October 11, 2024
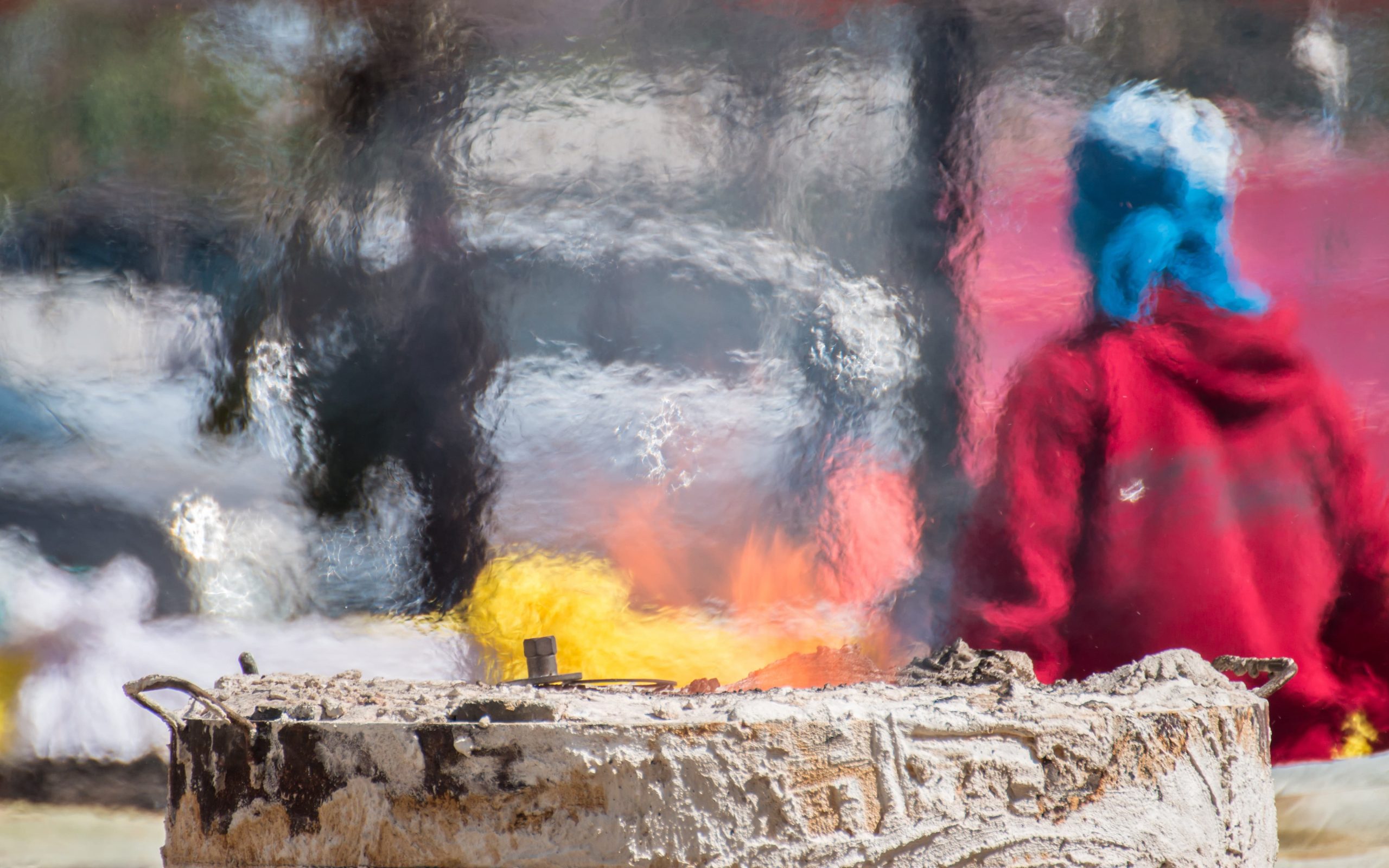
With the rapid development of modern industry, more and more high-temperature resistant materials are used in extreme environments, such as aerospace, automobile engine parts, nuclear power plants, etc. These materials need to have high heat resistance and excellent surface quality to ensure that they are not damaged during use. Sandblasting plays an important role in the surface treatment of high-temperature-resistant materials. It can improve the service life and performance of materials by cleaning, strengthening, deburring, and other treatments on the surface. However, choosing the right sandblasting material is crucial, which is not only related to the surface treatment quality of the workpiece but also directly affects production efficiency and cost control.
Currently, ceramic beads and aluminum sand are two commonly used media in sandblasting high-temperature resistant materials. They each have different characteristics and are suitable for various application scenarios. This article will compare these two sandblasting materials in depth from multiple angles such as material properties, high-temperature resistance, surface treatment effect, economy, and typical applications to help you make the best choice.
A basic introduction to ceramic beads
Composition and production process
The main component of ceramic beads is zirconium oxide or other oxides, which are made by high-temperature sintering process. Compared with traditional sandblasting media, ceramic beads have extremely high hardness and density and are usually used to treat workpiece surfaces that require high strength and heat resistance. Its production process is relatively complex, requiring the raw materials to be sintered at high temperatures and undergo precise screening and processing to ensure that each ceramic bead has uniform size and stable physical properties.
The chemical structure of ceramic beads enables them to remain stable at high temperatures and will not expand or break due to heat, making them an ideal choice for surface treatment in high-temperature environments. In addition, ceramic beads are extremely wear-resistant during use and can be reused many times without rapid loss due to frequent use.
Advantages of ceramic beads
- Extremely high hardness and wear resistance: The Mohs hardness of ceramic beads can reach more than 8, which is enough to handle a variety of high-strength materials, including high-temperature resistant alloys, titanium alloys, etc.
- Reusable: The high density and hardness of ceramic beads allow them to be reused many times, reducing the frequency of media replacement and reducing production costs.
- Less deformation and damage to the material surface: In the surface treatment of high-temperature materials, ceramic beads can ensure the cleaning effect while avoiding excessive grinding or scratching the workpiece surface.
- Environmental protection: Ceramic beads produce very little dust during the sandblasting process, which helps to improve the working environment of the workshop and reduce the impact on workers’ health.
Applicable scenarios of ceramic beads
Ceramic beads are widely used in industries with high requirements for surface treatment, especially in aerospace, and nuclear industries, and surface cleaning and strengthening of high-temperature alloy parts. For example, the turbine blades of aircraft engines need to work under extremely high temperatures and high pressures. Ceramic beads can clean and strengthen them without damaging the surface of the parts, thereby improving the fatigue resistance of the parts. In addition, ceramic beads are also suitable for the surface treatment of nuclear reactor components and can ensure their surface quality under high temperature and high-pressure environments.
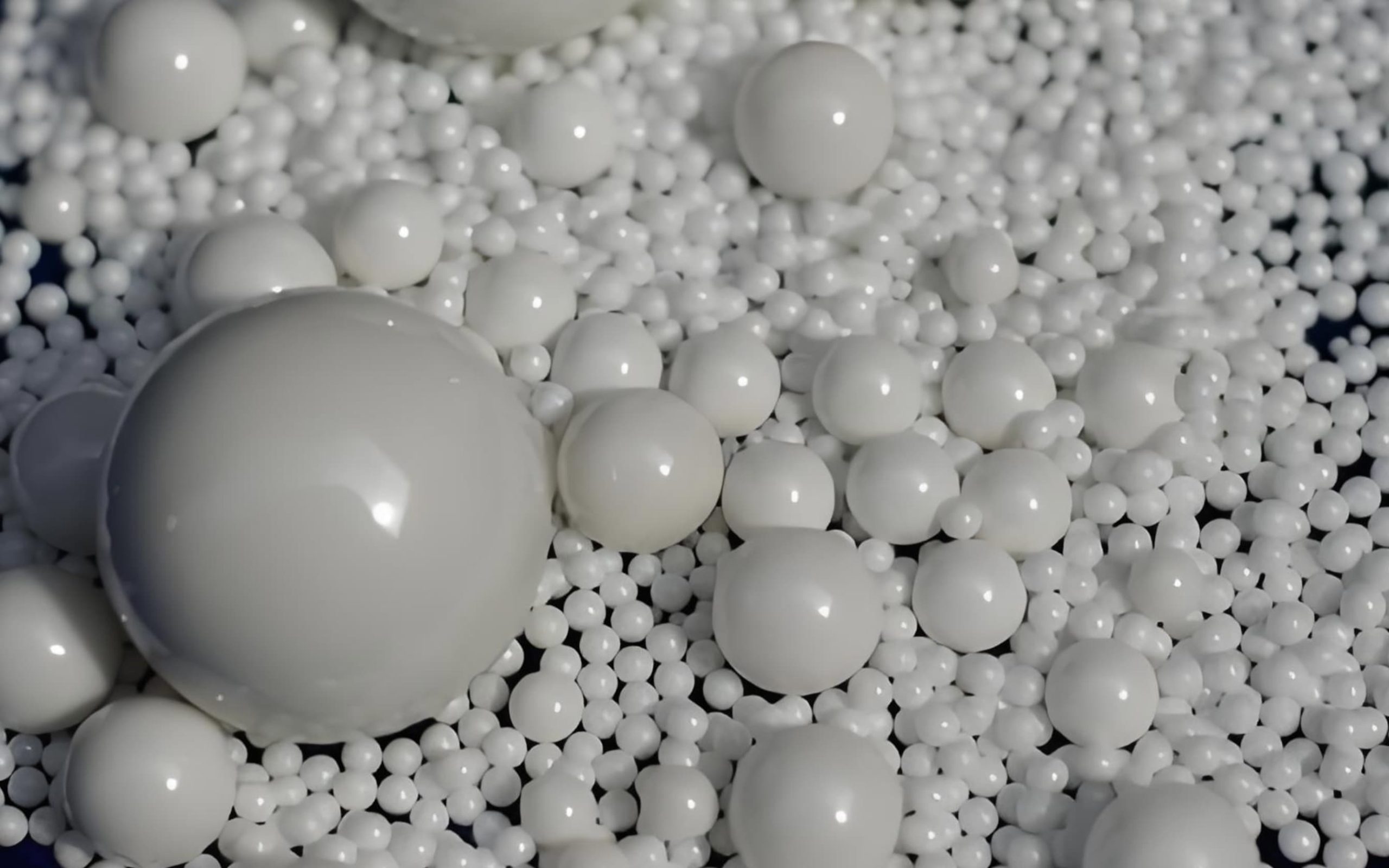
Ceramic beads
A basic introduction to aluminum sand
Composition and production process
Aluminum sand is a sandblasting medium made of high-purity aluminum oxide through melting and crushing processes. Aluminum sand has moderate hardness but a strong cutting force, which is suitable for quickly removing oxide scale, dirt, and impurities on the surface of the workpiece. Its production process is relatively simple and the cost is low, so it is widely used in cost-sensitive industrial fields. Aluminum sand is light in weight, easy for workers to operate and control, and is especially suitable for sandblasting and surface polishing of small and medium-sized parts.
Advantages of aluminum sand
- Strong cutting force: Aluminum sand has excellent cutting performance and can quickly remove impurities and oxide layers on the surface of the workpiece, especially suitable for cleaning rough surfaces.
- Lightweight: Aluminum sand is lighter than ceramic beads, which makes it easier for sandblasters to accurately control the spray force during operation.
- Relatively low cost: The production cost of aluminum sand is low, suitable for large-scale surface treatment operations, and has significant economic benefits.
- Suitable for workpieces of different sizes: Aluminum sand can be applied to workpieces of different sizes according to the particle size, with strong flexibility.
Applicable scenarios of aluminum sand
Aluminum sand is widely used in sandblasting and surface polishing of small and medium-sized parts in the automotive, aviation, and power industries. For example, automobile engine parts require frequent surface cleaning and deburring. The efficient cutting force of aluminum sand can quickly remove surface impurities and improve the surface finish of the workpiece. In addition, aluminum sand is also commonly used for surface treatment of electronic product housings to improve product appearance quality and durability by removing oxide layers.
Performance comparison – high-temperature resistance and surface treatment effect
High-temperature resistance
Ceramic beads have extremely high-temperature resistance and can usually withstand temperatures up to 1200 degrees Celsius or more. In ultra-high temperature environments, ceramic beads can still maintain their physical properties and will not break or fail due to temperature increases. This makes it an ideal choice for processing high-temperature alloys and other high-temperature resistant materials, especially in fields such as aerospace and nuclear industries that require extremely high heat resistance of materials.
In contrast, aluminum sand has relatively weak high-temperature resistance and can usually withstand high temperatures of around 600 degrees Celsius. In high-temperature environments, the structure of aluminum sand may change, resulting in a decrease in its cutting performance or even failure at extremely high temperatures. Therefore, aluminum sand is more suitable for surface treatment at medium or normal temperatures.
Surface treatment effect
Due to their high density and hardness, ceramic beads can provide a more uniform and delicate treatment effect during surface treatment. Since ceramic beads do not produce too many scratches during sandblasting, the surface of the treated workpiece usually has a higher gloss and smoothness. It is particularly suitable for surface treatment of workpieces that require high precision and high finish, such as surface strengthening of aircraft engine turbine blades.
Aluminum sand is known for its strong cutting force and can quickly process rough or oxide-layered surfaces. Although aluminum sand has a fast-processing speed, its cutting performance is relatively rough and is not suitable for workpieces with high surface finish requirements. Therefore, aluminum sand is more used in scenarios where surface quality requirements are not high, such as scale removal of automotive parts and surface cleaning of large castings.
Economic efficiency and service life
Economic efficiency of ceramic beads
Ceramic beads have a high initial purchase cost, but due to their strong wear resistance, long service life, and repeated use, they have high economic benefits in the long run. For projects that require long-term operation and high surface quality requirements, ceramic beads are undoubtedly a more economical choice.
Economic efficiency of aluminum sand
In contrast, aluminum sand has a lower cost and is suitable for projects that are more sensitive to budgets. Although aluminum sand has strong cutting force and high processing efficiency, it is not suitable for long-term or high-intensity applications because it is fragile, consumes quickly, and needs to be replaced frequently. However, for low-end and mid-range projects that do not require long-term and high-intensity use, aluminum sand is still a cost-effective choice.
Typical application cases
Ceramic beads application cases
Ceramic beads are often used in high-end aerospace fields for high-precision part surface treatment. A typical application is the turbine blades in aircraft engines. These blades are subjected to extremely high temperatures and huge mechanical stresses during operation, and the quality of surface treatment directly affects the life and performance of the engine. Through ceramic bead sandblasting, the surface of the turbine blades can be fully cleaned and strengthened to ensure its fatigue resistance and corrosion resistance at high temperatures. In addition, ceramic beads are also widely used in the surface treatment of key components in the nuclear industry, such as components of nuclear reactors. Because nuclear reactor components need to work under extreme conditions, the high hardness and temperature resistance of ceramic beads ensure the stability and safety of these parts in use.
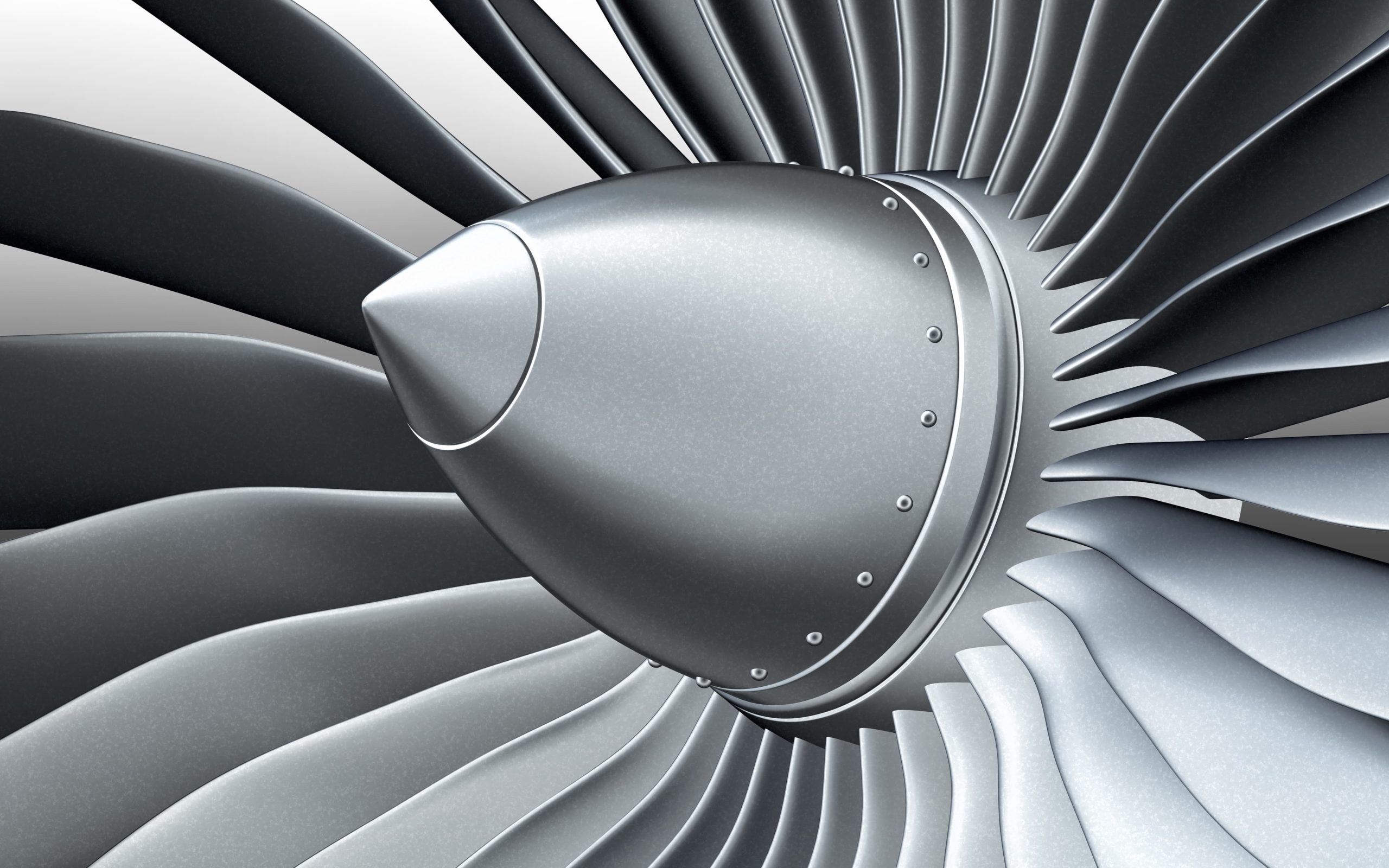
Engine turbine blades
In the oil and gas industry, since the equipment is often exposed to extremely high temperatures and high-pressure environments, especially parts such as drilling equipment, pipelines, and valves. During oil and gas drilling, the surface of the drill bit is subjected to huge pressure and temperature and will suffer severe surface wear and corrosion, so regular surface treatment is required. During the surface treatment process, ceramic beads can remove surface oxides without destroying the geometric accuracy of the drill bit, thereby improving the fatigue resistance of the drill bit. Therefore, they are widely used in the industry to strengthen the surface of these equipment to extend their service life. In addition, valves in the oil and gas industry are often exposed to high-temperature and high-pressure environments, and their working performance is often affected by corrosion or deposits. Strengthening the valve surface by ceramic bead sandblasting can improve its corrosion resistance and ensure the sealing and operating efficiency of the valve.
In the field of high-temperature metallurgy, such as the manufacturing and processing of metals such as steel and aluminum, surface treatment of high-temperature resistant materials is often required. The use of ceramic beads can effectively remove oxide scale and casting defects while enhancing the surface finish and maintaining the surface integrity of the workpiece.
Aluminum sand application case
Aluminum sand is used for sandblasting and cleaning small and medium-sized parts in the automotive, electronics, and other industries. For example, parts in automobile engines often accumulate a lot of oil and oxide scale. Aluminum sand sandblasting can quickly and efficiently remove surface impurities and improve the surface cleanliness of parts. In addition, surface treatment of electronic product housings is also one of the typical applications of aluminum sand. Aluminum sand can effectively remove the oxide layer on the outer shell of electronic products, enhance the gloss and touch of the product’s appearance, and improve its wear resistance.
In addition, aluminum sand is also widely used in the oil and gas and metallurgical fields due to its relatively low cost and strong cutting force. For example, oil and gas pipelines are exposed to harsh working environments for a long time, and thick oxides and corrosion layers often accumulate on the surface. Aluminum sand can quickly remove these impurities while maintaining the structural integrity of the pipeline with its lightweight and efficient cutting force. In addition, aluminum sandblasting is also commonly used in the primary polishing of iron and aluminum castings in the metallurgical industry, which can effectively remove the rough layer on the casting surface and provide a basis for subsequent fine processing.
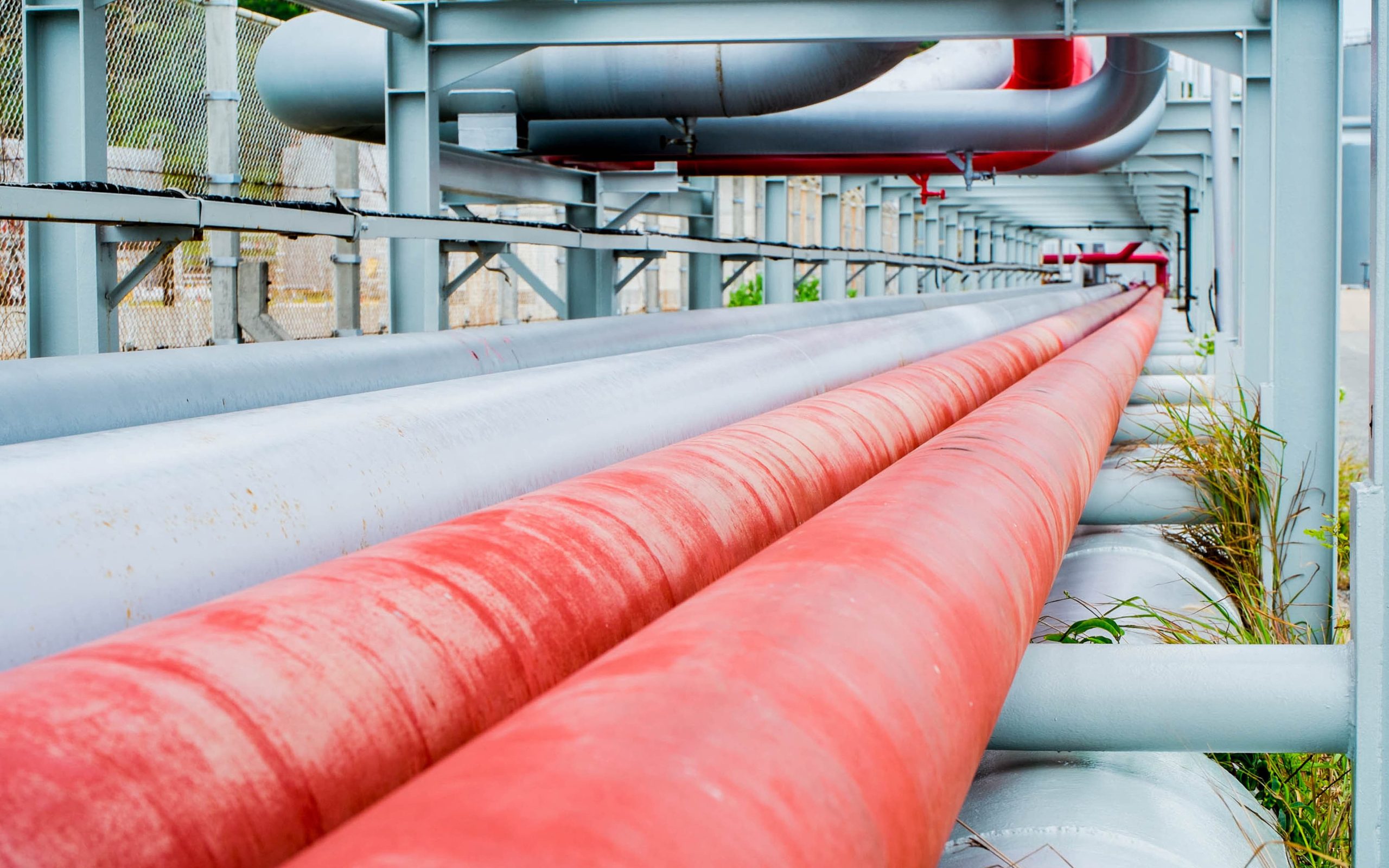
Oil pipeline
Although aluminum sand is not as resistant to high temperatures as ceramic beads, it can quickly remove oxides and surface impurities when processing rougher surfaces, which is suitable for some application scenarios with lower requirements.
How to choose? Recommendations based on specific application scenarios
When choosing ceramic beads or aluminum sand, the key is to clarify the specific needs and application scenarios of the workpiece. The following are recommendations for different scenarios:
- Workpieces with high precision and high temperature: If your workpiece is a high-precision, high-temperature resistant material that requires a high surface finish and long-term durability, then ceramic beads are undoubtedly the best choice. Ceramic beads perform well when processing high-demand workpieces such as turbine blades and engine covers, ensuring the service life of the workpiece under extreme conditions.
- Fast processing and cost-sensitive projects: If your project does not require high surface accuracy and has a limited budget, aluminum sand is a more cost-effective choice. Aluminum sand has strong cutting force and is suitable for quickly removing surface oxide scale and impurities, so it is more suitable for workpieces that require efficient processing, such as automotive engine parts and electronic product housings.
- Long-term projects that require repeated use of sandblasting materials: The high wear resistance and repeated use of ceramic beads make them very suitable for projects that require long-term surface treatment, especially when expensive parts are involved, ceramic beads can bring a better return on investment.
In summary, when choosing sandblasting materials, it is necessary to comprehensively consider the material type of the workpiece, the application scenario, the budget, and the specific requirements for surface quality. Ceramic beads are suitable for workpieces that require precision processing and high performance due to their excellent high-temperature resistance, wear resistance, and surface treatment effects, while aluminum sand is more suitable for processing common mid- and low-end workpieces due to its efficient cutting force and lower cost.
The final choice should be based on the specific needs of the project to ensure the best cost-effectiveness while ensuring quality. I hope this article can help you better understand the respective characteristics of ceramic beads and aluminum sand, and make the most suitable choice for your project.
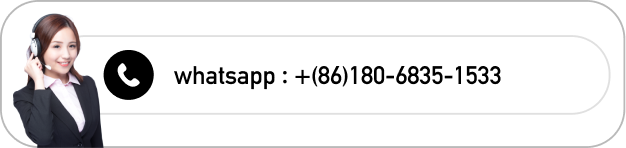