Full Analysis of Ceramic Beads blasting Specifications
August 28, 2024
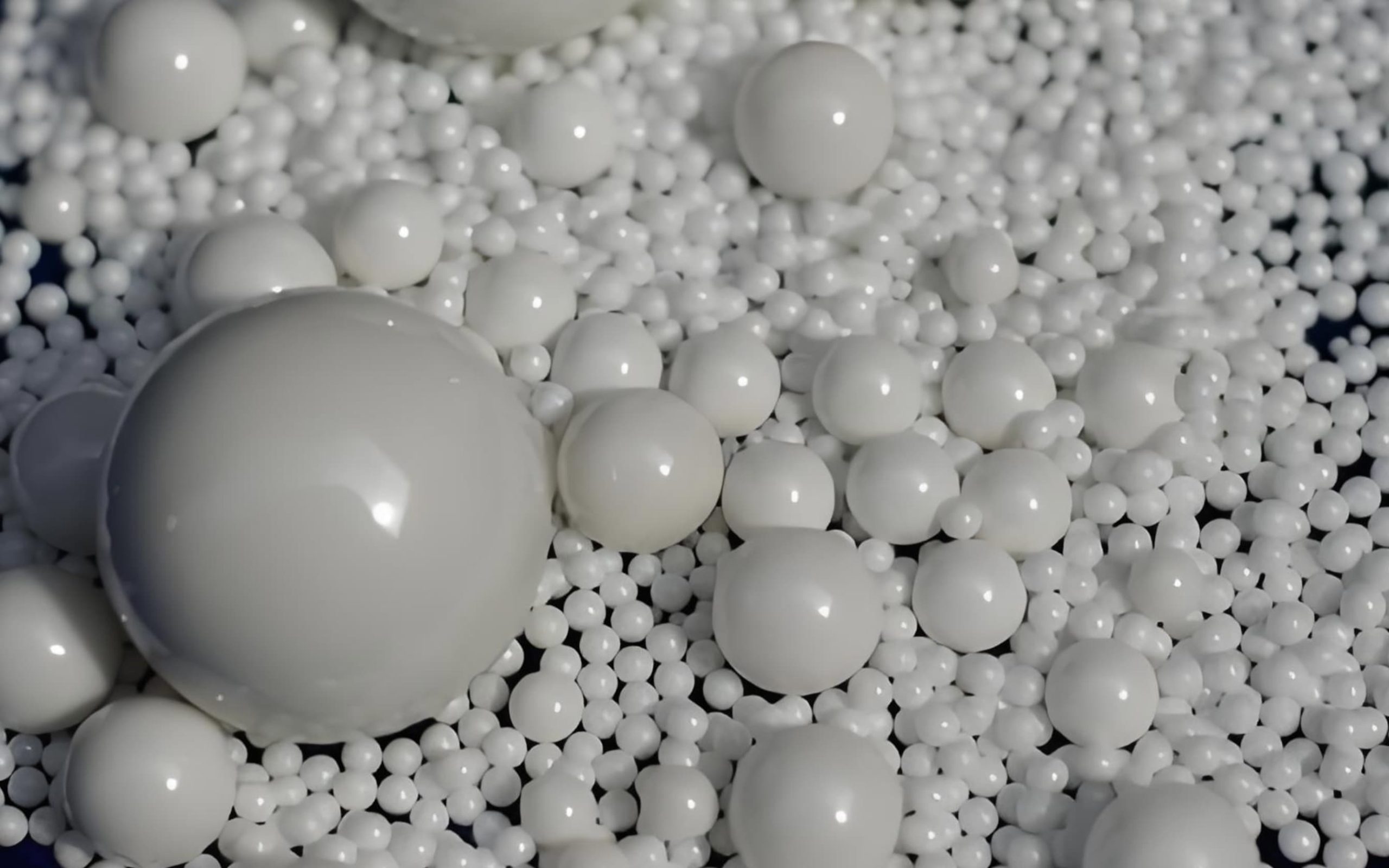
In the industrial sector, sandblasting is a commonly used surface treatment method. It can remove contaminants, oxide scales, rust, etc., from the surface of workpieces, while also increasing surface roughness to improve coating adhesion. Ceramic beads blasting media, as a new type of sandblasting material, has advantages such as high hardness, good wear resistance, and strong chemical stability, making it widely used in various fields. However, different sizes of ceramic beads blasting media are suitable for different applications. This article will provide a detailed introduction to all specifications of our company’s ceramic beads blasting media and their applicable scenarios, helping you better select the appropriate sandblasting material.
Characteristics of Ceramic Beads Blasting
- High Hardness
The hardness of ceramic beads is typically above Mohs 7, higher than traditional sandblasting materials such as quartz sand and glass beads. This allows ceramic bead sandblasting to more effectively remove stubborn contaminants and oxide scales from workpieces while reducing wear during the sandblasting process and extending the lifespan of the sandblasting equipment. - Good Wear Resistance
Ceramic beads have excellent wear resistance and are not easily broken or worn out during sandblasting. This not only ensures the stability of the sandblasting effect but also reduces the consumption of grit blasting materials, lowering production costs. - Strong Chemical Stability
Ceramic beads have strong chemical stability and are not easily chemically reactive with the workpiece surface. This makes ceramic beads blasting suitable for surface treatment of various materials, including metals, plastics, and rubber. - Environmental Protection and No Pollution
Ceramic beads blasting does not produce dust or harmful substances, making it environmentally friendly. Additionally, ceramic beads can be recycled, meeting environmental protection requirements.
Applicable Scenarios for Different Sizes of ceramic beads blasting:
600 – 850 Microns Ceramic Beads Blasting
- Applicable Scenarios
Mainly used for surface cleaning and roughening of large castings and steel structures. For example, in shipbuilding and bridge construction, large steel structures need surface treatment to improve coating adhesion and corrosion resistance. This specification of sandblasting can quickly remove surface rust, oxide scales, and other impurities, while creating a certain roughness on the workpiece surface, providing a good foundation for subsequent coating applications. - Advantages
- High Cleaning Efficiency: Due to the larger particles, it can remove a large amount of impurities in a shorter time.
- Moderate Roughness: Can create suitable roughness for coating adhesion, enhancing coating bonding strength.
- Minimal Workpiece Damage: During cleaning, the impact force on the workpiece is relatively small, reducing deformation and damage.
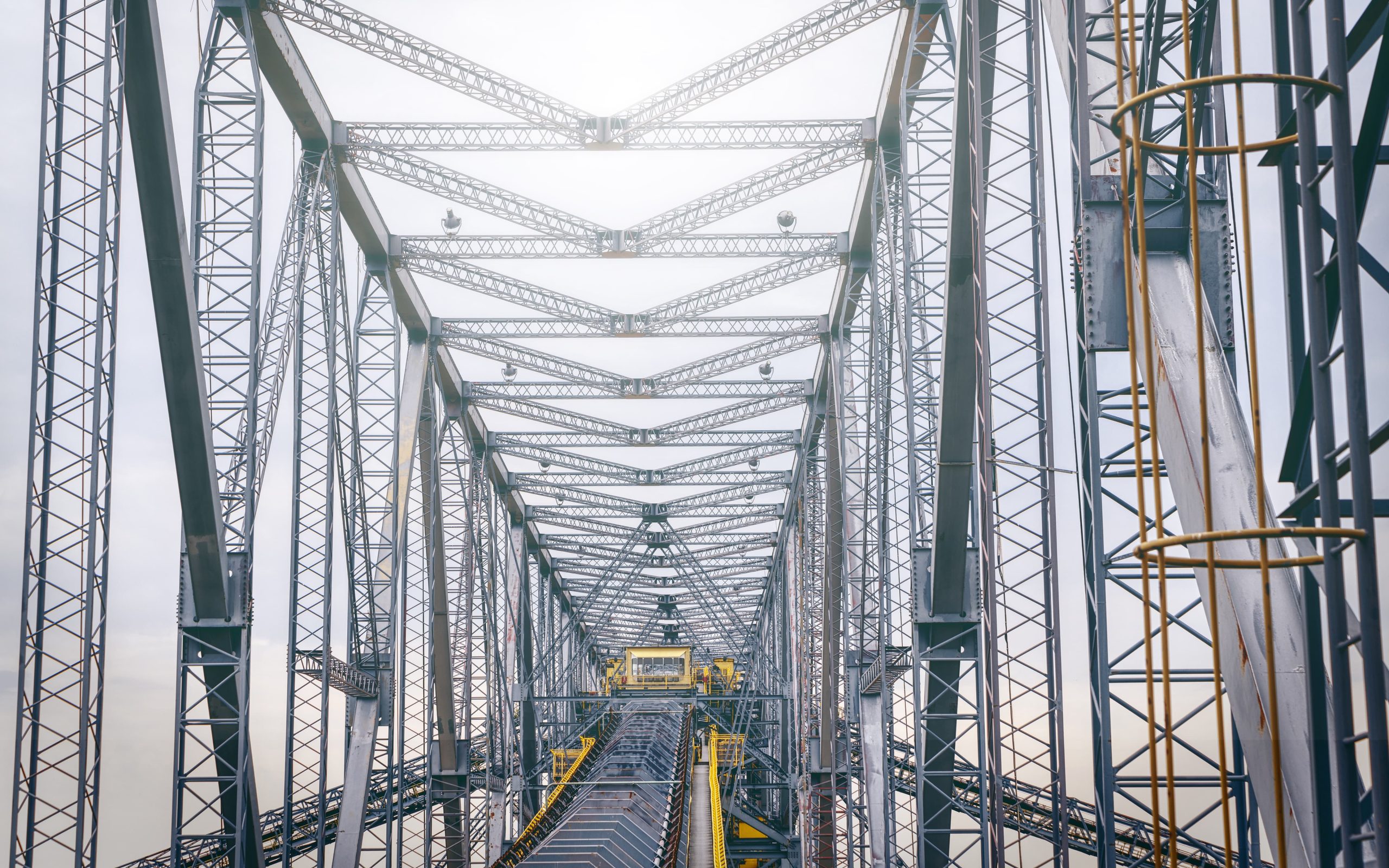
Large steel structures used in bridge construction
425 – 600 Microns Ceramic Beads Blasting
- Applicable Scenarios
Suitable for surface cleaning and strengthening of medium-sized castings and mechanical components. For example, in automotive manufacturing and machining, some medium-sized castings and mechanical components require surface treatment to enhance wear resistance and corrosion resistance. This specification of sandblasting can effectively remove surface oil, rust, and other impurities, while creating a certain strengthening layer on the workpiece surface. - Advantages
- Good Cleaning Effect: Can remove stubborn impurities, making the workpiece surface highly clean.
- Significant Strengthening Effect: Can create a certain strengthening layer on the workpiece surface, improving its performance.
- Wide Applicability: Suitable for surface treatment of various materials such as steel, aluminum alloys, and copper alloys.
250 – 425 Microns Ceramic Beads Blasting
- Applicable Scenarios
Suitable for surface cleaning and finishing of small castings and precision mechanical components. For example, in electronics and instrumentation, some small castings and precision mechanical components require surface treatment to improve surface quality. This specification of sandblasting can remove tiny impurities and burrs from the surface, while making the workpiece surface smoother and more even, enhancing the overall appearance. - Advantages
- High Cleaning Precision: Can remove tiny impurities and burrs, making the workpiece surface smoother.
- Good Finishing Effect: Can create uniform roughness on the workpiece surface, improving appearance quality.
- Minimal Workpiece Damage: Due to the smaller particles, the impact on the workpiece is reduced, minimizing damage.
125 – 250 Microns Ceramic Beads Blasting
- Applicable Scenarios
Suitable for surface cleaning and polishing of precision castings and optical components. For example, in aerospace and optical instruments, some precision castings and optical components require surface treatment to improve surface accuracy. This specification of sandblasting can remove fine impurities and scratches, while making the workpiece surface smoother and brighter, enhancing optical performance and surface quality. - Advantages
- Excellent Cleaning Effect: Can remove very fine impurities and scratches, making the workpiece surface extremely clean.
- Significant Polishing Effect: Can create a high gloss surface on the workpiece, improving appearance quality.
- Narrow Applicability: Mainly suitable for precision castings and optical components with very high surface quality requirements.
180 – 250 Microns Ceramic Beads Blasting
- Applicable Scenarios
Similar to 125 – 250 Microns ceramic bead sandblasting, it is suitable for surface cleaning and polishing of precision castings and optical components. However, its particles are slightly larger, making it more suitable for applications with slightly lower surface roughness requirements. - Advantages
- Good Cleaning Effect: Can remove fine impurities and scratches, making the workpiece surface clean.
- Moderate Polishing Effect: Can create a certain level of gloss on the workpiece surface, meeting most precision casting and optical component quality requirements.
- Relatively Lower Cost: Compared to 125 – 250 Microns ceramic bead sandblasting, it is relatively cheaper.
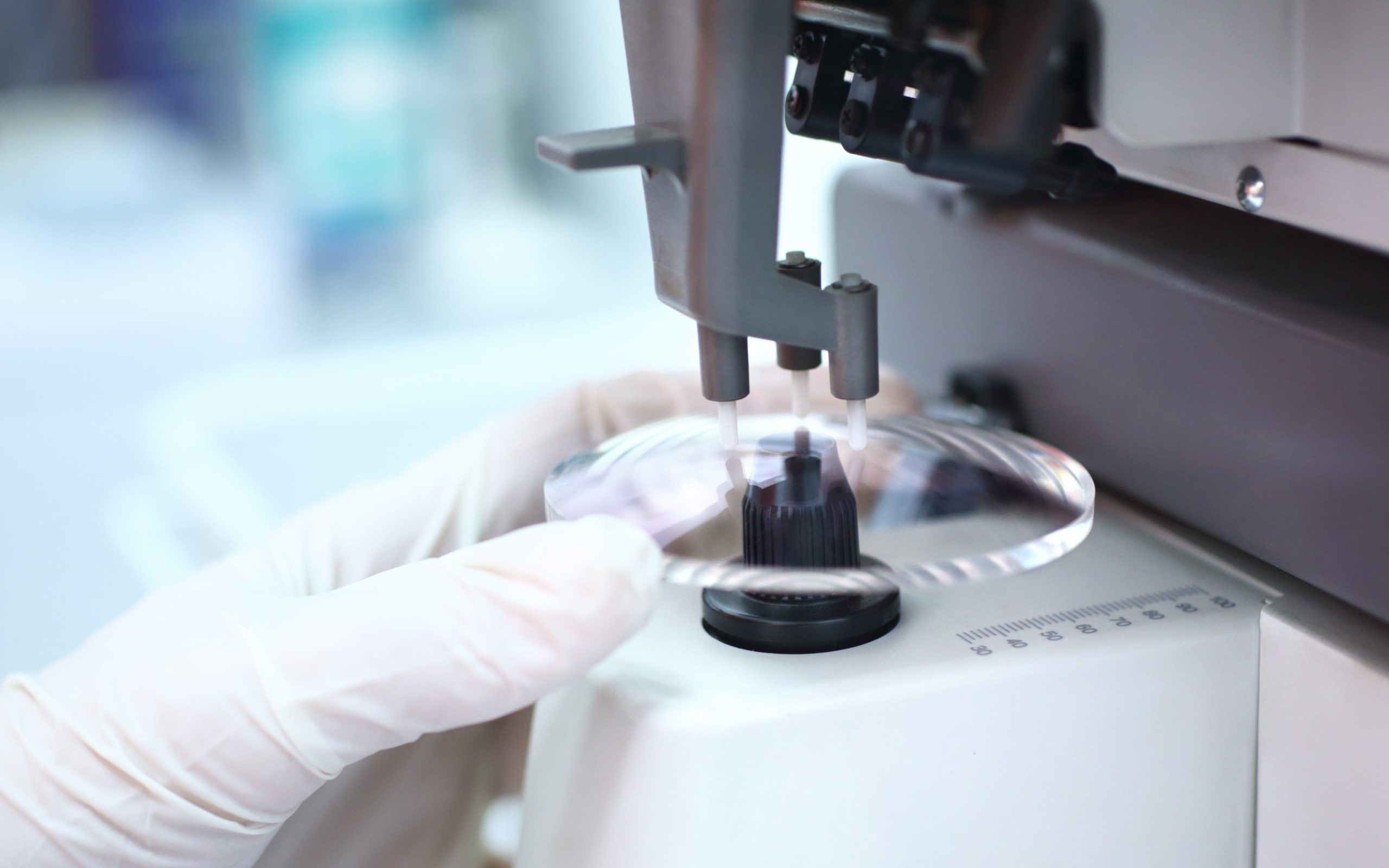
High precision and high quality optical instruments are required
125 – 180 Microns Ceramic Beads Blasting
- Applicable Scenarios
Suitable for surface cleaning and finishing of small precision castings and electronic components. It is a good choice for applications that require high surface quality but do not need to meet the optical component level of surface quality. - Advantages
- High Cleaning Precision: Can remove smaller impurities and burrs, making the workpiece surface smoother.
- Good Finishing Effect: Can create uniform roughness on the workpiece surface, improving appearance quality.
- Moderate Cost: Relatively reasonable price, suitable for most small precision castings and electronic components.
63 – 125 Microns Ceramic Beads Blasting
- Applicable Scenarios
Suitable for surface cleaning and decorative treatment of small metal parts, plastic products, etc. For example, in hardware and plastic products industries, some small parts need surface treatment to improve appearance quality and corrosion resistance. This specification of sandblasting can remove surface oil, dust, and other impurities, while creating a decorative effect on the workpiece surface, making it more attractive. - Advantages
- Good Cleaning Effect: Can remove most impurities, making the workpiece surface cleaner.
- Significant Decorative Effect: Can create unique textures and gloss on the workpiece surface, improving appearance quality.
- Lower Cost: Relatively cheap, suitable for a large number of small parts.
0 – 125 Microns Ceramic Beads Blasting
- Applicable Scenarios
Suitable for fine surface treatment of various materials, such as electronic product shells, medical devices, etc. In these fields, very high surface quality is required, necessitating fine surface treatment to ensure product perfection. This specification of sandblasting can remove extremely fine impurities from the surface, while making the workpiece surface smoother and more delicate, improving product quality. - Advantages
- Extremely High Cleaning Precision: Can remove extremely fine impurities, making the workpiece surface extremely clean.
- Good Surface Quality: Can create a very smooth and delicate surface on the workpiece, improving product appearance quality.
- Wide Applicability: Suitable for fine surface treatment of various materials, including metals, plastics, and ceramics.
45 – 90 Microns Ceramic Beads Blasting
- Applicable Scenarios
Suitable for surface cleaning and finishing of small precision parts, electronic components, etc. It is a good choice for applications with high surface quality requirements but not as high precision as electronic and medical devices. - Advantages
- Higher Cleaning Precision: Can remove smaller impurities and burrs, making the workpiece surface smoother.
- Good Finishing Effect: Can create uniform roughness on the workpiece surface, improving appearance quality.
- Relatively Lower Cost: Compared to 0 – 125 Microns ceramic bead sandblasting, it is relatively cheaper.
0 – 63 Microns Ceramic Beads Blasting
- Applicable Scenarios
Suitable for high-precision electronic products, optical instruments, etc. In these fields, extremely high surface quality is required, necessitating very fine surface treatment to ensure product performance and reliability. This specification of sandblasting can remove extremely fine impurities from the surface, while making the workpiece surface smoother and more even, improving overall quality. - Advantages
- Extremely High Cleaning Precision: Can remove extremely fine impurities and scratches, making the workpiece surface extremely clean.
- High Surface Quality: Can create a very smooth and delicate surface on the workpiece, meeting high-quality requirements.
- Specialized Applicability: Mainly suitable for high-precision fields requiring very high surface quality.
10 – 30 Micron Ceramic Beads Blasting
- Applicable Scenarios
Suitable for surface treatment of ultra-precision electronic products, semiconductor devices, etc. In these fields, there is a high requirement for surface quality, necessitating ultra-fine surface treatment to ensure product performance and reliability. This specification of sandblasting can remove extremely fine impurities on the surface and make the workpiece surface smoother and more even, thereby enhancing the product quality. - Advantages
- High Cleaning Precision: Capable of removing extremely fine impurities, resulting in a very high cleanliness of the workpiece surface.
- Excellent Surface Quality: Can create a very smooth and even surface on the workpiece, meeting the surface quality requirements of ultra-precision electronic products and semiconductor devices.
- Narrow Application Range: Suitable for ultra-precision electronic products and semiconductor devices with extremely high surface quality requirements.
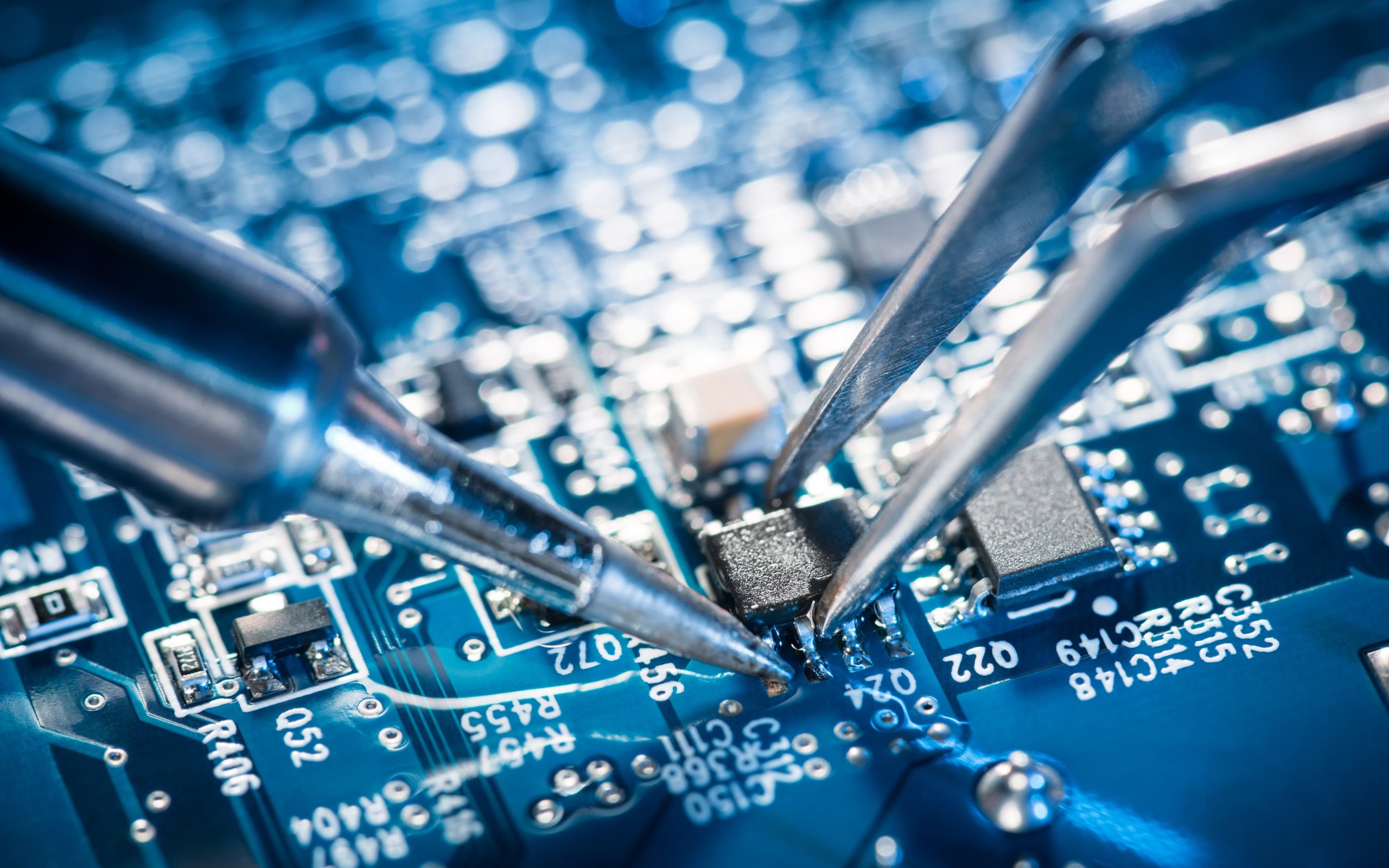
Precision semiconductor
Principles for Choosing Ceramic Beads Blasting
- Based on Workpiece Size: For large workpieces, choose larger particles to improve cleaning efficiency; for small workpieces, choose smaller particles to avoid damaging the workpiece.
- Based on Surface Quality Requirements: If high surface quality is required, choose smaller particles to improve surface smoothness; if surface quality requirements are lower, choose larger particles to enhance cleaning efficiency.
- Based on Material Hardness: For materials with higher hardness, choose larger particles to improve cleaning efficiency; for materials with lower hardness, choose smaller particles to avoid damaging the workpiece.
- Based on Production Cost: Different specifications of ceramic beads blasting vary in price. Choose the appropriate specification based on production cost. Generally, smaller particle ceramic beads are more expensive, while larger particles are cheaper.
Practical Operation and Precautions
In practical operations, ensuring good coordination between equipment and process conditions is key to achieving the desired sandblasting effect. Additionally, understanding common problems and their solutions, as well as mastering techniques to improve sandblasting results, are important factors for successful operation.
Equipment and Process Conditions Coordination
The effectiveness of ceramic beads blasting largely depends on the coordination between equipment and process conditions. Firstly, consider the selection of sandblasting equipment, including blasting pressure, nozzle size, and sandblasting chamber design. Blasting pressure affects the force and speed of sandblasting and should be adjusted based on the hardness and surface condition of the material being treated. The nozzle size should be selected according to the particle size of the sandblasting medium to ensure even blasting results. The design of the sandblasting chamber should ensure good ventilation and dust extraction to avoid dust from affecting the operating environment during the sandblasting process.
Secondly, controlling process conditions is also very important. The operation temperature, humidity, and flow rate of the medium need to be precisely controlled. Excessively high or low temperatures can affect the performance of the sandblasting media, while high humidity can cause medium clumping, affecting sandblasting results. Excessive or insufficient medium flow can affect the uniformity of sandblasting, so adjustments need to be made according to specific conditions.
Common Problems and Solutions
- Uneven Sandblasting: This may be caused by nozzle blockage, nozzle wear, or equipment malfunction. Regularly check and replace nozzles to ensure they are unobstructed; also, maintain and repair equipment to avoid malfunctions affecting the sandblasting effect.
- Unsatisfactory Sandblasting Results: This may be due to improper sandblasting pressure settings, unsuitable sandblasting medium selection, or operational issues. Adjust the sandblasting pressure to the optimal range, choose the appropriate ceramic bead specification, and ensure operators master correct sandblasting techniques.
- Rapid Wear of Sandblasting Medium: This may be related to the settings of sandblasting conditions. Reducing sandblasting pressure and the impact force of the medium can effectively slow down the wear rate. Additionally, regularly replacing and replenishing the sandblasting medium is a necessary maintenance measure.
Tips and Recommendations for Improving Sandblasting Effectiveness
To improve the effectiveness of ceramic bead sandblasting, consider the following tips and recommendations:
- Optimize Sandblasting Parameters: Adjust sandblasting pressure, flow rate, and nozzle angle according to actual needs. Higher sandblasting pressure can increase removal speed but avoid excessive wear.
- Keep Equipment Clean: Regularly clean sandblasting equipment, especially the nozzle and sandblasting chamber, to prevent dust and impurities from affecting sandblasting quality.
- Select Medium Appropriately: Choose the right ceramic bead specification based on the type and requirements of the material being treated. The particle size, hardness, and shape of the medium have a significant impact on sandblasting results.
- Control Sandblasting Environment: Maintain a dry and well-ventilated sandblasting environment to prevent high humidity from affecting the sandblasting media.
By optimizing the coordination of equipment and process conditions, addressing common problems, and employing techniques to improve sandblasting effectiveness, the efficiency and quality of ceramic bead sandblasting can be significantly enhanced.
The selection of ceramic beads blasting specifications should be based on the specific application and surface treatment requirements. The various specifications of ceramic beads each have their own characteristics and advantages, and suitable selection can improve cleaning efficiency, surface quality, and overall cost-effectiveness. Understanding these specifications and their applicable scenarios helps you make better choices in sandblasting process, achieving the desired surface treatment effect and meeting production needs. If you have any questions or need assistance, please feel free to contact us. We will be happy to provide professional advice and solutions.
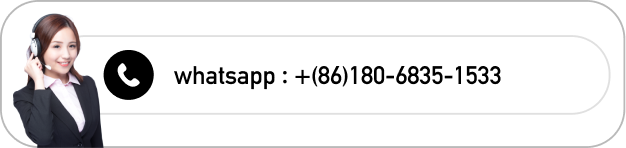