October 16, 2024
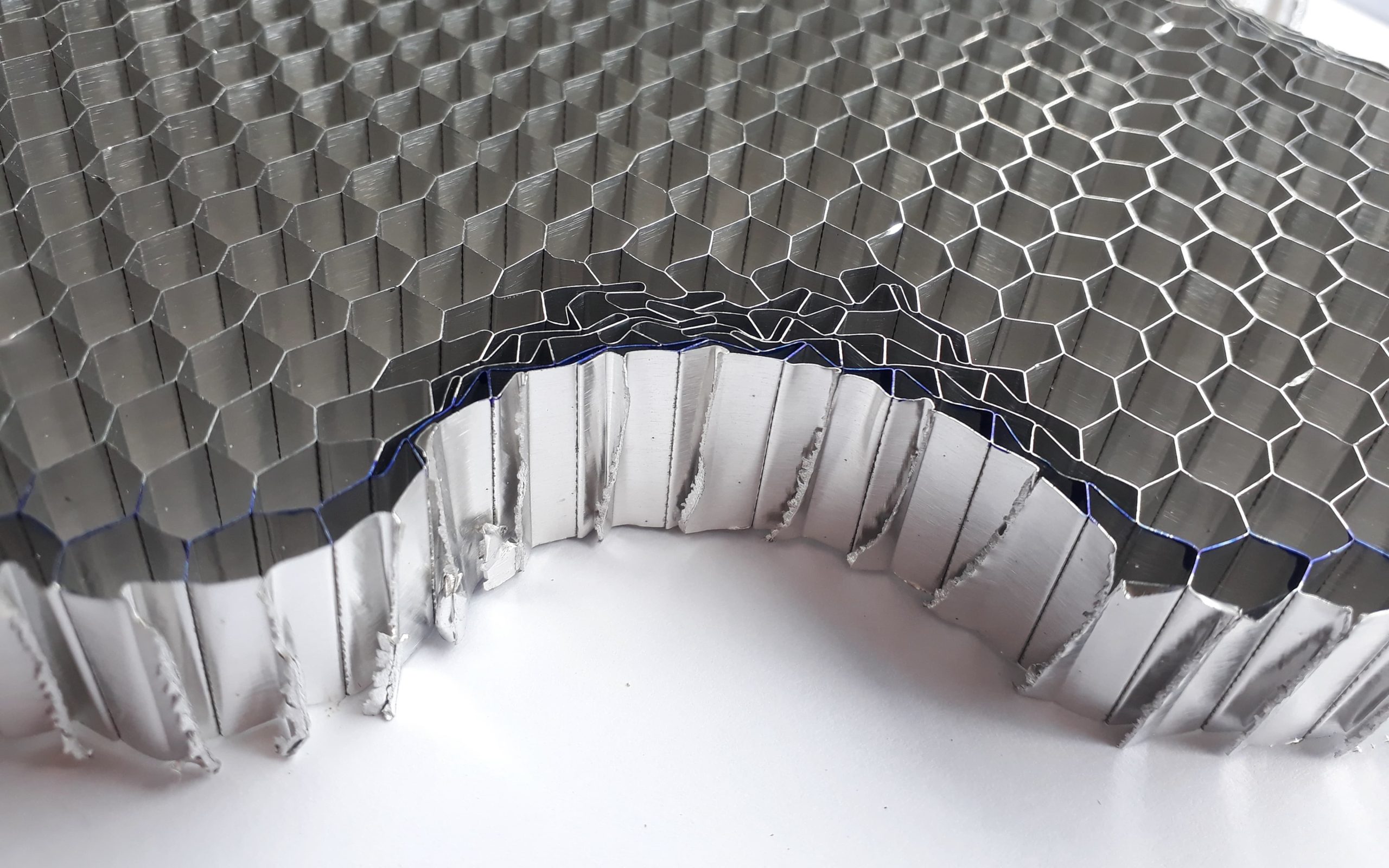
When a workpiece is born, it has a mission: whether it is an engine part of a car or a precision component of a mobile phone, it hopes to function in the most perfect posture. However, the road to growth is not always smooth. In the manufacturing process, those seemingly small and harmless corner burrs – may be just slight protrusions or excess metal or plastic debris, but they may become the biggest obstacle to the quality and function of the workpiece. Burrs not only destroy the appearance of the workpiece but also threaten its safety and service life. Therefore, the deburring process is very important.
The birth of burrs: the “trouble” of the workpiece begins
When every carefully designed metal or plastic workpiece is born from the production line, they are like a newborn baby – smooth surface, complete structure, full of hope for future use. However, as they gradually take shape, there are always some small “problems” that sneak up on them, they are burrs – those unwelcome little thorns.
In the manufacturing process of the workpiece, the formation of burrs is almost unavoidable. Whether it is cutting, drilling, milling, or grinding, friction and cutting force often cause some extra microscopic substances to appear on the edge or surface of the material. Burrs are born. They may be so small that they are almost invisible to the naked eye, but they can cause big trouble in future use. Just as a person will inevitably encounter some “troubles” in the process of growing up, burrs are also the “adolescent episodes” of workpieces in the production process.
There are many types of burrs, just like everyone has different personalities. We can divide burrs into three categories: cutting burrs, deformation burrs, and tearing burrs.
Cutting burrs are corners caused by incomplete or excessive material removal when the tool cuts the workpiece.
Deformation burrs are formed during material processing due to the deformation of metal or plastic, like irregular small protrusions extending from the workpiece.
As for tearing burrs, its formation process is more violent, usually when the metal is forcibly pulled off or separated, the material fails to separate.
Burr “prank”: the troubles of the workpiece are aggravated
As the workpiece enters the actual use stage, burrs begin their “prank” journey. Although they are small in size, their harm can be very serious. The surface of the workpiece, which should be smooth, is damaged by these irregular small burrs, which not only make the overall appearance rough and uneven but also these burrs are often hidden in the key parts of the workpiece, lurking to cause harm to the equipment operator, user and even the machine itself.
Burrs not only affect the appearance but also bring a series of hidden problems. For example, in fields such as aerospace and automotive parts that require high precision and high safety, burrs may cause poor assembly of key parts, and even accelerate wear and reduce the service life of parts due to their increased friction. In electronic products, tiny burrs may even cause circuit short circuits and cause equipment failures. In addition, in some medical devices, if burrs are not completely removed, they may also bring infection risks – imagine a catheter with burrs entering the human body, how dangerous it would be!
Therefore, burrs can be said to be the “troublemakers” in the life cycle of workpieces, and their small existence may have a huge impact. This is why workpieces must be deburred to ensure that they can play the best effect in actual use and avoid major problems caused by these “little troubles”.
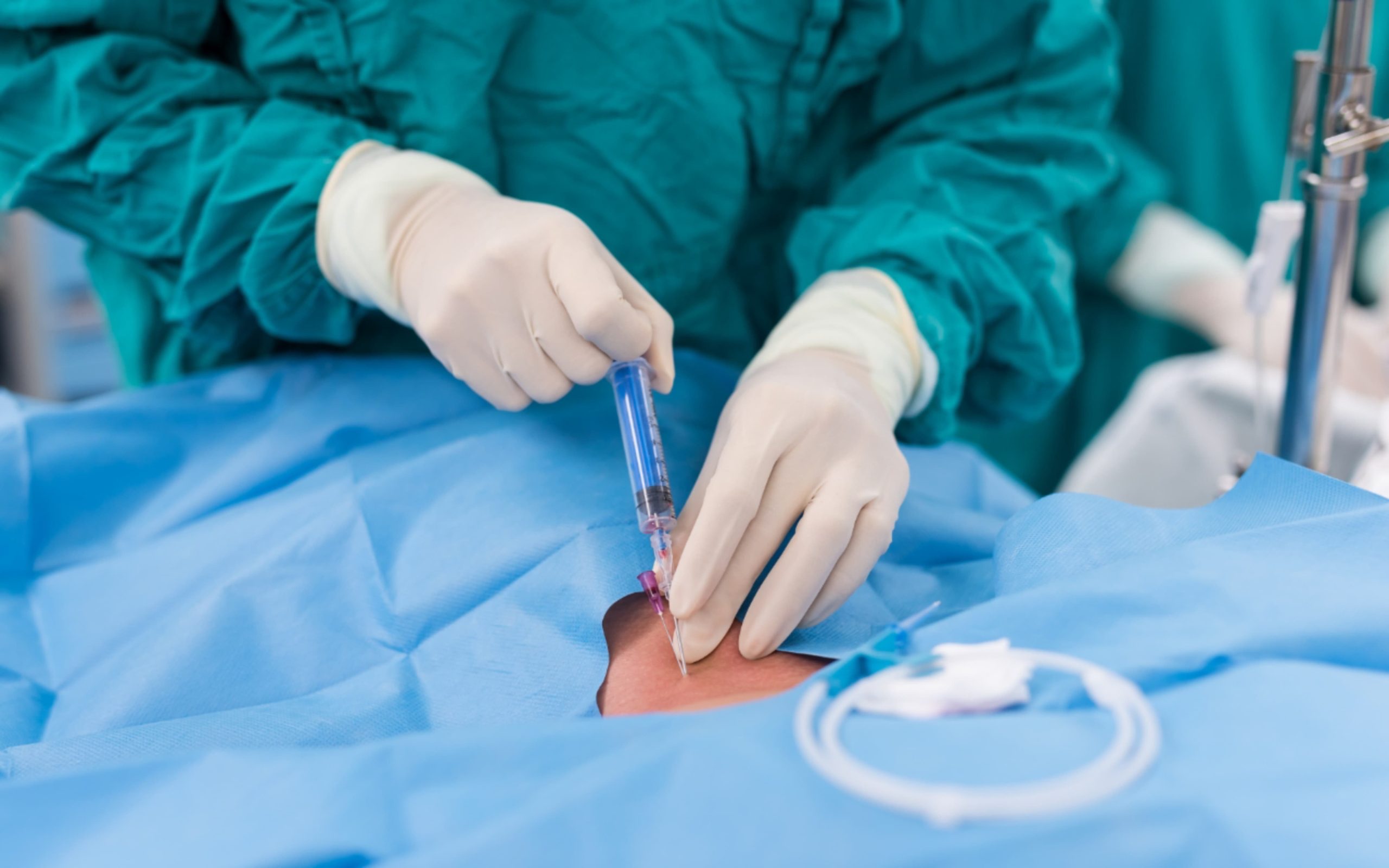
Medical devices that require flawless performance
The “wandering” of burrs: challenges in different scenarios
The formation of burrs usually stems from the mechanical and thermal stresses that the material is subjected to during processing. During the process of cutting, stamping, or grinding, the material is locally deformed after being subjected to pressure, producing fine metal chips or plastic fragments, which accumulate to form burrs. Burrs do not only exist in one field, they are a “wandering” trouble, and they may appear in different materials and industrial fields. For example, the formation of burrs is also very common in plastic parts. These burrs often appear at the edges or interfaces of injection molding. Although they are not as sharp as metal burrs, they will affect the appearance of the product and even affect the sealing and assembly accuracy in some scenarios.
In the field of metal processing, the existence of burrs is even more common. Especially in the process of cutting, punching, or welding, heat, and mechanical effects often cause burrs on the edges of metals. These burrs are not only a problem of appearance, but also cause wear of equipment in subsequent manufacturing links, and even cause danger in some high-pressure application scenarios. For example, in occasions with extremely high sealing requirements such as hydraulic valves or fuel systems, the presence of burrs may cause sealing failure, which in turn causes a series of problems such as leakage.
Especially in the field of high precision requirements, such as medical devices, electronic components, and even aerospace, the existence of burrs is even more intolerable. Tiny burrs may cause short circuits in electronic components and may bring unexpected health risks to medical devices. In these fields, deburring is not only to improve the appearance but also a key step to ensure safety and functionality.
“Fight back” of workpieces: the necessity of deburring
Faced with the various “pranks” brought by burrs, workpieces are obviously “fed up”. To get rid of these annoying “little thorns”, workpieces began to look for various ways to “fight back”, which is the necessity of deburring.
Deburring, as the name suggests, is to remove these extra edges and protrusions by physical or chemical means. In modern manufacturing, deburring technology has become quite diverse, from the most traditional manual deburring to modern automated deburring, and even laser deburring using high-tech. Each deburring method has its unique advantages and application scenarios. The deburring process is not just physical material removal, but also a deep understanding and application of processing disciplines, materials science, and mechanical engineering.
- Manual deburring: This method is the oldest and most intuitive. Workers use specialized tools such as whetstones, files, or sandpaper to grind the edges of the workpieces one by one to remove burrs. Although this method is flexible and can accurately handle workpieces of complex shapes, manual operation is time-consuming and labor-intensive and is not economical for mass production.
- Automated deburring: With the advancement of industrial technology, more and more companies are introducing automated deburring equipment. Through mechanical devices or CNC machine tools, automated deburring can not only greatly improve efficiency, but also ensure the accuracy and consistency of deburring.
- Laser deburring: This is one of the high-tech technologies that has developed rapidly in recent years. Using the high-temperature energy of the laser, burrs can be evaporated or melted in a very short time with almost no damage to the surface of the workpiece. This method is suitable for high-precision deburring needs, especially in high-demand industries such as microelectronics and aerospace.
The “end” of burrs: the victory of the deburring process
With the use of various deburring methods, workpieces have finally ushered in their “victorious moment”. Burrs, the “troublemakers” that once troubled workpieces, disappeared completely after a series of processes such as grinding, cutting, or evaporation, and the workpieces regained their smooth and flawless appearance. Whether it is metal or plastic parts, this process is not only a surface improvement but also a functional optimization and extended service life.
Deburring not only allows the workpiece to get rid of those unnecessary small burrs but also provides a guarantee for subsequent use and assembly. In the automotive industry, deburred parts can be assembled more smoothly, reduce friction, and improve mechanical efficiency. In the electronics industry, deburred circuit boards and electronic components can avoid short circuits and ensure the stable operation of products. In the field of medical devices, deburring is not only to improve the finish of the equipment but also to prevent risks to patients during use.
The victory of deburring is not only a victory for the workpiece but also a victory for the entire manufacturing industry. The deburring process, although it seems to be just a small step, largely determines the quality and safety of the final product. Therefore, both traditional manual deburring and advanced laser deburring are indispensable process links in modern manufacturing.
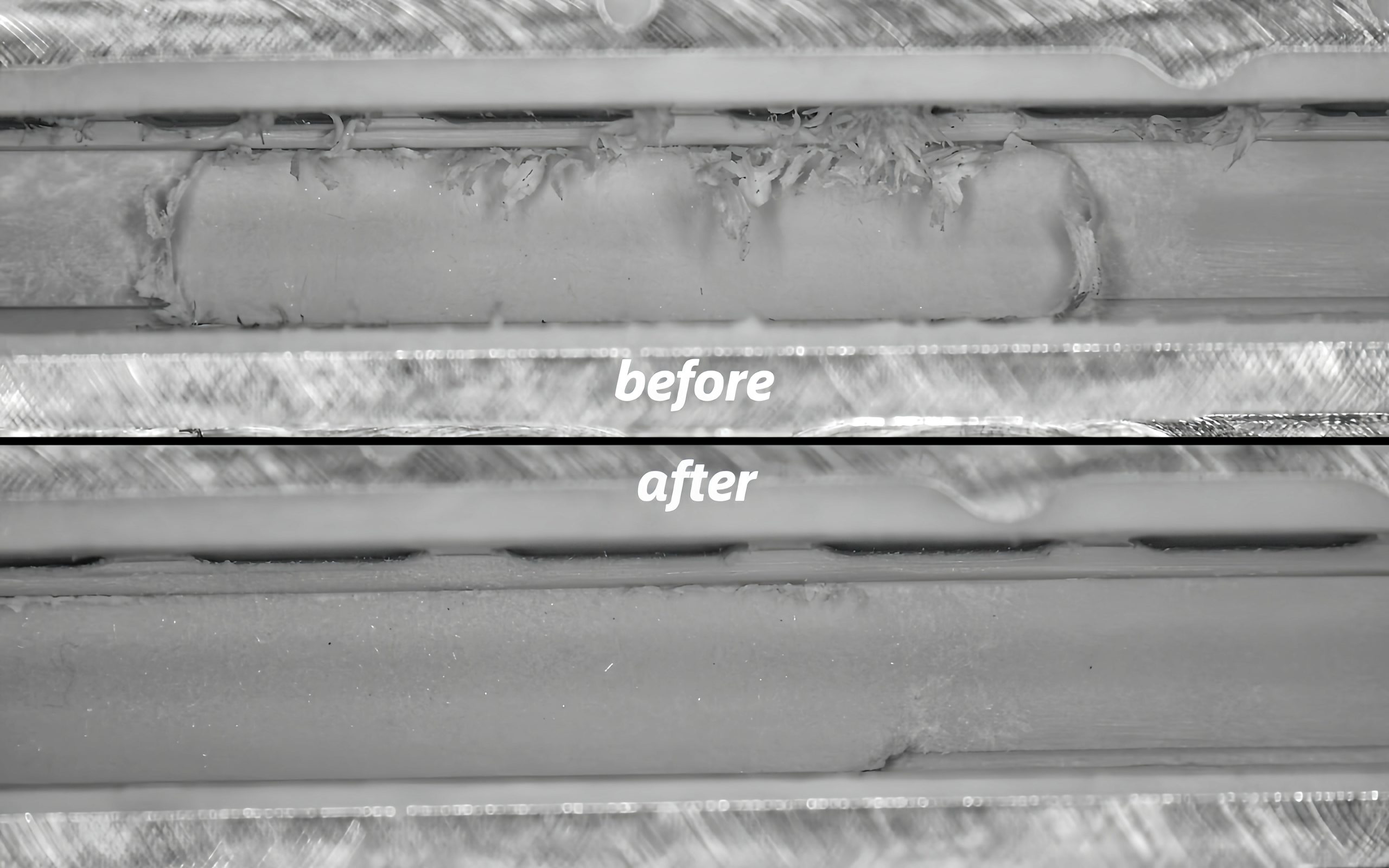
Comparison before and after deburring
Burr “lessons”: industry standards and challenges of deburring
Although deburring technology has made great progress, it still faces many challenges. Different fields have different requirements for deburring, especially in some high-precision and high-safety industries such as aerospace, nuclear industry, and medical devices, the standards for deburring are also more stringent.
In these industries, deburring not only needs to consider efficiency and precision but also must comply with relevant industry standards and specifications. For example, in the aviation field, any tiny burr may affect the normal operation of aircraft engine components, and may even have catastrophic consequences. Therefore, the International Organization for Standardization (ISO) and the aviation industry have established very strict deburring standards. In the field of medical devices, deburring is not only to ensure the smooth operation of the product, but also to ensure the safety of patients, and the safety certification and standards of medical devices must be strictly followed.
In addition, with the advancement of manufacturing processes, more and more new materials are being used in industrial production, bringing new challenges to deburring. For example, the materials used in 3D printing technology and its manufacturing processes may produce more diverse burr types than traditional processing. Therefore, for these emerging materials and technologies, the means of deburring also need to be continuously innovated and optimized.
The industry norms and standards for deburring provide clear guidance for producers, but at the same time, they also put forward higher requirements for manufacturers. How to improve efficiency and reduce costs while ensuring the deburring effect is a common challenge faced by every manufacturing company.
The “burr-free” world of the future
With the rapid development of automation and intelligent technology, deburring technology is also moving towards a more efficient and precise direction. The deburring process in the future may be more intelligent and automated. Through robotics, AI algorithms, and high-precision laser equipment, the deburring process will no longer rely on manual operation and become more intelligent and efficient.
In addition, the combination of deburring technology and other processing technologies will also become a future development trend. For example, the combination of 3D printing technology and deburring technology can directly perform efficient automatic deburring operations after printing is completed, saving a lot of manpower and time costs. For example, in the field of nanotechnology and micromachining, the deburring process will be more miniaturized to adapt to smaller and smaller product parts.
The future “burr-free” world will not only be limited to small improvements on the surface of workpieces, but will also become one of the key links to improve product quality, extend service life, and enhance industrial efficiency. It can be foreseen that with the continuous advancement of deburring technology, the manufacturing industry will usher in an era of smoother, flawless, and fully functional workpiece products.
The growth process of a workpiece is accompanied by the birth and removal of burrs, and finally, it can achieve true maturity. Just like a person gradually sharpens a better self from imperfection, the deburring process is also an important step in the transformation and optimization of workpieces. From the initial corner burrs to the final smooth surface, deburring not only improves the appearance quality of the workpiece but also ensures its safety and function in practical applications.
For the manufacturing industry, the value of deburring is self-evident. Whether it is to ensure the safety of aerospace components or to ensure the aseptic operation of medical devices, deburring is a vital part of the process. With the continuous innovation of technology, deburring technology will continue to advance and bring more innovation and development to the manufacturing industry.
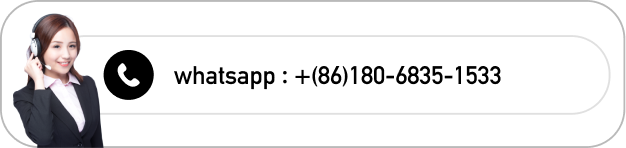