How do zirconia beads separate the core materials of lithium batteries?
December 24, 2024

Lithium batteries are a key component of modern science and technology. But how can the performance consistency and high purity of electrode materials be ensured in the manufacture of lithium batteries?
Battery performance often depends on the particle size and dispersion uniformity of active materials, and these parameters directly affect the energy density, cycle life, and safety of batteries. However, in traditional grinding and dispersion processes, materials are easily limited in performance due to contamination or uneven particle distribution, affecting end-product reliability.
So, is there a more efficient and reliable solution to break this bottleneck?
The emergence of yttria-stabilized zirconia beads (zirconia ceramic balls) has opened new possibilities for preparing lithium battery materials. This article will analyze how this advanced grinding media can provide solutions to the industry’s core pain points.
Table of contents
Background of the application of zirconia beads in lithium batteries
The production process of electrode materials for lithium batteries, especially positive electrode materials (such as lithium cobalt oxide, ternary materials, etc.) and negative electrode materials (such as graphite, silicon-based materials, etc.), requires extremely high particle uniformity and purity. The inhomogeneity of particles affects the energy density and cycle life of the battery, while the presence of impurities may lead to a decrease in battery performance.

In the production of lithium battery electrode materials, the raw materials are initially ground and dispersed, the particle size is refined, the particles are evenly distributed, and the performance of the materials is finally enhanced.
In the grinding and dispersion process of the materials, zirconium oxide beads play a critical role with their excellent high wear resistance, good chemical stability, and excellent particle size distribution control ability. With the use of zirconia ceramic balls, the material particles can achieve a more uniform distribution state, which is conducive to improving the purity of battery materials, reducing the impurity content, and effectively ensuring the stability of battery performance during long-term use.
Working principle of zirconia beads
Zirconium oxide beads play an extremely important role as a “grindstone” in the preparation of lithium battery electrode materials. Their working principle can be divided into three key processes: grinding, dispersion, and anti-pollution.
Grinding: A “micro hammer” that breaks materials
In the grinding equipment, zirconia beads rotate at high speed and “break” electrode material particles, such as lithium nickel cobalt manganese oxide or graphite, through kinetic impact and friction. Just like using a hammer to break up hard rocks, zirconia ceramic balls use their high density and hardness to grind these materials from original large particles into smaller micron or even nanometer levels. This refinement process ensures that lithium battery materials have a larger surface area when in use, thereby improving their electrochemical performance, such as battery capacity and cycle life.
Dispersion: Preventing particles from “clumping”
Particles tend to adsorb or agglomerate with each other during grinding, just like wet sand sticking together, and this “clumping” causes uneven material distribution. The smooth spherical design and uniform energy distribution of zirconia beads prevent particles from sticking and fully disperse them. The benefit of this uniform distribution is that the active materials of lithium battery electrodes can achieve more stable current output, thereby improving the overall performance of the battery.
Low-pollution performance: Guardian of pure materials
In the manufacture of lithium batteries, any impurities will seriously affect the safety and stability of the battery. Zirconia ceramic balls are made of high-purity zirconium oxide and yttrium, which are wear-resistant and chemically stable. During high-energy grinding, they will not drop metal ions or wear debris like other materials, so they will not contaminate electrode materials. This “cleanliness” characteristic helps lithium batteries achieve high purity requirements, especially in high-end applications such as new energy vehicles.
In summary, zirconia beads can not only crush particles, and maintain uniform distribution, but also avoid material contamination. They are indispensable grinding media in the preparation of lithium battery electrode materials.
The role of zirconia beads in improving the performance of lithium batteries
Increasing energy density
Through the efficient grinding of zirconium oxide beads, the electrode material particles of lithium batteries become smaller and more uniform. This micron or even nano-level refinement greatly increases the specific surface area of the particles and increases the contact range between the active material and the electrolyte, thereby increasing the energy density of the battery. This means that at the same volume, the battery can store more electrical energy to meet the needs of applications such as high-endurance equipment and new energy vehicles.
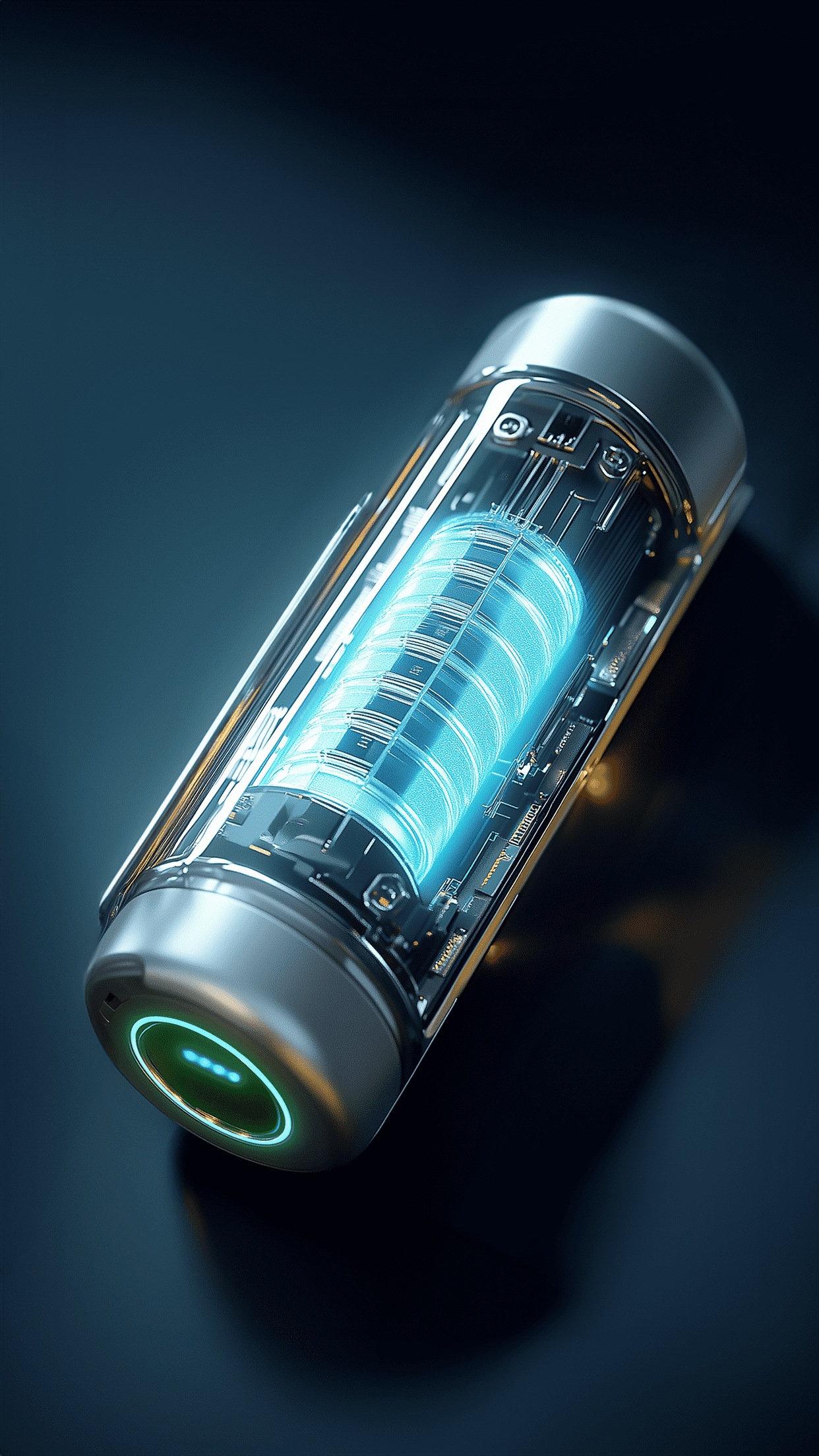
Enhanced cycle stability
Batteries often experience capacity decay during long-term charging and discharging, resulting in performance degradation. During the grinding process, zirconia ceramic balls ensure the high purity and uniform distribution of electrode materials and reduce the occurrence of particle agglomeration and microcracks. This not only improves the stability of the internal structure of the battery but also effectively reduces the probability of side reactions, thereby extending the service life of the battery.
Optimizing conductivity and ion migration
The dispersion effect of zirconia beads ensures that the electrode active materials can be evenly distributed on the electrode sheet, reducing the appearance of “dead zones”. This uniformity improves the conductivity of the electrode and optimizes the migration path of lithium ions during the charge and discharge process, thereby improving the overall output power and charging efficiency of the battery.
Through these effects, zirconia beads not only perform well in improving the performance of lithium batteries but also provide more reliable process support for the next generation of battery technology.
Case application
Grinding and dispersion of NCM ternary materials
A lithium battery manufacturer uses zirconium oxide beads to wet grind the ternary positive electrode material NCM. In the experiment, zirconia beads impact and refine the NCM material multiple times through high-energy stirring equipment, reducing its particle size from 3.5μm to 0.8μm. The particle size uniformity of the material is significantly improved (D50 particle size fluctuation is reduced by 30%) [1], while the impurity content is kept below 0.01%. This refinement effect improves the discharge capacity and rate performance of NCM, especially in high-rate tests, where its energy density is increased by about 15% [2].
Wet processing of graphite anode materials
In the processing of graphite anode materials, zirconia beads help disperse graphite particles and optimize the uniformity of the slurry. Experiments show that the viscosity of the graphite slurry after YSZ bead grinding is stable, and the particle distribution is concentrated in the range of 1-2μm, which is 20% higher than the dispersion efficiency of traditional ceramic beads [3]. The final electrode sheet exhibits superior conductivity and long-cycle stability, and the capacity retention rate of the single cell is increased to 94.8% (after 1000 charge and discharge cycles) [4].
Enhanced performance of lithium iron phosphate electrodes
The use of zirconia beads to wet grind and disperse LiFePO₄ (lithium iron phosphate) significantly improves the capacity retention rate and rate performance. After grinding, the particle size was reduced from 1.5 μm to 0.7 μm, and the material showed a 20% performance improvement in high-rate charge/discharge tests [5]. Compared with the untreated material, the capacity retention rate after 200 cycles increased by 10%.
According to actual cases, zirconium oxide beads can significantly improve particle performance and meet high purity requirements in the preparation of positive and negative electrode materials for lithium batteries, making them an ideal choice for grinding and dispersing high-performance lithium battery materials.
FAQs
What is the ideal size of zirconia beads for grinding lithium battery materials?
The ideal size of zirconium oxide beads depends on the type of material being processed.
Smaller beads are more conducive to achieving finer particle size and better dispersion. Generally, 0.3-0.4mm is used for grinding microbeads for new energy lithium batteries. The finer the better, preferably nanometer level. You can choose HLH’s YZ300 (0.25-0.3mm), YZ200 (0.2-0.25mm), and YZ150 (0.15-0.2mm).
For coarse materials or preliminary grinding, larger beads (e.g. 1.0–1.5mm) may be more appropriate.
(HLH offers custom sizes, click here for product details.)
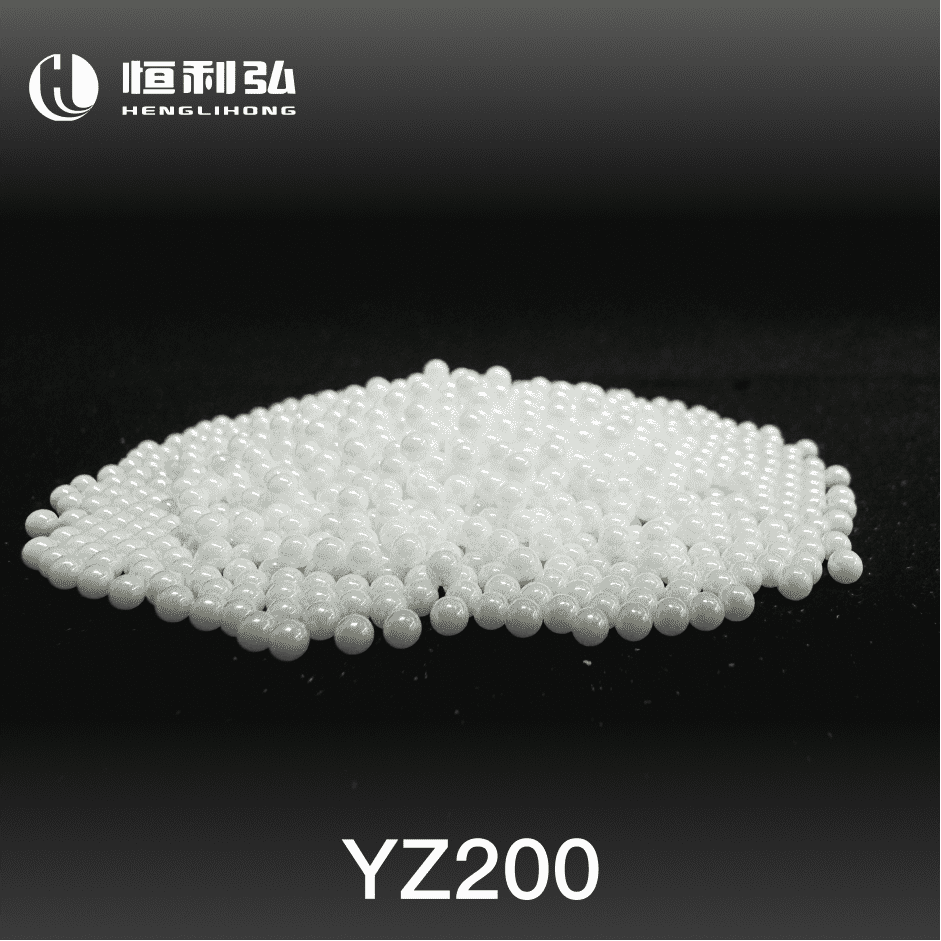
What machines are recommended for lithium battery material production?
High-energy bead mills (such as horizontal and vertical bead mills) are often used for grinding with zirconium oxide beads. These machines provide the necessary shear force to effectively break down materials such as NCM and graphite.
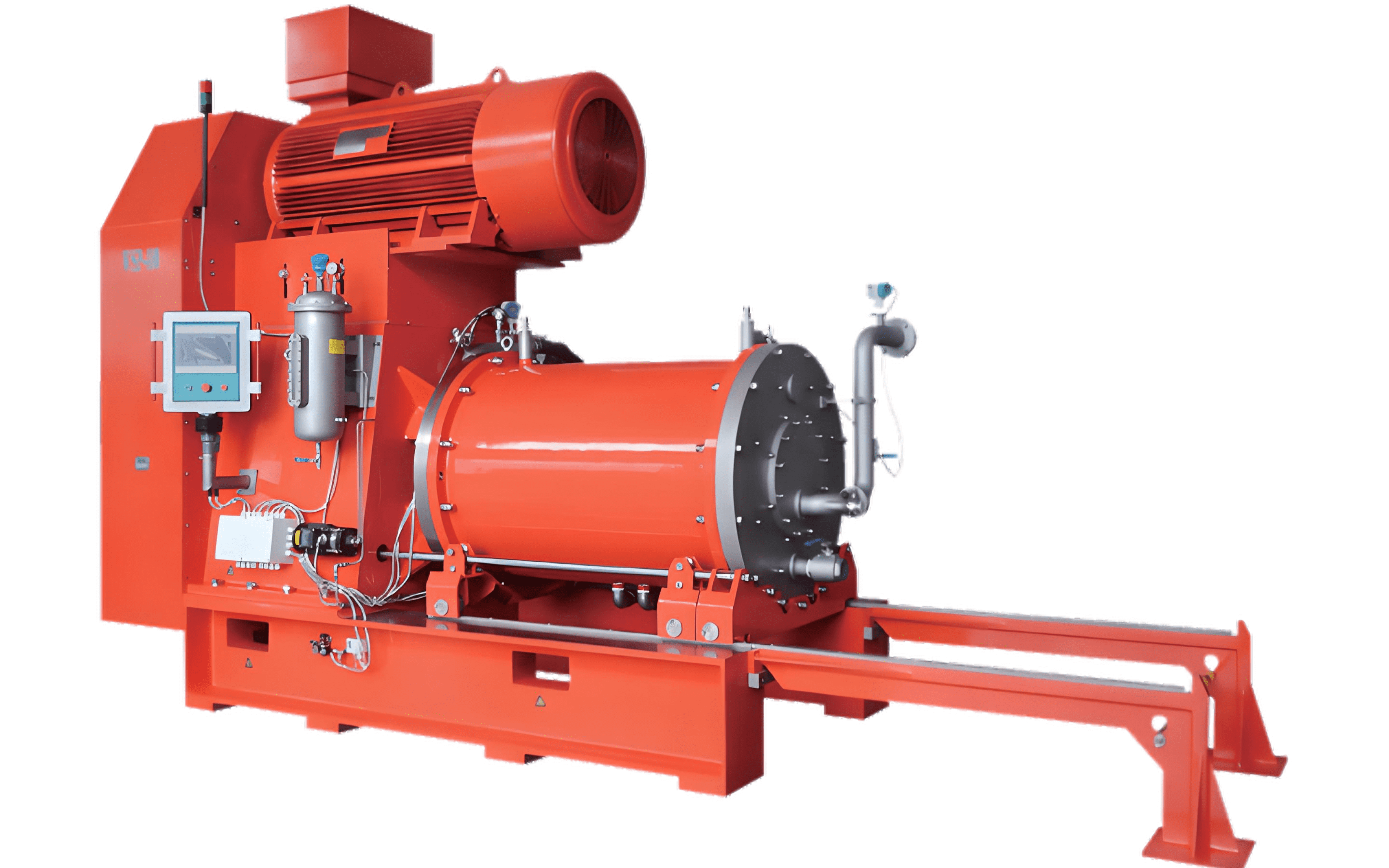
How long does the zirconia ceramic balls last during grinding?
Zirconia ceramic balls have a long service life due to their high durability and wear resistance. However, their lifespan depends on factors such as the hardness of the grinding material and the grinding speed. On average, zirconia beads last 500 to 1000 hours before they need to be replaced.
Can zirconium oxide beads be used for positive and negative electrode materials in lithium batteries?
Yes, zirconia beads are suitable for grinding cathode (e.g. NCM) and anode (e.g. graphite) materials because they maintain purity and prevent contamination during the grinding process.
What are the benefits of using zirconia beads compared to other grinding media such as glass beads?
Compared to other grinding media, zirconium oxide beads have excellent durability, chemical stability, and greater wear resistance. Their high hardness ensures longer service life and less contamination during grinding, making them ideal for high-precision applications in lithium battery production.
How to ensure consistent performance when using zirconium oxide beads in large-scale production?
To maintain consistent performance, factors such as bead size, grinding speed, and material loading need to be monitored and controlled. Regularly checking the wear of the beads also helps to maintain optimal performance throughout the production process.
Summary and prospects
Zirconium oxide beads significantly improve the performance of battery materials, including energy density, cycle stability, and conductivity, through efficient grinding and dispersion effects. With its low contamination and durability, it has become an ideal choice for high efficiency and environmental protection.
Looking ahead, with the continuous development of new battery technologies, zirconia beads have great potential for application in emerging fields such as solid-state batteries and sodium-ion batteries and may provide more stable and efficient solutions for the next generation of battery technology.
References
[1] Advanced Powder Technology, 2022, DOI: 10.1016/j.apt.2022.04.016.
[2] Journal of Power Sources, 2021, DOI: 10.1016/j.jpowsour.2021.230912.
[3] Electrochimica Acta, 2022, DOI: 10.1016/j.electacta.2022.139582.
[4] Energy Storage Materials, 2021, DOI: 10.1016/j.ensm.2021.04.015.
[5] Journal of Energy Chemistry, 2021, DOI: 10.1016/j.jechem.2021.02.027.
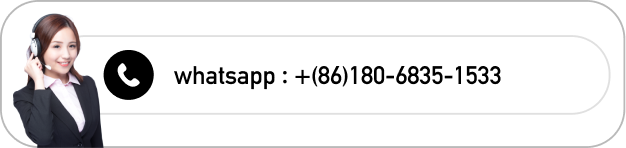