How to optimize coating application through surface preparation?
November 1, 2024
Why is surface preparation so important?
In construction and home decoration, have you ever encountered such a problem: the carefully selected coating still peels off, bubbles, or even mottles after application? This problem is not simply due to insufficient coating quality, but more likely due to insufficient surface adhesion, incomplete substrate cleaning, or neglect of environmental factors. How to solve these pain points through surface preparation and achieve perfect coating coverage? This article will help you find the answer and analyze how to optimize coating application through surface preparation to ensure that the construction effect is both durable and beautiful.
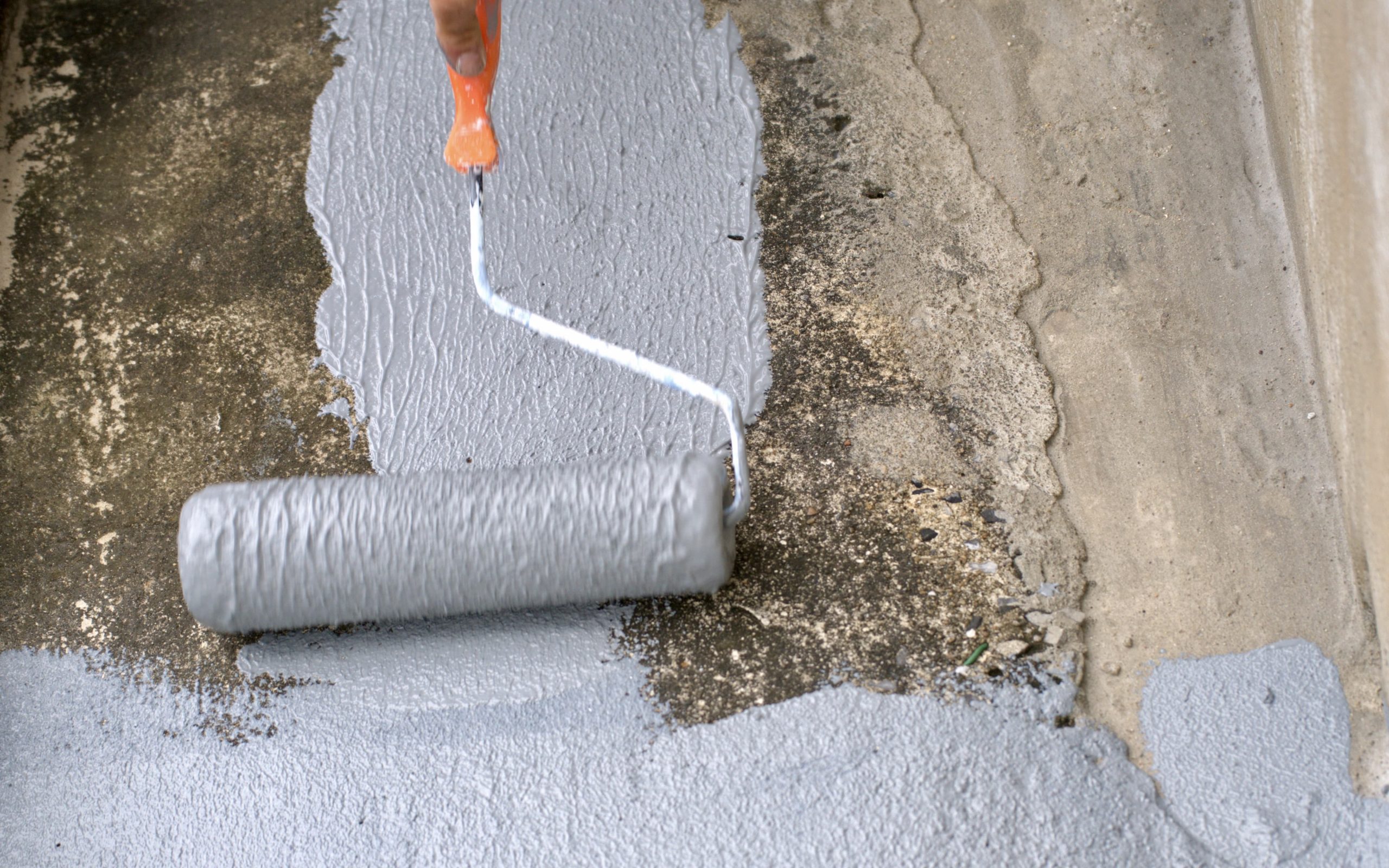
The core role of surface preparation in coating application
- Improve adhesion and durability
Coating adhesion is the key to ensuring the long-term effectiveness of the coating. Sandblasting or other preparation methods can remove oil, oxide layer, and dust on the surface, create a fine concave and convex structure, and make the coating more closely bonded to the substrate surface. For example, on hard materials such as metal and concrete, preparation can effectively prevent coating shedding and bubbling, thereby extending the service life of the coating.
- Extend coating life
Removing contaminants not only improves coating adhesion but also prevents premature aging. For example, if oxide residues on the surface of a metal substrate are not removed, the coating will fade, crack, and other problems. Pre-treating the substrate surface and adjusting the surface roughness can significantly extend the life of the coating and improve its oxidation resistance and durability.
- Improve the overall visual effect
In applications that focus on aesthetics, such as interior decoration and furniture coating, surface pre-treatment helps to make the coating more uniform and reduce color differences. For example, by sandblasting or grinding to remove stains and small defects on the substrate, the coating surface can be smooth and glossy, ensuring that the finished product appearance meets customer expectations.
Important needs for surface pre-treatment in coating applications
- Substrate types and common problems
In construction and decoration, the need for surface pre-treatment varies depending on the substrate. The following are common substrate types and their pain points in pre-treatment:
- Metal substrates: Commonly used in building structures and decorative parts, they are susceptible to oxides and rust, which affect coating adhesion. Sandblasting can effectively remove the oxide layer and improve the surface roughness.
- Wood substrate: Wood is mostly used for interior decoration and furniture, and dust, oil, etc. are easily left on the surface. Preparation can clean the surface and improve the uniformity of the coating.
- Concrete substrate: Walls and floors are typical applications. Because the surface is rough and porous, it is easy to absorb pollutants. Preparation helps to seal the substrate and enhance the adhesion of the paint.
- Plastic substrate: Some decorative panels and shells in home decoration use plastic, which usually has a smooth surface and is difficult to absorb paint. It is necessary to increase the roughness by grinding or sandblasting.
The respective characteristics of the surface of different substrates directly affect their bonding with the paint. The correct preparation method will reduce the risk of cracking and falling off of the coating in the later stage.
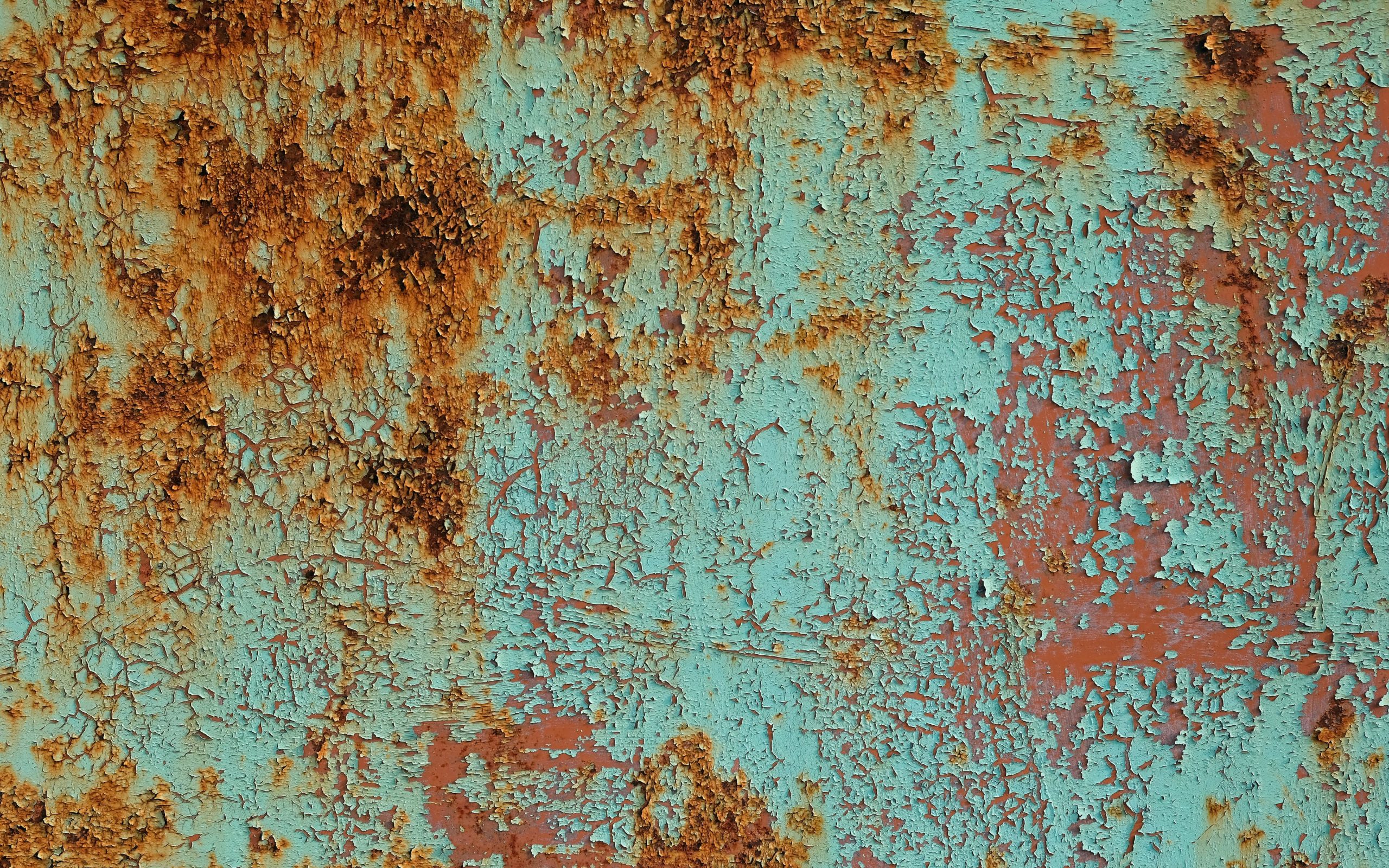
Peeling turquoise paint on a concrete wall
- Removal of pollutants: an important factor affecting surface quality
The presence of pollutants will weaken the bonding between the coating and the substrate, and even cause quality problems on the surface after construction. Common pollutants are as follows:
- Oil stains: Common residues in metal processing and wood coating. If not removed, the coating will not adhere firmly and affect the service life.
- Dust: Whether it is metal or wood, dust will hinder the uniform distribution of paint, especially fine particles will form uneven defects on the surface.
- Oxide layer and rust: Common problems on metal surfaces. The oxide layer will prevent direct contact between paint and metal, while rust will continue to spread under the coating.
Through appropriate preparation techniques, such as sandblasting, grinding, cleaning, etc., the residual pollutants can be significantly reduced, ensuring direct contact between the coating and the substrate surface and enhancing the bonding strength.
- Control surface roughness: The key to improving paint adhesion
Surface roughness affects the adhesion of paint on the substrate. For different coatings and substrates, it is particularly important to choose the appropriate roughness control method:
- Sandblasting technology: Through high-speed sand particles hitting the substrate surface, impurities and oxides are removed while forming microscopic roughness, which helps the paint to adhere evenly.
- Grinding and polishing: For delicate substrates such as wood, it is suitable to smooth the surface by light grinding, while forming tiny bumps and bumps to increase coating adhesion.
- Wet treatment: Use special solvents combined with mechanical grinding to effectively treat the concrete surface and improve the wettability of the paint.
The above methods not only optimize the coating effect but also reduce the subsequent maintenance costs. Roughness control needs to be selected according to the characteristics of different substrates and construction requirements to achieve the ideal adhesion effect.
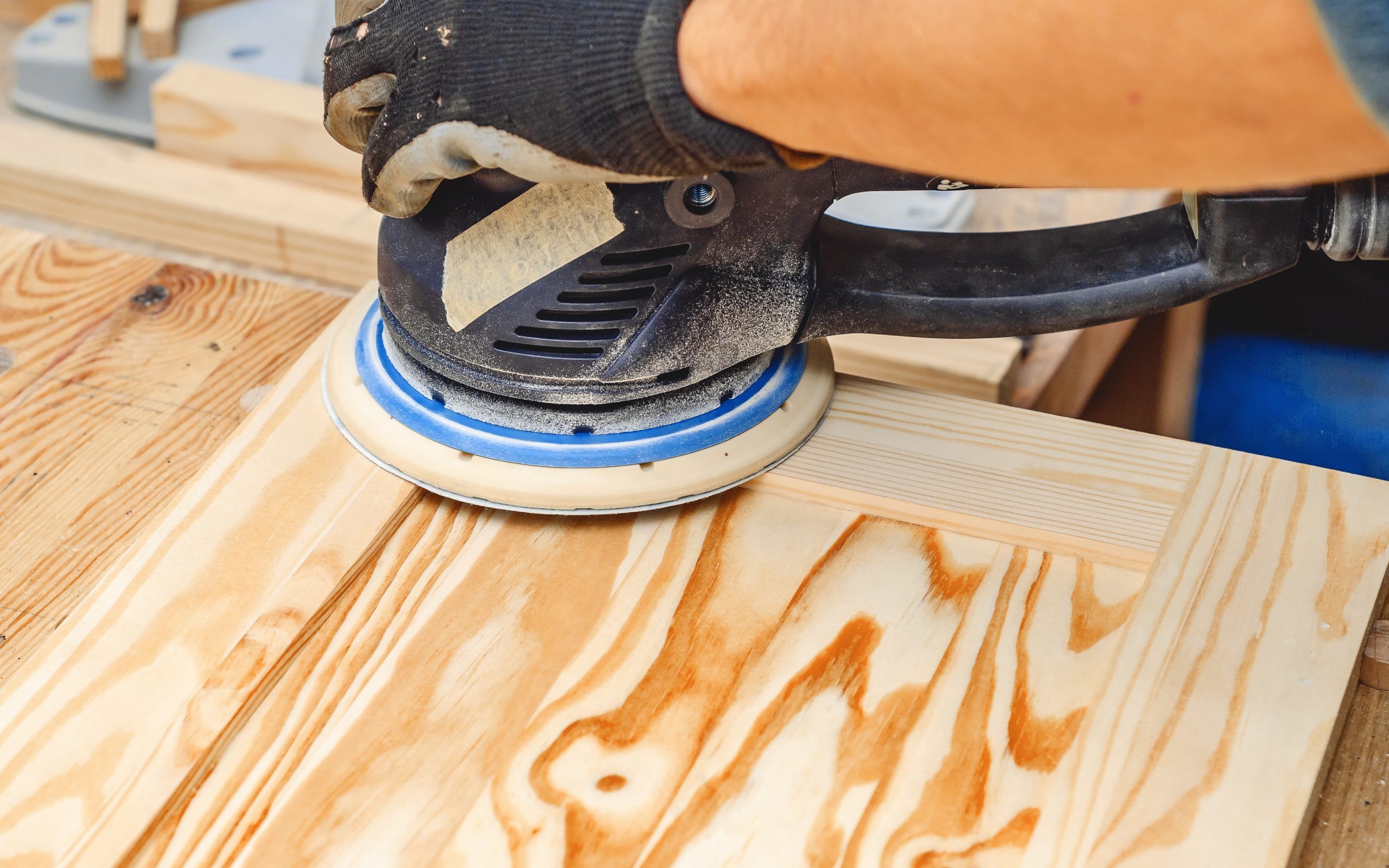
Manual sanding of wood
Surface cleaning technology supports coating applications
The selection and application of surface cleaning technology are crucial in optimizing coating adhesion and improving coating durability. If you are a customer engaged in the fields of construction, decoration, and DIY, then understanding different surface cleaning technologies can help you choose the most suitable solution to ensure the effective application of coatings. The following will introduce several cleaning technologies suitable for different substrates in detail.
- Ultrasonic cleaning: an efficient solution for deep cleaning
Ultrasonic cleaning technology uses sound wave vibration to generate tiny bubbles in the liquid, effectively removing tiny contaminants on the surface and gaps in the substrate. It is suitable for high-precision component cleaning, especially before painting, to ensure that the surface is completely free of dirt. The advantages of ultrasonic cleaning include:
- Efficient removal of fine particles: Ultrasonic cleaning can penetrate complex components and effectively remove fine oil and dust.
- Environmentally friendly cleaning method: Usually only water and mild detergent are needed, reducing the use of chemical solvents, which meets environmental protection requirements.
- Suitable for high-precision parts: For parts with extremely high requirements for surface finish and cleanliness, ultrasonic cleaning can provide an ideal solution.
- Sandblasting cleaning: An efficient and adaptable surface cleaning method
Sandblasting cleaning is a surface treatment technology widely used in the construction and decoration fields. It uses high-speed particles to impact the surface of the substrate to effectively remove dirt, rust, and oxides, thereby increasing the surface roughness and providing better adhesion for the coating. The advantages of sandblasting cleaning include:
- Strong applicability: Suitable for various substrates such as metal and concrete, and can effectively remove various dirt and rust layers.
- Improved adhesion: The microscopic roughness produced after sandblasting allows the coating to adhere better to the substrate and reduce the risk of falling off.
- Efficient operation: It can quickly process large areas of surface and is suitable for the needs of large engineering projects.
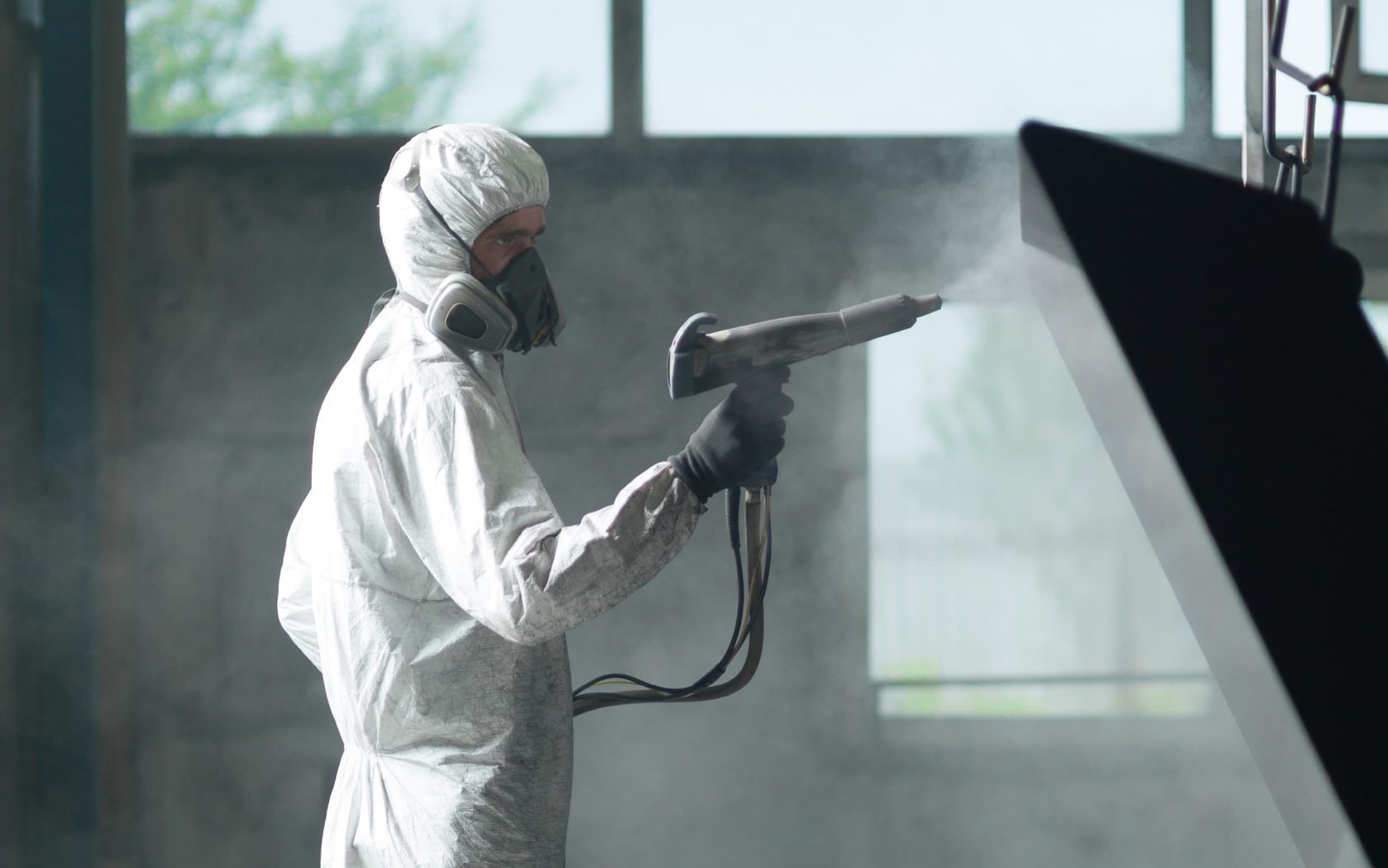
Sandblasting Demonstration
- Wet cleaning: Suitable for delicate surface cleaning
Wet cleaning uses a combination of water and detergent, and is suitable for treating more sensitive substrates such as wood and plastic. Wet cleaning can effectively improve the adhesion of coatings by removing surface oil and fine particles. The advantages include:
- Reduce static electricity and particles: Wet cleaning can remove static electricity and tiny impurities adsorbed on the surface of the substrate to ensure uniform coating.
- Suitable for a variety of substrates: When cleaning substrates such as wood and plastic, wet cleaning will not cause excessive surface roughness.
- Adjustable detergents: Users can flexibly adjust the formulation of detergents according to different types of contaminants to achieve the best cleaning effect.
- Mechanical cleaning: Combining multiple tools to improve efficiency
Mechanical cleaning methods use various cleaning tools such as brushes, cleaning machines, etc., combined with chemical solvents, and are suitable for surface cleaning of different substrates. This method is suitable for cleaning tasks with larger areas, especially in decoration construction:
- Efficient treatment of large areas: Mechanical cleaning can quickly clean larger areas and is suitable for construction sites.
- High flexibility: Different mechanical tools can be selected for cleaning according to different surface conditions and types of contaminants.
- Combined with chemical cleaning agents: By combining mechanical force and chemical cleaning agents, a deeper cleaning effect can be achieved.
Application of sandblasting equipment in construction and decoration
In construction and home decoration, choosing the right sandblasting equipment can not only improve work efficiency but also ensure the quality of surface treatment. Different sandblasting equipment has different functions and applicable scopes. Understanding the characteristics of these equipment can help professionals and DIY enthusiasts choose the best solution. The following are several types of sandblasting equipment suitable for the construction and decoration fields and their applications:
- Fixed sandblasting machine
Fixed sandblasting machines are suitable for large-scale sandblasting tasks and are common in industrial and construction sites. They have efficient working capacity and powerful processing capabilities and are suitable for the processing of large-area substrates such as concrete and steel. Its main advantages include:
- High efficiency: It can process large-area surfaces and is suitable for continuous operation in factories and construction sites.
- Versatility: Different types of sandblasting media can be replaced to meet different cleaning and surface treatment needs.
- High degree of automation: Many fixed sandblasting machines are equipped with automatic control systems, which can improve work efficiency and reduce the labor intensity of operators.
- Handheld sandblasting machine
For smaller projects or delicate work, handheld sandblasting machines are a flexible and convenient choice. This type of equipment is usually used for home decoration, DIY projects, and small-scale construction. Its advantages include:
- Flexible and convenient: Small size, simple operation, suitable for sandblasting in small spaces and on objects with complex shapes.
- Easy to carry: Lightweight design makes it easy to move between different locations, suitable for individuals and small projects.
- Fine control: A handheld sandblasting machine allows the operator to better control the strength and range of sandblasting, suitable for delicate cleaning and decoration.
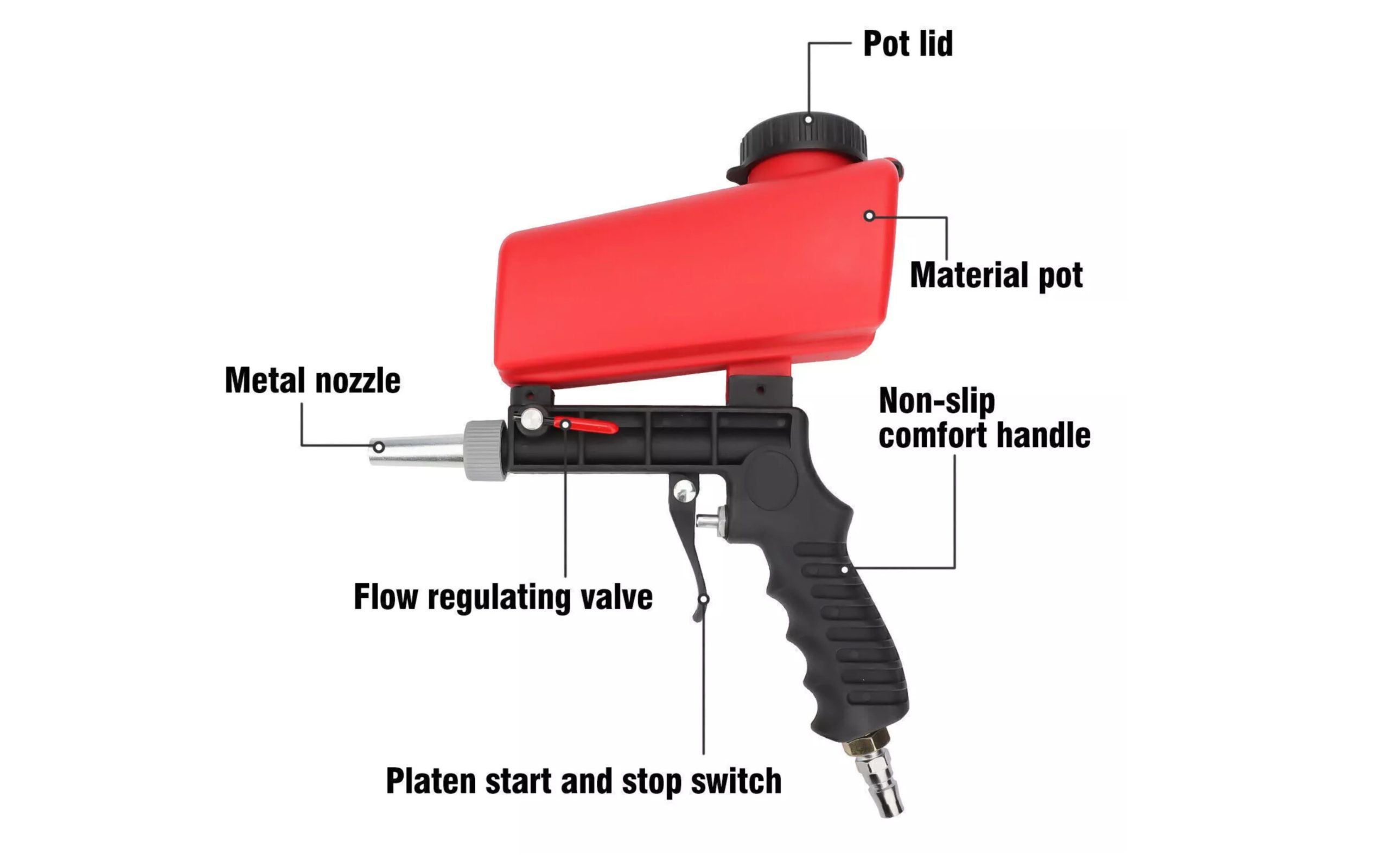
Handheld sandblasting machine
- Combination sandblasting machine
Combination sandblasting machine combines the advantages of fixed and handheld, suitable for projects of various sizes. This type of equipment is usually equipped with a variety of sandblasting modes and media, which can be flexibly applied in different surface preparation tasks. Its main features include:
- Versatility: Supports different sandblasting media and sandblasting methods, which can adapt to a variety of surface cleaning and treatment needs.
- Simple operation: Most combination sandblasting machines are designed for easy operation and are suitable for all types of users, including professionals and DIY enthusiasts.
- Wide range of applications: Whether it is a large construction site or a small home project, it can provide an effective sandblasting solution.
- Mobile sandblasting machine
Mobile sandblasting machines are designed for sandblasting in different workplaces, suitable for construction sites and exterior decoration. Its main advantages include:
- High mobility: It can be used flexibly in various construction environments and is suitable for external and internal sandblasting needs.
- Easy to adjust: The settings of the mobile sandblasting machine can be quickly adjusted according to the on-site conditions to improve work efficiency.
- Economical and practical: Compared with fixed equipment, mobile sandblasting machines have more cost advantages and are suitable for small projects with limited budgets.
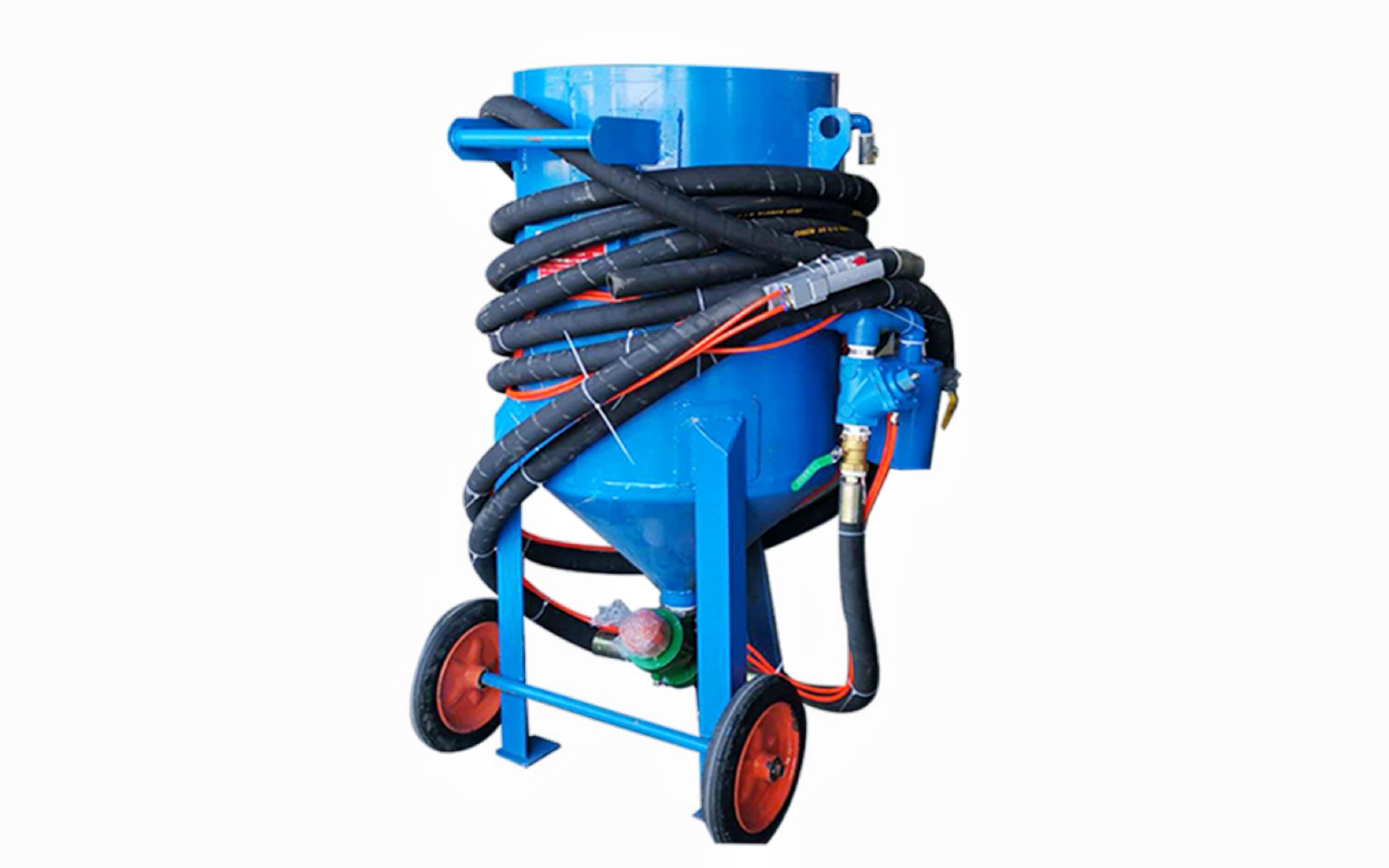
Mobile sandblasting machine
Optimization strategy of surface preparation for coating application
Effective surface preparation can significantly improve the adhesion and durability of coatings and sealants, thereby ensuring the quality of construction. Here are some key optimization strategies:
- Determine the appropriate preparation method
Depending on the type of substrate and the specific requirements of the coating, it is crucial to choose the appropriate preparation method. Here are some common preparation methods and their applicable situations:
- Sandblasting: Applicable to hard surfaces such as metal and concrete, it can effectively remove rust, dirt, and old coatings, enhance the roughness of the substrate, and improve adhesion.
- Chemical cleaning: For grease and chemical residues, chemical cleaning can quickly and effectively remove surface contamination, especially suitable for plastics and coating-sensitive materials.
- Mechanical grinding: Sanding with sandpaper or a grinder can increase the roughness of the substrate and increase the adhesion surface of the coating. It is suitable for wood and some metal materials.
- Control surface roughness
Surface roughness has a significant impact on the adhesion of the coating. Studies have shown that moderate roughness can provide a larger adhesion surface, which helps sealers and coatings form a stronger bond on the substrate. Surface roughness can be controlled by the following methods:
- Sandblasting adjustment: By adjusting the particle size of the sandblasting media and the sandblasting pressure, the surface roughness can be controlled to achieve the best adhesion effect.
- Manual polishing: Choose the right sandpaper and polishing technique to ensure that the surface reaches the ideal roughness and avoids excessive wear.
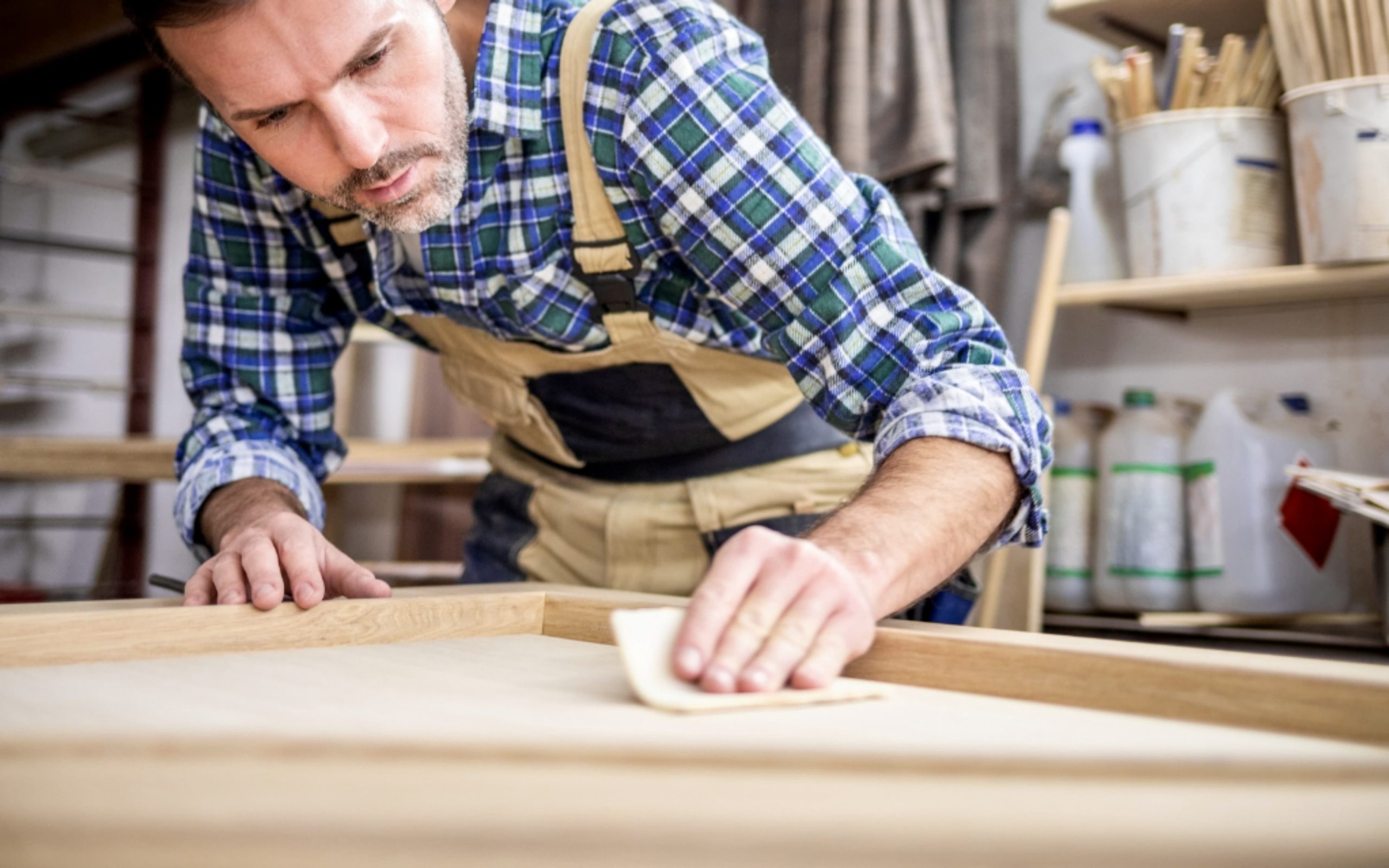
Sandpaper polishing
- Ensure appropriate humidity and temperature
The humidity and temperature of the construction environment have an important impact on the curing and adhesion of the coating. High humidity and extreme temperatures may cause the coating to deteriorate. The following measures should be taken to ensure a suitable construction environment:
- Environmental monitoring: Check the temperature and humidity before construction to ensure that they meet the recommended standards of the paint manufacturer.
- Adjust the construction time: Avoid construction in humid weather or when the temperature is too low. If necessary, use heating equipment to increase the ambient temperature.
- Surface contaminant removal methods
Surface contaminants are one of the main reasons that affect the adhesion of paint. Here are some effective contaminant removal methods:
- Pressure water washing: High-pressure water washing can effectively remove dust and oil on the surface and is suitable for cleaning large areas.
- Solvent cleaning: Using a suitable solvent to clean can quickly remove grease and other chemical residues, and is suitable for metal and plastic surfaces.
- Consider the nature of the substrate
Different substrates have different adhesion to paint. When pre-treating, the nature of the substrate should be fully considered to select the most appropriate treatment method. For example:
- Metal substrates: Usually require sandblasting or pickling to remove the oxide layer and surface impurities to improve coating adhesion.
- Wood substrates: Need to be sanded and cleaned to remove old coatings and impurities, and may require the use of special wood treatment agents.
Surface preparation is crucial in the application of coatings and sealants. Through effective cleaning and roughness control, the adhesion of the coating can be significantly improved, ensuring the durability and beauty of the coating. Whether you are a construction professional or a DIY enthusiast, understanding how to optimize the preparation process will help overcome common problems in coating applications.
Choosing the right cleaning method and equipment, such as a sandblaster, can effectively cope with the challenges of different substrates and levels of contamination. With the advancement of technology, the use of environmentally friendly and efficient preparation technology will become a future development trend, helping users better meet market demand and improve construction quality and efficiency.
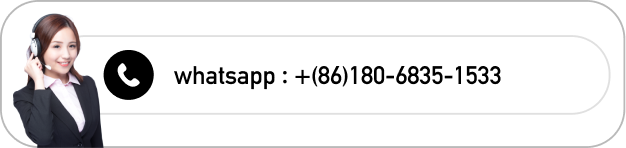