Which sandblasting media are suitable for my workpiece?
September 26, 2024
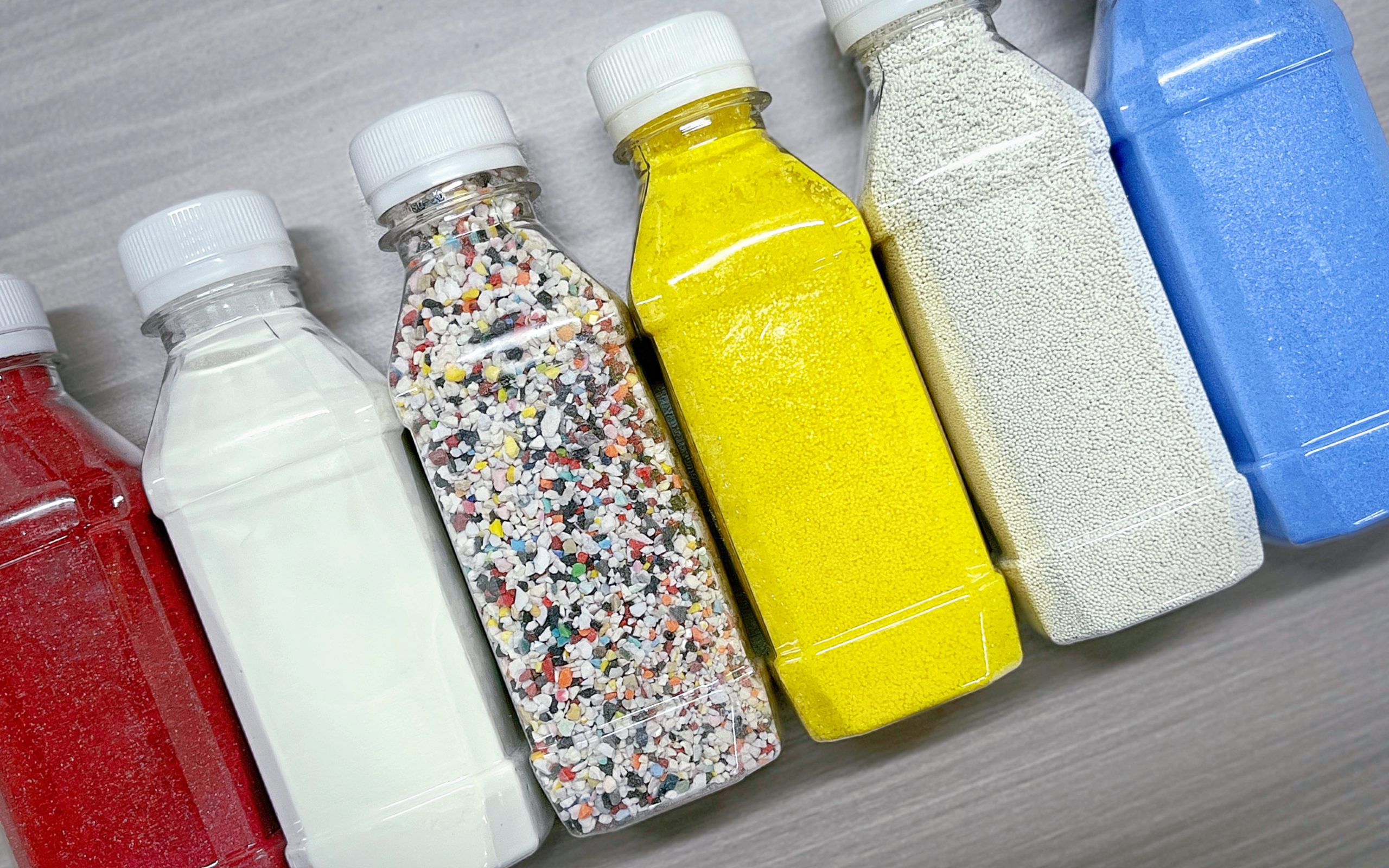
In modern manufacturing, sandblasting is an efficient surface treatment method widely used in the processing of various materials such as metals, plastics, and ceramics. Choosing the right sandblasting media is crucial to improving product quality and extending the service life of workpieces. However, the wide variety of sandblasting media on the market makes users confused when choosing. This article will explore in depth how to scientifically select the right sandblasting media based on the material, surface requirements, size and shape, processing purpose, thickness and strength, as well as environmental protection and economic benefits of the workpiece to ensure the best processing effect.
First of all, when choosing the sandblasting media suitable for the workpiece, multiple factors need to be considered. Here are some key conditions I listed:
- Workpiece material: Workpieces of different materials have different requirements for the hardness and type of sandblasting media. Understanding the material characteristics of the workpiece can help choose the most suitable sandblasting media.
- Workpiece surface requirements: Select the right media according to the requirements for the surface finish of the workpiece.
- Workpiece size and shape: Complex shapes or precision workpieces require the selection of sandblasting media with smaller and softer particles to prevent excessive wear or surface damage.
- Processing purpose: Different workpiece processing purposes (such as deflashing, surface cleaning, or polishing) require different types of media.
- Workpiece thickness and strength: Thin or fragile workpieces require mild media, otherwise the workpiece may be damaged. Thicker or durable workpieces can withstand stronger impact.
- Environmental protection and process requirements: Some industries (such as medical devices and food processing) have high requirements for cleanliness, so it is necessary to choose pollution-free and recyclable sandblasting media.
According to these conditions, customers can better match the appropriate sandblasting media to ensure the best processing effect and extend the service life of the workpiece. Let’s take a closer look at the performance comparison of common media and the specific breakdown of each condition.
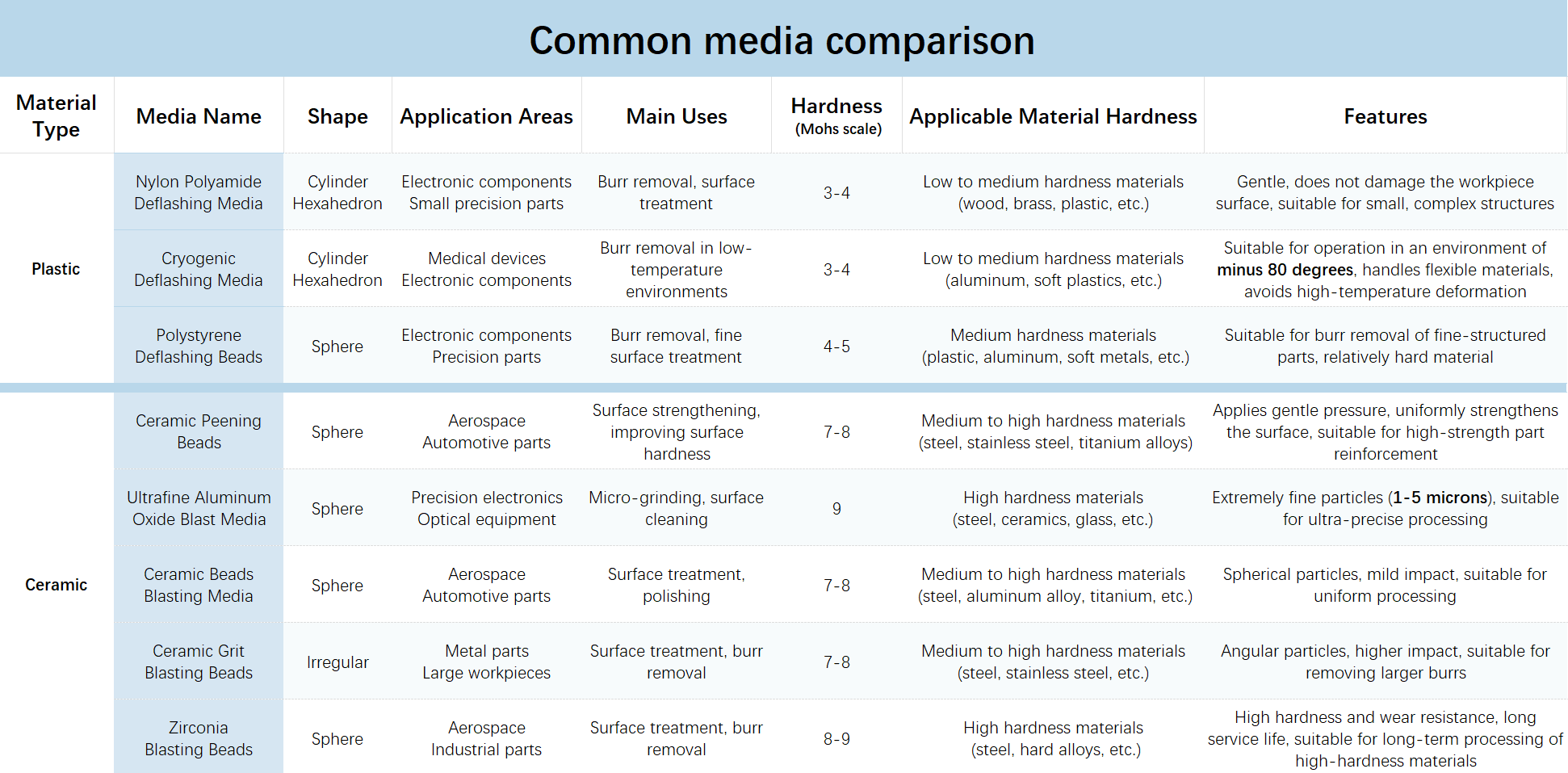
Workpiece material
- Metal materials: such as aluminum, steel, copper, etc., are usually hard, and sandblasting media with higher hardness can be used.
– Features: Metal materials are wear-resistant and are suitable for hard media such as steel grit or aluminum oxide, which can effectively remove surface dirt and rust.
– Applicable products: Ultrafine aluminum oxide blast media, ceramic peening beads, zirconia blasting beads.
- Plastics and soft materials: such as polypropylene, polyurethane, nylon, etc., are suitable for softer sandblasting media.
– Features: Plastic materials are easily damaged, and mild media should be selected to avoid scratching the surface.
– Applicable products: Nylon polyamide deflashing media, polystyrene deflashing beads.
- Ceramic materials: such as alumina ceramics, silicon nitride, etc., have strong wear resistance.
– Features: Ceramic materials usually have smooth surfaces and are suitable for precision machining.
– Applicable products: Zirconia blasting beads, ceramic grit blasting beads.
- Composite materials: such as carbon fiber, glass fiber, etc., are usually fragile.
– Features: Composite materials have high strength and rigidity, but are susceptible to excessive wear.
– Applicable products: Cryogenic deflashing media, ceramic beads blasting media.
Workpiece surface requirements
- Smooth surface: Fine sandblasting media is required to avoid surface scratches.
– Features: Smooth surfaces are usually used for parts with high visual beauty or functional requirements.
– Applicable products: Ultrafine alumina sandblasting media, polystyrene deflashing beads.
- Rough surface: A harder medium may be required to remove surface impurities.
– Features: The treatment of rough surfaces may require more abrasive force.
– Applicable products: Ceramic shot blasting, ceramic grit blasting beads.
- Special surface treatment: Pre-treatment such as spraying and anodizing.
– Features: Ensure that the surface is clean for the effect of subsequent processes.
– Applicable products: Cryogenic deflashing media, zirconia blasting beads.
- Coated surface: When treating zinc-plated, chrome-plated, and other surfaces, it is necessary to choose a suitable medium.
– Features: Avoid damage to the coating and maintain surface quality.
– Applicable products: Polystyrene deflashing beads, ceramic beads blasting media.
Workpiece size and shape
- Small parts: For electronic components, it is suitable to use media with smaller particle sizes.
– Features: Fine sandblasting can enter tiny gaps to ensure comprehensive cleaning.
– Applicable products: Nylon polyamide deflashing media, cryogenic deflashing media, ultra-fine aluminum oxide sandblasting media.
- Large parts: For mechanical parts, it is more appropriate to use medium-sized media.
– Features: It can withstand greater wear, but still needs to maintain a certain degree of mildness.
– Applicable products: Ceramic grit blasting beads, ceramic shot blasting.
- Complex geometric shapes: For parts with curved surfaces or holes, a gentle medium needs to be selected.
– Features: Prevent excessive wear or surface damage and ensure shape integrity.
– Applicable products: Cryogenic deflashing media, polystyrene deflashing beads.
- Flat workpieces: For example, metal plates, and larger particles can usually be used.
– Features: High processing efficiency, suitable for rapid surface burr removal.
– Applicable products: Ceramic beads blasting media, zirconia blasting beads.
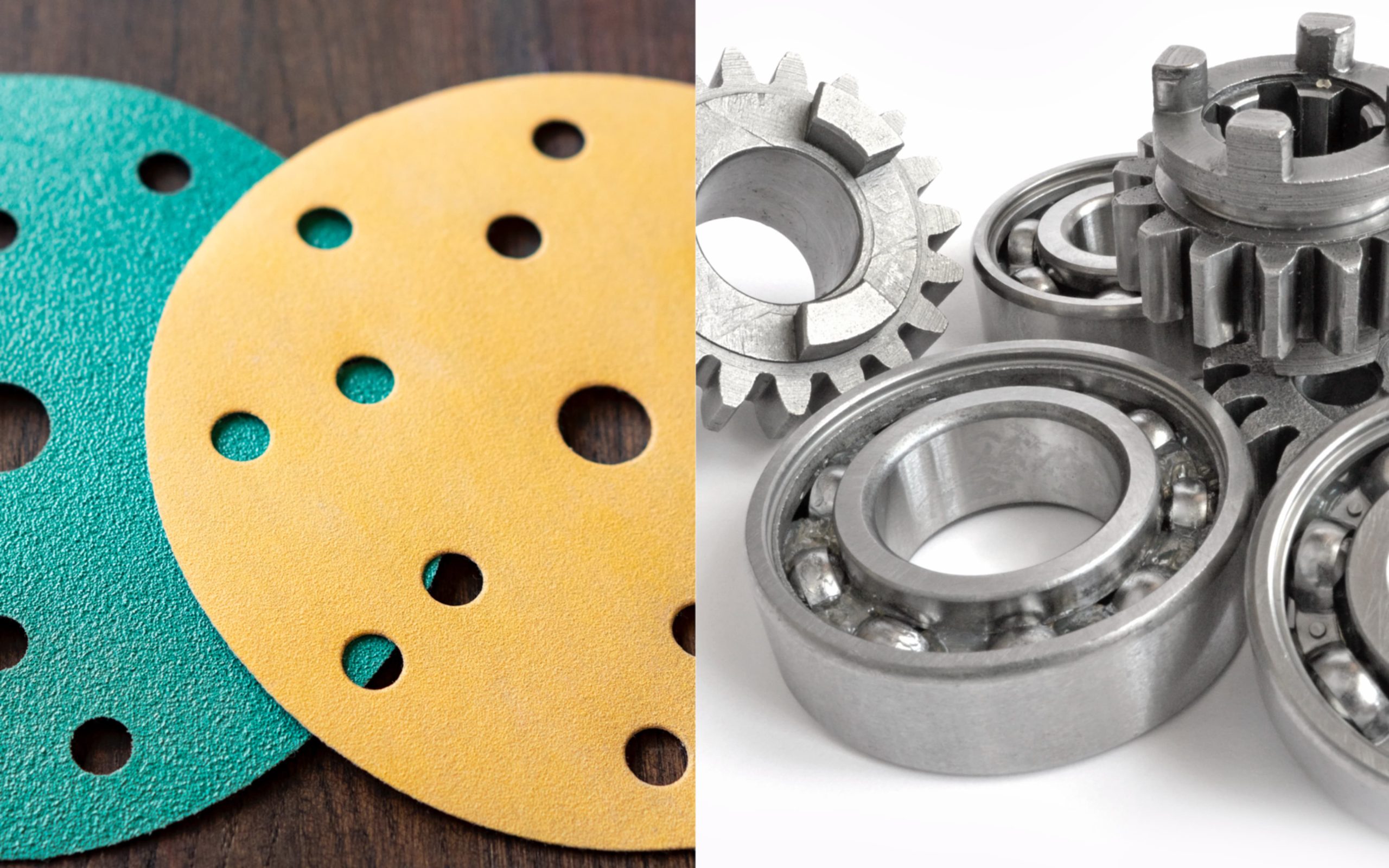
Simple and complex parts comparison
Processing purpose
- Deflashing: Select a medium that can effectively remove burrs.
– Features: Usually a harder or medium hardness medium is required.
– Applicable products: Ceramic shot blasting, nylon polyamide deflashing media.
- Surface cleaning: Remove impurities such as oil, rust, etc.
– Features: A mild-medium can be used to protect the surface of the workpiece.
– Applicable products: Polystyrene deflashing beads, cryogenic deflashing media.
- Polishing: Improve surface finish and enhance aesthetics.
– Features: Use finer media to avoid scratches.
– Applicable products: Ultrafine aluminum oxide blast media, ceramic grit blasting beads.
- Strengthening treatment: Such as shot peening to increase the surface hardness of the workpiece.
– Features: Increase surface strength through the impact of hard media.
– Applicable products: Ceramic peening beads, zirconia sandblasting beads.
Workpiece thickness and strength
The thickness and strength of the workpiece directly affect the selected media.
- Thin workpieces: Such as films and thin plates, use mild media.
– Features: Vulnerable, choose softer media to prevent cracks.
– Applicable products: Polystyrene deflashing beads, cryogenic deflashing media.
- Thick workpieces: For large mechanical parts, stronger media can be used.
– Features: Able to withstand stronger impact to ensure effective processing.
– Applicable products: Ceramic peening beads, zirconia sandblasting beads.
- Fragile workpieces: Such as glass and ceramics, use fine media.
– Features: Avoid breakage and maintain surface integrity.
– Applicable products: Ultrafine aluminum oxide blast media, polystyrene deflashing beads.
- High-strength workpieces: such as cemented carbide, suitable for high-hardness media.
– Features: Strong impact can be used to remove burrs.
– Applicable products: Ceramic grit blasting beads, zirconia blasting beads.
Environmental protection and process requirements
Specific industries have high requirements for cleanliness and environmental protection.
- Medical devices: Extremely high requirements for cleanliness, and non-polluting media are required.
– Features: Ensure that there is no contamination or residue on the product.
– Applicable products: Cryogenic deflashing media, polystyrene deflashing beads.
- Food processing: Also requires non-polluting materials to ensure food safety.
– Features: Sandblasting media must be certified to strict hygiene standards.
– Applicable products: Cryogenic deflashing media.
- Electronic components: Special requirements for anti-static and cleanliness.
– Features: Avoid electrostatic damage while keeping the surface clean.
– Applicable products: Nylon polyamide deflashing media, ceramic grit blasting beads.
- Environmental regulations: Sandblasting media that complies with local regulations to reduce environmental impact.
– Features: Recyclable or non-toxic materials should be selected to reduce ecological risks.
– Applicable products: Cryogenic deflashing media, ceramic grit blasting beads.
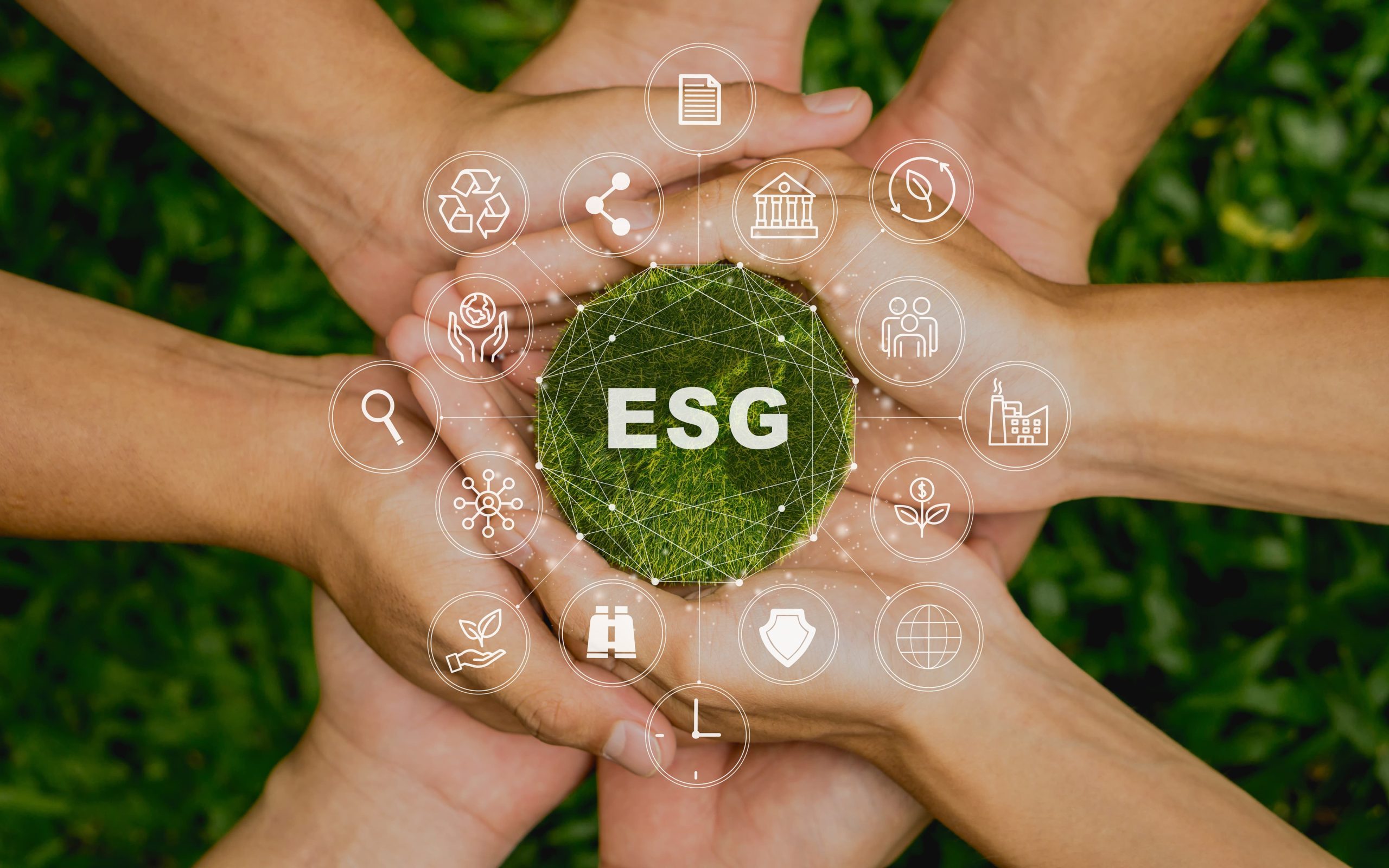
In addition, the selection of sandblasting equipment, sandblasting technology and methods, economy, and efficiency are also factors that need to be considered.
Selection of sandblasting equipment
Choosing the right sandblasting equipment is crucial to the effectiveness of the sandblasting process. Different equipment types are suitable for different sandblasting media and workpiece characteristics.
- Pneumatic spray gun:
– Features: High flexibility, suitable for small and complex-shaped workpieces.
– Advantages: Simple operation, uniform sandblasting effect, suitable for delicate workpiece processing.
– Applicable products: Nylon polyamide deflashing media, Ceramic grit blasting beads.
- Gas jet machine:
– Features: Can be mass-produced, high sandblasting efficiency.
– Advantages: Suitable for handling large or heavy workpieces, suitable for continuous production lines.
– Applicable products: Ultrafine aluminum oxide blast media, ceramic peening beads.
- Wet sandblasting equipment:
– Features: Use water and sandblasting media to reduce dust and environmental pollution.
– Advantages: Suitable for workpieces with high cleanliness requirements and reduce material loss.
– Applicable products: Cryogenic deflashing media, nylon polyamide deflashing media.
- Automated sandblasting system:
– Features: Programmable control, suitable for mass production.
– Advantages: Ensure the stability and consistency of the sandblasting process and improve production efficiency.
– Applicable products: Ultrafine aluminum oxide blast media, cryogenic deflashing media.
Sandblasting technology and methods
The sandblasting technology and methods will affect the sandblasting effect, so it is crucial to choose the right technology.
- Dry sandblasting:
– Features: Use dry sandblasting media, suitable for various materials.
– Advantages: Remove burrs and surface dirt, often used for cleaning metal workpieces.
– Applicable products: Ultrafine aluminum oxide blast media, ceramic grit blasting beads.
- Wet sandblasting:
– Features: Add water during sandblasting to reduce dust and media dispersion.
– Advantages: Suitable for workpieces with high requirements for surface finish.
– Applicable products: Cryogenic deflashing media, nylon polyamide deflashing media.
- Ultrasonic sandblasting:
– Features: Use ultrasonic vibration to accelerate the sandblasting media.
– Advantages: Suitable for complex shapes and precision workpieces, and can process the surface more carefully.
– Applicable products: Nylon polyamide deflashing media, polystyrene deflashing beads.
- Shot blasting process:
– Features: Use a high-speed rotating shot blasting machine to project the sandblasting media onto the workpiece.
– Advantages: It can quickly remove impurities on the surface of the workpiece and is suitable for large-scale production.
– Applicable products: Ceramic peening beads, zirconia blasting beads.
Economy and efficiency
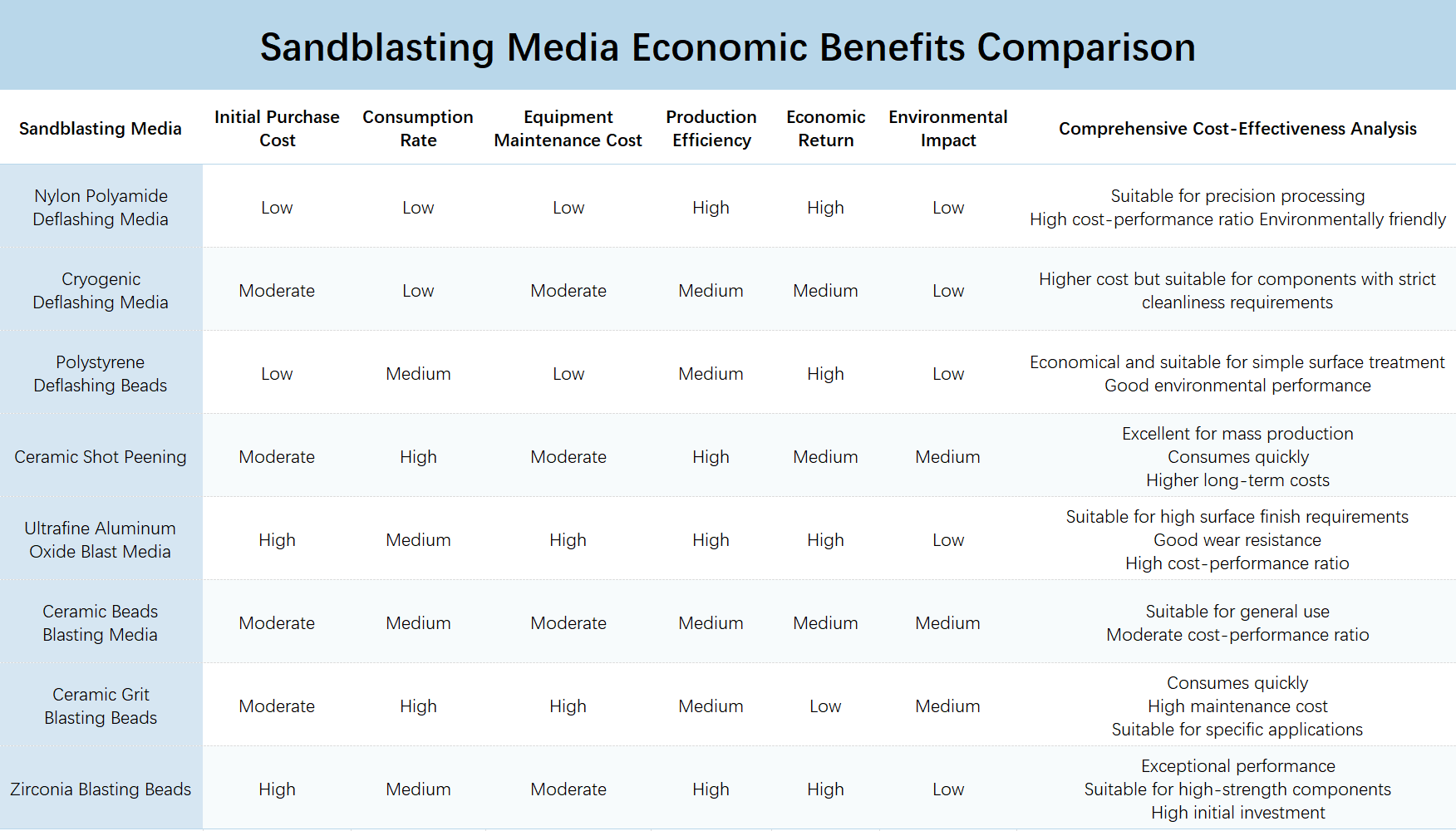
- Medium cost:
– The purchase cost of different sandblasting media varies greatly, and the economy of long-term use should be considered when choosing.
- Production efficiency:
– Selecting efficient sandblasting equipment and suitable media can significantly improve production efficiency and shorten the production cycle.
– Automated sandblasting systems generally provide higher efficiency and are suitable for large-scale production needs.
- Maintenance costs:
– The maintenance cost and frequency of equipment will also affect the overall economy. Choosing more durable, low-maintenance equipment can reduce long-term expenses.
– Using easy-to-clean sandblasting equipment can reduce downtime and improve production efficiency.
- Material loss:
– Material loss during sandblasting should be minimized. Choosing suitable media and equipment can reduce waste and improve overall efficiency.
– For example, wet sandblasting technology can effectively reduce the loss of sandblasting media and maintain good sandblasting results.
As can be seen from the figure, nylon polyamide deflashing media and ultrafine aluminum oxide blast media have become ideal choices for a variety of fine processing due to their high production efficiency and environmental protection characteristics. Although the initial cost of ultrafine aluminum oxide blast media is higher, it performs well in industries that require high cleanliness and is suitable for workpieces with strict surface requirements. Polystyrene deflashing beads are suitable for gentle surface treatment due to their low cost and good environmental protection.
Although ceramic grit blasting beads are consumed faster and may increase costs for long-term use, they are still highly efficient in large-scale production. Although zirconia blasting beads require a higher initial investment, they are suitable for high-strength workpieces due to their excellent performance. On the whole, companies should reasonably select sandblasting media according to specific needs and workpiece characteristics to achieve the best economic return and production efficiency.
In summary, choosing the right sandblasting media is not only related to the processing effect but also directly affects the safety and service life of the workpiece. In industrial production, customers should carefully evaluate the various characteristics and requirements of the workpiece, and select the most suitable sandblasting media in combination with the specific processing purpose. At the same time, with the improvement of environmental awareness, the selection of pollution-free and recyclable sandblasting materials is also becoming an industry standard. By choosing the right blasting media, your business can not only improve production efficiency but also gain an advantage in a highly competitive market.
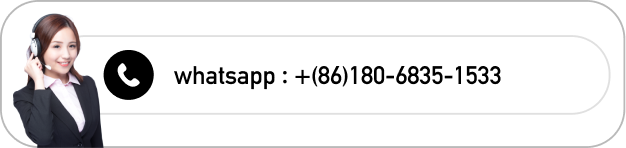