Ceramic vs Glass Beads for Mold Finishing
February 7, 2025
In the competitive world of mold manufacturing, surface finishing quality directly impacts product performance and production efficiency. However, many Indian manufacturers face persistent challenges with traditional glass beads, such as high defect rates, excessive dust, and frequent maintenance issues.
This report dives into the key reasons why ceramic blast beads are becoming the preferred choice for mold cleaning, backed by performance data, technical insights, and real-world case studies.
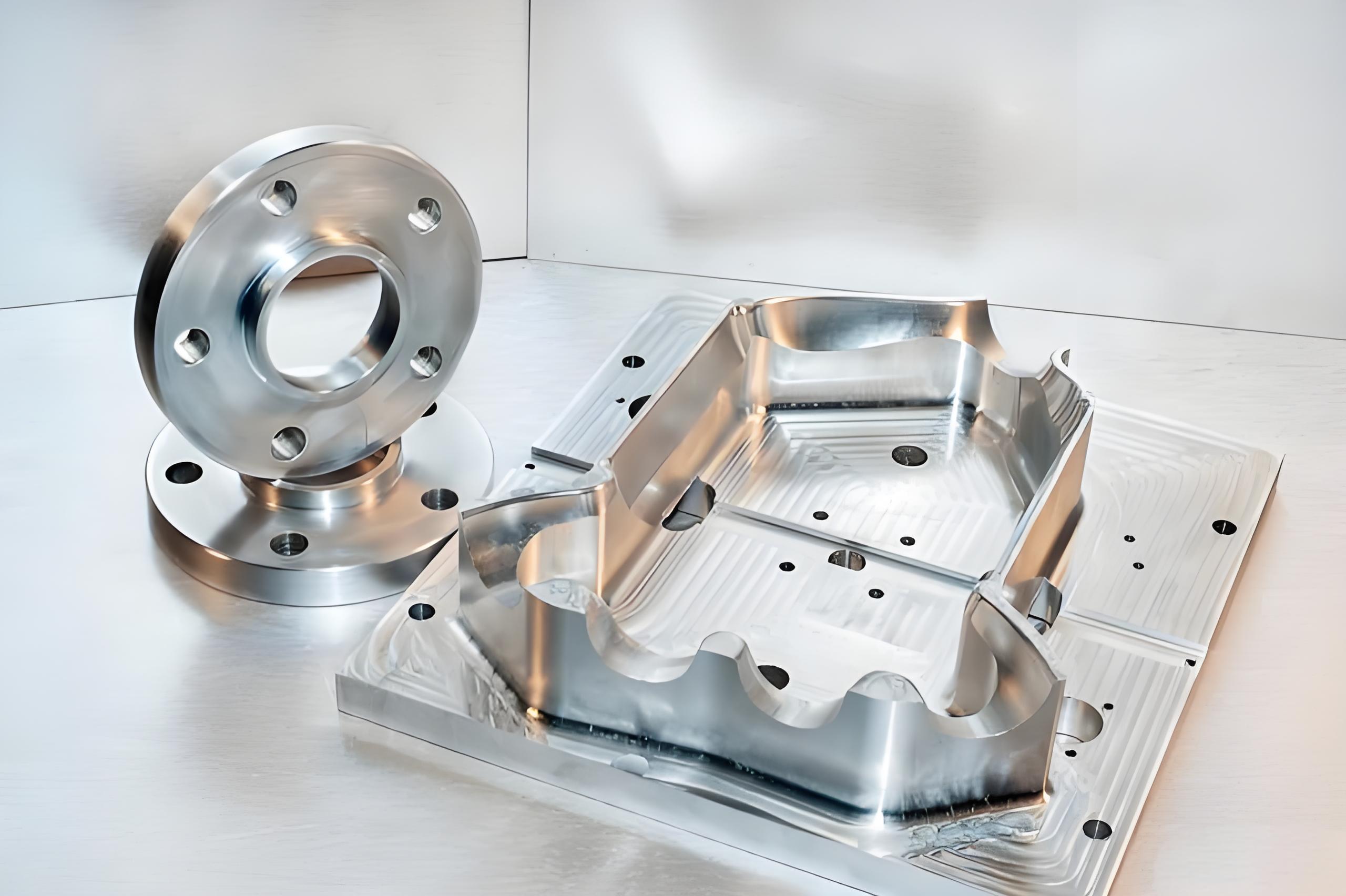
Performance Comparison: Glass Beads vs. Ceramic Beads
To understand why ceramic beads outperform glass beads, let’s examine six critical performance metrics:
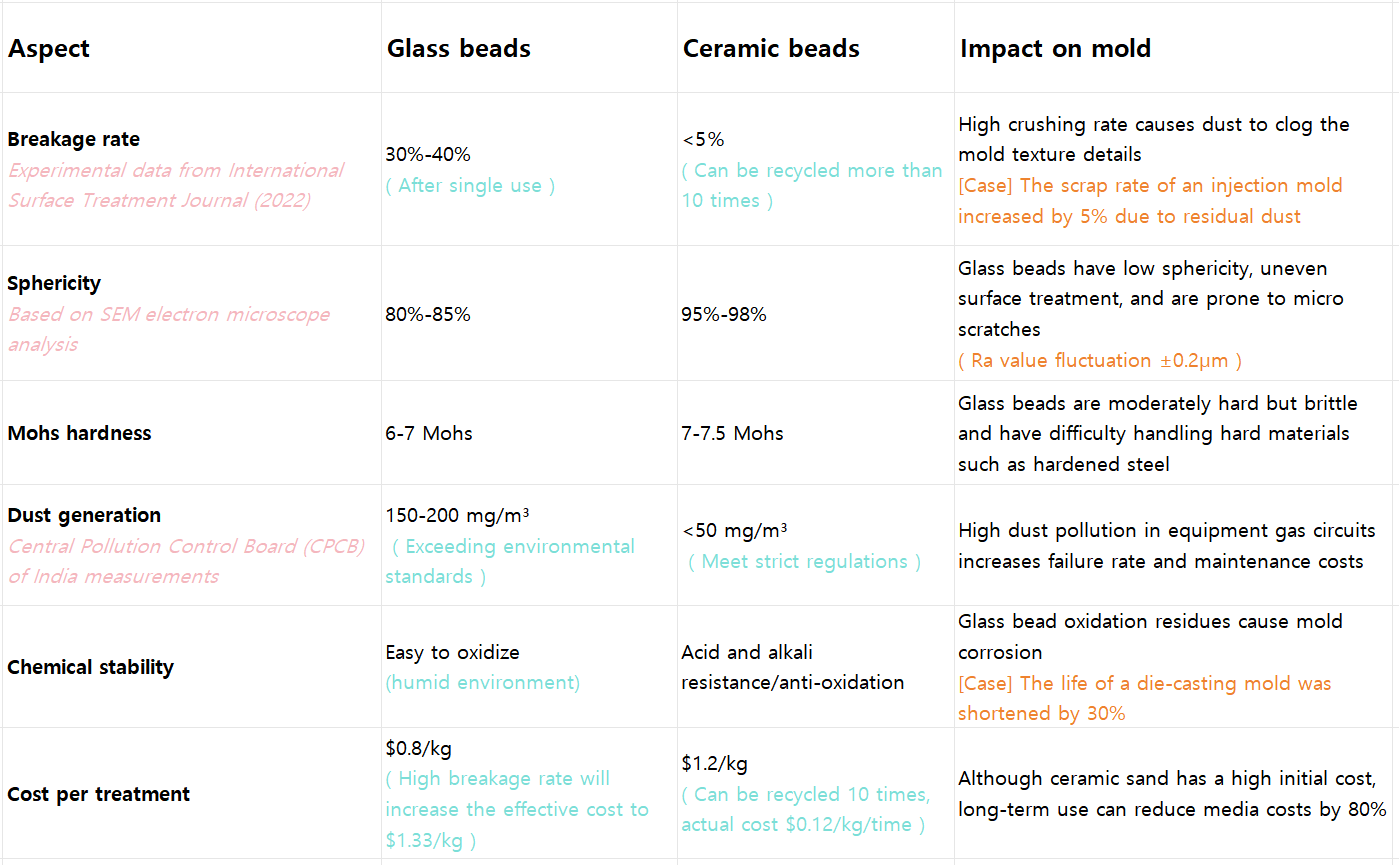
Technical Principles: How Media Properties Affect Mold Finishing
Breakage Rate and Mold Cleanliness
Glass beads shatter into fine dust (<10µm), which embeds into mold pores, causing sticking and defects. In contrast, ceramic beads’ toughness-enhanced abrasives (composed of zirconia and alumina) minimize breakage, ensuring cleaner molds and longer lifespans.
Sphericity and Surface Contact Mechanics
Glass beads’ lower sphericity (80%-85%) leads to uneven pressure distribution, creating micro-scratches. Ceramic beads’ near-perfect sphericity (95%-98%) ensures uniform particle distribution, protecting mold geometry and achieving consistent Ra values.
Hardness and Material Compatibility
While glass beads (6-7 Mohs) are suitable for softer materials, they fail on hardened steels. Ceramic beads (7-7.5 Mohs) strike a balance between hardness and toughness, making them ideal for a wide range of materials, from aluminum to titanium alloys.
Chemical Stability and Mold Longevity
Glass beads oxidize in humid environments, leaving corrosive residues. Ceramic beads’ chemical stability ensures no contamination, extending mold life and reducing maintenance costs.
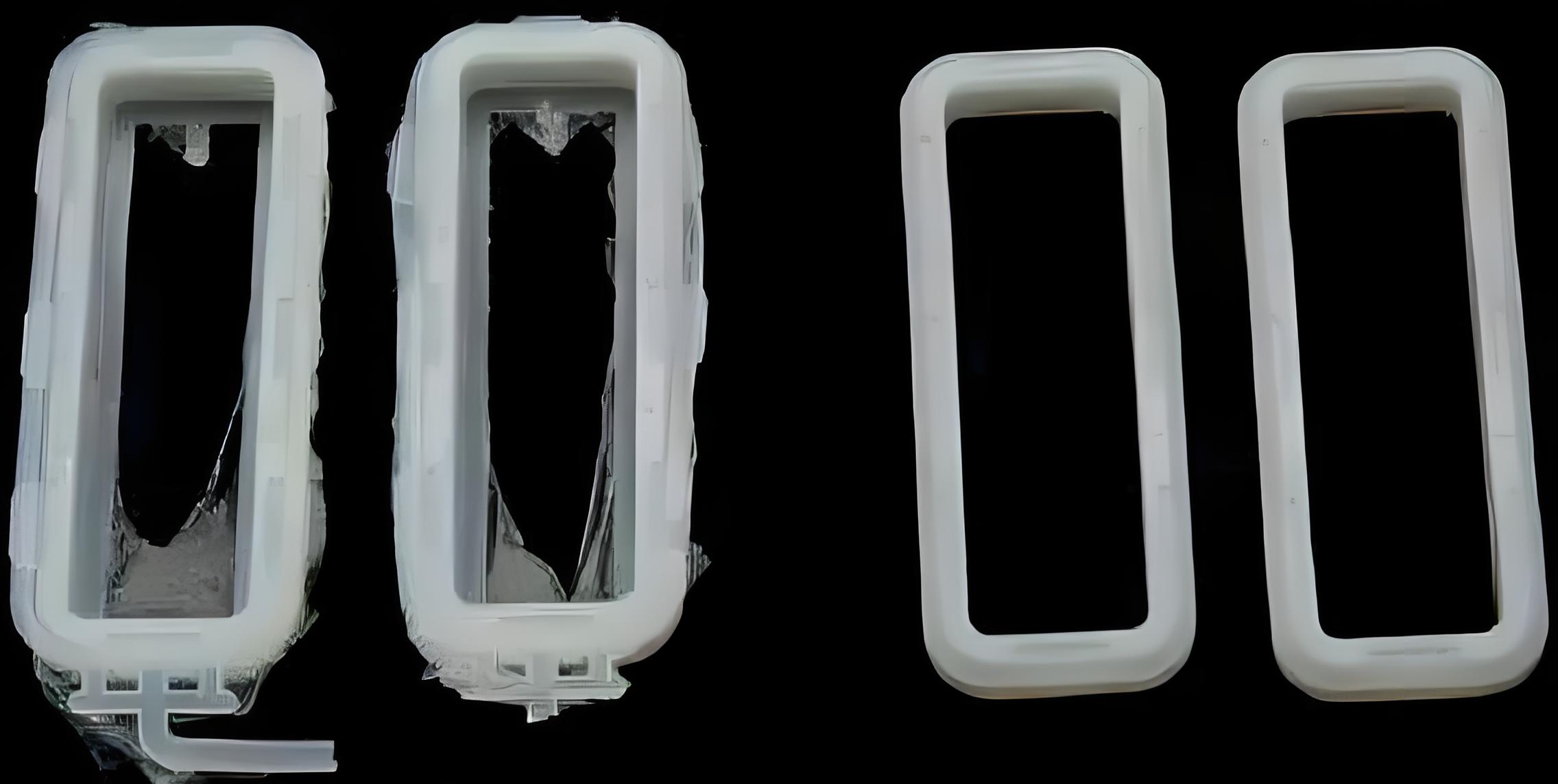
How Ceramic Beads Adapt to Different Mold Materials
Plastic Molds (e.g., Injection Molds)
Plastic molds are relatively soft, and even a slight scratch may affect the demolding effect or the quality of the finished product.
Ceramic beads can effectively reduce the impact force and avoid scratches with its perfect sphericity, while providing a uniform polishing effect. By adjusting the sandblasting pressure (50-80 PSI), precise control can be achieved to perform gentle polishing suitable for plastic molds.
In addition, the low dust characteristics of ceramic bead blasting reduce the embedding of particles into the mold pores to avoid affecting demolding.
Aluminum Molds (e.g., Die Casting Molds)
Aluminum alloy molds are prone to oxide layers and burrs, but the material is relatively soft, and the hardness and impact force of the medium must be controlled during cleaning.
Ceramic bead blasting has a moderate hardness, higher than glass beads but lower than corundum media, and can effectively remove defects without damaging the mold surface. Its spherical structure ensures uniform force and achieves a uniform surface finish. At the same time, it has high chemical stability, does not react with aluminum alloys, and does not leave any pollutants.
Stainless Steel Molds (e.g., Precision Stamping Molds)
Stainless steel molds are often used in industries such as precision stamping and medical device manufacturing. The surface needs to be highly clean and free of chemical pollution.
Ceramic beads can effectively remove welding slag, oxide scale and stubborn stains under 80-120 PSI sandblasting pressure, while avoiding microcracks or surface deformation. Its high wear resistance and recyclability reduce the cost of consumables and are suitable for mass production needs.
Titanium Alloy Molds (e.g., Aerospace Components)
The aerospace field has extremely high requirements for the surface of titanium alloy molds. The high hardness of ceramic bead blasting can remove the oxide layer, while having good toughness to prevent microcracks. Its high temperature resistance ensures stable performance in extreme environments, and there is no chemical residue, which meets the standards of the aerospace industry.
Rubber Molds (e.g., Tire Molds)
Rubber molds are prone to accumulate residues and release agents, which affect the service life and quality of the finished product.
The low impact force of ceramic beads ensures gentle cleaning and avoids mold damage. Its spherical structure improves fluidity, helps to thoroughly remove fine residues, and improves demolding efficiency. In addition, ceramic bead blasting is low in dust, environmentally friendly, and reduces equipment maintenance costs, making it an ideal choice for eco-friendly blasting.
Customer Case Studies: Real-World Results
Case 1
Problem:
An Indian automotive mold manufacturer had an ongoing problem with its bumper molds – glass bead blasting left dark spots on the mold surface, resulting in a high defect rate of 12%. These defects affected the appearance of the final product and increased rework costs.
Solution:
To improve surface consistency and durability, the manufacturer switched to B120 ceramic beads, which offer excellent hardness and recyclability. Through an optimized blasting process, the ceramic beads were reused 10 times, ensuring a more uniform surface finish without compromising the integrity of the mold.
Results:
After switching to ceramic beads, the surface roughness stabilized at Ra = 0.8µm ± 0.05, significantly reducing visual inconsistencies. As a result, the defect rate dropped from 12% to only 2%, reducing waste and rework. In addition, the increased reusability and efficiency of the ceramic beads saved $18,000 per year and improved overall production profitability.
Case 2
Problem:
A leading supplier of precision electronic connector molds encountered a major challenge – glass bead dust was clogging complex pin molds. This contamination affected mold performance and required frequent cleaning, with maintenance intervals as short as every two weeks.
Solution:
To reduce dust accumulation and extend mold life, the supplier adopted high-purity ceramic beads combined with a turbo blasting system to significantly reduce airborne dust levels to less than 30 mg/m³. Improved media selection minimized particle contamination while ensuring precise cleaning of delicate mold features.
Results:
After introducing ceramic beads, maintenance intervals were significantly extended from 2 weeks to 3 months, reducing downtime and labor costs. This change not only improved operational efficiency, but also ensured consistent mold performance, solidifying the supplier’s reputation for high-precision manufacturing.
The switch from glass to ceramic blasting beads is revolutionizing mold finishing, delivering superior performance, cost savings, and environmental benefits.
Ready to upgrade your mold finishing process? Contact us for a free media compatibility test and find the perfect solution for your needs.
Stay tuned for our next article, where we explore the innovative use of ceramic blasting beads in 8 categories of mold cleaning.
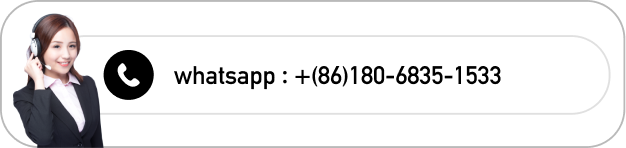