October 29, 2024
In modern manufacturing, deburring is a crucial link that directly affects the quality and performance of the product. With the continuous advancement of production technology, more and more companies have begun to pay attention to the selection of deburring machines. Choosing a suitable deburring machine can not only improve production efficiency but also reduce the scrap rate, thereby saving costs. However, there are many types of deburring machines on the market, and how to choose a machine that suits their needs has become a difficult problem faced by many companies. This article will conduct an in-depth analysis from multiple angles, including common deburring media, types, and characteristics of deburring machines, operation and maintenance, and common misunderstandings and challenges, to help you make a wise choice.
Common deburring media
Before choosing a deburring machine, you first need to understand the common deburring media. The type of deburring media directly affects the deburring effect, applicable machine type, and production efficiency.
- Cryogenic deflashing media
- Basic introduction: Usually a milky white cylinder or hexahedron, mainly made of polymer materials, can work at temperatures between -70°C and -196°C. By cooling the material, the burrs become brittle and can be easily removed in the subsequent deburring process.
- Application industries: Widely used in medical devices, aerospace, precision machinery, and other industries, especially suitable for parts with extremely high requirements for surface finish and dimensional accuracy.
- Nylon polyamide deflashing media
- Basic introduction: The colors are divided into red, green, yellow, etc., which can be customized, with bright colors and easy to distinguish. The shape is cylindrical or hexahedral. Nylon polyamide deflashing media has good wear resistance and elasticity, suitable for surface treatment of plastics and composite materials, and can effectively remove burrs from metal parts without causing damage to the workpiece.
- Application industries: Mainly used in electronics, automobiles, medical, and other industries, especially in precision parts cleaning and metal parts deburring.
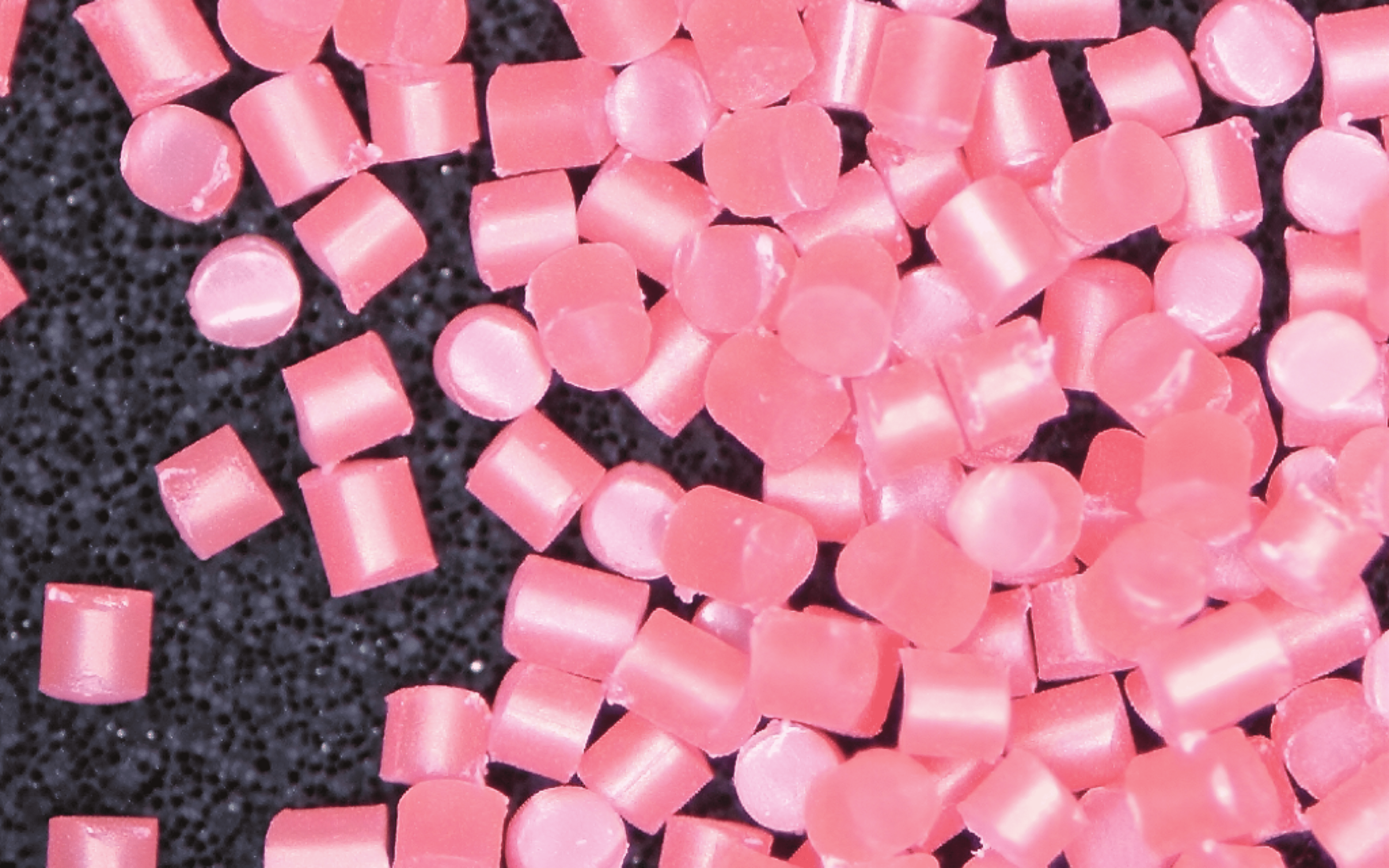
- Polystyrene deflashing beads
- Basic Introduction: Polystyrene beads usually have high hardness and strength. They are usually transparent white beads with uniform shape, easy to flow in the machine, and can effectively remove surface burrs. They are often used in deburring processes such as sandblasting and shot peening.
- Application Industry: Widely used in automobiles, aerospace, home appliances, and other fields, especially suitable for processing metal and plastic parts.

- Ceramic deburring media
- Basic Introduction: Ceramic Deburring Media is a high-hardness, high-wear-resistant material, usually white or beige, spherical or granular in shape. It is often used to process high-strength metal and alloy materials, and can effectively remove stubborn burrs and surface defects.
- Application Industry: Widely used in aerospace, automobile, medical equipment, and other industries, especially suitable for parts that withstand high stress and high temperature.
- Plastic media
- Basic Introduction: Plastic media are generally granular, usually presenting a rich variety of color combinations: white, light gray, pink and green, etc. The color can be used to distinguish different uses or particle size specifications. Plastic media has less impact on the workpiece surface and is suitable for processing workpieces with sensitive surfaces. It also has good acid and alkali resistance and is suitable for surface treatment in certain corrosive environments.
- Application industries: automotive manufacturing, consumer electronics, toy manufacturing, and other industries, especially suitable for parts that do not require high surface smoothness.
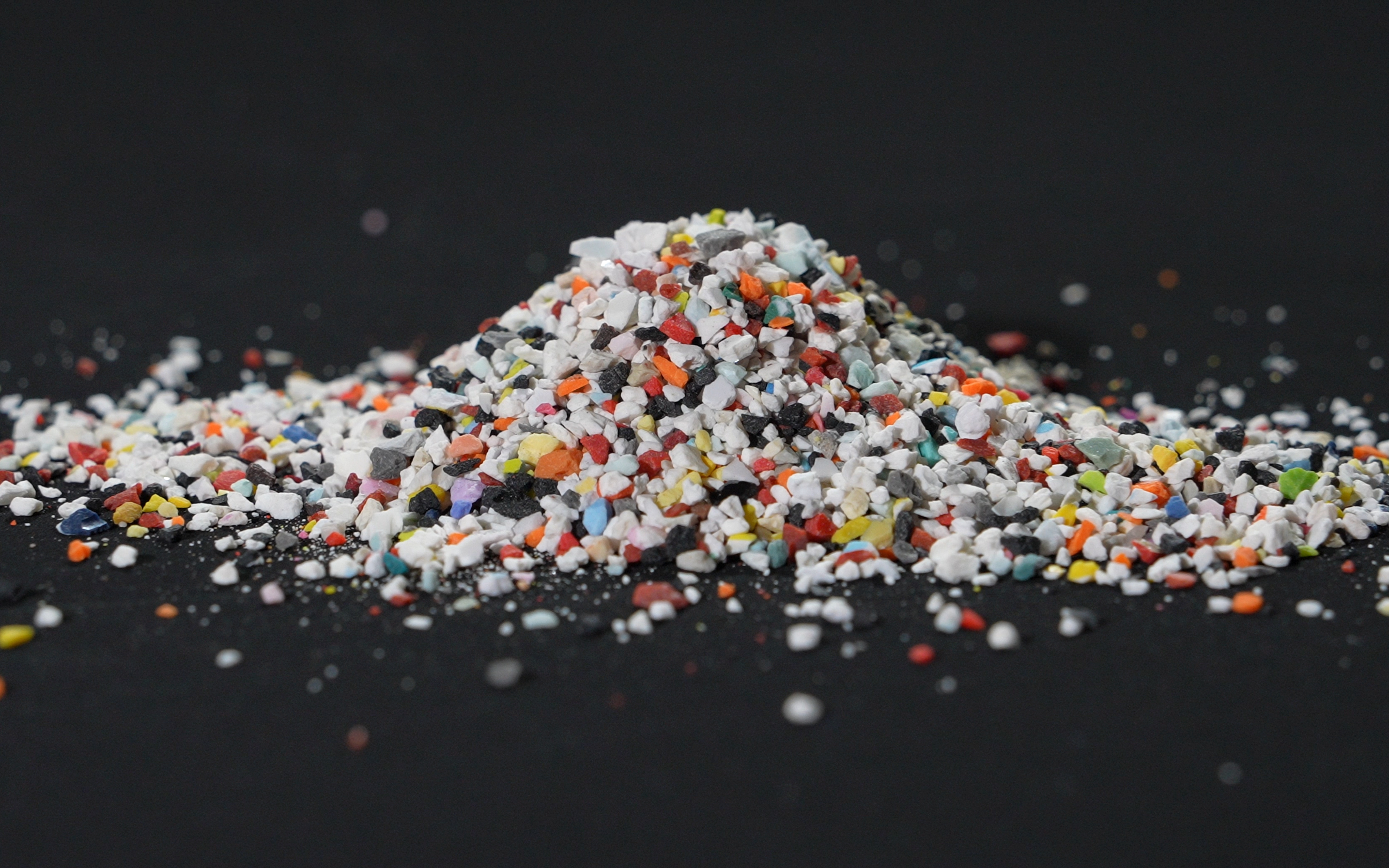
Types and characteristics of deburring machines
Choosing a suitable deburring machine is crucial to improving production efficiency and ensuring product quality. The following are several common types of deburring machines and their characteristics:
- Precision Sandblasting Machine
- Basic introduction: Precision sandblasting machine has the characteristics of high precision and high efficiency. It uses advanced spraying technology and high-pressure gas to spray the deburring medium onto the workpiece surface. It accurately controls the spraying pressure, medium flow rate, and nozzle angle to achieve uniform spraying on the workpiece surface, remove burrs without damaging the workpiece, and efficiently remove burrs and improve surface finish. The machine usually has a high-precision control system that can realize automatic operation and is suitable for occasions with extremely high requirements for surface treatment.
- Applicable media: Suitable for cryogenic deflashing media, nylon polyamide deflashing media, polystyrene deflashing beads, and other media.
- Applicable industries: Widely used in medical equipment, precision machinery, and aerospace industries.
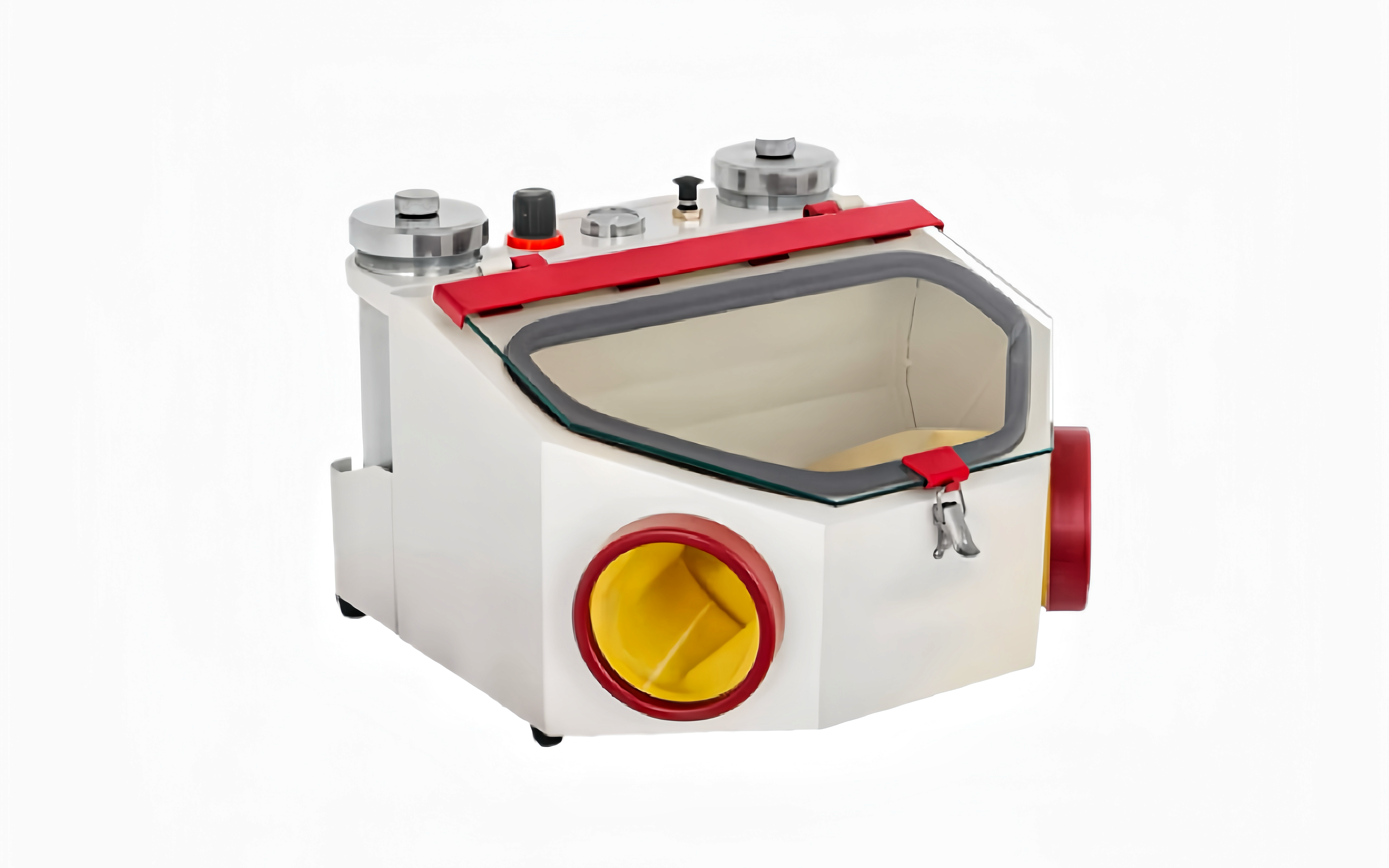
- Wheel Blaster
- Basic introduction: The wheel blasting machine is efficient and economical. It ejects the media onto the surface of the workpiece through a high-speed rotating wheel, which is suitable for processing large-area workpieces. The machine has high efficiency, simple structure, convenient operation, low maintenance cost, high economy, and is suitable for mass production. At the same time, it can also be adjusted according to different workpiece shapes and sizes to meet different production needs.
- Applicable media: Suitable for ceramic deburring media, polystyrene deflashing beads, and other media.
- Applicable industries: Commonly used in industries such as automobiles, shipbuilding, and construction, especially suitable for occasions where large-area deburring is required.
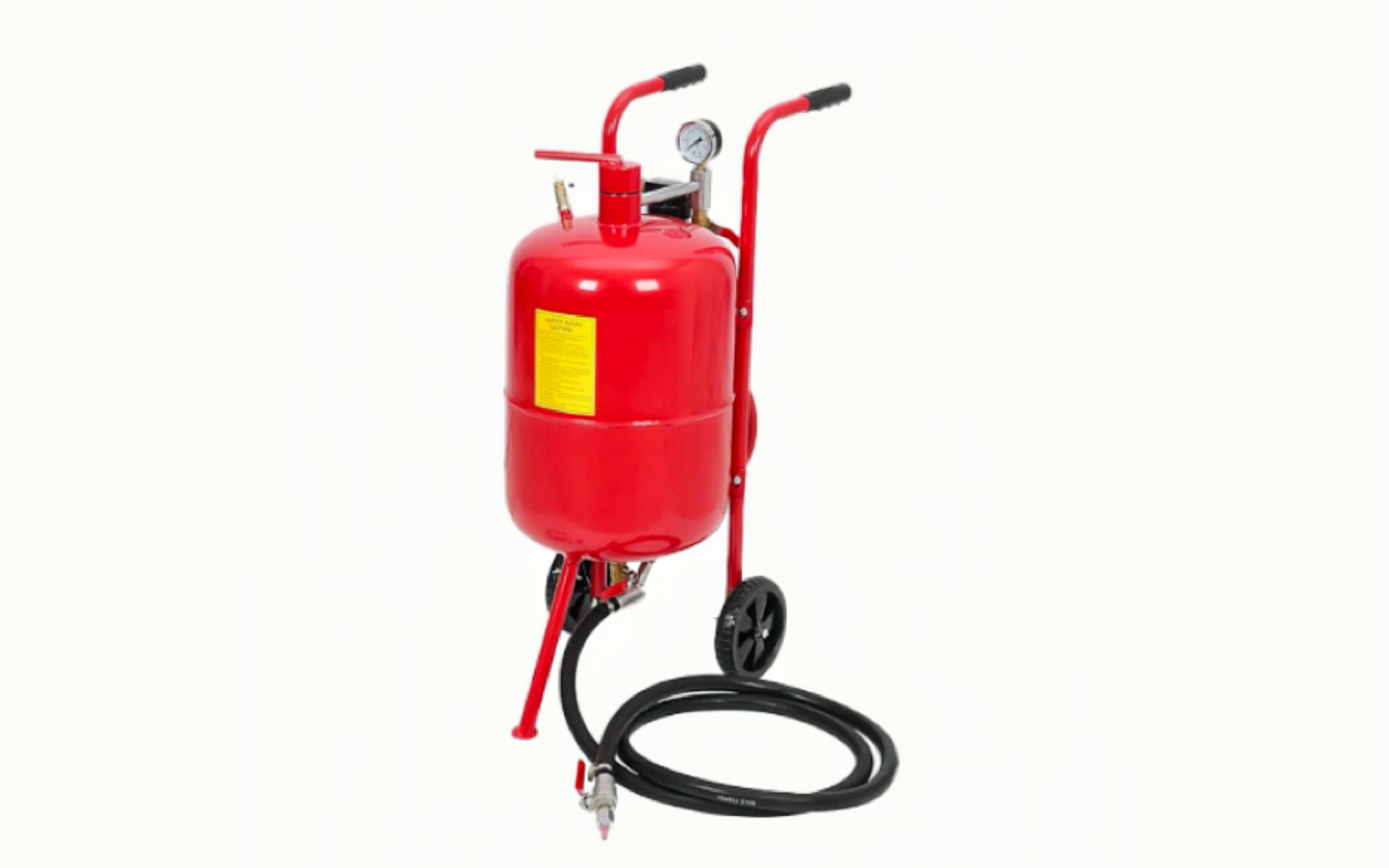
- Vibratory Deburring Machine
- Basic introduction: The vibratory deburring machine mixes the workpiece and the deburring medium through vibration, and uses the friction of the medium to remove burrs on the surface of the workpiece. This method is particularly suitable for processing small or complex-shaped workpieces, such as gears, springs, and other precision parts. Vibration deburring machines are usually set with different vibration frequencies and time settings to adapt to different materials and deburring requirements.
- Applicable media: Applicable to nylon polyamide deflashing media, plastic media, and other light-deburring media. By choosing the right media, it is possible to protect the surface of the workpiece while removing burrs.
- Applicable industries: Widely used in electronics, jewelry, mold manufacturing, and other industries. Especially in jewelry and precision machinery manufacturing, vibration-deburring machines are favored for their high efficiency and meticulous processing capabilities.
- Jet Blaster
- Basic introduction: Jet deburring machines use high-pressure air to spray deburring media onto the surface of the workpiece, which is suitable for quickly removing surface burrs and irregularly shaped materials. This machine is flexible in operation and suitable for workpieces of various sizes.
- Applicable media: Polystyrene deflashing beads, nylon polyamide deflashing media, etc. can be used. Choose the right media according to the material of the workpiece to achieve the best deburring effect.
- Applicable industries: commonly used in industries such as automobiles, aerospace, and precision instrument manufacturing, and are particularly suitable for processing parts with complex shapes.
Operation and maintenance of deburring machines
Operation matters
- Equipment settings: Before using the deburring machine, ensure that the correct equipment settings are made according to the material, size, and characteristics of the deburring medium, including pressure, spray angle, and time.
- Media selection: It is very important to choose the right deburring medium. Different media have different processing effects and speeds and should be selected according to the specific workpiece requirements.
- Workpiece preparation: Before operation, ensure that there are no impurities such as oil, dust, etc. on the surface of the workpiece to improve the deburring effect.
- Safety measures: When operating the deburring machine, the operator should wear appropriate protective equipment such as goggles, earplugs, and dust masks to ensure safety. At the same time, follow the operating procedures to ensure that the machine operates under normal working conditions.
- Monitoring and adjustment: During the deburring process, check the deburring effect regularly and adjust the machine settings as needed. For large-scale batch production, it is recommended to set up a dedicated person to monitor the deburring effect to ensure consistency.
- Environmental requirements: The deburring machine should be placed in a well-ventilated environment to prevent moisture and dust from affecting the performance of the machine. The area around the machine should be kept clean to prevent contamination of the medium and workpiece.
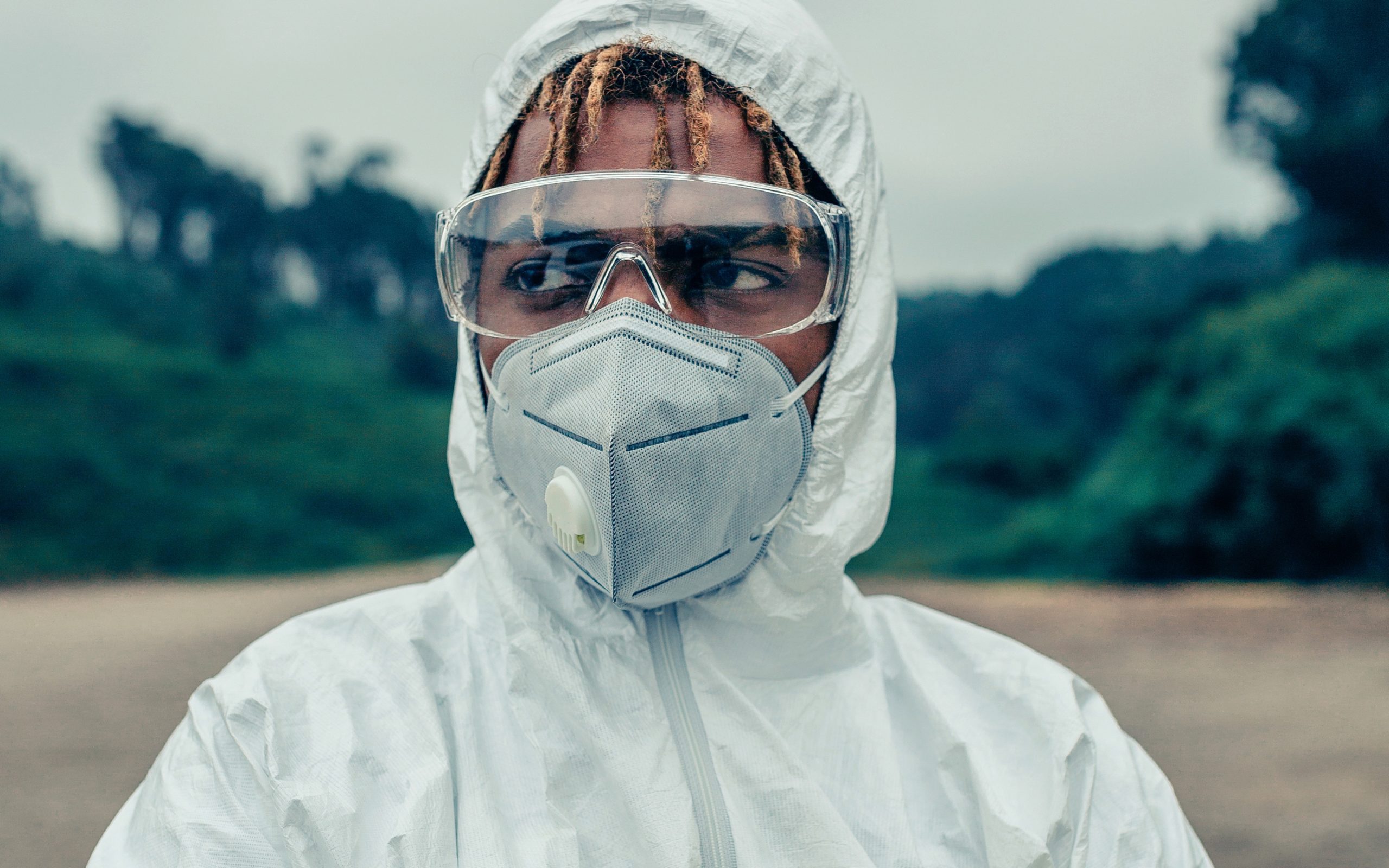
Protection Demonstration
Maintenance
- Clean the nozzle and filter regularly
Nozzles and filters are parts that are easily clogged in deburring machines, so they need to be cleaned regularly. Nozzle clogging will affect the injection pressure and medium flow, reducing the deburring effect; filter clogging will affect the recycling of the medium and increase costs.
When cleaning the nozzle and filter, you can use special cleaning tools and cleaning agents to remove the blockage. At the same time, you also need to check the wear of the nozzle and filter and replace them in time if they are worn.
- Check the injection effect
Regularly checking the injection effect is an important part of maintaining the deburring machine. You can judge whether the injection effect is good by observing the deburring effect of the workpiece and measuring the surface roughness of the workpiece.
If the injection effect is not good, you should adjust the injection pressure, medium flow nozzle angle, and other parameters in time to improve the deburring effect. At the same time, you also need to check the quality of the deburring medium and replace it in time if it is deteriorated or worn.
- Establish an equipment maintenance plan
To ensure the long-term and stable operation of the deburring machine, it is necessary to establish an equipment maintenance plan. The maintenance plan should include regular inspection, cleaning, lubrication, maintenance, etc., and clarify the maintenance time, responsible person, etc.
When executing the maintenance plan, it is necessary to strictly follow the plan to ensure that each maintenance work is implemented. At the same time, it is also necessary to record detailed information about each maintenance, such as maintenance time, maintenance content, replaced parts, etc., for subsequent inquiries and analysis.
- Record detailed information on each maintenance
It is very important to record the detailed information of each maintenance, which can help us understand the operation of the equipment, find problems in time, and deal with them. The record content should include maintenance time, maintenance content, replaced parts, equipment operation status, etc.
Through the analysis of maintenance records, the failure rules and maintenance experience of the equipment can be summarized, which can provide a reference for future maintenance work. At the same time, a more scientific and reasonable maintenance plan can be formulated based on the maintenance records to improve the maintenance efficiency and quality of the equipment.
Common misunderstandings and challenges
Misunderstanding 1: Thinking that all deburring machines can handle all materials
Many people tend to ignore the importance of different materials in the selection of machines and media when choosing deburring machines. Different deburring machines and media are targeted at different types of materials. For example, ceramic deburring media are suitable for high-hardness metals, while nylon polyamide media are suitable for plastics and composite materials. Therefore, when choosing, you must choose according to the material and characteristics of the workpiece to avoid unsatisfactory processing results or damage to the workpiece.
Misunderstanding 2: Only focus on deburring speed and ignore the effect
In the context of increasingly fierce market competition, companies tend to pursue deburring speed, however, deburring effect and quality are more critical. Excessive pursuit of speed may cause burrs on the surface of the workpiece to not be removed cleanly, and may even cause surface scratches, breakage, and other problems. Therefore, when choosing a deburring machine, it is necessary to balance speed and effect to ensure that both can reach the best state.
Misunderstanding 3: Ignoring subsequent maintenance and care
Many companies tend to ignore the maintenance and care of deburring machines after purchasing them. Regular maintenance and cleaning are essential for the long-term stable operation of the machine. Ignoring maintenance may cause machine failure, downtime, and even increase maintenance costs. Therefore, companies should establish a good maintenance system to ensure that the machine is always in good working condition.
Challenges
When choosing a deburring machine, customers may face a trade-off between price and performance. Many companies may choose low-priced machines with limited budgets, but these machines often cannot meet the needs of efficient deburring, thus affecting product quality. Therefore, it is a challenge to find a cost-effective solution. It is recommended that companies make multiple comparisons when choosing and considering long-term operating costs and maintenance expenses.
Choosing the right deburring machine is the key to ensuring product quality and production efficiency. By understanding the characteristics of different deburring media, the types of machines and their applicability, and the key points of operation and maintenance, you can make wise decisions and help companies stand out in a competitive market. I hope this article can provide you with a practical reference when choosing a deburring machine, helping your production process to be smoother and more efficient.
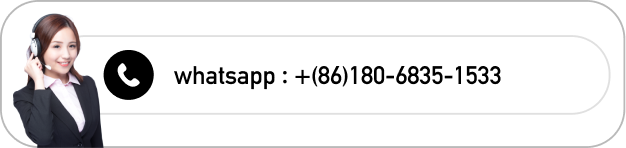