October 15, 2024
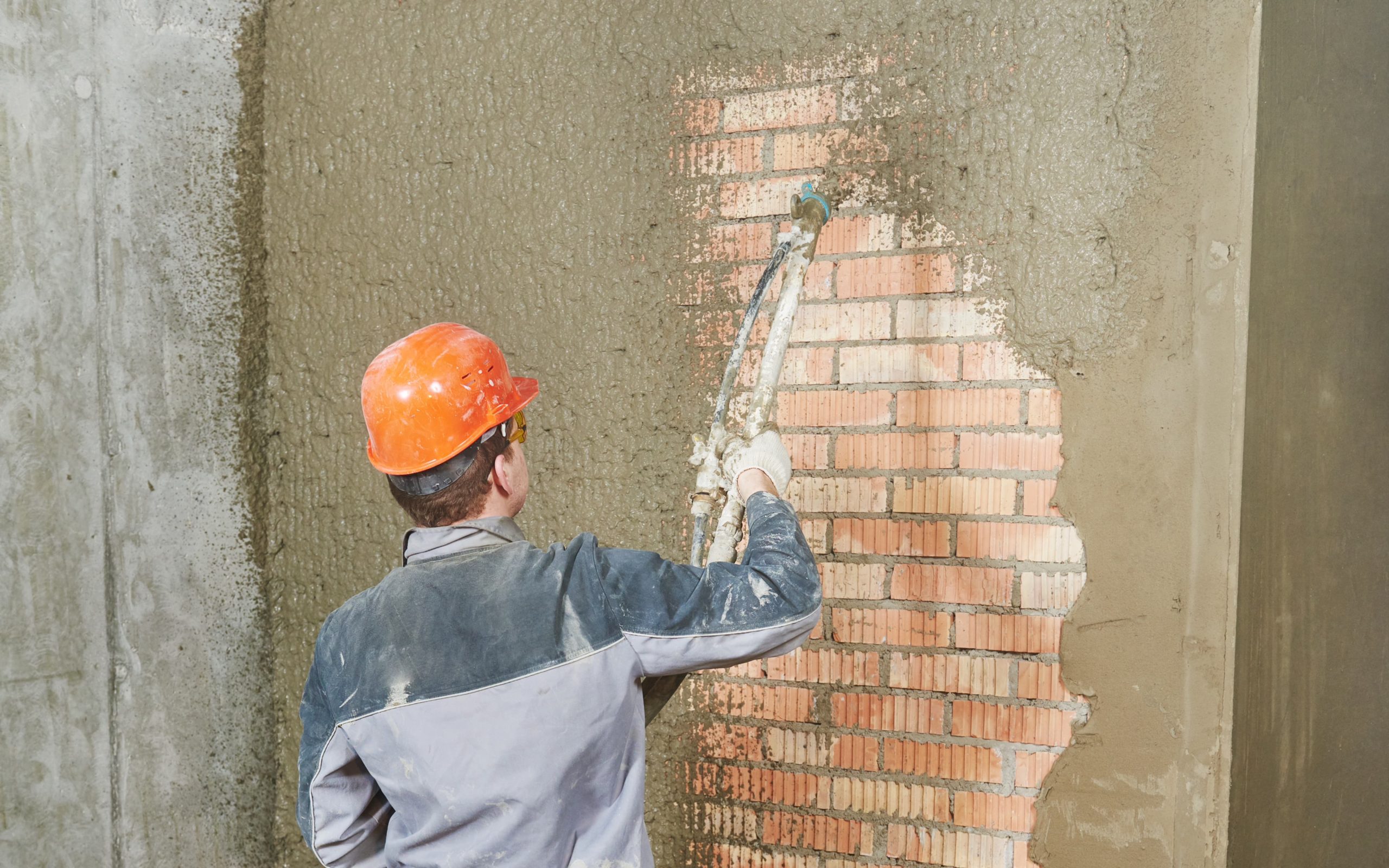
Etching is a process that uses physical or chemical methods to produce fine textures on the surface of materials. It is widely used in the surface treatment of hard materials such as glass, metal, and ceramics. Whether it is to enhance the adhesion of the coating or improve the functional properties of the material surface, the etching process plays a vital role in many industries. In modern industrial applications, mechanical etching is particularly common. Through means such as sandblasting, precise surface processing can be achieved to achieve a delicate texture effect.
In engineering manufacturing, coating adhesion is essential for the product’s long-term stability, durability, and performance. To ensure that the coating adheres firmly to the surface of the substrate and does not fall off or fail due to environmental changes or wear and tear, the etching process is used to enhance the adhesion between the surface and the coating. Therefore, this article will discuss “How Industrial Etching Enhances Coating Adhesion” and analyze its value in mechanical applications.
Basic Principles of Etching
Etching is the process of etching or corroding the surface of a material by chemical, physical, or mechanical means to achieve the purpose of changing the surface characteristics. This process can refine the surface structure and increase the surface roughness, thereby enhancing the adhesion between the coating and the material surface.
Chemical Etching vs Mechanical Etching
In industrial applications, etching is generally divided into two methods: chemical etching and mechanical etching.
- Chemical etching: This is the reaction of chemical reagents (such as acid or alkaline solutions) with materials to cause corrosion on the surface. Chemical etching is particularly suitable for the treatment of large-area materials and has good coverage of workpieces with complex shapes. For example, in the aerospace and semiconductor industries, chemical etching is widely used for surface treatment of metal materials and semiconductor wafers.
- Mechanical etching: It mainly relies on physical actions such as mechanical grinding or sandblasting to remove the surface layer. Sandblasting etching achieves a uniform surface modification effect by using high-hardness materials (such as aluminum oxide sand or ceramic grit blasting beads) to impact the surface at high speed. The advantage of mechanical etching is that it is harmless to the environment and the depth of surface treatment can be precisely controlled. Sandblasting mechanical etching is widely used for processing metal and glass surfaces.
Both etching methods have their advantages and disadvantages. Chemical etching is suitable for large-area and complex-shaped surfaces, while mechanical etching excels in applications that require highly precise control of surface texture and physical properties.
How Etching Processes Enhance Coating Adhesion
To understand how etching enhances coating adhesion, we first need to understand the relationship between surface energy and adhesion. The higher the surface energy between the coating and the substrate, the stronger the adhesion of the coating. Etching increases the contact area between the surface energy and the coating by changing the microstructure of the substrate surface, allowing the coating to adhere better to the substrate.
Principles of surface energy and adhesion
The surface of each material has a property called “surface energy”, which affects the wettability of liquids (such as paint) on the surface. High surface energy materials are more easily wetted by liquid coatings, while low surface energy materials do not easily form a strong coating.
Through etching, sandblasting materials (such as ceramic grit blasting beads or aluminum oxide) can remove contaminants and uneven layers on the surface of the material, revealing a clean and rough substrate surface. The rough surface forms a large number of tiny concave and convex structures, which greatly increases the contact area between the coating and the substrate. Due to the increase in contact area, the molecules of the coating can be more tightly bonded to the substrate surface, and the adhesion is significantly improved.
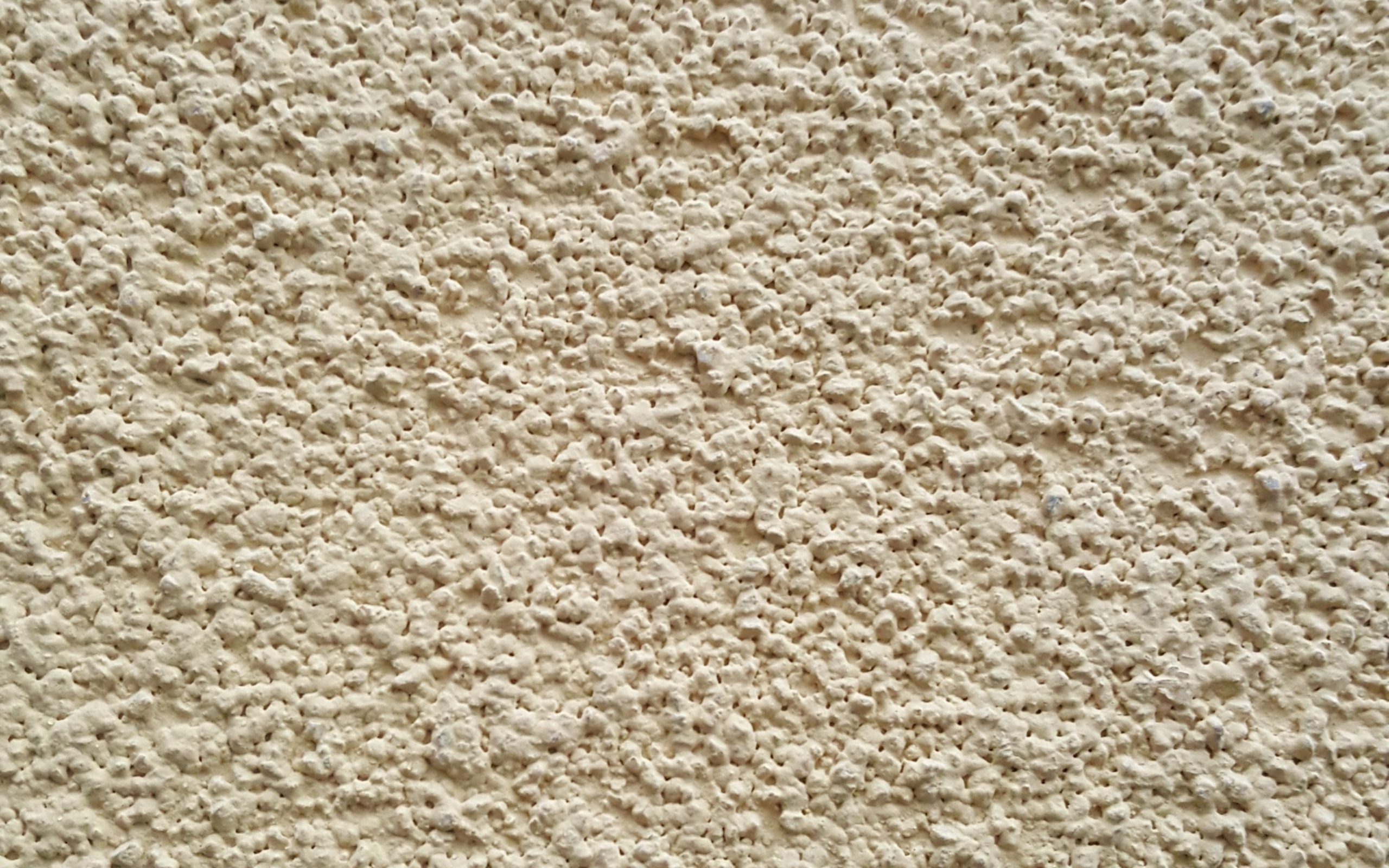
Surface roughness has a direct impact on the adhesion of the coating
Enhanced mechanical bonding
In addition to the increase in surface energy, etching further enhances the adhesion of the coating by creating microscopic mechanical locking points. After etching, the grooves and protrusions on the substrate surface provide more “gripping points” for the coating, allowing the coating to be more firmly fixed to the surface. This mechanical bond is particularly important for coating applications in high-stress environments, such as equipment surfaces under high temperature, high pressure, or heavy load conditions.
In practical applications, sandblasting etching not only provides better physical bonding for the coating but also reduces the peeling and cracking of the coating. Especially in industrial equipment that is used for a long time, the etched surface can effectively extend the service life of the coating and reduce maintenance and replacement costs.
Comparison with other surface treatment methods
Compared with surface treatment methods such as chemical etching or heat treatment, mechanical etching achieves surface modification through physical means. This method is not only more environmentally friendly but also avoids the pollution problems that may be introduced during chemical treatment. Mechanical etching can also more accurately control the etching depth and texture size, making it the preferred process in industries that require high precision.
For example, in the automotive manufacturing industry, the anti-corrosion coating of the car body requires a high degree of adhesion to cope with mud, salt, and other corrosive substances on the road. Through mechanical etching, the surface of the car body can not only obtain a uniform roughness but also ensure that the coating can resist external corrosion for a long time.
Applicable sandblasting materials and their effects
In actual operation, different types of sandblasting materials will have different effects on coating adhesion. For example, alumina sandblasting materials are often used in precision industrial etching processes because of their high hardness, uniform particle size, and strong controllability. Its high-density structure can bring stable and consistent surface treatment effects to metal or ceramic surfaces, greatly enhancing the adhesion of the coating.
For workpieces that require higher surface strength and durability in extreme environments (such as key parts in the aerospace and oil and gas industries), surface etching using alumina sandblasting can effectively improve the protective ability of the coating.
Industrial etching applications
In industrial manufacturing, etching is not only a process to enhance aesthetics, but also an important step to lay the foundation for subsequent processes. We have learned from the above principles that the most important thing for the coating to be tightly bonded is the surface roughness and changes in surface roughness directly affect the adhesion of the coating. The controllable surface texture formed by etching can effectively enhance the adhesion of the coating, improve the durability of the product, and ensure that it still has excellent performance in extreme environments. The following industries and workpieces are important application areas of etching technology:
Metal Manufacturing
In the field of metal processing, mechanical etching technology (such as sandblasting) is widely used for surface treatment before painting. When producing metal parts, the adhesion and uniformity of the coating are crucial. Etching can remove the oxide layer, oil, and other contaminants on the metal surface while increasing the surface roughness to make the coating adhere more firmly.
Aerospace equipment, such as wing components, engine turbine blades, jet engine casings, etc., need to withstand high temperatures, strong winds, and harsh external environments, so the adhesion of the coating is particularly important. Others, such as aircraft shells, wings, and engine parts are often exposed to humidity, temperature changes, and ultraviolet rays. Through etching, aerospace parts can obtain precise surface textures, effectively improve the adhesion of protective coatings, and ensure that the coating does not peel or crack under extreme conditions. In addition, many parts of spacecraft must also withstand tremendous pressure. The etched surface can not only provide stronger mechanical bonding but also enhance corrosion resistance, ensuring flight safety and the long life of the equipment.
Automobile Manufacturing
In automobile manufacturing, especially on the chassis, doors, and exterior surfaces of the vehicle body, the quality of the anti-corrosion coating directly affects the service life of the vehicle. Vehicles are prone to rust when exposed to air, moisture, salt, and other environments for a long time. Through etching technology, the surface of automobile parts can produce uniform roughness, thereby enhancing the adhesion of the anti-corrosion coating and preventing the formation of rust spots.
Alumina sandblasting materials are widely used in this field. They can quickly and efficiently process large areas of the vehicle body surface to ensure that the coating has optimal adhesion. In addition, etching can also reduce the unevenness of the coating and improve the overall quality of the coating, thereby improving the durability of the vehicle.
Glass products
As a brittle material, the etching process can give glass unique optical effects and surface characteristics by controlling the depth and surface texture. In industrial design, mechanical etching can not only improve the aesthetics of glass but also enhance its scratch resistance and crack resistance. This process is also often used in the processing of high-end architectural glass, display screens, and electronic equipment housings.
For example, the display screens, electronic housings, protective glass, architectural decorative glass, etc. of modern smartphones can be treated with sandblasting etching technology to not only prevent fingerprint residue but also enhance the adhesion of the coating and prevent glass scratches or cracks.
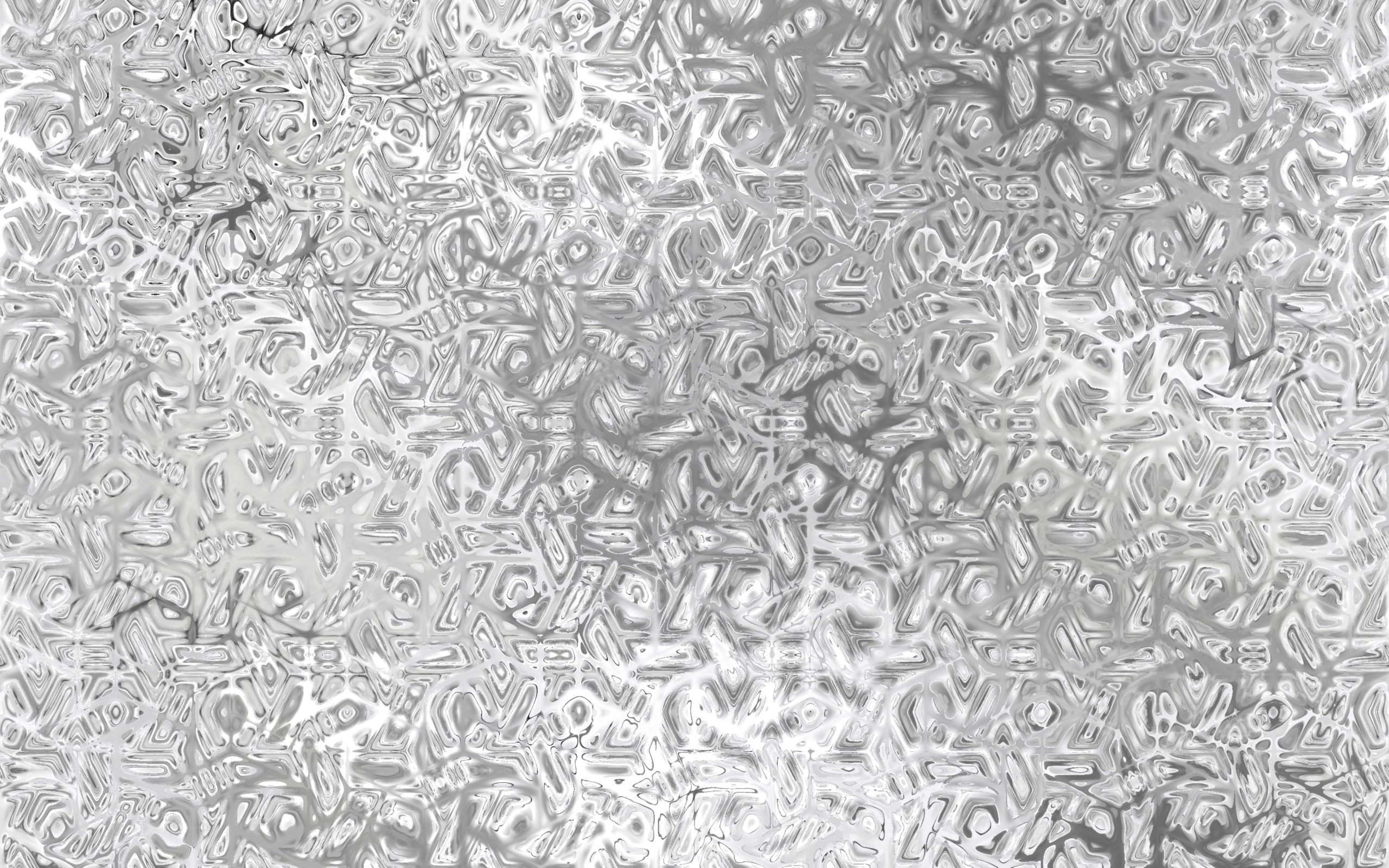
The patterns on decorative glass
Oil and Gas
Equipment in the oil and gas industry, such as drill bits, pipe joints, valves, and other high-pressure components, often work in extremely high temperature and high-pressure environments, and the equipment components need to have high wear resistance and corrosion resistance. The etching process can enhance the adhesion of the coating by forming a micro-texture on the surface, ensuring that the coating on the surface of the equipment will not fall off or fail under these harsh conditions.
In oil drilling and natural gas transmission equipment, components such as drill bits and valves are particularly prone to wear and corrosion due to frequent contact with sand, gravel, corrosive gases, and liquids. Through etching, the surface of the equipment can not only improve wear resistance but also reduce the failure rate of the equipment.
Electronics Industry
The electronics industry has extremely high requirements for the accuracy of surface treatment, especially for micro components such as integrated circuits and chips, whose surfaces must be etched with high precision. Mechanical etching can control the depth and uniformity of the surface texture when processing these precision devices, ensuring that the components are not affected by the external environment during use, and ensuring their long-term reliability and stability.
At the same time, metal shells in the electronics industry (such as laptop shells and tablet back shells) are also widely used in etching processes for surface beautification and strengthening.
Sandblasting media for optimal etching effects
When performing etching processes, it is crucial to choose the right sandblasting media. Different material properties, particle sizes, and shapes have a direct impact on the etching effect. The following are several common sandblasting media and their applicable scenarios.
- Alumina sandblasting
Alumina is a commonly used sandblasting media with high hardness and grinding ability, suitable for etching on a variety of materials such as metals, glass, and ceramics. It is worth noting that when choosing aluminum oxide as a sandblasting medium, the choice of particle size should be considered. Smaller particle sizes such as ultrafine aluminum oxide blast media are suitable for detailed etching, while larger particle sizes are more suitable for large-area processing.
Its advantages include:
- Powerful removal ability: The hardness of aluminum oxide enables it to effectively remove surface rust and old paint layers.
- Adaptability: Suitable for a variety of industries, including automotive manufacturing, aerospace, electronics, etc.
- Controllable surface texture: Aluminum oxide can precisely control the etching depth to ensure the best bonding between the coating and the substrate.
- Ceramic grit blasting beads
Ceramic grit blasting beads are also highly efficient sandblasting media, especially suitable for surface treatments that require a higher finish and are very suitable for surface treatments that require a high gloss, such as the housings of medical devices and high-end consumer electronics. Its advantages include:
- Lower wear rate: Compared with aluminum oxide, ceramic grit blasting beads have less wear on the substrate during treatment and are suitable for surface treatment of precision parts.
- Environmental protection: Ceramic grit blasting beads are pollution-free and suitable for industries with high environmental requirements.
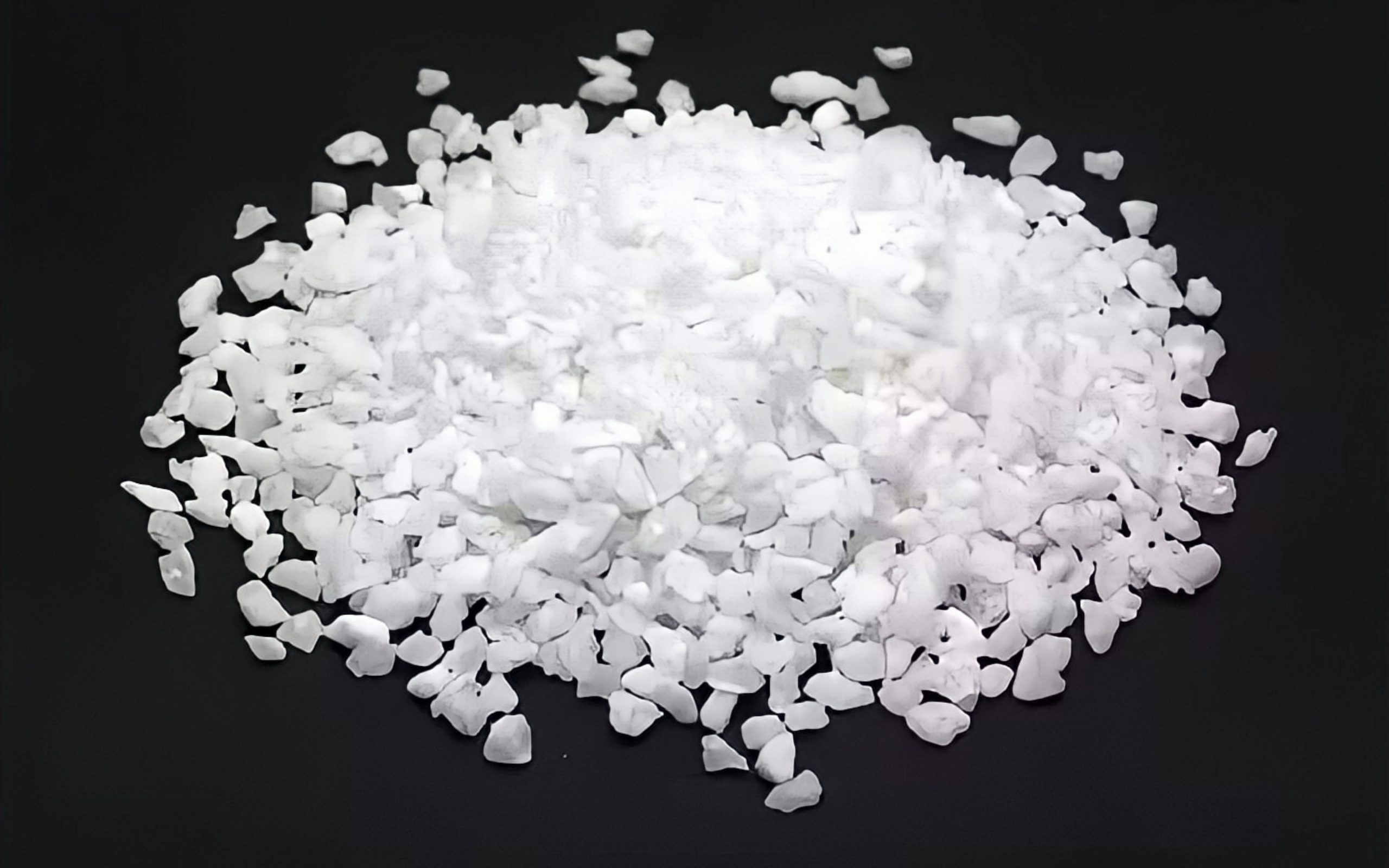
Ceramic Grit Blasting Beads
- Silica sand media
Silica sand is the most traditional sandblasting medium, mainly used for surface cleaning and grinding, suitable for industries such as construction and shipbuilding, but it needs to be carefully selected when processing high-precision parts.
Its characteristics include:
- Economical: Compared with other sandblasting media, silica sand has a lower cost and is suitable for large-scale industrial applications.
- Effective decontamination: Suitable for removing thicker rust and paint layers, but may cause a certain degree of roughness to the surface.
- Pad blasting media
Pad blasting media is a new type of media that has become increasingly popular in recent years, mainly used for surface treatment that requires low wear. This media is very suitable for industries that require extremely high surface finish, such as optical devices and high-end consumer products.
Its advantages include:
- Flexible treatment: Gentle cleaning of the surface to reduce substrate damage.
- Versatility: Suitable for a variety of materials, including glass and plastic.
- Other special blasting media
In addition to the common media mentioned above, there are some special blasting media, such as plastic particles, corundum, etc., each of which has a specific application scenario. The selection should be analyzed according to the specific etching requirements and material properties.
When selecting blasting media, in addition to considering material properties, the following factors should also be considered:
- Workpiece material: Different materials have a great influence on the selection of blasting media. Materials such as metal, glass, and ceramics require different media.
- Surface requirements: Select the appropriate media particle size and type based on the requirements for surface roughness and finish.
- Processing scale: Large-scale industrial applications may require more economical media, while high-precision work requires more specialized materials.
By comparing and selecting different sandblasting media, the best etching effect can be achieved, thereby improving the adhesion of the coating and ensuring the safety and efficiency of industrial applications.
Industrial etching is of great importance in improving the adhesion of coatings. By selecting the appropriate sandblasting media and technology, more precise etching effects can be achieved. This has not only been used in many industries such as aerospace, automotive manufacturing, and oil and gas but also provides strong technical support for modern industry. With industrial development and technological progress, etching processes will continue to evolve to meet higher performance requirements and more complex application scenarios. Mastering the scientific principles and practical applications of etching will give companies more advantages in the fierce market competition.
I hope this article can provide readers with a deep understanding of etching and its application in coating adhesion, and inspire deeper exploration of this field.
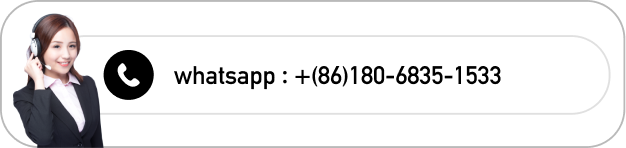