How to remove ceramic coatings efficiently?
October 30, 2024
In the field of precision manufacturing, how to efficiently remove ceramic coatings without damaging the substrate is a major challenge faced by customers. With the increasing application of ceramic coatings in industries such as aerospace, medical devices, and automobiles, it is particularly important to ensure surface quality and consistency after coating removal. Traditional removal methods make it difficult to balance efficiency, environmental protection, and precision, resulting in increased production costs, easy damage to the substrate, and affecting the performance and life of the final product. Therefore, choosing a process that can remove coatings efficiently, accurately, and safely has become a pain point that many industries need to solve urgently.
Industrial demand for ceramic coating removal
- Application scenarios of ceramic coatings
Ceramic coatings are widely used in the field of precision manufacturing, especially in industries such as aerospace and automobiles, to protect parts from extreme environments such as wear, corrosion, and high temperature. The following details the specific needs of ceramic coatings in different applications:
- High wear resistance and corrosion resistance: For example, parts such as turbine blades, combustion chamber inner walls, and pistons in automobile engines in aerospace often need to work in high-temperature and high-pressure environments. Ceramic coatings extend the service life of parts by forming a high-hardness, chemical-resistant protective barrier.
- Thermal barrier effect: In extremely high-temperature environments (such as gas turbines and internal combustion engines), ceramic coatings can act as thermal barriers to help maintain the operating temperature of parts, reduce thermal stress, and improve performance stability.
- Diversity of industrial needs: Ceramic coatings are not only used in the aviation and automotive industries but also drilling equipment in the oil and gas industry, sensitive parts in the electronics industry, etc. In these fields, the demand for removing ceramic coatings continues to increase with product upgrades and maintenance cycles, and more precise removal methods are needed to ensure the performance of parts after updates.
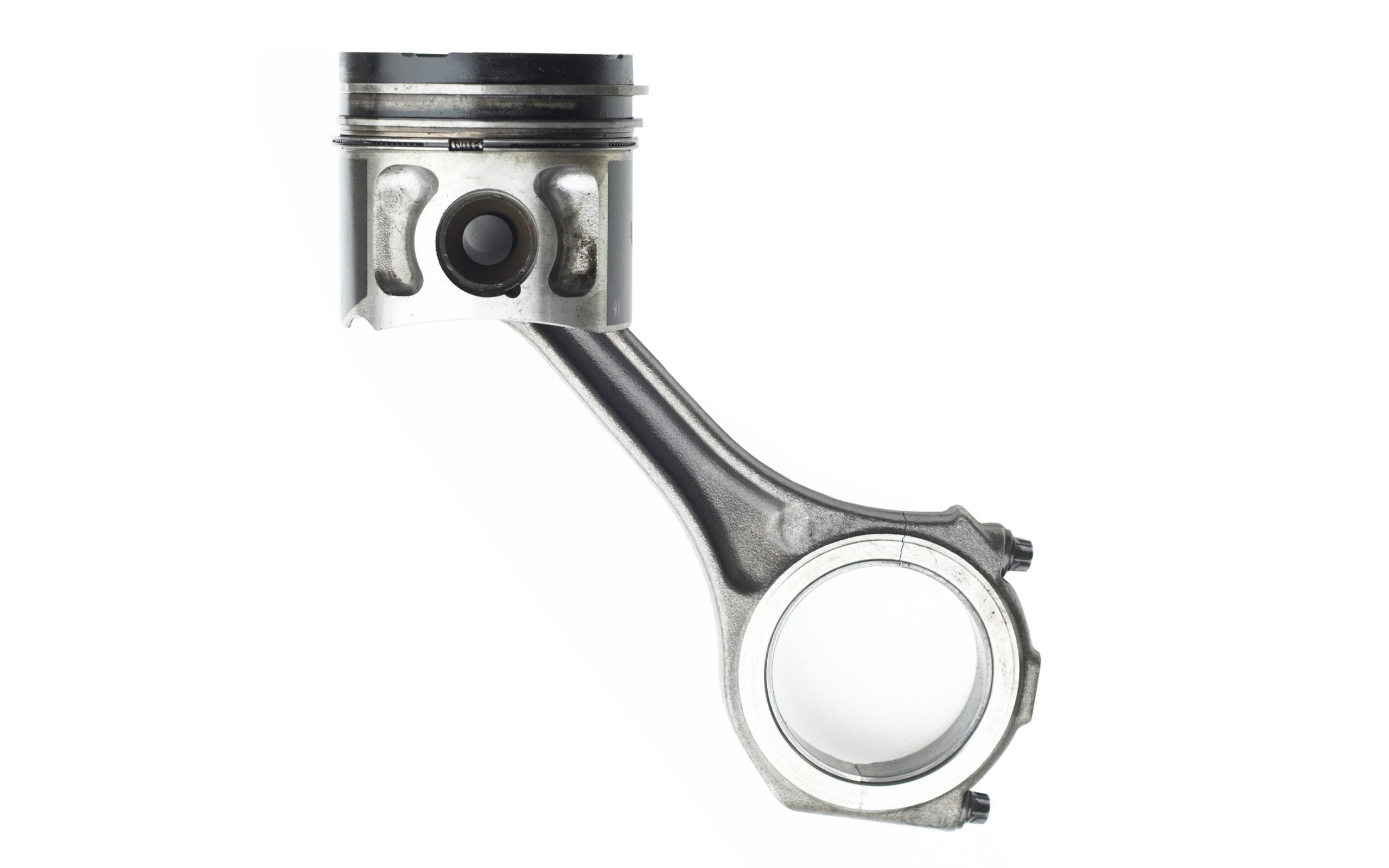
Engine piston and connecting rod
- Difficulties in removing old coatings
However, as the use time increases, the ceramic coating will gradually age or wear out, causing it to lose its protective effect or even crack, which will affect the function of the parts. Therefore, to extend the life of the parts, it is necessary to remove the old coating and reapply a new coating, but in various industries, the removal of old coatings is often not so easy. The following discusses the main pain points:
- Adhesion and residue problems of old coatings: Ceramic coatings usually have strong adhesion and high hardness, which makes the removal process more challenging. Traditional methods make it difficult to completely remove residues without damaging the substrate, which may affect the uniformity of subsequent coatings.
- Complex shapes and vulnerable parts of parts: Aircraft engine blades, automobile engine parts, etc. often have complex geometric shapes, and it is easy to damage small structures or sharp corners when removing the coating.
- Differences in thickness and material: The thickness, hardness, and material of the coating vary, which puts higher requirements on the removal process. It is necessary to choose the appropriate removal method to ensure the best effect.
- High standards for ceramic coating removal in precision manufacturing
Especially in precision manufacturing, the surface quality and substrate protection of parts are crucial, so there are strict requirements for the coating removal process.
- The necessity of protecting the substrate: In industries such as aerospace and medical, the substrate of parts is usually made of expensive high-performance metals or alloys, and any improper removal may cause damage to the substrate. Especially for the combustion chamber or guide vanes of the engine, if the strength of the substrate is weakened when removing the coating, it will affect the performance and safety of the parts.
- Efficiency and cost control: Traditional coating removal methods are often time-consuming and costly, and may cause parts to deform or contaminate due to heat. Modern manufacturing companies need a process that can ensure efficient coating removal and protect the substrate to shorten production cycles and reduce maintenance costs.
Advantages of sandblasting in ceramic coating removal
In the industrial field, sandblasting has gradually become a key choice for removing ceramic coatings. Its advantages are mainly reflected in precise control, environmental protection, and adaptability to complex shapes. The core characteristics of sandblasting and different removal schemes are described in detail below.
- Characteristics of sandblasting
- Precise control of thickness removal: During the removal of ceramic coatings, sandblasting can accurately operate according to the thickness of the coating, and the type and complexity of the substrate. For example, by adjusting the sandblasting pressure, flow rate, and angle, the thickness of the removal can be effectively controlled. Especially in the removal of thin layers of coating, this precision avoids the risk of excessive wear of the substrate.
- Environmentally friendly and chemical-free: Compared with chemical solvent removal methods, sandblasting relies entirely on physical impact to remove ceramic coatings, reducing chemical pollution to the environment. Sandblasting is particularly suitable in industries with high standards of environmental protection, such as aerospace and medical equipment manufacturing.
- Adapt to complex shapes: Traditional mechanical removal or chemical dissolution methods have the problems of low efficiency and inadequate edge processing when dealing with complex part shapes. The flexibility of the sandblasting process allows it to easily cope with these challenges. For example, special structural surfaces such as blades, sharp corners, and inner cavities can achieve uniform removal effects, and the human error is small, which is suitable for standardized processing requirements in mass production.
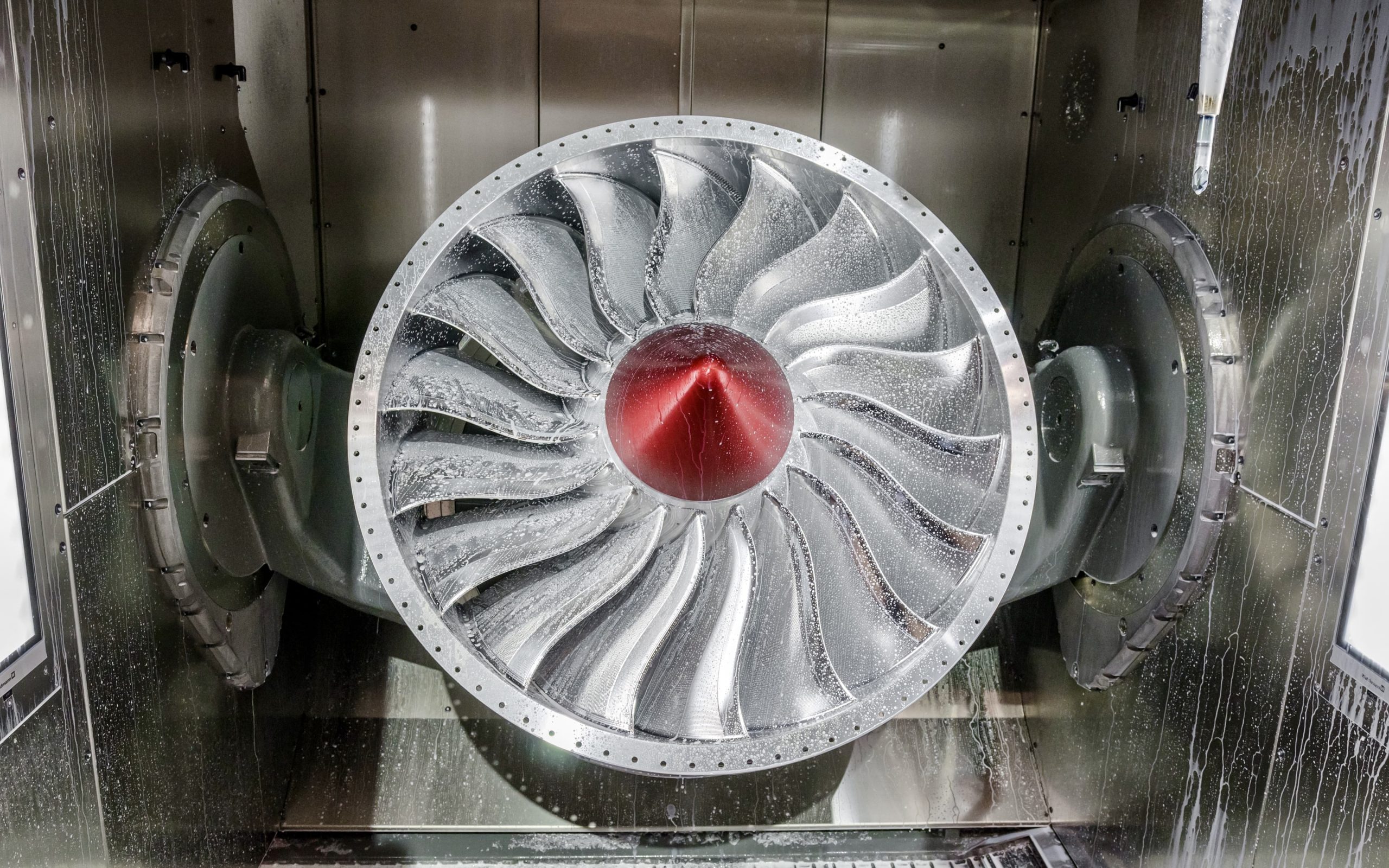
turbine
- Efficiency of sandblasting removal
Compared with traditional mechanical grinding and chemical solvent removal methods, the sandblasting process has obvious advantages in speed and quality control:
- Rapid removal of coatings: Sandblasting peels off the coating by high-speed impact of particles on the surface. Compared with chemical removal, it can save processing time and avoid the long process of coating immersion and dissolution. It is suitable for production lines with high requirements for removal efficiency.
- Reduce the thermal impact on the workpiece: The mechanical removal process often causes the workpiece to deform due to frictional heat generation, while the particles used in sandblasting have a lower temperature and will not generate thermal stress on the substrate, ensuring the accuracy and structural integrity of the parts.
- Removal solutions for different thicknesses
The sandblasting process can achieve efficient removal of coatings of different thicknesses by selecting different sandblasting media. In industrial practice, there are the following optimization solutions for thin and thick ceramic coatings:
- Removal of thin ceramic coatings: Fine-grained sandblasting media (such as ultrafine aluminum oxide blast media) can accurately control the thickness of the removal, which is especially suitable for minor repairs of precision parts. Aluminum oxide particles are hard and fine, and produce a weak but stable impact force on thin coatings, causing the coating to gradually peel off without affecting the microstructure of the substrate.
- Removal of thick ceramic coatings: Thick ceramic coatings usually require higher-strength sandblasting media (such as silicon carbide), which has strong cutting ability and high wear resistance. By removing layer by layer, the impact damage to the substrate caused by large-area peeling can be avoided, which is suitable for workpieces with high heat resistance and hardness requirements. In addition, the hardness and sharpness of silicon carbide particles enable each impact to accurately remove the preset thickness, improving the removal efficiency.
Sandblasting media suitable for removing ceramic coatings
To meet the removal needs of ceramic coatings of different thicknesses and materials, it is crucial to select appropriate sandblasting media. The characteristics of the sandblasting media determine the efficiency of the removal process, the protection effect of the substrate, and the degree of processing refinement. The following will introduce four commonly used sandblasting media in detail, and analyze their respective advantages, disadvantages, and typical application scenarios.
- Alumina
- Basic characteristics: Alumina is white or brown, mostly in the shape of angular particles, with high hardness and good wear resistance. The sharp edges of aluminum oxide particles make it suitable for removing thinner ceramic coatings, providing stable impact force while avoiding excessive wear on the substrate.
- Application scenarios: In high-demand industries such as aerospace and automobiles, aluminum oxide sandblasting is often used for minor repairs of precision parts. For example, when the coating is unevenly worn or needs to be repainted, aluminum oxide can evenly remove the old coating on the surface without affecting the flatness of the substrate. This characteristic makes it efficient and controllable when removing thin coatings, especially suitable for the need for detailed surface treatment of parts, such as surface cleaning and surface roughening of small parts. After using aluminum oxide to remove thin layers of ceramic coatings, the surface of the workpiece can remain relatively smooth and the substrate is almost unaffected, meeting the strict requirements of the precision manufacturing industry for substrate protection.
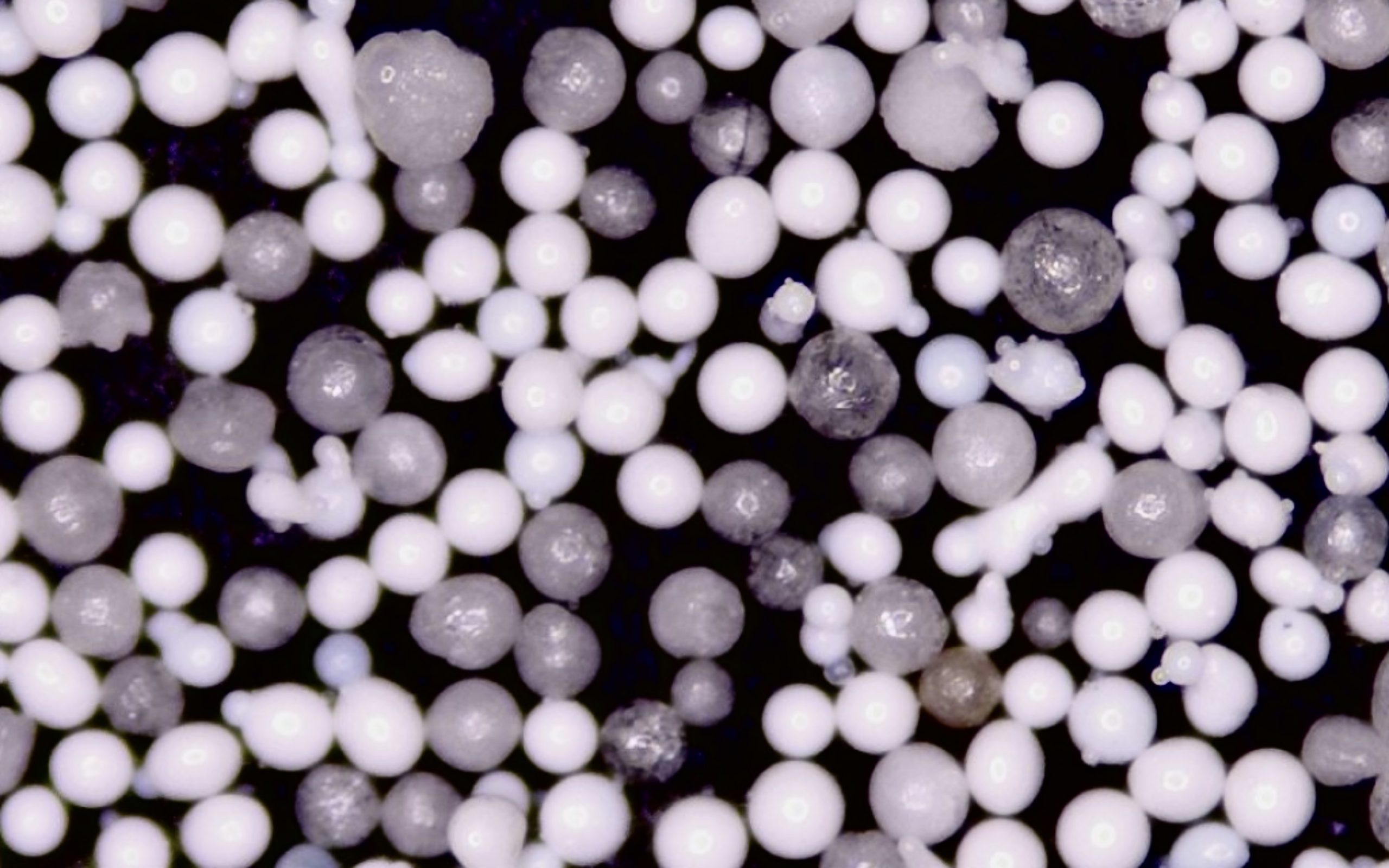
Ultrafine Aluminum Oxide Blast Media by HLH
- Silicon carbide
- Basic characteristics: Silicon carbide is dark gray or black, with sharp particles and higher hardness than aluminum oxide. Its extremely high cutting force makes it excellent for removing thick coatings. It is particularly suitable for surface treatment of high-temperature resistant and high-hardness parts, and can quickly peel off thick ceramic coatings.
- Application scenarios: Silicon carbide is widely used in aviation, power generation equipment, and other industries that are frequently exposed to high-temperature environments. In the past, traditional mechanical removal of thick coatings was often time-consuming and caused great damage to the substrate, while silicon carbide can remove ceramic coatings layer by layer in an efficient manner, especially on thermal spray or electroplating coatings. By removing thick coatings with silicon carbide, the surface of the workpiece is smooth and the substrate is highly intact, meeting the surface requirements of complex shapes and high-hardness materials. While ensuring the removal speed, the hardness and stability of silicon carbide avoid secondary wear of the substrate, meeting the reprocessing requirements of high-standard parts.
- Glass beads
- Basic characteristics: Glass beads are transparent to translucent, round particles in shape, relatively moderate in hardness, and suitable for gentle removal of lightweight coatings. Its round particle structure can produce a relatively uniform impact force on the surface, avoiding damage to the substrate by sharp edges.
- Application scenarios: Glass beads are widely used in medical devices and small precision parts. For parts with fragile materials or extremely high surface requirements, glass beads can ensure a gentle removal effect. For example, in the reprocessing of medical devices, using glass beads to remove old coatings can avoid damage to the device itself and maintain the integrity and smoothness of the substrate. The surface texture after glass beads are removed is fine and smooth, without obvious scratches, which is suitable for precision parts with high requirements for surface finish, providing a good foundation for subsequent processing.
- Ceramic beads
- Basic characteristics: Ceramic beads are generally white or gray, with a relatively round and smooth particle shape, and moderate hardness and toughness. It has excellent high-temperature resistance and has a good effect in removing hard ceramic coatings.
- Application scenarios: Ceramic beads are widely used in parts with high surface quality requirements, especially in the automotive and electronics industries. Compared with aluminum oxide and silicon carbide, ceramic beads have a relatively mild impact force, which is suitable for removing coatings while keeping the surface intact and avoiding the impact on fine structures. In situations where higher requirements are placed on surface finish and uniformity, ceramic beads can provide a stable removal effect and reduce the surface roughness of the workpiece. The surface of the workpiece after removal by ceramic beads is smooth and has high consistency, laying the foundation for the improvement of product appearance and performance, and is suitable for high-end consumer electronics and high-demand automotive parts processing.
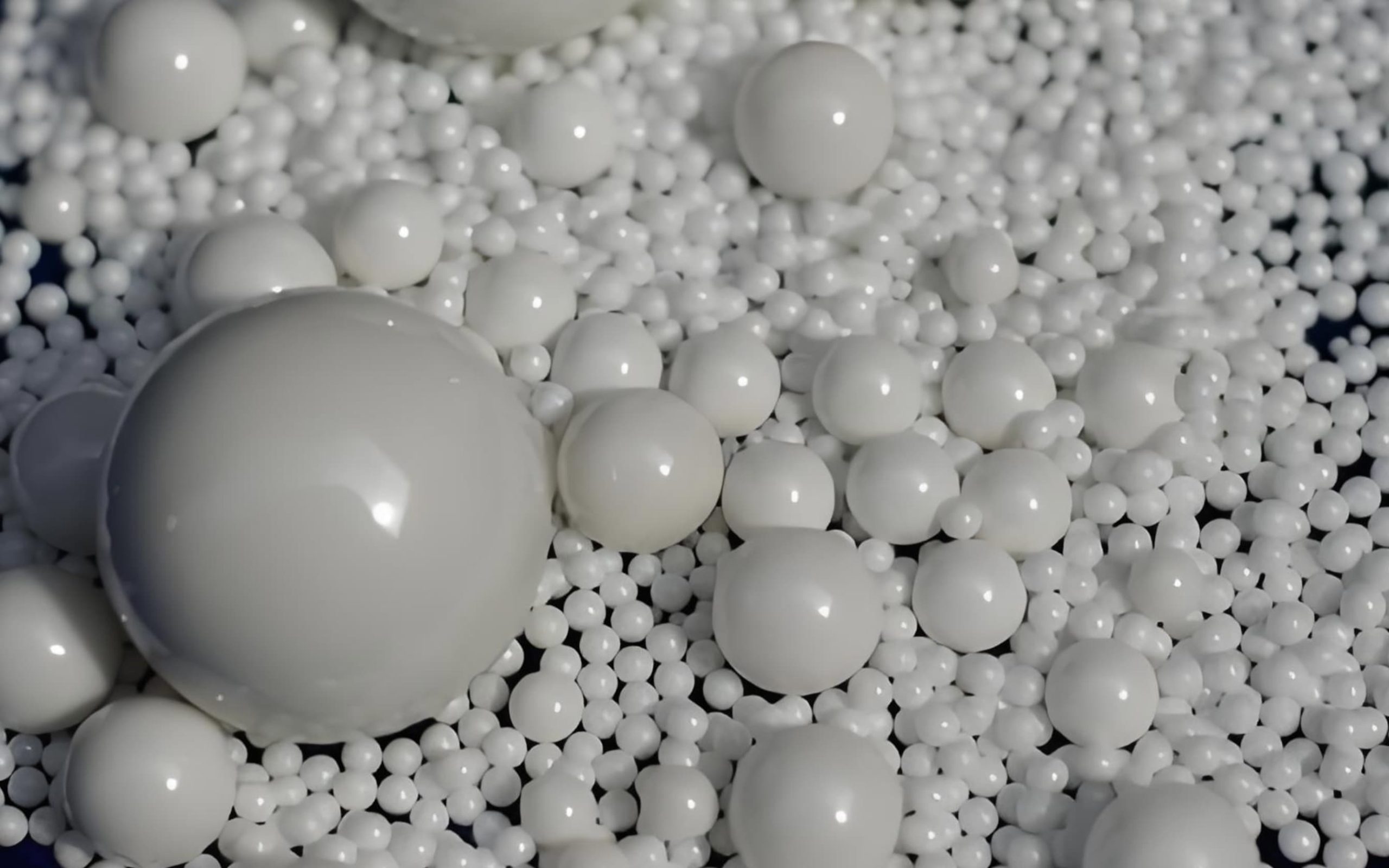
Ceramic Beads by HLH
Sandblasting technology shows obvious advantages in removing ceramic coatings. By selecting the right sandblasting media, the accuracy, speed and environmental friendliness of coating removal can be ensured, while effectively protecting the integrity of the substrate. This flexible surface treatment method not only provides a reliable solution for coating removal but also meets diverse industrial needs. The following is a summary of several key advantages of sandblasting technology in coating removal:
- Efficient and controllable: The diversity of sandblasting media enables both lightweight thin coatings and strong thick coatings to find suitable removal solutions, thereby achieving precise surface treatment.
- Environmentally friendly and pollution-free: Compared with traditional chemical removal methods, sandblasting technology avoids the use of harmful chemicals and reduces the risk of environmental pollution.
- Wide applicability: The choice of sandblasting media adapts to a variety of substrates and complex structures, making it suitable for use in multiple industries such as aviation, medical, electronics, and automobiles, making it an ideal choice for precision manufacturing.
- Ensure substrate safety: While achieving effective removal of coatings, the sandblasting process can maintain the original characteristics of the substrate, which is especially suitable for industries with strict protection requirements for the substrate.
- Meet industrial standards: The sandblasting process can meet the industry’s high requirements for precision parts, meet the consistency standards of safety and surface quality, and is an important coating removal method in processing in various industries.
The continuous development of sandblasting technology for removing ceramic coatings and the innovation of sandblasting media have enabled precision manufacturing to meet higher technical requirements and cost control goals. With the in-depth application of sandblasting technology, the selection of different sandblasting media and their optimization solutions will continue to play an irreplaceable role in removing ceramic coatings, and escort product quality and production efficiency in all walks of life.
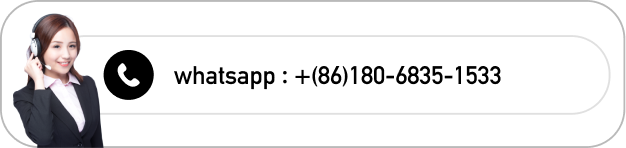