Sandblasting effectively removes rust from metal
October 22, 2024
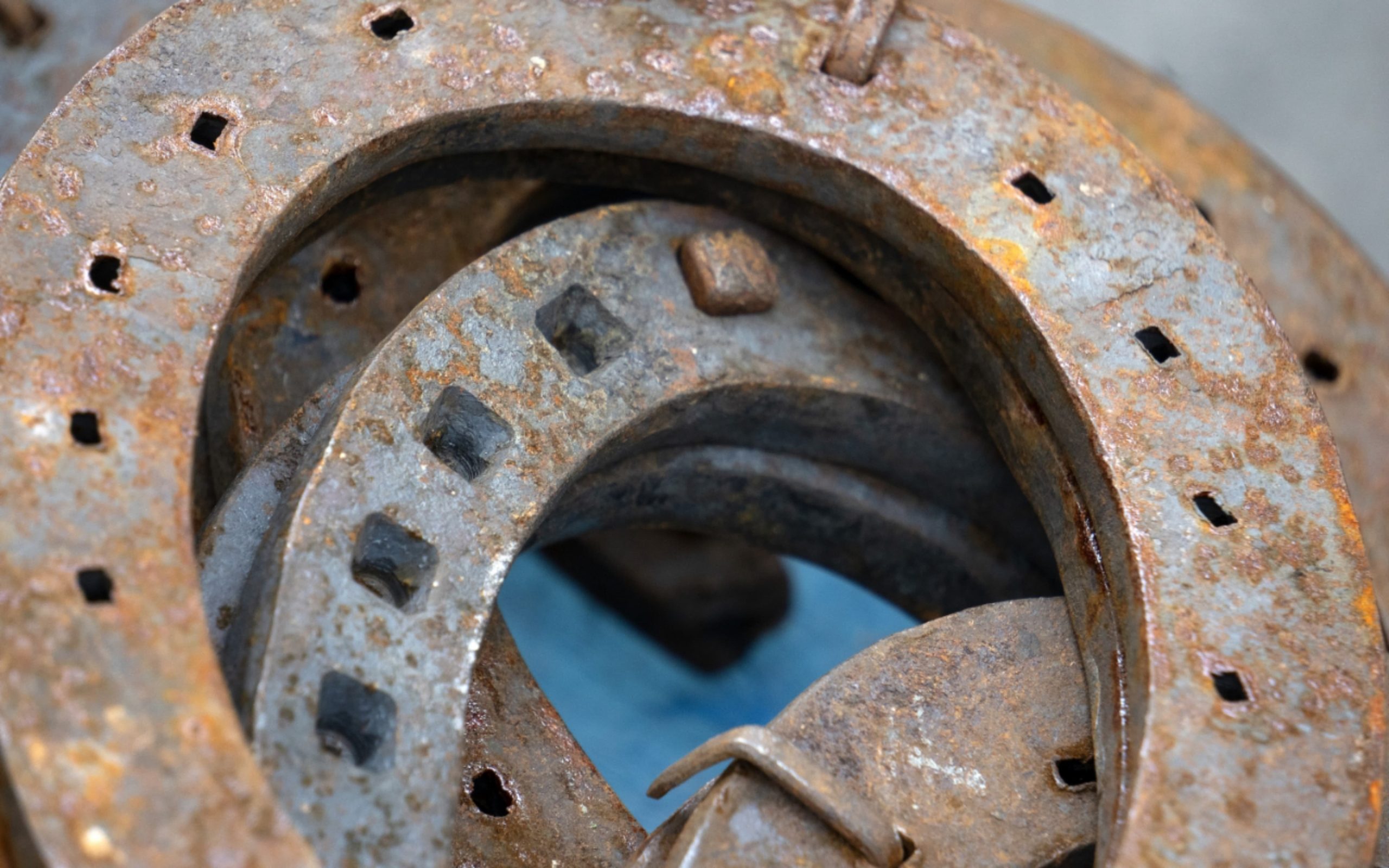
When you walk in a factory workshop or a construction site, or see metal structures that have been baptized by the years, have you ever wondered how serious the rust problem on the metal surface is? Metal rust affects the object’s appearance and poses a huge threat to its structural strength and service life. So, how do you effectively remove rust on the metal surface? This is a difficult problem that has troubled many companies and engineers. Among the many rust removal methods, the sandblasting process has unique advantages. But before we take a closer look at the sandblasting process, let’s take a look at the defects of traditional rust removal methods.
Traditional rust removal methods
- Chemical method
Chemical rust removal is a common rust removal method, which mainly uses acidic chemical solutions for rust removal. This method has a certain effect on small-scale rust or less serious rust. However, chemical solutions may damage the metal surface. While removing rust, acidic solutions will also react with metals, causing the metal surface to become rough and may even weaken the structural strength of the metal. In addition, chemical solutions will generate a large amount of wastewater and waste gas during use. If they are directly discharged without treatment, they will cause serious pollution to the environment.
- Manual rust removal
Manual rust removal mainly involves manually using grinding tools to remove rust. This method is suitable for small-scale rust treatment, but it is extremely inefficient for large metal surfaces. For example, when dealing with surface rust on a large storage tank, it may take dozens of workers several days or even weeks to complete. In addition, the quality of manual rust removal is also difficult to guarantee. Due to the limitations of manual operation, it is difficult to ensure the uniformity and thoroughness of rust removal, which will affect the subsequent coating or painting treatment effect.
- Electrolytic rust removal
Electrolytic rust removal is a method of removing rust from metal surfaces using electrochemical principles. It is suitable for small metal parts, but for large-scale production, it is costly and takes a long time to process. Electrolytic rust removal requires not only professional equipment but also technicians to accurately control parameters such as current and voltage, otherwise it may cause damage to metal parts. Moreover, compared with other rust removal methods, electrolytic rust removal takes a long time to process, which may affect production progress for companies that need to rust a large number of metal parts, such as the automotive manufacturing industry.
- Sandblasting for rust removal
Sandblasting for rust removal is a new type of rust removal method, which has many advantages over traditional methods. But before introducing its advantages, let’s first understand the working principle of sandblasting for rust removal.
Sandblasting rust removal
- Basic introduction to sandblasting
Sandblasting is a method of using high-pressure air or water flow to carry abrasives to quickly remove rust on the metal surface. Its working principle is mainly to accelerate the abrasive to a certain speed through compressed air or high-pressure water flow, and then spray it onto the metal surface, using the impact force and friction of the abrasive to remove rust.
Sandblasting equipment usually consists of a compressed air source, a spray gun, an abrasive storage tank, and a control system. When working, compressed air blows the abrasive out of the storage tank and sprays it onto the metal surface through the spray gun. The operator can adjust the parameters such as sandblasting pressure, abrasive flow rate, and spray angle through the control system to achieve the best rust removal effect.
- Common sandblasting materials
- Brown corundum
Brown corundum is an abrasive with a higher hardness, and its main component is aluminum oxide. It has good wear resistance and cutting force and is suitable for removing more serious rust and scale. The particle shape of brown corundum is irregular, which can form a certain roughness on the metal surface, which is conducive to the subsequent coating or paint treatment.
When using brown corundum for sandblasting and rust removal, it is necessary to select the appropriate particle size according to the degree of rust on the metal surface and the required rust removal effect. Generally speaking, for more serious rust, you can choose brown corundum with larger particles; for minor rust, you can choose brown corundum with smaller particles.
Aluminum oxide is a white abrasive with high hardness, second only to diamond, and stable chemical properties. It has good cutting force and wear resistance and is suitable for removing rust from various metal surfaces. The particle shape of aluminum oxide is relatively regular, which can form a relatively uniform roughness on the metal surface, which is conducive to improving the adhesion of coating or painting.
Compared with brown corundum, the price of aluminum oxide is relatively high, but it has a longer service life and can reduce the cost of sandblasting to a certain extent. In addition, aluminum oxide is a more environmentally friendly sandblasting material.
- Silica sand
Silica sand is cheap, widely available, has a certain hardness and cutting force, and is suitable for removing mild rust and scale. The particle shape of silica sand is relatively regular, and it can form a relatively smooth surface on the metal surface, which is beneficial to improve the appearance quality of the metal. However, silica sand also has some disadvantages. First, the hardness is relatively low, and the effect of removing more serious rust is not good. Secondly, silica sand is easy to generate dust during use, which will have a certain impact on the environment and the health of operators.
- Glass beads
Glass beads are spherical abrasives with low hardness, stable chemical properties, good fluidity, and rebound force. It is suitable for removing mild rust and scale and can form a relatively smooth surface on the metal surface, which is beneficial to improve the appearance quality of the metal.
- Steel sand
Steel sand is a high-hardness abrasive, the main component of which is iron. It has good wear resistance and cutting force and is suitable for removing more serious rust and scale. When using steel sand for sandblasting and rust removal, you need to pay attention to the hardness and particle size of the steel sand. If the hardness of the steel sand is too high, it may cause damage to the metal surface; if the particles of the steel sand are too large, it may cause uneven rust removal.
- Surface treatment effect
Sandblasting can not only remove rust from the metal surface but also make the metal surface have a certain degree of roughness, which helps to improve the adhesion of the coating and extend the service life of the coating.
In addition, sandblasting can also remove impurities such as oil, dust, and other impurities on the metal surface and improve the cleanliness of the metal surface. This is very important for some coating processes with higher requirements. For example, in the automobile manufacturing industry, the metal body needs to be sandblasted to remove rust and impurities on the surface and then painted to improve the appearance quality and corrosion resistance of the body.
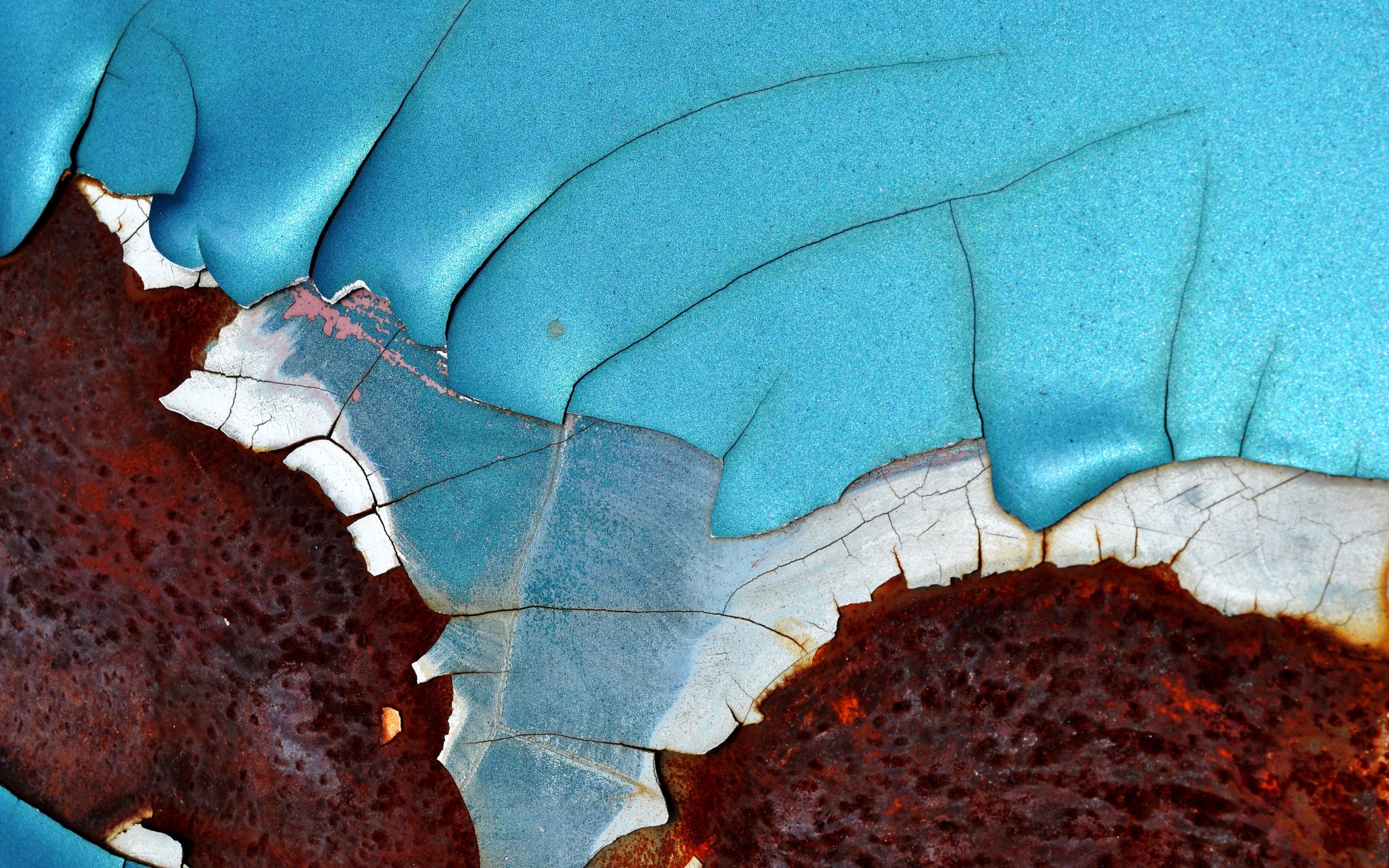
Removing paint from car surfaces
- Advantages of the sandblasting process in rust removal
- Speed and efficiency
Compared with manual or chemical methods, sandblasting can handle large areas of rust in a shorter time, especially suitable for large industrial equipment. Sandblasting equipment can achieve efficient rust removal by adjusting the sandblasting pressure and abrasive flow. In addition, sandblasting equipment can work continuously without being restricted by manpower and time, which can save a lot of valuable time for some companies that need to deal with metal surface rust problems urgently. For example, in some petrochemical enterprises, if the surface rust of storage tanks and pipelines is not handled in time, it may cause leakage accidents.
- Precise control
The operator can control the treatment process by adjusting the sandblasting pressure and the type of medium to avoid damaging the metal substrate. Different metal materials and rust levels require different sandblasting pressures and abrasive types. For metal materials with higher hardness, larger abrasive particles, and higher sandblasting pressures can be selected; for metal materials with lower hardness, smaller abrasive particles, and lower sandblasting pressures need to be selected.
In addition, the sandblasting equipment can also be equipped with an automated control system to achieve precise sandblasting operations, automatically adjust parameters such as sandblasting pressure, abrasive flow rate, and spray angle, and improve the accuracy and efficiency of rust removal operations.
- Wide adaptability
It is suitable for metal surfaces of different thicknesses and types, such as steel, stainless steel, aluminum, etc., and is widely used in multiple industries. The sandblasting process can select appropriate abrasive types and sandblasting parameters according to different metal materials and rust levels to achieve efficient rust removal operations. For example, for rust on the surface of steel, you can choose abrasives with higher hardness such as brown corundum or steel sand; for rust on the surface of stainless steel, you can choose relatively mild abrasives such as glass beads.
In addition, the sandblasting process can also be applied to metal structures of various shapes and sizes, such as pipes, storage tanks, bridges, etc. No matter how complex the shape of the metal structure is, the sandblasting equipment can achieve comprehensive rust removal by adjusting the angle and position of the spray gun.
- Benefit Analysis
- Cost-effectiveness
Rust removal by sandblasting has significant cost-effectiveness. First, the sandblasting process can complete the rust removal of equipment in a shorter time, reducing labor costs and losses caused by equipment downtime.
Secondly, the sandblasting process can select appropriate abrasive types and sandblasting parameters according to different metal materials and rust levels to achieve efficient rust removal. This can reduce the cost of sandblasting to a certain extent and improve the economic benefits of rust removal.
Finally, the metal surface after sandblasting has a certain degree of roughness, which helps to improve the adhesion of the coating and extend the service life of the coating.
- Environmental benefits
Unlike chemical rust removal, the waste generated during sandblasting is mainly abrasives and rust, which can be recycled and processed to achieve resource reuse. In addition, the sandblasting process can also reduce the company’s dependence on chemical rust removers and reduce the risk of environmental pollution caused by chemical rust removers. In some areas with high environmental requirements, such as water source protection areas and nature reserves, the sandblasting process is a more environmentally friendly rust removal method.
Actual application case: Rust removal of industrial equipment
Rust removal of factory pipelines
In a large chemical plant, the rust problem of pipelines has been plaguing the company’s production and safety. Because the pipelines are exposed to a humid environment for a long time, the surface rust is serious, which can easily lead to pipeline leakage and cause safety accidents.
To solve this problem, the company used the sandblasting process to remove rust from the pipeline. First, the technicians evaluated the degree of rust on the pipeline and determined the appropriate sandblasting parameters and abrasive types. Then, professional sandblasting equipment was used to perform comprehensive rust removal operations on the pipeline. During the sandblasting process, the technicians strictly controlled the sandblasting pressure and abrasive flow to ensure the rust removal effect while avoiding damage to the pipeline.
After sandblasting, the rust on the surface of the pipeline was completely removed, revealing the true color of the metal. To improve the corrosion resistance of the pipeline, the company also coated the pipeline, which greatly improved the corrosion resistance and effectively extended the service life of the pipeline.
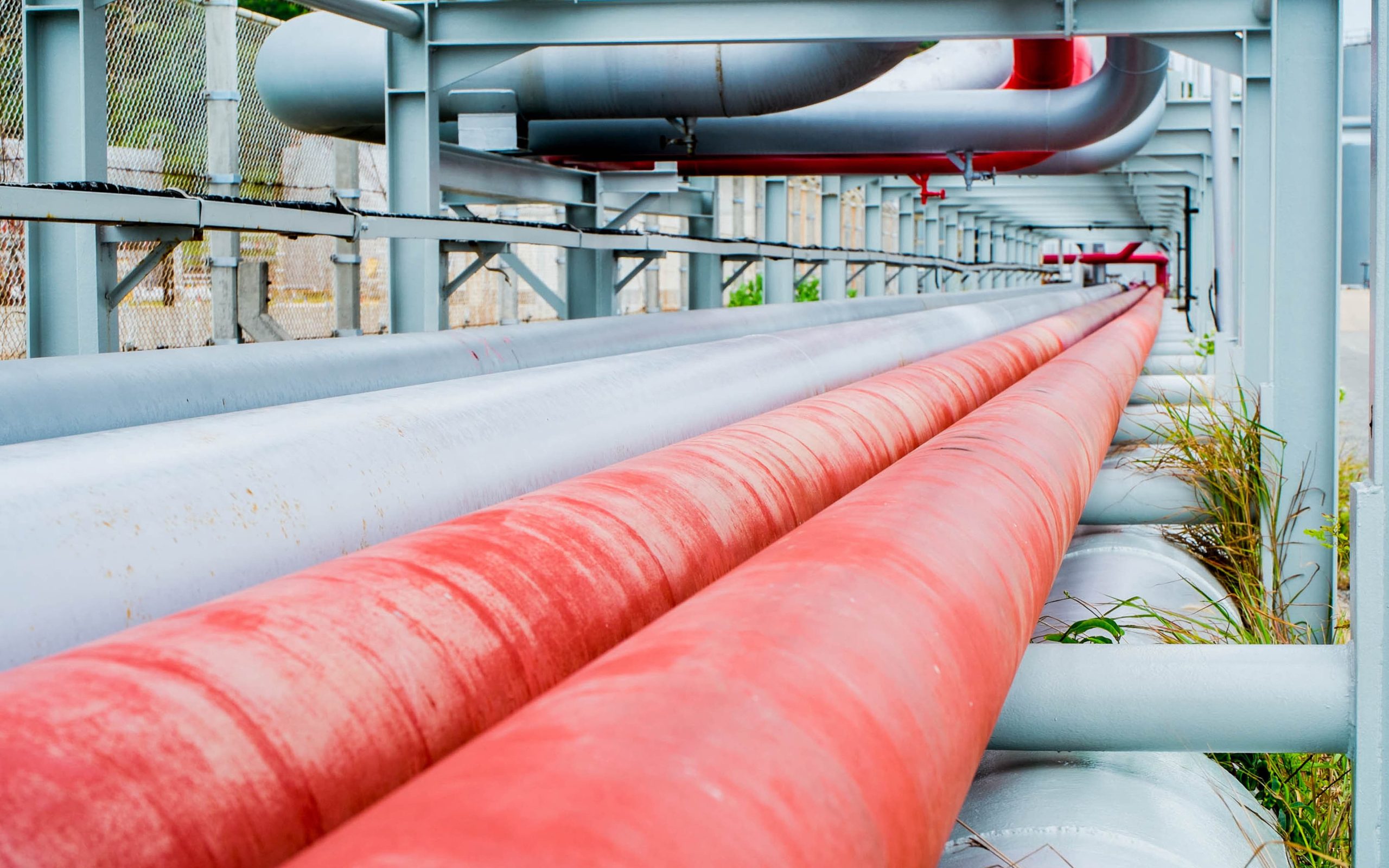
Oil and gas pipelines
Rust removal of storage tanks
Storage tanks are common equipment in petrochemical enterprises. Due to the long-term storage of various chemicals, the surface of the storage tanks is prone to corrosion and rust. If not handled in time, the rust will continue to expand and affect the safety performance of the storage tanks.
The surface of the storage tanks of a petrochemical enterprise is seriously rusted and needs to be rusted. The company used a sandblasting process for rust removal. Before the rust removal operation, the technicians first conducted a detailed inspection of the structure and degree of rust of the storage tanks and formulated a reasonable rust removal plan.
First, use a high-pressure water gun to clean the surface of the storage tank to remove impurities such as oil and dust on the surface. After that, use sandblasting equipment to perform comprehensive rust removal operations on the storage tank. During the sandblasting process, the technicians selected different sandblasting parameters and abrasive types according to the different parts and degree of rust of the storage tank. For example, for parts such as the top and bottom of the tank that are prone to water accumulation, larger abrasive particles and higher sandblasting pressure are selected to ensure the rust removal effect; for parts such as the side of the tank, smaller abrasive particles and lower sandblasting pressure are selected to avoid damage to the tank. In the last step, to improve the corrosion resistance of the tank, the company also carried out anti-corrosion treatment on the tank.
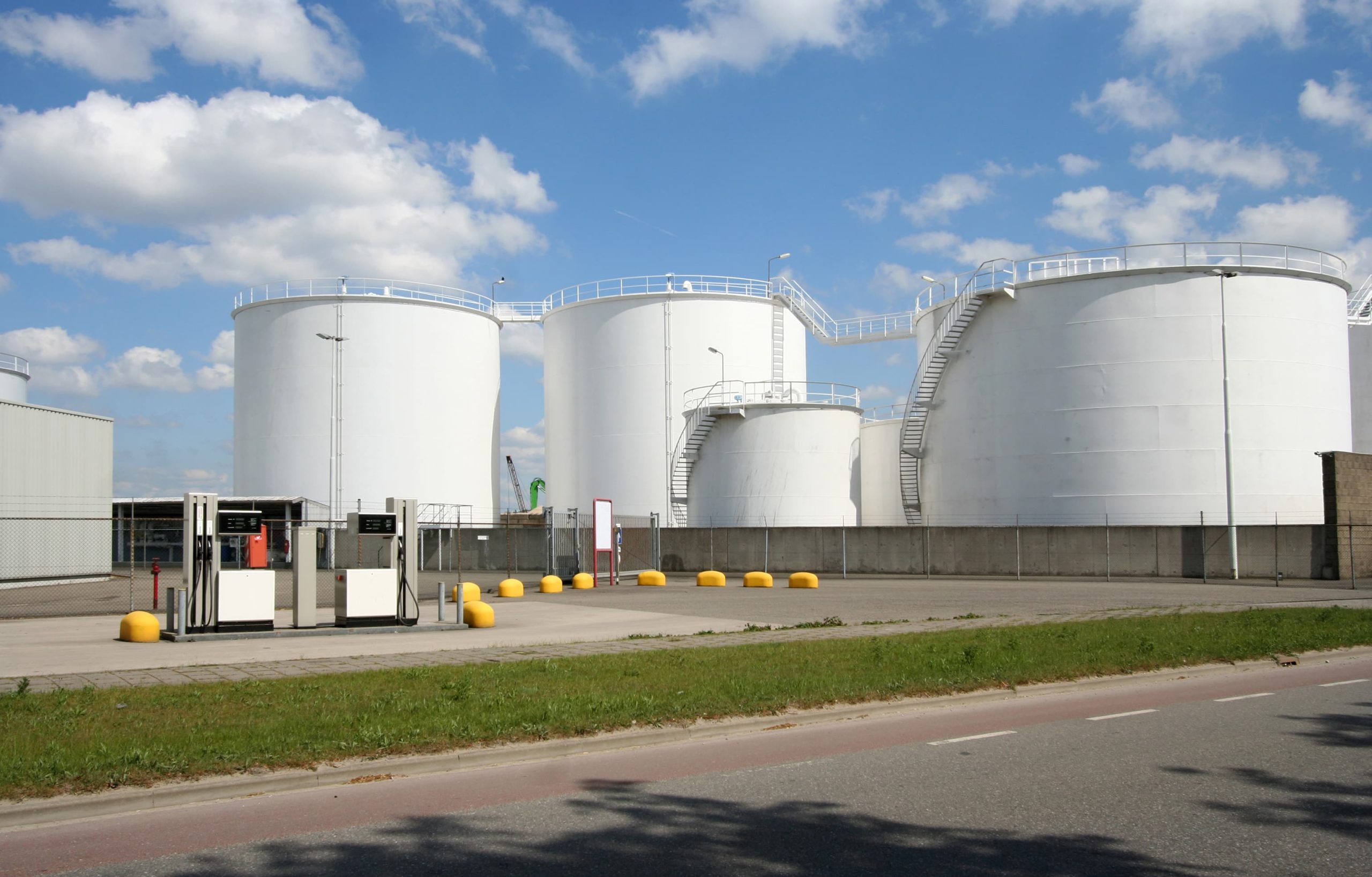
Large oil tank
In summary, the sandblasting process is efficient and reliable in metal rust removal. Compared with traditional rust removal methods, the sandblasting process has the advantages of fast speed, high efficiency, precise control, and wide adaptability. In practical applications, the sandblasting process can effectively remove rust on the metal surface, prepare for subsequent coating or paint treatment, and significantly extend the service life of the equipment.
At the same time, the sandblasting process also has obvious advantages in environmental protection and safety. Unlike chemical rust removal, sandblasting does not require the use of harmful chemicals, which reduces pollution to the environment. During operation, as long as strict safety measures are taken, sandblasting equipment can be safely operated in a confined space to reduce the impact on the surrounding environment. Therefore, I encourage you to consider sandblasting as the preferred rust removal solution when facing the problem of metal surface rust.
What do you think? Feel free to share with me in the comments.
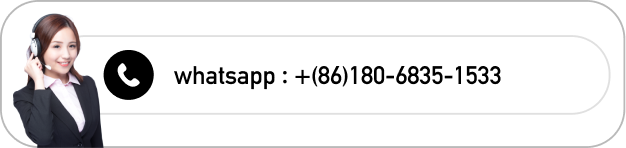