How electronic components adapt to harsh environments?
January 3, 2025
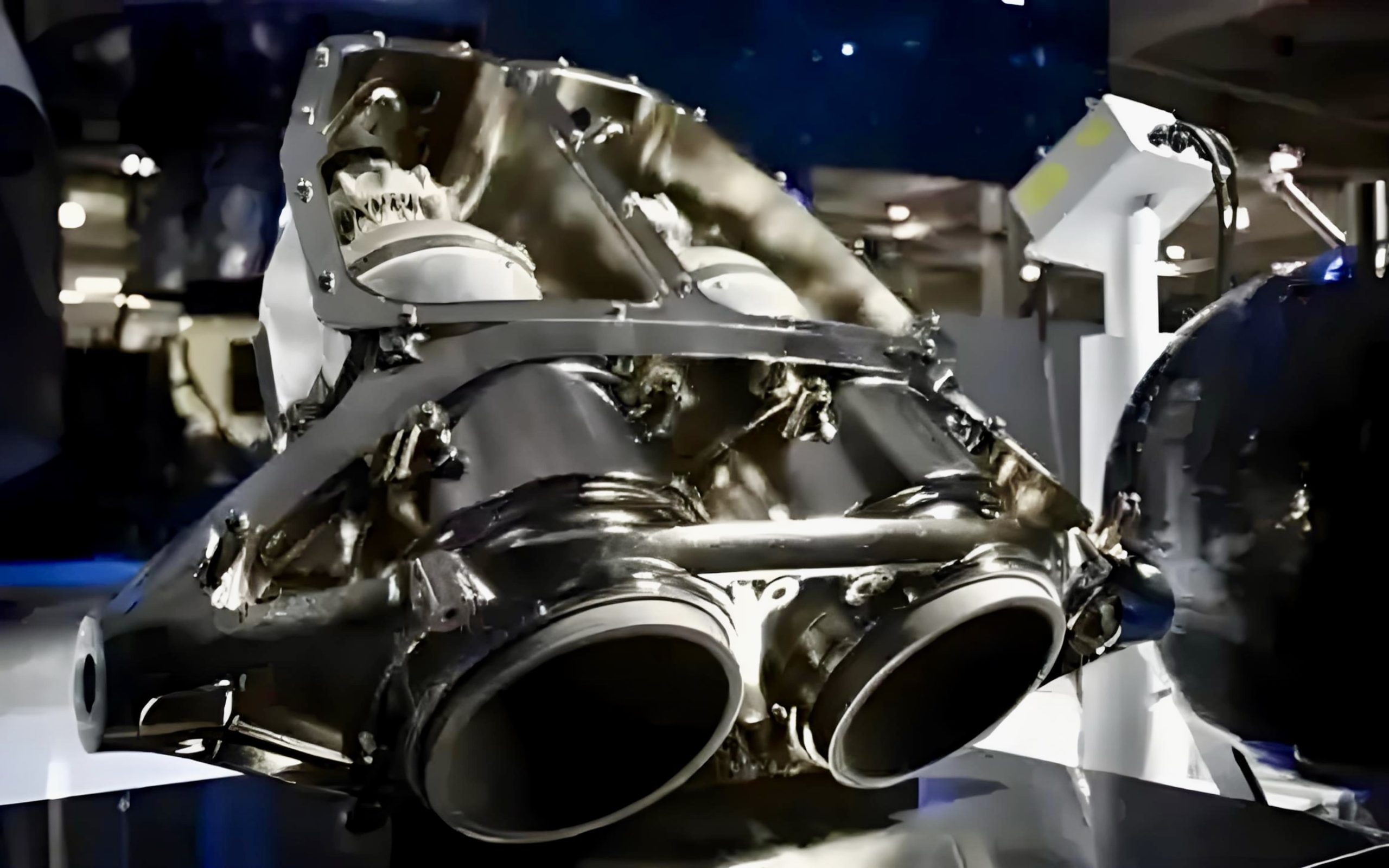
In aerospace, precision electronic components are not only the core control components of spacecraft and aircraft but also shoulder key tasks such as communication, navigation, and power management. For example, satellite orbit operation, aircraft navigation, aircraft engine monitoring, etc. must maintain high reliability and durability in extreme environments.
However, the operating environment of aerospace is extremely complex and harsh. Electronic components face extreme temperature changes, strong vibration and radiation, and minor faults that may lead to serious consequences.
Therefore, enhancing the adaptability of components in harsh environments has become a key issue in aerospace electronics manufacturing and surface treatment. With the development of surface strengthening and protection technology, the potential of processes such as sandblasting and shot peening has gradually emerged, providing an effective way to solve the problem.
Main types of precision electronic components
In the field of aerospace, the following precision electronic components are crucial:
- Navigation and control components: such as inertial navigation systems and flight control computers, are responsible for the attitude and trajectory management of aircraft.
- Communication equipment: including high-frequency radio frequency modules and satellite antennas to ensure real-time data transmission.
- Power system sensors: such as temperature, pressure, and vibration sensors, monitoring engine and propulsion system performance.
- Power management module: efficient battery packs and power distribution systems to maintain the stability of spacecraft power supply.
- Electronic connectors and interconnects: such as PCB connectors and circular connectors to ensure the reliability of electrical signal and power transmission.
The common characteristics of these components are high precision, high sensitivity, and versatility, and they must maintain stable operation under various extreme conditions.
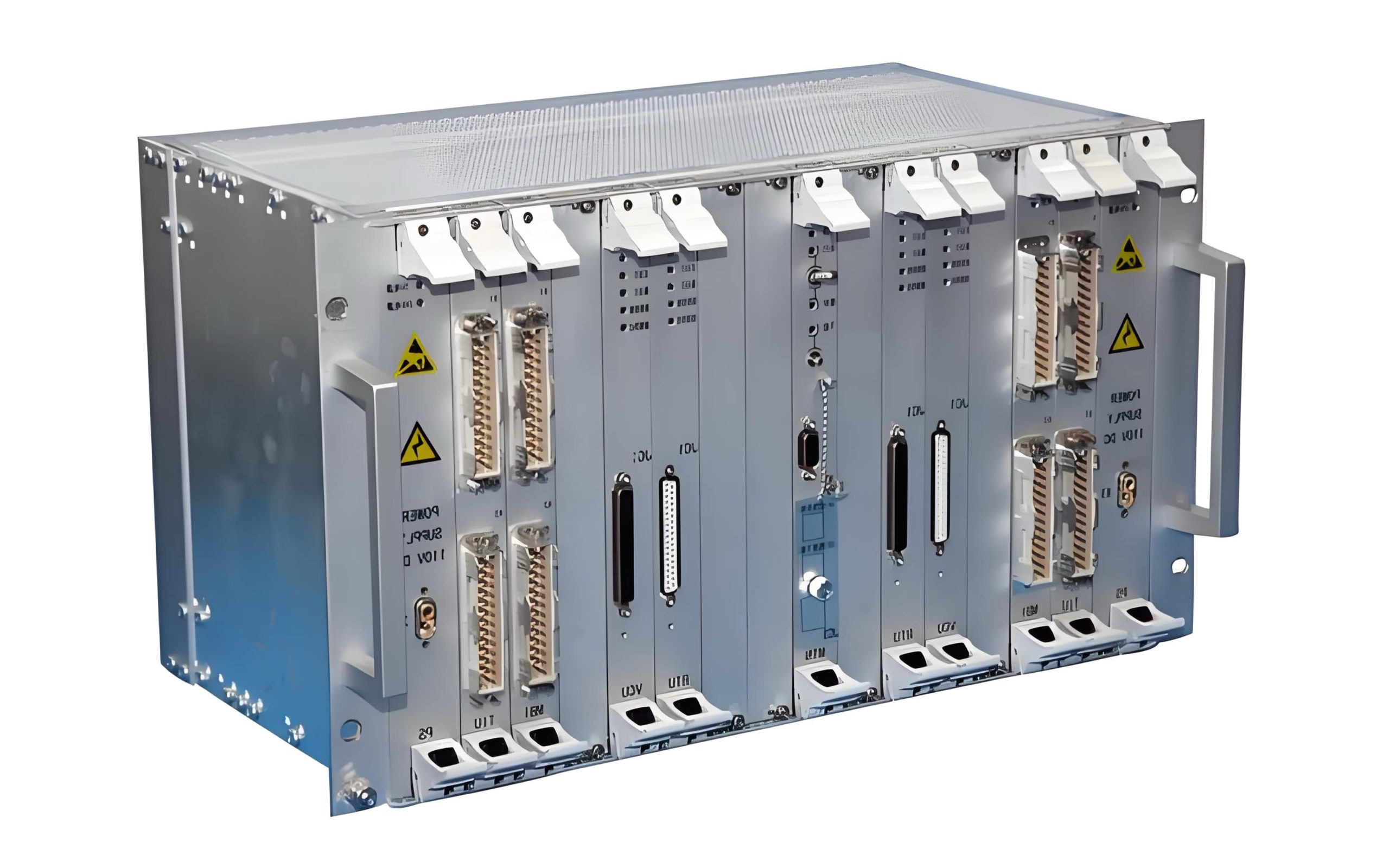
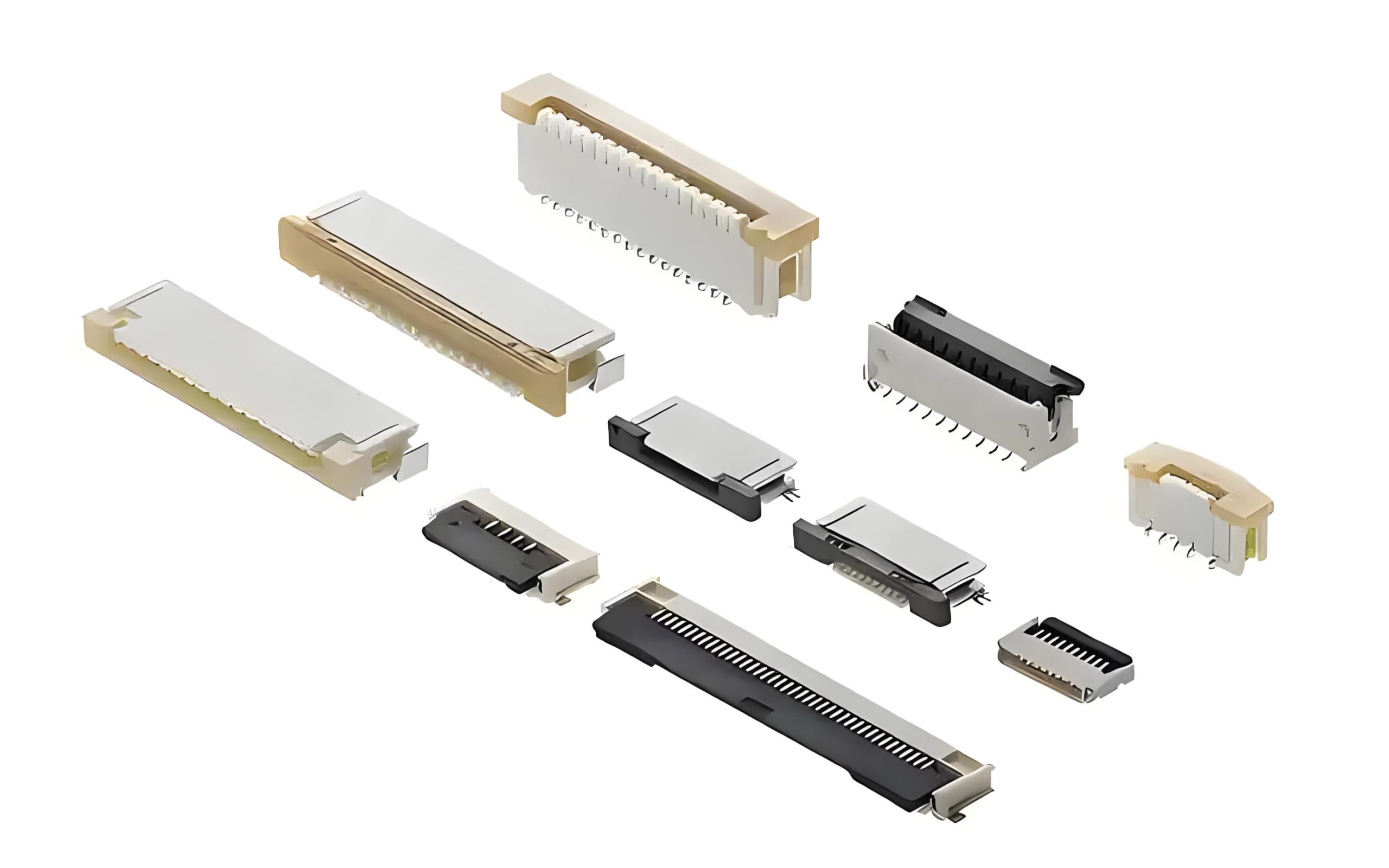
Harsh environment challenges in aerospace
- Extreme temperature changes: from -60°C on the surface of the earth to +125°C in the space environment, the temperature changes dramatically.
- Strong vibration and shock: aircraft takeoff and landing, propulsion system ignition, and long-term flight will produce continuous high-frequency vibrations.
- Cosmic radiation exposure: high-energy particle radiation has a degrading effect on the semiconductor materials and microcircuits of electronic components.
- Low pressure and vacuum environment: resulting in reduced heat dissipation capacity and increased risk of thermal failure of devices.
- Chemical corrosion and wear: such as coolant leakage, fuel residue, or dust particles that physically erode the surface of components.
For this reason, surface strengthening treatment, heat dissipation performance optimization, and structural reinforcement technology have become key means to solve these challenges.
Solutions to improve adaptability
Material and design optimization
- Selection of high-performance materials
- Ceramic materials: have excellent high-temperature stability and corrosion resistance, and can be used for housings and protective covers.
- Special metal alloys: such as titanium alloys and aluminum alloys, have high temperature and impact resistance, suitable for structural components and conductive components.
- Polymer material coating: can be used to improve radiation resistance and reduce the degradation of component surfaces caused by high-energy particle erosion.
- Modularity and structural design
- Modular design: by reducing complexity and separating sensitive components, the transmission impact of environmental shocks can be effectively reduced.
- Structural shock absorption design: using buffer materials and optimized layout to resist damage to precision components caused by vibration and mechanical shock.
The key role of manufacturing process
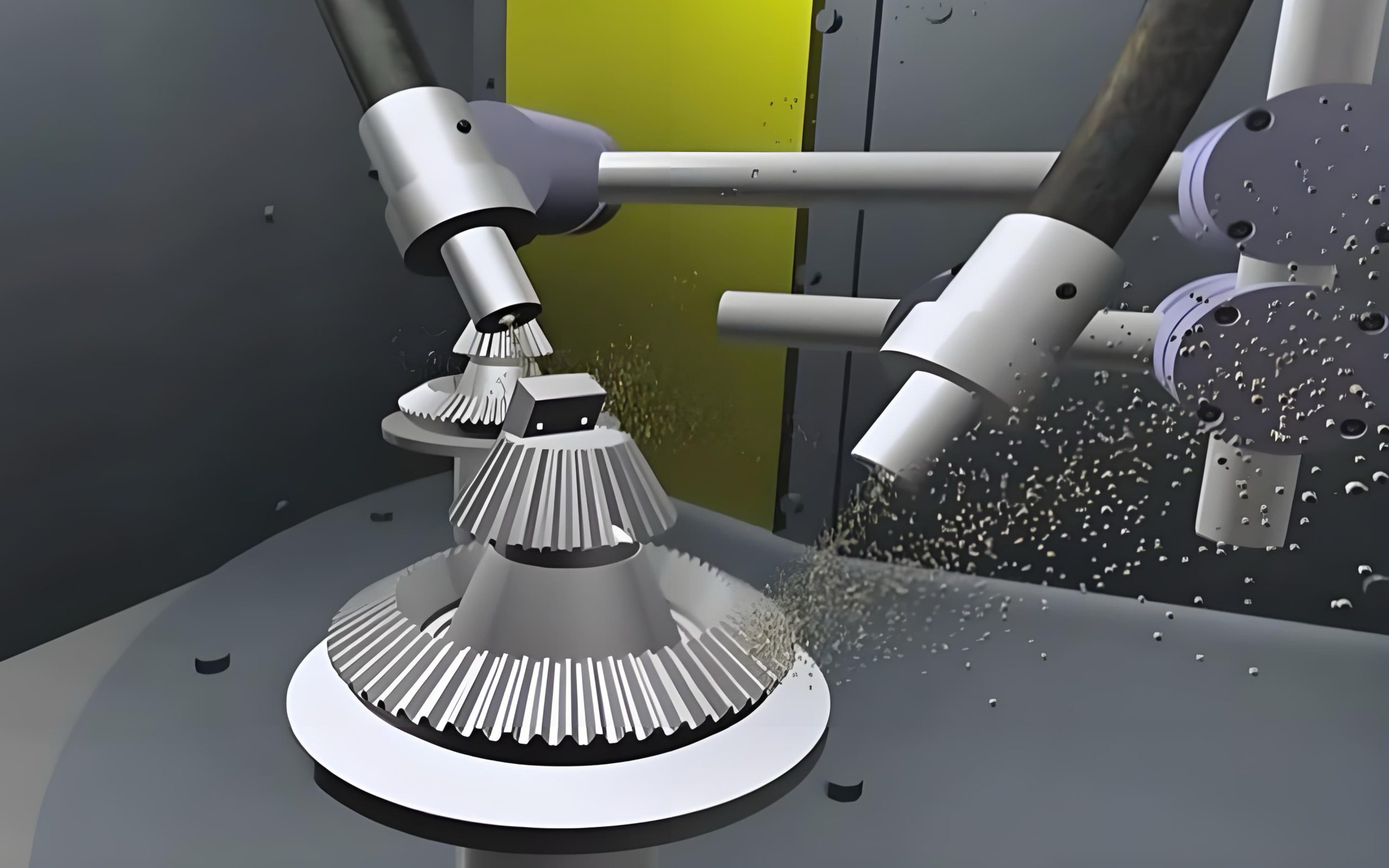
- Precision machining technology
- High-precision machining ensures the matching and durability of components and reduces the risk of failure caused by tolerance problems in harsh environments.
- Precision micromachining technology is used in semiconductor devices to effectively reduce surface defects and improve overall performance.
- Surface treatment technology
- Sandblasting process: Use high-performance ceramic beads or alumina media to clean the surface, eliminate burrs and microcracks, and enhance the corrosion resistance and fatigue resistance of components.
- Shot peening process: Use high-strength particles to impact the material surface, induce compressive stress distribution, and enhance the component’s ability to resist mechanical impact. It is especially suitable for aircraft engine parts that need to withstand vibration.
- Coating technology: For example, high-temperature-resistant and radiation-resistant coatings can further improve the environmental adaptability of electronic components.
Surface treatment media help improve durability
The role of sandblasting technology
Sandblasting technology provides reliable protection and performance optimization for precision electronic components by using high-efficiency media to impact the material surface:
- Improve surface finish
For the optimization of the finish of the connector housing, sandblasting media (such as ultra-fine alumina) can remove tiny burrs or irregular surfaces during processing and prevent the initiation and expansion of microcracks. This is crucial for spacecraft connectors or sensor housings and can effectively extend their service life.
- Remove metal oxides and contaminants
High-purity alumina media can quickly remove the oxide layer on the metal surface with its chemical stability, preventing the source of corrosion from affecting the conductive properties of precision components. For example, the solder joints and contact points of avionics modules need to be kept clean and free of oxidation, and sandblasting can precisely accomplish this requirement.
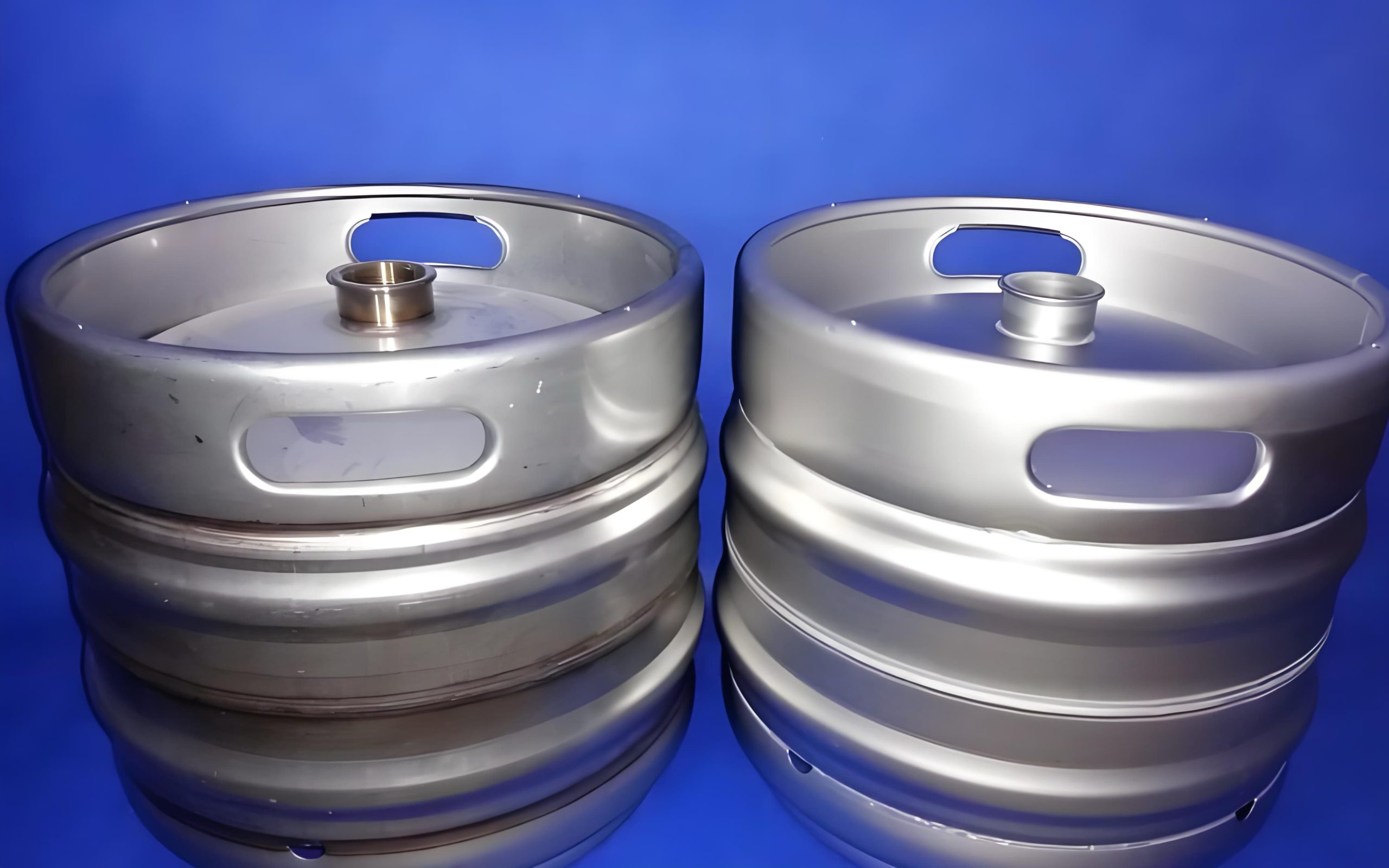
- Adapt to complex geometries
The sandblasting process, combined with the refined media particle size, can easily enter the complex surfaces of electronic components, such as the multi-pin structure of aviation connectors. This ability ensures uniform surface treatment throughout, with no dead angles that affect reliability.
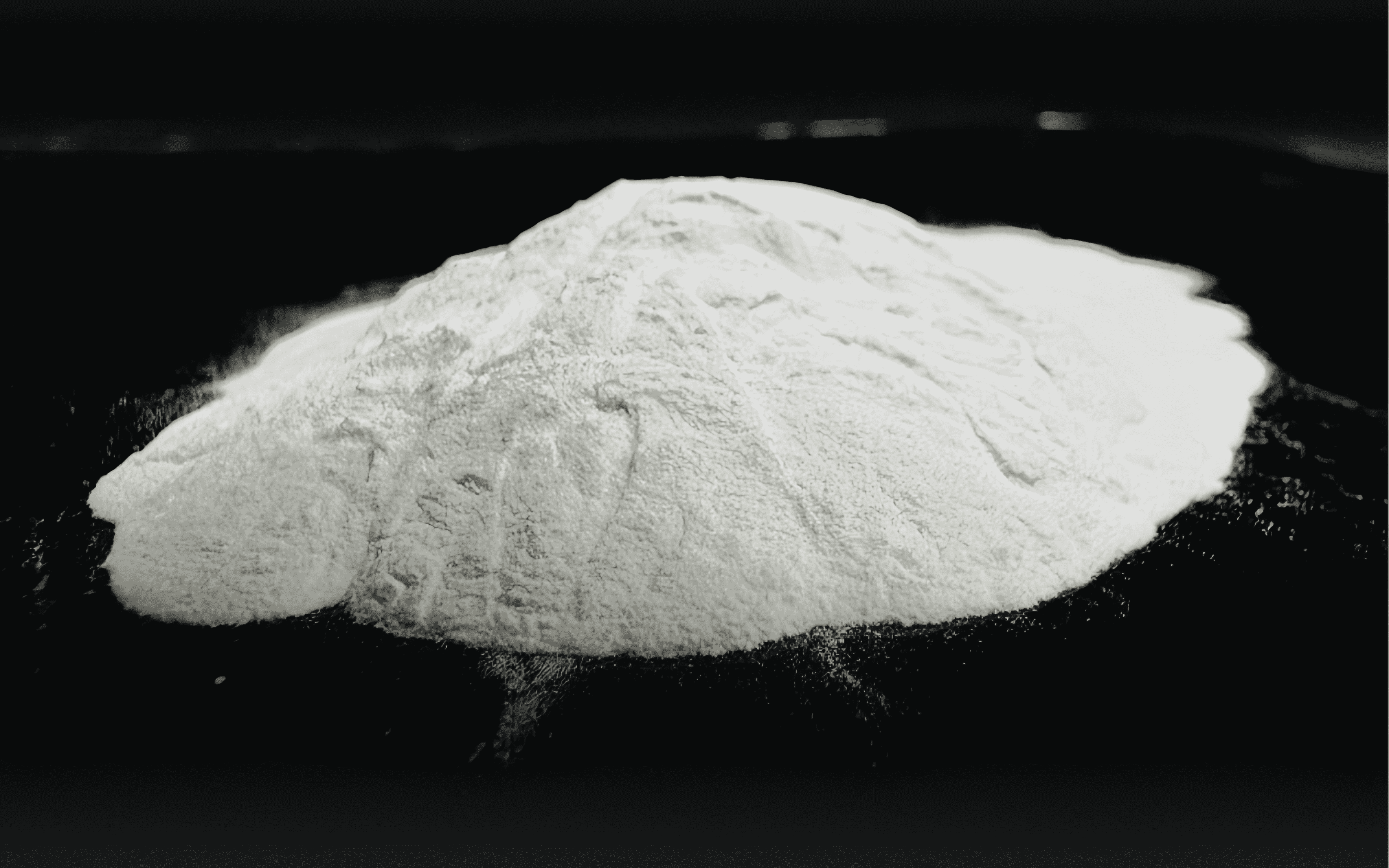
- Improve fatigue resistance
Precision electronic components are susceptible to mechanical stress damage in high-vibration environments (such as aviation propulsion systems). Shot peening with ceramic beads or zirconium oxide beads can form a compressive stress layer on the surface of the housing, reduce the crack growth rate, and improve fatigue life.
- Prevent stress corrosion cracking
Electronic modules and controllers in aerospace are prone to failure when exposed to corrosive chemicals. Shot peening enhances the surface’s corrosion resistance. For example, in modular packaging housings used for flight control electronic units, shot peening can significantly reduce the erosion of metal materials by salt spray and moisture.
- Strengthening composite surfaces
For new composite materials used in spacecraft, zirconium oxide shot blasting media can improve their interfacial bonding strength, ensure lightweight design, and achieve high reliability. This is particularly critical for precision sensor components in aircraft engine support frames.
Recommended media and their characteristics
Ceramic Blasting Beads for Surface Finishing
Features: Ceramic beads have high hardness and excellent durability, smooth surface, and consistent particle size, which can reduce dust generation during processing and ensure environmental protection and cleanliness.
Applicable scenarios: Suitable for electronic component housings that require high-precision surface treatment, such as aerospace connector housings and sensitive electronic components.
Problem-solving: Effectively remove surface defects while improving corrosion resistance to ensure reliability in harsh environments.
Yttria-Stabilized Zirconia Beads
Features: Zirconia beads are known for their high density and excellent impact resistance. They are suitable for strengthening the surface of materials, especially showing excellent stability under high temperature and high-stress environments.
Applicable scenarios: Recommended for strengthening shot blasting processes for aircraft engine components, motor housings, and electronic module protective layers.
Problem Solving: Improve the fatigue resistance and stress corrosion resistance of components through surface stress strengthening, and extend the service life of components.

Ceramic Shots for Shot Peening
Features: Ceramic shot peening beads have consistent particle size distribution and excellent wear resistance, and can accurately introduce compressive stress during surface treatment without damaging the substrate surface.
Applicable Scenarios: Suitable for strengthening the shell of spacecraft and sensitive electronic modules, such as navigation and control units in high-vibration environments.
Problem Solving: Reduce surface crack propagation, significantly improve the fatigue life of materials, and enhance the resistance of the surface layer to corrosion.
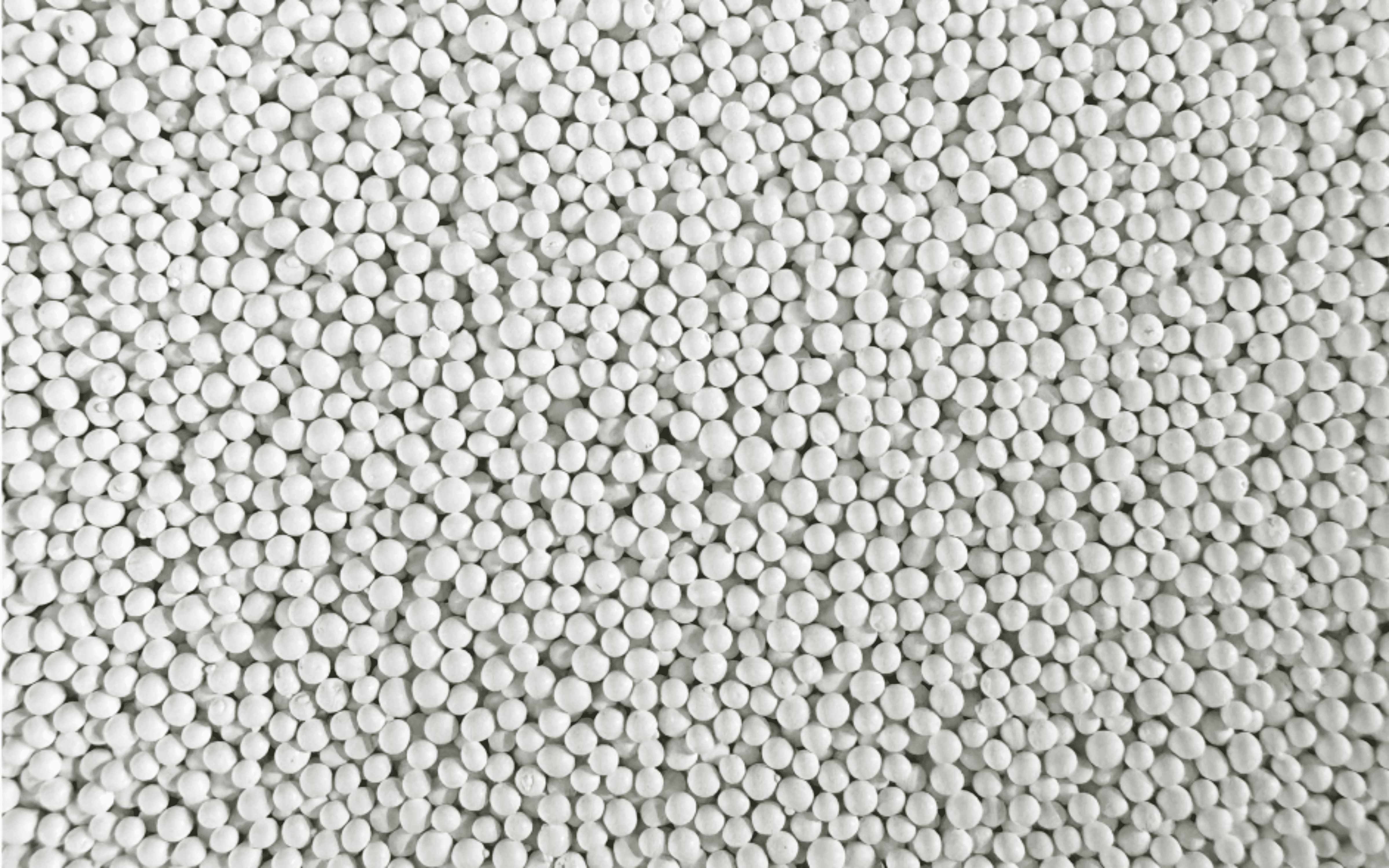
Features: Known for its ultrafine particle size and high hardness, it can achieve extremely high-precision surface treatment while maintaining the integrity of the processed workpiece, and stable chemical properties, and will not contaminate the treated surface.
Applicable Scenarios: Especially suitable for micro-processing of microsensors, PCB connector pins, and other sensitive electronic components.
Problem Solving: Remove oxides and contaminants, optimize surface finish, and improve the conductivity and corrosion resistance of precision electronic components.
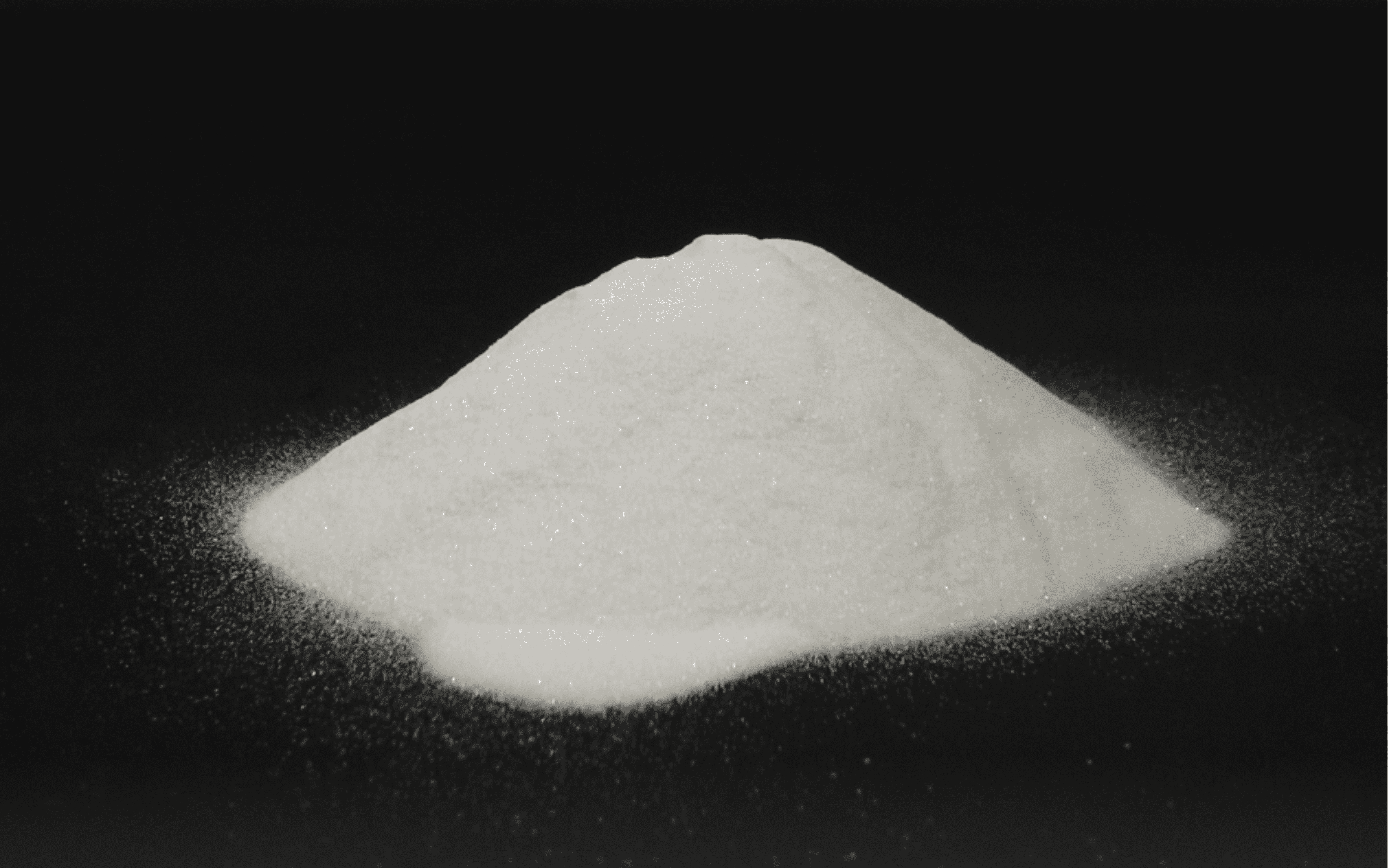
Through the synergy of sandblasting and shot peening, these surface treatment media have become the core booster for precision electronic components to achieve high reliability and durability in harsh environments.
Actual application cases
Zirconia beads strengthen spacecraft sensor housings.
Case: An aerospace company uses zirconia beads to shoot peen the spacecraft sensor housing to improve its fatigue resistance and stress corrosion resistance. Zirconia beads have extremely high hardness and wear resistance. After fine shot peening, the sensor housing shows better resistance to impact and environmental changes. After this treatment, the fatigue resistance of the sensor in extreme environments is improved by about 30%, and the service life is extended.
Ceramic beads improve the surface roughness of aviation connectors.
Case: In an avionics project, ceramic beads are used to improve the surface roughness of aviation connectors. Through the sandblasting process, ceramic beads can effectively remove tiny surface defects and improve the electrical conductivity and signal transmission performance of the connector. The surface roughness of the treated connector is reduced by 40%, which greatly improves the performance stability of the connector in high-speed data transmission and high-temperature environments.
Alumina media removes surface oxides from components.
Case: A military enterprise uses alumina media to sandblast precision parts of aircraft engines to remove surface oxides. Alumina particles not only remove oxide scales but also protect metal surfaces from further corrosion. After testing in high-temperature and high-pressure environments, the treated parts showed 25% higher durability than untreated parts. This technology has been used in multiple aircraft engine projects, significantly extending the service life of engine components.
Through these cases, we can see that choosing the right surface treatment media is crucial for precision electronic components in aerospace, which can not only improve the performance of components but also significantly extend their service life.
Since its establishment in 2001, Henglihong has focused on the field of sandblasting and shot peening abrasive media, combined with German Nabotum equipment technology to ensure high-standard automated production. We have 38,000 square meters of modern plant and a senior R&D team to provide customized solutions for customers around the world.
With ISO9001, ISO14001 and EU CE, ROHS certification, our products have superior performance and the production process meets environmental standards. We adhere to the principle of “customer first”, provide efficient delivery and personalized service, and establish long-term cooperative relationships.
Today, Henglihong has won the trust of customers around the world with its excellent quality, quick response, and environmental commitment. Choosing Henglihong means choosing a trustworthy partner!
We provide free consulting services to help you choose the most suitable sandblasting materials. Send us samples, we will test and recommend the best solution according to your needs. At the same time, we support small batch trials to ensure that you make a wise choice.
For more product information or to get a quote, please contact us!
Don’t forget to bookmark our website, we will update the blog regularly to bring more industry information and practical tips.
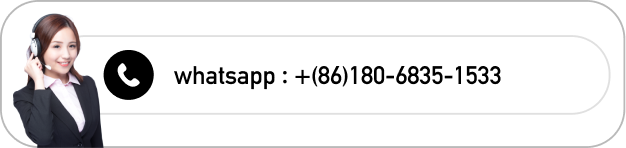