How Alumina Blast Media Polish Aluminum
December 5, 2024
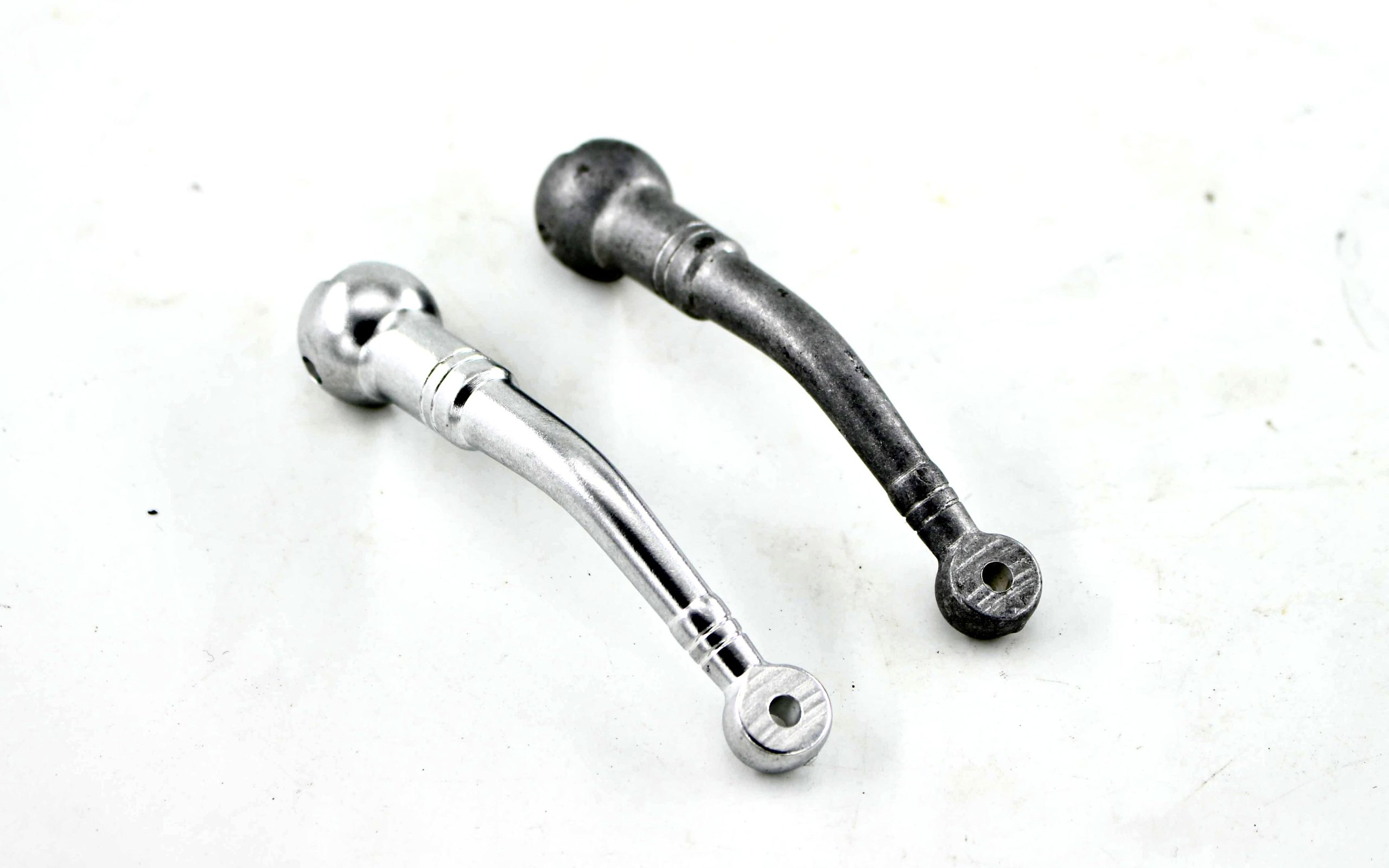
Why is aluminum polishing so important
Aluminum has become an indispensable material in the modern industry because of its lightweight, high strength, and corrosion resistance. From aerospace to automotive manufacturing, to consumer electronics and the construction industry, aluminum plays an important role in many fields. However, during the processing of aluminum, problems such as oxidation, scratches, and burrs often occur on the surface, which puts higher requirements on the performance and appearance of the product.
Polishing is a key surface treatment technology that aims to eliminate aluminum’s surface defects while improving its visual effect and functionality.
Three major purposes of aluminum polishing
Aluminum polishing is not only for aesthetics but also to meet the following core needs:
- Improve product performance: By removing surface oxides and burrs, improve the sealing and assembly accuracy of parts.
- Enhance material durability: After polishing, the surface roughness and friction coefficient are reduced, and the material is more resistant to corrosion and wear.
- Optimize visual effects: Provide a smooth and uniform surface for high-end products and increase their commercial value.
Common challenges of aluminum polishing
Although the polishing process is crucial to the application of aluminum, its implementation process is not always smooth. Here are some common challenges:
- Surface damage: Aluminum is softer than steel and is easily scratched by traditional polishing media.
- Incomplete oxide layer cleaning: The natural oxide film on the surface of aluminum is hard, requiring efficient and fine polishing media.
- Difficult to ensure consistency: Traditional polishing methods often have difficulty in achieving uniform surface treatment of large areas or complex structures.
- Environmental and compliance issues: Many traditional polishing materials and processes produce pollutants and do not meet modern industrial environmental standards.
Core challenges of aluminum polishing
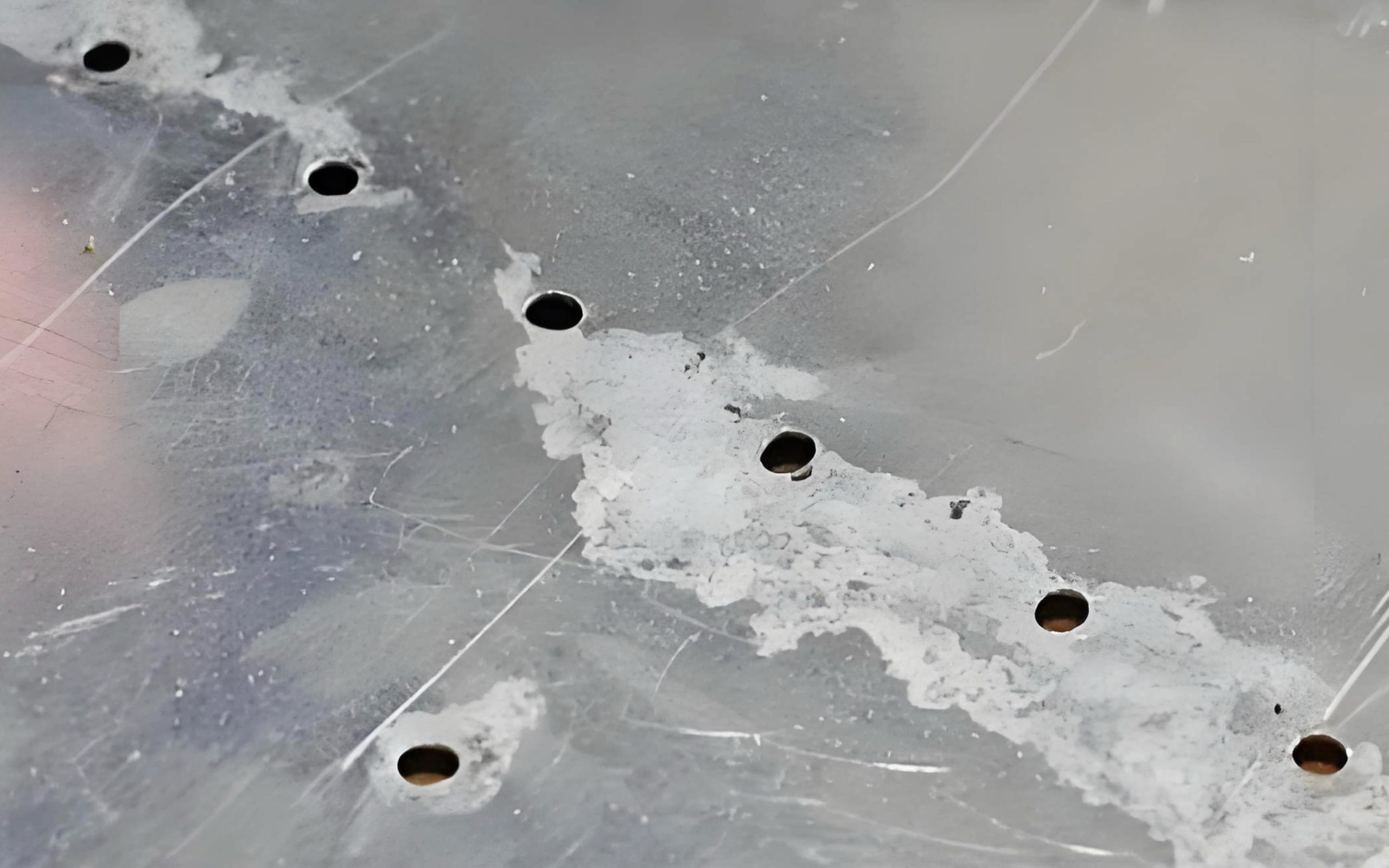
Surface sensitivity
Aluminum is particularly susceptible to scratches due to its soft texture (Brinell hardness is usually in the range of 30-150, depending on the alloy composition). During the polishing process, choosing the wrong hardness of the medium will cause the following problems:
- Scratches and surface defects: Media with too high a hardness may leave deep scratches on the aluminum surface, especially thin-walled aluminum or complex curved surfaces.
- Uneven wear: Media with too low a hardness cannot evenly remove the oxide layer or impurities, affecting the surface finish.
For example, in the precision machining of aluminum alloy aviation parts, the surface roughness requirement is extremely high (usually the Ra value needs to be less than 0.4 microns). If the medium is irregular in shape or the hardness is too low, it may lead to poor local surface treatment, thereby increasing the rework rate and production costs.
Pollution problem
Traditional sandblasting media (such as quartz sand, or steel shot) may leave impurities or microparticles on the surface of aluminum, which not only affects the appearance of the final product but may also cause the following problems:
- Reduced material properties: Surface residues may cause local corrosion and reduce the corrosion resistance of aluminum.
- Impact on subsequent processes: In the automotive industry, spraying and electroplating have extremely high requirements for surface cleanliness, and any contamination will cause reduced coating adhesion or defects.
Process efficiency
Traditional polishing materials are inefficient, especially when processing large batches of workpieces or complex geometries. The following problems are particularly prominent:
- Increased working hours: Uneven or poor fragility of medium particles will lead to longer polishing time. The traditional sanding process takes an average of 3-5 times longer to achieve the desired effect.
- Excessive energy consumption: Due to poor polishing efficiency, equipment operation time is extended, and energy costs increase accordingly.
Environmental protection and compliance
Global requirements for industrial emissions are becoming increasingly stringent, especially in industries involving aluminum processing. The use of traditional media is often accompanied by the following environmental issues:
- Dust pollution
- Difficulty in media recycling
Advantages of spherical alumina media
Balance between surface sensitivity and high hardness
The surface of aluminum is soft and easily scratched, and the media must have appropriate hardness to balance cleaning ability and surface protection.
- High-purity spherical alumina blast media has a Mohs hardness of up to 9, which can effectively remove oxide layers and surface defects, while its spherical structure avoids scratches that may be caused by irregular media.
- Long life characteristics: Compared with traditional sandblasting media,spherical alumina blast media has strong wear resistance and can be used repeatedly, thus reducing the replacement frequency and overall cost.
After polishing, the surface of aluminum molds or body parts needs to maintain consistency and smoothness. The high hardness of spherical alumina combines with gentle surface contact ability to ensure that the surface structure of aluminum is not damaged.
Fine size and uniform polishing
Aluminum often involves the surface treatment of complex shapes or micro parts, and the media size and distribution uniformity become key.
- Spherical alumina blast media provides a minimum particle size option of 5 microns, which can achieve high-precision polishing, especially suitable for aluminum parts with complex geometries or high-demand surfaces, such as aircraft engine components or electronic product housings.
- Through uniform particle shape and distribution, matte or mirror effects can be presented after polishing without obvious textures.
- In the surface treatment of aluminum alloy turbine blades or 3C electronic products, spherical alumina blast media brings consistent surface treatment effects with its fine size, meeting the fine appearance requirements of related industries.
Pollution and cleaning efficiency
Aluminum is easily contaminated by the medium during the polishing process. Traditional materials such as quartz sand or glass beads may leave debris or chemical residues, affecting the quality of the finished product.
- The purity of spherical alumina medium is as high as 99% or more, and no impurities or chemical pollution are generated during use.
- Its fragility and rapid decomposition characteristics make it almost residue-free after processing, significantly reducing cleaning time and subsequent process costs.
- For example, when aluminum parts are used in the food or medical industry, the surface cleanliness requirements are extremely high. The high purity properties of spherical alumina ensure that there is no residue on the surface after polishing, which will not affect the safety of use.
Process efficiency and environmental adaptability
In high-temperature, high-intensity continuous production environments, the corrosion resistance, heat dissipation performance, and process efficiency of the medium become core considerations.
- Corrosion resistance: Spherical alumina blast media remains stable in humid or acidic environments, does not decompose, and does not affect the polishing effect.
- Efficient heat dissipation: The medium structure design facilitates heat dissipation, effectively reduces the temperature of the workpiece and medium under high-frequency use, and avoids thermal deformation.
- In large-scale industrial production (such as automobile manufacturing), spherical alumina not only increases the polishing volume per hour but also reduces the cooling demand of equipment due to its heat dissipation performance and extends the service life.
Environmental protection and industry compliance
Under strict environmental regulations, the environmental performance and production standards of industrial polishing media are crucial.
- Spherical alumina is ISO9001:2015 and ISO14001 certified to ensure its environmental compliance during production and use.
• Its recyclable nature significantly reduces its waste disposal volume. It reduces industrial pollution and reduces corporate processing costs.
• For the new energy industry (such as aluminum battery housing production), environmental regulations require that waste emissions be minimized during production. The environmental properties of spherical alumina help companies meet international standards.
Specific application cases
Aviation industry: efficient deoxidation and precision polishing
An aviation manufacturing company successfully achieved a surface roughness of Ra 0.2 µm by treating aircraft aluminum alloy skins with spherical alumina sandblasting media.
This media not only improves surface precision but also reduces media residue and cleaning time through its high hardness and rapid decomposition characteristics, greatly improving production efficiency.
This process also complies with AS9100 standards and environmental regulations, making it an ideal choice for surface treatment of aviation parts. [1]
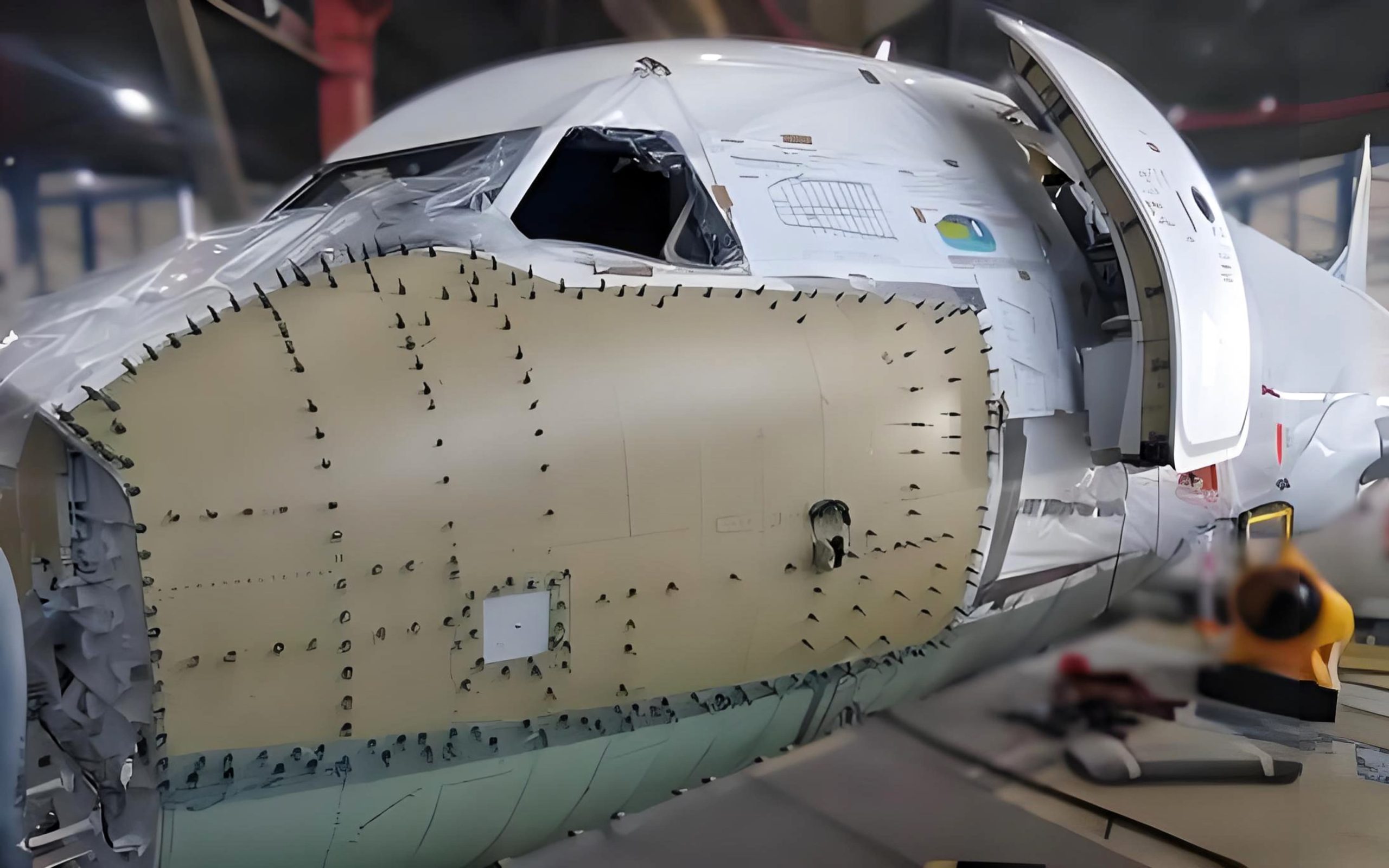
Automobile manufacturing: efficient treatment of engine parts and car bodies
Automakers who use BA-10 spherical alumina blast media to treat aluminum alloy engine parts have found that the media is about 15% more efficient than traditional polishing media. In addition, its rapid decomposition characteristics significantly reduce the cleaning costs of the production line, reducing the cleaning time per batch from 40 minutes to 25 minutes. These advantages are also fully reflected in the surface treatment and appearance optimization of the car body. [1]
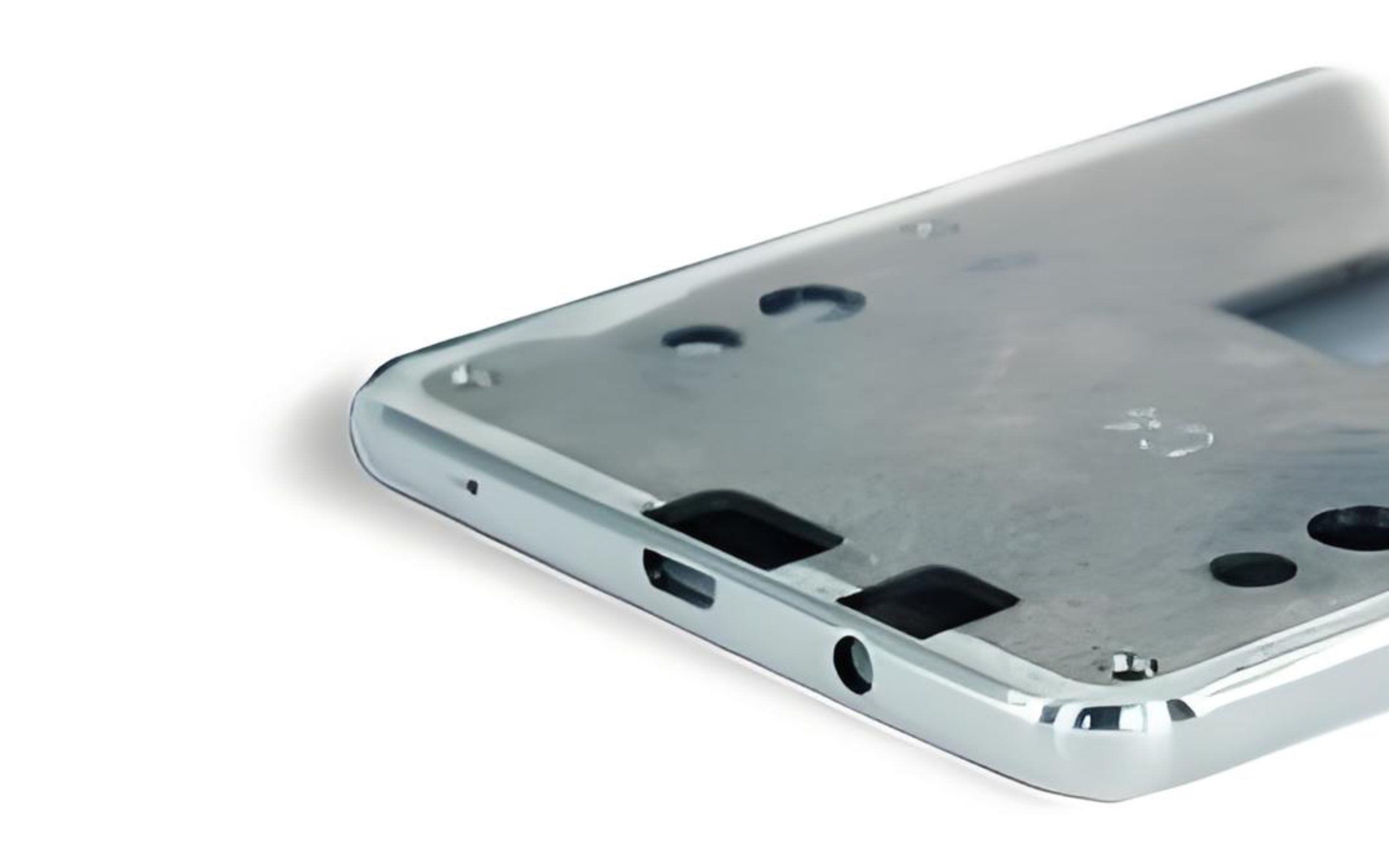
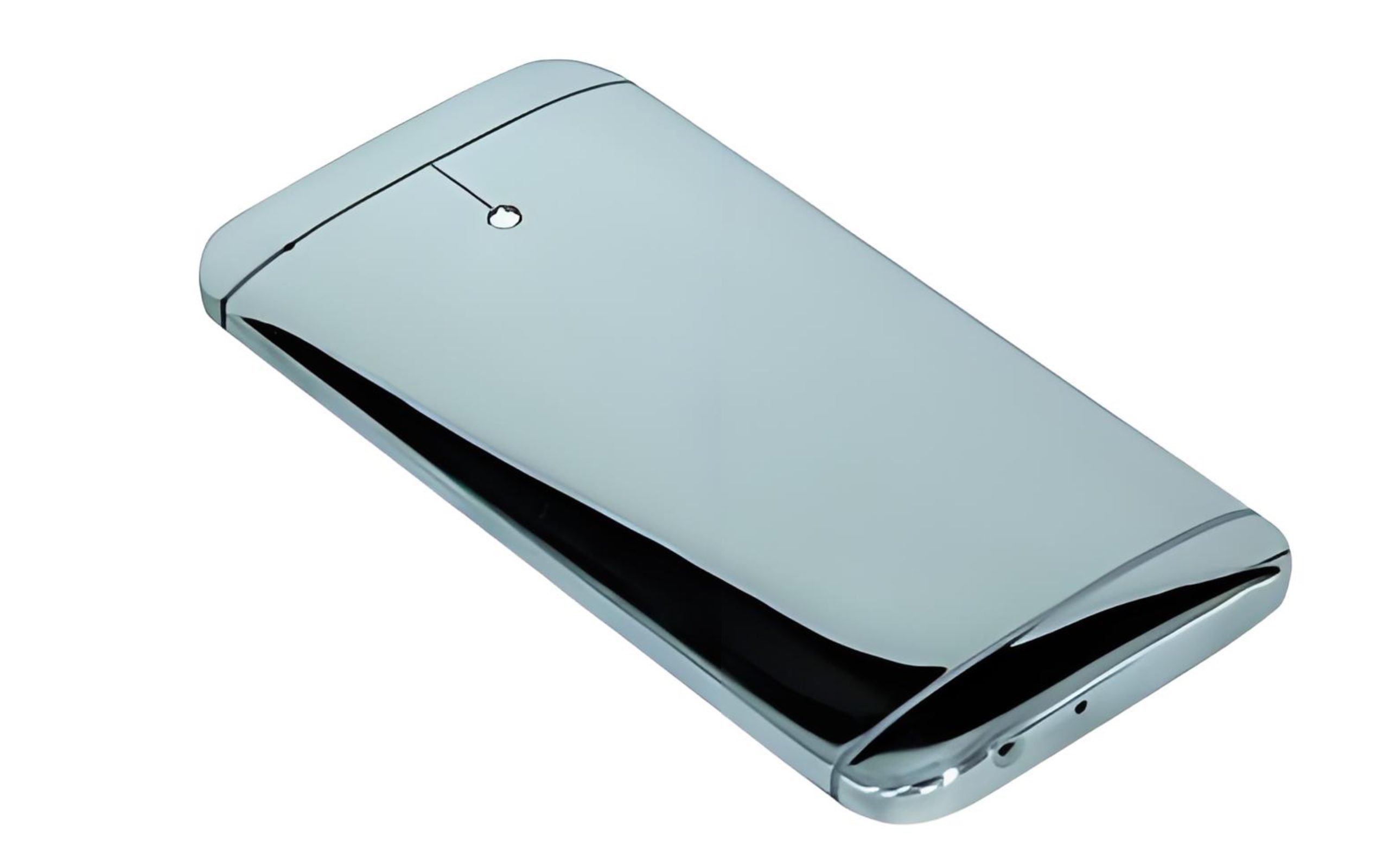
Electronic products: surface consistency polishing of housings and components
The finish of aluminum housings in electronic products directly affects their market competitiveness.
A consumer electronics manufacturer uses spherical alumina to polish smartphone housings to a matte finish while maintaining a roughness of Ra 0.1 µm.
This high-purity media eliminates contamination residues, ensures product consistency in aesthetics and functionality, and meets consumer demand for high-end electronic devices.
In addition, the excellent heat dissipation performance of spherical alumina further improves the overall performance of electronic products when polishing internal components such as heat sinks. [2]
Why choose us?
Our spherical alumina sandblasting media is the ideal choice for high-precision surface treatment in the industry due to its unique properties and design. The following is an overview of our product advantages and features:
Ultra-fine particle size: fine and uniform treatment
The minimum particle size can reach 5 microns, which is suitable for processing complex geometric shapes and penetrating fine areas to ensure uniform and fine polishing effects, especially suitable for surface treatment of high-end electronic products and complex components.
Efficient polishing: shortened production cycle
The spherical design and ultra-fine particle size enable the media to remove surface roughness and defects in a short time, greatly improving polishing efficiency. The production cycle is shortened, the number of processes is reduced, production costs are significantly reduced and output is increased.
High purity: reduce impurities and ensure quality
High-purity materials avoid contamination, ensure the cleanliness of each processing process and the quality of the final product, and are suitable for industries with extremely high cleanliness requirements, such as medical and semiconductor manufacturing.
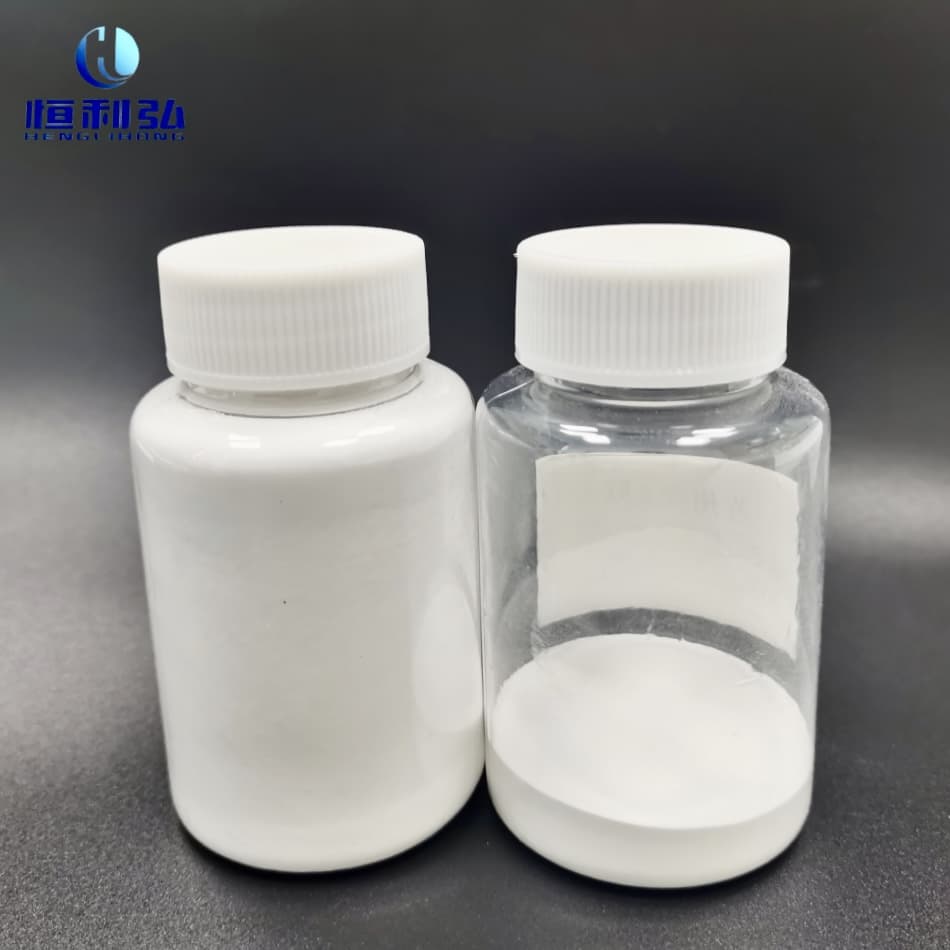
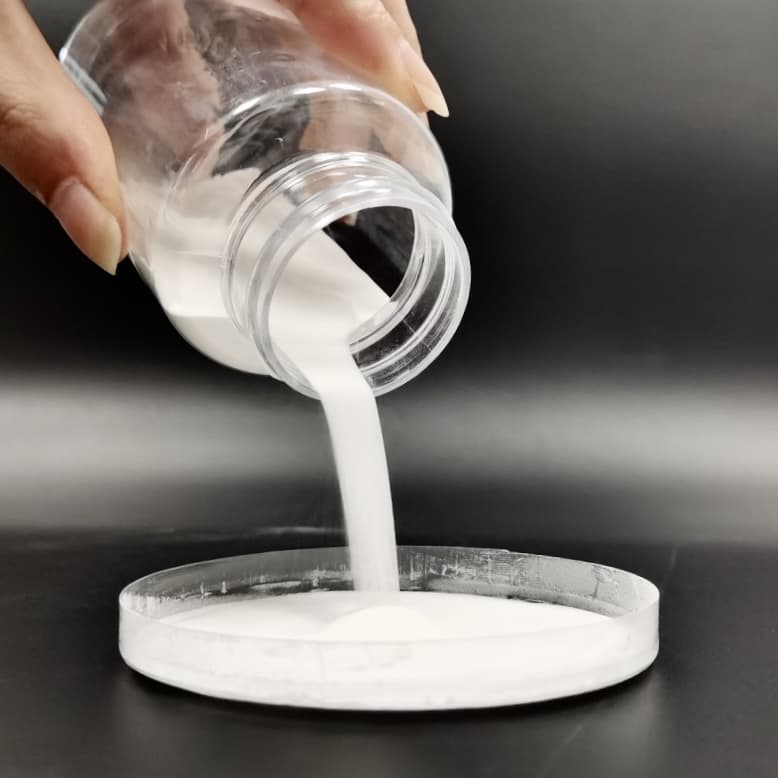
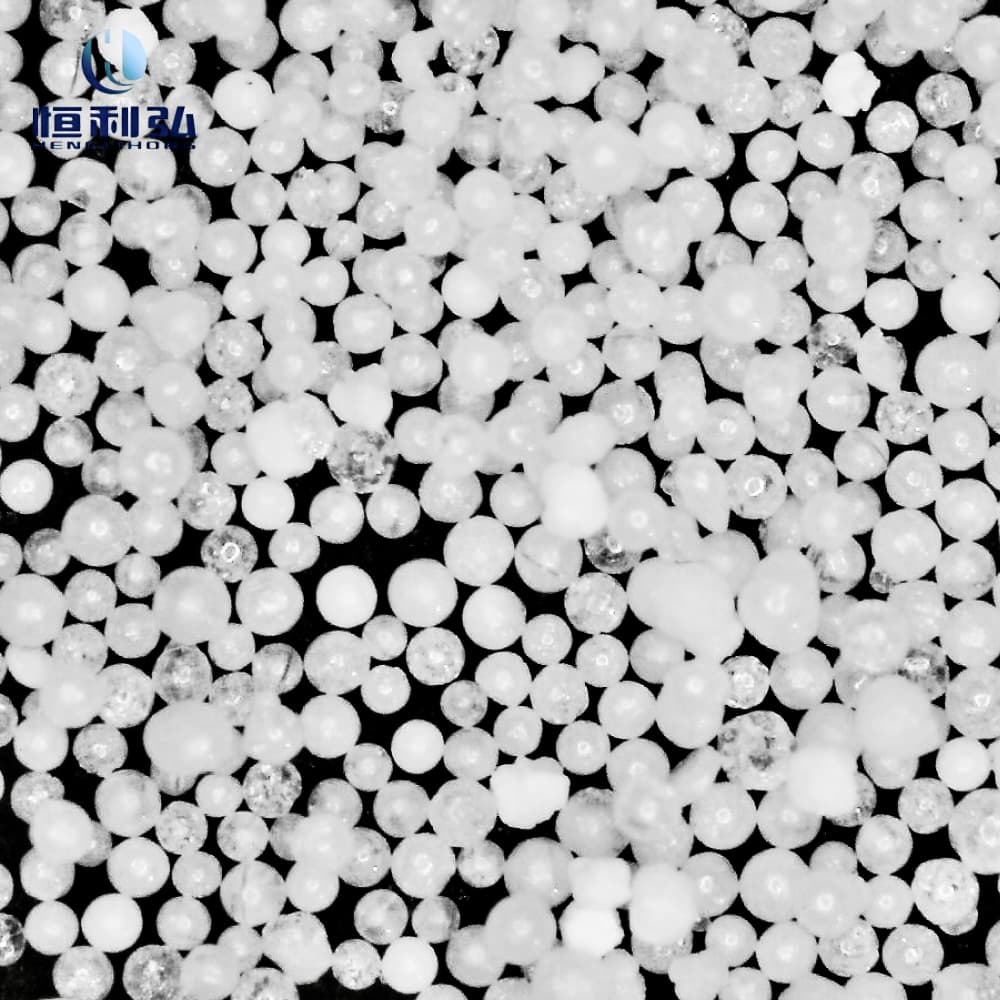
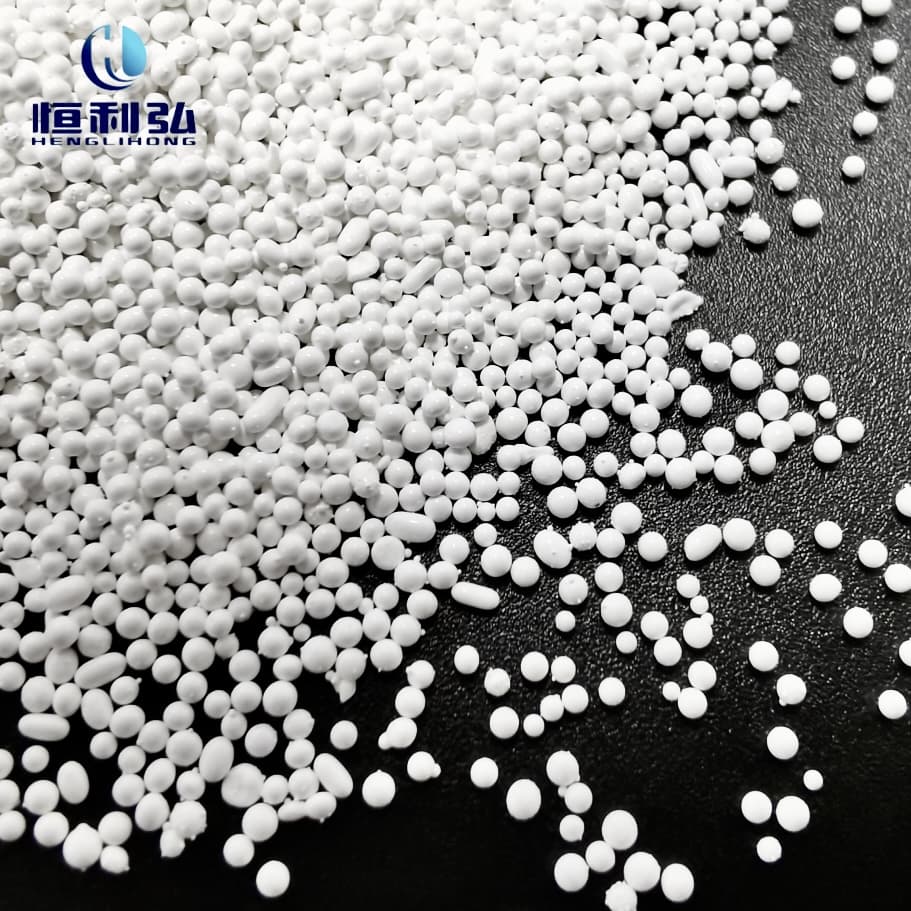
Matte surface effect: both beautiful and functional
The treated surface presents an elegant matte effect, avoiding the reflection problem caused by excessive brightness, while retaining the natural texture of the material, improving the beauty and touch of the product.
Wide applicability: meet the needs of multiple fields
The medium can be widely used in mold sandblasting, 3C electronic products, automobile manufacturing, aerospace, and other industries to meet the surface treatment needs of different environments and process requirements, ensuring high precision and consistency.
Improve durability: reduce friction and increase life
The treated surface is smoother and more delicate, reducing friction resistance, and thereby significantly improving the durability and service life of the product. This feature is particularly important for parts that are often affected by friction, extending the maintenance cycle of the equipment.
Contact us for customized services
We encourage customers to contact us at the beginning of the project to discuss your specific needs. Our team of experts will provide you with professional technical support and customized solutions to solve your problems in the shortest possible time.
Free trial and sample testing
To let you fully understand the performance of our products, we provide free trial services.
By trying our samples, you can intuitively feel the product’s efficient polishing ability and excellent surface treatment effect, and verify our technical advantages and product quality.
Or you can send us your workpiece to see how our operation works, which can effectively save your analysis time.
Please rest assured that we will give you a satisfactory solution!
Contact information
If you would like to obtain more product information, technical support, or customized services, please feel free to contact us. You can contact us in the following ways:
- WhatsApp phone: +86 180-6835-1533
- Email: contact@hlh-js.com
- Official website: https://hlh-js.com/
We will provide a range of product specifications, safety data, and real user cases. With this additional information, you can better evaluate whether the product meets your needs.
We look forward to your consultation and are willing to provide professional support and services for your project.
[1] From Valence Surface Technologies and polishing cases in aviation and automotive manufacturing, which shows its wide industry applicability.
[2] From Denka Company Limited’s detailed description of the application of spherical alumina in electronic components and thermal management.
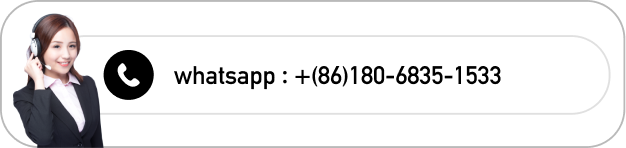