October 12, 2024
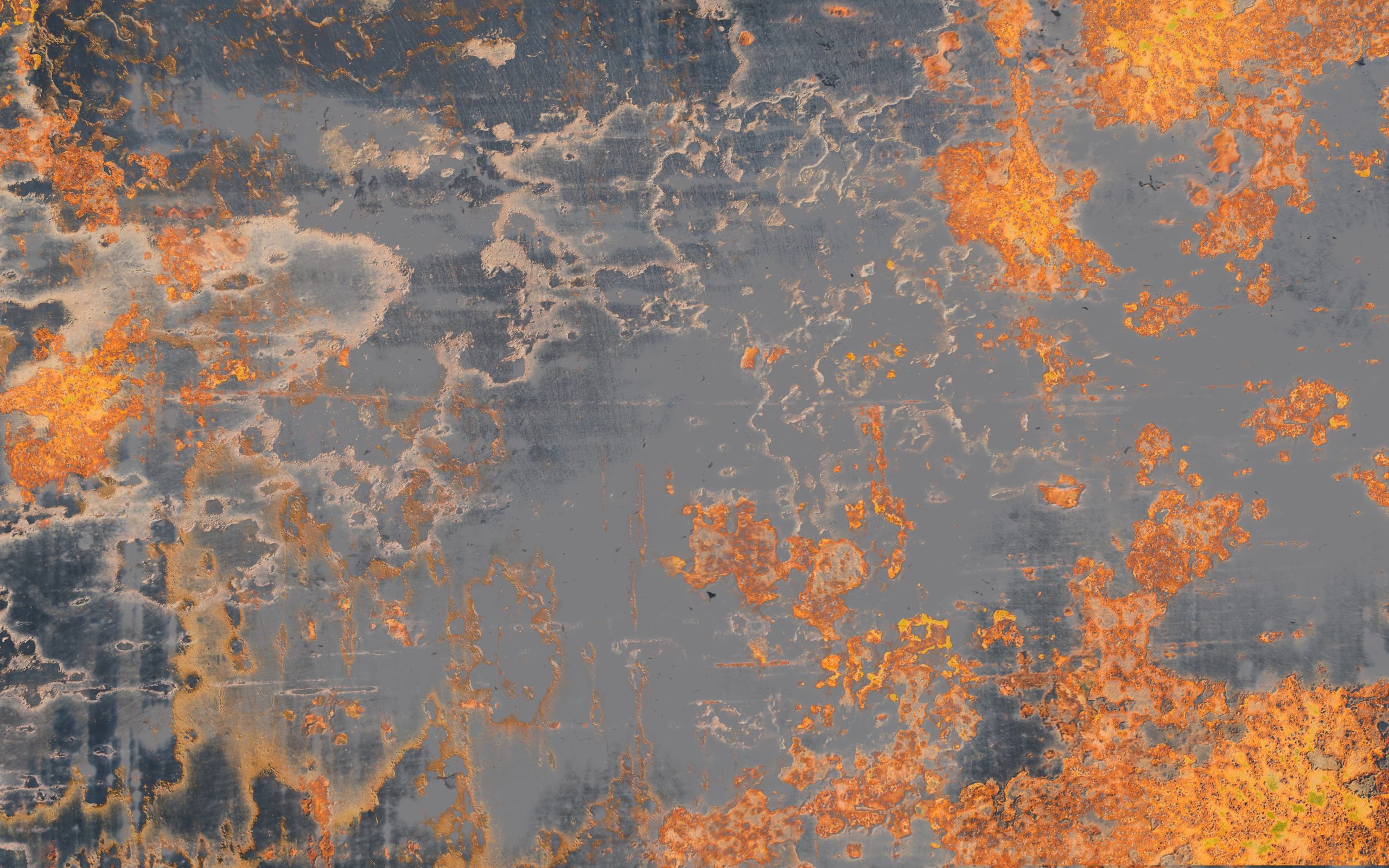
Alumina blasting is an important industrial surface treatment technology that is widely used in a variety of industries, especially in removing stubborn rust and aged paint layers. As modern industrial products have increasingly higher requirements for surface quality and durability, aluminum oxide blasting has become the preferred method in many industries due to its high efficiency, applicability and environmental friendliness. This article will explore the characteristics of aluminum oxide blasting, its working principle and its specific application in different industrial fields, and analyze why this technology is so indispensable in rust and paint removal processes.
Durable surface treatment needs
Modern industrial equipment and structures are exposed to complex and changing environments, and long-term use will inevitably produce rust and paint aging. This phenomenon is particularly evident on metal materials exposed outdoors such as ships, automobiles, bridges, and building facilities. Rust and paint layers not only affect the appearance, but more importantly, they also damage the structural integrity and performance of the equipment. Traditional cleaning methods, such as manual grinding or chemical solvent treatment, are often inefficient and may damage the workpiece itself. In contrast, aluminum oxide sandblasting can not only quickly remove stubborn rust, but also efficiently remove aged paint layers. Its hardness and cutting force can easily remove surface impurities, but it is gentle enough not to cause secondary damage to the substrate, laying a solid foundation for subsequent coating or surface treatment. This sandblasting material is particularly suitable for those occasions that require high surface finish and durability, such as automobiles, ships, aerospace equipment, etc.
Basic characteristics of aluminum oxide
Hardness and wear resistance
Aluminum oxide (Al₂O₃) is one of the commonly used sandblasting materials in industry, and is favored for its high hardness and strong wear resistance. The Mohs hardness of aluminum oxide is 9, second only to diamond, and much higher than the hardness of rust and most paint layers. This extremely high hardness allows aluminum oxide to quickly and effectively remove stubborn rust and thick paint layers without easily breaking or wearing. At the same time, the high-density structure of aluminum oxide also means that it can provide greater kinetic energy in the process of removing surface impurities, improving the overall cleaning efficiency.
Chemical stability
Aluminum oxide has excellent chemical stability and does not react chemically with most metal materials during sandblasting. This feature ensures that the workpiece surface will not be corroded or contaminated by any chemicals during the cleaning process. For workpieces that require high purity and subsequent coating adhesion, the chemical residue-free characteristics of aluminum oxide sandblasting are critical to ensure the smooth progress of subsequent processes.
Multiple recycling
Aluminum oxide particles are very durable and can be recycled many times, reducing overall material consumption and production costs. Although the initial investment cost of aluminum oxide is relatively high, its long service life makes it extremely cost-effective in long-term applications. Therefore, it is very suitable for large-scale industrial production.
Formation and removal difficulties of rust and paint layer
Rust formation
Rust is formed due to the chemical reaction of metal with oxygen and moisture in the air to form iron oxide (ie rust). This process not only affects the appearance of the workpiece, but also weakens the structural strength of the metal, causing embrittlement or fracture of the material. If not handled in time, rust will gradually expand and penetrate into the substrate, eventually destroying the overall performance of the workpiece. Therefore, quick and thorough removal of rust is essential to maintain the service life and reliability of the workpiece.
Aging of the paint layer
Aging of the paint layer is usually manifested as fading, cracking, peeling or loss of gloss. Due to long-term exposure to sunlight, moisture, wind and sand, and chemicals, the protective properties of the paint layer will gradually weaken and lose its protective effect on the substrate. Aged paint layers are often tightly attached to the surface of the workpiece, and manual grinding is difficult to completely remove, while chemical solvents may damage the substrate. Only alumina blasting can accurately break and peel off the paint layer, avoiding the potential risks of chemical treatment.
Reasons for difficulty in removal
Rust and paint layers are often embedded in the surface micropores of the workpiece during the formation process, and are tightly attached, making it difficult to completely remove them by traditional methods. The strong cutting force and granular structure of aluminum oxide sandblasting can penetrate deep into the surface micropores, completely remove stubborn impurities, and ensure that the surface is as bright as new.
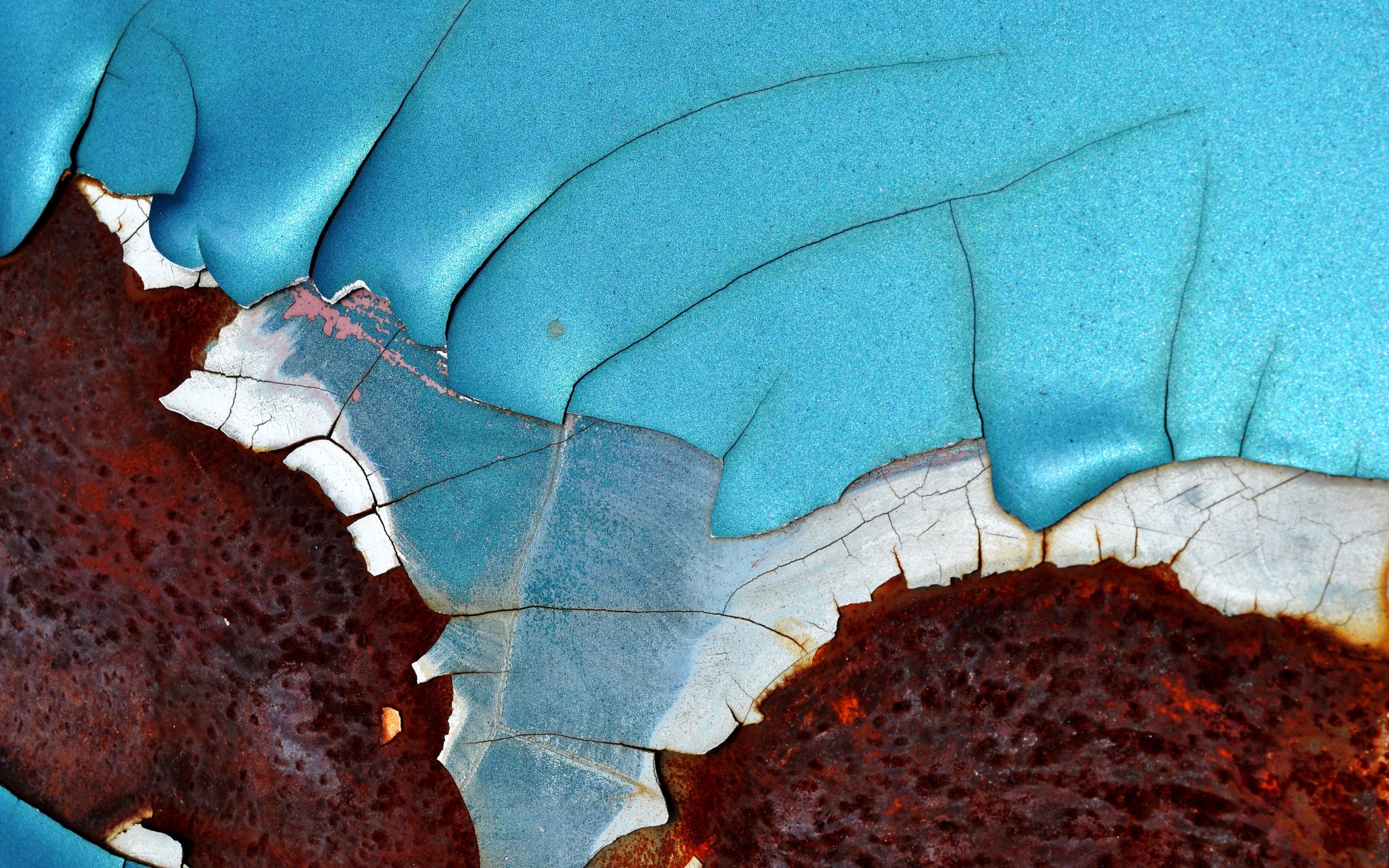
Cracked and peeling paint on an old car
Main advantages of alumina blasting
Efficient rust and paint removal
Alumina blasting is extremely efficient in removing rust and paint layers. Due to the high hardness and high density of aluminum oxide, its particles can quickly hit and cut rust and paint layers under high pressure, causing them to fall off the substrate. Compared with traditional chemical cleaning and manual grinding, alumina sandblasting is not only more efficient, but also more environmentally friendly.
No damage to the substrate
Although the hardness of aluminum oxide particles is high, their shape and particle size are specially designed to remove surface impurities while minimizing damage to the substrate of the workpiece. For some workpieces that require high surface finish (such as automobile shells or aircraft parts), aluminum oxide sandblasting can provide a uniform cleaning effect to ensure that the workpiece surface is free of scratches or dents.
Applicable to a variety of workpieces and materials
Aluminum oxide sandblasting is suitable for workpieces of many different materials, including steel, aluminum alloys, titanium alloys and composite materials. By adjusting the size of the sandblasting particles and the injection pressure, aluminum oxide sandblasting can handle almost any complex shape or size of workpiece, from small parts to large structures.
In order to better demonstrate the specific application of aluminum oxide sandblasting in industry, we will further analyze some actual cases in some application industries. Workpieces in these industries often require more powerful surface treatment technology due to special working environments and process requirements.
Applicable industries and workpiece analysis
Oil and gas industry
In the oil and gas industry, equipment such as drill bits, valves, and pipelines are often exposed to corrosive liquid and gas environments. Especially on offshore drilling platforms, salt spray and high-pressure environments accelerate the oxidation and corrosion of metal surfaces. Stubborn rust often accumulates on the surface of these equipment, which may cause equipment failure or safety hazards if not cleaned in time.
Alumina sandblasting plays an important role in the maintenance of these equipment. Through its efficient rust removal ability, alumina sandblasting can quickly clean rust on the surface of drill bits and valves, while providing an ideal adhesion surface for the next step of anti-corrosion coating. Its hardness ensures that deep rust can be removed without causing excessive wear to the equipment itself. The operating environment of the oil and gas industry is extremely harsh, and the durability and long-term operation of the equipment depend on reliable surface treatment technology, and the excellent chemical stability of alumina sandblasting is undoubtedly one of the best choices.
Metallurgical industry
The surface treatment tasks of workpieces such as high-temperature furnaces and steel castings in the metallurgical industry are extremely challenging. In a high-temperature environment, after multiple heat treatments of steel castings, the metal surface is easily oxidized, forming a thick oxide scale that is difficult to remove by ordinary mechanical means. Alumina sandblasting can easily remove these impurities and prepare for the next step of processing due to its strong cutting ability and high temperature resistance.
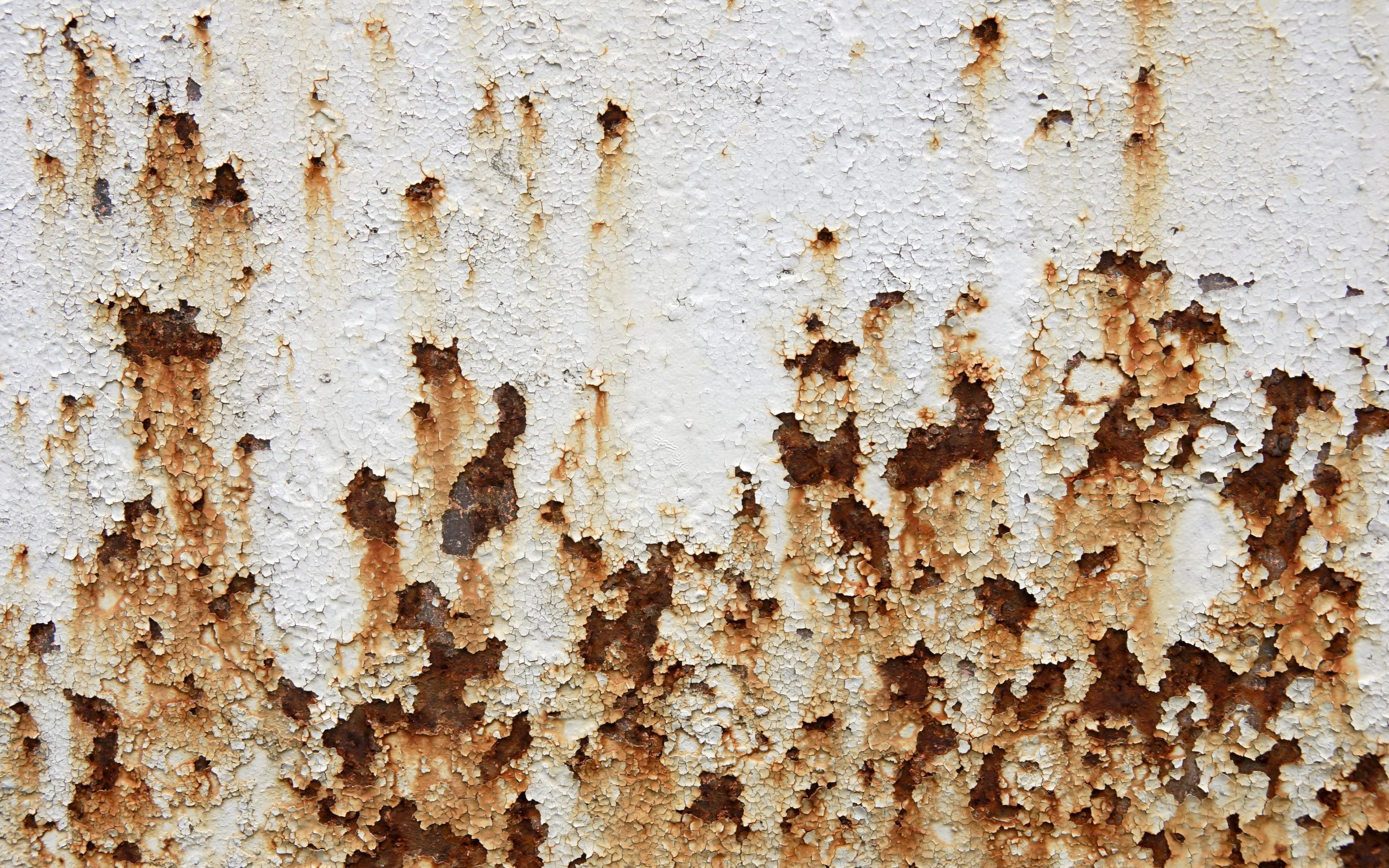
Metal Oxidation
Aerospace field
In the aerospace field, the surface treatment of engine parts, wings and other key components requires extremely high precision and cleanliness. Aircraft equipment is exposed to harsh and changeable environments for a long time, and is also easily troubled by oxidation, rust and other problems. In the treatment of key components such as turbine blades and engine casings, the precise operation of aluminum oxide sandblasting can ensure that the workpiece will not fail due to excessive wear. It can not only efficiently remove rust and oxide layers, but also ensure the smoothness and integrity of the workpiece surface, providing ideal surface conditions for subsequent processes such as spraying and welding, and has a very high maintenance effect.
Automobile Manufacturing and Restoration
The metal body of the car is often exposed to rain, snow, road salt and air pollution. These elements work together to accelerate oxidation reactions and form rust. The peeling and aging of the paint layer not only affects the appearance of the car body, but also makes the metal substrate more susceptible to rust. Aluminum oxide sandblasting can efficiently remove rust and aged paint layers, while providing a clean and uniform surface for repainting or electroplating.
Ship and marine equipment
The hull is in a humid and high-salinity seawater environment for a long time, and the rust and paint aging problems are particularly serious. Alumina sandblasting can not only thoroughly clean the rust and paint on the surface of the hull, but also provide an ideal base for subsequent anti-corrosion treatment (such as spraying anti-corrosion paint).
Environmental protection and safety
In industrial production, environmental protection and operational safety have become the focus of more and more companies. Alumina sandblasting, as an environmentally friendly and efficient surface treatment method, can reduce the negative impact on the environment in the process of removing rust and aging paint.
Environmental performance: pollution-free and recyclable
Compared with methods such as chemical rust removal and mechanical grinding, alumina sandblasting has obvious environmental advantages. Many chemical rust removers contain toxic substances, which may pollute soil and water sources and even cause serious harm to workers’ health. Mechanical grinding will produce a lot of dust and pollute the operating environment.
As a naturally occurring material, alumina has extremely stable chemical properties and will not produce any harmful substances during the sandblasting process. Moreover, in a suitable sandblasting environment, the particles after alumina sandblasting can be recycled and reused many times. Through recycling, enterprises can not only save costs, but also reduce waste emissions, which meets the green production requirements of modern industry. In the long run, the amount of waste from aluminum oxide sandblasting is much lower than other surface treatment methods, which is conducive to reducing the pressure on the environment.
Safety performance: reducing health risks
Worker safety is the core concern of every manufacturing company. Compared with the irritation that chemical cleaning agents may cause to the skin and respiratory system, the operating environment of aluminum oxide sandblasting is safer. In standardized sandblasting operations, workers only need to wear conventional protective equipment such as dust masks and protective clothing to work under relatively safe conditions.
In addition, the dust generated during aluminum oxide sandblasting can be effectively collected and treated by setting up dust collection equipment to avoid air pollution in the working area. Advanced sandblasting equipment can ensure the efficiency and safety of the cleaning process by accurately controlling the spray intensity and spray angle, and further improve the comfort and work efficiency of workers.
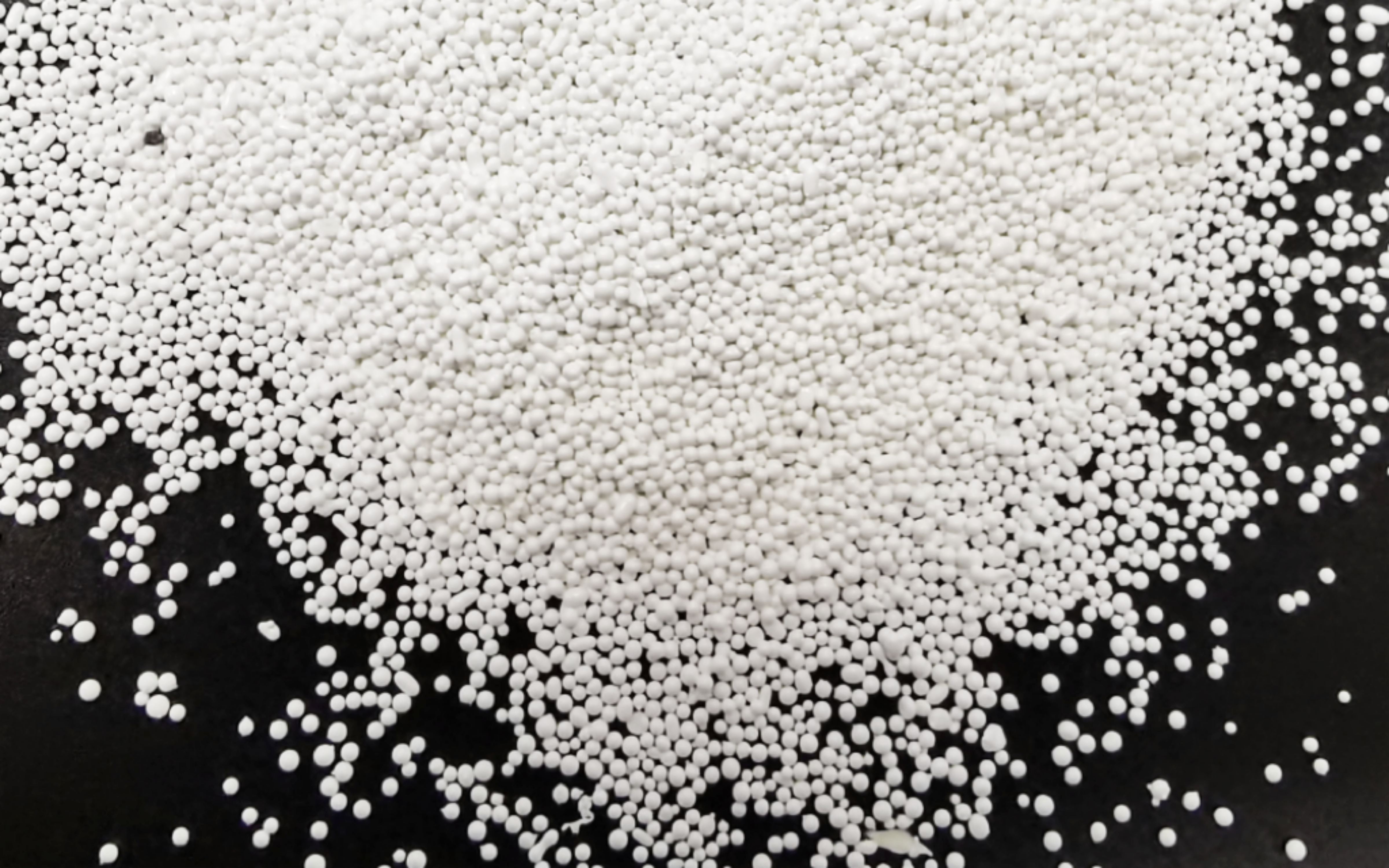
aluminum oxide sandblasting
Economic efficiency and service life
In industrial production, cost-benefit analysis is an important consideration for enterprises when choosing surface treatment materials. Although alumina blasting is more expensive at the initial purchase, its efficiency and durability make it an economically viable option in the long run.
High productivity
Due to its high hardness and strong cutting force, aluminum oxide sandblasting can remove rust and paint much faster than other methods, which means that more workpieces can be processed in the same amount of time, improving production efficiency. For large-scale industrial production, improved efficiency directly means reduced operating costs. Especially on large-scale production lines, the time and labor costs saved by aluminum oxide sandblasting are unmatched by other methods.
Multiple uses and material durability
Alumina blasting materials have good durability and can maintain their performance during multiple uses. Depending on the actual use scenario and particle size, aluminum oxide sandblasting can be reused dozens of times or more, which significantly reduces the frequency of material replacement and the overall unit cost will be significantly reduced.
Comparison with other sandblasting materials
Compared with other sandblasting materials such as glass beads or steel grit, aluminum oxide has a longer service life. Glass beads and steel grit usually break or wear after several uses, while aluminum oxide, due to its unique structure and hardness, can still maintain efficient rust and paint removal performance after multiple cycles. Therefore, the economy of aluminum oxide sandblasting far exceeds these materials, especially for enterprises that require long-term large-scale cleaning operations.
Alumina blasting has become a key tool in the field of industrial rust and paint removal due to its excellent cutting force, high hardness and wear resistance. Whether it is aerospace, automotive, shipbuilding, or petrochemical industries, it can effectively remove stubborn rust and old paint layers. Compared with other media, alumina sandblasting is not only suitable for large-area operations, but also can provide precise processing without damaging the substrate. Its recyclable characteristics make it an ideal choice for efficiency and environmental protection. In the future, as process requirements increase, alumina sandblasting will show broad application prospects in more fields.
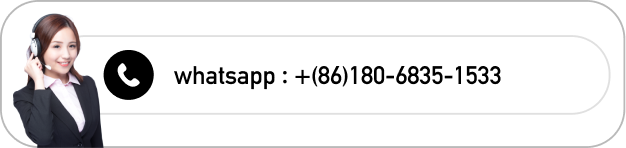