Type II VS Type III: How to choose the right plastic media
December 3, 2024
Type II plastic media and Type III plastic media are widely used in sandblasting operations due to their excellent performance and versatility, especially for sensitive and delicate components. What is the difference between them? How can we make the right choice for different processing tasks and materials?
Main application areas
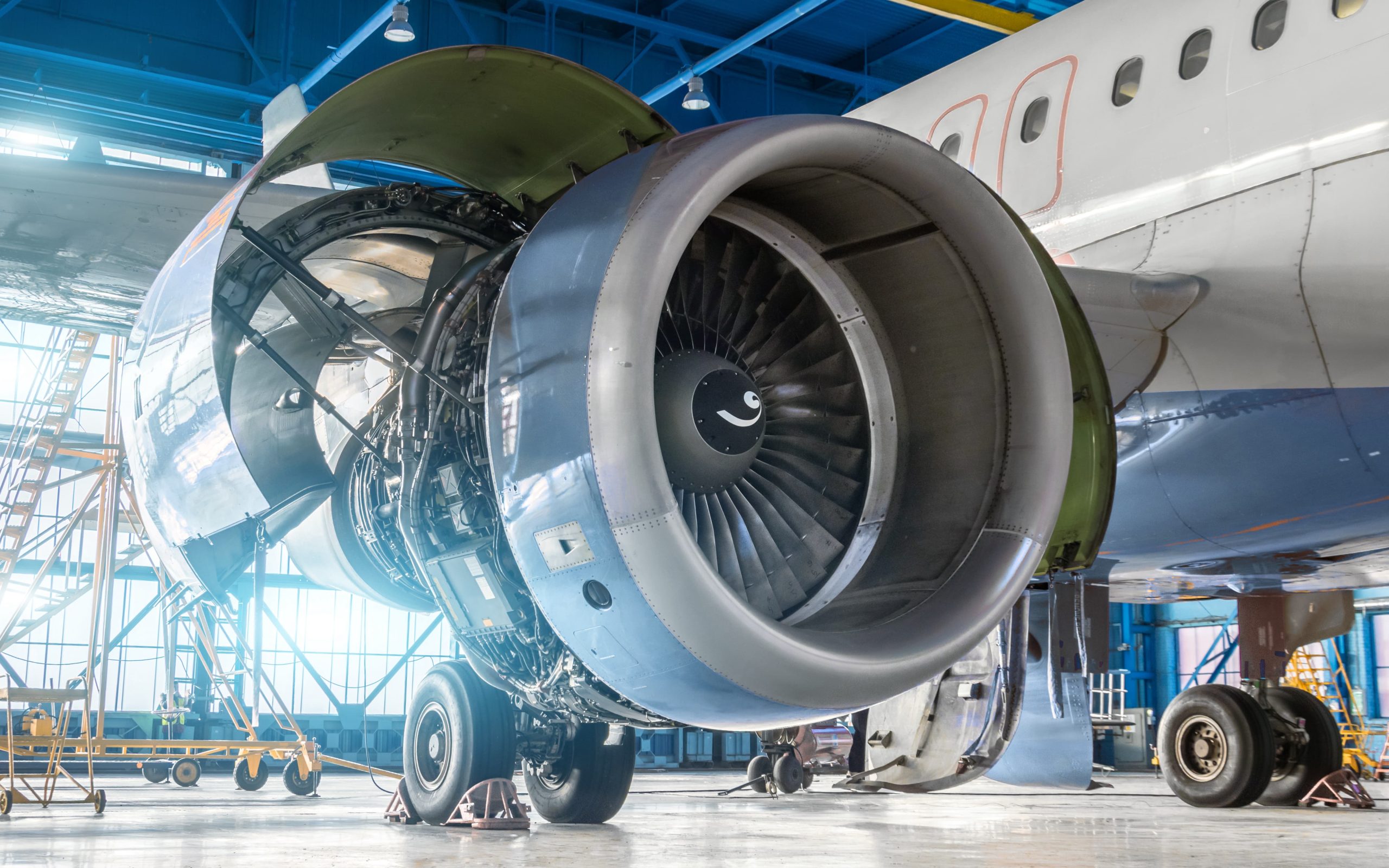
Type III plastic media
- Industrial equipment maintenance
The higher hardness and cutting force of Type III plastic media allow for quick cleaning of the surfaces of steel equipment or large machinery, improving processing efficiency while reducing the frequency of media consumption.
- Automotive Repair and Parts Remanufacturing
Excellent performance when cleaning, such as engine parts or chassis structures, effectively removing contaminants and creating an ideal surface for subsequent painting or assembly.
- Fiberglass and Composite Cleaning
Irregular shapes and small sizes make it easy to handle these complex materials, ensuring cleaning efficiency while preventing over-cutting.
- High-end Paint Pretreatment
Strong cutting performance quickly completes roughening tasks and significantly improves subsequent coating adhesion.
Type II plastic media
- Aerospace industry
The low hardness of Type II plastic media effectively removes oxide layers, old coatings, and dirt without damaging the substrate, making it ideal for cleaning aircraft interior structures and light metal components.
- Electronic components and circuit boards
Gently remove dirt from sensitive areas while avoiding damage to conductive paths that can be caused by higher-hardness abrasives.
- Precision plastic parts and molds
Precisely clean mold and finished surfaces while maintaining smoothness and functionality.
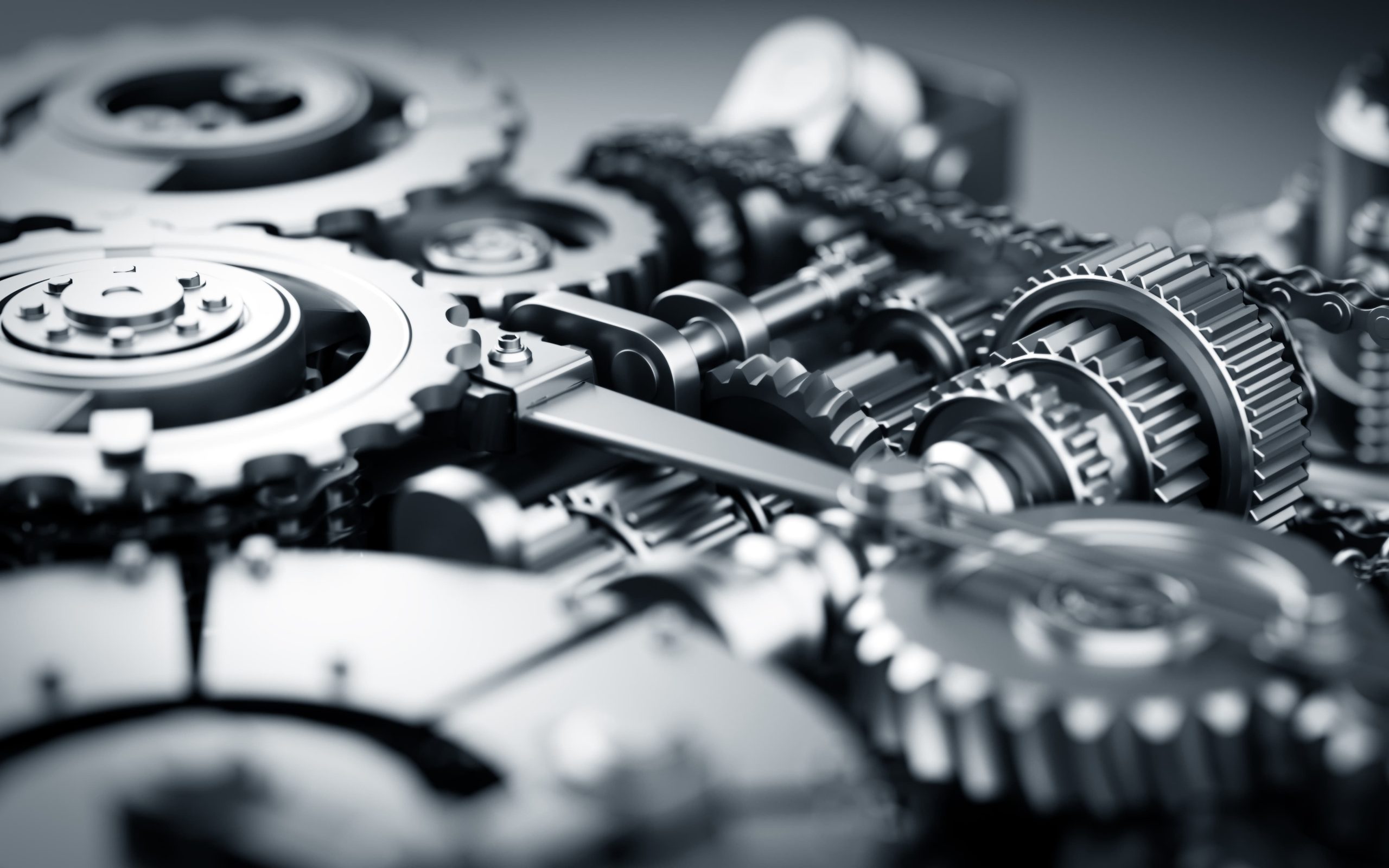
Commonalities
Although Type II plastic media and Type III plastic media differ in specific application scenarios, they are both suitable for a variety of materials, including but not limited to:
- Fiberglass
- Aluminum
- Copper/Brass
- Plastic/Rubber
- Electronic components and circuit boards
- Other composite materials
Main functions
- Surface cleaning: Removes oxide layers, dirt, and old coatings on the surface to ensure the purity of the substrate.
- Surface optimization: Improves aesthetics, functionality, or adhesion of subsequent coatings by adjusting the surface texture.
However, in specific operations, customer needs often involve more detailed considerations, such as material properties, cost, environmental requirements, etc. We will discuss these in-depth to help customers make the right choice according to their actual situation.
Factors in selecting abrasive media
In sandblasting operations, choosing the right abrasive media is the key to ensuring treatment effects and cost efficiency. The following five core factors will provide customers with a clear reference direction.
Materials to be sandblasted
Different types of materials have their requirements for the hardness, impact force, and processing methods of abrasives:
Soft materials
- Aluminum parts cleaning in the aerospace field
- Surface treatment of fiberglass products
- Decontamination of precision plastic parts, etc.
(such as aluminum alloys, composite materials, and plastic parts) The surface is relatively soft and easily damaged or deformed by impact, so it is necessary to select abrasives with low hardness and low impact force to achieve a gentle cleaning effect.
Therefore, Type II plastic media will be more suitable for such materials. Its lower hardness and lighter density can protect the substrate from damage while removing surface dirt and oxide layers.
High-hardness materials
- Surface rust removal of industrial equipment
- Old paint cleaning of large structural parts
- Surface treatment of wear-resistant alloy parts
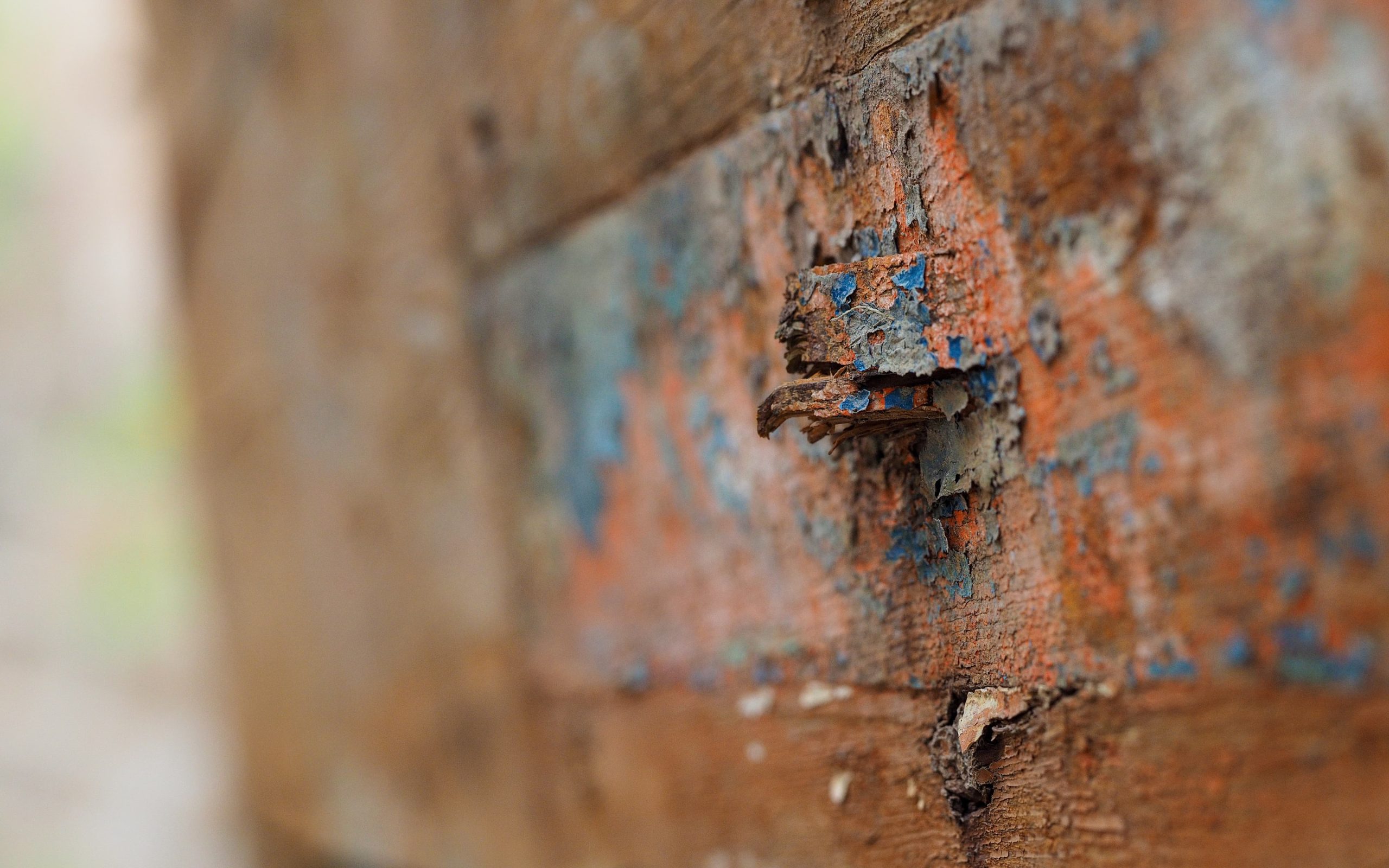
(Such as stainless steel, carbon steel, titanium alloy) usually have high strength and wear resistance, and the rust or coating on the surface is relatively stubborn. It is necessary to use a medium with higher hardness and sharper particle shape to enhance the cleaning efficiency.
Type III plastic media has the highest hardness among plastic media, and its sharp angular particles can also quickly clean stubborn coatings or rust layers while maintaining high processing efficiency.
Summary
According to the properties of the material, it is recommended to give priority to Type II for soft materials to ensure the safety and processing accuracy of the workpiece; while for high-hardness and stubbornly contaminated surfaces, Type III plastic media is more suitable and can significantly improve work efficiency.
Surface finish
One of the core goals of sandblasting is to adjust the surface finish of the workpiece. Different cleaning or processing tasks have different requirements for surface roughness, which affects the choice of abrasive media.
Rough surface
- Surface pretreatment before painting to ensure long-term adhesion of the coating.
- Surface roughening of industrial equipment or large workpieces.
- Treatment of bonded parts or welded surfaces to enhance bonding performance.
Some industrial applications require a higher surface roughness to ensure that the coating or bonding material can adhere firmly. Such operations tend to choose media with a stronger cutting force. Since Type III usually has angular particle shapes, it has a stronger impact and cutting ability, which can quickly achieve surface roughening, and improve adhesion and mechanical bonding strength.
Smooth surface
- Cleaning and polishing of optical instrument parts.
- Decorative treatment of precision plastic or composite parts.
- Fine sandblasting for electronic components or thin-walled workpieces.
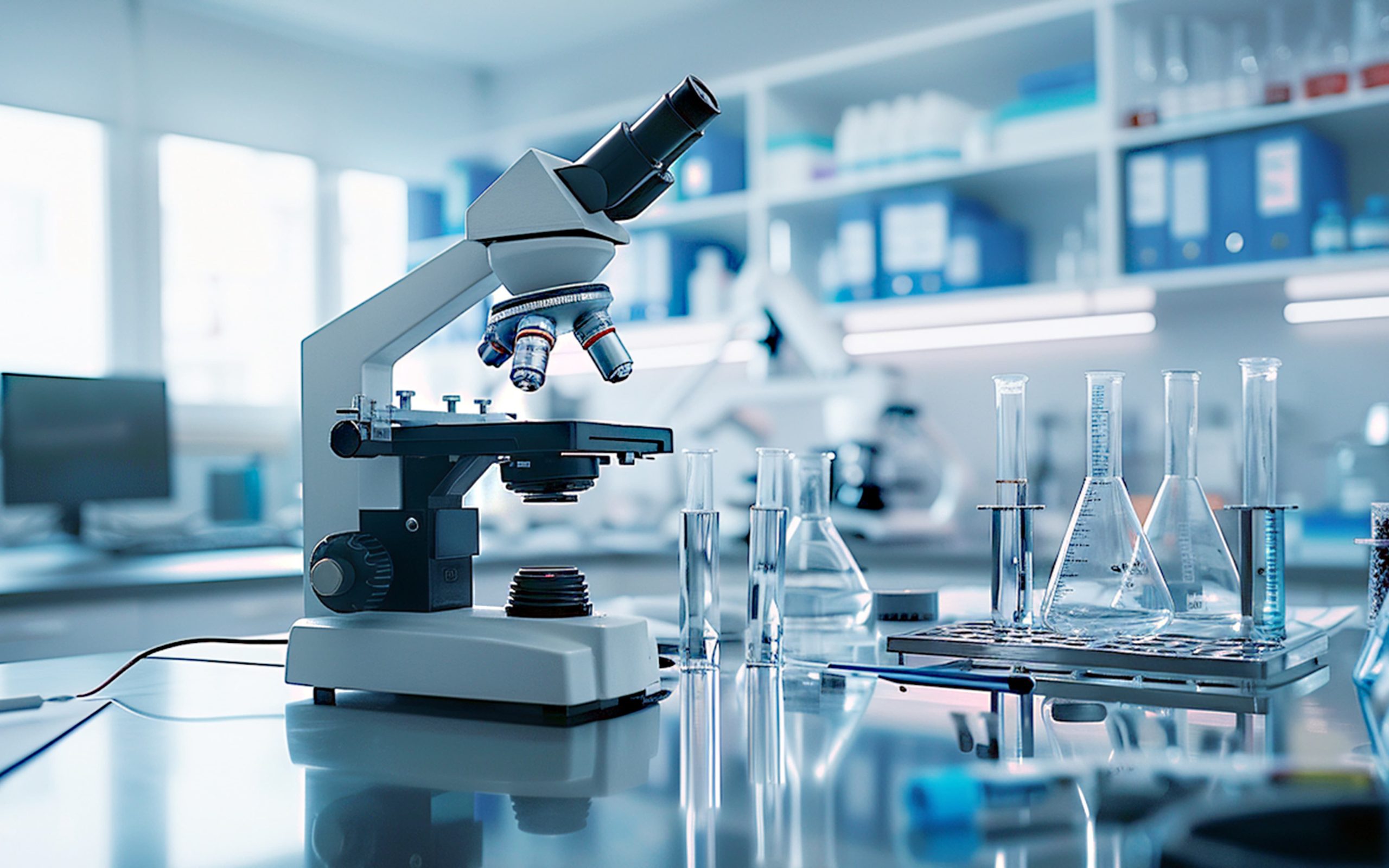
For exterior decoration or precision machined parts, customers usually want a smooth and uniform surface to enhance visual effects or meet functional requirements. Such scenarios prefer to use media with lower impact and less wear. Type II plastic media is more suitable. Its gentle action can remove surface contaminants while maintaining the integrity and smoothness of the workpiece surface.
Summary
If your goal is to achieve a clean, smooth surface, Type II is a better choice, especially for workpieces with high requirements for appearance or surface integrity; when the goal is to increase the roughness to meet functional requirements, the cutting ability of Type III is more suitable.
Compatibility with existing equipment
The choice of abrasive media depends not only on the workpiece requirements but also on the compatibility of existing sandblasting equipment. Equipment type, blasting pressure, nozzle shape, etc. may affect the sandblasting effect and the service life of the media.
Low-pressure equipment
Generally suitable for processing lighter media, such as plastic abrasives. This type of equipment has lower requirements for nozzle wear resistance but relies more on the flexibility and shape stability of the media.
Type II abrasives have a relatively low density (about 1.48 – 1.52 g/cm³), and the irregular triangular particle shape allows them to act evenly on the surface during sandblasting, which is particularly suitable for small or portable sandblasting systems with limited equipment output pressure.
High-pressure equipment
Designed to handle high-hardness, high-density media, it can provide sufficient impact force for stubborn coatings and rust, but it requires higher wear resistance for the nozzle and the inner wall of the equipment.
Type III plastic media is very suitable for high-pressure sandblasting equipment (especially equipment with high-hardness nozzles). It can give full play to the cutting performance of its angular particles under high impact, and it is more wear-resistant. It can maintain its integrity and operating efficiency during long-term high-pressure operations.
Summary
In terms of equipment adaptability, the characteristics of Type II make it more suitable for low-pressure and portable equipment, especially in terms of flexibility and equipment protection; while Type III can show higher cleaning ability under high-pressure environments, suitable for industrial-grade equipment and high-intensity tasks.
Cost factors
Cost is a key consideration when choosing abrasive media. The cost of sandblasting includes not only the purchase price of the abrasive, but also its durability, recyclability, and potential impact on the equipment and workpiece.
Procurement cost
The manufacturing cost of both Type II and Type III is relatively low, so their market price is competitive. The difference is that Type II is particularly suitable for small businesses or one-time projects that are cost-sensitive. Type III generally offers a high cost-effectiveness in high-end industrial applications.
Service life
Durable abrasives can be recycled multiple times, thus reducing the cost of a single cleaning. Type III has significantly better wear resistance than Type II due to its higher hardness and toughness, and is suitable for industrial scenarios with more cycles, which can reduce total costs in the long run.
Related expenses
Including equipment maintenance costs, dust control measures, and compensation costs for workpiece damage that may be caused by improper use.
Type II plastic media:
- Less wear on equipment can reduce the frequency of nozzle and pipe replacement.
- Due to the light particles, less dust is generated during the spraying process, which can reduce dust management costs.
Type III plastic media:
- Better performance in high-pressure equipment. Although the hardness is the highest among plastic media, it causes little wear on the nozzle and the inner wall of the equipment, saving maintenance costs.
- Heavier particles may lead to higher transportation and storage costs, but at the same time reduce the amount of suspended dust in the air after spraying, which helps to optimize the working environment.
Summary
In terms of cost, these two media are comparable, both are economical, and also have wear resistance in subsequent use, and are cost-effective in the long run.
Environmental issues
Includes the recyclability of abrasive media, dust emissions, potential pollution risks to the environment, and compliance with laws and regulations.
Recyclability
Environmentally friendly abrasives should have a high recycling capacity to reduce the frequency and cost of waste disposal. Both Type II plastic media and Type III plastic media are recyclable, and the breakage rate is low during multiple cycles, which significantly improves recycling efficiency.
Dust management
Excessive dust not only affects the working environment but also may endanger the health of workers. Therefore, the shape, density, and durability of the abrasive will directly affect the dust level.
Due to the low density and irregular shape of Type II particles, less dust is generated during the spraying process, no residue, and simple waste disposal.
Due to the high density and more regular shape of Type III particles, the dust generated during the spraying process is easy to settle quickly, significantly reducing the concentration of suspended particles in the air and reducing the potential threat of dust to workers’ health.
Regulatory compliance
Environmental regulations in different regions have strict requirements on emission standards for industrial operations. Selecting compliant abrasive media can reduce the legal risks faced by enterprises.
Type II waste is mainly composed of plastic substrates, which can be recycled and reused in a centralized manner. Standardized treatment can reduce the risk of microplastic pollution.
Type III is non-toxic and harmless, with only a small risk of microplastics. It can meet strict environmental standards as a whole and is especially popular in the European and American markets. It is often recommended for high-end environmental protection projects.
Summary
In terms of environmental performance, Type II is suitable for short-term light operations, and its low dust generation is suitable for companies with strict requirements on the working environment; while Type III’s high durability and low waste generation are more suitable for industrial projects that pursue long-term environmental benefits. Enterprises need to choose the most suitable media based on the intensity of the operation and environmental compliance requirements.
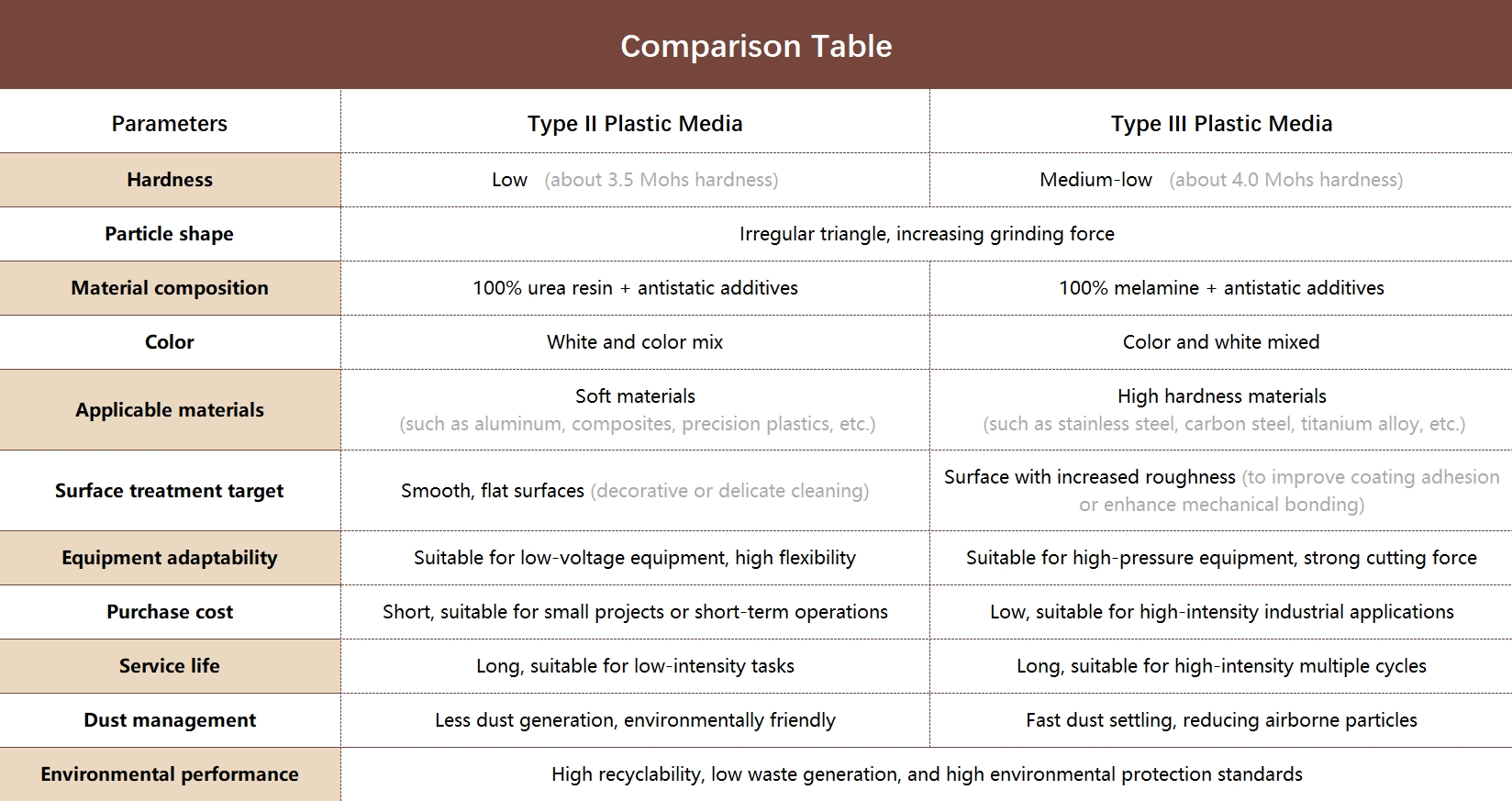
Case Overview
Background:
An industrial equipment manufacturer faces a key challenge – reducing dust emissions during polishing and extending the life of consumables while maintaining part quality. Although traditional abrasive media (such as glass beads) can achieve a smooth effect, their high fragmentation rate leads to a high frequency of consumable replacement and a high overall cost.
Challenges:
- Environmental friendliness: Traditional media generate a lot of dust, affecting worker health and environmental compliance.
- Durability: Existing abrasives have a limited lifespan in high-intensity grinding and often need to be replaced frequently.
- Economy: The increased frequency of replacement directly leads to higher operating costs.
Solution:
After multiple tests, the customer chose Type II plastic abrasive media, which has the following features:
- Irregular triangular particle design can enhance grinding efficiency and coverage.
- Lower hardness, reducing potential damage to part surfaces.
Results:
- 30% longer consumable life: Compared with glass bead media, Type II has a 25% lower dust generation rate and less maintenance.
- 15% lower total cost: The frequency of consumable replacement is reduced, and production efficiency is improved. [1]
- Compliance with environmental regulations: The customer passed OSHA standard dust emission requirements and enhanced employee health protection.
Application scenario:
An aircraft maintenance company uses Type III plastic abrasive to clean aircraft engine parts and composite surfaces. The goal is to remove coatings and impurities while maintaining the integrity of the material without causing any deformation or overheating issues.
Abrasive used: Type III Melamine 12-16 mesh (1.7-1.2 mm) for fine cleaning tasks.
Cleaning targets:
- Aircraft composites: Remove old coatings and corrosion sealants from the surface.
- Aluminum alloy parts: Remove corrosion layers and retain a smooth surface.
Results:
- Cleaning time is reduced by 30% [2] compared to traditional glass bead methods, and surface finish consistency is significantly improved.
- No deformation or thermal stress is induced on the substrate.
- Meets MIL-P-85891 standard (military coating stripping standard).
Get a customized sandblasting solution now!
We provide free professional consultation services to help you accurately select the most suitable sandblasting materials.
Simply send us your samples and we will complete the test according to your specific needs and recommend the best sandblasting materials (single or combination).
In addition, we support small batch sample trials for you to test the effect and ensure that you make the right choice.
Interested in learning more about our products or getting a quote? Welcome to leave your contact information!
At the same time, don’t forget to bookmark our website. We will update the blog regularly to bring you more industry information and practical tips to help you make every sandblasting operation more efficient and outstanding.
Click the link to contact us!
[1] Application case analysis from the Extrude Hone website
[2] According to the case on the Kramer Industries’ official website
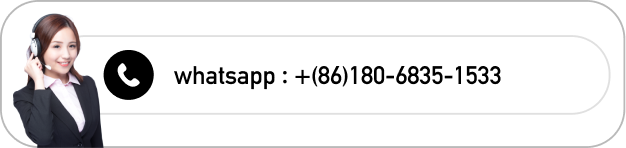