Choosing the right size of cryogenic deflashing: improving product quality and safety
September 25, 2024
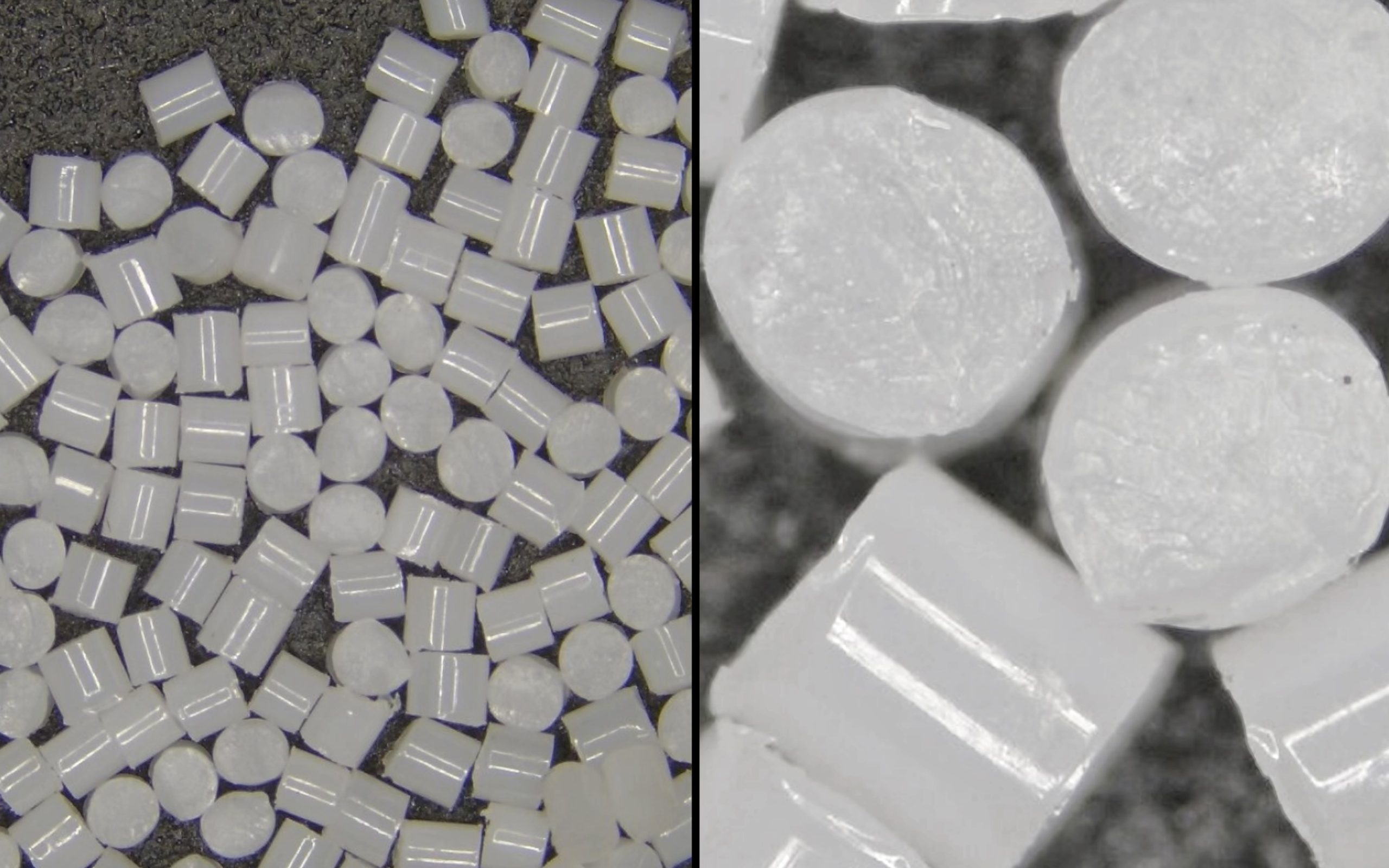
In industrial manufacturing, burrs are a common problem. Burrs not only affect the appearance of products, but may also cause serious safety hazards. For example, in recent years, several mobile phone brands have been recalled due to battery short circuits or explosions. After investigation, it was found that some of these cases were directly related to burrs on internal components. These negative events not only caused huge economic losses, but also seriously affected the brand reputation and made consumers question the safety of the products. Therefore, the importance of deflashing cannot be underestimated.
Deflashing is indeed a key step to ensure product quality and safety, especially when manufacturing products involving electronic components. Through an effective deflashing process, problems such as short circuits and poor contact caused by burrs can be avoided, thereby improving the reliability and service life of the product. In addition, the surface finish of the workpiece can be improved, the overall aesthetics can be improved, and the market competitiveness of the product can be enhanced.
After recognizing this problem, choosing the right deflashing media and technology is what needs to be studied. Whether it is for plastics, metals or composite materials, different types of deflashing media have different effects on deflashing effects, applicable materials and process requirements. This article will focus on introducing the different sizes of cryogenic deflashing media for you. Choosing the right media size not only affects the quality of deflashing, but also directly affects production efficiency and cost. Too large a size may lead to uneven deflashing and damage the surface of the part; too small a size may reduce the deflashing efficiency. Therefore, the correct choice of media size can help customers improve production efficiency, reduce defective rates, and ensure product quality.
Industry classification and demand
Aerospace: Precision rubber seals and connectors
The aerospace industry has extremely high requirements for component precision, especially the application of soft materials such as rubber seals, plastic connectors, and cable sheaths. These components usually require high elasticity, high heat resistance, and high strength of the material, but burrs are prone to occur during the production process, which in turn affects the sealing and overall performance. To ensure the reliability and safety of aerospace equipment, the aerospace field mostly uses small-sized media, such as PC-40 (0.4mm) and PC-50 (0.5mm), which can effectively handle burrs on the surface of parts without damaging soft materials.
Automotive industry: Rubber seals and interior parts
In the automotive industry, rubber and plastic materials are widely used in components such as door seals, engine seals, interior parts, and headlight housings. These parts not only need to maintain good durability during use but also meet stringent airtightness and surface finish requirements. For example, the airtightness of the door seal is crucial to the vehicle’s waterproof, windproof, and soundproof functions. Medium-sized media, such as PC-75 (0.75mm) and PC-100 (1.0mm), are particularly suitable for removing burrs on these complex-shaped parts to ensure their smooth and flawless surfaces.
3D Digital Electronics: Small Plastic Components and Flexible Connectors
The development of 3D printing technology and the digital electronics industry has promoted the large-scale application of small plastic components and flexible connectors, which are usually complex and delicate and require extremely high surface accuracy. In particular, flexible circuit boards, small plastic packages, and parts with complex geometries must be deburred accurately to every detail. Small-sized media such as PC-40 (0.4mm) and PC-50 (0.5mm) can penetrate the fine structures of these parts, effectively remove burrs, and ensure high precision and damage-free parts.
Application Guide for Different Sizes
PC–40 (0.4mm)
- Aerospace: Small seals (O-rings)
- Material: Polyurethane or Silicone
- Effect: Ensure airtightness and liquid sealing, remove tiny surface burrs, and improve sealing performance.
- Automotive: Small rubber seals, such as window seals
- Material: EPDM or Neoprene
- Effect: Prevent water and air infiltration, and ensure sealing and durability.
- 3D Digital Electronics: Small housing components for 3D printing
- Material: PLA or ABS plastic
- Effect: Improve surface smoothness and appearance, and ensure good fit with other parts.
PC–50 (0.5mm)
- Aerospace: Edge treatment of lightweight composite structural parts
- Material: Carbon fiber or glass fiber
- Effect: Remove burrs, ensure structural strength and surface smoothness.
- Automotive: Small interior plastic parts
- Material: Polypropylene or ABS
- Effect: Improve appearance, remove burrs to increase comfort.
- 3D digital electronics: Small sensor housings
- Material: Nylon or polyester
- Effect: Ensure the housing is airtight and durable.
PC–75 (0.75mm)
- Aerospace: Sealing gaskets
- Material: Polymers (such as PTFE)
- Effect: Ensure good sealing performance and remove surface burrs to prevent leakage.
- Automotive: Fuel system components (such as fuel pump housings)
- Material: Polycarbonate or nylon
- Effect: Remove burrs to prevent fuel leakage and ensure smooth flow.
- 3D digital electronics: 3D printed connectors
- Material: PLA or PETG
- Effect: Improve connection stability and ensure smooth signal transmission.
PC–100 (1.0mm)
- Aerospace: Medium-sized composite parts (such as deflectors)
- Material: Carbon fiber composites
- Effect: Remove surface defects to ensure aerodynamic performance and strength.
- Automotive: Dashboards and door trim panels
- Material: ABS or PVC
- Effect: Improve appearance quality and remove burrs to enhance comfort.
- 3D digital electronics: Medium-sized housing components
- Material: Polyamide or polycarbonate
- Effect: Improve overall stability and durability.
PC–120 (1.2mm)
- Aerospace: Large composite structural parts (such as wing brackets)
- Material: Aluminum alloy or carbon fiber
- Effect: Remove burrs to ensure structural strength and safety.
- Automotive: Medium-sized seals (such as engine cover seals)
- Material: EPDM or polyurethane
- Effect: Ensure engine compartment sealing and reduce noise and vibration.
- 3D digital electronics: Large-sized flexible circuit board housings
- Material: Polyester or polyimide
- Effect: Ensure signal stability and ensure housing durability.
PC–150 (1.5mm)
- Aerospace: Large seals
- Material: Fluororubber or polyurethane
- Effect: Suitable for high-strength parts to ensure good sealing performance.
- Automotive: Large interior parts
- Material: Polypropylene or ABS
- Effect: Remove burrs to improve appearance quality and comfort.
- 3D digital electronics: Large-size 3D printed parts
- Material: PLA or PETG
- Effect: Improve appearance and function, and ensure the strength of the parts.
PC–200 (2.0mm)
- Aerospace: Heavy composite structural parts
- Material: Aluminum alloy or carbon fiber composite
- Effect: Remove rough surfaces to ensure structural integrity and safety.
- Automotive: Large rubber seals (such as door seals)
- Material: EPDM or neoprene
- Effect: Ensure good sealing and durability.
- 3D digital electronics: Large electronic component housings
- Material: Polycarbonate or ABS
- Effect: Ensure component safety to avoid potential electrical failures.
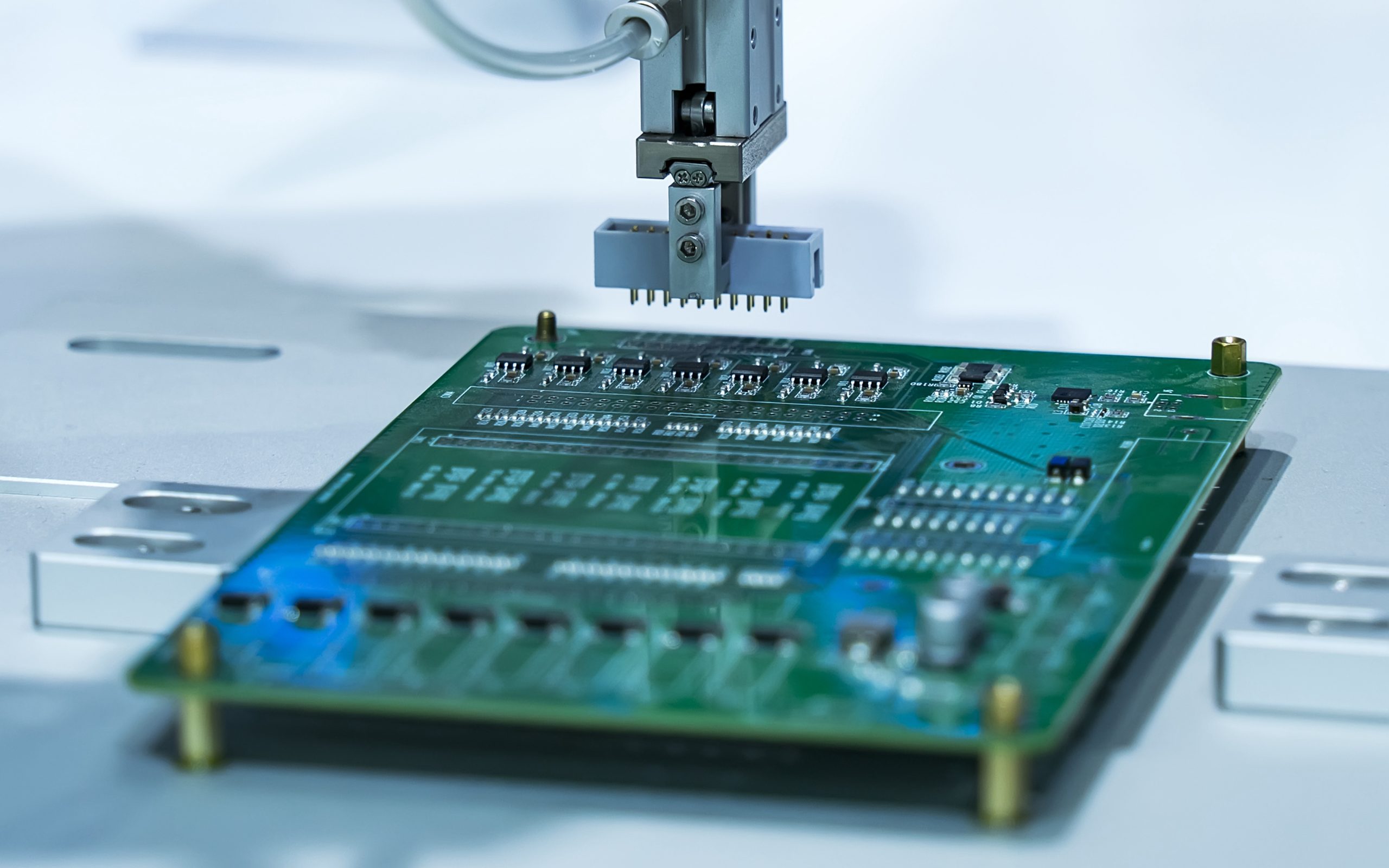
Precise circuit board
Media Combination
Sometimes a workpiece requires two or more different media to be polished together. This situation usually occurs in the following situations:
- Different process requirements: Some workpieces may need to use one medium to remove large burrs or rough surfaces during processing, and then use another finer medium for fine grinding. For example, the initial deflashing of automotive parts may use a larger cryogenic deflashing media, and then use a smaller medium for surface smoothing.
- Material properties: Workpieces of different materials may require different types of media when deflashing. For example, composite structural parts in aerospace may be treated with cryogenic deflashing media to maintain their structural strength, and then other abrasive materials (such as ceramic or plastic media) are used for more detailed surface treatment.
- Optimization effect: Using a combination of media can achieve better processing results. Different media can complement each other, cryogenic deflashing media provide burr removal, while other media can provide better surface finish or specific surface characteristics.
- Complex shape: For workpieces with complex shapes, a single medium may not be able to fully achieve the desired effect. Combining media can ensure that each part is properly processed.
[Friendly reminder]
Usually, the pre-treated workpiece itself has various conditions, and the surface treatment may not be completed by only one medium. Therefore, we will provide customers with customized deflashing solutions. You can contact us through the phone on the upper right side of the page or directly click the blue button “Get a Quote” and send us your workpiece samples. We will evaluate according to your requirements, workpiece quality, workpiece material, and other factors, and use the most time-saving and labor-saving method to complete the surface treatment and then deliver it to you. We have a reliable supply chain and strong technical support to escort your production plan.
Give some specific examples:
Composite structural parts in aerospace
- Workpiece type: wing bracket
- Combined media: cryogenic deflashing media + ceramic grinding media
- Reason: After the initial removal of large burrs, ceramic media is used to improve surface smoothness and ensure aerodynamic performance.
Fuel system components in automobiles
- Workpiece type: fuel pump housing
- Combination media: cryogenic deflashing media + plastic abrasive media
- Reason: First remove burrs to ensure fluid flow, then use plastic media to improve surface finish to prevent fuel leakage.
Seals in medical devices
- Workpiece type: polyurethane seals
- Combination media: cryogenic deflashing media + fine abrasives
- Reason: After initial treatment to remove burrs, fine abrasives are used to improve biocompatibility and sealing performance.
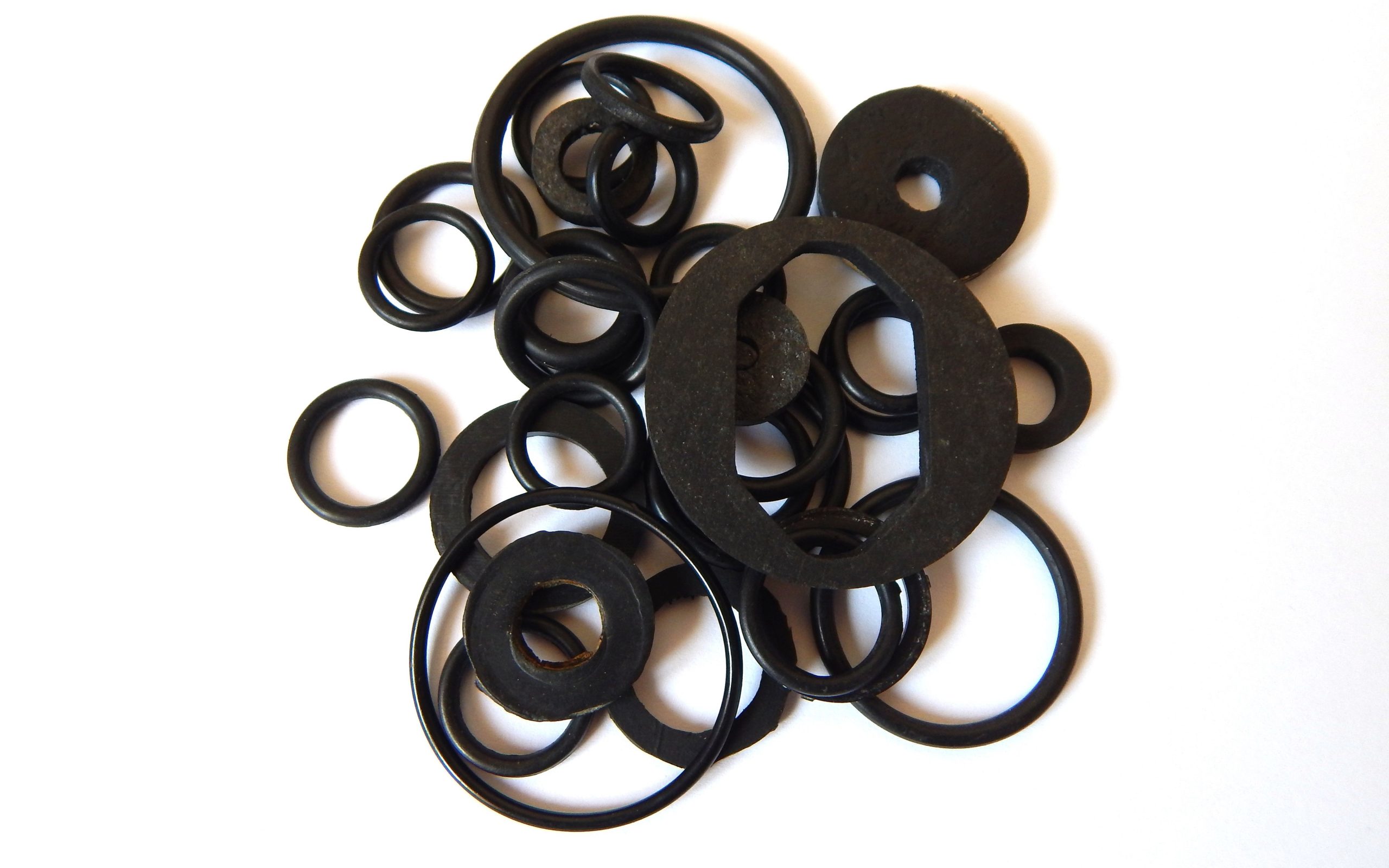
o-ring
Equipment introduction
In addition to selecting the appropriate media size, the choice of equipment is also a key factor in ensuring the quality of deflashing. The following introduces 4 machines suitable for this media.
- Liquid nitrogen cryo-finishing machine
A liquid nitrogen cryo-finishing machine is the most commonly used cryogenic deflashing equipment. Liquid nitrogen is used to cool the workpiece to an extremely low temperature, making the material surface brittle, and then the burrs are removed by mechanical friction of the media. Advanced deflashing equipment is usually equipped with an automated control system that can accurately control the part material and media size to ensure efficient deflashing.
Advantages:
- Automated control: Precisely control temperature and vibration frequency to ensure consistent deflashing.
- Versatility: Suitable for different materials and parts, including plastics, metals, and composite materials. From small precision parts to large structural parts, they can be processed efficiently.
- Environmental protection: Use liquid nitrogen cooling, no pollution, and more in line with environmental standards.
- Vibration deflashing machine
The workpiece and abrasive are mixed through vibration, and the burrs are removed by friction. It can be combined with cryogenic deflashing media to enhance the deflashing effect.
Advantages:
- Uniformity: It can ensure uniform deflashing of the workpiece surface, which is suitable for mass production.
- Versatility: Deflashing and surface smoothing can be performed at the same time, saving time.
- Application scenarios: Suitable for mass production of automotive parts and electronic components, especially workpieces with complex shapes.
- Sand blasting machine
Use compressed air to spray cryogenic deflashing media at high speed onto the workpiece surface to remove burrs and impurities. The spray pressure and medium particle size can be adjusted to adapt to different workpieces.
Advantages:
- Efficient removal: suitable for removing large or hard burrs with significant results.
- Diverse applications: can be used for a variety of materials such as plastics and metals, and can be widely processed.
- Application scenarios: in industries such as aerospace, automobiles, and electronic manufacturing, it processes engine parts, housing components, etc.
- Ultrasonic cleaning machine
Using high-frequency sound waves to generate tiny bubbles in the liquid, when the bubbles burst, a strong impact force is generated, which can remove tiny burrs on the surface of the workpiece.
Advantages:
- Meticulous: suitable for workpieces with complex geometries, ensuring that every detail is processed.
- Environmentally friendly cleaning: using water-based solutions to reduce the impact on the environment.
- Application scenarios: mainly used in industries such as medical devices and electronic components to process small or precision workpieces.
In today’s highly competitive industrial manufacturing environment, burr removal is not only the key to improving product quality, but also a necessary step to ensure safety and reliability. We strive to provide customers with comprehensive solutions through application guides and equipment introductions for different sizes of media. If you have more questions about cryogenic deflashing media and their applications, please feel free to contact us. We will wholeheartedly provide you with professional advice and customized solutions to help your production plan go smoothly.
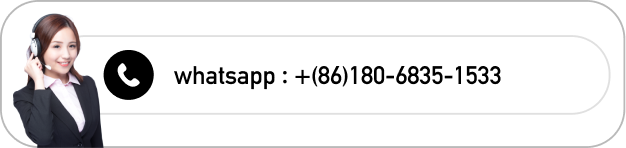