Quickly understand nylon polyamide deflashing media
September 10, 2024
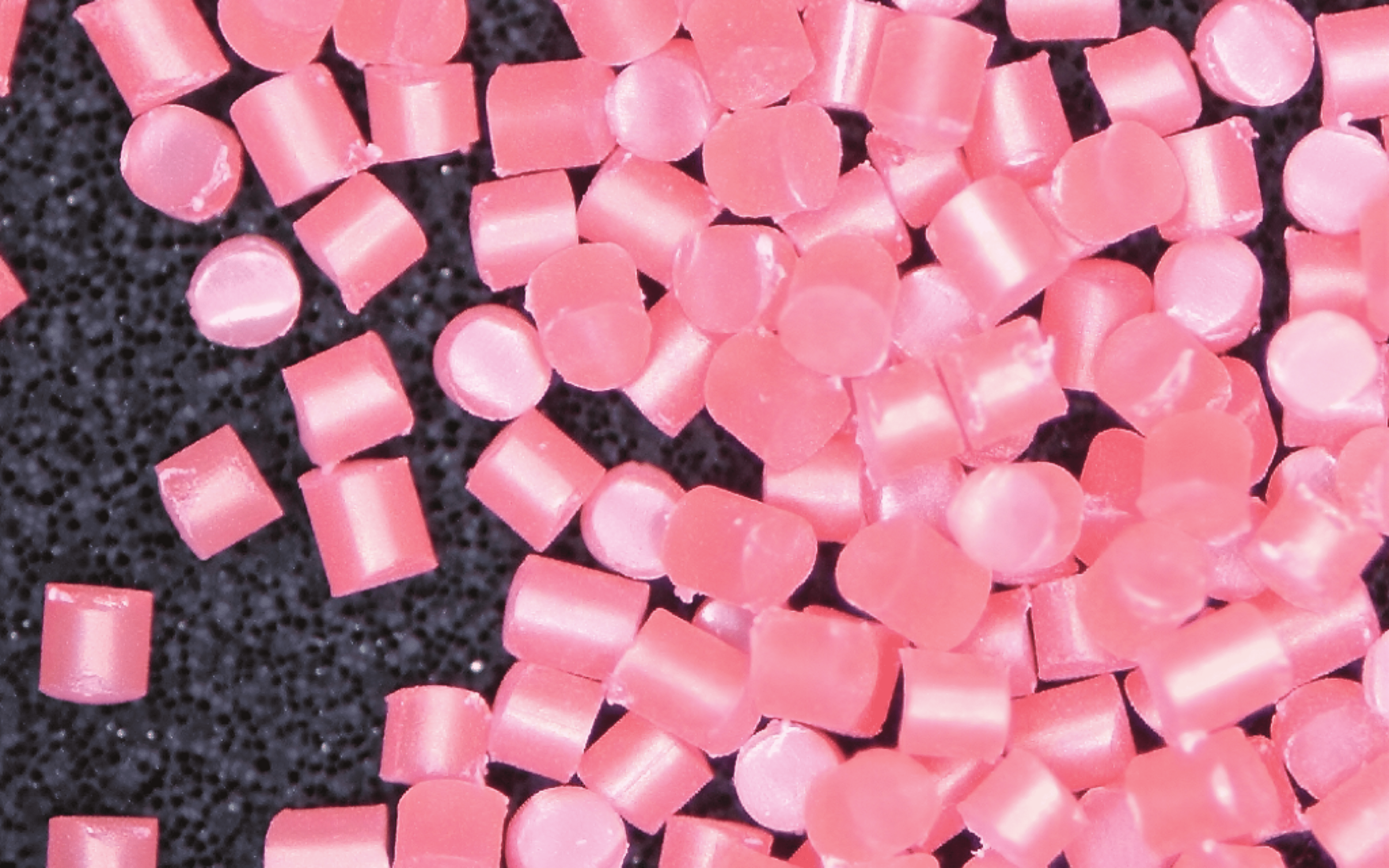
In modern manufacturing, deflashing technology is a key link to ensure product quality and performance. Burrs not only affect the appearance of parts, but may also cause assembly difficulties and functional failures. Therefore, choosing the right deflashing media is crucial to improving product quality. Deflashing media removes these burrs through mechanical friction or impact to improve the quality and performance of parts. As an efficient deflashing medium, nylon polyamide (PA) is widely used in many industries due to its unique physical and chemical properties. This article will introduce the characteristics and advantages, applications and economic benefits of nylon polyamide deflashing media in detail to help you better understand this medium.
What is nylon polyamide?
Nylon polyamide is a material widely used in deflashing and surface treatment of the edges of thermosetting plastic products and metal parts. It is made of polyamide monofilaments and usually presents cylindrical or polyhedral particles. Due to its efficient deflashing performance and fine processing ability on the surface of the workpiece, it has become an indispensable surface treatment material in many manufacturing industries. Product information can be viewed here. The following is a detailed data interpretation:
- Material properties
- Material
It is composed purely of polyamide 6 (PA6), that is, nylon 6, which has excellent mechanical properties and chemical resistance. This allows nylon polyamide to withstand large mechanical loads during the deflashing process and is compatible with a variety of workpiece materials, including plastics, rubber, metal, etc. PA6 achieves a good balance between strength and toughness, and is not easily broken or deformed by high pressure or friction, ensuring the stability and efficiency of the deflashing process.
- Particle shape
Mainly cylindrical and hexahedral shapes. Different particle shapes can provide a variety of striking effects. Cylindrical particles are usually used to provide a milder deflashing effect and are suitable for fine surface treatment, while hexahedral particles are more suitable for workpiece surfaces that require higher removal efficiency because their edges and corners can generate stronger friction. Particles of different shapes allow nylon polyamide to be flexibly selected according to the needs of the workpiece, providing higher processing efficiency while ensuring that there is no excessive wear where precision processing is required.
- Color
Nylon polyamide comes in a variety of colors: translucent milky white, yellow, red, and green. This appearance design actually has practical application significance. Nylon polyamide of different colors can help users easily distinguish the types of media in mixed or multi-step processes and improve operating efficiency. Color differentiation also helps to identify the wear state, facilitate timely replacement of materials, and ensure the consistency of processing results.
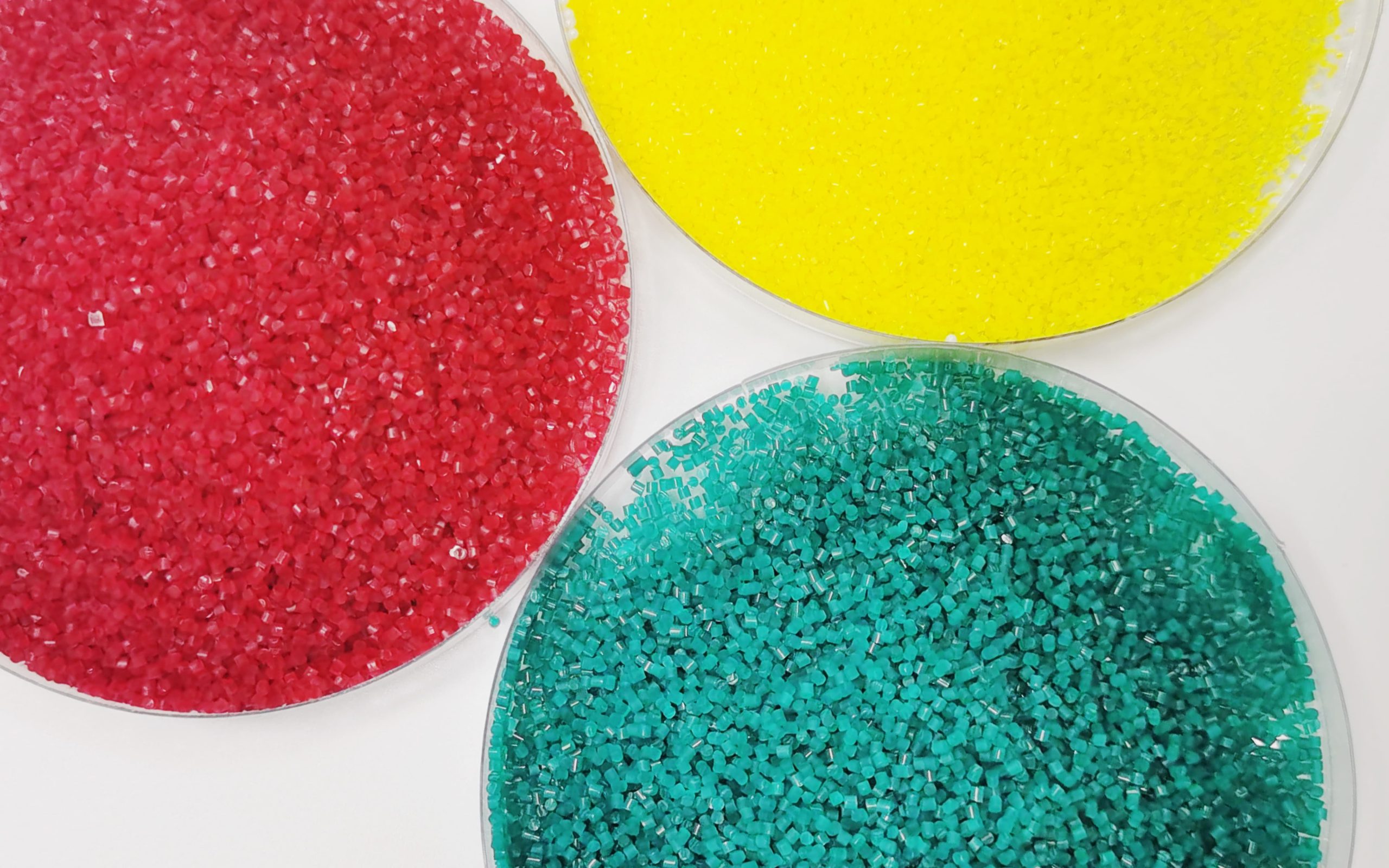
Different colors of nylon polyamide 6
- Physical properties
- True specific gravity
True specific gravity refers to the density of a material in a non-porous and bubble-free state, and is usually used to describe the properties of solid materials. The true specific gravity of nylon polyamide deflashing media is between 1.461 and 1.53, which means that its density is 1.461 to 1.53 times heavier than water. The high specific gravity means that nylon polyamide 6 has better strength and durability, and can provide stronger removal ability during impact while avoiding damage to more fragile materials.
- Bulk density
The lower bulk density (0.93-0.96g/cm³) means that nylon polyamide occupies a relatively large volume in the container and can cover more surface area, thereby improving the uniformity of the deflashing process. This helps the surface of the workpiece to be treated more consistently and reduce omissions.
- Water absorption rate
Water absorption rate is a measure of the material’s ability to absorb water in a humid environment. Nylon polyamide 6 has a low water absorption rate (1.8%) and can maintain its mechanical properties and dimensional stability in a humid environment. Even in a humid processing environment or one that requires water cooling, deflashing operations can still be performed effectively without processing errors caused by swelling due to water absorption.
- Mechanical properties
- Tensile strength
Tensile strength is a measure of the material’s ability to resist tensile force. The high tensile strength of nylon polyamide 6 (750kg/cm²) means that it is not easy to break or wear during use, and can remain stable for a long time under high load conditions (high pressure, high friction), thereby extending the service life and reducing material costs.
- Bending stress
Bending stress is a measure of a material’s ability to resist bending deformation, which means it will not deform easily when it hits or contacts a workpiece at high speed. Nylon polyamide has a high bending stress (1000kg/cm²), which can provide consistent impact force and removal effect during processing, and is particularly suitable for processing hard or irregular workpiece surfaces.
- Molding shrinkage
Molding shrinkage indicates the dimensional change of a material when it cools. The low shrinkage of nylon polyamide (1.2-1.5) allows it to maintain dimensional stability in high temperature environments or after molding, without significant deformation or volume change, ensuring consistency and precision in processing.
- Thermal properties
- Heat deformation temperature (HDT)
The heat deformation temperature refers to the temperature at which a material deforms under a certain pressure. Nylon polyamide 6 has an HDT of up to 205℃, which means it can maintain its shape and strength in high temperature environments, and will not soften or deform due to high temperature, making it very suitable for deflashing in high temperature processes.
- Melting point
The melting point of nylon polyamide is 220℃, which means it can remain solid in an environment close to this temperature. This makes nylon polyamide suitable for high-temperature processing, such as deflashing thermoplastic parts.
- Other characteristics
Nylon polyamide 6 has a low surface resistivity, which means it has good electrical insulation properties, ensuring that nylon polyamide does not generate static electricity when processing electronic or precision equipment, avoiding damage to parts due to electrostatic discharge, which is particularly important for processing electronic parts or other workpieces that are sensitive to static electricity.
In addition, nylon polyamide 6 does not produce odor during processing. The odorless property improves the quality of the factory’s working environment and reduces the impact on workers’ health.
Characteristics and advantages
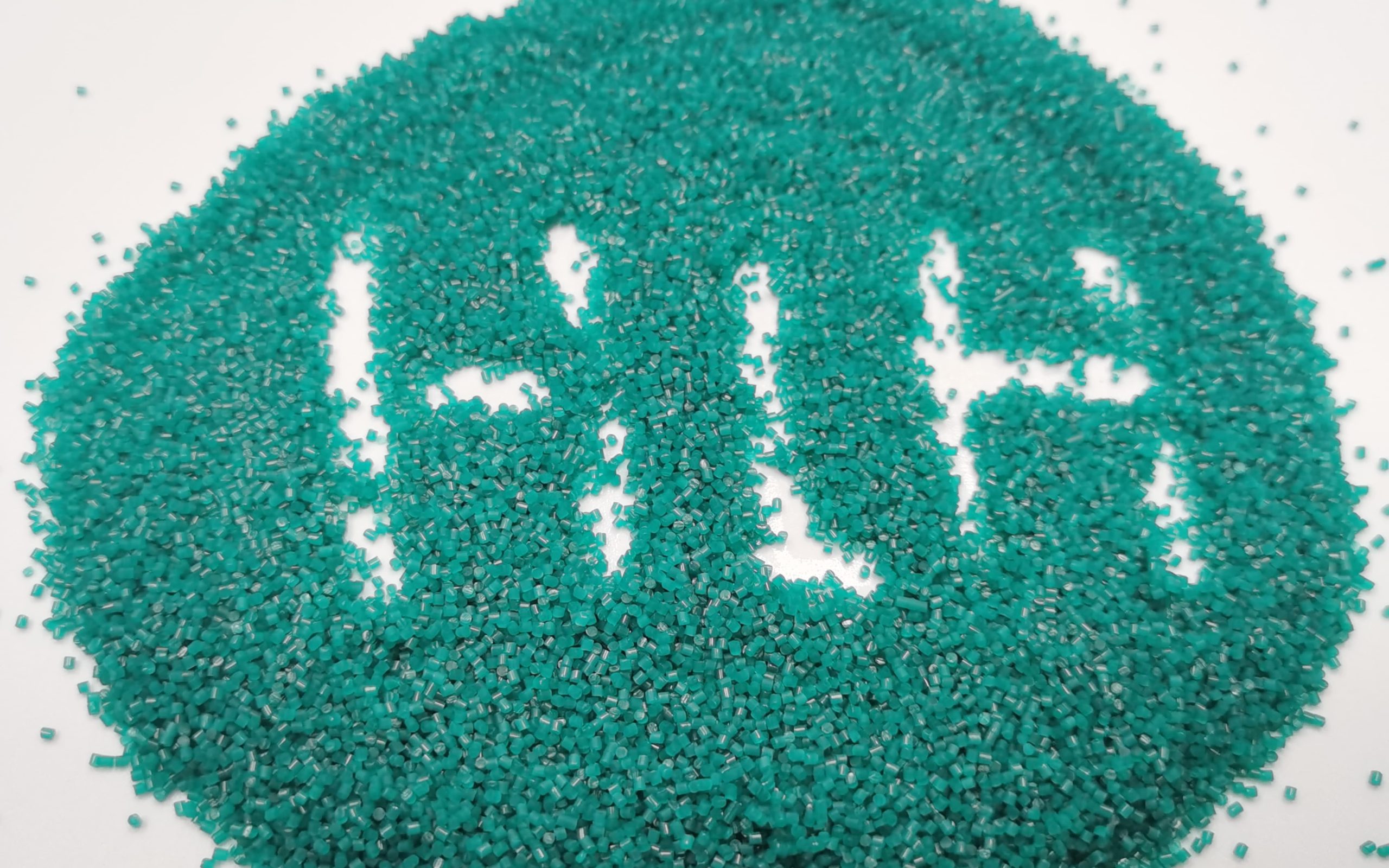
Based on the above product information, I have summarized the five major characteristics of nylon polyamide deflashing media and their corresponding advantages:
- High wear resistance
Nylon polyamide has excellent wear resistance, can maintain effective grinding ability for a long time, and quickly deburr. At the same time, it can maintain the stability and consistency of the medium itself during high-intensity use, reducing the need for frequent replacement and reducing maintenance costs.
- Excellent elasticity
The mechanical strength and elasticity of nylon polyamide enable it to effectively handle materials of different hardness and shapes during the deflashing process, especially for workpieces with complex geometries and hard-to-reach areas. Its excellent impact resistance ensures that it is not easy to break under high-intensity operation, and its good elasticity can flexibly provide uniform grinding effects, improving processing quality and precision.
- Stable chemical properties
Nylon polyamide 6 has good corrosion resistance to many chemicals, including grease, acid, alkali and chemical solvents, and can withstand high temperature and high humidity, adapting to use in various industrial environments, reducing performance degradation caused by harsh environments, thereby improving overall production reliability and economy.
- Less dust
Nylon polyamide 6 produces very little dust during the deflashing process, which can reduce the need for ventilation systems, and has low noise, which is very friendly to the health of workers and meets the environmental protection requirements of modern industry for the working environment.
- Excellent processing performance
Nylon polyamide can be easily processed into various shapes and sizes, making it suitable for different application requirements. This flexibility allows nylon polyamide to be widely used in different industrial fields and can meet specific process requirements, improving the efficiency and effect of the deflashing process.
Application fields
- 3D printing
- Removal of support materials and burrs: During the 3D printing process, the printed parts usually have burrs generated by support materials or the printing process. Nylon polyamide deflashing media can effectively remove these unwanted parts to ensure that the surface of the printed parts is smooth and fine.
- Surface treatment: Nylon polyamide can also be used to polish the surface of 3D printed parts to improve the surface gloss and touch.
- Shorten processing time: According to experimental data from 3D Printing Industry, nylon polyamide media can shorten the processing time by about 30% in the process of removing support materials and burrs of 3D printed parts.
- Automotive manufacturing
Removing casting burrs: During the casting process of automotive parts, burrs will appear on the surface of the casting. Nylon polyamide deflashing media can remove these burrs to ensure the accuracy and quality of the parts. In addition, the cost of subsequent processing and finishing is also reduced. According to data from automakers, this can reduce the production cost of each vehicle by about 5%.
- Aerospace
- Removing milling and drilling burrs: In the manufacturing process of aerospace parts, the accuracy of the parts is crucial. Milling and drilling are usually required, and the burrs generated must be removed. Nylon polyamide deflashing media can efficiently remove these burrs, ensure the precision and reliability of the parts, and meet strict industry standards.
- Surface polishing: Nylon polyamide 6 can also be used to polish the surface of aerospace parts to improve surface smoothness and durability. According to data from Aerospace Engineering Journal, parts treated with nylon polyamide have a lifespan of about 15% longer than untreated parts.
- Electronic manufacturing
- Removing burrs from electronic components: For electronic components that require precise connections, burrs or irregularities on the surface will cause subsequent use. Nylon polyamide can effectively remove these burrs, improve the matching accuracy of components, and ensure the functionality and reliability of electronic components.
- Improve product reliability: Removing burrs from electronic components can improve the overall reliability of the product and reduce the failure rate. According to the test of Electronics Manufacturing and Testing Journal, the failure rate of electronic components treated with nylon polyamide is reduced by about 20%.
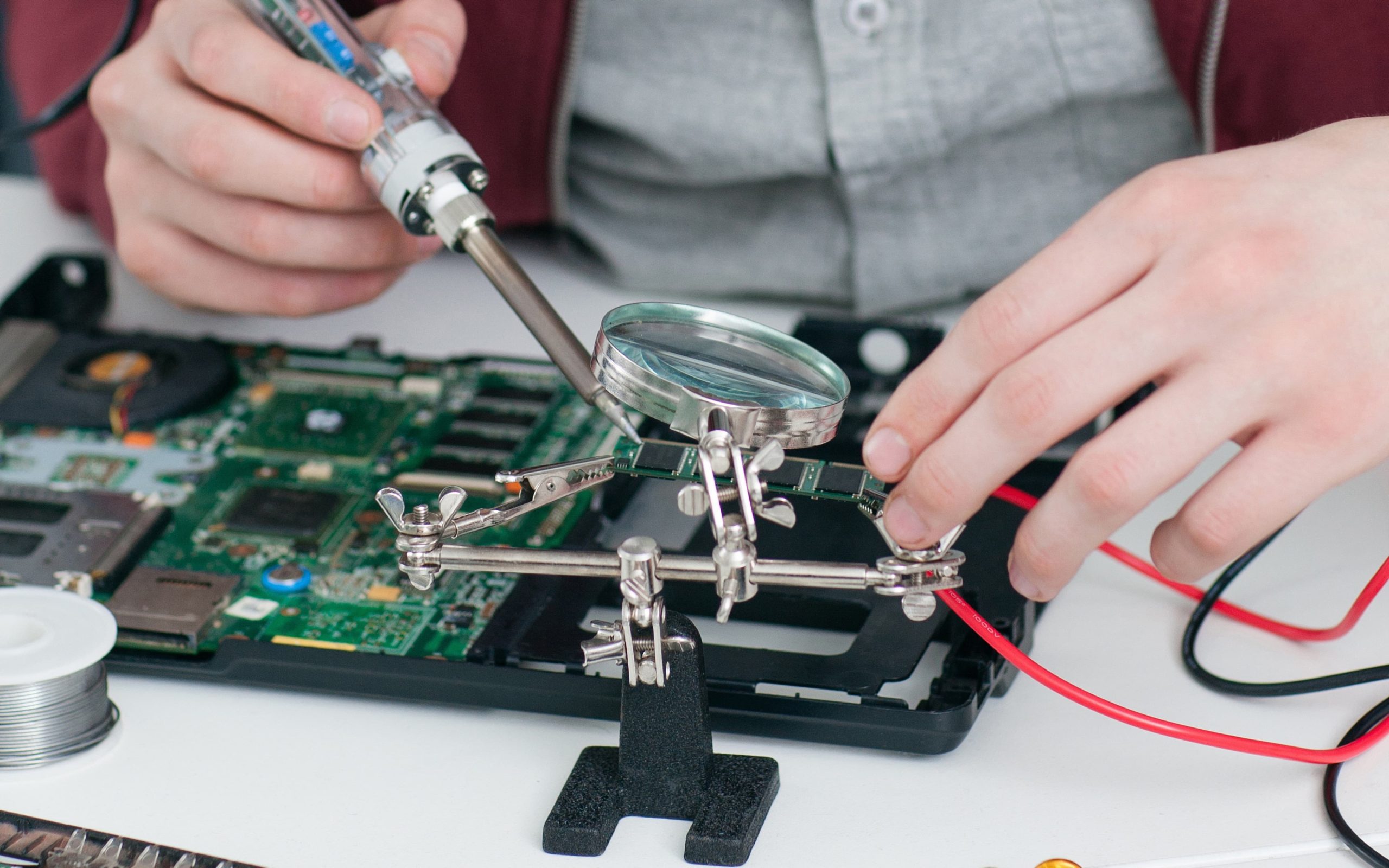
Electronic components that require precision handling
Economic Benefits and Environmental Protection
Economic Benefits
- Cost-effectiveness
Nylon is a mature material with a very mature production process, so it has a relatively stable and competitive material cost. In addition, nylon has good processability and can be processed by a variety of processing methods such as injection molding, extrusion and blow molding. This flexibility helps to improve production efficiency and reduce processing costs.
- Durability and long life
Nylon has excellent wear resistance and reduces the need for replacement and maintenance, which makes it economically beneficial in the long term. In addition, the high impact strength of nylon makes the product more durable in actual use, thereby reducing the frequency of damage and replacement and reducing the overall cost of use.
- Lightweight
As a plastic medium, nylon has a low density, so it can be used to replace traditional metal materials to reduce the weight of the final product. This is particularly economical for applications that require weight reduction, such as automotive and aerospace, which can improve fuel efficiency and reduce transportation costs.
- Design flexibility
Nylon can be made into parts with complex shapes through a variety of molding techniques, reducing the number of parts required for assembly. This design freedom can reduce production and assembly costs while improving product performance and aesthetics.
- Recycling and reuse
Nylon materials have good recyclability, and recycled nylon can be used to produce new products, further reducing material costs and environmental burden.
Environmentally friendly
- Environmental protection during production
Nylon processing generally produces less waste, especially in processes such as injection molding and extrusion. This helps to reduce the impact on the environment during production. In addition, modern nylon production processes have been optimized and energy efficiency has been improved, reducing energy consumption and emissions during production.
- Sustainability
Nowadays, more and more nylon products are beginning to use bio-based raw materials (such as plant-derived polyamides) to reduce dependence on petroleum resources. The use of such materials can reduce carbon footprint and environmental impact. Although traditional nylon is not easy to degrade, some new biodegradable nylons are being developed to reduce environmental pollution.
- Service life and waste reduction
Nylon’s durability and corrosion resistance make the product less likely to be replaced during its life cycle, thereby reducing waste generation and having a long service life. And because of its good durability, it reduces the frequency of maintenance and replacement, which helps to reduce overall resource consumption and environmental impact.
- Resource conservation
Nylon is very light, which helps to reduce energy consumption during transportation and use of products and reduces carbon emissions. In some applications, nylon can replace scarce or resource-intensive materials such as metal or glass, reducing the demand for these materials.
Nylon polyamide deflashing media stands out in modern manufacturing with its excellent physical and chemical properties, and implements the perfect combination of technology and environmental protection. From the fine processing of 3D printing to the finishing of castings in automotive manufacturing, to the precision processing of aerospace parts and the reliability improvement of electronic components, nylon polyamide has demonstrated its multifaceted charm and practical value in various fields. Through the introduction of this article, I believe you have some basic understanding of this medium. With the development of science and technology, this medium will continue to bring more possibilities and breakthroughs to the manufacturing industry, leading us to a more sustainable and high-quality future.
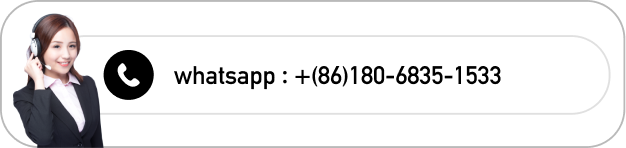