Everything About Ceramic Grit Blasting Beads
August 29, 2024
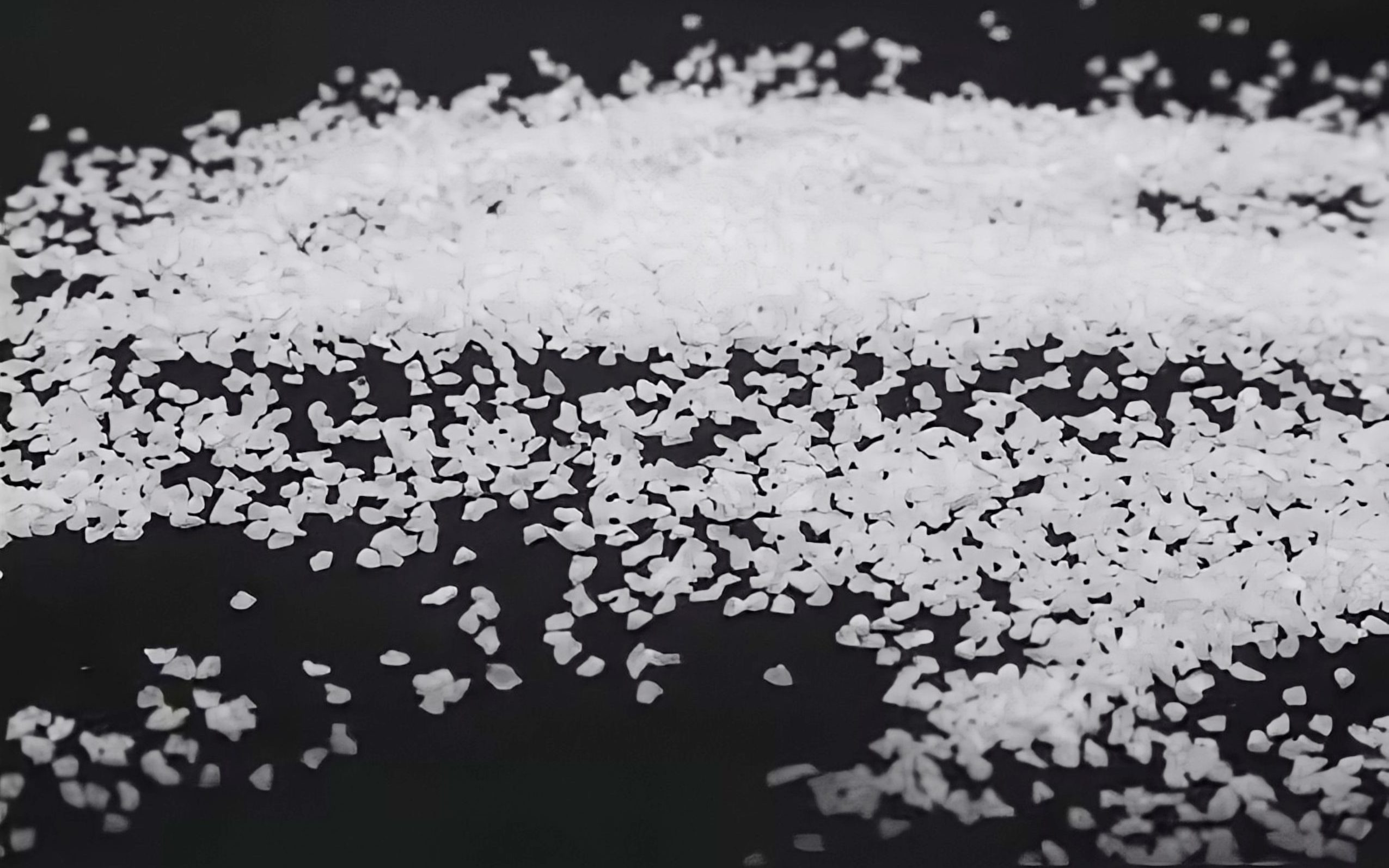
In modern manufacturing, surface treatment processes play a crucial role. Sandblasting technology, as a common surface treatment method, involves the high-speed projection of abrasives onto the surface of a workpiece to achieve cleaning, deburring, or enhancing surface hardness. Among various sandblasting media, ceramic grit blasting beads stand out due to their unique physical properties and superior performance.
Ceramic grit blasting beads and ceramic beads blasting media are similar in composition, mainly consisting of zirconium oxide and silicon dioxide. However, they differ in shape: ceramic grit blasting beads are angular, while ceramic beads blasting media are spherical. This shape difference significantly affects their application performance. This article will explore in detail the composition, manufacturing process, physical characteristics, application areas, advantages, and challenges of ceramic grit blasting beads, and provide best practices and economic benefit analyses to help you better understand this media.
Composition and Manufacturing Process
Composition Analysis
Ceramic grit blasting beads primarily consist of zirconium oxide (ZrO₂), followed by silicon dioxide (SiO₂). This composition endows them with unique advantages in surface treatment.
- Zirconium Oxide (ZrO₂): Provides excellent hardness and wear resistance, enabling the beads to maintain their structure during high-intensity sandblasting processes. It is widely used in applications requiring high durability.
- Silicon Dioxide (SiO₂): Enhances the chemical stability of the beads, providing certain toughness and heat resistance.
Manufacturing Process
The manufacturing process of ceramic grit blasting beads involves three main steps: raw material preparation, shaping, and sintering.
- Raw Material Preparation: High-purity zirconium oxide powder is mixed with silicon dioxide powder in specific proportions. The mixed raw materials are finely processed to ensure uniformity and performance stability of the final beads.
- Shaping: Initial beads are formed using spray drying or other shaping techniques. To achieve the angular structure, molds or special shaping processes are typically used. This shape provides greater cutting force and surface contact area.
- Sintering: The shaped beads are sintered in a high-temperature kiln. The temperature and time control during sintering are crucial for the final hardness and density of the beads. After sintering, the beads are screened and graded to ensure consistency in size and shape.
Characteristics
Shape Analysis
The angular structure of ceramic grit blasting beads offers significant advantages. During sandblasting, angular beads provide greater cutting force and stronger surface cleaning effects compared to spherical beads. Moreover, they are more effective at removing dirt and impurities from complex geometries or hard-to-reach areas.
Key Physical Properties
- Hardness: Ceramic grit blasting beads typically have a hardness of Mohs 7. This high hardness allows the beads to perform well when treating high-hardness materials without causing severe wear.
- Density: Ceramic grit blasting beads generally have a density of 3.8 g/cm³. A higher density means the beads can generate greater impact force during blasting, enhancing the impact on and cleaning effect of the workpiece surface, making them suitable for high-intensity surface treatment tasks.
- Wear Resistance: Due to their high hardness and angular structure, ceramic grit blasting beads exhibit excellent wear resistance. In long-term, high-intensity sandblasting operations, the beads maintain good performance and extend their service life.
Comparison with Ceramic Beads Blasting Media
The main difference between ceramic grit blasting beads and ceramic beads blasting media is their shape. Spherical media are typically used for applications with lower surface requirements, such as deburring or rough surface treatment, while angular beads, due to their greater cutting force and surface contact area, are suited for high-precision and efficient surface cleaning tasks. They also offer better flexibility when dealing with complex shapes or confined spaces.
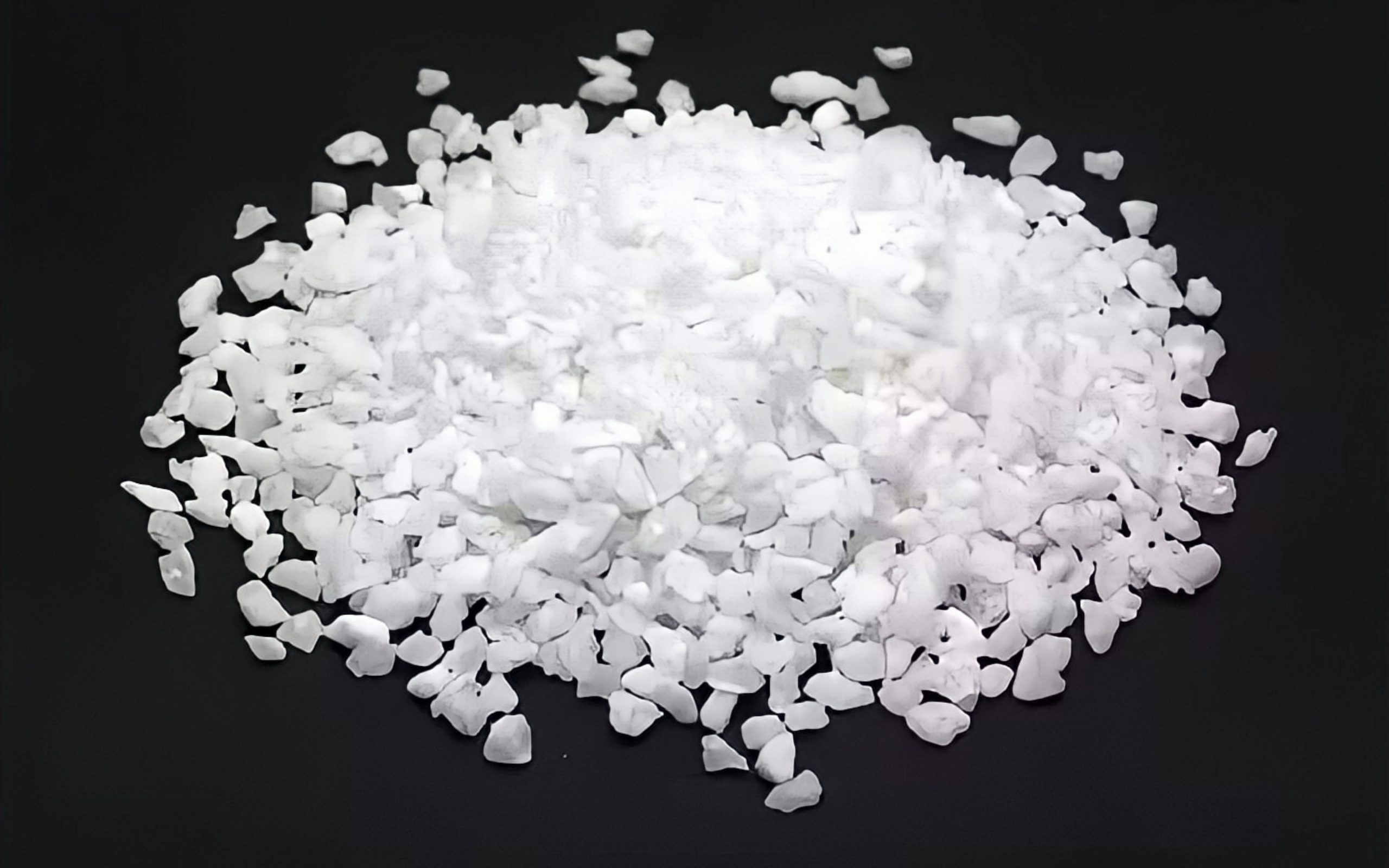
Prismatic ceramic grit blasting beads
Application Areas
Ceramic grit blasting beads are widely used in various industries due to their excellent performance, especially in industries with high surface treatment requirements. Here are some typical application scenarios:
Aerospace
In the aerospace industry, surface treatment of components is crucial for ensuring the safety and performance of aircraft. The high hardness and wear resistance of ceramic grit blasting beads make them an ideal choice for treating critical components like turbine blades and engine casings. These parts are usually made from high-temperature alloys with very high hardness and complex geometries. Ceramic grit blasting beads can remove oxide layers and other impurities without damaging the workpiece surface, providing a good foundation for subsequent processing.
Consumer Electronics
In the manufacturing of consumer electronics, such as smartphones, tablets, and laptops, the quality of surface treatment directly affects the product’s appearance and durability. Ceramic grit blasting beads are used to clean and enhance the surfaces of metal housings, providing better adhesion and aesthetic appeal. Additionally, in the manufacture of microelectronic components, ceramic grit blasting beads can remove fine burrs and residues, ensuring the precision and reliability of components.
Military
Military equipment requires stringent surface treatment standards. Ceramic grit blasting beads are widely used for surface treatment of tank armor, weapon components, and other military equipment to effectively remove rust, coating residues, and provide a smooth surface for new coatings. Their efficient cleaning effect and long service life make them an indispensable material in the military industry.
Automotive Manufacturing
In automotive manufacturing, surface treatment of vehicle bodies and engine components is crucial. Ceramic grit blasting beads are used to clean surfaces of body panels, aluminum wheels, and other metal parts. They can remove oxide layers and impurities, providing a smooth and even surface for subsequent painting and coating. Additionally, the durability of ceramic grit blasting beads helps reduce production costs and improve efficiency.
Application Case Studies
Case 1: Aerospace Industry
- Background: Boeing needed to process a large number of turbine blades and engine casings, requiring the removal of oxide layers and impurities without damaging the workpieces.
- Application: Ceramic grit blasting beads were used for sandblasting treatment. Their high hardness and cutting force successfully removed surface oxide layers while maintaining geometric precision.
- Effect: The surface quality of the workpieces was significantly improved, and the adhesion of coatings in subsequent processing steps was significantly enhanced, increasing production efficiency by 20%.
Case 2: Consumer Electronics Industry
- Background: Apple needed to treat the metal housings of its smartphones to enhance product appearance and durability.
- Application: Ceramic grit blasting beads were used to clean and enhance the surfaces of metal housings, improving coating adhesion and aesthetics.
- Effect: The product appearance became smoother and more consistent, with consumer satisfaction regarding the product’s appearance increasing by 15%.
Case 3: Military Industry
- Background: Lockheed Martin needed to treat tank armor surfaces, removing rust and old coatings and providing a smooth surface for new coatings.
- Application: Ceramic grit blasting beads were chosen for sandblasting treatment, effectively removing old rust and coatings and providing a good base for new coatings.
- Effect: The quality of armor surface treatment was significantly improved, and the adhesion and durability of new coatings were significantly enhanced, reducing maintenance costs.

An armored tank that requires precise parts to be assembled
Advantages and Challenges
Advantages
- Efficient Surface Cleaning: The angular structure of ceramic grit blasting beads provides greater cutting force and surface contact area, allowing for more efficient removal of surface contaminants and impurities.
- Long Service Life: High hardness and wear resistance ensure excellent performance over prolonged use, reducing replacement frequency and thus lowering operational costs.
- Strong Adaptability: Ceramic grit blasting beads can adapt to various complex shapes and materials, particularly excelling in treating high-hardness and complex geometrical workpieces.
Challenges
- Equipment Wear: The high hardness of ceramic grit blasting beads, while enhancing cleaning efficiency, can accelerate wear on sandblasting equipment over time. Therefore, equipment maintenance and component replacement become critical issues.
- Bead Loss: During sandblasting, the angular structure of ceramic grit blasting beads may lead to higher breakage rates, affecting their service life and cleaning effectiveness. Regular monitoring of bead condition and appropriate recovery and replacement are necessary.
How To Achieve the Best Results?
1. Choosing the Right Specification
Selecting the appropriate ceramic grit blasting bead specification is crucial for achieving the best sandblasting results. The size, shape, and hardness of the beads should match the material and surface treatment requirements of the workpiece. Generally, larger beads are suitable for coarse surface treatments, while smaller beads are used for fine processing. Below are the three specifications of our ceramic grit blasting beads and their respective functions:
F120 63-125 Microns
- Advantages
- High Cleaning Efficiency: Larger bead size provides stronger impact force, suitable for removing thick coatings, rust, or stubborn impurities.
- Wide Application Range: Capable of processing various materials, including metals and concrete, with significant effects.
- Lower Wear Rate: Larger beads usually do not excessively wear equipment during surface treatment, extending equipment life.
- Usage Scenarios
- Heavy Cleaning: Used for treating thick coatings and rust, such as large machinery parts and engineering equipment.
- Casting Part Processing: Suitable for cleaning and deburring castings, especially in casting and metalworking industries.
- Surface Preparation: Pre-treating rough surfaces before spraying or coating to improve subsequent coating adhesion.
F170 45-90 Microns
- Advantages
- Uniform Cleaning Effect: Medium-sized beads provide uniform cleaning effects, suitable for medium-thickness coatings and impurities.
- Efficient Surface Processing: Balances cleaning effectiveness and bead consumption, applicable to a broad range of applications.
- Lower Dust Generation: Compared to larger beads, F170 produces less dust during processing, improving the work environment.
- Usage Scenarios
- Fine Surface Treatment: Used in automotive manufacturing, electronics, etc., for cleaning thin coatings or fine impurities.
- Standard Cleaning: Suitable for various standard cleaning applications, such as treating general metal surfaces and removing light rust.
- Surface Preparation for Painting: Effective for preparing surfaces for painting or coating, ensuring a smooth and clean base.
F20 50-63 Microns
- Advantages
- High Precision: Small bead size provides precise cleaning effects, suitable for detailed work and precision parts.
- Good Surface Finish: Capable of achieving a high-quality surface finish, improving the appearance and functional quality of the workpiece.
- Reduced Equipment Wear: Smaller beads result in less wear on equipment, extending its service life.
- Usage Scenarios
- Precision Parts Cleaning: Used for treating small or delicate parts in electronics, aerospace, etc.
- Surface Enhancement: Suitable for enhancing surface quality, such as removing fine burrs and achieving a smooth finish.
- Micro-Processing: Ideal for processing small workpieces or intricate parts, where precision and surface quality are crucial.
2. Optimization of Operating Conditions
To maximize the effectiveness of ceramic blasting beads, it is essential to optimize the operating conditions during the blasting process. This includes factors such as blasting pressure, blasting angle, and blasting time. Appropriate blasting pressure ensures that the beads effectively impact the surface of the workpiece, while the correct blasting angle and time help avoid excessive wear and uneven treatment. (You can refer to this article)
3. Equipment Maintenance and Bead Recovery
Regular maintenance of the blasting equipment is crucial to ensure its long-term stable operation. It is necessary to regularly check for wear and tear on the equipment and replace worn parts promptly. Additionally, the recovery and reuse of beads also help to reduce costs and minimize waste. By properly screening and cleaning, used beads can be effectively recovered, extending their service life.
Economic Benefits and Environmental Friendliness
Cost-Effectiveness Analysis
The initial cost of ceramic blasting beads is higher, but their excellent abrasion resistance and long lifespan allow for a reduction in unit costs over time. Compared to other blasting media, ceramic blasting beads offer significant economic advantages in large-scale production due to their efficient cleaning effect and extended service life. Specifically, overall production costs can be significantly reduced by decreasing the frequency of replacements and maintenance costs.
Environmental Friendliness Discussion
Due to their main components being zirconia and silica, which have minimal environmental impact during production and use, ceramic blasting beads also perform well in terms of environmental friendliness. Additionally, they are easy to recycle and reuse, which helps reduce waste and lower the environmental burden. The low dust generation during use also contributes to a better working environment. Furthermore, the introduction of eco-friendly production processes and materials can further enhance their environmental performance.
Future Development Trends
Technological Advancements
With advancements in material science and manufacturing technology, the production processes and performance of ceramic blasting beads are expected to improve further. The application of new ceramic materials and more refined manufacturing techniques will make ceramic blasting beads more efficient and economical.
Market Demand
As industrial applications continue to expand, the market demand for ceramic blasting beads is also growing. In the future, new emerging industries and application scenarios will drive market development, such as the new energy industry and high-tech fields.
Environmental Protection and Sustainable Development
Against the backdrop of increasingly strict environmental regulations, the production and use of ceramic blasting beads will focus more on environmental protection and sustainable development. Future developments may include reducing environmental impacts during production and increasing the recycling rate of the beads.
Ceramic grit blasting beads, with their unique angular shape and high hardness, offer numerous advantages for surface treatment applications. They provide efficient cleaning, long service life, and adaptability to various materials and complex geometries. Despite some challenges such as equipment wear and bead loss, proper selection, maintenance, and optimization can maximize their benefits. In industries such as aerospace, consumer electronics, military, and automotive manufacturing, ceramic grit blasting beads play a crucial role in achieving high-quality surface treatments and improving overall production efficiency. Their economic benefits, including cost-effectiveness and increased efficiency, make them a valuable choice for various surface treatment tasks.
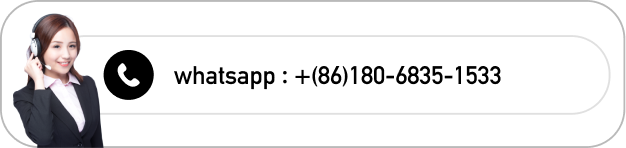