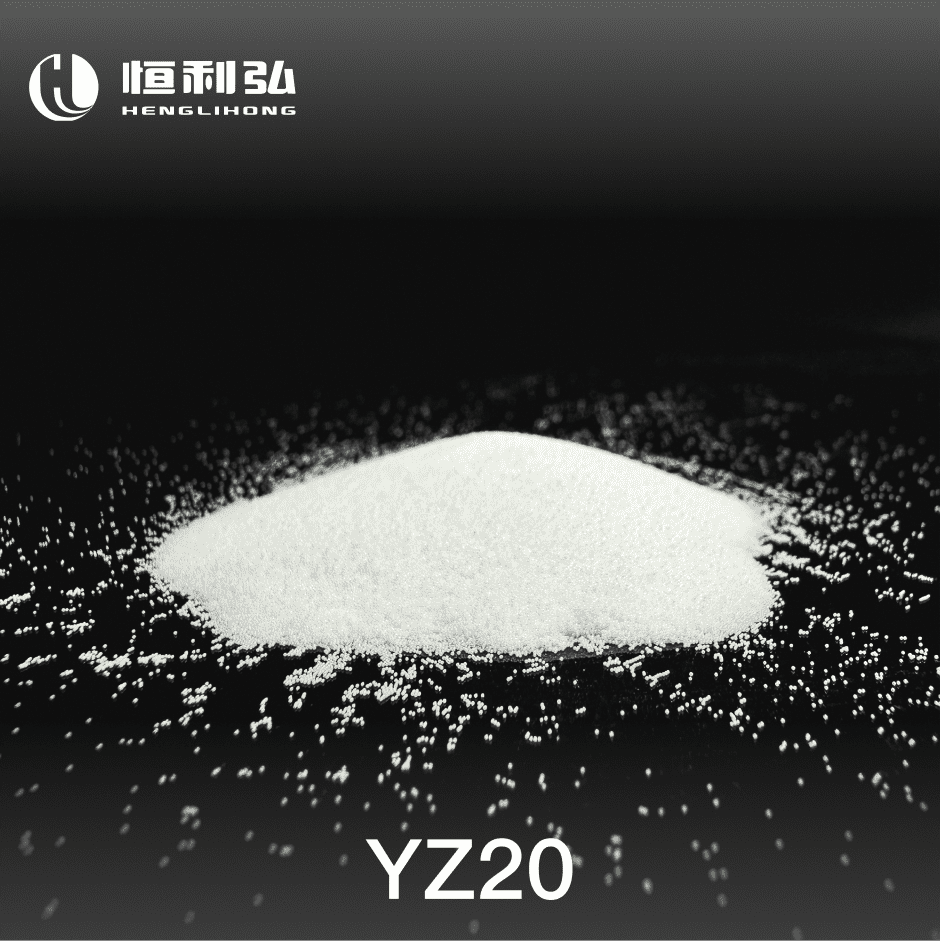
Reduce dust and pollution
Compared with other sandblasting media, zirconia beads produce less dust and do not release harmful substances during processing, which is more environmentally friendly, reduces pollution to equipment, and extends the service life of the equipment.
Strong adaptability
Yttria-stabilized zirconia beads can provide efficient surface finishing effects in various industrial environments. Whether it is metal, ceramic, glass, or other materials, zirconia beads can provide the most suitable surface treatment solution according to different workpiece materials and requirements. Therefore, it is widely used in aerospace, automotive, electronics, glass products, and other industries, showing strong adaptability.
Comparison with other sandblasting materials

Compared with brown corundum
As a traditional sandblasting medium, brown fused aluminum oxide has a higher hardness (Mohs hardness is about 9) and is often used for rough machining and deburring. However, compared with Yttria-stabilized zirconia beads, brown corundum has slightly lower wear resistance and produces more dust during use.
Compared with glass beads
Glass beads is a lighter sandblasting medium, usually used for delicate surface polishing, such as metal surface gloss treatment. Although glass beads provide better results in some application scenarios, they are also significantly less durable than zirconium beads, are prone to breakage, and cannot withstand high-intensity sandblasting operations. In addition, the surface finishing effect of glass beads is not as uniform as that of zirconia beads, and their high temperature and corrosion resistance are also weaker.
Compared with plastic media
Plastic sandblasting materials are generally used on softer surfaces, mainly for removing coatings or deburring, but the application industry is relatively limited, and usually can only handle lighter surface finishing needs. In contrast, the application range of zirconium beads is much larger.

Compared with ceramic media
Both ceramic media and zirconium beads have high hardness and wear resistance. In comparison, yttria-stabilized zirconia beads have higher and stronger energy transfer efficiency than ceramic sand (it can be said to be an enhanced version of ceramic blasting media), which can provide greater impact during surface finishing and achieve better processing effects.
In addition, zirconium beads are more stable in high temperature and high humidity environments, which can reduce wear and particle cracking during surface finishing and maintain a longer service life.
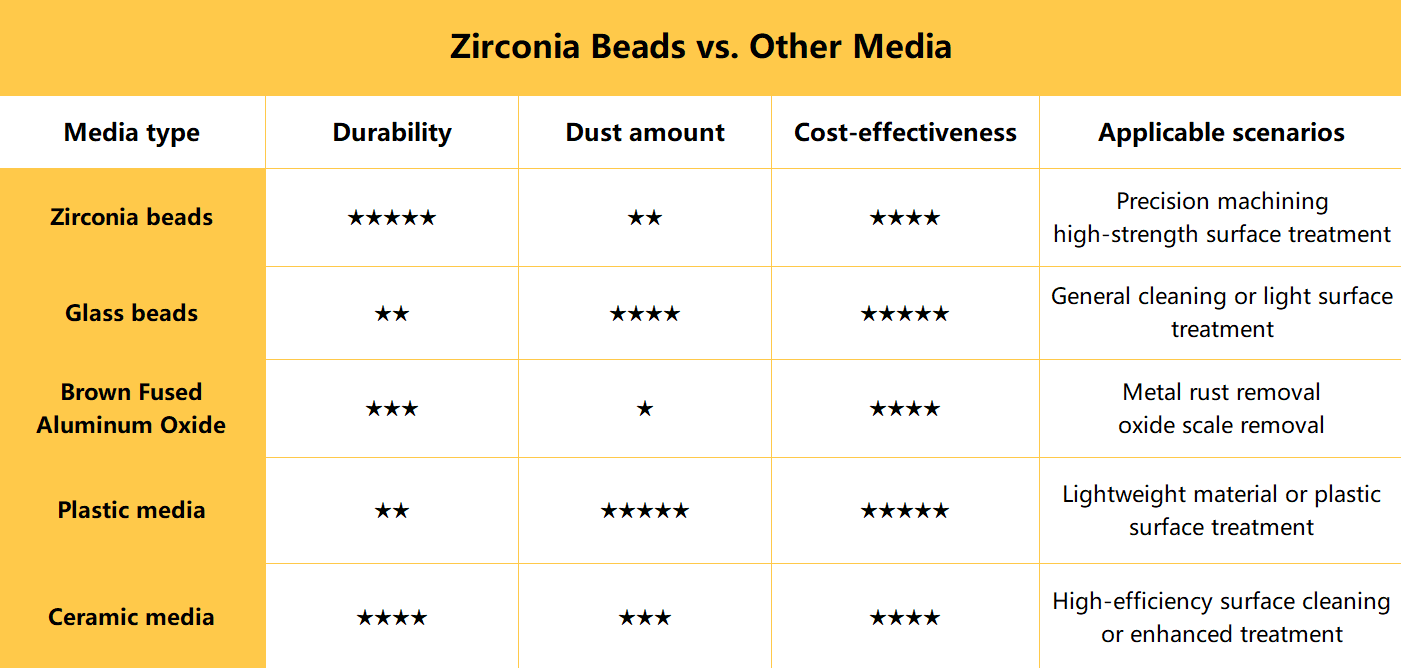
Industry application scenarios

Automotive industry
Zirconium beads are often used in surface cleaning and strengthening of engine parts (such as cylinder heads, and turbocharger parts) and brake systems, especially in the sandblasting process of aluminum alloy and steel parts.
The surface smoothness of engine parts treated with zirconium beads can be improved by about 30%, and the coating adhesion is improved by 15%-20%.
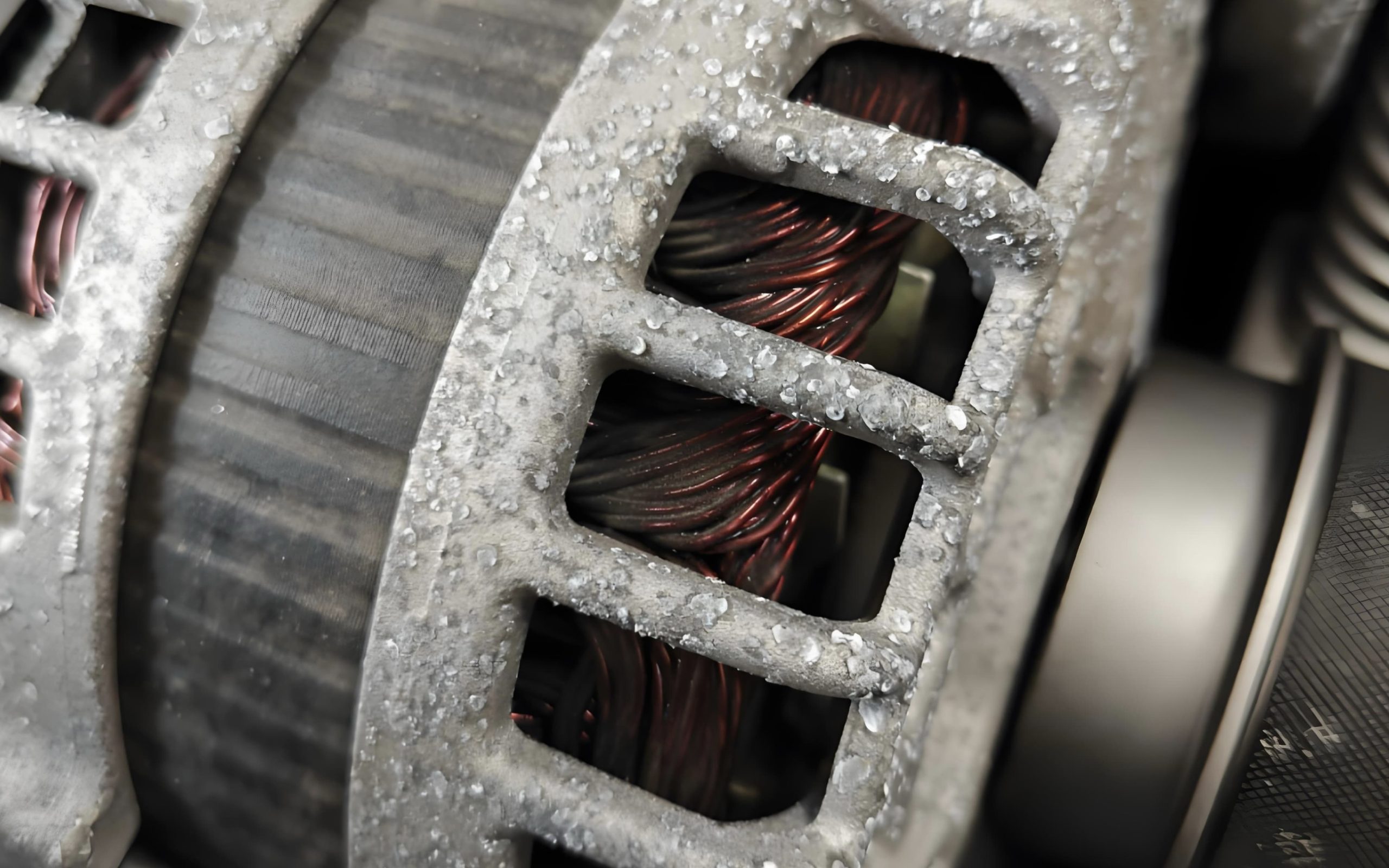
Aerospace industry
Yttria-stabilized zirconia beads are mainly used for surface cleaning, deburring, and strengthening of aircraft parts (such as aircraft engine blades, landing gear, and fuel pipes).
Zirconia beads can not only remove the oxide layer of aluminum but also reduce microcracks and corrosion on the surface of parts. After sandblasting with zirconium beads, the fatigue resistance of aviation parts is improved by 25%, and the service life is significantly extended.
Glass products industry
Zirconium beads are used for the surface frosting of glass products (such as automotive glass and instrument glass) to remove surface microcracks and dirt.
Yttria-stabilized zirconia beads can form a uniform frosted effect on the glass surface and increase the optical transparency by 10%.
Medical device industry
Commonly used for deburring, cleaning, and polishing of surgical instruments (such as surgical scalpels, hemostats, and needles).
Remove tiny burrs on the surface of surgical instruments to ensure that they are free of contamination and reduce bacterial accumulation. The surface roughness of surgical instruments treated with zirconia bead blast is reduced by 40%, and the corrosion resistance of the instruments is effectively improved.
Electronic industry
Yttria-stabilized zirconia beads are used for surface cleaning, deburring, and smoothing of electronic components (such as integrated circuit boards, sensor components, and optical fiber ports).
Zirconia bead blast can accurately remove impurities on the surface of electronic components and reduce short circuits and poor contact problems caused by burrs. Test data shows that after zirconium beads are sandblasted, the stability of electronic components is improved by 12% and the surface defect rate is reduced by 20%.
Precision machinery industry
Zirconia beads are widely used in deburring, cleaning, and strengthening precision machinery parts (such as precision gears, bearings, shafts, etc.).
Effectively improve the surface smoothness of mechanical parts, reduce friction and wear, and improve mechanical efficiency. According to mechanical performance tests, the friction coefficient of precision mechanical parts treated with zirconia bead blast is reduced by 15%, and the service life is extended by 20%.
Chemical Engineering Industry
Zirconium beads are used for surface treatment of chemical reactors, pipelines, valves, and other equipment, mainly used to remove deposits, clean internal and external surfaces, and improve the corrosion resistance of equipment.
The chemical stability of zirconia bead blast makes them excellent in chemical engineering and can clean deposits under high temperature and high-pressure environments. The corrosion resistance of equipment treated with yttria-stabilized zirconia beads is improved by 30%, effectively reducing the maintenance frequency and downtime of equipment.
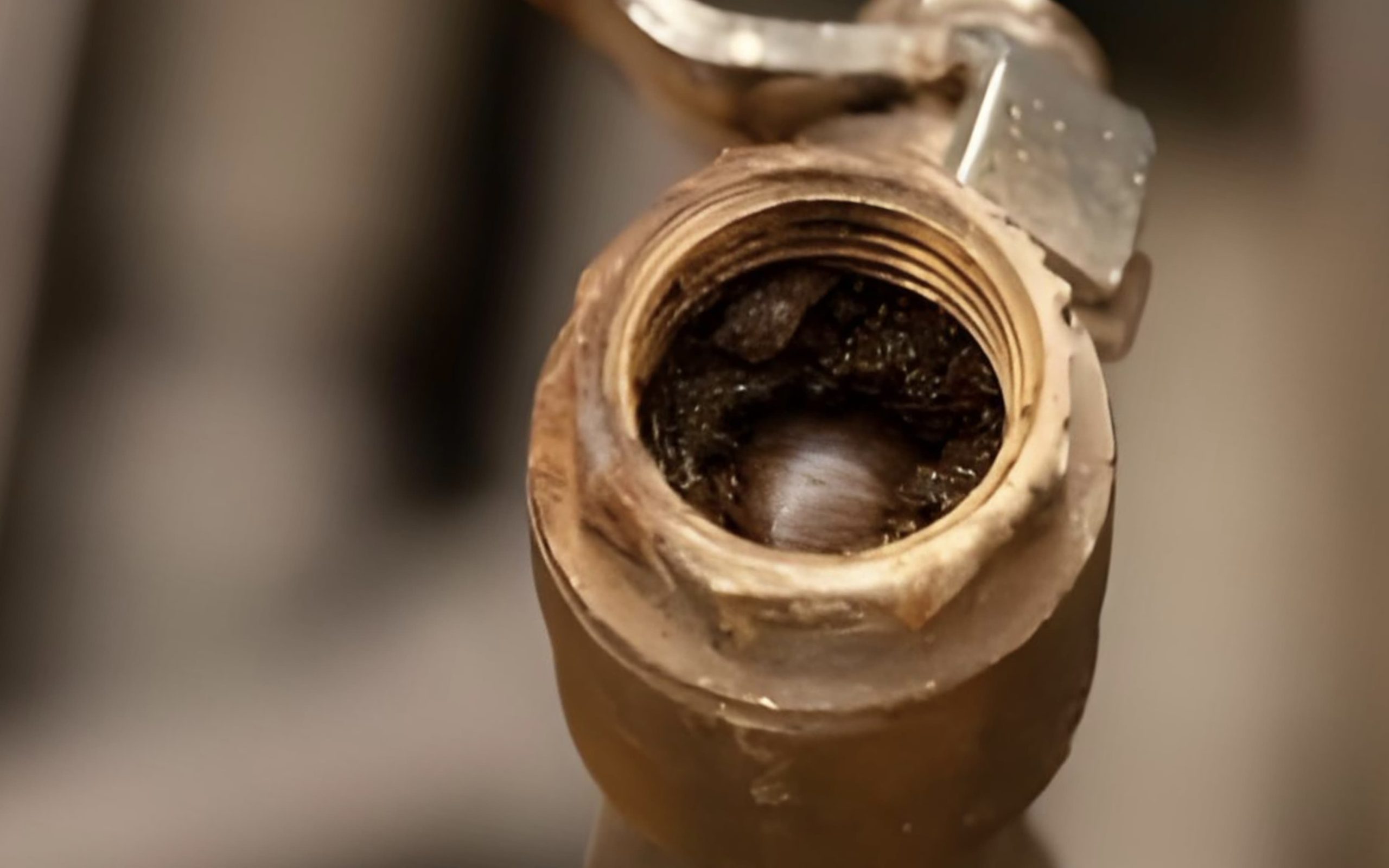
How to choose the right Zirconia Beads?
Choosing the right zirconia bead blast is a key step to ensure the surface treatment effect and improve production efficiency. Different workpiece materials, surface finishing requirements, and operating costs will affect the selected particle size and type. The following are some factors to consider when choosing the right zirconium beads.
-
Consider the workpiece material
Consider the workpiece material
Generally speaking, softer metals (such as aluminum alloys) or plastic materials are suitable for using zirconia bead blast with smaller particle sizes (such as YZ100), which can provide finer surface finishing effects and reduce surface damage.
Whereas hard metals (such as stainless steel) or alloy materials are more suitable for using zircon beads with larger particle sizes (such as YZ300), which can be roughened or strengthened and more efficiently remove thicker oxide layers or dirt.
-
Surface finishing requirements
Surface finishing requirements
If the goal is to obtain a smooth surface or improve gloss, zirconia bead blast with smaller particle sizes is more suitable; if you need to increase surface roughness, enhance coating adhesion, or strengthen treatment, you should choose zircon beads with larger particle sizes.
-
Operating costs
Operating costs
Choose the appropriate zirconia bead model based on the balance between budget and durability. Zircon beads are generally more durable and have a longer service life. Yttria-stabilized zirconia beads with larger particle sizes are relatively cheap, while the smaller the particle size for processing delicate workpieces, the more expensive it is. Choosing the right particle size can help optimize cost-effectiveness.
For mass production, choosing medium-sized zirconia beads (such as YZ150) may achieve a good balance between effect and cost.
Particle size selection recommendation
The following are 3 common zirconium bead models and their applicable scenarios:
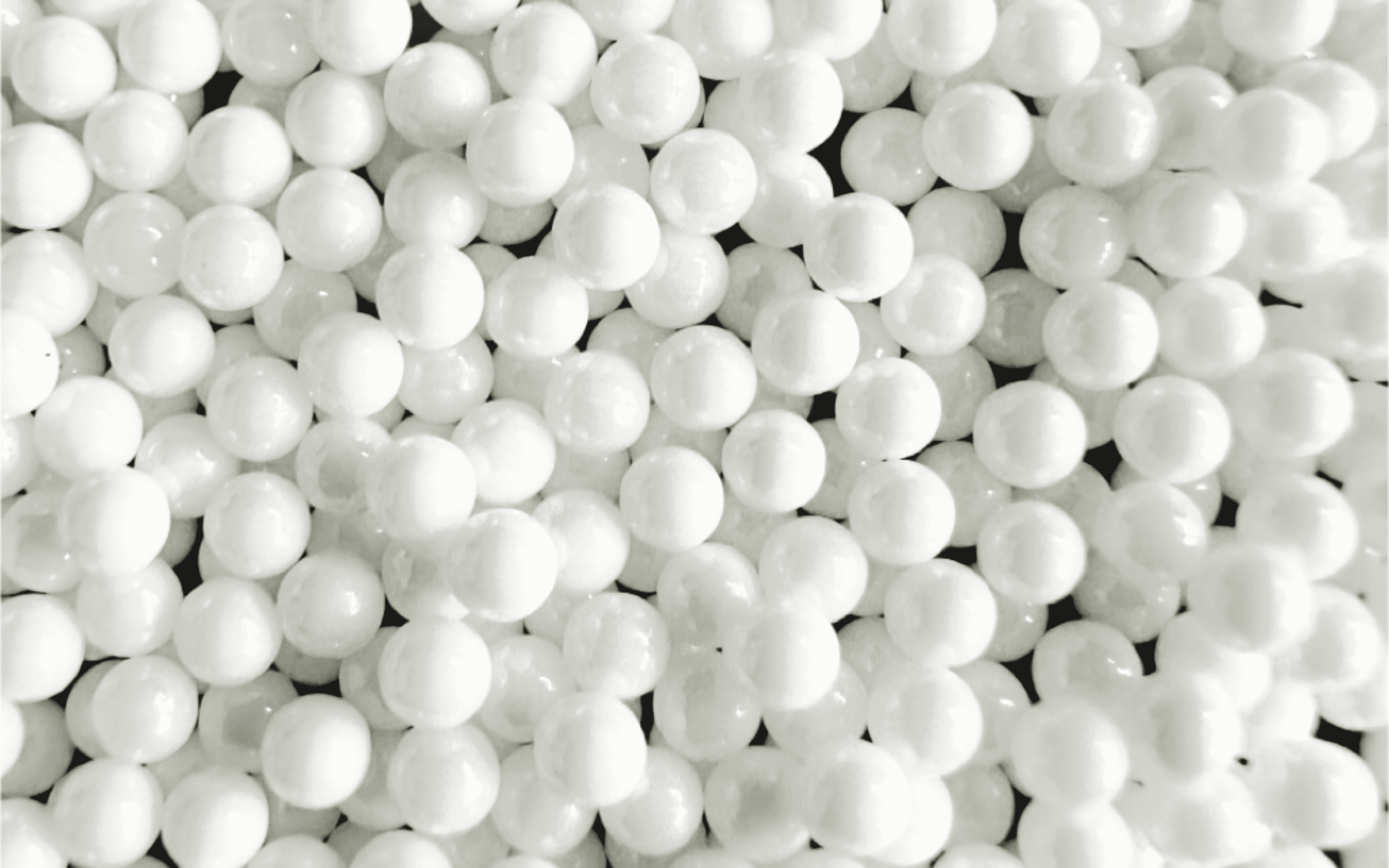
YZ300 (250-300 microns)
- Suitable for rough processing and strengthening of large metal parts, aluminum alloys, and aerospace parts.
- Applicable industries: automobiles, aerospace, and heavy machinery.

YZ100 (80-125 microns)
- Suitable for fine sandblasting and strengthening of medium-sized metal parts, turbine blades, and electronic components.
- Applicable industries: aerospace, electronics, and precision machinery.
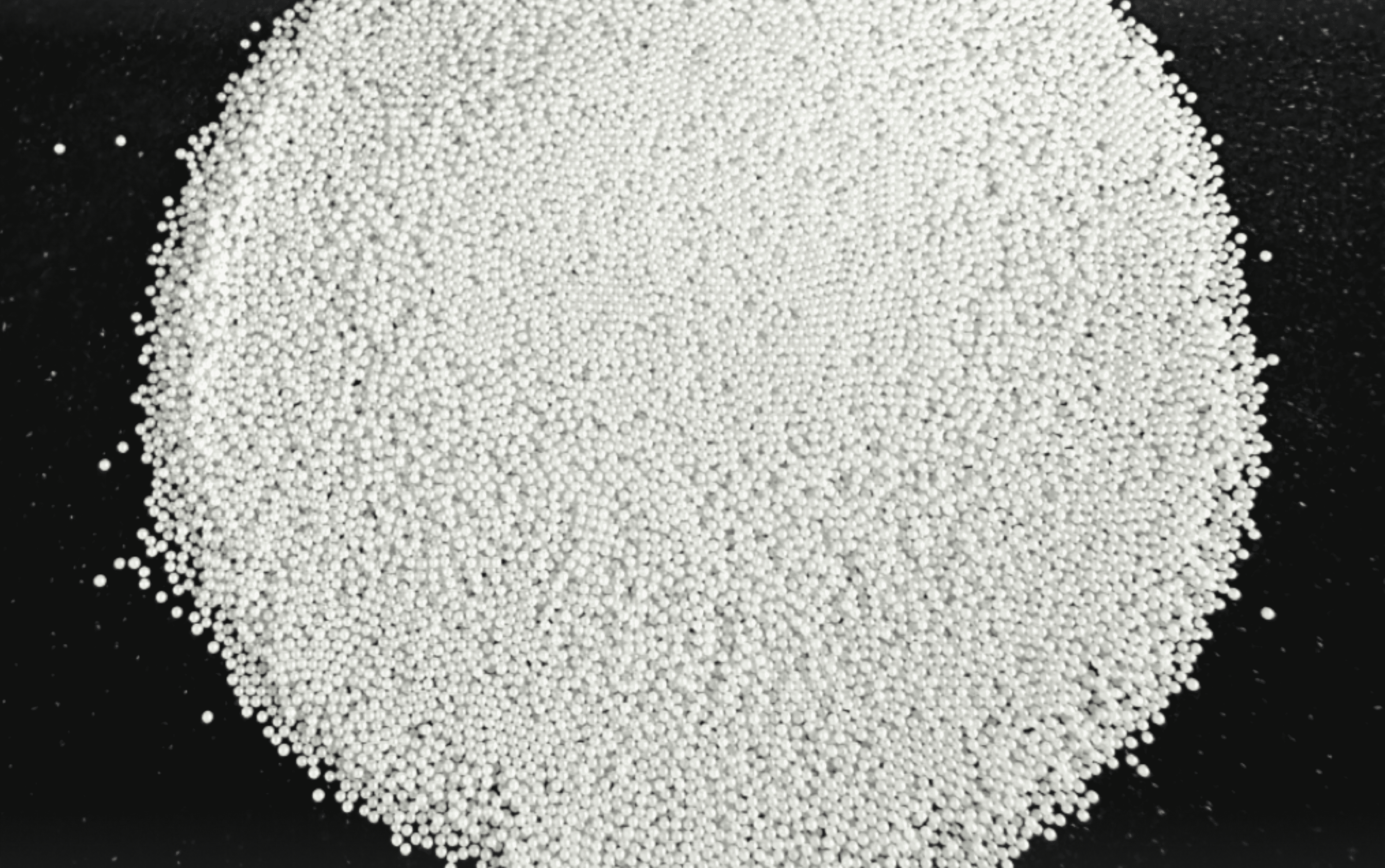
YZ50 (45-90 microns)
- Suitable for precision surface polishing, surgical instruments, jewelry processing, and other smooth surfaces.
- Applicable industries: medical, electronics, and optics.
Larger sizes
We also have larger sizes: 400, 500, 600, 800, 1000, 1250, 1500, 1750, 2000, 2350μm.
- Suitable for extreme surface finishing needs, such as surface strengthening, roughening, etc.
- Applicable industries: steel, building materials, military industry.
Contact us to learn how to use HLH’s Zirconia Beads to improve production efficiency!
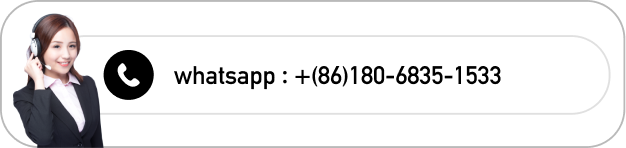