Why are urea plastic media ideal for cleaning sensitive parts?
November 22, 2024
Cleaning and refurbishing sensitive parts is challenging in the industrial sector, especially in the aerospace, automotive, marine, and heavy machinery industries. Due to their high-performance requirements and precision design, these parts must be handled carefully to avoid damaging or changing their critical properties.
Type II urea plastic media, with its unique low hardness and controlled cleaning capabilities, is an important solution in these scenarios:
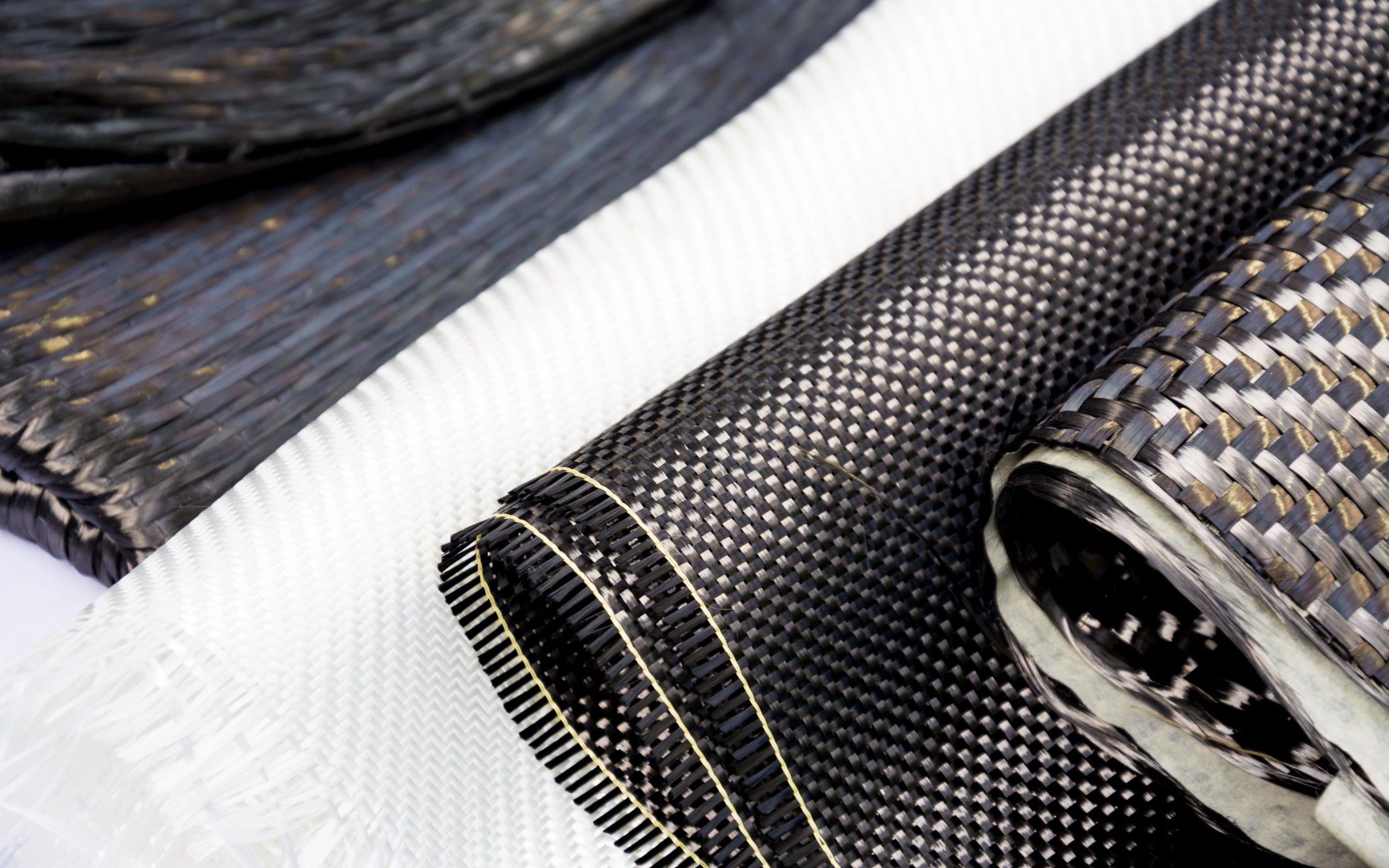
Aerospace
- Turbine blades: complex materials, crucial surface coatings, aerodynamic properties, and high-temperature resistance must be maintained.
- Fuselage composite parts: such as carbon fiber and aluminum alloys, material fatigue, or fiber breakage must be avoided during cleaning.
- Internal engine parts: oxide or paint layers need to be cleaned, but the surface coating must not be damaged.
Automotive
- Aluminum body panels: lightweight aluminum parts are covered with a thin coating to prevent corrosion, but the surface is easily scratched.
- Magnesium alloy parts: such as wheels and engine parts, are soft materials, and deformation or surface roughening must be prevented during cleaning.
- Plastic bumpers: covered with a light layer of paint, the plastic substrate needs to be protected when used for refurbishment or repainting.

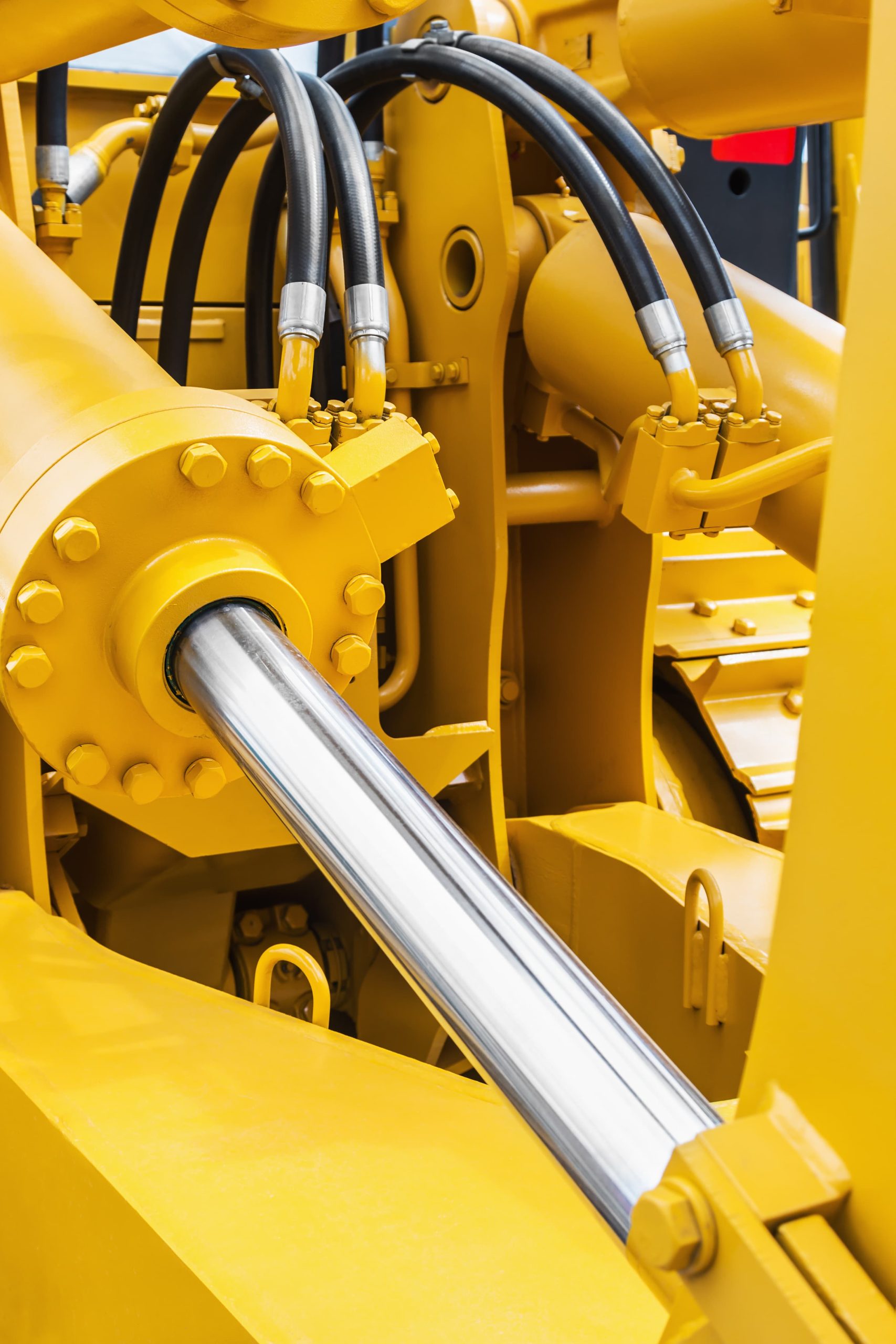
Ships
- Lightweight composite parts: such as hull panels and hatch covers, usually need to be cleaned regularly to maintain performance.
- Propellers and propulsion systems: Underwater dirt and coatings need to be removed to avoid damaging the surface finish or coating adhesion.
Heavy machinery
- Precision molds: Surface coatings or residues need to be completely cleaned, and the mold shape and texture need to be avoided.
- Hydraulic system components: such as piston rods and cylinder bodies, are needed to avoid dimensional deviations and performance damage.
It is not difficult to find that these parts’ complex structures and special materials put extremely high demands on the cleaning process. When removing the surface coating, it is necessary to ensure that the coating can be completely removed and to avoid damaging the substrate’s surface characteristics or functional properties. Therefore, it is essential to choose the right sandblasting media.
Type II urea blasting media, with its unique physical and chemical properties, has become an ideal solution to meet these needs.
Core advantages of urea plastic media
Suitable for sensitive surfaces
Type II urea blasting media, with its low hardness (Mohs hardness 2.5-3.5) and lightweight characteristics, can achieve gentle cleaning and avoid surface scratches or deformation of sensitive parts (such as carbon fiber, aluminum, magnesium and other soft metals, composite materials, and plastic parts).
Efficient removal of thin coatings
Urea resin is designed for removing thin coatings (such as anodized films, anti-corrosion thin layers of coatings, aged paint, or varnish surfaces). Its granular form is usually irregular particles. Different particle sizes can be selected according to the needs of the workpiece to provide different cleaning strengths and fineness.
Due to its chemical inertness, it is not easy to react chemically with the surface coating during use, and can effectively strip the coating without damaging the substrate.
Easy to clean complex geometric structures
It is known that urea resin is usually irregular or small granular in shape, which enables it to enter complex grooves, corners, and other hard-to-reach parts of parts. During the cleaning process, the particles can effectively adhere to the surface of the coating and use their friction to remove the coating while avoiding damage to the substrate due to the hard material.
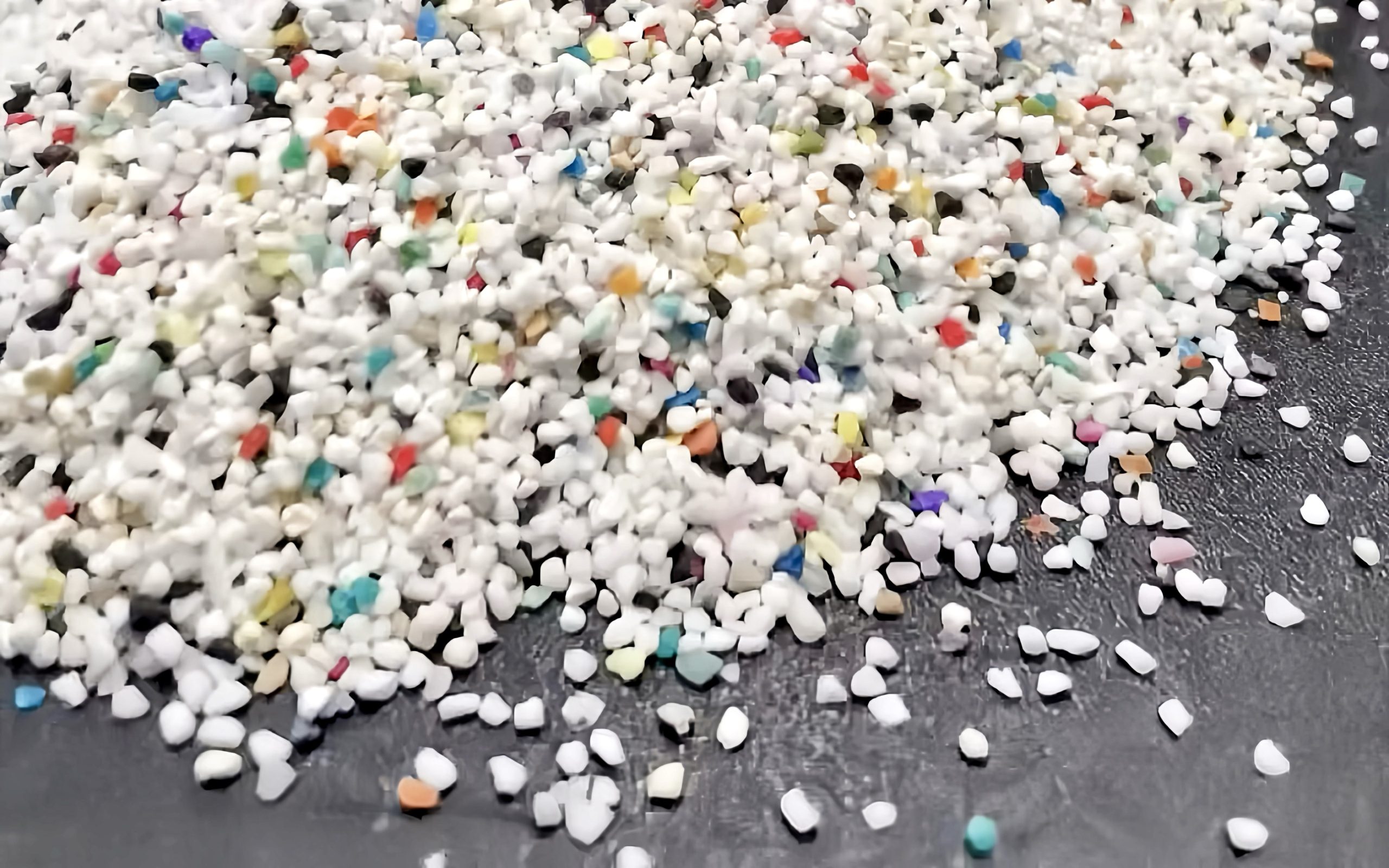
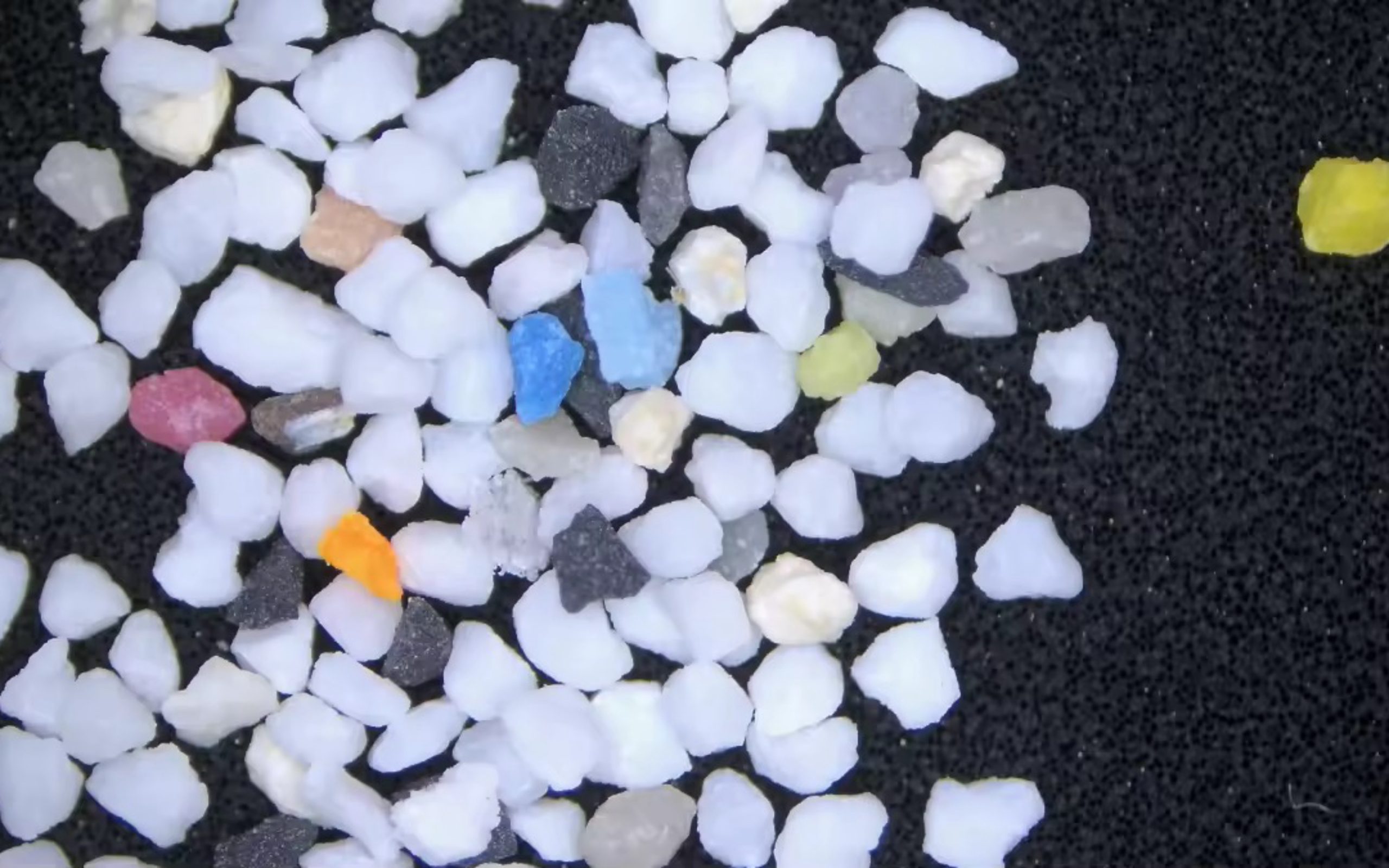
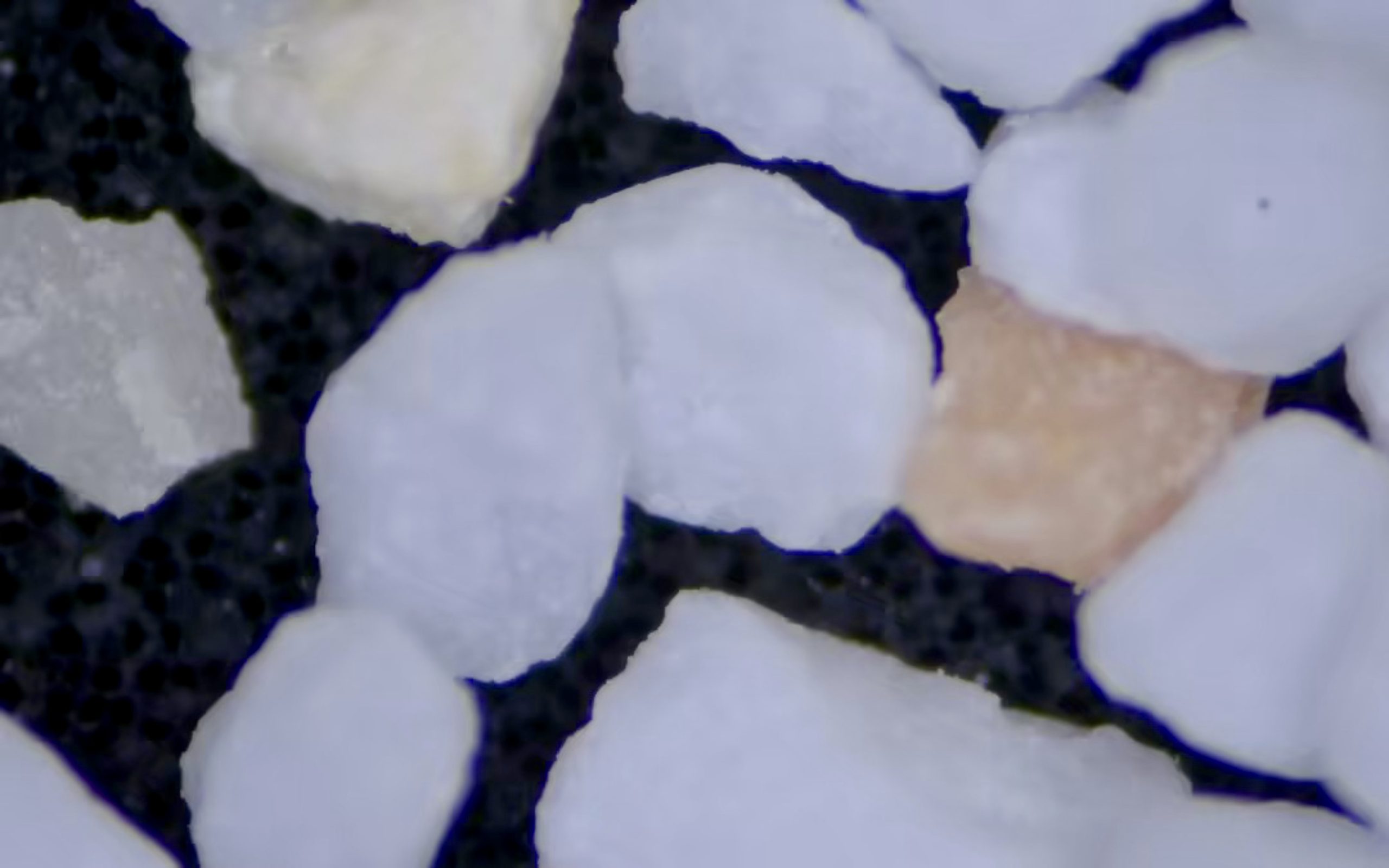
Reduce the risk of thermal effects
Compared with other sandblasting media with the same function (such as glass beads, etc.), urea resin has a smaller impact force, which reduces the heat accumulation caused by friction during the sandblasting process, thereby avoiding thermal deformation or material degradation of sensitive workpieces.
High operational safety
Urea resin is dust-free, non-toxic, and environmentally friendly, and will not cause adverse effects on operators and the working environment. Our urea resin also has special anti-static properties, which greatly reduces the problem of static electricity accumulation during the treatment process and ensures its wide application in industries with high safety standards.
Economic and repeatable
The medium has strong wear resistance, can still maintain its performance after multiple uses, and has excellent economic efficiency.
These advantages make Type II blast media an ideal choice for processing sensitive parts such as aviation and automobiles and show unparalleled results in the surface treatment of workpieces.
Why not other media?
Some media have some or even more overlap with urea resin in terms of function, but each has its limitations in the surface treatment of sensitive parts. I will explain to you why these media have limitations in application scenarios and how Type II blast media stand out with its unique advantages.
Type I Plastic Media
Also a plastic substrate, it has the characteristics of lightweight and softness, suitable for processing sensitive workpieces with high surface protection requirements, which is partially consistent with the application scenarios of urea resin.
Application Scenarios
- Aerospace: Surface cleaning and coating removal of composite materials and light metal parts.
- Electronics industry: Decontamination and fine treatment of the surface of small electronic components.
- Automotive industry: Removal of plastic parts and light coatings, such as bumpers, dashboard parts, etc.

Features
- Moderate hardness, suitable for a wide range of coating cleaning.
- High operational flexibility, support for a variety of equipment, and adapt to surface treatment tasks of different sizes.
Disadvantages
- Relatively brittle, easy to break during sandblasting, and may cause uneven cleaning effects on sensitive workpiece surfaces.
- Hardness and density are relatively high, and the efficiency of cleaning thin coatings or contaminants is not as good as Type II plastic media.
- When processing sensitive materials that require a high finish, a rougher surface texture may be left, which does not achieve the expected effect.
Class Beads
Glass beads and Type II urea plastic media are similar in some applications and are used for sandblasting of sensitive materials, especially in scenarios where a high surface finish is required and slight coatings or contamination are removed.
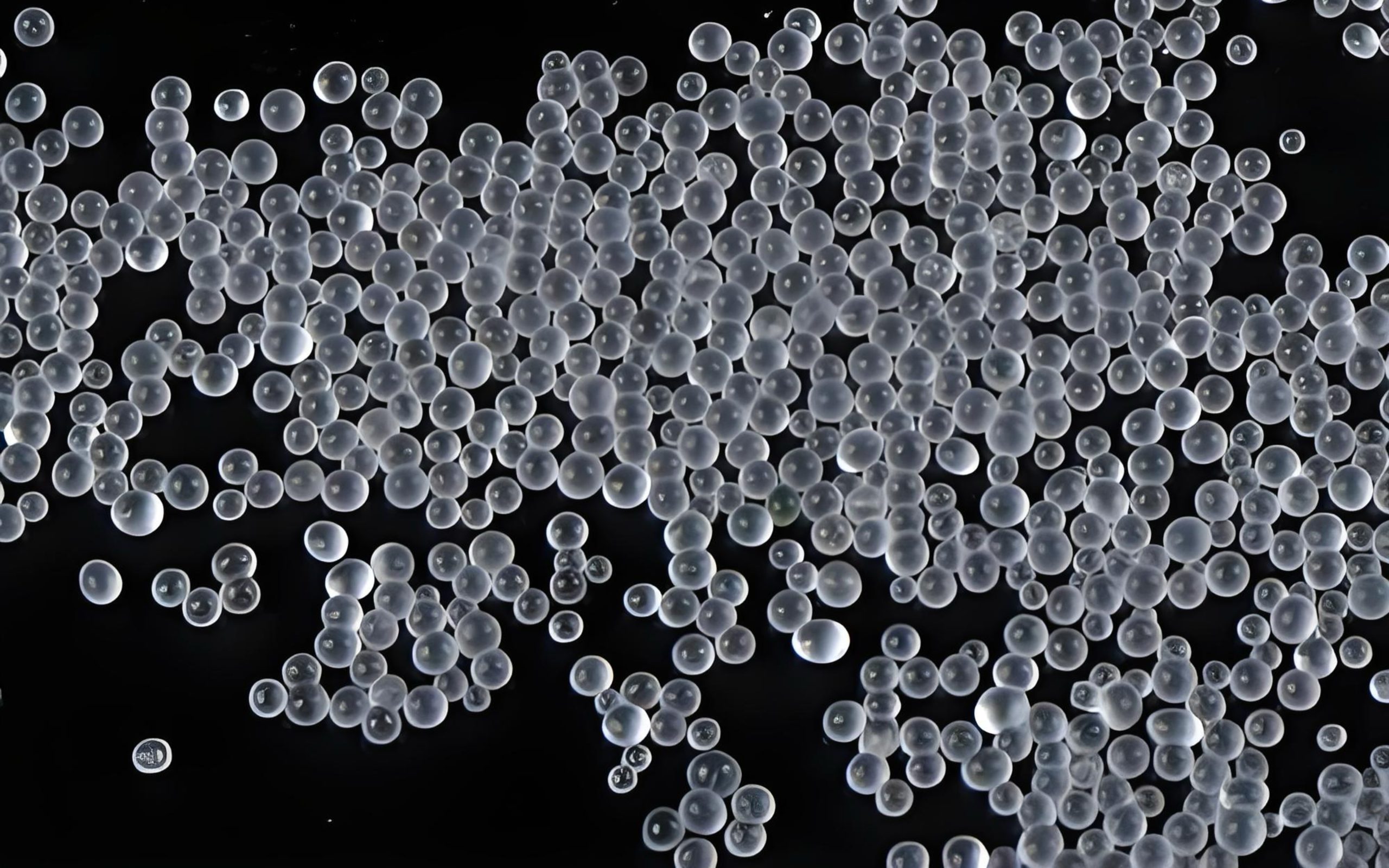
Application scenarios
- Aerospace: smooth surface treatment of aircraft parts.
- Automotive industry: surface polishing and light dirt removal.
- Industrial molds: surface cleaning and finish improvement, especially molds that require fine grinding.
Features
- Medium hardness: Mohs hardness 5~6, suitable for removing oxide scale, light dirt, and thin coatings.
- Smooth spherical structure: reduces direct cutting action on the surface, gentle cleaning without easily damaging the substrate.
- Strong chemical inertness: no chemical corrosion to sensitive materials (such as aluminum, magnesium alloys, etc.).
Disadvantages
- Compared with urea resin, glass beads are still harder and may cause minor scratches or wear on ultra-sensitive materials (such as flexible plastics, thin film coatings, or soft metals).
- The particle density and weight are large, and the ability to clean complex geometric structures is limited.
- The unit cost of glass beads is higher than that of plastic media, and the overall economics are inferior to urea resins due to the higher unit cost of glass beads and the higher equipment pressure requirements.
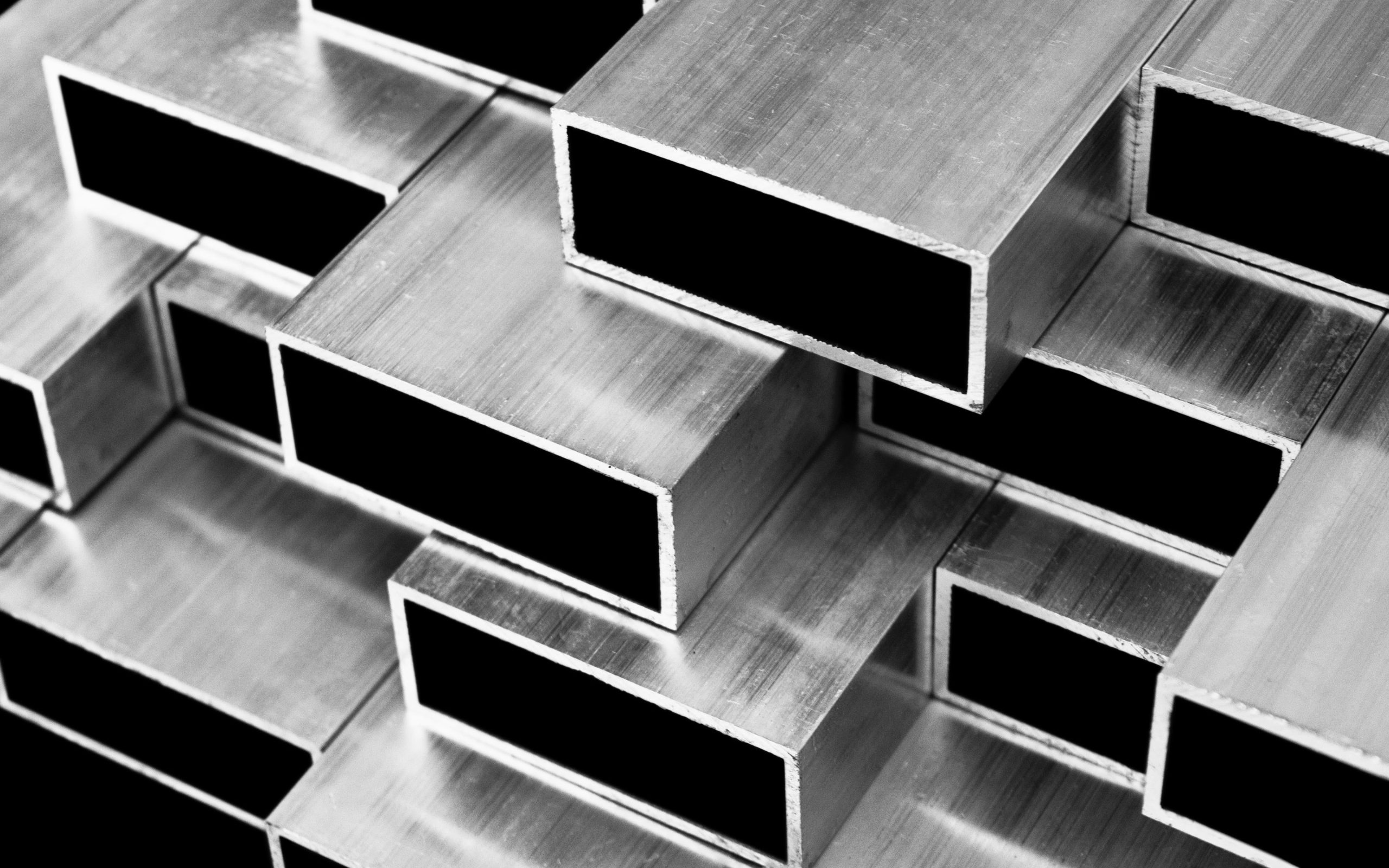
Microblast Ceramic Blasting Beads
Microblast Ceramic Blasting Beads have tough and uniform particles and are commonly used in the aerospace and automotive industries. It and urea resin both emphasize the protection of the surface integrity of the workpiece and are suitable for polishing soft parts and removing light dirt.
Application Scenarios
- Aerospace: Precision surface cleaning and finish optimization of aircraft parts.
- Automotive industry: Sandblasting and polishing of automotive parts.
- Industrial parts: Surface strengthening and cleaning of metal parts.
Features
- Strong durability: Long-term repeated use, stable performance, low breakage rate.
- Strong cleaning effect: Quickly and effectively remove surface coatings and contaminants.
Disadvantages
- High hardness requires strict control of sandblasting parameters, otherwise it is easy to cause excessive surface cleaning or damage to the material.
- Medium to high sandblasting pressure is required to achieve optimal performance, and it is not flexible enough when dealing with sensitive parts that require low-pressure operation or precise coating removal.
- The particles are dense and regular in shape, making it difficult to fully enter small grooves or corner structures.
After understanding the shortcomings of these common media, I will explore the application of urea plastic media through actual case analysis.
Specific case analysis
Case 1: Aerospace surface coating removal
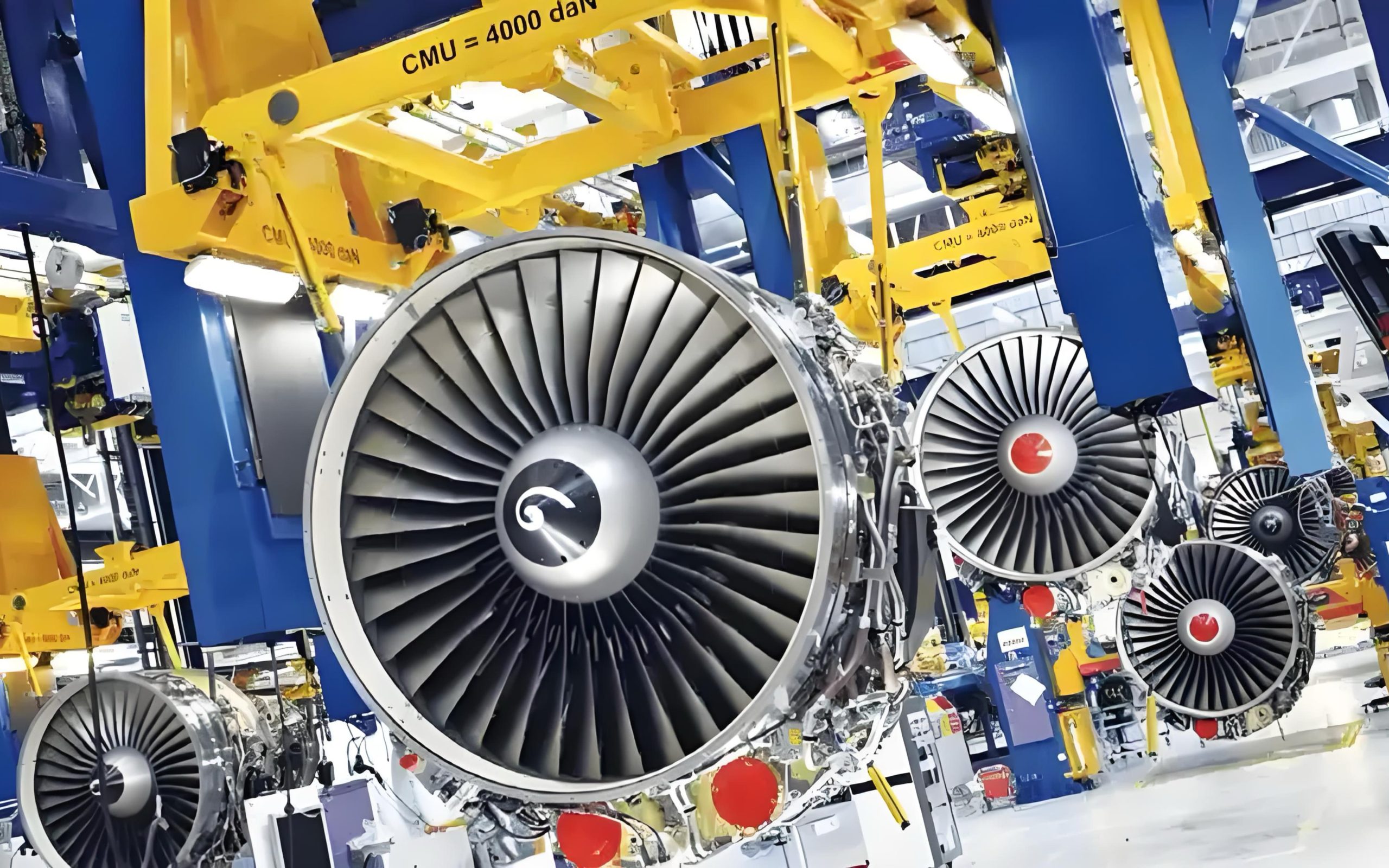
- Background: Composite surfaces in the aerospace field often need to be cleaned or coated regularly, but their substrates are very fragile and have limited tolerance to hardness and friction.
- Problem description: Traditional sandblasting media (such as ceramic sand or aluminum oxide) make it easy to scratch the surface of composite materials due to their high hardness, and even destroy their performance. In addition, some media will produce high dust during the cleaning process, which is not conducive to the operating environment.
- Solution: After using Type II blast media, the surface of the composite material remains intact and the cleaning efficiency is improved by 30%. At the same time, its low dust characteristics greatly improve the cleaning environment.
Case 2: Surface cleaning and refurbishment of automotive parts
- Background: During the refurbishment or reuse of automotive plastic parts (such as bumpers), it is often necessary to remove old coatings or surface contaminants.
- Problem description: Traditional hard media can easily scratch the surface of plastic parts, while low-hardness media such as glass beads are inefficient, resulting in longer processing time and increased costs.
- Solution: In actual applications, the customer completed the refurbishment of 2,000 bumpers using Type II urea plastic media, shortening the processing time by 40%, and the surface gloss of the parts fully met production requirements.

Case 3: Safe cleaning of medical devices
- Background: The outer shell of medical devices is usually made of precision plastics, which have extremely high requirements for surface cleanliness and safety.
- Problem description: Traditional media are easy to remain on the surface of the device, posing a risk of contamination; at the same time, improper cleaning methods may damage the precision structure and affect performance.
- Solution: Type II blast media is not only non-toxic and environmentally friendly but its low hardness and easy-to-clean characteristics also ensure the safety and integrity of medical devices. After using urea plastic media, the customer effectively improved the cleaning efficiency of the equipment, while ensuring the safety of the product, and was able to successfully pass the ISO certification audit.
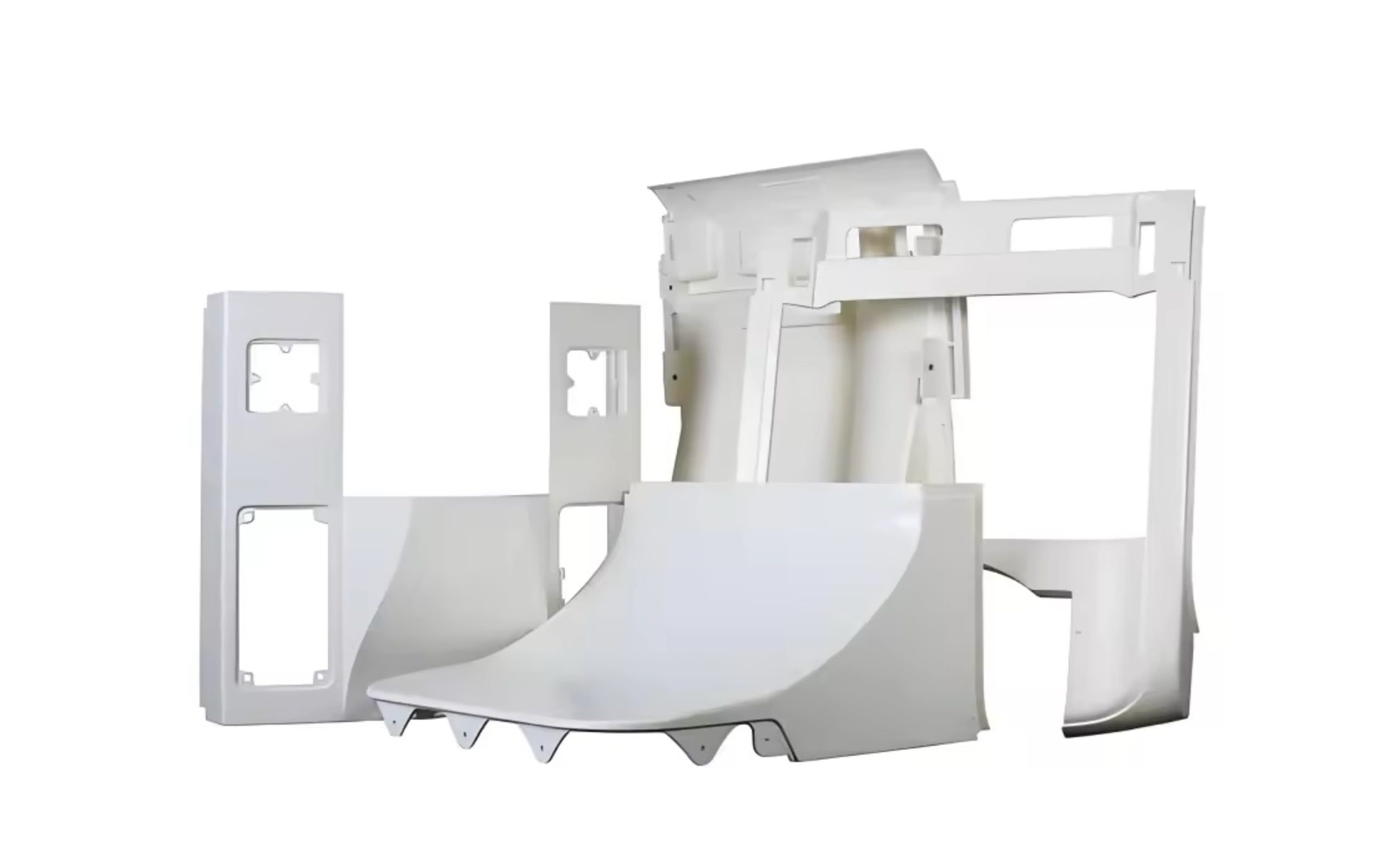
Common customer problems and solutions
- Improper control of cleaning force (excessive/inadequate)
The hardness of urea plastic media is moderate and controllable, and the cleaning force can be precisely adjusted to achieve efficient and non-damaging surface treatment effects.
- Scratches or corrosion on sensitive substrate surfaces
Type II urea plastic media has a gentle cleaning performance and can effectively protect sensitive substrates, especially for high-demand appearance parts.
- Environmental protection and dust control requirements
Type II blast media has extremely low dust generation during processing and use, meets environmental protection requirements, and helps customers save post-processing costs.
- Cleaning efficiency in complex geometric structures
Type II plastic media can penetrate every corner of complex structures due to its light particles and strong fluidity, ensuring comprehensive cleaning.
- Excessive cost (including material and equipment loss)
Urea plastic media has high durability and supports multiple cycles; its low hardness can also reduce equipment loss and significantly reduce long-term costs.
- Low material recycling rate
Type II urea plastic media has excellent recycling performance. Through reasonable screening and cleaning, it can be used multiple times, which effectively improves the material utilization rate.
- Multiple specifications of media are required to adapt to the diverse applications of different workpieces
We provide Type II blast media with a variety of particle sizes and shapes and can tailor solutions according to customer needs.
- Insufficient operational safety (high static electricity or toxic dust)
Type II urea plastic media is non-toxic, environmentally friendly, and has anti-static properties, which greatly improves the safety of operation.
Why choose our urea plastic media?
As a professional surface treatment solution provider established in 2001, we have won industry recognition and customer trust with high-quality products and excellent services for more than 20 years.
The following points reflect the unique advantages of our Type II urea plastic media:
Internationally certified, quality guaranteed.
Each of our products strictly follows the international quality and environmental management system and has passed ISO 9001:2015 quality management system certification and ISO 14001 environmental management system certification. This not only proves the consistency and reliability of our products but also ensures their environmental performance.
Stable and reliable product performance
Our Type II urea plastic media are made of polymer materials, with low hardness, high durability, environmental protection, and non-toxicity, which greatly reduces the cost of use for customers. At the same time, we support customized particle specifications according to customer needs to ensure that each product can perfectly match the application scenario.
Antistatic treatment to ensure safety and efficiency
In response to the common static risks in industrial environments, our urea plastic media have undergone special antistatic treatment. This feature greatly reduces the impact of static electricity accumulation on production efficiency and improves operational safety.
Special design for sensitive parts
With a moderate hardness of 2.5-3.5 on the Mohs scale, our media can achieve the goal of “effectively removing the coating without damaging the substrate” during the cleaning process. It is suitable for a wide range of industries, especially for cleaning sensitive parts in high-standard industries such as aerospace and automobiles.
By choosing our Type II urea plastic media, you will get not only high-quality sandblasting materials but also a reliable partner to help you achieve greater success in industrial surface treatment.
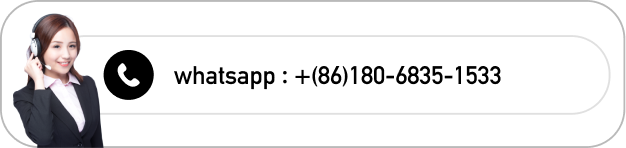