Achieving a mirror effect on metal: sandblasting for surface polishing
November 4, 2024
For the manufacturing industry that pursues a perfect surface, having mirror-smooth metal is not only a pursuit of beauty but also a symbol of craftsmanship and quality. In the fields of automobiles, aerospace, and high-end decoration, the glossiness of the metal surface often determines the product’s market competitiveness. So, how can this polishing effect be achieved through simple but efficient means? Sandblasting polishing is a key step to achieve this goal.
This article will explore in depth how sandblasting can achieve a mirror effect on different metals, including suitable abrasives, process control, and common application cases. You can learn about the role of sandblasting in surface polishing in this article to improve the quality of your workpiece and achieve a truly “reflective” surface effect.
What is surface polishing?
The core value of surface polishing
Surface polishing is an important step in improving the quality and appearance of workpieces, especially in high-precision manufacturing fields such as automobiles, aerospace, and luxury decoration. Through surface polishing, workpieces can obtain higher corrosion and wear resistance and can also effectively improve the material’s reflective effect, presenting a delicate visual experience.
In metal manufacturing, the “mirror effect” is not only about aesthetics but also an important way to improve the durability of materials. Smooth and flawless surfaces reduce particle adhesion and contaminant accumulation, making them easier to clean, while also performing better in terms of friction and corrosion. This is of great significance for metal parts that are exposed to harsh environments for a long time.
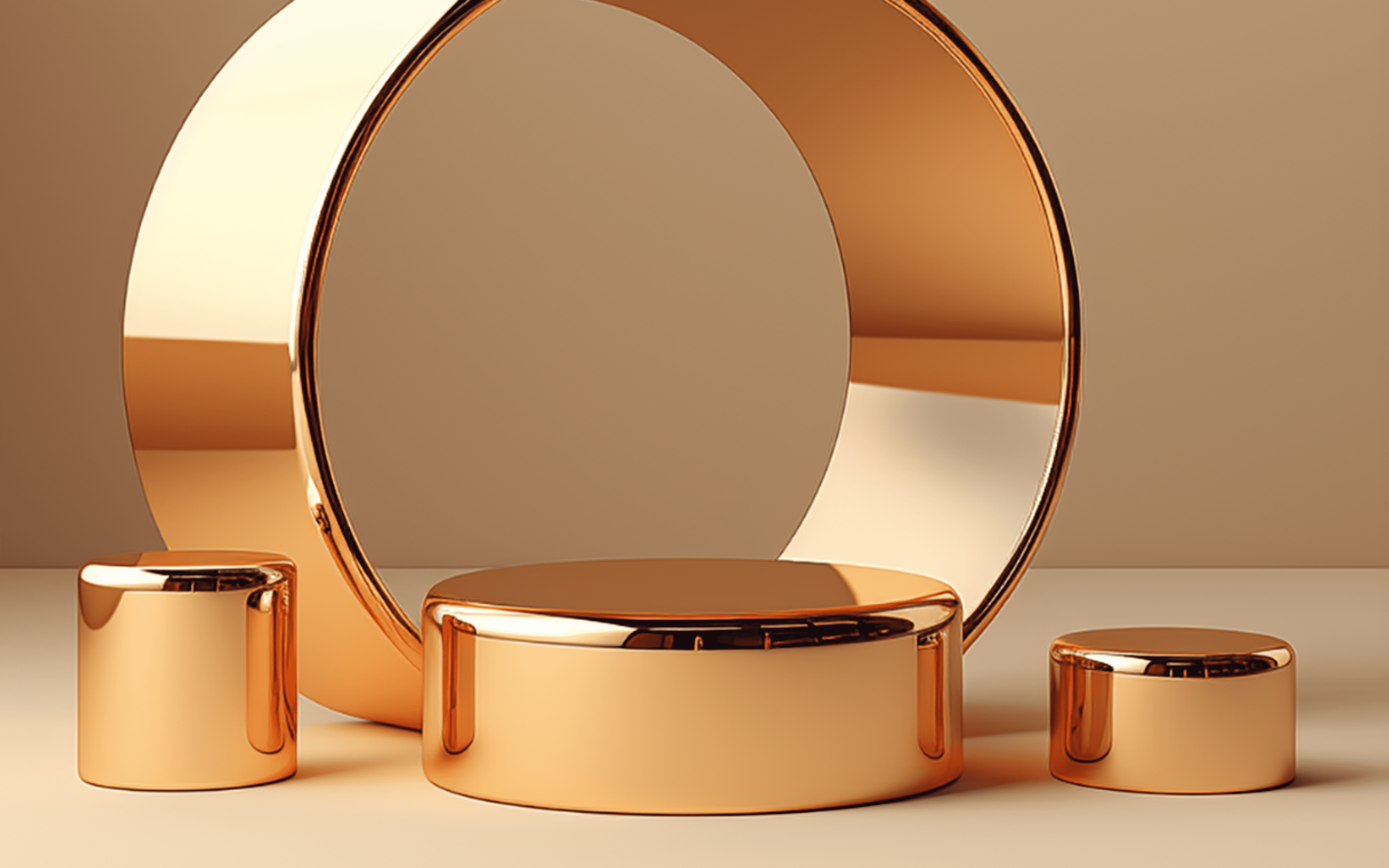
Metal mirror effect
Sandblasting: Achieving a mirror effect
Sandblasting polishing is an important means of surface polishing. It is a process in which high-pressure jet abrasives are driven by high-pressure airflow to hit the metal surface. It can gradually smooth the rough surface layer and achieve uniform grinding of the material, thereby achieving a smooth surface effect and improving the gloss of the metal.
Compared with traditional polishing methods such as chemical polishing and electrolytic polishing, the advantage of sandblasting polishing lies in its controllability and wide applicability. By adjusting parameters such as the type, particle size, and jet pressure of the abrasive, a variety of effects can be achieved, thereby flexibly adapting to different polishing needs. Sandblasting polishing can also be combined with precise process control to achieve higher efficiency than traditional methods.
Demands for metal polishing in different industries
Aerospace: high precision and durability first
Metal parts in the aerospace industry are often exposed to harsh environmental conditions, including high temperatures, extreme air pressures, and corrosive chemicals. Therefore, surface treatment involves not only polishing but also protection and durability. Sandblasting polishing technology combines high-hardness materials such as ceramic beads and zirconium oxide sandblasting abrasives to significantly improve the wear resistance of metal surfaces. It is suitable for aircraft engines, cabin parts, etc. Compared with the automotive industry, this field requires higher polishing precision. It is necessary to ensure that the particle size of the sandblasting abrasive is round and uniform to avoid uneven surfaces and affect the service life.
Luxury consumer goods: exquisiteness and high gloss
Luxury consumer goods such as watches, jewelry, and high-end electronic products have extremely high requirements for the polishing effect of metal surfaces. Sandblasting technology can be used for the initial polishing of these metal surfaces, and then more fine process treatment to achieve the ultimate mirror effect. In these applications, the use of micro-granular sandblasting abrasives such as ultra-fine ceramic beads and glass beads can bring a uniform and delicate high-gloss effect, meeting the aesthetic needs of high-end consumers for product appearance.
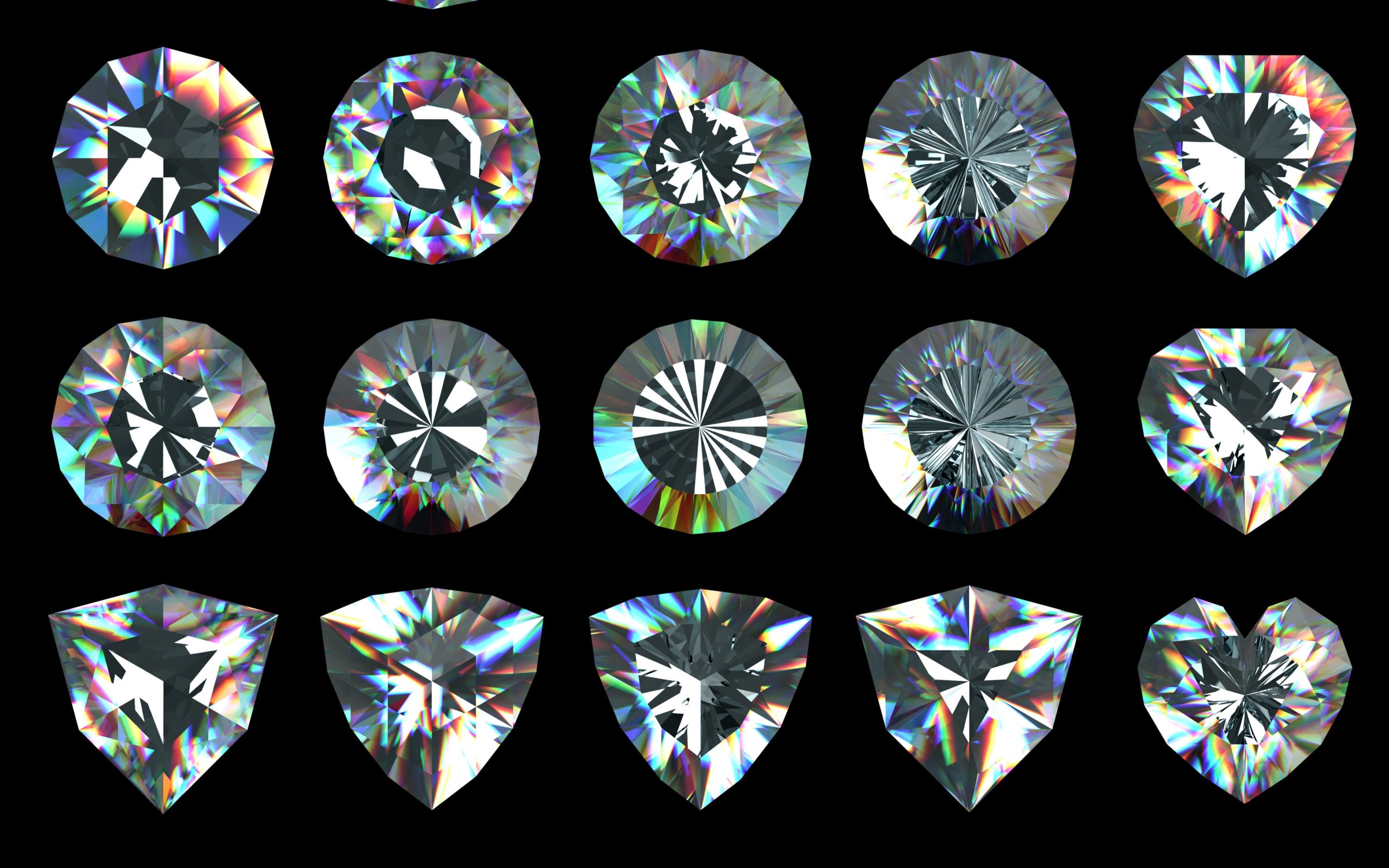
Fine polishing of the diamond surface
Architectural decoration: aesthetics and durability
In the construction and decoration industry, especially for high-end architectural design and decoration scenes. Sandblasting polishing can give the metal surface a high-gloss mirror effect, giving it a unique decorative beauty. At the same time, sandblasted metal materials have stronger antioxidant capacity, are suitable for long-term exposure in indoor and outdoor environments, and reduce maintenance costs. Ceramic beads and glass beads are common polishing abrasives that can help increase gloss and reflective effects without affecting the strength of the metal.
Automotive industry: balance between appearance and durability
The automotive industry pursues both high-gloss visual effects and sufficient wear resistance and corrosion resistance of metal surfaces. In the sandblasting process, it is crucial to choose the right abrasive. For example, aluminum oxide sand and glass beads are often used for surface treatment of body parts, which can help achieve uniform smoothness and improve the metal’s antioxidant capacity. In addition, by adjusting the pressure and distance of sandblasting, a delicate gloss and mirror effect can be achieved, making the gloss of the body surface lasting and stable.
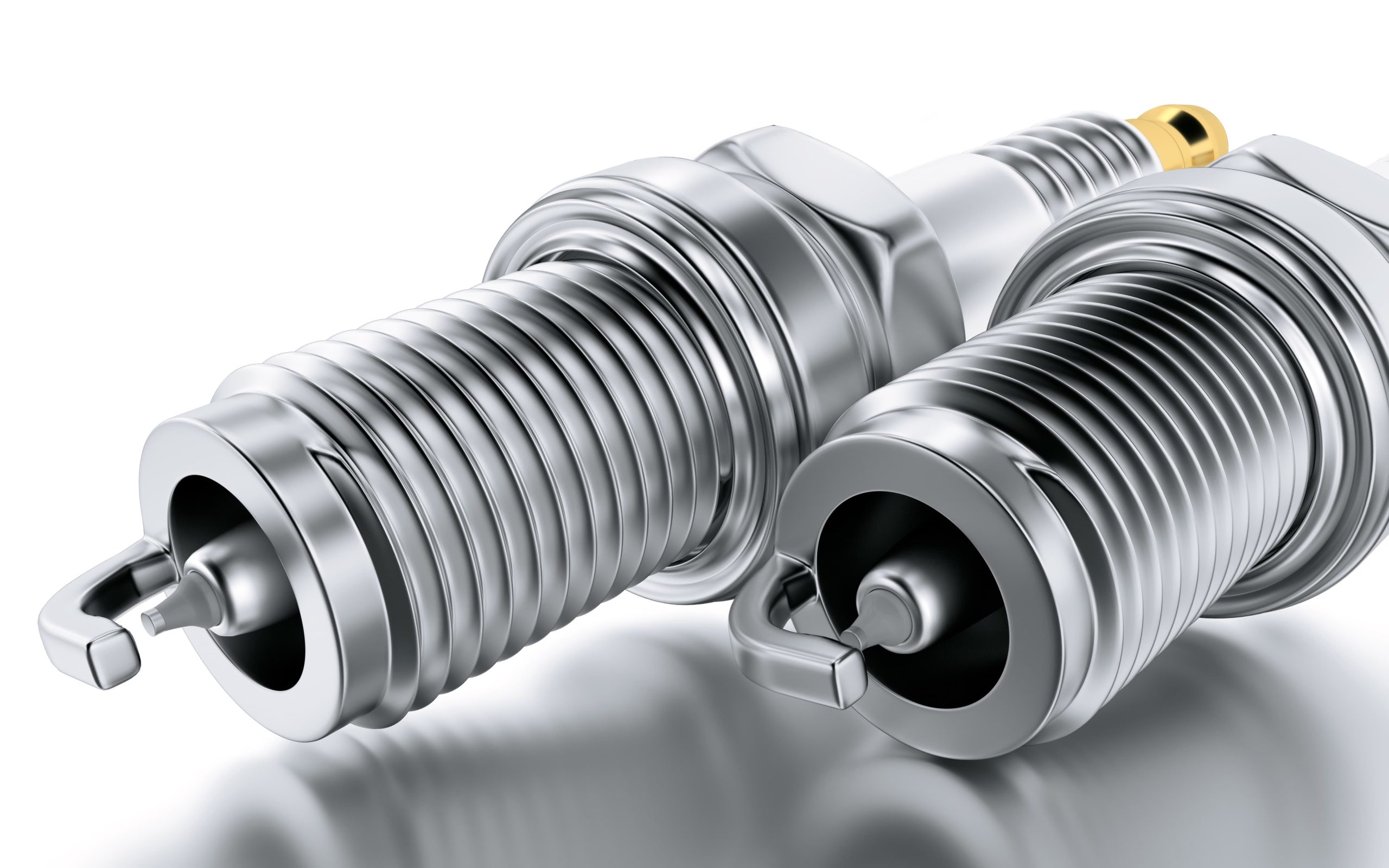
Automobile spark plug accessories
Commonly used metals for polishing
In different industry applications, different metal materials are suitable for different needs of mirror polishing. The following are several common types of metals used for mirror polishing and their characteristics:
- Stainless steel
Stainless steel is a highly corrosion-resistant alloy material with excellent reflective properties, which can easily achieve high gloss and mirror effects. Stainless steel surfaces can be sandblasted and polished to achieve a highly reflective mirror-like finish, making them popular in kitchenware, high-end automotive parts, and luxury decorative accessories.
- Aluminum
Aluminum is lightweight and highly reflective, making it common in aerospace and automotive manufacturing, where quality and strength are important. However, aluminum is susceptible to oxidation after polishing, which causes the surface to lose its luster, so polished aluminum parts are often sealed to maintain their finish and brilliance.
- Brass and Copper
Brass and copper are highly reflective after polishing, and their warm metallic tones are common in high-end decorative and artistic fields, such as decorative lamps and sculptures. Because copper is more susceptible to oxidation, it is usually treated with protective treatments after polishing to extend its surface finish and life.
This targeted selection of metal materials and surface treatments helps achieve the desired mirror effect and meet the dual requirements of beauty and functionality in various industries.
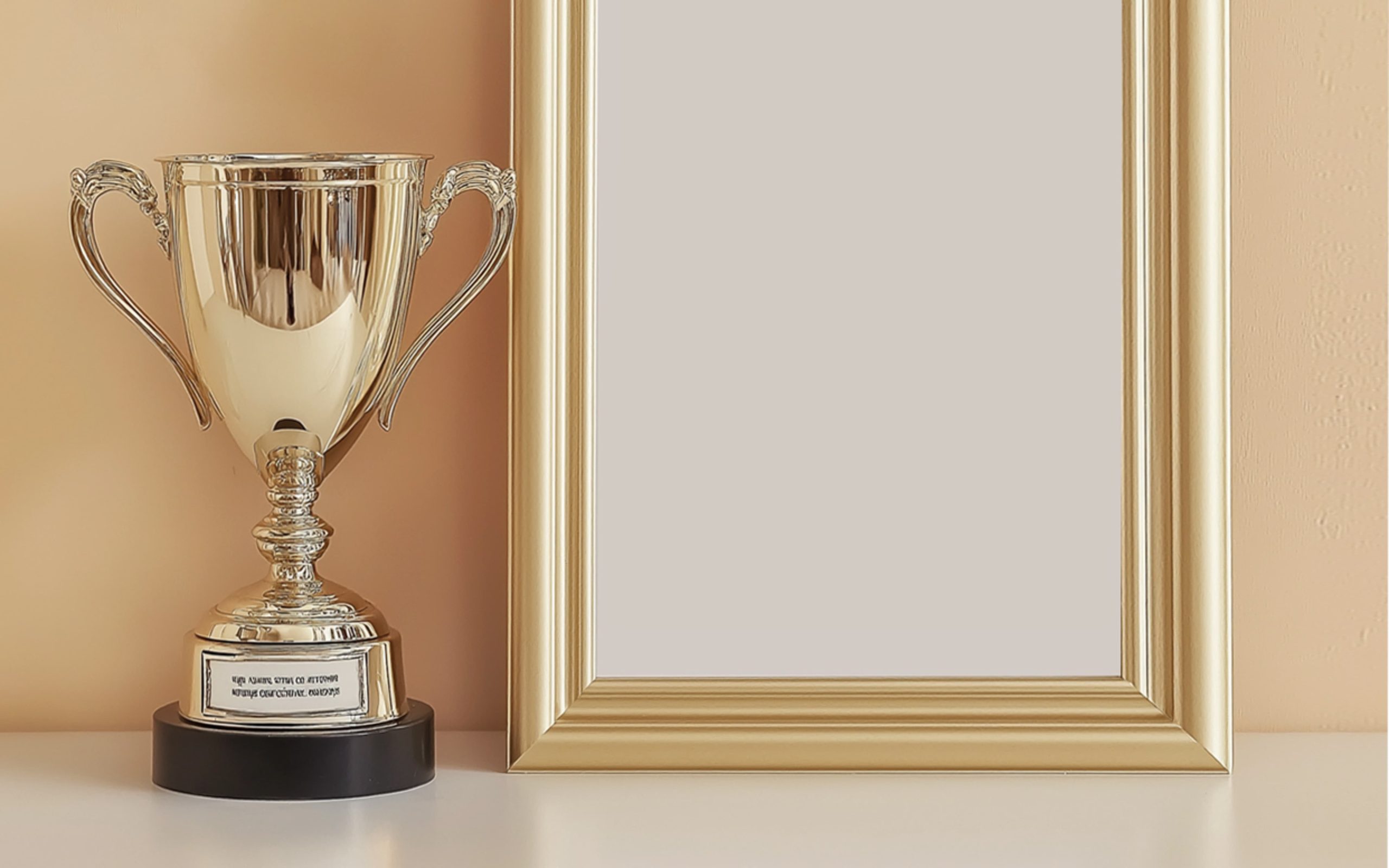
Mirror effect of brass trophy
Sandblasting media for polishing
When achieving a mirror effect on metal, the choice of sandblasting media is critical. Different types of blasting media have unique properties that affect the final polishing effect. The following media are widely used in the mirror polishing process:
- Glass beads
Glass beads are a common blasting medium used for metal surface polishing, mainly used in the final stage of the polishing process. Because the round particles of glass beads have low cutting force, they do not significantly change the structure of the metal surface, but gently polish the surface layer, giving the metal surface a highly reflective effect. Glass beads are particularly suitable for metals that need to be smooth and shiny, such as stainless steel and aluminum. After polishing, the reflective effect of the metal is enhanced, and at the same time, the glass beads will not cause additional damage to the metal surface, which is an ideal choice for improving the mirror effect.
Aluminum oxide is a high-hardness blasting medium with a strong cutting force. It is usually used in the surface pretreatment stage to help level the metal surface and remove coarse defects. In the mirror polishing process, the role of aluminum oxide is not limited to surface cleaning. It can also help the surface achieve the desired roughness so that it is easier to obtain a uniform high-gloss effect in subsequent polishing. The abrasive particle size of aluminum oxide can be selected according to the needs of pretreatment. Generally, finer particles are used to avoid leaving deep scratches on the surface, laying a good foundation for the next step of mirror polishing.
The strong durability of ceramic beads makes them suitable for the later stages of high-pressure sandblasting and mirror polishing processes. Its high surface hardness is suitable for removing tiny unevenness or scratches on the metal surface and can form tiny indentations on the metal surface to further enhance its finish. Ceramic beads are particularly suitable for workpieces that require long-term polishing. For example, in the fields of aerospace and automotive manufacturing, metal parts need to withstand long-term high-pressure sandblasting without damaging the surface. Ceramic beads can also reduce the generation of tiny scratches during the polishing process and provide a highly reflective surface for the metal.
In addition, I would like to specifically explain the effect of abrasive size and hardness on finish and reflectivity. Generally speaking:
- Abrasive size: Abrasives with larger particles will remove surface defects faster, but may leave deeper scratches or indentations. Therefore, in the final stage of polishing, fine-grained abrasives are usually selected to gently and evenly polish the surface to create a high gloss and mirror effect. For example, glass beads or ceramic beads with a diameter of less than 100 microns are often used in the final mirror polishing process.
- Abrasive hardness: Abrasives with higher hardness (such as aluminum oxide and ceramic beads) can remove impurities and oxide layers from the surface faster, but the force needs to be controlled during polishing to avoid affecting the surface finish. In the final stage of polishing, abrasives with slightly lower hardness (such as glass beads) are usually selected to reduce surface scratches and achieve a smooth and bright effect.
In the final stage of mirror polishing, the choice of fine abrasives is particularly critical because the gentle grinding action of fine abrasives ensures that the metal surface is smooth and free of marks, making it present a mirror-like high reflectivity effect.
Application Examples
Sandblasting technology is widely used in various industries. Here are some industries and application examples that show how sandblasting can effectively achieve mirror effects:
Automobile Manufacturing
In automobile manufacturing, body parts such as aluminum alloy wheels, decorative strips, and engine hoods often require mirror polishing to enhance appearance and improve corrosion resistance. For example, after sandblasting, aluminum alloy wheels can not only remove surface defects but also achieve a high-gloss reflection effect, improving the overall appearance of the vehicle. At the same time, the mirror effect also helps to reduce the adhesion of dirt and facilitate subsequent cleaning.
Aerospace Industry
The aerospace industry has extremely high requirements for the surface finish of materials to ensure their performance and durability. Sandblasting technology is used to treat aluminum alloy and titanium alloy parts to achieve a mirror effect. These treatments not only enhance the appearance of the parts but also improve aerodynamic performance and reduce air resistance. For example, after sandblasting and polishing, aircraft wings and engine parts can significantly improve their reflectivity and increase their oxidation resistance.
Luxury decoration and artwork
In the field of luxury decoration, sandblasting is widely used in metal artworks, furniture accessories, and architectural decoration. Artists and designers use sandblasting technology to make the metal surface achieve a mirror effect and show a unique artistic style. For example, after sandblasting, the surface of a copper sculpture can achieve an excellent reflection effect and enhance its visual appeal. At the same time, sandblasting can also be used in combination with other polishing techniques to achieve more complex visual effects.
Medical devices
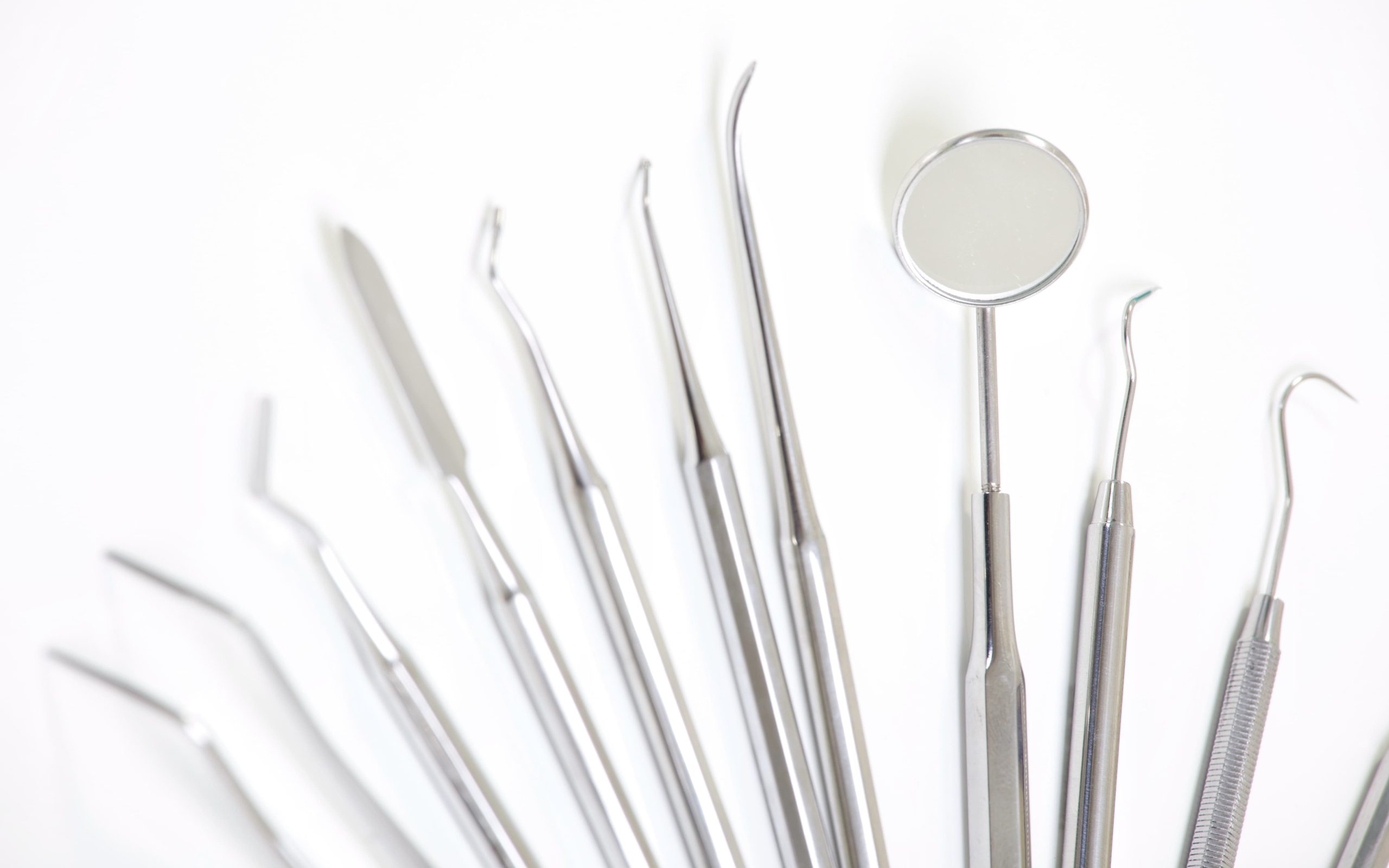
Medical devices need to be kept smooth to reduce bacterial adhesion
The surface treatment of medical devices is also paying more and more attention to the mirror effect. Sandblasting technology plays an important role in the surface polishing of metal implants and surgical tools, ensuring that their surfaces are smooth and defect-free to reduce the risk of bacterial attachment and improve the biocompatibility of the device. For example, after sandblasting and polishing, the surface smoothness and reflectivity of titanium alloy implants are enhanced, which significantly improves their performance.
Electronic products
In the electronic products industry, sandblasting technology is used for the surface treatment of mobile phone casings, computer accessories, etc., aiming to enhance the aesthetics and market competitiveness of the products. Through sandblasting, the metal casing can achieve high gloss and modernity to attract the attention of consumers. At the same time, sandblasting can also remove surface oil and scratches to ensure the excellent appearance of the product.
Architectural decoration
In modern buildings, especially some high-end commercial buildings, metal decorative parts on the facade (such as aluminum alloy curtain walls and stainless steel decorative strips) often need to achieve high gloss and mirror effects. The use of aluminum oxide sandblasting technology can remove the oxide layer and impurities on the metal surface, achieve an elegant gloss, and make it present a beautiful reflective effect under sunlight, which not only improves the visual effect but also enhances the corrosion resistance of the metal.
With the continuous advancement of science and technology, sandblasting technology will continue to innovate and develop. In the future, we can expect more efficient and environmentally friendly sandblasting media and processes to appear to meet the higher requirements of various industries for metal surface treatment. At the same time, as the emphasis on product quality and appearance continues to increase, the application of sandblasting technology in more fields will also be expanded, bringing more surprises and value to the manufacturing and art fields.
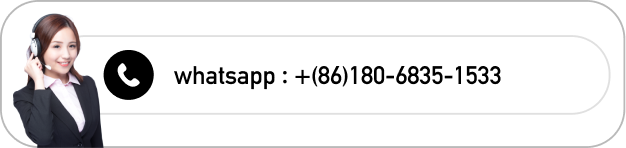