November 10, 2024
When dealing with complex structures or precision parts, do traditional rust removal methods always fail to meet your needs? Faced with hard-to-reach areas and complex geometries, how can you ensure that rust is completely removed without damaging the surface? Sandblasting rust removal technology is becoming an ideal choice for solving these problems with its high efficiency and customizability. This article will explore the application of sandblasting rust removal in complex structures and reveal its key advantages in the treatment of precision parts.
First of all, compared with traditional manual rust removal methods, sandblasting rust removal has the following significant advantages:
- High efficiency: Sandblasting technology can efficiently clean metal surfaces over a large area, much faster than manual grinding or chemical cleaning.
- Strong adaptability: Sandblasting can be applied to parts and components of various complex shapes, and can easily clean hard-to-reach areas.
- Controllable surface treatment effect: The sandblasting process can adjust the spray pressure, nozzle angle, and abrasive type as needed to ensure accurate rust removal of workpieces of different materials and shapes.
- Environmental friendliness: Modern sandblasting equipment can reduce the use of harmful chemicals, and many sandblasting media (such as glass beads and renewable ceramic particles) are recyclable and environmentally friendly.
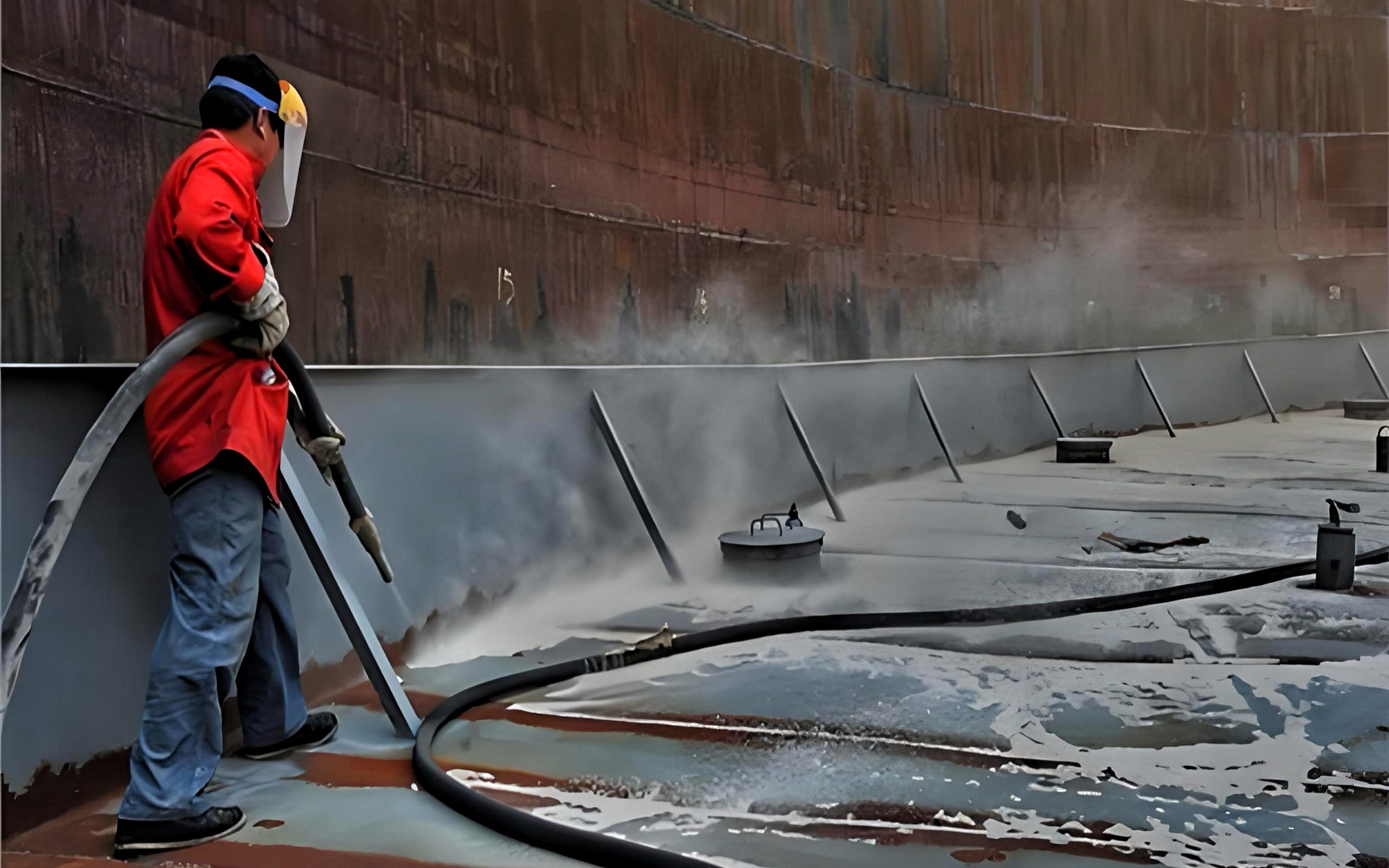
How sandblasting can deal with complex structures
Customer pain points
In industrial production, many companies often face problems that cannot be handled by traditional manual or chemical methods when removing rust on complex surfaces such as steel frame structures, equipment components, and precision mechanical parts. Especially when the parts have complex shapes difficult-to-reach gaps and dead corners, traditional rust removal methods often cannot completely remove rust and may even cause surface damage. In response to these challenges, sandblasting rust removal technology has emerged as an efficient and precise rust removal method and has become an ideal choice for many industries to deal with rust removal problems with complex geometries.
- Steel frame structures and large equipment components
Steel frame structures and large equipment components usually have complex geometries and large-scale surfaces. Sandblasting technology can completely remove rust through large-scale sandblasting without leaving dead corners or missing areas. Compared with traditional manual processing, sandblasting technology can improve work efficiency, reduce labor intensity, and avoid omissions and local uneven rust removal effects.
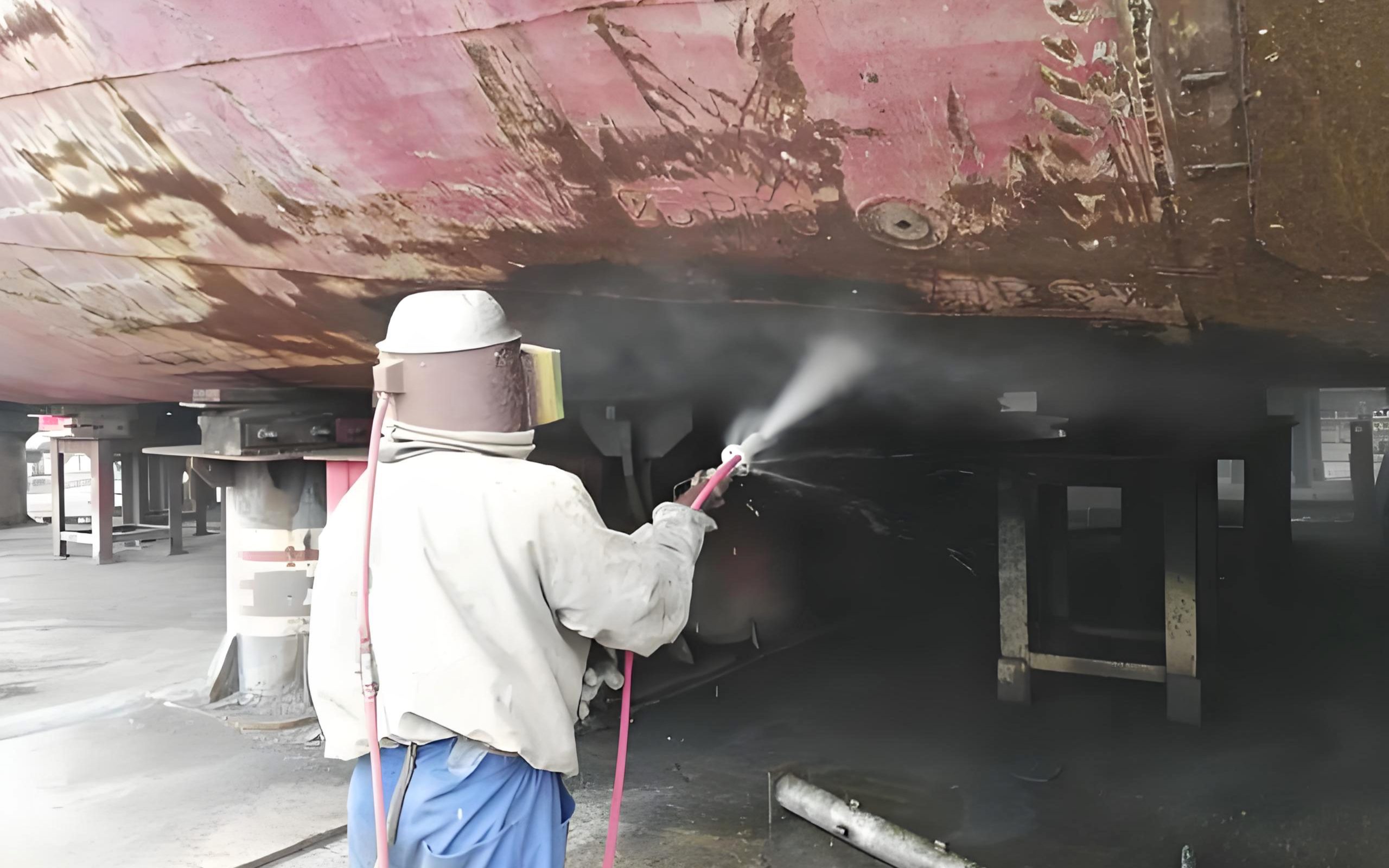
Removing rust from large equipment
- Precision mechanical parts and small parts
Precision mechanical parts are usually complex in shape and have many small gaps on the surface. These complex structures often bring great challenges to rust removal. Traditional rust removal methods make it difficult to remove rust embedded in the gaps. At the same time, due to the limitations of manual operation, it is easy to cause surface damage, affecting the function and appearance of parts.
Sandblasting technology can accurately process different surfaces of precision mechanical parts, especially rust removal in narrow gaps and complex contours. The angle, pressure, and type of sandblasting media can be adjusted according to the geometry of the workpiece. For some precision parts, the sandblasting system can accurately control the spray path to ensure that the high-precision surface is not damaged, avoiding the risk of damage that may be caused by traditional rust removal methods.
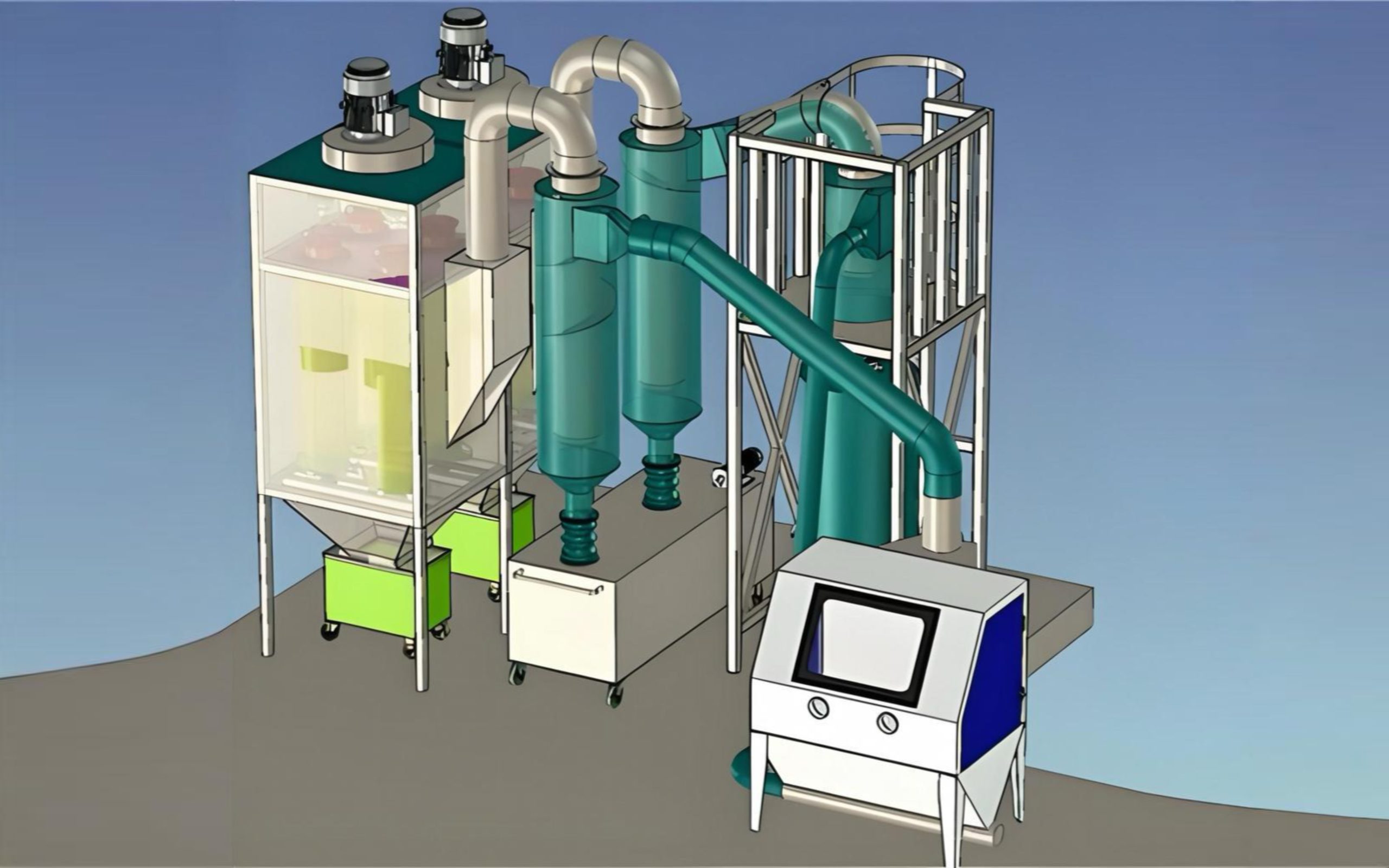
Schematic diagram of sandblasting small workpiece
Customized sandblasting equipment
Customer pain points
When processing parts with complex shapes and high precision requirements, standard sandblasting equipment often cannot meet the personalized needs of enterprises. Therefore, customized sandblasting equipment has become a must-have tool for many industries to solve rust removal problems. Customized sandblasting equipment can be tailored to the different needs of the workpiece to ensure efficient rust removal while protecting the surface from damage.
- Rotary sandblasting and automated sandblasting
For hard-to-reach areas and special-shaped parts, traditional sandblasting equipment may not provide uniform sandblasting effects. To solve this problem, rotary sandblasting systems and automated sandblasting systems came into being. These customized sandblasting equipment are uniquely designed to better cover hard-to-reach areas during the sandblasting process, ensuring no omissions and uniform rust removal effects.
- Rotary sandblasting system: Rotary sandblasting equipment allows the workpiece to rotate during the sandblasting process, ensuring that the sandblasting media can evenly cover every surface of the workpiece, especially on parts with complex geometries, which can better remove those hard-to-reach areas
- Automated sandblasting system: Automated sandblasting systems control the sandblasting process through preset programs, and can accurately control the sandblasting path, sandblasting pressure, nozzle angle, and sandblasting time to avoid errors and uneven effects caused by manual operation. Automated systems are particularly suitable for the rapid processing of mass-produced workpieces while maintaining a high degree of accuracy and consistency.
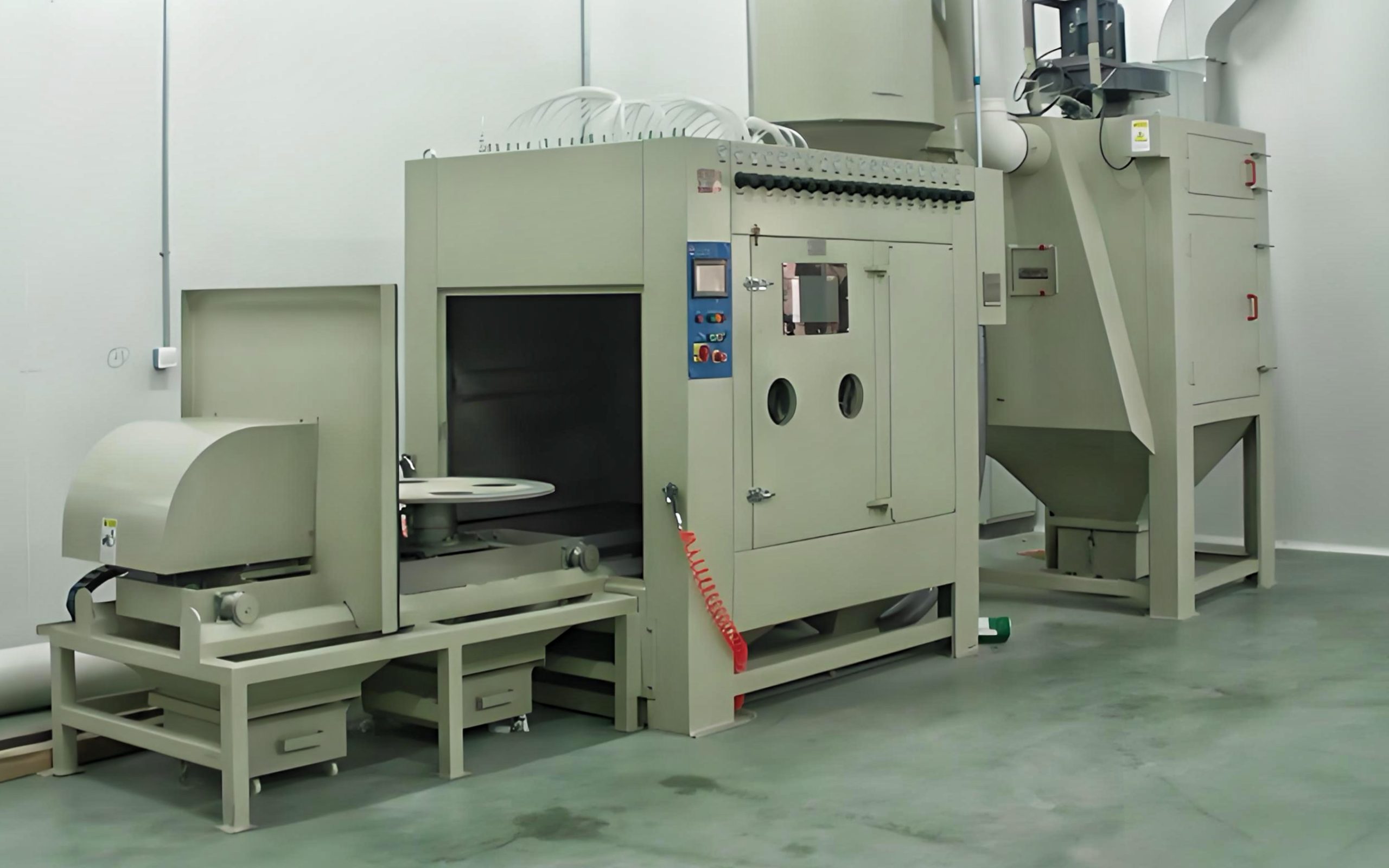
Automatic sandblasting equipment
- Benefits of customized equipment
- Optimize the sandblasting process: Customized sandblasting equipment can design the most suitable sandblasting solution according to the shape, size, and surface requirements of specific components. Whether it is a large-scale equipment component or a precision mechanical part, the best treatment effect can be obtained.
- Reduce errors and damage: Customized equipment can accurately control the various parameters of sandblasting, reduce errors and unnecessary damage, ensure that each workpiece is finely processed, and meet the precision requirements of the enterprise.
- Adapt to special needs: For some special parts, customized equipment can tailor sandblasting solutions according to their complex shapes and working environments, ensure efficient cleaning without damaging the surface quality, and extend the service life of the equipment.
Precision control
In the process of sandblasting and rust removal, how to balance the removal of rust and the maintenance of surface quality is a common concern of customers. Especially in the field of high precision requirements, factors such as sandblasting pressure, nozzle size, and the selection of sandblasting materials must be strictly controlled to ensure that the surface finish and precision are not affected while removing rust. Therefore, precision control has become a key link in the sandblasting and rust removal process.
- Adjustment of sandblasting pressure and nozzle size
Sandblasting pressure and nozzle size are key factors affecting rust removal effect and surface quality. By precisely controlling these two parameters, companies can adjust the strength and range of sandblasting according to the material and surface requirements of different workpieces to achieve the best rust removal effect.
- Sandblasting pressure: Excessive sandblasting pressure will cause excessive wear on the surface, while too low sandblasting pressure may not effectively remove rust. By fine-tuning the sandblasting pressure, you can ensure the rust removal effect while avoiding unnecessary damage to the surface.
- Nozzle size: The size of the nozzle determines the flow rate and coverage area of the sandblasting. By choosing the right nozzle size, you can ensure that the sandblasting covers the workpiece surface evenly and accurately, avoiding uneven rust removal during the sandblasting process.
- Selection of sandblasting materials
The selection of sandblasting materials is also crucial. Different sandblasting media have different hardness, particle size, and cleaning effects. Companies need to choose the most suitable sandblasting material according to the material and rust removal requirements of the workpiece. For example, for harder metal surfaces, choosing a blasting medium with higher hardness, such as aluminum oxide sand or steel shot, can ensure that rust is removed quickly and effectively; for metals with lower hardness, ceramic beads, and zirconium shots can be selected, and for more fragile materials, nylon sand, and resin sand can be selected.
- The impact of precision control on surface quality
In the process of removing rust, precision control can ensure the smoothness of the surface and avoid excessive wear and surface damage. Precision control is particularly important in fields with high precision requirements (such as aviation, precision machinery, etc.). By finely adjusting each link in the sandblasting process, it can be ensured that the surface of the workpiece maintains both efficient rust removal and unnecessary wear, meeting high standards of surface quality requirements.
The future of sandblasting rust removal
With the continuous advancement of industrial technology, sandblasting rust removal technology is also constantly innovating. Although traditional sandblasting rust removal has achieved remarkable results in many fields, with the increasing requirements for environmental protection, precision, and efficiency, new sandblasting technologies are constantly emerging, which has promoted the sandblasting industry to develop in a more efficient, precise, and environmentally friendly direction. In the future, sandblasting rust removal not only needs to continue to optimize existing technologies but also actively meet the challenges of intelligence and environmental protection.
- Innovation of new sandblasting media
With the improvement of sandblasting precision requirements and strict environmental regulations, more and more new sandblasting media have emerged. These new materials can improve rust removal efficiency while reducing the impact on the environment.
- Renewable ceramic media: Ceramic media are widely used in sandblasting and rust removal due to their high hardness and strong wear resistance. In recent years, environmentally friendly ceramic media have gradually been promoted. This type of media can be recycled and reused after use, which greatly reduces the generation of waste and can improve the economy of the operation. The use of this type of media not only reduces the consumption of natural resources but also reduces the generation of dust during sandblasting, which helps to improve the safety of the operating environment.
- Environmentally friendly sand media: In addition to ceramic media, some new environmentally friendly sands have also become the new favorites of the sandblasting industry. These sand media are made of natural ores or renewable materials, have strong decontamination ability, and generate less dust during sandblasting, reducing the harm to workers and the environment.
- Glass beads and plastic media: Glass beads and plastic media are gradually becoming the ideal choice for rust removal of precision equipment and vulnerable parts due to their lightweight and low wear. Especially when treating precision parts or vulnerable surfaces, glass beads can effectively remove rust, while causing less impact on the surface, reducing damage to the material.
- Advancement of automation and intelligent equipment
With the advancement of automation technology, sandblasting, and rust removal equipment are also developing in a more intelligent and automated direction. Automated sandblasting systems can greatly improve production efficiency while ensuring the consistency and stability of sandblasting quality.
- Automated sandblasting machines: More and more sandblasting equipment is equipped with automated systems. These systems can monitor parameters such as pressure, speed, and nozzle angle during sandblasting in real-time, and automatically adjust according to feedback, which can not only improve sandblasting efficiency but also ensure the stability and consistency of the sandblasting process, especially suitable for rust removal in mass production.
- Robotic sandblasting technology: Robotic sandblasting systems can achieve highly customized operations and adapt to sandblasting and rust removal tasks for complex workpieces. They can accurately identify the geometric shape of the workpiece through 3D scanning technology, and then adjust the sandblasting parameters according to actual conditions to ensure accurate rust removal effects. Robotic sandblasting technology is particularly suitable for high-demand industries such as aerospace and automobile manufacturing.
- Remote control of intelligent sandblasting equipment: With the development of Internet technology, many sandblasting equipment have remote monitoring and control functions. Operators can monitor the operating status of sandblasting equipment in real-time through the cloud platform, obtain data during the sandblasting process, and make adjustments as needed. This intelligent control system greatly improves the convenience of equipment management, reduces manual intervention, and improves the efficiency of equipment use.
- Environmentally friendly sandblasting technology
Sandblasting and rust removal, as an efficient cleaning method, also face environmental pressure. How to reduce the generation of dust during sandblasting and reduce environmental pollution has become an urgent problem to be solved in the industry.
- Low-dust sandblasting technology: In the traditional sandblasting and rust removal process, a large amount of dust is generated when the sandblasting medium collides with the workpiece, posing a threat to the health of workers and the environment. In order to solve this problem, low-dust sandblasting technology came into being. Low-dust sandblasting equipment minimizes the generation and spread of dust by improving the sandblasting room design and optimizing the nozzle and dust suction system. This technology is particularly suitable for large equipment and long-term operation environments.
- Wet sandblasting technology: Wet sandblasting is a new type of sandblasting and rust removal method that sprays by mixing sandblasting media with water. This method can effectively reduce the generation of dust, and at the same time improve the cooling effect of sandblasting, avoiding thermal damage to the workpiece surface due to excessive temperature. Wet sandblasting is particularly suitable for rust removal on metal surfaces, especially those with more delicate and fragile parts.
- Harmless sandblasting media: Use natural, harmless, and degradable sandblasting media, such as natural sand, orange peel particles, pepper particles, etc. These materials are not only environmentally friendly but also can reduce harm to human health. This type of sandblasting media has broad application prospects, especially suitable for food, pharmaceutical, and other industries.
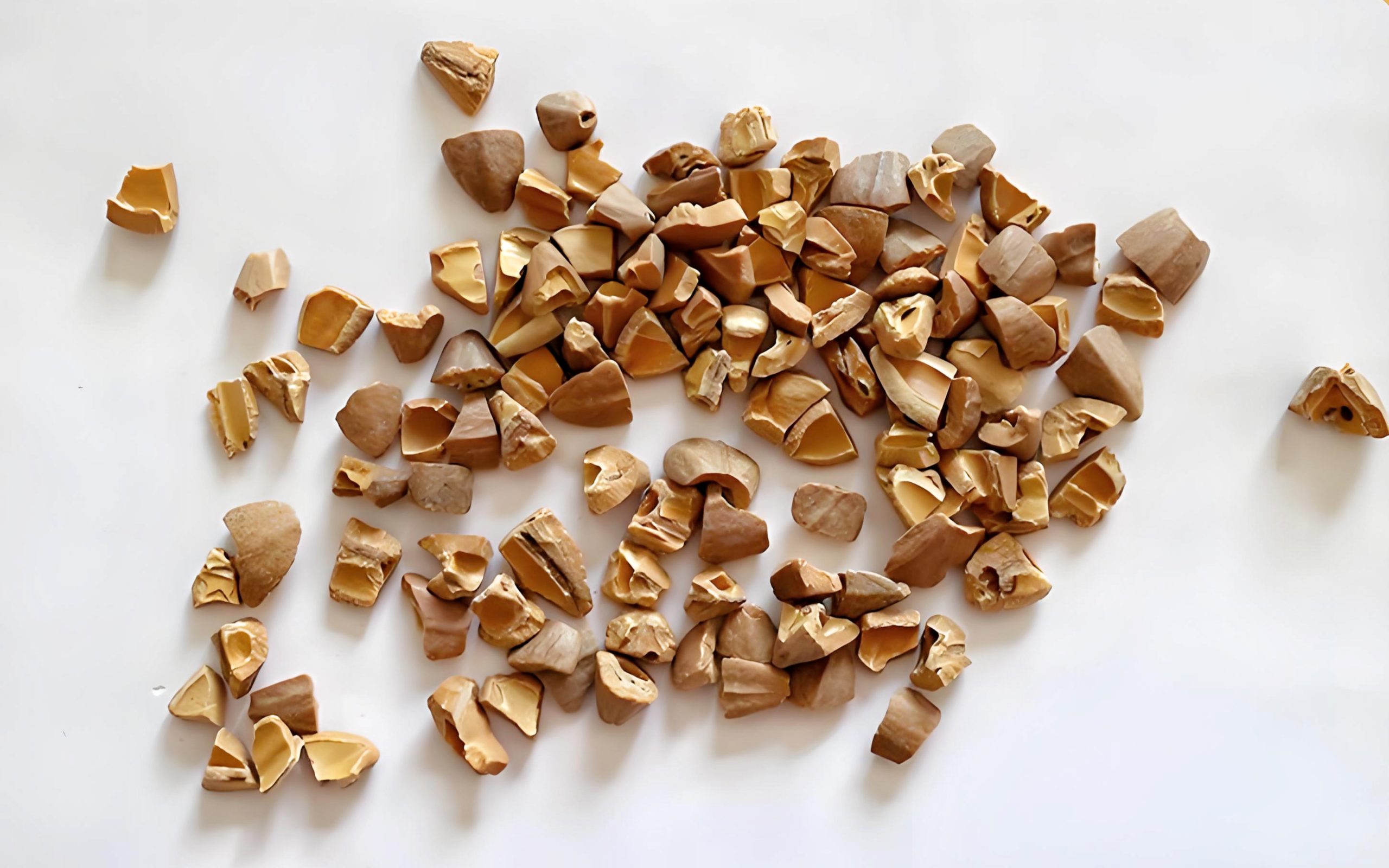
Walnut shell sand
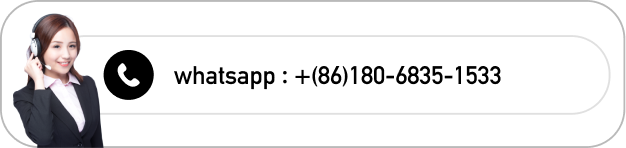